Belt Conveyors
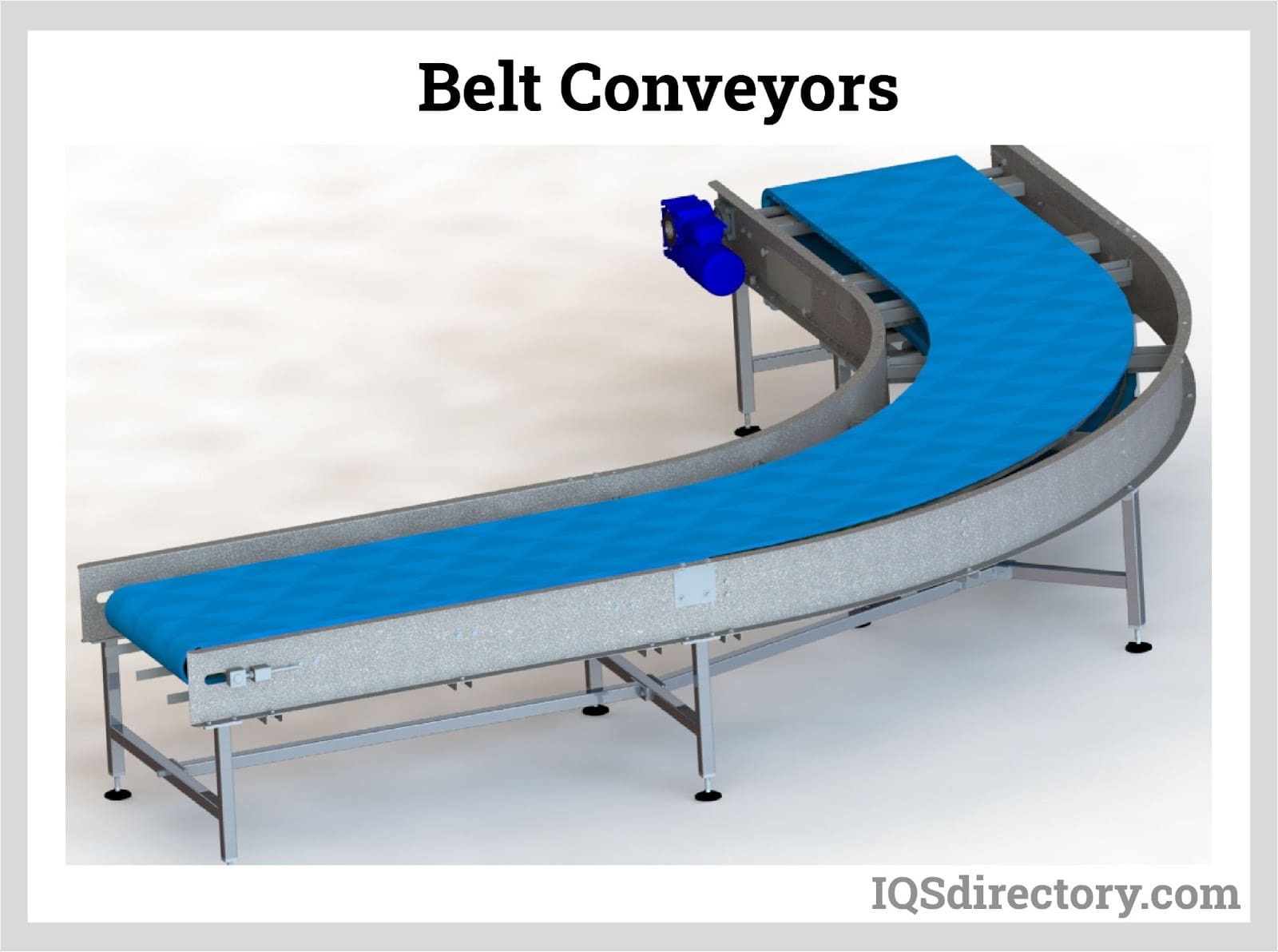
In industrial and manufacturing settings, the supply chain plays a pivotal role by managing the flow of raw materials and products to customers. This intricate network handles every machine, tool, part, and component, ensuring seamless production and distribution. Material handling, at the core of this chain, involves a specialized network of professionals and equipment dedicated to precise part placement and meticulous inventory control.
Essential to material handling are the tools and machinery used to transport goods efficiently within production or to consumers. The careful selection of this equipment is crucial for optimizing supply chain operations and material handling efficiency. The right equipment choices impact various facets of company operations, influencing production factors and profit margins alike.
Material handling equipment is categorized based on its specific roles within the supply chain. These functions encompass transportation, positioning, load formation, and retrieval. In today's advanced material handling technology, sophisticated software systems are integrated as essential tools alongside engineered hardware solutions.
In material handling, the transportation category encompasses a diverse array of tools and equipment designed to efficiently move goods, supplies, and materials. This group includes hoists, cranes, and conveyors used for transporting materials within a facility between processing stations, production areas, and packing or assembly points. Complementing these are forklifts, dollies, hand trucks, and pallet jacks, which facilitate more direct handling of materials.
The efficiency of assembly and manufacturing processes hinges significantly on the speed at which raw materials are delivered to processing points. The choice of method depends on the specific product and its destination within the production line. Modern manufacturing leverages advanced technologies such as automated robotics and specialized feeders designed to precisely position components for seamless integration into the final product.
When people think of material handling, they often picture the shipping and receiving department where materials are received and prepared for shipment. This facet of material handling is integral, utilizing a range of tools, equipment, and machinery to streamline and optimize various aspects of the process.
Key to shipping and handling operations are tools like side-loaders, pallet trucks, walkie stackers, order pickers, and locators, along with platform trucks such as dollies and hand trucks. Movable roller conveyors, which can be flexibly positioned, play a crucial role in loading and unloading trucks efficiently.
A specialized aspect of material handling focuses on the efficient management of bulk materials. This involves using equipment specifically designed to handle various substances such as chips, cereals, gravel, sand, and other granular or powdered materials. Each type of equipment, including stackers, hoppers, grain and bucket elevators, belt and screw conveyors, and rotary car dumpers, is meticulously engineered to optimize the handling process for specific materials. These tools are critical in industrial and agricultural operations, ensuring precise and reliable handling of bulk materials to enhance productivity and operational efficiency.
Every manufacturing, industrial, and commercial enterprise relies on efficient methods for storing raw materials while maintaining precise inventory oversight. At the core of these operations is warehousing, a crucial component meticulously managed as part of the company's assets.
Warehousing entails a structured approach to material placement and retrieval. Materials are methodically organized in bins, shelves, and cabinets, each item labeled and categorized with precision. Among the diverse functions of material handling, warehousing demands careful planning and preparation, utilizing specialized tools tailored to accommodate the specific nature of stored items.
Smooth and efficient retrieval of stored goods—facilitated by forklifts, pallet jacks, dollies, or hand carts—is ensured when all operational elements are effectively coordinated. Modern warehousing practices integrate sophisticated computer software for streamlined inventory tracking and allocation to support distribution efforts.
Material handling, often perceived simply as the process of collecting, storing, and retrieving goods, is, in reality, a complex and meticulously orchestrated automated system. This system relies on specialized equipment to guarantee flawless movement and management of a company's assets throughout its operational lifecycle.
Bulk material equipment and systems are designed with specific tasks in mind, each unit tailored to fulfill its intended function. Despite these variations, most systems share common components and features. A complete system typically includes:
An unloading station. The system requires an entry point where materials can be introduced into the system. This component can vary widely, from railcar unloading stations to straightforward bag dumping stations.
A conveying system. In bulk material handling systems, conveying typically involves pneumatic conveyors as the primary method, though others utilize screw conveyors, bucket elevators, or drag chain conveyors. Many systems employ a combination of two or more of these conveyor types for efficient material transport.
Material Storage Equipment. Storage equipment for materials ranges from large silos to smaller bins or hoppers, essential components in any bulk material handling system, ensuring materials are stored until required for processing.
Batching Equipment. Batching equipment is indispensable for optimizing the efficient use of bulk materials by precisely dispensing them for both processing and packaging purposes. This specialized equipment ensures accuracy in measuring and transferring materials, essential for maintaining quality and consistency throughout production cycles.
A filling or packaging station. After processing bulk materials, the system requires a reliable method to unload the final product for packaging, shipment, or sale. This station serves as a crucial endpoint where products are prepared and organized for distribution, ensuring they meet quality standards and are ready for market delivery.
In virtually all bulk material systems, these core types of equipment are essential, although each system may incorporate slight variations and additional components to suit specific application requirements. For instance, in a food processing facility, a bulk material handling system would typically utilize large storage silos instead of smaller bins, given their frequent handling of substantial quantities of grains, powders, and other materials.
In addition to the equipment mentioned earlier, such facilities typically incorporate mixing equipment to ensure thorough ingredient blending. Furthermore, some systems are specialized for transporting and handling materials composed of fine particles, while others excel with larger granules. These systems are highly customizable to meet the precise demands of different tasks or processes.
Several critical considerations arise during the installation of bulk material equipment or systems. Not all equipment is universally compatible with every type of material, and the consistency of the material significantly impacts the quality of the end product. Key factors to consider when selecting equipment include:
Experts advise thorough material testing before purchasing equipment to understand its processing capabilities. For instance, particle densities can vary across different stages of material handling, making it risky to assume uniform efficiency across equipment. Pneumatic conveyors, crucial in bulk material systems, highlight the need to choose the right type for transporting specific solids effectively. For example, abrasive materials require different handling than sticky ones. Some materials perform better with dense phase conveying, while others suit dilute phase methods. These considerations, pivotal for conveying systems, also influence other components like batching equipment, mixers, and feeders, impacted by particle size and cohesion affecting material dispensation. Thus, understanding material properties ensures optimal equipment selection and efficient processing.
Granulated and dry bulk materials such as grain, powdered chemicals, sugar, flour, and dry cereal demand specialized conveying, mixing, and processing systems. These systems are tailored for industrial applications that involve handling delicate, friable, sticky, or free-flowing solids, ensuring integrated mixing, conveying, measuring, and packaging capabilities.
Unlike discrete parts and products conveyed via belt and chain conveyors during fabrication, assembly, and packaging, bulk solids and powdered materials require systems like closed screw conveyors, flexible screw conveyors, or pneumatic conveyors. These systems prevent issues such as caking, packing, liquefying, contamination, and agglomeration, crucial for maintaining material integrity.
Industrial mixers, dryers, pulverizers, and vibratory feeders are seamlessly integrated into these bulk material handling systems to ensure comprehensive processing from raw material intake to final product packaging.
Belt conveyors belong to a class of conveyor systems designed to transport various materials from one point to another and across different stages of processing. Conveyor systems employ diverse methods to facilitate this movement, including floor chain conveyors, overhead chain conveyors, and more. Among these, belt conveyors stand out as the most prevalent type.
Belt conveyors utilize a wide polymer or rubber belt that loops around two or more uni-directional pulleys, which rotate to propel goods and parts of varying shapes and sizes along the conveyor. They find extensive use across multiple industries such as industrial manufacturing, retail manufacturing, pharmaceuticals, food and beverage processing, defense, paper, aerospace, and automotive sectors.
Learn more about belt conveyors.
Bulk bag equipment is essential in handling and transporting bulk bags, which are sturdy fabric containers designed for storing and transporting dry, flowable materials like plastic granules, grain, fertilizer, and sand.
This equipment plays a crucial role in various applications, including pneumatic conveying projects. It is widely utilized across diverse facilities such as greenhouses, agricultural operations, food distribution centers, pharmaceutical plants, manufacturing facilities, and beyond. Explore further insights into bulk bag equipment.
Industrial dryers encompass a broad category of equipment designed for manufacturing, industrial, or large-scale commercial drying purposes.
While they are indeed used in laundromats and hotels for drying clothes and linens, their applications extend far beyond. Industrial dryers are indispensable across diverse industries such as agriculture, food processing, manufacturing, pharmaceuticals, pollution control, water treatment, and paper and pulp. These industries rely on industrial dryers to remove moisture from materials ranging from fertilizers, grains, and chemicals to dairy products, minerals, papers, and plastics.
Industrial dryers operate through three primary methods: air drying, infrared drying, and spray drying. Air drying, the most common method, involves exposing materials to hot air to facilitate evaporation of moisture. Infrared dryers use electromagnetic radiation within a specific wavelength to dry solid materials. Spray dryers utilize jets of hot steam to rapidly evaporate moisture, known as flash drying.
Constructed predominantly from stainless steel, industrial dryers come in various models tailored to specific needs. They are generally larger than household dryers and are typically not used for drying laundry outside of commercial settings like laundromats and hotels.
For further information, contact an industrial dryer manufacturers to explore the range of options available to meet specific drying requirements.
The term "industrial dryers" encompasses a wide range of drying equipment, regardless of their specific drying method—whether air, infrared, or spray drying. Due to this diversity, industrial dryers vary greatly in design and configuration. While there is no universal model, many share common traits such as being constructed from robust, sanitary stainless steel, prized for its strength and corrosion resistance.
These dryers can take the form of cylindrical tanks or rectangular boxes, equipped with multiple intake and output valves, connections, openings, gauges, and controls. Some operate continuously, utilizing conveyor belts to process a steady stream of materials, while others work in batches. Their capacity varies widely depending on the type of dryer and the material being dried—ranging from units capable of drying over 25,000 pounds per hour to smaller models designed to handle just one cubic foot at a time.
Industrial dryers play indispensable roles across pharmaceutical, food processing, manufacturing, agricultural, pollution control, water treatment, and paper industries. They serve multiple functions in handling chemicals, dairy products, fertilizers, grains, minerals, paper, plastics, refuse, and more. Each dryer is tailored to meet specific industry needs, ensuring efficient moisture removal and product preservation.
Mixers and blenders are pivotal industrial equipment designed for precision mixing and blending operations across sectors such as agriculture, food processing, mining, and pharmaceuticals. These machines are integral in the production of diverse products including cosmetics, baking ingredients, fertilizers, and pet foods.
Ensuring consistent quality is paramount in these industries, necessitating mixers and blenders equipped with precise speed controls, carefully regulated internal temperatures, and meticulously engineered mixing components. They are adept at handling both wet and dry materials, with specialized configurations for each, requiring robust power for efficient blending of heavier, wet substances at high speeds.
Maintaining hygienic standards is facilitated through effective dust seals, safeguarding facility environments from contaminants. The machines' modular design allows for easy component removal and cleaning, enhancing operational efficiency. Additionally, their adaptability is showcased through the availability of various attachments tailored to specific material batches.
Key types of mixers and blenders include auger mixers, high-capacity mixers, and ribbon blenders, each fulfilling distinct operational requirements in industrial settings.
In bulk material handling systems, one of the most ubiquitous mixers is the auger mixer. Standing tall within facilities on robust metal frames, these powerful machines swiftly blend bulk materials into a seamless consistency. An external electric motor drives the auger, spinning it rapidly through the material. Depending on the desired blend, the auger attachment can vary in length; longer augers ensure even distribution throughout the tank, while shorter ones concentrate finer contents at the bottom. Some auger attachments match the tank's diameter closely, facilitating thorough mixing. Materials enter through an overhead opening and exit via a pneumatic conveyor or a bottom discharge door after blending. Typically crafted from stainless steel, these mixers are designed for easy cleaning between uses to prevent contamination and material buildup, enhancing equipment longevity and ensuring product integrity. The auger head can be detached for external cleaning or to accommodate different attachments.
The design of the auger features sharp blades that efficiently move material up the center and down the tank walls, ensuring thorough mixing. This continuous cycling motion is key to the auger mixer's effectiveness. In smaller models, the auger operates horizontally. Operators access the mixer through a top-opening access door to load bulk materials, after which the door is closed for mixing to commence once the machine is activated. Horizontal auger mixers typically incorporate transparent fiberglass doors, allowing operators to monitor material consistency changes during operation.
Large-scale bulk material handling systems are designed to manage substantial quantities of material daily, requiring mixers that match their batch sizes. These systems, though costly, operate most efficiently when processing high volumes continuously. Industrial facilities utilize one or more high-capacity mixers for this purpose. These mixers typically feature a large central auger that stirs materials, akin to standard auger mixers but on a much larger scale. Resembling storage silos, these mixers include a top hatch for material input and a bottom door for discharge into bulk bags or bins post-mixing. Optionally, a pneumatic conveying system can be installed on the top or side to extract materials once mixing is complete. Industrial-grade high-capacity mixers often exceed 1000 cubic feet in volume, ensuring they can handle large material volumes while maintaining precise mixture consistency.
Powerful variable speed motors drive the mixing mechanism, effortlessly blending heavy materials to ensure uniformity. Precise control over the mixer's speed allows operators to achieve consistent texture in every batch. Sensors and instruments integrated into the mixer relay crucial data to the control unit, displaying vital statistics to facility operators. This information aids in optimizing efficiency and maximizing batch output, while also facilitating prompt identification and resolution of performance issues. High-capacity mixers find essential use across industries requiring high-volume production, such as cosmetics, food processing, pharmaceuticals, and more. For instance, in cosmetic production, efficient handling of bulk materials is crucial to maintaining cost-effectiveness throughout the manufacturing process.
A ribbon blender serves as a high-speed mixing solution for bulk material handling facilities. Similar to an auger mixer but typically smaller in size, it features a ribbon or auger designed in a helical pattern for thorough and homogeneous mixing. Once the batch is complete, the blender efficiently discharges the mixture. Available in vertical and horizontal configurations, the choice of blender type and size depends on the specific materials processed and space constraints of the facility. The ribbon, housed in a U-shaped trough, gently pulls and lifts materials, creating a uniform blend as they cascade back together into a central pile. After blending, materials are discharged through a bottom door, operated manually or automatically. During discharge, the blender remains operational, guiding materials towards the center opening where they drop into a collection bin below. Post-operation, the blender can be safely cleaned by accessing its components through an accessible door.
Like most equipment used in bulk material handling, ribbon blenders are commonly fabricated from stainless steel. This material not only offers exceptional strength and corrosion resistance but also facilitates easy cleaning—a critical factor in facilities concerned with preventing ingredient cross-contamination between batches. Ribbon blenders find extensive application across various industries, including food processing, pharmaceuticals, and cosmetics, due to their ability to achieve uniform blending and consistent mixing quality. Available in a range of sizes, these blenders cater to the needs of both small and large-scale plants, enabling efficient blending solutions in any available space.
Palletizers are machines designed for handling pallets during loading, unloading, and storage processes. They facilitate the efficient consolidation of numerous smaller units into larger, easier-to-handle pallet loads, commonly used for mass shipping and distribution purposes.
Many manufacturing and distribution plants utilize automated palletizers and robotic systems for efficient pallet loading and unloading. Automated conveyor palletizers are categorized as either low-level, loading from ground level, or high-level, operating on elevated platforms. These palletizing systems can handle various types of products, including bags, cases, drums, and bottles, depending on specific machine configurations. Large-scale facilities often employ depalletizers for unloading packaged units, while accessories like pallet dispensers and load transfer stations aid in managing pallets and loads effectively. Some professionals interchangeably use terms like "palletizers" and "case pickers"; however, "case picking" typically refers to individual product retrieval in distribution operations.
A pneumatic conveying system transports bulk materials from one location to another using gas flow, commonly air, as the conveying medium. The system's design aims for efficiency, practicality, and cost-effectiveness in moving materials to single or multiple destinations.
Pneumatic conveying equipment plays a pivotal role in transferring dry bulk and powder materials through a fully enclosed pipeline. This movement relies on a combination of pressure differentials and the flow of gases like nitrogen. Key components of the system include a feeder, an air mover, a dust collection system, a termination vessel, and a belt conveyor.
It's important to note that the system transports materials such as cement, flour, sand, minerals, and various food products. It's essential that these materials are in granular form and dry. Substances in paste or slurry form are unsuitable and can lead to complications in the system. Explore further insights into pneumatic conveyors.
Screw conveyor systems are essential mechanisms designed to efficiently rotate and transport a wide range of fluids, solids, and granular materials between different stages of a process. In essence, they facilitate the seamless transfer of materials.
These systems are alternatively referred to as auger conveyors, helix conveyors, worm conveyors, or flexible screw conveyors.
Vibratory feeders, also called vibratory conveyors or bowl feeders, are crucial for handling bulk materials, and facilitating their conveyance and sorting. They consist of a vibrating unit, a bowl, and a control box for adjusting vibrations, often integrated with a conveyor track. These feeders excel in gently handling sticky or delicate materials, ensuring damage-free conveyance through controlled vibrations.
Powered by a unit beneath the bowl, vibratory feeders move and sort materials. While their design is straightforward, features can vary between models. Some include troughs for sifting materials, while others use vibrating or trommel screens for sorting bulk products simultaneously.
Vibratory feeders are categorized into two types: bowl feeders, which align parts before packaging to ensure correct discharge, and conveyors, designed to transport materials efficiently from one point to another. Explore the versatility and applications of vibratory feeders in material handling.
Weighing systems and scales play a crucial role in various industries that handle bulk materials, such as agriculture, food processing, pharmaceuticals, mining, and oil and gas. These systems are indispensable as they ensure accurate weighing and packaging of products.
These systems vary widely in size and configuration. Some are compact, capable of measuring items with precision down to the gram, while others are robust enough to weigh entire loaded pallets or trailers. They employ diverse mechanisms like load cells, springs, balances, or hydraulics to determine weights, often displayed digitally or analogously.
There are several common types of scales used in various industries: platform scales, hanging scales, and bench scales. Platform scales, or floor scales, are flush with the ground and typically feature a large platform for weighing large bulk loads. Hanging scales suspend loads in mid-air and measure weight based on gravitational force. Bench scales are ideal for weighing small to medium-sized loads, standing a few inches to feet above the ground for easier handling and transportability.
Load cells are devices used in bulk material handling systems to measure the weight and force of large quantities of materials. They help test mechanical systems and monitor their performance during production. Load cells are crucial for ensuring the accuracy of industrial scales used to weigh bulk products. They typically measure compression and tension forces. Most load cells contain an internal strain gauge, a device that uses electrical signals to measure strain on an object. Similarly, force gauges measure push-pull forces or flow in various applications.
Pressure sensors are used to measure the flow of liquids or thick bulk materials. This helps determine how fast and with what force these materials move through a system, aiming to improve efficiency. Digital load cells are widely used to collect data from these sensors during operations. In food processing, load cells are crucial for accurately measuring ingredients before they are mixed, ensuring consistent product quality. One of the key roles of load cells is to precisely weigh loads such as loaded pallets. This accuracy is essential for logistics and billing when shipping bulk goods. Load cells provide highly precise readings, typically within 0.25%, which is critical in industries where a single load can weigh several tons.
So how does a load cell actually work? A load cell converts mechanical force into electrical signals. These signals are then transmitted to a data collection system within the device. The system processes this information to produce an output or reading, which operators can view when items are placed on scales or materials flow through tubes. While analog load cells still exist, digital ones have largely replaced them due to their superior accuracy and ease of use. In some applications, load cells are used to trigger alarms when specific conditions are met, such as shutting down equipment in case of an emergency. Load cells can be equipped with multiple gauges to enhance sensitivity and accuracy. Factors like required precision, type of force being measured, and response time are crucial considerations when designing a load cell for a specific application.
Load cells are essential components in equipment used across various industries like mining, food processing, pharmaceuticals, oil & gas, agriculture, and more. Despite their small size, load cells significantly enhance the efficiency and cost-effectiveness of large-scale operations. Some manufacturers focus on specialized load cells tailored to specific materials or applications through collaboration with industry experts. Others produce more versatile load cells suitable for a wide range of bulk handling tasks.
Bulk material handlers across industries rely on scales to weigh their products accurately, crucial for packaging, shipping, and storage. Since many bulk products are sold by weight, precise measurements are essential. Scales vary in size and type: from small scales for tiny objects to larger ones capable of weighing loaded pallets or even entire trailers. Common types include bench scales, raised off the ground for easier loading, platform scales level with the floor for large bulk loads, and hanging scales that suspend loads to measure gravitational force. Scales come in two main types: digital and analog. Analog scales display weight using a meter and needle, which can be accurate but are less precise and easy to read compared to digital scales. Digital scales provide decimal readings, ensuring high precision when weighing bulk products.
When choosing an industrial scale for bulk operations, the most critical factor is its maximum weight capacity, which can range from a few grams to over 80,000 pounds. Selecting a scale that meets your application's needs prevents technical errors and ensures accuracy. In bulk weighing scenarios, products are typically on pallets or in containers. The weight of the container or pallet can be entered into the scale to isolate the weight of the bulk material. This ensures distributors are billed accurately based only on the bulk material's weight, not the container. Scales employ various mechanisms such as hydraulics, balances, springs, or load cells to determine weight. Complex scales may combine these technologies to achieve accurate measurements.
In many industries, scales must comply with regulatory standards set by the National Institute of Standards and Technology (NIST). These standards ensure both worker safety and the accuracy of bulk goods measurements. In bulk material handling systems, scales are positioned alongside other equipment and can be loaded manually by workers or intermittently by automated machines. Automated systems rely on scale feedback to determine when a load meets the required weight. Industries such as agriculture, food processing, and pharmaceuticals rely heavily on industrial scales to weigh products before packaging or shipping. In some cases, scales are used to weigh small quantities added to larger mixtures in processing plants, where precision is critical for maintaining consistency and quality across bulk products.
Weighing and batching equipment are crucial components of bulk material handling systems, ensuring precise quantities for packaging or shipping. Weigh batching systems accurately fill containers such as bags, drums, or bottles with consistent amounts of material. They can also ensure the correct proportions of materials are added to mixing batches. These systems offer accuracy and repeatability, essential in bulk material handling. They operate on two principles: gain-in-weight and loss-in-weight. Gain-in-weight systems measure the material added to achieve the desired weight, while loss-in-weight systems measure the material removed to maintain a constant weight. Various types of weight batching systems are employed across industries to meet specific operational needs in bulk material handling.
In a gain-in-weight batching system, a volumetric feeder feeds material into a weighing hopper. The hopper continuously measures the weight as material is added, and feeders release material until the hopper reaches a predetermined weight, triggering a stop mechanism. Many applications involve adding multiple materials to the batch. Each material is added individually to the weigh hopper. When the desired weight for one ingredient is reached, its feeder stops, and the next ingredient's feeder starts until its target weight is achieved. This process repeats until all ingredients are added. Consequently, the hopper accumulates layers corresponding to each ingredient added separately. Automated controls in this system precisely manage material release, preparing bulk materials for subsequent process stages.
In a loss-in-weight batching system, multiple ingredients are fed into a collection hopper using feeders equipped with precise weighing sensors, like load cells. These sensors monitor the weight of material within each feeder as it releases into the hopper. This method ensures accurate measurement, particularly beneficial in applications where exact weight control is critical, especially with smaller amounts.
Moreover, by introducing all materials simultaneously into the hopper, rather than sequentially, batch mixing times are significantly reduced. This approach promotes faster blending of ingredients to achieve a homogeneous mixture efficiently.
There is a diverse range of machinery available within weight batching systems, catering to different sizes and adaptable to the available floor space in commercial or industrial facilities. Recent advancements in industrial technology, such as improved digital controls and sensors, have significantly enhanced the precision of bulk material weight batching systems. Modern systems can now offer comprehensive control and display units installed onsite, allowing operators to monitor efficiency and output effectively. This technology enables adjustments to be made instantly with the touch of a button, particularly advantageous for suppliers handling high volumes of materials across various industries daily.