Force Sensors
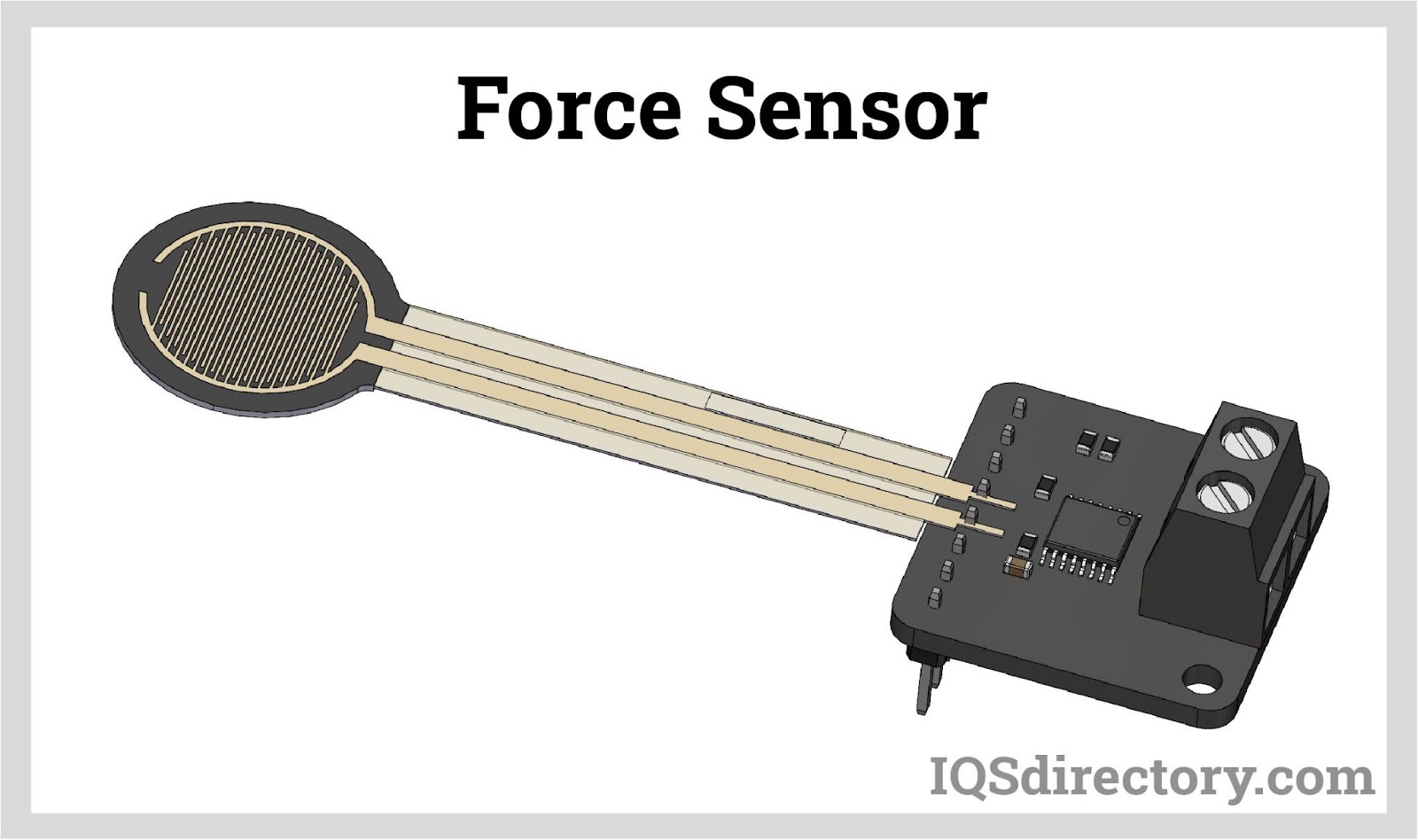
Force sensors are transducers that transform mechanical input forces like weight, tension, compression, torque, strain, stress, or pressure into an electrical output signal whose value can be used to...
Please fill out the following form to submit a Request for Quote to any of the following companies listed on
This article provides comprehensive information regarding load cells and their use.
You will learn:
A load cell is a transducer that converts tensile and compressive force into measurable electrical output. The majority of load cells have a spring element with strain gauges attached and are made of steel or aluminum, which makes them sturdy with little elasticity.
The predominant form of load cell is the strain gauge type. Other types are pneumatic and hydraulic. Pneumatic load cells are used in hazardous conditions, while hydraulic ones are used in locations where there is a limited power supply. In either case, a load cell converts mechanical force into digital values that can be read and recorded.
The inner workings of load cells differ in accordance with how they will be used but are designed to measure mechanical force or the weight of objects. They are depended on for their accuracy and precision with classifications determined by how accurate they are and their capacity.
Types of load cells
In a load cell, areas, structures, or groups of areas are designed to be stressed when a linear force is applied. The areas of a load cell sense the force applied under pressure and provide an electrical output signal proportional to the force. The output is normally in millivolts and needs amplification in order to be read.
Transducers come in several forms with strain gauges being the most common and widely used. Other forms of transducers include capacitive, piezoelectric, vibrating, and magnetic, which use different principles to supply data.
Strain gauge transducers work on the principle of changing electrical resistance as the conductor is being elastically deformed. Tensile stress causes the conductor’s cross section to narrow and elongate as compressive stress widens and shortens it. The amount of stress is converted, transduced, forced, pressured, compressed, torqued, and weight into measurable electrical resistance.
The stamp-like patterns of parallel wires are bonded onto the surface of a metal body. As the body experiences stress, the wires deform and resist the applied stress, which is measurable since the resistance is proportional to the stress from the applied force.
Capacitive force transducers change the capacitance, which is the ability of a system to maintain change when voltage is applied. In parallel plate capacitors, capacitance is proportional to the overlap in the plates and the dielectric between them but inversely proportional to the gap between them.
The basic principle of a capacitive force transducer is to take advantage of a material’s capacitance, its electric charge storage. The main part of the instrument is the capacitor which can be flat, cylindrical, or spherical and are also known as capacitive strain gauges.
A simple capacitive force transducer consists of two parallel plates separated by an elastic material that also acts as a dielectric. Applying force across the plates increases the capacitance as the dielectric deforms across the plates. Capacitance depends on the area and distance between the plates.
Piezoelectric transducers use the piezoelectric effect, which is the ability of certain materials to produce an electric charge under mechanical stress. They are an electroacoustic transducer that converts electrical charges from various types of materials. The term piezoelectric means electricity produced by pressure.
The elements of a piezoelectric transducer begin to oscillate when voltage is applied. They respond in microseconds, which makes them useful for a wide range of applications. They are small but have a wide measuring range, which makes them easy to handle and install. Piezoelectric transducers have a high frequency range that allows them to shift quickly.
Load cells that use the piezoelectric effect usually measure forces in one direction only. If a measurement is needed from other directions, more transducers are installed. Although piezoelectric transducers are self generating, they require a cable connection for an electrical interface.
Vibrating wire transducers use the principle of natural frequency change of a tensioned wire or string. For a given length, mass, and material of a string, the higher the tension, the higher is the frequency. The tension in a string is directly proportional to the square of its frequency of vibration.
In this type of transducer design, a wire or string is used as the force sensor. An electronic oscillator circuit causes the wire to vibrate at its natural frequency. The wire is attached to a diaphragm where pressure is applied. As the pressure changes on the diaphragm, so is the tension experienced by the wire. The change in tension also changes the wire’s vibration frequency, which is then measured by a sensing coil, which is converted into an electrical signal.
Magnetic transducers, also known as the “Pressductor” load cells, were developed by ABB. They use the magneto-elastic effect or the change in permeability in a magnetic core, occurring when a force is applied to the core. When exposed to mechanical force, ferromagnetic elements change the magnetic moments of its “Weiss” domains when pressure is applied, resulting in changes in the magnetic characteristics in the directions in which the mechanical forces act.
This transducer consists of a laminated iron core with two perpendicular windings. An alternating current through the primary winding sets up an alternating magnetic field in the core according to the “no load” pattern, where no voltage is induced in the perpendicular secondary winding. When load is applied to the iron core, the change in permeability in the magnetic core causes the magnetic flux lines to change their orientation. The change in orientation sets up a magnetic flux that passes through the secondary winding. A voltage is induced in the secondary winding which is converted into a readable signal.
A hydrostatic force transducer consists of a working fluid, a piston or diaphragm, and a cylinder. The pressure trapped between these components is measured and converted into readable indications such as dial movement via a Bourdon tube gauge. Pneumatic and hydraulic load cells belong in this category. Hydrostatic force transducers are used in hazardous areas where an electric load cell with a high ingress protection rating or ATEX rating is economically impractical.
The Wheatstone bridge, or resistance bridge, measures unknown resistance by balancing two legs of a bridge circuit with one leg having unknown resistance. It has two known resistors, an unknown resistor and a variable resistor, which are connected to form the bridge. The circuit includes a galvanometer and an electromotive force (EMF) source.
The four resistors of a Wheatstone bridge are arranged as a quadrilateral ABCD. The EMF is attached between points A and B while the galvanometer is connected to points C and D. Current that flows through the galvanometer depends on the difference across it. Resistances are chosen such that the galvanometer needle does not deflect, which is called the balanced condition of the bridge.
The variable resistor of a Wheatstone bridge is the sensing element or the strain gauge. If the resistance changes in the variable resistor relative to the others, the current will pass through a meter. Basically, the Wheatstone bridge converts the change in resistance due to strain into a measurable electrical signal. The purpose is to measure unknown resistance.
The Wheatstone bridge configuration for strain gauge load cells has four strain gauges where all four strain gauges deform and change resistance. The strain gauge load cell is balanced at around 350 ohms. It has a regulated excitation voltage with resistance remaining constant when no load is applied. With the application of force, the resistance changes for all four strain gauges and is converted to weight.
Other Wheatstone bridge designs use two variable resistors to improve the system's sensitivity and to provide an enhanced voltage variation as a function of the changing input. When applied to a force sensor system, the bridge circuit has two fixed resistors and two variable resistors. A direct current (DC) voltage source supplies energy to the circuit. The Wheatstone bridge output is the gap voltage measured at Vout. The gap voltage is proportional to the difference in the transducers’ resistance values relative to the reference resistance in the bridge configuration.
This design allows for the measurement of very small changes and reduces the effects of noise on the gap voltage. If the input voltage fluctuates, it does not affect the gap voltage since it is related to the ratio of the resistances. Since all resistors are affected, the effect is canceled out regarding the effects of varying temperatures.
Many force transducers use simple elastic elements or a combination of elements, such as pillars, beams and rings, in their construction. Force application causes deformation or deflection on elastic elements and the strain gauge senses the movement, which is converted into measurable output by the Wheatstone bridge.
In the tension or compression type, a combination of strain gauges are placed along the side of a cylinder or a straight beam. The strain gauges are oriented either in the transverse or longitudinal direction and are connected to the Wheatstone bridge accordingly. As the column is compressed, longitudinal strain gauges contract while the transverse stretches.
A Roberval mechanism is a scale in which two horizontal beams, one over the other, are attached to a vertical beam at both ends. This configuration is applied to strain gauges load cells having four thin portions two at each of the upper and lower beams. One end of the double beam is fixed in a cantilever manner, while the other end carries the applied load. The strain gauge is attached to the top and bottom surfaces adjacent to the thin portions.
This configuration is well suited for high-precision load cells since all four arms of the Wheatstone bridge are active, creating higher sensitivity. When a load is applied, this elastic element deflects as shown in the figure above, where two strain gauges are in tension and the other two are in compression.
For shearing strained elastic elements, the strain gauges are oriented at 45° angles with respect to the direction of the applied load. In this configuration, it is possible to measure loads accurately independent of where the load is applied. This is because of the cancellation of the bending strain experienced by the strain gauges. Half of each strain gauge will experience some bending strain, while the other half will experience the same magnitude but in the opposite direction.
The shearing strained elastic elements can be further classified as:
These elastic elements can be constructed from different materials. The most common materials are alloy steel, aluminum, and stainless steel. Alloy steels are used because of their cost with AISI 4330 being the most popular, which is a medium carbon, low-alloy steel consisting of chromium, nickel, and molybdenum. It has good hardenability, high transverse strength, and toughness.
Aluminum is used in single-point, low capacity applications. The main advantage of using aluminum elastic elements is its cost since it is the cheapest of the three materials. Aluminum alloy 2023 is used because of its low creep and hysteresis characteristics.
Stainless steel is the material of choice for wet or corrosive applications. Stainless steels are generally more expensive than alloy steels. The popular stainless steel used for load cell construction is alloy 17-4PH, or AISI 630, which is a martensitic chromium-nickel stainless steel stabilized with niobium. Aside from corrosion resistance, it has high strength and toughness.
Load cells may also be classified based on their outer shape. Different shapes have their own specific applications, which are used individually or in combination of elastic elements.
Canister load cells are the earliest designs of load cells. Their elastic element is a single or multiple stretched or compressed column that is hermetically sealed to protect the strain gauge. Canister load cells can have a capacity from 100 lbs up to 500,000 lbs, depending on the number of columns. They measure tension or compression but are limited due to their inability to withstand side loads.
Bending beam load cells, at first glance, may be thought of as being similar to the shear beam. However, the two have different elastic elements. Bending beam load cells do not have a reduced cross-section for the strain gauges but have a beam that is machined all the way through. The strain gauges are bonded as shown in the Roberval-type load cell.
Single-ended shear beam load cells use the concept of the “I”-profile shear beam. In this design, the elastic element of spring material has a reduced cross section where the strain gauges are bonded. One end of the shear beam contains the mounting holes, while the other end is where the load is applied. These are commonly used in low profile scale applications.
The double-ended shear beam is similar to the single-ended. Instead of being secured only at one end with the load applied to the other end, the double-ended shear beam is secured at both ends with the load applied to the center of the load cell.
Load measuring pins or bolts are used to measure tension and have rod shaped elements. These are actually short, thick-walled tubes with strain gauges bonded on each side of the center section at 45⁰ angles with respect to the tube axis and have a spring element that applies perpendicular force to the horizontal axis. Load measuring pins or bolts are typically installed into machines in place of normal shafts wherein it acts like a normal piece of the assembly.
These are hollow disc load cells that have a circular array of holes located about half of the radius from the center of the disc. Shear strain gauges are located within these holes at 45° angles with respect to the loading axis. They have a very low profile and can be mounted between components for compression or used in tension. Force is applied to the center of the cell where the beam arms meet.
These load cells have an elastic element deformed by tension or compression at both ends. Its strain gauges are usually configured in an “X”-pattern. These strain gauges are compact, inexpensive, monolithic, and easy to install. They are commonly used in tension applications and are found in hanging scales or other suspended weighing applications. S-type load cells can be suspended from shackles or mounted between items using eye bolts at their top and bottom.
These are based on the principle of a wire wound spring. The helix works by converting the applied load into a torsional moment in the wire. This configuration is insensitive to off-axis loading due to how the torsional moment propagates through the helix. The orientation of the strain gauge is unimportant.
The elastic element is usually a bent ring, bent membrane, or a diaphragm depending on the manufacturer’s design, but it uses the principle of bending beam elastic elements. These load cells have a low profile enabling them to be used in a variety of applications. However, they can only measure compression. The low profile of button load cells causes them to be referred to as a miniature load cell.
Tension Link load cells are a versatile form of load cell that can be customized for low, medium, and high load applications. They are used in crane and hoist scales, pull testing, and tensile strength measurement. Tension link load cells have a figure 8 shape so that they can be linked between cables, ropes, or chains. Their loading axis is vertical with the strain gauges placed parallel to each other to measure loading strain.
Load cells are categorized by their output signal or method for detecting weight. The function of load cells is the measuring of force, turning the measurements into digital values, and transmitting the values in various forms to be read and recorded. The significance of the work of load cells is the simplicity of their design and the complexity of the formulations they use to provide weight and force data.
Hydraulic load cells measure weight based on the change in pressure placed on an internal fluid. With a diaphragm hydraulic force sensor, the load acts on a loading head that causes a piston to compress fluid in a confined elastomeric diaphragm chamber. As the force increases, pressure on the fluid rises. The output is linear and unaffected by the amount of fluid or the fluid’s temperature.
Pneumatic load cells operate on a force balance principle and use multiple dampener chambers that provide highly accurate readings. They have an elastic diaphragm that is attached to a platform surface. When an object is placed on the load cell, pressurized air or gas balances its weight. The air needed to balance the weight determines the weight of the object.
Pneumatic load cells are used in industries where small weights are measured and cleanliness and safety are important. They are explosion proof, unaffected by changes in temperature, and do not have any fluids that would contaminate a process if the diaphragm of the load cell ruptured.
Strain gauge load cells are the most common type of load cell with a capacity rating between 5 N to more than 50 MN. They have high-res digital indicators with ideal force transfer standards. Strain gauge load cells are transducers that change electrical resistance when under stress or strain with the resistance proportional to the strain placed on the cell. The readings from a strain gauge load cell are linear and can be converted to force and weight.
Miniature load cells are compression load cells designed to work with high capacity loads where there is minimal space. They can be miniature or subminiature with a diameter of 51 mm or two inches. Their small size and diameter make them ideal for test benches, industrial weighing, and prototypes. Miniature load cells have twist lock connectors and cable connections with metric configurations ranging from 0 to 100 N to 0 to 50,000 N.
Donut load cells, also known as thru hole load cells, measure compressive forces and are called donut load cells because of their shape. They are smooth and round with a hole in the middle for parts or bolts and are used in oil and gas pumps. Donut load cells are used in applications that require the load structure to pass through the load cell. They come in tension or compression models and can measure 150 g up to 100 tons. Donut load cells are used for bolt force measurements, clamping force, monitoring overloads, and monitoring rolling mill systems.
Capacitive load cells use capacitance, the ability to store a charge, as a measuring method. They have two flat parallel plates. When current is applied to the plates, it is stored between the plates. The amount of charge that is stored, capacitance, determines how large the distance is between the plates. When a load is placed on the plates, the distance between the plates shrinks, which can be calculated into weight.
There are two types of capacitive load cells, which are low and mid.
Micro load cells are resistive load cells that use the principle of zero piezoresistivity. When a load, force, or stress is applied to the sensor, the resistance changes, which causes the output voltage to change because the input voltage has changed. Micro load cells are used for compression force measurements in cramped spaces that require precision and durability. They can have a weight capacity of 10 g up to a ton. Micro load cells are 10 mm high and as low as 3.3 mm.
Multi-axis load cells measure force and torque that occurs in several directions and can measure up to six different components. They are ideal for measuring multidimensional loads that form along the x, y, and z vectors or three spatial directions and convert the data into an electrical output signal. Multi-axis load cells are commonly used in robotics and for monitoring machines for load limiting purposes.
Although it is possible to use several load cells to measure the force and torque of multiple applications, multi-axis load cells make it possible to take the functions of several load cells and compact the work into a single load cell. They are designed and manufactured to measure a multitude of forces simultaneously using a single load cell.
Multi-axis load cells provide multiple bridges that precisely measure force from one direction with little or no cross-talk from other forces or moments. Multi-axis load cells combine simultaneous measurement, compact design, and error reduction. They are chosen for their force range, accuracy, easy mounting, and ability to endure a variety of environmental factors.
Unlike single point load cells, multi axis load cells are capable of measuring tension, compression, and torque in all directions. They have multiple strain gauge bridges to measure forces and torque in one direction with little to no interference from forces applied in other directions. Multi axis load cells save space in assembly and installation time.
Multi-column load cells have four or more small columns, each with its own strain gauge, which are connected in a series in the bridge arms. Much like multi-axis load cells, multi-column load cells are compact than high stress column load cells. They are known for their better discrimination of the effects of off axis load components and have less creep. Multi-column load cells are designed with a shear web spring to provide better output, linearity, lower hysteresis, and quicker response time.
Although multi-column load cells are heavier, which restricts their use for lightweight applications, they have an accuracy of 0.0125% of a full scale. An exceptional aspect of multi-column load cells is their high capacity that ranges between 100,000 lbf. Up to 2.25 million lbf (10N). Multi-column load cells can be combined with a 50,000 lbf load cell and 1000 lbf load to cover a range from 40 lbf up to 600,000 lbf
High capacity load cells can measure extreme loads such as the roof on a mine and the thrust force of a rocket. They are integrated into machines, systems, and instruments and are small, lightweight, and compact. High capacity load cells are custom designed to fit the requirements of each individual application and may need to be inserted into an existing mechanism.
Dynamometer load cells, or dynos, measure force, torque, and power. A dyno, combined with load cell sensing technology, creates a dynamometer load cell, which is used to measure engine power output. They provide extremely accurate measurements of cabling and wiring installation for increased safety. Dynamometer load cells are designed to measure loads of several tons.
Single point load cells have one load cell and are used in individual device applications, such as supermarket scales. To provide accurate readings, the load has to be correctly aligned due to the design of single point load cells. They are commonly used with platform scales. There are endless numbers of single point load cell designs since they come in a wide variety of shapes and sizes for different applications. All single point load cells are distinguished by their inner aperture, which is a cut out of the load cells body.
S beam load cells are bending beam load cells used for weighing applications under 50 lbs. (22 kg). They have a metal spring element that deforms when a force or weight is placed on the load cell. The strain gauge in the load measures the fractional change in the length of the deformation. S beam load cells are used in scales and tension applications.
S beam load cells are very popular due to their precision, low price, and ease of installation. They are designed for inline applications and are sensitive to outside loads and torque. S beam load cells must be centered to the load and have proper directionality.
In line load cells are installed in line to the load axis for tension measurement and come with a variety of thread configurations. They are designed to be able to withstand off axis loads, which makes them an ideal choice for applications where side loading cannot be avoided. In line load cells can easily fit into an existing work system that has tight spacing or clearance. The popularity of in line load cells is due to their durability and reliable readings.
The different types of in line load cells are designed with temperature compensation for excellent performance. They are capable of measuring tensile and compressive loads up to 5000 N with ±0.25% non-linearity. In line load cells are bi-directional with a compact construction for long term stability. They are used in the auto industry and robotics for force sensing.
Load Pins, known as clevis pins or dynamometric axles, are a type of weight sensor used for overhead equipment. They have rod shaped elements and are short, thick-walled tubes with strain gauges bonded on each side of the center section at 45° angles with respect to the tube axis. A spring element applies perpendicular force to the horizontal axis and measures the acting force. Load pins are typically installed into machines in place of normal shafts and act like a normal piece of the assembly.
The strain limitation on a shaft is the foundation for the design requirements for a load pin with the most critical parts being those in contact with the holding plate, which are thinner than the central tool. Force load pins have a range between 150 N/mm² and 200 N/mm² while hoist load pins have a range of 100 N/mm² and 120 N/mm². Of the force, hoist, and lift load pins, lift load pins have the lowest strain at 50 N/mm². These design factors ensure the mechanical and fatigue of a load pin and its mounting.
The area of the load pin between the forces measured on the exterior is defined by two grooves. The pressure the fixed support applies is the polar opposite of that produced by the lug or sheave. Load pins measure the force or pressure and transmit the measurement to a weight display. They continuously monitor the load's weight, promote safety, and prevent overload damage. Load pins are made of corrosion resistant stainless steel and are located internally.
Load pins are strain gauges with a Wheatstone bridge circuit that generates variable output voltage proportional to the force acting on the elastic element when activated by a fixed voltage source. As a result, the mechanical input quantity is changed into electrical output.
Load pins are made of high-strength alloy steel or stainless steel, which makes it possible to use them in hostile corrosive environments. They are simple to install and are a cost effective method for load measuring. Load pins are available with thermal compensation and electronic wireless transmitters for monitoring.
The proper use of a load pin requires that it be rated for the amount of weight it will measure. If it has too high a capacity, it won’t provide accurate data. How a load pin is mounted, the span of the corresponding mounting, and the hardness of the material holding it influence its sensitivity. The diameter of load pins varies between 7 mm up to 480 mm with capacities between 2000 N up to 30 MN. Higher capacities can be produced but require special planning.
Other factors that influence the use of a load pin include where it will be located, proper certifications, and the types of materials that will touch the load pin such as liquids, gases, or solids, which require an understanding of a load pin's ingress protection (IP) rating . As with all forms of equipment, a load pin must be designed to meet the variations in temperature where it will be used. Physical or mechanical factors need to be considered including vibrations, airflow, and wind that influence measurements.
Load pins are made with signal amplifiers for mV/V output: 4-20mA, 0-10V (and derived), RS485, Modbus, and CAN. Analog amplifiers can be tuned to allow overloads without signal saturation using a range from "0" to nominal capacity or any other capacity.
The purpose of a load pin is to quantify force or weight using a sensor that transforms force into an electrical signal. Load pins have a small internal bore that is machined along its neutral axis to protect internal instrumentation from the outside environment. The viability and use of load pins has radically increased over the years since they can be engineered to fit any application.
Twin bridge, two independent strain gauge circuits, is offered by clevis pins. Dual bridge transducers can utilize just one bridge for measurement while saving the other bridge as a backup, or they can use both bridges simultaneously for control and measurement.
With either single or dual connectors, electrical terminations can be either radial or axial. Cables that are permanently attached are also an option.
Wireless load pins are used where cable installations are challenging or expensive. They have a long battery life and provide precision measurements, resolution, and stability. Wireless load pins have a simple configuration, calibration, data logging, and recording interface with a transmission range of up to 800 m (2600 ft) and can be used with unique clevis pins.
Force sensitivity load pins, sometimes called clevis pins or clevis bolts, are load sensors that use an internal strain gauge transducer with flat load cells and tension links. Strain gauges are installed at the clevis to clevis eye interfaces and sealed in axial holes in the load pin. Positioned at a neutral plane in one direction, the load pin can detect strains caused by the shear stresses at two sections.
Four strain gauges—two at each location—are electrically connected to create a full bridge. Since each strain gauge's signal is additive, the output of the bridge is proportional to the total loads communicated by the pin's shear planes. The circuit often includes temperature compensation, signal trim, and balancing resistors that terminate in suitable connector sockets or integral cables.
Detailed calibration data up to 500,000 lbs. are included in standard force sensing load pins/bolts. Therefore, standard force sensing load pins/bolts need higher capacity calibration data. Although calibrations are meant to mimic installed settings, it is advised that an in-place calibration be carried out to take into account any installation, tolerance, and alignment impacts that may alter sensor data.
A special form of force sensitivity load pins are standard wire rope load pins that are used with cranes, marine mooring lines, and hoists and are used to replace clevis pins in wire rope socket hardware. They have the same structure as other force sensitivity load pins and provide high capacity calibration data. In conjunction with wire rope load pins, shackle load bolts or pins are used with Crosby anchors and chain shackles.
Sheave and pulley systems use a variety of load pin designs that are placed around a clevis pin or are used with an existing sheave. They are used to gauge line tension. A critical aspect regarding the use of sheave and pulley load pins is the wrap angle, which can be variable or constant and determines whether there will be one or two strain gauge bridges.
As durable and resilient as load pins are, they are susceptible to various factors that can influence their readings. Regular Calibration, at intervals, is required to ensure a load pin is operating within its specifications, since all load pins experience degradation through usage, abuse, drift, or aging. Electrical impact, mechanical effects, instrumentation errors, and loose wires reduce load pin performance and reliability over time. Particulate matter can also accumulate that can cause failure if a load pin is not properly cleaned, which can lead to operational problems. Load pin manufacturers strongly advise that regular maintenance be performed on load pins to ensure accurate readings.
Force sensors are transducers that transform mechanical input forces like weight, tension, compression, torque, strain, stress, or pressure into an electrical output signal whose value can be used to represent the force's magnitude. To notify operators or act as inputs for controlling machinery and processes, the signals may be delivered to indicators, controllers, or computers.
The fundamental idea behind force sensors is their reaction to applied force, which they transform into quantifiable data. They typically consist of electrodes and sensing material. When force is applied to an object, it can be determined by measuring how much resistance the force sensing resistors, major components of force sensors, experience.
The operation of force sensing resistors is based on the contact resistance property. In force sensing resistors, a conductive polymer sheet changes resistance when force is applied to its surface. The polymer sheets contain a matrix of sub-micrometer-sized, electrically conducting, and non-conducting particles.
When force is applied, the micro-sized particles from the polymer sheets touch the sensor electrodes, which alters the resistance of the film. The degree of change serves as a gauge in regard to the amount of applied force that changes the electrical resistance. These changes can be measured in terms of mechanical force or pressure.
Industrial and manufacturing plants use load cells in measuring quantities of their raw materials and finished products. Moreover, along the process line, there is a need to know how much material is present so process parameters can be adjusted accordingly. Load cells are used on industrial equipment such as hoppers, silos, tanks, conveyors, packaging machines, etc.
Popular equipment that uses load cells under this category is the universal testing machine. Laboratory scales also use load cells with very high precision. However, other force transducer principles are used other than the strain gauge.
Output signals from load cells can be used as feedback signals by process lines for automation. Load cells are used for automatic packaging, distribution, and sorting.
Load cells are also used in truck platforms, weighbridges, cranes, railways, etc. Load cells in this category are mainly used for measuring goods loaded onto trucks and containers.
Force sensors are available in a wide range of sizes and shapes. Their three fundamental parts are force sensitive components that change when stress or force is applied, a conversion component to produce measurable units, and a circuit. Typically formed of enameled wire or PCB board with force sensitive components, the circuit is composed of aluminum alloy, alloy steel, and stainless steel. It is created by connecting gauges across the sensing element. The conversion element is a strain gauge made of a coil or can be a piezoelectric sensor that runs on a crystal.
The outputs for force sensors can be analog voltage, analog current, analog frequency, switch or alarm, serial, or parallel and have measuring circuits with four gauges. Up to thirty gauges can be included in more intricate sensor measurement circuits. A force sensor's sensitivity to detecting and tracking measurement deviations increases with the number of gauges with the Wheatstone bridge equation used to govern the creation of the gauges and circuits.
The manufacture of force sensors includes the use of micro electromechanical systems fabrication that is used to produce miniaturized sensors, actuators, and other forms of transducers. The specific purpose of MEMS fabrication is to develop microsensors that convert measured mechanical signals into electrical signals.
The process for manufacturing a force sensor begins with an insulator wafer with silicon nitride coated on both sides of the silicon. Using a photolithographically designed etch mask and a reactive ion etcher, the front side of the silicon nitride is etched to expose the thin silicon on the front side and leaving a nitride ring at the front side’s outer section.
To protect the semiconducting silicon from the resistors that rest on the oxide, silicon oxide is formed on the front side. For the other side, the nitride is etched to create square windows that resemble thin diaphragms. The silicon is then anisotropically etched in potassium hydroxide (KOH) with the nitride serving as an etch mask and the original oxide as an etch stop. The square silicon diaphragms that hang over open cavities are released after the KOH etching, which are sealed with Pyrex® wafers.
Using hydrofluoric acid and a chromium-gold etch mask, channels are etched into the Pyrex® wafer that has a clean reversal face on the back and an engraved face on the front. After the Silicon on Insulator wafer and Pyrex® wafer have been anodically connected, resistors are etched into a metal coating and deposited on the front side by thermal evaporation.
To waterproof and insulate the resistors, a thin film of parylene polymer is placed on the front side. A die saw is used to separate individual pressure sensing cells or pressure sensing arrays from the bonded wafer pair before testing and packaging. Metal needs to be patterned once it has been initially placed on the wafer and deposited after the KOH etching, which is followed by bonding. Between KOH etching and bonding, metal patterning is not possible.
Wheatstone Bridge Circuit is used to detect and measure minute changes in resistance since the variations in the resistances are very small. Piezoresistive pressure sensors and strain gauge pressure sensors use this arrangement.
The basic four types of force sensors are capacitive, inductive, piezoelectric, and piezoresistive elements. The distinction between the four types is based on how their sensing element behaves. The structure, endurance, and durability of each type of force sensor make it possible for them to function successfully in several types of environments.
An inductive force sensor detects or measures items using the electromagnetic induction and converts it into voltage or current output through a conversion circuit. As an electric current passes through the inductor, it develops a magnetic field. An inductive sensor can function in damp or soiled environments because non-metallic objects, such as liquids or dirt, do not interact with the magnetic field. Some inductive sensors alter their characteristics to measure force, such as self-inductance, mutual inductance, or eddy current creation.
Inductive force sensors are used for low force readings and displacement measurements. With the development of a bi-directional inductive force sensor, it is possible to measure a force's amplitude and direction in a plane. The inductance of inductive sensors is reduced by eddy currents, which produce an opposite magnetic field.
Capacitive force sensors measure and detect anything that is conductive or has a dielectric constant. When force is applied, the distance between the conductive plates in the sensor changes, which causes a change in capacitance that is proportional to the applied force. They are designed with single plates, parallel plates, and interdigitated capacitive sensors, each of which has an advantage and are chosen to fit exacting requirements. Their high sensitivity, low power requirements, temperature stability, and cost make capacitive force sensors attractive.
A piezoelectric force sensor uses the piezoelectric effect, which is when a material generates an electric charge when mechanical stress is applied to it. Some materials produce an electric voltage when mechanical stress or forces are applied along specific planes. Piezoelectric force sensors measure changes in pressure, acceleration, temperature, strain, and force by converting them into an electrical charge. The heart of a piezoelectric force sensor is a quartz crystal that produces an electric charge when placed under mechanical stress. An amplifier is used to convert the charge into an easy to understand measurement.
Piezoresistive force sensor operates on the same principle as a piezoelectric force sensor. The structure of a piezoresistive force sensor includes a thin, flexible diaphragm that deforms when force is applied. It is a resistive type of force sensor that varies its resistance and produces the necessary output while monitoring various environmental factors including force, strain, and pressure. A force sensing substance that can either be directly manufactured on the sensor or joined to the sensor is used as a strain gauge.
A resistive force sensor detecting technique involves the resistive element being deformed against the substrate when an external force is applied to the sensor. The conductive material on the substrate comes in touch with the active area when air from the spacer aperture is forced through the air vent in the tail. As a result, conduction is feasible and the material's resistance reduces.
Optical force sensors measure the effect of pressure on light in order to identify changes in pressure. In its basic form, an optical force sensor can be a mechanical device that dims light when the pressure rises. The phase difference provides extremely accurate measurements of minute pressure changes.
A rise in pressure will result in a progressive blockage of a light source in an intensity based optical pressure sensor. The sensor gauges the variation in received light. The pressure causes a diaphragm to move, and the associated opaque vane further dims the LED's brightness. The photodiode detects the decrease in light intensity and measures the pressure.
A reference photodiode, which is never obstructed by the vane, is necessary for a straightforward optical pressure sensor and enables the sensor to compensate for variations in supply voltage and changes in the light output caused by other variables.
Force transducers are used to measure weight during production and metering force in industrial equipment and systems, such as presses, assembly lines, or end-of-line inspections. Scales are the most common application that come in a wide variety of designs, sizes, and configurations. Force sensors provide accurate results regardless of the materials being weighed. They are built into scales at the self-service checkout at local grocery stores for weighing produce.
In the medical field, force sensors are used in applications such as fluid monitoring, MRI machines, dialysis machines, endoscopic surgery, and physical therapy equipment. They are essential for medical applications that require special authorizations and testing.
To maintain the health of roads and highways, force measurement is essential. Force sensors are used to measure and assess commercial trucks regarding their axle load, which are precision measured for effective monitoring of their weight when loaded. They are used in cars to measure trailer couplings to determine data in connection to driving behavior on the road and supply information on the weight of the trailer. Force sensors are used for vehicle control technology to help a driver respond more effectively to various situations on the road.
In the railway sector, force sensors calculate the weight of cargo, passengers, and tractive forces on the drawbar. The gathered information is made available to guarantee a secure and safe operation within suggested limits. In addition to their use on the train itself, force sensors are used throughout the entire track system.
Aerospace applications use force sensors for force feedback, flap detection, autopilot operations, and flight recorder data. Objects are tested to determine how much force is being applied to them.
Reference measures are used to produce domestic and worldwide comparability between measured values. Systems are tested by metrological institutes all around the world using incredibly precise force transducers. Reference values are then provided by these institutes for both domestic and global economies. Force transducers are frequently used on test benches to ensure that a desired material load can be properly controlled.
The strain gauge is made up of thin wires which are prone to the effects of the environment. Varying temperatures can expand or contract a strain gauge creating noise and inaccurate measurements. Corrosion can also creep into the elastic element, which will shorten the life of the device. Aside from the possible deterioration, the load cell itself may cause safety problems to the environment. For applications in an industrial plant such as a refinery or chemical plant, there is a risk of igniting flammable liquids and gasses. For these reasons, load cells are constructed in either of the following.
Ingress Protection (IP) Rating:The ingress protection rating is a measures the protection a load cell has against solid objects and liquids. The IP rating consists of two numbers with the first indicating the protection against solid objects while the second number refers to protection against liquids. An IP rating of IP67 means that a device is dust tight and can be immersed. The image of the scale below has the definitions of the first numbers or solid objects on the left and the numbers for liquids on the right. It is part of the International Electrotechnical Commission's standard 60529 and serves as a general rule for all load cell manufacturers.
Ingress Protection Rating Scale | |||
---|---|---|---|
1st Numeral | Degree of Protection | 2nd Numeral | Degree of Protection |
0 | No Protection At All Against Solid Objects | 0 | No Protection At All Against The Ingress Of Water |
1 | Protection Against Solid Objects Greater Than 50mm In Diameter | 1 | Protected Against Fallling Water Drops |
2 | Protection Against Solid Objects Greater Than 12.5mm In Diameter | 2 | Protected Against Fallling Water Drops At An Angle Of Up To 15° |
3 | Protection Against Solid Objects Greater Than 2.5mm In Diameter | 3 | Protected Against Sprayed Water Drops At An Angle Of Up To 60° |
4 | Protection Against Solid Objects Greater Than 1.0mm In Diameter | 4 | Protected Against The Splashing of Water From Any Direction |
5 | Protected Against The Ingress Of Dust In Such An Amount That It Will Not Interfere With The Operation Of The Equipment | 5 | Protected Against Water Jets From Any Direction |
6 | Total Protection Against The Ingress Of Any Dust | 6 | Protected Against Powerful Water Jets From Any Direction |
7 | Protected Against The Ingress Of Water When Temorary Immersed Of Between 0.15 m And 1 m | ||
8 | Prtected Against The Ingrss Of Water When Continuously Immersed To A Specified Depth |
Hermetically sealed load cells offer the best protection available. This is achieved by welding, epoxy sealing, or glass-to-metal bonding. The inside cavity is filled with a pressurized inert gas. Hermetically sealed load cells are air and water tight characterized by Ingress Protection (IP) rating.
These are designed in normal environments in indoor or protected outdoor applications. Environment protection of open load cells is through soft resin or rubber covering. This type of protection makes the strain gauge vulnerable to moisture and temperature fluctuations.
Explosion proof means the load cell will contain or prevent an explosion that may originate within the device. For any device or equipment with internal cavities exposed to flammable gasses, these gasses will eventually creep inside, filling the cavity with an explosive mixture. Sparks from the load cell will ignite this mixture, causing an explosion. An explosion proof rating can be achieved by a combination of containment, energy limitation. and segregation.
When designing a system using load cells, it is important to consider the following.
Rated Capacity or rated load is the maximum capacity or weight that a load cell can measure. When designing a system to measure a certain weight, the load cell rated capacity must be greater than the weight.
Overload Rating (Safe) is the maximum load that can be applied to a load cell without causing a permanent change in measuring characteristics or performance.
Overload Rating (Ultimate), on the other hand, is the maximum load which can be applied without causing damage to the load cell.
Rated Output is the electric output signal per strength of the excitation voltage expressed in mV/V.
Zero Balance is the electric output signal with rated excitation voltage when no load is applied.
Excitation Voltage is the voltage supplied to the transducer circuit.
Non-linearity is the load cell‘s calibration curve deviation from a straight line, starting from zero load up to the cell‘s maximum rated capacity. This is the weighing error over its entire operating range.
Hysteresis is the difference between two load cell output readings for the same applied load. One reading is obtained by increasing the load from zero, while the other by decreasing the load from the load cell‘s maximum rated capacity.
Combined Error is the combination of non-linearity and hysteresis.
Repeatability is the maximum difference between load cell output readings for repeated loads under identical loading conditions.
Temperature Effect on Rated Output is the deviation in output readings caused by temperature changes.
Temperature Effect on Zero is the deviation of the zero balance caused by temperature changes.
Input and Output Resistance is the resistance of the load cell‘s circuit measured at the positive to negative and negative to positive excitation leads, respectively.
Insulation Resistance is the resistance of the load cell measured between the load cell circuit and the load cell housing.
All industries that require weighing use load cells due to their compact profile as compared to mechanical scales. The load cell application is not limited to weighing; load cells are also used in automation and structure monitoring. Listed below are the general applications of load cells.
Industrial and manufacturing plants use load cells in measuring quantities of their raw materials and finished products. Moreover, along the process line, there is a need to know how much material is present so process parameters can be adjusted accordingly. Load cells are used on industrial equipment such as hoppers, silos, tanks, conveyors, packaging machines, etc.
Popular equipment that uses load cells under this category is the universal testing machine. Laboratory scales also use load cells with very high precision. However, other force transducer principles are used other than the strain gauge.
Output signals from load cells can be used as feedback signals by process lines for automation. Load cells are used for automatic packaging, distribution, and sorting.
Load cells are also used in truck platforms, weighbridges, cranes, railways, etc. Load cells in this category are mainly used for measuring goods loaded onto trucks and containers.
The best way to ensure the proper performance of a load cell is to follow the manufacturer's installation guide. All manufacturers are available to supply guidance and perspectives regarding the use of their load cells in a project.
The correct frame and fixture are one of the most critical factors related to load cell installation. They maximize stiffness while minimizing weight and costs. The frame should be capable of supporting the measuring device and rigid enough to be able to withstand deformation and flexing.
Several factors that can cause vibrations that affect the frame such as compressors, pumps, actuators, and engines. In certain areas, seismic activity can interfere with measurements. Having the frame set on a hard flat surface can significantly reduce the effects of vibrations.
The frame should be designed to allow for thermal expansion and contraction clearance, which can damage the load cell and its frame.
The load cell frame should be designed to limit that its rotation and movement. This will prevent damage to the hardware of the frame.
When the frame is assembled, it should be done out of the presence of the load cell since stray currents from welding can damage it.
All loads and forces should be sent through the load cell. If they are not, the measuring system will not accumulate correct readings. The axial direction is marked on the load cell and is perpendicular to the loading surface.
Force sensors are transducers that transform mechanical input forces like weight, tension, compression, torque, strain, stress, or pressure into an electrical output signal whose value can be used to...
A load pin is a sensor utilized to measure force or weight in various research, control, measurement and testing applications. The load pin force sensor converts a force into an electrical signal. The load pins provide...
A strain gauge, or strain gage, is a sensing device used for measuring strain experienced by an object. It is made from a long, thin piece of conductor bonded to an elastic backing material called a carrier...
At the heart of every weighing device is a sensor called a load cell. When an item is put on a load cell, it senses the force of the gravitational pull of the weight, which an electronic circuit processes to display...
A platform scale is a scale that measures the weight of objects loaded on a flat platform. The function of the platform is to transmit the weight of the object to the internal measuring device and to support the object during weighing...