Automated Parts Washers
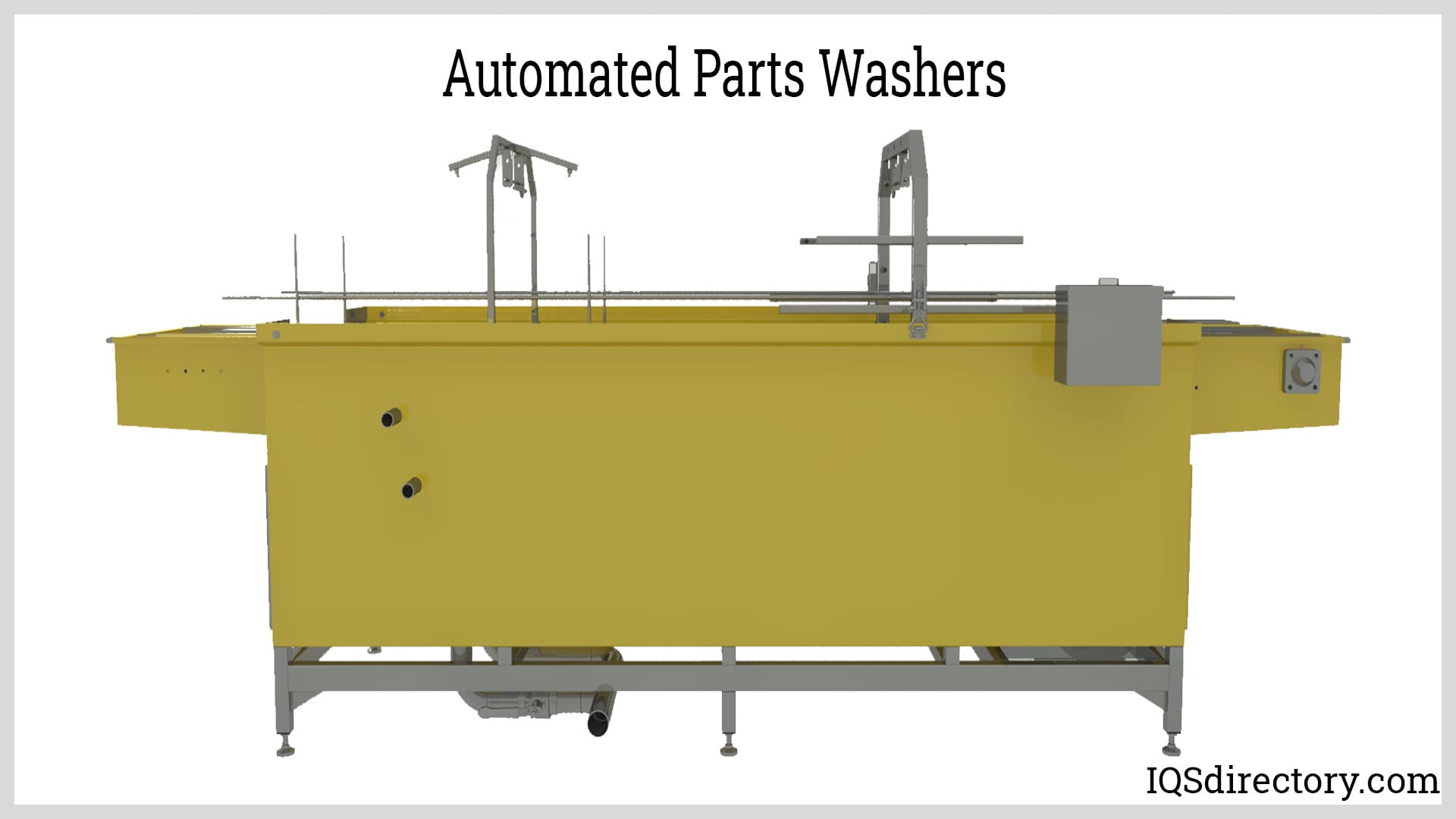
Automated parts washers are mechanical devices designed to efficiently remove grit, oil, grime, dirt, paint and other contaminating substances from parts with minimum manual supervision. These substances are removed...
Please fill out the following form to submit a Request for Quote to any of the following companies listed on
This article will take an in-depth look at aqueous part washers.
The article will bring more detail on topics such as:
This chapter will discuss aqueous part washers, their designs, and their function.
An aqueous part washer is an automated or semi-automated machine manufactured to clean, remove tough grease, and dry large or small parts before distribution or surface treatment.
The washing is necessary since the machines, upon manufacture, are usually forged and fabricated in parts coated with chemicals, oils, and other unwanted residues that remain in the fabrication process.
In the basic design of aqueous part washers, one must first consider the size, shape, and configuration of the parts that need cleaning. Other special aspects to consider are weight angles of parts, surface area, and blind holes. Manufacturers also consider CNC programming, front or back loading baskets, rack systems, trays, conveyor belts, and rotary tables for some types of washers.
Most parts washers are usually aqueous, with a water-based solvent used to soak, boil, or blast dirty parts. The basic components of the parts washers are the water heater, pumps, filtration system, brushes, scrubbers, and cabinet or enclosed space.
The water heater plays an important role in the heating unit. It can be powered by gas, steam, or electricity, and it raises the temperature of the cleaning solution to shorten the duration of the cleaning process. A higher temperature in the cabinet speeds up the rate of chemical reactions of the solvents, detergents, and the chemicals used.
The filtration system filters the water flowing into the system. Upon activation, the cleaning solution or solvent will flow from the cleaning tank and into the storage tank. It's driven through two filters when it flows from the cleaning tank to the storage tank. The first filter consists of a large grid that can capture the large particles before entering the tank. The second filter is designed to hold small particles that would have escaped the larger filter.
The pump is designed to function underneath the solvent, water, or detergent. It pumps the cleaning solutions to the cleaning tank. The pump works continuously and drives water from the storage tank to the cleaning tank. They are designed to operate at high temperatures and drive water at a very high rate of speed. If these factors happen to be low, the parts washer will not be able to remove the dirt completely.
The scrubbers on parts washers are usually a sprayer or a set of brushes. The pump will circulate the cleaning solution from the tank to the scrubbers.
The size and general capabilities of the washer cabinets are wide and varied. The whole process involves a high-pressure application of the aqueous cleaning solution, and it takes place in the cabinet or along the conveyor belt. The water pressure for the cleaning parts must have sufficient force to remove the contaminants. The cabinet is strongly built to withstand deforming from the pressured liquid and continued exposure to corrosive agents.
The greater concern for the storage tank is the level of water inside. If the level drops to very low levels, the exposed heaters may get damaged, and an automatic low water kill valve will turn off the parts washer. It will remain that way until the water level is restored to its minimum required level.
The part washer is operated in timed intervals. First, the parts to be cleaned are placed into the washer atop the turntable, and the door and latches are closed. Then, the timed cleaning cycle is initiated. During the cycle, a high temperature and pressure water and detergent solution is used to blast soils and dirt from the parts.
The washer makes use of a closed-loop waste minimization technology. Following are the factors that ascertain how the washer works.
The topmost factor of the washer’s ability to clean is its power. Higher power can blast and strip away the dirt from the parts. The power is dependent on the pressure and flow of the liquid, or rather, it is the physical force required to remove the residues and soils.
As the temperature increases, the oil and grease become more fluid, and their viscosity is decreased. The grease is usually the primary binder that holds and contains the soil, and when the temperature is increased to up to 160 °F (71 °C), the heat contributes to better and more thorough results of the cleaning.
Furthermore, the chemical reactions inherent to the cleaning solutions are sped up when the temperature increases. It is a general rule that for every 54 °F (12.22 °C) rise in the temperature, the speed of the chemical reaction doubles.
Chemical use is another key factor that greatly affects the industrial strength of the washers. The chemicals are necessary to enhance the solvent’s cleaning power, as some have abrasive and corrosive capabilities that enable the aggressive removal of stains and greasy oils. The chemicals are alkaline to reduce environmental impacts.
There are numerous types of aqueous part washers, and they are mainly categorized by their general build and how they function.
Spray washers use spray cabinets that clean parts by spraying a jet of heated solutions at moderate to high pressures inside an enclosed cabinet. The cabinets have a range of sizes depending on the parts that need to be cleaned, ranging from small to very large-sized cabinets. The spraying nozzles can clean away the heavy and difficult residues of soil, grease, oil, buffing substances, heat debris, and other contaminants.
The parts are loaded into the mechanism through the cabinet door in the front into a porous basket. The basket is then periodically rotated inside the cabinet while the parts are subjected to the high-powered spray that consists of the cleaning chemicals, detergents, and water. This type of part washer is an efficient and very convenient method of cleaning numerous parts at a single time.
A sink top aqueous part washer is simply a sink on a drum, and it is the most common and basic type of part washer. Sink tops are designed to clean or wash individual or very few parts. The mechanism consists of a drum with a sink mounted on top of it containing the solvent or water supply line. The mechanism comes with a pump and brushes for channeling and controlling the solvent.
Some complex equipment parts require intensive cleaning since some contaminants and oxidation results are very difficult and cannot be cleaned by normal pressure sprays or any immersion means. On the other hand, ultrasonic systems make use of ultrasound at varying frequencies ranging from 20 to 400 kHz, in addition to a unique solution. An ultrasonic system consists of three main components. Firstly, a tank is used to hold the cleaning liquid and contain the dirty equipment. Secondly, a generator is used to convert the line voltage into a pitched ultrasonic signal.
Lastly, transducers are used to translate the ultrasonic electrical signals into kinetic and mechanical energy. The cleaning process uses the cavitations of bubbles produced by very high-frequency sound, which in turn agitate the cleaning liquid and heat energy. The energy from the agitation then goes deep into the tiny holes, thin cracks, and the crevices of the part to be cleaned to remove the hard-to-reach contaminants. The ultrasonic part washers are usually bench top and can even take up very large volumes of space.
Immersion part washers have cleaner tanks that use a primitive and rugged design with a pneumatically powered and reciprocating stage for the agitation of parts in the water-based fluid. The immersion parts washers use a system of agitation and oscillations to clean the parts in the bath of cleaning solvents.
The parts are first completely dipped into the solvent. When the part is completely coated with the solvent, an oscillatory vibrating action then creates turbulence inside the solution to make a clean wash to the parts.
The conveyor parts washing systems use an enclosed and automated transport system. The conveyor washers use various belt alternatives like continuous flat wire, interlocking plastic, wire mesh, roller, and chain belts. The guide rails may be fixed or adjustable, and they secure the components and contents of the belt.
The mechanism moves baskets or the fixtures of parts through each section of the cleaning process. The designs of the mechanism differ from one another depending on the specifications of each cleaning stage. The processes in the conveyor parts washer have numerous features that streamline the parts washing. Within each stage, there are processes where the parts are fed through robotic and mechanized means. Some conveyor washers have settings for controlling the variable speed steel belts, moisture blow off, precise filtration units, heaters, and ducts for releasing exhaust. The systems facilitate a continuous inline flow with high-temperature wash zones, rinsing zones, and finishing air drying zones. Specifications can be made depending on the part to be cleaned parameters.
The notion behind the conveyor continuous flow systems is the throughput of a constant flow of the parts with minimum direct handling. The differentiation of the systems is greatly dependent on whether each system has a fixed or varying speed and also on the products which can be processed. Belt conveyor part washers have an outstanding efficiency and a very high speed of processing.
Rotary drum washers make use of a rotating drum with an internal helix which is premeditated to advance and tumble parts within the drum through one or a set of multiple stages. The rotary drum washers are commonly used in the cleaning of very small parts in high volumes. Same as in the conveyor parts washer, the cleaning, rinsing, and drying of the parts happens automatically with the high-pressure sprayer used in the cleaning process. Coupled with the high-pressure spray is an immersion agitation mechanism, which facilitates a deep and thorough cleaning inside the tubes and hollows.
The drum sizes usually vary from 12 to up to 72 inches (30.48 to 182.88 cm), and the pitch and height of the inside helix can be altered or custom-made so that it meets the working requirements of part geometry and the optimum feed speeds. The rotary drum washers also allow for spray, immersion, or both, including washing, rinsing, drying, oil separation, and other advanced features.
The applications and benefits of aqueous part washers include:
Aqueous part washers are used in many applications ranging from industrial applications to day-to-day commercial activities. The incorrectness of a machine can spoil the entire system and cause serious tarnishing to the products or even the brand at large and even ruin future sales. Part washers are widely used in the automotive industry. Part washers are used for the degreasing and cleaning of parts and equipment where grease and oil spill over.
The parts are cleaned to ensure reconditioning and servicing for continued, efficient usage. In addition to part washers being used in the aerospace sector, they are also used to clean aeronautical components, as they ensure a deep and thorough cleaning for reliable and continued use. Part washers are also ideal for the cleaning of metal pipes. The washers are very reliable as they can clean up any type of pipe regardless of size, shape, or material used in the manufacturing process.
Some chemicals that are involved in the cleaning of parts are very harmful and dangerous to human health. Typical examples are trichloroethylene, perchloroethylene, and n-propyl bromide. These chemicals are known to release very volatile organic compounds (VOCs). They are highly flammable and have catastrophic health issues ranging from headaches and dizziness to respiratory problems and spiking of allergy symptoms. Part washers play a pivotal role because they minimize the direct contact between these chemicals and humans. Furthermore, part washers rely primarily on just water, heat energy, and very alkaline detergents that have no serious health concerns.
The chemicals not only pose a threat to the livelihood of human and animal life but also to the surrounding environment. The use of solvent cleaners causes land and air pollution, and all of this can be minimized by the use of comparatively harmless aqueous part washers. The materials used in the aqueous part washers are gentler on the environment, and residues are well taken care of before disposal.
It is ideal for facility owners to choose worker safety over business needs. Aqueous part washers have very short run times, which means less impact on the costs of electricity and fewer human resources required in the processes. The aqueous part washers automatically qualify to be very economical with increased mechanical efficiency.
Looking back on industrial machines that produce final products in the manufacturing processes, adequate cleaning and periodic routine maintenance remain crucial to achieving uninterrupted operations across all functionalities. The upkeep of equipment makes sure that all machines are in perfect working condition with minimal downtime. The aqueous part washers and other cleaning appliances play an important role in ascertaining the safety and endurance of the equipment and, therefore, the quality of the products. The following explains how aqueous part washers are aiding the manufacturing business.
Generally, the incorrectness of any component can spoil the whole product in addition to causing severe harm to the brand image. Furthermore, it can spoil the performance and workability of the machine and cause breakdowns and interruptions. Parts cleaners can clean all possible remains and help the machine operate smoothly. Additionally, scheduled maintenance prevents surface damage, which is one of the most problematic issues for industrial machines. Using stock resource baskets and ultrasonic baskets can be very beneficial in avoiding part damage.
Waste products are a regular outcome of any production phase. These scrap materials add to the cost of production; however, most of the scrap can be reduced by aligning maintenance and parts washing. Taking note and fixing damages on the parts and removing debris and greasy elements help achieve this goal easily.
Production delays tend to be a serious problem in any production facility. They can result in drastic delays in the production output, and this will eventually affect the product sales and brand. Making use of parts cleaning machines guarantees that there is no delay due to the unforeseen breakdown of machinery.
The continued use of machines that do not receive periodic checks and maintenance leaves them prone to frequent breakdowns. Repairs and maintenance procedures have a substantial demand on the budget, but they are worth the input. Some utilities like conveyor parts cleaners, part cleaning systems, and industrial cleaners, due to their dependable output performance, greatly reduce the need for frequent investment in maintenance and replacement of the industrial machines.
Aqueous part cleaners have a moderate to very high initial startup cost. Setting up the mechanism requires technical expertise to ensure the machine will be reliable and efficient in the future. Washers make use of electrical energy for the heating and energy conversions that occur, and this makes them more expensive than regular solvent units. Aqueous part washers are also prone to corrosive agents like oxygen or water. Because of this, measures must be taken to reduce rusting of the parts through the use of rust inhibitors and additional drying mechanisms to ensure no moisture remains on the equipment. Some stains and residues that require cleaning are very stubborn and difficult to handle.
Most chemical change effects leave residues that are difficult to remove even when an ultrasonic part washer is used. Aqueous part washers demand a lot of attention, and maintenance is very intensive. The washers require periodic maintenance to ensure that there are no blockages, clogs, or damage from the tiny dirt particles left over from washed parts. The contained and potentially limited build of part washers makes some of them unsuitable for cleaning very large parts. The cleaning compartments of some of the part washers are very small and will not be able to accommodate larger parts that require cleaning.
Aqueous part washers function just like any other industrial part washers, with the prime objective being to remove dust, oil, and grease from the surfaces of machine parts. However, the way these devices launder equipment is different from the methods used by other washer categories. The aqueous cleaners use detergents, water, corrosive agents, and heat energy to remove debris from mechanical parts. They are considered safe machines to operate, but part washers can be a huge threat if they become contaminated beyond operational working limits. When working beyond operational limits, the machines become more likely to achieve flash points greater than 140 °F (60 °C), which increases the flammability risk of the parts cleaning operation.
Along with the increase in heat output, the aqueous cleaning systems tend to pose other serious safety concerns. Without proper supervision, the aqueous cleaning system can reach pH levels lower than 2.0 (very acidic) or higher than 12.5 (very alkaline), with both situations having harsh impacts on the environment.
As implied by the name, an aqueous cleaning apparatus makes use of water to bathe and clean machine parts. The businesses involved must control the amount of water they use so that they adhere to water usage regulations and keep their water bills under control. Facilities utilizing aqueous cleaning appliances to wash machine parts must consider employing the following techniques to control water usage.
To ensure the protection of final developed products and employees during production and cleaning, operators must keep track of the hazard level of the cleaning solution. Some part washing systems are marketed based on their property of being non-toxic or non-hazardous. But as time moves on, the so-proclaimed safe solutions become potential threats to both people and the machines. The cleaning solution will eventually become more toxic and potent in metal-bearing oils and grease-infested elements. Following are some techniques to control the levels of toxins in the solution:
The other crucial component in part washing cleaners is the chemical or detergent used. The detergent used depends on the parts that need to be cleaned, and the method used, either ultrasonic or spray technique.
The parts cleaning involves the usage of part cleaning detergents and chemicals, many of which are dangerous, toxic, and hazardous. Therefore, it is very important to monitor the workplace environment so that there is sufficient control over these toxic chemicals to avoid illness and injuries.
The detergents and chemicals used in parts cleaning are typically:
Cleaning parts is a complex procedure that utilizes specially designed materials that can remove grease, oil, grime, chemical solutions, and soil debris from high volumes of parts manufacturing. In accordance with an increase in environmental concerns, manufacturers are making use of biodegradable ingredients.
Oil eating detergents are a very effective technique for cleaning industrial parts and can be used as an acid-free degreaser.
All water-based cleaning chemicals have a neutral pH that is non-toxic, non-flammable, non-irritating, and can be employed in bioremediation systems.
The detergents for aqueous parts cleaners are designed to be utilized in jet sprayers and power stream washers. For the highest efficiency, detergent solvents have a deformer that floats to the top of the cleaning solution surface to avoid foaming.
Numerous types of washing solutions are designed to be used in ultrasonic parts cleaners. The different types include acidic chemicals, alkaline chemicals, high caustic solutions, deionized water, enzymatic chemicals, neutral solution, and mildly alkaline chemicals.
Ultrasonic washing solutions are either demulsifying or emulsifying. Demulsification is used to remove oily contaminants, and the demulsifiers must be drained from the tank soon after cleaning. Emulsifying solutions, on the other hand, suspend contaminants inside the tank. If they are used over several cleaning cycles, the debris may stick to the parts upon removal.
Very strong abrasive chemicals are used to guarantee proper washing and incomparable performance of parts cleaners. Regardless of the technique used to wash the parts, very powerful cleaning agents are necessary and include chemical solutions such as Trichloroethylene, Sodium Hydroxide, Butyl Cellosolve, Acetone, Toluene, Bacteria, Benzene, and Acetone.
Trichloroethylene is a water-like chemical used in cleaners and solutions. Sodium Hydroxide is a scathing cleaning agent that can liquefy grease, oil, fatty acids, and protein deposits. Butyl Cellosolve is a common chemical found in cleaners mainly used in industries and household chemicals. Acetone is a common cleaner and is also used to treat metals before they are painted.
Toluene is a chemical half as powerful as acetone solution and butanone, and it is the primary component in paint thinner. It can dissolve adhesives, rubbers, and sealants. A bacterium is used in part cleaners to provide a natural technique of removing stains and soils through bioremediation. Benzene is a popular chemical used in manufacturing processes that requires extra care because of its harmful effects.
In summation, aqueous part washers are a form of machinery used to clean small to medium parts of industrial machines through the use of water-based solvents and temperature controls.
Automated parts washers are mechanical devices designed to efficiently remove grit, oil, grime, dirt, paint and other contaminating substances from parts with minimum manual supervision. These substances are removed...
A parts cleaner is a cleaning device that uses various types of solvents, cleaning agents, and processes to remove grease, grime, and contaminating materials from manufactured parts prior to shipment or movement for further processing...
A parts washer is a mechanical device designed to remove grit, grime, oil, miscellaneous debris, dirt, paint, and other contaminating substances from parts in preparation for their use in assembly operations, packaging, or coating...
A wastewater evaporator is a method of removing water from water-based waste by converting the water in the waste to a vapor and leaving contaminants. The function of a wastewater evaporator is to reduce the volume of waste materials...
Parts washers are designed for cleaning, degreasing of equipment, and drying of mass quantities of small or large parts in preparation for surface treatment, assembly, inspection, or shipment...
Industries worldwide utilize abrasive blasting for various purposes, including cleaning rust and oil, removing surface coatings like paint and pollutants, preparing surfaces for paint and coatings, reinforcing metal surfaces and...
Deburring is a secondary operation of a machining process that enhances the final quality of the product by removing raised edges and unwanted pieces of material, known as burrs, left by the initial...
Finishing machines are machines used for metal finishing, which is the last stage of the metal fabrication process; the stage encompasses the use of machines in finishing the metal surface...
Sandblast cabinets include systems or machinery and components for projecting blast media against a part‘s surface to abrade, clean, or modify the surface. Sand, abrasive, metal shot, and other blast media are driven or propelled using pressurized water, compressed air, or a blast wheel...
Sandblasting equipment includes systems or machinery, and components for projecting blast media against a part‘s surface to abrade, clean, or modify the surface. Sand, abrasive, metal shot, and other blast media are driven or propelled using pressurized water, compressed air, or a blast wheel...
Shot peening equipment includes systems or machinery and components for projecting shot peening media against a part‘s surface to modify the surface or surface engineer the part...
A tumbling machine is a durable deburring and metal-polishing machine designed for finishing large parts or batches of smaller parts. A tumbling machine is also known as a barreling machine or a mass-finishing...
An ultrasonic cleaner is a type of sonic cleaner or sonic cleaning machine that uses cavitation to remove unwanted material. The cleaning effect is created by the compression and refraction of a cleaning medium. Miniscule vibrations propagate throughout the...
Ultrasonic cleaning is a type of cleaning process which uses cavitation induced by alternating compression and rarefaction cycles at ultrasonic frequencies. Ultrasonic frequencies are sound waves vibrating at 20 kHz or higher...
Vibratory tumbler is the equipment used in a vibratory finishing process, one of the most common methods in mass finishing. But how does a vibratory tumbler work...