Conveyor Belts
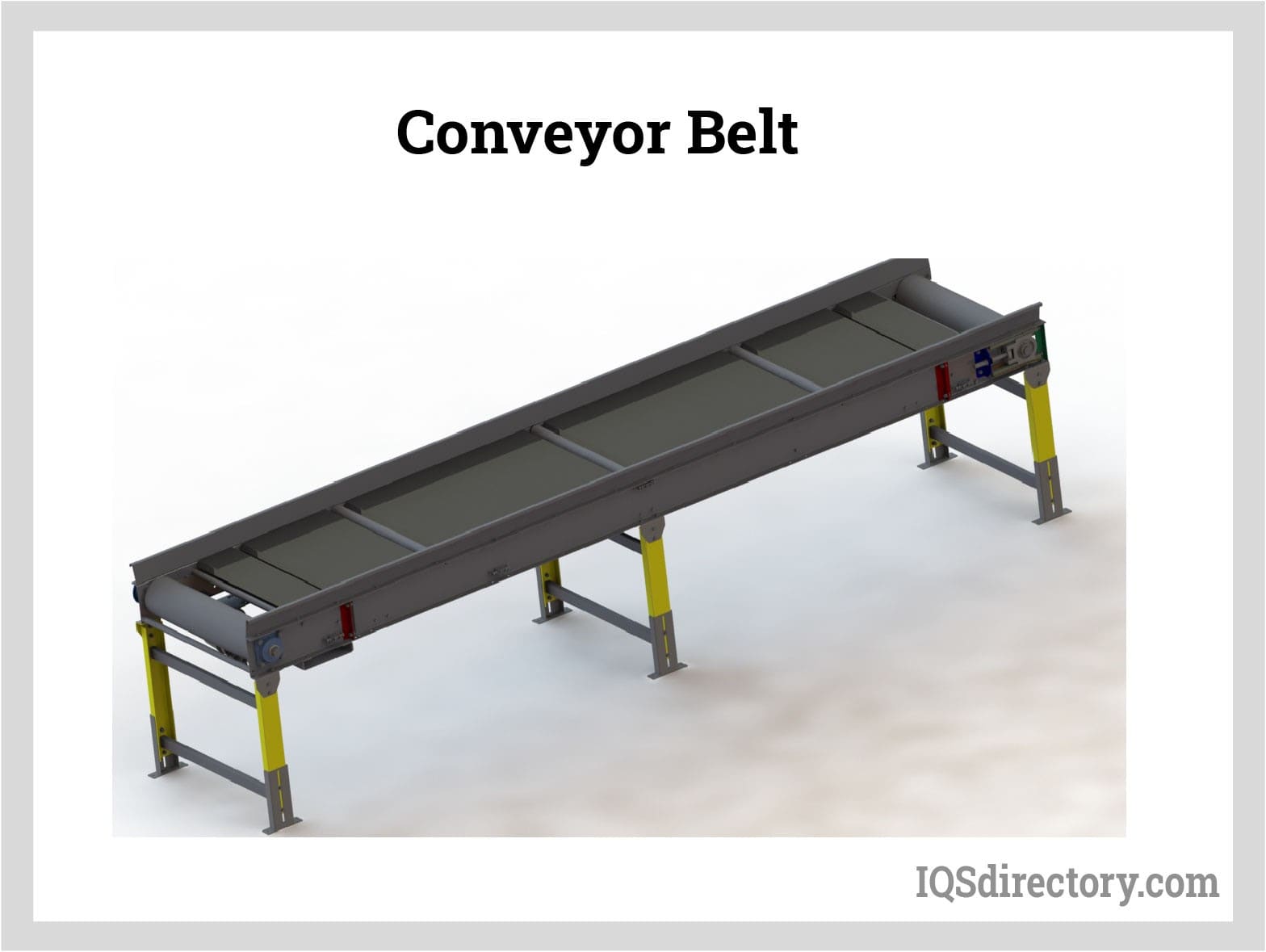
In a production facility, the transport of raw materials and finished products is a complex yet essential operation. The most efficient and time-saving approach to accomplish this task is by employing conveying equipment. This equipment can be seamlessly integrated and installed in any location, tailored to meet specific requirements as needed.
The main types of conveying systems include belt, roller, motorized roller, and overhead hanging. The key distinction between them lies in their mounting: floor-mounted on braces or brackets versus overhead hanging attached to the ceiling. These systems are designed to efficiently transport materials, parts, or finished products in a controlled sequence.
The speed of a conveying system depends on the requirements of the receiving unit. Processes vary: some demand fast movement on a timed basis, while others handling delicate or technical items can operate at slower speeds or stop as needed. Each facility sets its own operational standards accordingly.
The overhead configuration of a conveying system operates above the parts or pieces it transports. This design offers the advantage of not occupying any floor space, thereby releasing it for other uses. The decision to implement an overhead system is typically based on the available space within the facility.
The predominant form of conveying system is floor-mounted. While these systems may appear fixed to the floor, there exist flexible options that can be easily moved or adjusted to suit operational requirements. This type of conveying is commonly utilized on shipping docks or assembly lines.
Among conveying systems, the most basic type is the belt conveyor. It offers adjustable speeds tailored to process requirements. Conveyors are designed primarily for material transport rather than serving as work surfaces, directing items to different locations or storage areas.
Gravity rollers facilitate the effortless movement of heavy materials without requiring lifting or carrying. These systems can be detached from the floor and relocated as needed, enhancing operational flexibility. Their popularity stems from improved efficiency and reduced risk of worker injuries.
Chain conveying systems are well-suited for heavy or irregularly shaped pieces. Featuring multiple contact points, they securely hold items in place during transport and can handle loads such as pallets, totes, or industrial containers. Known for their robust construction, chain conveyors excel in moving heavy components like engines, automobile chassis, and other substantial parts.
Chain and roller conveying systems have been integrated in various configurations for diverse applications. One such system involves combining chains driven by motors with rollers, known as the CDLR (chain-driven live roller) system. Specifically designed for transporting heavy materials, this configuration addresses the requirements of robust material handling operations.
Overhead systems are available in various styles and power configurations. In certain industries, they are operated manually without motorization, with materials loaded and moved manually by pushing them from one point to another. Similar to roller systems, this type of conveying system eliminates the need for manual carrying of materials between locations.
Motorized overhead conveying systems feature trolleys connected via a chain drive, which can be enclosed within a track or configured as an open I-beam. These systems are specifically engineered for use in production lines and assembly operations.
The design, configuration, and selection of a conveying system require careful consideration to ensure it meets its intended purpose. Manufacturers invest time, planning, and expertise to tailor systems that align with the specific needs of their customers.
Conveyor belts are essential transportation systems for goods, bulk materials, or energy. They utilize rollers, wheels, and pulleys to drive and support continuous movement platforms. These systems range from simple designs with a belt around two rollers on a frame to highly intricate setups. Complex conveyor systems play crucial roles in manufacturing processes, managing tasks from raw material handling to container packing for shipping. They vary widely in scale, from small applications like drive belts in vacuum cleaners and sewing machines to large-scale installations capable of moving farm equipment, airplanes, and more.
Learn more about conveyor belts.
Conveyor systems encompass various material handling equipment that efficiently transport packages, products, parts, food, or equipment within a facility. They facilitate movement through different stages of manufacturing, finishing, or distribution processes, as well as between different locations. Beyond material handling, conveyor systems support applications in shipping, receiving, distribution, sintering, finishing, parts washing, packaging, and warehousing. These systems are critical in many industries, including aerospace, automotive, commercial manufacturing, retail, food processing, industrial manufacturing, military, defense, paper, and pharmaceutical sectors.
Conveyor systems cater to diverse applications, prompting manufacturers to provide various standard configurations. These include belt, chain, roller, overhead, vertical, and chute conveyor systems. While most systems are automated, some, like chute and roller systems, are not. Conveyor systems can combine different configurations to move items vertically or horizontally, and efficiently divert, lift, curve, and sort products.
Learn more about conveyor systems.
Conveyors are material handling equipment designed to move products, packages, food, or equipment within a facility or through various stages of automated manufacturing or finishing. To accommodate a wide range of items, different conveyor configurations are available. Common types include belt conveyors, chain conveyors, roller conveyors, spiral conveyors, overhead conveyors, vertical conveyors, and complex conveyor systems that combine multiple types.
Conveyors are typically motorized, though some types, such as ball transfer and chute conveyors, operate by gravity. Pneumatic conveyors, which use air power, are specialized for transporting bulk powders. Various industries, including manufacturing and packaging, rely on different types of conveyors to move parts, products, and packages through processing systems. In manufacturing, conveyors are often set up between workstations.
Learn more about conveyors.
When it comes to essential workshop tools, hose reels are often underrated. Yet, their ability to enhance workspace functionality and organization makes them indispensable. A hose reel, essentially a cylindrical device for storing hoses and similar materials, simplifies the process of winding and unwinding, preventing tangles and kinks. Available in plastic, fiberglass, or metal, and in various sizes, hose reels accommodate everything from garden hoses to industrial fire hoses. Additionally, they can store large amounts of rope or cable and even provide an electric connection.
Learn more about hose reels.
Lubricants, or lubes, are substances that reduce friction and heat between surfaces, facilitating particle transport and temperature regulation. They also serve as conductive agents, enhancing current flow. Essential for the maintenance and proper function of machines with moving parts, lubricants are used across various industries, including automotive, aerospace, marine, metal fabrication, and food and beverage.
Learn more about lubrication systems.
Lubricants, or lubes, are substances used to reduce friction and heat between surfaces. They facilitate particle transport, regulate temperature, and can enhance electrical conductivity. Essential for the proper function and maintenance of machinery with moving parts, lubricants are widely used in industries such as automotive, aerospace, marine, metal fabrication, and food and beverage.
Learn more about lubricants.
Screw conveyor systems, also known as auger, helix, worm, or flexible screw conveyors, are mechanisms designed to transport fluid, solid, and granulated materials between processes.
Learn more about screw conveyors.
A pneumatic conveying system transfers bulk materials using gas flow, typically air, as the conveying medium. Efficiently designed systems are practical and economical for moving materials to single or multiple destinations. Primarily used for dry bulk and powder materials, these systems utilize pressure differentials and gas flow, such as nitrogen, within enclosed pipelines. Key components include a feeder, air mover, dust collection system, termination vessel, and belt conveyor. Suitable materials include cement, flour, sand, minerals, and food products, provided they are dry. Materials in paste or slurry form are unsuitable.
Learn more about pneumatic conveyors.