Types of Metal Finishing
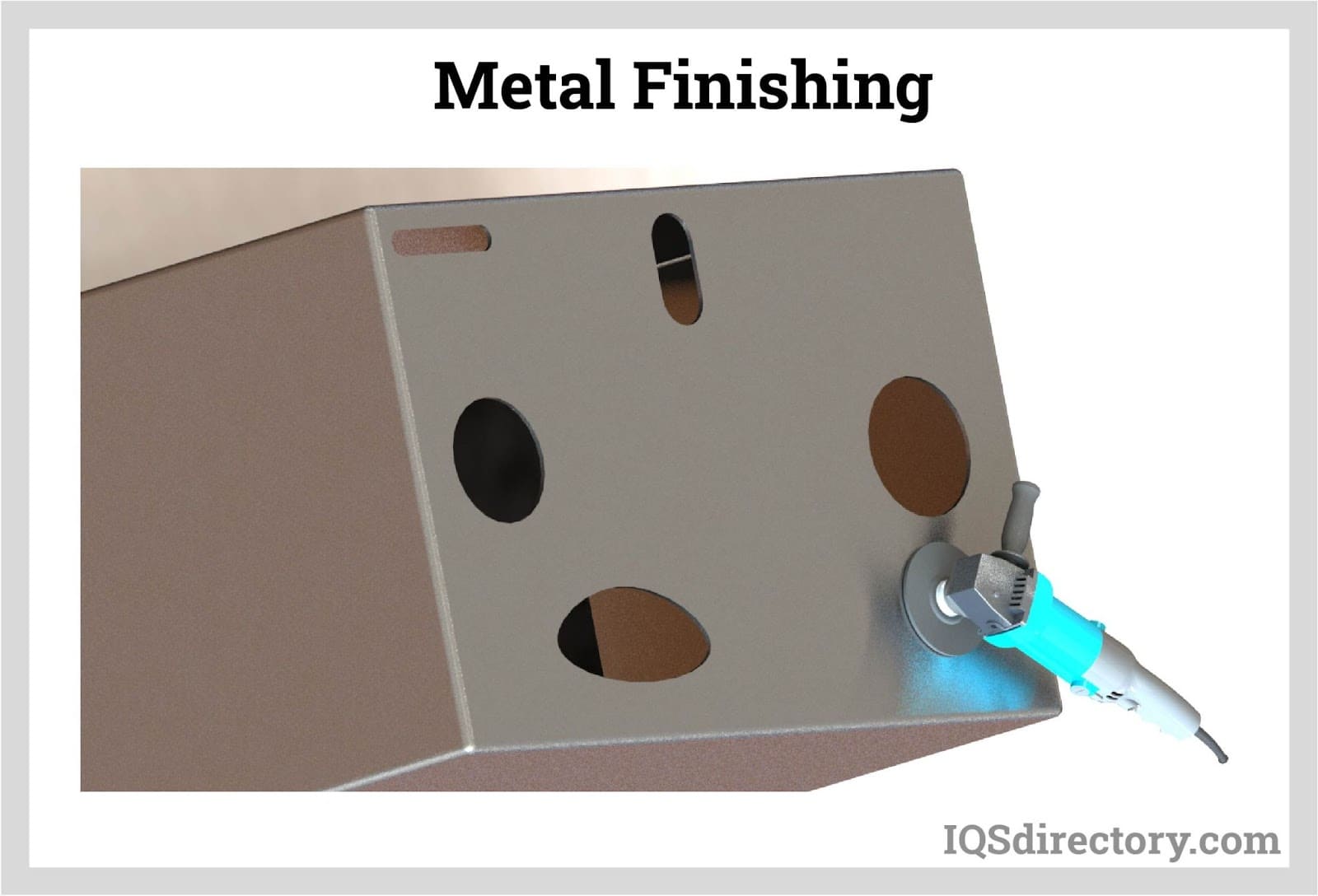
Metal finishing describes various procedures or processes that can be as simple as buffering to adding a special type of coat to the substrate. Included in the description of metal finishing are a number of cleaning...
Please fill out the following form to submit a Request for Quote to any of the following companies listed on
This article takes an in-depth look at anodized aluminum.
Read further and learn more about:
Anodized aluminum is aluminum that has undergone an anodizing process to create an exceptionally durable, corrosion-resistant, and aesthetically appealing surface. An electrochemical process involving a series of tanks is used to grow an anodic layer on the surface of the aluminum. Since the layer is formed from the metal, it never chips, peels, or flakes. Aluminum anodizing makes aluminum three times harder than standard aluminum and 60% lighter than stainless steel and copper.
The anodizing process creates a stable aluminum oxide layer that is integrated with the underlying aluminum substrate and makes raw aluminum harder and stronger. The added anodic layer is porous, which makes it suitable for the application of dyes, paints, lubricants, and adhesives. Aluminum anodizing enhances aluminum’s corrosion and wear resistance enabling it to withstand the harshest environmental conditions.
Anodizing creates a stable aluminum oxide layer fully integrated with the underlying aluminum substrate. This layer is harder and stronger than raw aluminum. It is resistant to chipping, peeling, scratching, and flaking because this layer is intact with the aluminum substrate and not applied on the surface. The structure of this layer may be highly porous, making the anodized part suitable for the application of dyes, paints, lubricants, and adhesives. Lastly, this layer significantly imparts corrosion and weathering resistance to the raw aluminum, allowing them to withstand harsh environments.
Anodizing does not interfere with the recyclability of aluminum. In addition, this process is more environmentally friendly than electroplating and spraying.
Anodized aluminum parts exhibit a smooth, lustrous surface which makes them appealing. Anodizing allows these parts to be dyed or colored brightly. The colored film is highly fade-resistant. Hence, anodized aluminum is widely used in decorative and architectural applications.
Anodizing is an electrolytic passivation process that increases the thickness of the natural oxide film on the surface of a part. The created film or layer is durable, stable, and enhances aluminum’s natural corrosion resistance. Aluminum anodizing is a controlled oxidation process that involves the use of an acidic electrolyte bath in tanks with direct electrical current (DC) supplied to anodes and cathodes.
Aluminum parts being anodized act as the anode. A cathode plate or rod made of platinum, stainless steel, lead, or carbon supplies the negative part of the electrical circuit. As voltage is applied to the circuit, an aluminum part loses positive ions and attracts negative ones, which causes a layer of aluminum oxide to grow on the aluminum part.
Anodizing is commonly performed in aluminum, though non-ferrous metals such as magnesium, zinc, and titanium; even conductive plastics can also be anodized. However, Anodizing is not beneficial to ferrous metals such as carbon steel due to ferrous oxide or rust formation instead of a stable and corrosion-resistant film.
An anodizing operation may be batch or continuous. In batch anodizing, the parts are placed in a rack and immersed in a series of baths. The parts are collected at the end of the process. Batch anodizing is employed in cookware, castings, and bent or machined parts. In continuous or coil anodizing, the pre-rolled material is unwound and continuously goes through the process steps. Once the steps are completed, the material is coiled and shipped to the customer. Continuous anodizing is performed in less deformed parts, wires, plates, sheets, and foils.
There are four stages in an aluminum anodizing operation:
The pre-treatment stage is crucial because it greatly affects the anodized part‘s finishing quality and final appearance. It involves cleaning the contaminants such as dirt and grease from the raw aluminum part surface that can hinder the process and removing minor surface imperfections. In addition, machining processes, such as drilling, cutting, and welding, must be performed before this stage.
Chemical or mechanical methods may be performed as a pre-anodizing treatment:
Chemical pre-treatment involves using several chemical solutions to remove dirt and grease (by an acid or an alkali cleaner) and surface oxides and heat-treat scales (a deoxidizing agent). After that, an etching or a brightening step is performed to modify the texture of the surface, which produces a distinct appearance:
An etching step produces a dull or matte finish. This step removes a uniform layer from the aluminum part surface, thus reducing the minor surface defects. Etching is accomplished by immersing the parts in hot sodium hydroxide or trisodium phosphate (alkali etching) or aqueous ammonium bifluoride (acidic etching).
A brightening step produces a shiny or mirror-like finish. The microscopic peaks and imperfections on the aluminum part surface are flattened and smoothened in this step. Thus, the roughness is reduced, which results in a highly reflective surface. Brightening is accomplished by immersing the parts in a phosphoric or nitric acid bath. Additives are mixed with the acid bath to enhance its brightening ability and reduce toxic fumes.
Mechanical pre-treatment involves procedures such as abrasive polishing, sandblasting, and shot peening to expose. Sandblasting and shot peening can improve the aluminum part‘s fatigue resistance, hardness, and coating adhesion. Good coating adhesion is necessary for the stability of the coating.
Electrolysis is the central process of an anodizing operation. In this stage, the aluminum part is submerged into an electrolytic solution bath that contains many positively and negatively charged ions. The aluminum part and the cathode are connected to the positive and negative terminals of the DC power supply, respectively. As DC is applied to close the circuit, the part becomes positively charged as electrons are withdrawn from its surface. These electrons migrate through the electrolyte bath to the cathode interface and react with hydrogen ions to form hydrogen gas. The aluminum cations at the surface react with water, creating the aluminum oxide (Al₂O₃) layer. The chemical reactions are summarized as follows:
Chemical Reactions | |
---|---|
Reactions at the Anode |
Al → Al3+ + 3e
2Al3+ + 3O2- → Al2O3 2Al3+ + 3OH → Al2O3 + 3H+ |
Reactions at the Anode | 2H+ + 2e- → H2(g) |
Overall Recation | 2Al + 3H2O → Al2O3 + 6H+ 6e- |
There are two types of oxides films produced during the electrolysis process, depending on the chemical composition of the electrolyte bath:
A barrier oxide film is formed on the part surface when the film is grown in a neutral solution (e.g., ammonium borate, phosphate, or tartrate compositions), in which aluminum oxide is insoluble. This film is durable, unreactive with the solution, and protects the underlying aluminum from the environment. The thickness of the barrier oxide film depends on the voltage applied between the cathode and the anode. However, only a maximum voltage can be used before side reactions such as sparking, solute oxidation, and oxygen evolution occur.
A porous oxide film is formed on the surface when grown in a dilute acidic solution (i.e., around 10% acid content). The commonly used acidic electrolyte bath is sulfuric acid, though anodizing in phosphoric acid, oxalic acid, chromic acid, and mixtures of inorganic and organic acids are performed. The acidic solution can retain a high concentration of All₂Ol₃ molecules.
The reaction at the anode side results in forming a barrier aluminum oxide film. As the current flows through the part, it concentrates on the relatively weak and reactive spots on the part surface, producing a highly porous or cellular structure film. The aluminum oxides removed from the pores are dissolved in the acidic solution.
The film thickness is proportional to the electrolysis time and voltage, and the longer electrolysis times and higher voltages produce thicker oxide films. And a deeper column-like hollow structure. Meanwhile, the pore dimensions depend on the bath‘s voltage, temperature, and acid concentration.
There are three main types of aluminum anodizing processes according to MIL-A-8625 specification (anodic coatings for aluminum and aluminum alloys). These types produce a distinct set of properties.
Type I anodizing utilizes chromic acid to create the aluminum oxide film. This type produces the thinnest aluminum oxide film, measuring around 20-100 microinches thick while offering good corrosion resistance when appropriately sealed. In addition, this film is dielectric and non-conductive and is used as a primer for paint and adhesive application. Type I anodizing is suitable for tight tolerance parts; it does not change the part dimensions significantly.
Type I anodized aluminum parts have good forming qualities, and they can be utilized under high stress and bending conditions. These parts are widely used in the aerospace and aircraft industries. These parts appear grayish, even when dyed black. The low film thickness limits the dye absorbed by the film.
However, there are environmental concerns when employing this type since chromic acid is toxic and carcinogenic. Facilities offering Type I anodizing services require a special wastewater treatment facility to treat the chromic acid wastes.
Type II anodizing is the most common type of anodizing process and utilizes sulfuric acid instead of chromic acid. Sulfuric acid as an electrolyte solution produces porous structures efficiently. Hence, Type II anodized parts can easily absorb dyes, paints, and adhesives. In addition, they can be dyed with various colors for decorative purposes. Type II anodizing process produces a thicker oxide film whose measurement ranges from 100-1000 microinches wide. This film is also dielectric and non-conductive.
Type II anodized parts have good abrasion and corrosion resistance and are harder than type I anodized parts. These parts are used in decorative applications, architectural, consumer electronics, consumer goods, military kitchenware, military weapons, optical components, etc.
Type II anodizing is less expensive than Type I because of the cost of the chemicals consumed, energy requirements, and waste treatment requirements.
Type III anodizing also utilizes sulfuric acid as the electrolyte solution. However, this type is performed using a higher current density, higher voltage, and lower temperature than Type II anodizing. Type III anodizing produces a much thicker and highly porous oxide film which measures greater than 1000 microinches thick. This type also has the hardest and most durable coatings. However, it may not suit parts with extremely tight tolerances as it can slightly modify the part dimensions. This type also produces a dark film typically left undyed or dyed black.
Type III anodized parts, commonly known as a hard coat, offer superior abrasion, wear resistance, and good electrical insulation. In addition, the coefficient of friction may be diminished by PTFE impregnation, which is beneficial for parts frequently subjected to frictional forces. They also have excellent corrosion resistance. However, the increased thickness of the oxide film penetrating beneath the aluminum part surface decreases the fatigue resistance of the part.
Type III anodized parts are widely used in the military, aircraft, and aerospace industries. They can be used to manufacture sliding parts, linear guides, pistons, valves, hinges, gears, insulation plates, compressor fittings, automotive parts, and a lot more.
Like Type II, Type III anodizing is safe and environmentally friendly but more expensive due to the required process conditions.
The other types of aluminum anodizing processes are the following:
Boric-sulfuric acid anodizing (BSAA) is an alternative to Type I anodizing due to the environmental and safety concerns brought by Type I anodizing. BSAA offers excellent paint, lubricant, and adhesive adhesion as Type I anodizing. It also imparts good corrosion resistance and is suitable for parts with tight tolerances. BSAA is also widely employed in aircraft and aerospace parts manufacturing.
Phosphoric acid anodizing, also known as PAA or the Boeing Process, is an alternative to Type I anodizing and utilizes phosphoric acid to create oxide films. The rough morphology of PAA-created films has protrusion and whiskers on its surface, giving the oxide film an excellent adhesive property. This film can also withstand high humidity. Therefore, PAA can be used to prepare the aluminum surface for the application of bonding primer. PAA is commonly used in structural adhesive bonding.
Thin-film sulfuric acid anodizing (TFSAA) uses a sulfuric acid-based electrolyte bath with a lower concentration than Type II anodizing. As a result, TFSAA produces a thinner oxide film than those produced by Type II and Type III anodizing. Hence, it can be considered an alternative to Type I anodizing.
TFSAA-anodized parts have higher fatigue strength than Type II and Type III anodized parts because of their relatively thin oxide film. Hence, these parts are suitable under high-stress conditions. They can also be dyed easily. However, these parts have poorer corrosion resistance compared to Type II and Type III anodized parts.
Clear anodizing involves sulfuric acid anodizing followed by sealing the anodized part in a hot water bath. The finishing produced is not transparent; this process is instead used to create a uniform, transparent film on the aluminum part, which enhances its aesthetic value. The anodized part is usually left undyed, and the color produced depends on the thickness of the oxide film. Clear anodizing is typically used to finish automotive trims, window and door frames, railings, sidings, photography plates, and extrusion profiles.
Bright dip anodizing involves a pre-treatment of phosphoric and sulfuric acid mixture, which gives a glossy and highly reflective finish. The pre-treatment is followed by a Type II anodizing. The anodized part is then dipped into a coloring dye before the porous film is sealed. The resulting appearance depends on the grade of aluminum alloy. Nonetheless, bright dip anodizing enhances the overall aestheticity of the part.
Black anodizing involves a standard anodizing step followed by coloring the anodized part with an organic or inorganic black dye. Black dyes are one of the dyes specially formulated in coloring aluminum parts. Inorganic dyes such as ferric ammonium oxalate produce a more lightfast finish than organic dyes. Lightfast is the property of a finish which describes how fade-resistant it is when exposed to light. Electrodeposition of a coloring metal to produce a black anodized finish may also be performed.
Color anodizing involves a standard anodizing step followed by dip coloring using organic dyes. The colors of organic dyes available are more varied than inorganic dye colors. Color anodizing is mainly used for aesthetic applications. However, organic dyes produce a less lightfast finish than black anodized parts.
The dye or pigment fills the porous aluminum oxide film formed by electrolysis in the coloring step. The dyes of an anodized part are intact with the film. The "coating" of anodized aluminum is durable and cannot be scratched off from the surface. A highly porous surface is ideal for the introduction of dyes and pigments.
After rinsing the anodizing solution from the part and subsequent drying, Coloring is done. It can be accomplished by one of the following methods:
In electrolytic two-step anodizing, the anodized part from the electrolysis step is immersed in a bath containing metallic salts. Next, an electrical current is applied to the part. Metallic ions are electrolytically deposited deep in the pores of the oxide film, which gives a distinct color to the anodized part. The common coloring metals are cobalt, tin, copper, and nickel. The produced color and its quality depend on the metal deposited and the amount of metallic deposits in the pores.
In interference coloring, the oxide film pores‘ bases are enlarged to deposit more metallic ions electrolytically. This method produces light-fast colors ranging from blue, green, and yellow to red due to the optical interference of the visible light waves.
In integral coloring, the anodizing and the coloring steps are combined as the oxide film is colored. The anodizing bath is composed of organic acid and sulfuric acid. As a result, the produced "coating" is thicker and more abrasion-resistant. However, this method is expensive, and the colored oxide films are harder to produce. The colors are also limited to pale to dark yellow and bronze, brown, black, and gray.
The anodized part is immersed in a coloring bath that contains the dye in dip coloring. The dye is adsorbed on the surface of the pore opening of the oxide film. The resulting color depends on the type and chemistry of the dye. Dip coloring is an inexpensive method that allows the manufacturer to coat the aluminum parts with various colors. However, the colored film is not resistant to UV, unlike the colored films produced by other methods.
A lubricant or an adhesive replaces the coloring agent in processes involving the application of such substances. The coloring step is skipped for undyed parts.
The final stage of this process is sealing the aluminum anodizing operation. It locks the absorbed dye, lubricant, or adhesive on the porous film. It protects the porous film from corrosion, staining, and absorbing unwanted molecules. It also protects the color from fading. It is accomplished by treating the part with a sealing agent which closes the pores or reduces the pore opening diameters of the film. Sealing must be performed immediately after the coloring step due to the sensitivity of the oxide film.
Aluminum anodizing is an environmentally friendly process that creates an aluminum oxide layer for the manufacture of products with a durable and weather resistant finish. The result of anodizing increases the design possibilities for companies who produce aluminum products.
Aluminum anodized phone cases make phone cases resistant to scratching, impacts, and the natural wear tear that phone cases experience during their use. The layer of anodized aluminum makes it possible to use a treated phone case in a wide range of environments regardless of humidity, moisture, or exposure to certain chemicals.
Aside from the protective properties created by aluminum anodizing, phone cases made from anodized aluminum have an appealing appearance with a smooth stylish finish and come in colors that meet a user's requirements. They provide a snug fit with cuts specifically designed for each type of phone. As with all aluminum products, anodized aluminum phone cases are lightweight with a profile that conforms to the phone they are protecting.
As with all aluminum products, the grade of aluminum used to produce aluminum anodized cases determines the level of protection the case provides. The variations in the grades of aluminum are determined by the amount of chromium and other alloys.
One of the necessities for laptops is protection since they are a sensitive instrument that contain electrical elements that can be easily broken. Anodized aluminum laptop frames significantly increase the level of protection provided by aluminum. Non-anodized aluminum can become bent or damaged upon impact while anodized aluminum, due to its strength and durability, is unaffected by impacts, bumps, or punctures.
Laptops need to be lightweight and portable, which is one of the main reasons for their popularity. Although stainless steel has many of the properties of aluminum, it is heavier and increases the weight of products. This particular drawback is one of the reasons that anodized aluminum, with its superior strength and lightweight, is so popular as frames for laptops.
As manufacturers have rapidly discovered, laptops have to be adjusted and customized to fit the needs of users. A laptop for a college student is far different than one that is designed for an engineer. Additionally, the features and size of a laptop for a business executive is far different from ones for musicians and composers. These characteristics require that manufacturers attune their products to the needs and requirements of their users. Anodized aluminum frames are easily customizable and adaptable to meet the conditions, demands, or designs of all users.
The main material for the production of a tablet enclosure is anodized aluminum, which is the foundation of tablets and serves as its back case and composes 17% of the weight of a tablet. The aluminum tablet enclosure houses the main components of a tablet and protects the components from damage. It is for this reason that anodized aluminum is the main material. In the manufacture of tablets, aluminum is the first choice as a protective and durable material capable of withstanding the many conditions where tablets are used.
The porous properties of anodized aluminum make it possible for tablet enclosures to be colored or painted in a full array of colors, which is essential for marketing and meeting the needs of users. Additionally, coatings or painting enhance the protective properties of an aluminum anodized enclosure.
The logic board of a tablet is connected to the tablet enclosure using tin as the soldering agent. When possible both the aluminum and the tin solder are made from recycled materials. Since tablets have to endure more stressful use, their aluminum enclosure or case is made of anodized aluminum instead of plastic or stainless steel. Plastic is not capable of surviving the types of impact that tablets must endure, and stainless steel is too heavy for such a compact device.
The choice of anodized aluminum for window frames is due its long useful life, which can be as long as 20 years or more. Additionally, the anodizing process produces a smooth metallic finish that is aesthetically appealing and does not change color or appearance over time.
The main concern when considering structural elements for buildings is their resistance to wear. In many cases, painted or coated aluminum is chosen as the best material for window and door frames due to its appearance and resistance to corrosion and rust. The addition of an anodizing layer to aluminum heightens its weather resistance and wear resistant properties far beyond those of untreated aluminum.
The anodized layer of anodized aluminum is a passive film and a thick layer of oxide that radically improves the corrosion resistant properties of aluminum. It is chemically inert and does not break down over time, which is a key feature that builders and architects want to include in their projects. Anodized aluminum window frames will not fade, peel, or deteriorate and provide a long lasting, durable finish.
Curtain walls serve as an exterior cladding system that has an anodized aluminum frame capable of withstanding weathering, wear, corrosion, and rust. Architects include curtain walls in their designs due to their exceptional appearance and aesthetic appeal. In order to maintain their appearance, curtain walls have to be made of robust material with properties that are strong and durable, which is one of the main reasons for the use of anodized aluminum.
Anodized aluminum is highly prized as a functional part of curtain walls due to its weight to strength ratio. Additionally, the use of anodized aluminum provides architects with sufficient flexibility of design such that they can create customized features that meet the needs of their clients.
Other features that make anodized aluminum the perfect choice for curtain walls is their prevention of fire since they reduce its spread. This is in addition to their lower cost when compared to other construction methods. Aside from their safety features and low cost, anodized aluminum curtain walls assist in lowering power consumption by stabilizing building temperatures and increasing lighting efficiency.
Anodized aluminum doors are similar to anodized aluminum windows and have the same aesthetically appealing appearance and smooth finish. Doors made with anodized aluminum have their finish shine through, which gives them a more vivid appearance in comparison to painted or coated aluminum.
Unlike coated and painted doors that fade with age and yellow due to exposure to UV rays, anodized aluminum doors retain their shiny appearance over time and do not yellow. During their use, doors take a great deal of abuse due to being opened and closed multiple times. As a result, they get scratched and dinged. The strength and durability of anodized aluminum prevents and protects doors from losing their appearance due to constant use.
A part of doors that takes the most abuse are kick plates, which discolor, tarnish, and get damaged. Anodized aluminum kick plates are able to withstand the constant punishment and provide a polished decorative appearance that is undamaged. Additionally, kick plates and doors with aluminum anodizing can be coated with brass or bronze finishes to further enhance their appearance.
A popular use for anodized aluminum is as material for facades due to its lightweight and wide assortment of colors that are a bonded part of the molecular structure of the metal. This aspect of the anodized aluminum gives architects several options when determining the exterior appearance of a building. Its natural metal look makes it a perfect and desirable solution to issues of design.
Anodized aluminum facades refract and reflect light to keep the interior of a structure comfortable and pleasant. This particular feature of the facades is a practical energy saving consequence of the superior quality of anodized aluminum. It protects a building from the adverse effects of weather and heat while providing a comfortable environment.
The high strength to weight ratio of anodized aluminum makes it possible to bend, shape, form, and configure it around corners, over edges, and meet the requirements of double curved designs. It can be roll formed, stamped, engraved, and perforated as a screening material for parking garages. Anodized aluminum facades provide a strong and viable solution to any type of architectural challenge.
Most automotive trim is made of anodized aluminum due its ability to create a hard, smooth, and impenetrable surface. Many of the components of vehicles are made of aluminum due to the need to lighten their weight to save on gas and decrease gas usage per mile. Anodized aluminum is used in the construction of automobiles because of its strength, durability, lightweight, recyclability, formability, and its ability to accept different forms of surface treatments.
As with any product, lowering the cost of manufacturing is a necessity for customer satisfaction. Anodized aluminum trim is easy to install, provides exceptional protection, and requires little finishing or maintenance at low cost. These factors play a role in its use in automotive manufacturing. Additionally, it can be treated to enhance the appearance of a vehicle.
The benefits of using anodized aluminum in the auto industry include its chemical stability, inability to decompose, being nontoxic, and its ability to be recycled, which has become a major issue nationally and internationally. With the ever growing concern for the environment, anodizing is appealing since it does not add any material to aluminum but simply enhances its natural properties. Since anodizing actively restructures the surface of aluminum, it does not produce any waste material, which assists in cost savings.
As with other aluminum products, bike frames depend on aluminum as a construction material due to its lightweight, stability, durability, and low cost. Anodized aluminum bike frames are made from aluminum alloys 6061 and 7005 that have enhanced and improved properties due to their alloys. The stability and strength of anodized aluminum is one of the main reasons it is used for bike frames, which take a beating when constantly used.
Aluminum grade 6061 is precipitation hardened and contains percentages of silicon and magnesium. It has high tensile strength, good mechanical properties, weldability, and is a general purpose aluminum alloy. Grade 6061 is ideal for bike frames due to its ability to provide a smooth ride over rough terrain.
Aluminum grade 7005 is most commonly used in bike frames due to its weldability and tensile strength of 350 MPa with a fatigue factor of 150 MPa. Unlike aluminum grade 6061, grade 7005 contains zinc in place of magnesium, which makes it more expensive than grade 6061. The zinc content in grade 7005 makes its bike frames stronger especially when the frame becomes thinner for the manufacture of road bikes.
The three versions of bike frames are single butted, double butted, and triple butted, which refer to the thickness of the aluminum tube used to produce the frame. Single butted bike tube has the same thickness for all of its tubing. Double butted has thin and thick tubing while triple butted has three thicknesses. Grade 6061 anodized aluminum is commonly used for single butted bike frames while grade 7005 is used for double and triple butted frames since it can be thinner and still retain its strength.
Cookware is made from several materials including cast iron, stainless steel, copper, and aluminum. Cast iron was one of the first types of cookware but has lost its appeal to lighter metals such as copper and aluminum. Anodized aluminum cookware and standard aluminum cookware have the same properties of corrosion resistance, resistance to rust, and exceptional heat transfer.
The deviation between anodized aluminum cookware and standard aluminum cookware is its resilience. As with other anodized aluminum products, anodized aluminum cookware does not chip or flake and can withstand temperatures up to 500o F (260o C). . Handles of anodized aluminum cookware remain cool and easy to position during cooking. Standard aluminum pans have to have a coating or cover on their handle.
A concern when cooking with standard aluminum is metal leaching into the food or having a reaction with acidic foods. Anodized aluminum is sealed to prevent leaching and acidic reactions. The surface is scratch resistant and exceptionally easy to clean. Anodization produces a dark aluminum oxide sealed surface that is safer and healthier.
There are two classes of anodized aluminum based on MIL-A-8625:
Class 1 anodized aluminum refers to the undyed anodized parts. The coloring step is skipped for these parts. The produced color will depend on the type of alloy, anodic thickness, and anodic treatment and sealing parameters. The produced color is usually clear gray or bronze and shall be the final color of the part.
A class I anodic coating has a minimum thickness of 0.7 mils or 18 microns. This coating is considered a "high-performance anodic finish ."Class I-coated parts are typically used as a building or construction material intended for continuous outdoor exposure. These parts include guard rails, curtain wall panels, rain screens, and fences.
Class 2 anodized aluminum refers to dyed or pigmented anodized parts.
The classes of architectural anodic coating based on the Aluminum Association designation are as follows. These classes are different from those specified by MIL-A-8625.
A class II anodic coating has 0.4 mils or 10 microns minimum thickness. Class II-coated parts are used in interior or light-exterior building applications which are not subjected to high fatigue and wear. These products include radiators, wall fins, column covers, trims, and storefronts.
Metal finishing describes various procedures or processes that can be as simple as buffering to adding a special type of coat to the substrate. Included in the description of metal finishing are a number of cleaning...
Metal plating is a process where a thin layer of metal coating is applied on the surface, or on the substrate of a metal part, product, or component. The process of metal plating can consist of electroplating...
Aluminum 1100 is the softest of the aluminum alloys, which makes it easy to shape and form into a wide range of products for industrial and home use. It can be cold and hot worked but is frequently shaped by...
An aluminum channel is a structurally sound metal component that is made by the extrusion process to produce shapes, forms, and designs for a wide variety of applications. The major benefit of aluminum channels is their weight, which is...
The term "aluminum coil" describes aluminum that has been flattened into sheets where their width is significantly higher than their thickness and then "coiled" into a roll. Stacks of individual aluminum sheets are difficult to...
Aluminum trim is an aluminum product that is produced by extrusion to create long, narrow, pliable, and adaptive pieces of aluminum that can be used for architectural decorative applications and accents, indoor and outdoor lighting, and engineering design...
Aluminum piping and tubing is silvery-white, soft, and ductile. The metal belongs to the boron group. Aluminum is the third most abundant element present on earth. Aluminum has low density. When exposed...
Extruded aluminum is a continuous piece of aluminum that usually has a constant profile or cross-section throughout its length. It is made by forcing a block of aluminum, called a billet, through a die opening which is smaller than the original cross-sectional area of the billet...
Aluminum is the most abundant metal on the Earth’s crust, but it rarely exists as an elemental form. Aluminum and its alloys are valued because of their low density and high strength-to-weight ratio, durability, and corrosion resistance...
Aluminum extrusion, or the extrusion process, owes its beginnings to three men – Joseph Bramah, Thomas Burr, and Alexander Dick. Each of them advanced and perfected the process so that inventors from the industrial revolution could improve it...