Data Acquisition Systems
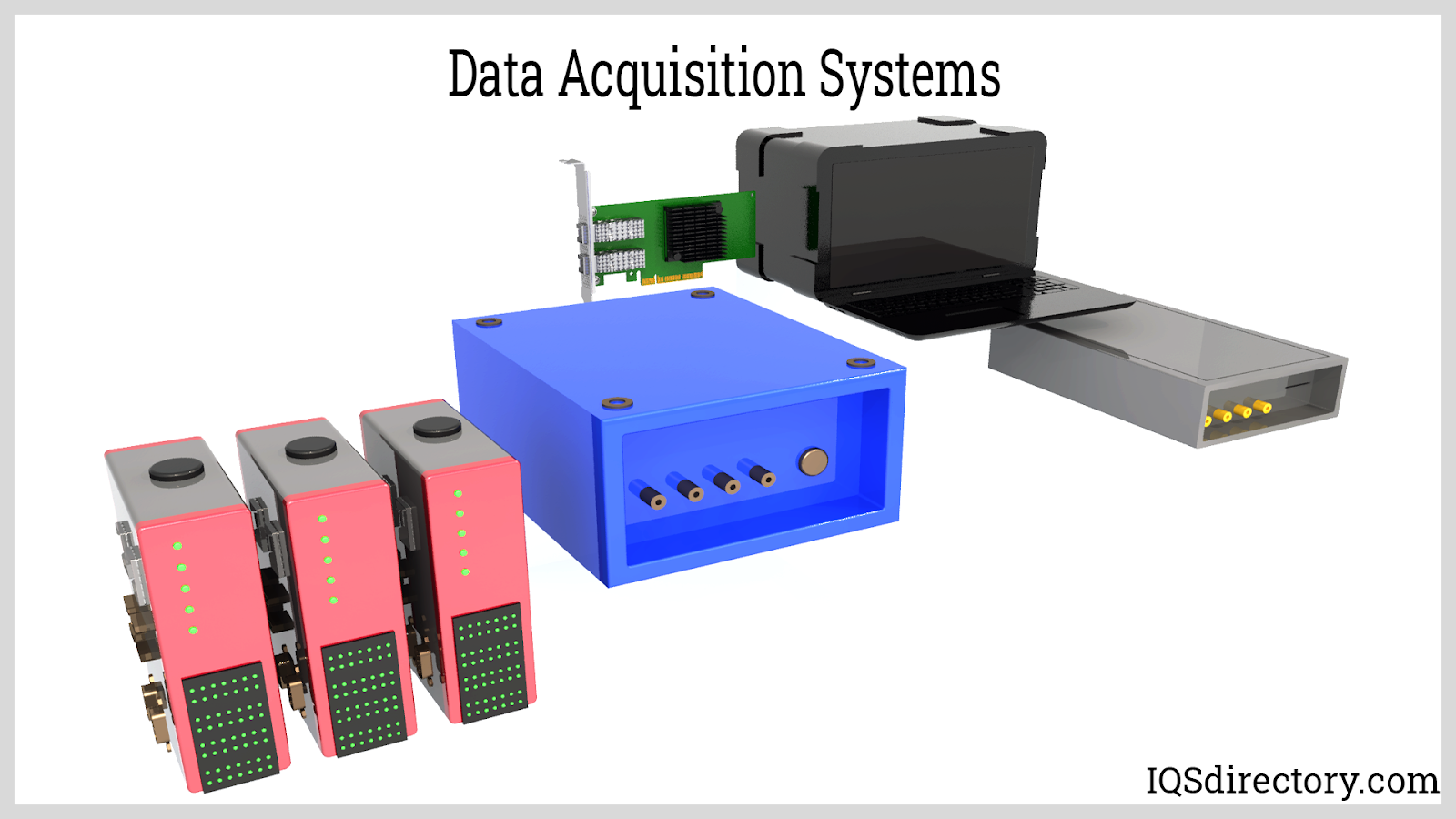
A data acquisition system is a system that comprises sensors, measurement devices, and a computer. A data acquisition system is used for processing acquired data, which involves collecting the information...
Please fill out the following form to submit a Request for Quote to any of the following companies listed on
This article contains everything you need to know about Platform Industrial Scales.
Read further and learn more about:
A platform scale is a weighing device that consists of one or two metal plates that hold items to be weighed and can have a smooth or diamond surface. They are heavy duty simple tools that are very sturdy with a high capacity and come in a wide range of sizes, capacities, styles, and models in order to meet the needs of a variety of industries.
The low profile of platform scales makes it possible to weigh pallets, animals, large loads, or individual crates and boxes. The material to be weighed is placed on the scale.
The function of the platform is to transmit the weight of the object to the internal measuring device and to support the object during weighing. Several types of devices can be installed within the platform scale to aid in the calculation of weight. There is a wide range of platform scale designs, sizes, and load capacities available depending on the needs of the customer or the user.
Platform scales are practically used everywhere. They are widely used in trading, manufacturing, logistics, and service industries to measure or verify the weight of material. In those number-driven industries, having the correct weight measurement matters when it comes to generating revenues, maintaining safety, and upholding the quality of services and products. The application of platform scales is not limited to commercial and industrial purposes; these scales are also capable of making small-scale weight measurements for personal, domestic, medical, and laboratory applications.
The operation of platform scales is straightforward for the user. The object to be weighed is placed on the platform, and the rest of the work is performed by the platform scale. The object applies compressive force to the platform; this force is transmitted to the mechanism inside the platform scale that is responsible for converting it into a weight measurement the user can read and record. The process ends by displaying the reading on the screen or indicator of the platform scale.
The two main classifications of platform scales are electronic and mechanical platform scales. They differ on the mechanism used for determining the weight of an object. The latter is a type of platform scale that relies on levers, springs, and reference weights in obtaining the weight measurement.
Load cells are transducers that convert tensile and compressive forces into measurable electronic output using a spring with a strain gauge attached. They work by changing mechanical force into digital values. The types of load cells used on platform scales vary according to the size of the items to be weighed and type of scale.
Strain gauge load cells are the most common and widely used. They are a type of device that measures the amount of strain, or change in dimensions, applied to a material. Strain gauges convert tension, force, and pressure into electrical signals that can be digitally displayed.
In the manufacture and design of load cells, strain gauges are an essential component that picks up the amount of force or strain placed on the structure of a load cell and converts it to electrical signals. The amount of strain experienced by a load is transferred directly to a strain gauge or strain gauges, which responds with linear change in electrical resistance.
In load cells, strain gauge assemblies are inside the load cell housing and act as an electronic sensor. They contain a metal foil insulated by a flexible substrate that changes its resistance in response to an applied external force. Voltage fluctuations cause a deformation of the metal foil as electrical current passes through its leads. The change in voltage is converted by a digital meter into measurable weight readings.
The types of strain gauge load cells commonly used in platform scales include single point, planar beam, bending beam, shear beam, dual shear beam, and S-type load cells.
A shear beam load cell has a piece of metal that elastically deforms under the force of a load. The strain is picked up by a strain gauge in the metal and changed to an electrical signal.. Shear beam load cells are used for medium loads of less than five tons.
Single point load cells have an aperture that is the cut out of the body of the load cell. The aperture controls the thickness of the metal across the load cell body. When a load is applied, the shape of the load cell deforms, which is detected by strain gauges as the body of the load cell is distorted. The deformation creates a voltage signal that is proportional to the force of the weight.
Magnetic force restoration scales are advanced types of electromechanical balances that use electrodynamic converters with permanent magnets to change the force applied to the platform of a scale into proportional electric current. They are the most expensive type of scale and have excellent stability and repeatability.
Unlike strain gauge scales that measure the force of a load, MFR scales create a counteracting force that works against the weight of the load. Force is measured when the weighing platform is in balance, which allows for more precise measurements.
The platform with the material to be weighed is attached to a force coil that is floating in a magnetic field created by an amplifier, which produces the right current to maintain balance. The necessary current, that flows through a resistor, produces the measurable voltage required to keep the platform in balance and is the measure of the weight of the material.
The measurement from the scale is produced by an A/D unit that changes the voltage readings into a digital signal that is sent to a microprocessor with the right software to show the weight on a display. The accuracy of the readings are ensured by a displacement detector and temperature sensor that control the amplifier.
The weighing of oversized bulky materials requires the use of a very durable and resilient scale capable of withstanding the constant demands of heavy duty weighing. Of the many types of available weighing solutions, platform scales are used the most due to their ability to simplify and streamline the industrial weighing process.
Regardless of their simple operation, platform scales have technical aspects that make them capable of producing exceptionally accurate weight readings. They are very versatile and have scale indicators that are connected to their platform.
All platform scales have certain basic components, which include load cells and strain gauges, a platter or deck, platform base, and indicators. At the heart of all platform scales are load cells that endure the force of the material to be weighed and provide the readings. The platter or deck sets on top of the load cells and provides a base upon which the load can be placed. The indicator or terminal displays the readings that are sent from the load cells.
Floor scales are designed to weigh heavy oversized cumbersome loads that cannot be placed on a typical scale. A floor scale system has a deck, weight indicator, and four shear beam load cells. A junction box inside the scale platform has a summing box that adjusts each load cell such that they all weigh the same.
The various types of floor platform scales are designed to sit on the floor and to be used in factories, warehouses, and shipping departments. They are constructed to carry heavier loads in harsh and hazardous conditions. There are several kinds of floor scales, each of which has different capabilities and features.
A basic floor scale is the simplest type of floor scale. Items are placed on top of its rectangular platform, which simply sits on the floor. The top of the platform is inclined from the floor. The items are placed on the top of the floor scale either manually or by moving equipment, such as pallet jacks, forklifts, pushcarts, or hand truck, There are two options in facilitating the mounting of items onto a basic floor scale:
Ramps may be installed on the edges of the floor scale to effectively load and unload the items to be weighed. However, the ramp takes up additional floor space, especially if multiple edges must be accessed. It can also be risky for the worker to push a heavy load onto the floor scale.
Placing the floor scale in a pit frame is another option for basic floor scales to eliminate the hazard to the worker and minimize floor space. Pit frames may be installed slightly below the floor to level the platform of the floor scale with the surface of the floor. However, the installation creates additional costs.
A low profile floor scale is a type of floor scale that is similar to the basic floor scale, but its platform is much closer to the ground. The inclination of the platform top ranges from 1 – 2 inches above the ground. This makes manual loading and unloading easier for the worker, and it becomes more accessible to the moving equipment. A hinged ramp may be installed on the edge of the scale to facilitate the loading and unloading of items.
Low profile floor scales may have raised side rails with load cells underneath them to accurately weigh large items. However, this design can be an issue for oddly-shaped items.
Washdown scales (or lift scales) are a type of floor scale that has a liftable top deck to allow access to its interior components for thorough cleaning and maintenance. The top deck may be lifted manually or automatically by using a pneumatic or hydraulic system. The electronic components are protected during washing and exposure from the harsh substances during their operation.
Washdown scales are used for weighing liquids and corrosive chemicals and for applications that require high levels of sanitation such as food, beverage, agricultural, and pharmaceutical products. Those applications require frequent cleaning to keep the scale in top condition and to avoid chemical and microbial contamination. Washdown scales are made from materials that have high chemical and corrosion resistance, such as stainless steel, to withstand these applications.
Portable floor scales have increased mobility when compared to other floor scale types. Having a portable floor scale is oftentimes more economical than setting up multiple floor scales in the vicinity where it is installed.
To gain from their mobility advantage, most portable floor scales are battery-powered with a rechargeable feature to readily operate them at multiple locations without depending on a stationary electrical outlet. They have durable caster or rubber wheels at the bottom of their platform to move the portable floor scale by sliding. These features allow you to weigh objects anywhere in an industrial setting. A ramp may also be installed for added convenience.
Flexure lever scales have a S beam load cell that is able to withstand shock loading. They are a type of floor scale that is used in weighing conditions where there is the potential of heavy, sudden impact that creates stress on a scale.
Truck scales are used for weighing vehicles and their carried load for the tracking of overloaded vehicles on highways and bridges and for monitoring incoming and outgoing volumes in various facilities.
The various types of truck scales are similar to large floor scales with a very high load capacity. They are situated in highway checkpoints and inspection stations. Since truck scales measure large volumes, they require more load cells. A typical truck scale has 6 to 12 load cells.
Platform scale manufacturers offer accessories that can enhance the performance of their products and meet the specific needs of their customers. The types, kinds, and sizes of the types of materials that need to be weighed can vary widely, which may necessitate the need for additional features to avoid the need to purchase another scale.
Pit riser stands are frames used to anchor a floor scale to its existing pit that is deeper than the standard depth of the scale. They are installed under the scale using anchor bolts and increase the height of the floor scale system.
Portability frames are used to convert fixed floor scales into portable ones. There are a wide variety of options for transforming fixed floor scale systems into portable ones including castor and forklift designs.
The option of access ramps increases the use of a floor scale and adapts it for use for weighing loads on pallets or boxes placed by a dolly. They provide a more maneuverable approach for loading and unloading materials to be weighed. Access ramps are useful for floor scales for loading barrels and drums wheeled on trolleys.
Pit frames are a method for transforming a floor scale that sits on the floor to a low profile platform floor scale. The process includes using the existing deck and placing it in a pit for easier access.
Bumper guards serve two important functions, the first of which is to protect a platform scale from contact by forklift forks, pallet jacks, and incidental impact. They also are an alert system for employees that may be in the area of the scale and prevent them from tripping or being harmed by contact with the edge of the scale.
The sturdy and durable construction of bumper guards makes them capable of absorbing and deflecting the force of a collision with some types having a reflective surface for higher visibility.
Mixing scales are used in the accurate weighing of very fine ingredients in production processes that result in a large impact on the quality and characteristics of a product. They are commonly used in manufacturing automotive paint.
SAW scales are a new technology in the platform scale industry. Unlike transitional platform scales that rely on strain gauges, SAW scales measure displacement using receiver transducers and transmitter transducers. The interaction between the two transducers creates a wave that passes back and forth between them.
The transmitter transducer of a SAW scale creates a wave that passes to the receiver, which is passed back to the transmitter. When an item to be weighed is placed on the scale platform, its spring bends and changes the frequency of the waves being passed between the transmitter and receiver. The weight of the item on the platform is determined by the change in frequency.
Digital platform scales are the standard for the platform scale industry. They are capable of weighing very large objects that can weigh up to 10 tons. Digital platform scales have bearings and pivots on their sides and sliding or spring dials. The popularity of digital platform scales is their accuracy and ability to provide clear and concise weight readings.
The various types of digital platform scales are grouped as electronic instruments that are a necessary part of industrial and manufacturing processes. Weight measurement is an important part of production operations and must be precise and accurate. For many years, mechanical platform scales were used to measure components, parts, and raw materials but provided inaccurate measurements.
The introduction of digital technology provides manufacturers with exceptionally accurate measurements consistently and efficiently. The enhancement of weighing processes and the improvement of measurement readings offers a competitive edge and greater profitability for product producers.
The previous chapter listed the different types of platform scales that offer diverse features depending on the customer‘s needs and desired level of service and automation. The following aspects need to be examined when choosing, upgrading, and maintaining a platform scale:
Capacity is the heaviest load the platform scale can measure. This is one of the most important specifications to look for in platform scales. However, platform scales with higher capacities are not always the best option, as increasing capacity generally reduces accuracy. Investing in and maintaining higher capacity platform scales is also more expensive. Therefore, you should select a capacity only reasonably higher than the estimated heaviest load to be weighed.
Readability refers to the smallest division at which the scale or balance can be read. It designates the number of decimal places on the measurement value to be produced by the platform scale. Higher readability means higher accuracy and a greater number of significant figures of the measurements produced by the scale. This aspect is critical for laboratory scales in reducing calculation errors and for weighing valuable items in which every milligram matters. Also, smaller increments mean higher functionality of weighing sensors used in the scale.
Accuracy is the closeness of the measurement obtained from the platform scale to the true measurement value. The accuracy of platform scales is monitored and preserved by periodic calibration.
Linearity is the property of a scale that refers to its capability of obtaining the correct weight from zero weight to its full capacity. It is measured experimentally by obtaining the measurements of objects with known weights. When the data is plotted, it should generate a straight line. Another way to test linearity is to cut a stable sample into exact halves and weigh the individual halves separately. The sum of the weights obtained must be equal to the measurement if they are weighed together.
Drift refers to fluctuation while weighing a sample, causing the readings to erratically change. This instability causes inconsistent and inaccurate measurement. Drift is attributed to environmental factors such as temperature inconsistency, vibration, air currents, static electricity, and radio frequency interference (RFI). It can be eliminated by the installation of ionizers and by placing the platform scale in an area with no RFI, vibration, or air current.
The materials of construction must be considered when choosing a platform scale. Platform scales must be made with rigid and tough materials, such as steel (e.g., carbon steel, stainless steel) and aluminum (for smaller capacities) in order to support the load during weighing. Corrosion resistance is another factor and is enhanced by the application of a coating. Rugged platform surfaces may also be chosen to prevent the slipping of loads during placement.
When choosing a platform scale, consider the volume of the items to be weighed and the floor space available where it will be situated. Voluminous items are suited to be weighed on a floor scale, while smaller items can be accommodated on a bench scale. Also, check the inclination of the platform scale and assess if a ramp or a pit frame is necessary. It will be challenging to place heavier loads on the platform if the inclination is too high.
When the platform scale is exposed to harsh and wet environments (i.e., prone to spills), and it could be a cause of cross-contamination, cleaning must be done regularly and frequently. There are types of platform scales that are flexible enough, such as washdown scales, to accommodate and ease regular cleaning and sanitation.
Automated systems, such as automated weight verification and data transmission and collection systems, may be integrated into platform scales to increase the efficiency and accuracy of operations. However, more automatic features require higher investment costs.
There are several types of industrial scales that are used to measure and weigh products and materials. Each type varies in accordance with the industry where it is used, the type of materials to be weighed, the method of weighing, and precision of the weight measurements. Of the many types of scales, platform scales have a simple flat platform that is capable of weighing cumbersome and awkwardly shaped loads.
Platform scales can be used in any industry for any purpose. From warehouses to production facilities, platform scales provide durability and accuracy regardless of the harshness of a work environment. They can be used as a single scale for one or multiple locations.
The flat platform design of platform scales makes them capable of weighing heavy loads. A forklift can set a pallet on the scale platform, have it weighed, and remove it in one fluid efficient motion. Readings and measurements are instantly provided in a short amount of time, which is an advantage for time sensitive applications.
Loads can be easily and quickly measured with accurate results, which helps increase productivity and saves time, which helps in reducing turnaround times and improves the ability to meet deadlines.
An aspect of every operation that management struggles to control is errors in data and calculations that slow down an operation. Sophisticated and technologically advanced platform scales have security software and digital readouts that prevent poor judgements and careless errors. When a load leaves a location, it is accurate and as promised.
There are several errors that can be caused by overloading a truck, which include increased stopping distances, poor brake performance, and mechanical failures. These factors can lead to accidents, delayed deliveries, and increased costs.
Platform scales provide precise and extremely accurate measurements that ensure that a truck is loaded to its recommended capacity. Keeping truck loads within their limits helps shipping operations to stay within state and local regulations and prevents a company from being fined for violations of weight restrictions.
A data acquisition system is a system that comprises sensors, measurement devices, and a computer. A data acquisition system is used for processing acquired data, which involves collecting the information...
Force sensors are transducers that transform mechanical input forces like weight, tension, compression, torque, strain, stress, or pressure into an electrical output signal whose value can be used to...
A load cell is a transducer which converts mechanical energy (tensile and compressive forces) into electrical signals. There are different transducer operating principles that can be utilized to convert forces...
A load pin is a sensor utilized to measure force or weight in various research, control, measurement and testing applications. The load pin force sensor converts a force into an electrical signal. The load pins provide...
A strain gauge, or strain gage, is a sensing device used for measuring strain experienced by an object. It is made from a long, thin piece of conductor bonded to an elastic backing material called a carrier...
At the heart of every weighing device is a sensor called a load cell. When an item is put on a load cell, it senses the force of the gravitational pull of the weight, which an electronic circuit processes to display...