Force Sensors
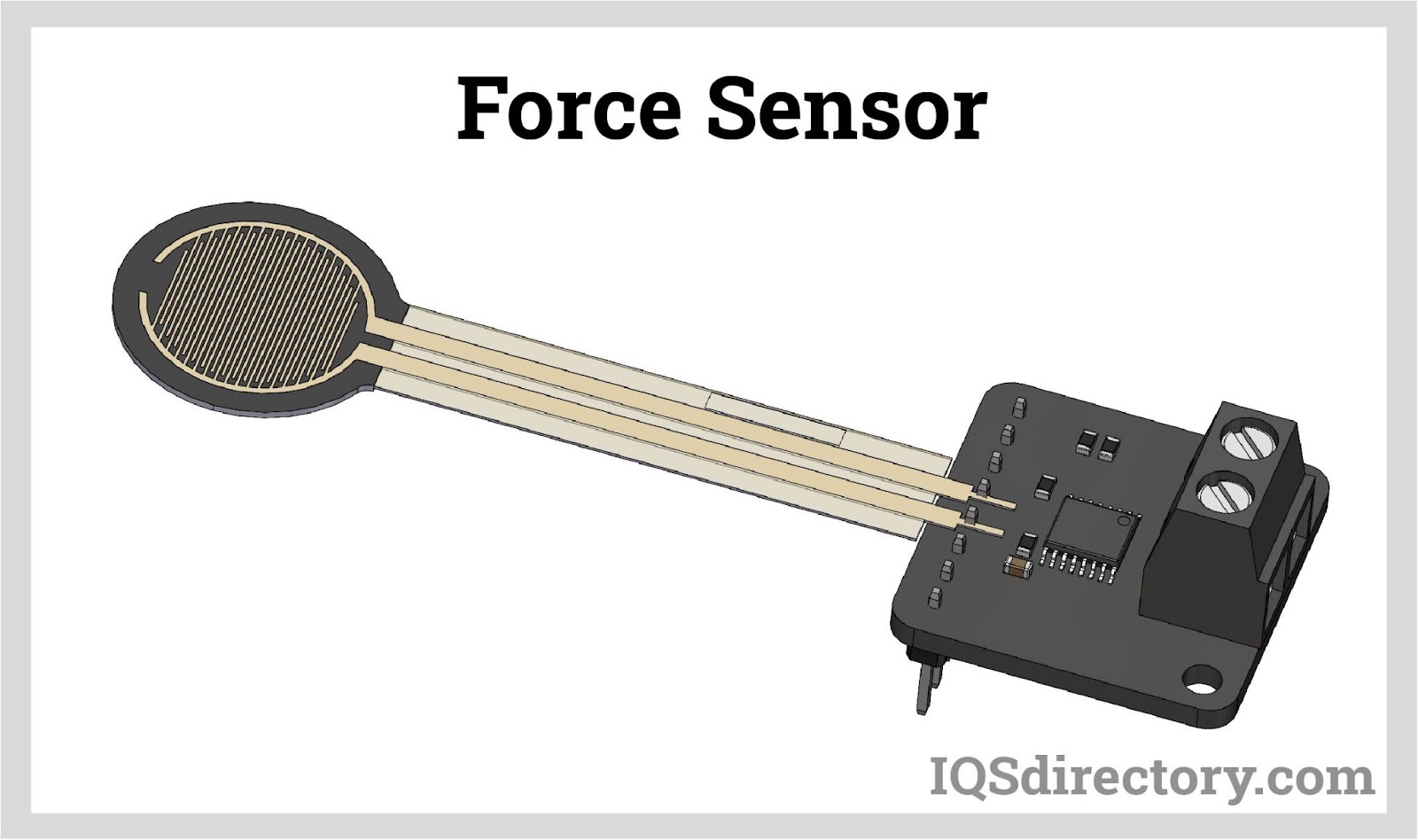
Force sensors are transducers that transform mechanical input forces like weight, tension, compression, torque, strain, stress, or pressure into an electrical output signal whose value can be used to...
Please fill out the following form to submit a Request for Quote to any of the following companies listed on
This Article takes an In-depth look at Load Cells
You will learn more about topics such as:
A load cell is a transducer for converting tensile, tension, compression, pressure, and torque into electrical signals or output. When an item is put on a load cell, it senses the force of the gravitational pull of the weight and an electronic circuit processes it to be displayed as data. Load cells are highly accurate mechanical transducers used to provide measurements and readings.
A force transducer is a term that describes a mechanism for converting force into electrical digital readouts that can be measured and standardized. An increase in the force that is applied to a transducer or load cell creates a corresponding increase in the electrical signal.
Load cells are precision measurement instruments that are commonly used to measure weight. The accuracy and conciseness of load cells makes them capable of measuring a needle’s weight or a drilling machine.
The world standard for measuring weight is in kilograms (kg). Load cells use this standard for measuring and also use newtons (N), which is the force a mass exerts at average gravity. One kilogram equals 9.8 N. Load cell measurements can be displayed in newtons (N), meganewtons (MN), or kilonewtons (KN) to provide the most accurate measurements.
Load cells measure weight in the inner workings of a mechanism. They have a spring, made of steel or aluminum, with a strain gauge. The spring is very sturdy but minimally elastic and responds to every load regardless of how small.
Strain gauges are very small and measure the strain of an object by converting internal deformation into an electrical signal that precisely measures the weight, force, tension, or strain. The sensing element can also be piezoelectric sensors that are electroacoustic transducers that convert electrical charges from different materials. With a strain gauge, an electrical conductor is attached to a film. When the film is pulled, it gets longer and gets shorter when it contracts. The changes in elongation and contraction create resistance in the conductor. As the film lengthens, the strain increases resistance. When the film contracts, resistance lessens. The resistance is what a load cell converts into digital readings.
The types of load cell outputs include analog voltage, current, frequency, switch or alarm, serial, and parallel. Basic designs of load cells have four gauges, while complex load cells, such as Wheatstone bridges, can have up to thirty gauges for measuring circuits. The more gauges a load cell has, the more sensitive its measurements are.
When determining the capacity of a load cell, manufacturers examine force value, the dynamics of the system, the effects of placing the transducer in the force path, and the maximum extraneous loads that the load cell can handle.
For a load cell to perform properly, all loads or forces should be sent directly through it. The issue of directionality is crucial to receiving proper and precise readings. Physical constraints include size, mounting or frame, the level of accuracy, vibrations, and environmental conditions. Assessing these factors ensures that a load cell will perform properly.
There are four accuracy classes for load cells, which are A, B, C, and D with class A being the most accurate, having the highest number of verification intervals in their maximum range and class D being the lowest. The International Organization of Legal Metrology (OIML) and the United States Department of Commerce’s National Institute of Standards and Technology (NIST) established load cell classifications and common load cell symbols.
Using the standardized symbols, the measuring ranges for load cells are expressed as:
The OIML requires specific information placed on certified load cells to identify their capacity, accuracy class, application, temperature, and humidity rating.
Load cells can be categorized by their output signal or their method for detecting weight. In all cases, load cells are methods for measuring mechanical force and turning the measurements into digital values to be read and recorded.
Hydraulic load cells measure weight based on the change in pressure placed on an internal fluid. With a diaphragm hydraulic force sensor, the load acts on a loading head that causes a piston to compress fluid in a confined elastomeric diaphragm chamber. As the force increases, pressure on the fluid rises. The output is linear and unaffected by the amount of fluid or the fluid’s temperature.
Pneumatic load cells operate on a force balance principle and use multiple dampener chambers that provide highly accurate readings. They have an elastic diaphragm that is attached to a platform surface. When an object is placed on the load cell, pressurized air or gas balances its weight. The air needed to balance the weight determines the weight of the object.
Pneumatic load cells are used in industries where small weights are measured and cleanliness and safety are important. They are explosion proof, unaffected by changes in temperature, and do not have any fluids that would contaminate a process if the diaphragm of the load cell ruptured.
Strain gauge Load Cells are the most common type of load cell with a capacity rating between 5 N to more than 50 MN. They have high-res digital indicators with ideal force transfer standards. Strain gauge load cells are transducers that change electrical resistance when under stress or strain with the resistance proportional to the strain placed on the cell. The readings from a strain gauge load cell are linear and can be converted to force and weight.
Canister load cells are compact and cost effective load cells used for single and multiple weighing applications. As with many load cells, canister load cells are hermetically sealed and water resistant. Their heavy duty design is able to withstand harsh inhospitable environments. Canister load cells are ideal for axial compression applications and can measure a variety of capacities such as tanks, hoppers, and vehicles.
Compression load cells have a strain gauge to measure pushing force along a single axis, which is denoted as a negative force. They are perfect for applications with limited space and have excellent long-term stability.
Tension load cells have a strain gauge to measure pulling apart or positive force along a single axis.
Force sensors use strain gauges to test push-pull and measure flow. They are similar to "load cells" but measure loads in all directions. Earth's gravitational force is not relevant to how they are installed.
Pressure sensors are transducers that are similar to load cells that measure pressure, applied force, and strain in gas pressure, altitude, and liquid pressure. Their sensors are often piezoelectric.
Piezoelectric crystal force transducers are used for measuring crystalline materials. When a force is applied to a crystalline material, an electrical charge is generated. A piezoelectric force transducer, with its charge amplifier, measures the electrical charge and converts the measurement into a digital signal.
Miniature load cells are compression load cells designed to work with high capacity loads where there is minimal space. They can be miniature or subminiature with a diameter of 51 mm or two inches. Their small size and diameter make them ideal for test benches, industrial weighing, and prototypes. Miniature load cells have twist lock connectors and cable connections with metric configurations ranging from 0 to 100 N to 0 to 50,000 N.
Also known as thru-hole load cells, measure compressive forces and are called donut load cells because of their shape. They are smooth and round with a hole in the middle for parts or bolts and are used in oil and gas pumps.
Have a straight block of material fixed on one end with loaded material on the other. Beam load cells, known as bending load cells, are used for industrial weighing, including industrial floor scales and tank, silo, and onboard vehicle weighing. Bending beam load cells are low capacity load cells made of aluminum alloys with a capacity of 1 to 500 kg.
Capacitive load cells use capacitance, the ability to store a charge, as a measuring method. They have two flat parallel plates. When current is applied to the plates, it is stored between the plates. The amount of charge that is stored, capacitance, determines how large the distance is between the plates. When a load is placed on the plates, the distance between the plates shrinks, which can be calculated into weight.
There are two types of capacitive load cells, which are low and mid.
Low capacity transducers are miniature transducers used in medical testing equipment, wind tunnel sensors, and weight counting machines. They are limited to measuring weights between 0.9 ounces and 150 pounds, making them suitable for residential and retail machines.
Mid capacity transducers can accurately measure weights between 200 to 20,000 pounds and are ideal for industrial and manufacturing applications. Common uses are industrial scales, truck and truck weighing, bolt force measurement machines, and platform scales.
Micro load cells are resistive load cells that use the principle of zero piezo-resistivity. When a load, force, or stress is applied to the sensor, the resistance changes, which causes the output voltage to change because the input voltage has changed.
Multi-axis load cells are designed and manufactured to measure a multitude of forces simultaneously using a single load cell. They provide multiple bridges that precisely measure force from one direction with little or no cross-talk from other forces or moments.
High capacity load cells can measure extreme loads such as the roof on a mine and the thrust force of a rocket. They are integrated into machines, systems, and instruments and are small, lightweight, and compact. High capacity load cells are custom designed to fit the requirements of each individual application and may need to be inserted into an existing mechanism.
Specialty transducers are used underwater or in outer space. They can measure compression, tension, pressure, capacity, and much more.
Pin load cells is made with load measuring pins, or load pins, that sense applied force using strain gauges installed in a small bore that runs through the center of the load cell. They are used on anchors, shackles, sheaves, bearing blocks, and pivots. They work well underwater because the pin is protected, and the load cell is made of cable and stainless steel with hermetically sealed end caps.
Pancake load cells can be used for both tension and compression measurements in materials and component fatigue testing as well as axial force measurements, where a high accuracy, low-profile device is needed. They have female threads through their center and several holes around the outer ring for mounting purposes. Pancake load cells can measure from 50 lbs up to one million lbs.
Dynamometer load cells or dynos, measure force, torque, and power. A dyno, combined with load cell sensing technology, creates a dyno load cell, which is used to measure engine power output. They are rather expensive and only used when absolutely necessary.
Single point load cells have only one operating load cell and are used in individual device applications, such as supermarket scales.
S Beam load cells are bending beam load cells used for weighing applications under 50 lb. or 22 kg. They have a metal spring element that deforms when a force or weight is placed on the load cell. The strain gauge in the load measures the fractional change in the length of the deformation. S beam load cells are used in scales and tension applications.
S beam load cells are very popular due to their precision, low price, and ease of installation. They are designed for inline applications and are sensitive to outside loads and torque. S beam load cells must be centered to the load and have proper directionality.
Multi axis load cells are capable of measuring tension, compression, and torque in all directions. They have multiple strain gauge bridges to measure forces and torque in one direction with little to no interference from forces applied in other directions. Multi axis load cells save space in assembly and installation time.
The Wheatstone bridge was developed during the first industrial revolution by Charles Wheatstone, who took the initial design by Samuel Hunter Christie and perfected it. In essence, a Wheatstone bridge is an electrical circuit used to measure or compare the resistance of a resistor by creating a balance between the two legs of the bridge. The bridge consists of four arms that form a quadrilateral with points A, B, C, and D.
There are different bridge configurations with the most basic design having two known resistance, one variable resistance, and one of unknown resistance. Included in the circuit of the bridge are electromotive force (EMF) and a galvanometer. The galvanometer is connected to arms B and D while the EMF is connected to A and C.
The Wheatstone bridge principle is based on the idea of null deflection. When the ratio of resistances in the arms is equal, there isn't any current flow. If zero current passes through the galvanometer, the bridge is in a balanced condition, and the voltage difference between B and D is zero.
Wheatstone bridges are more accurate than ammeters and voltmeters and offer more precise results. They can measure temperature variations, strain and pressure, and variations in incident light.
The output from a load cell is in so many millivolts per volt output signal (mV/V), which is an excitation signal produced by the strain gauge. The excitation voltage, strain gauge resistance in each leg, and bridge resistance are major factors in a load cell’s readings. The difference between analog and digital load cells is how the Wheatstone output signal is processed.
Analog load cells use an ADC so that the radio frequency identification (RFID) chip can send the collected information wirelessly to the reader. In order to send their readings, they require an extra electrical circuit. Readings are taken from one cell in the Wheatstone bridge instead of all of the cells. Analog load cells provide continuous information in real time.
The strain gauge on a load cell begins with analog electrical voltage. In a digital load cell, the signals are changed to digital signals. Two to six volts of energy are required for this process, which makes digital load cells stronger than analog ones. The data, in a digital load cell, is sent from each cell in the Wheatstone bridge and uses a binary language that is safe from outside interference, electromagnetism, and temperature variations.
Digital load cells take bits and pieces of information multiple times per second accurately recording measurements from hundreds of loads in seconds. It is for this reason that digital load cells are required for complex and intricate applications.
Ingress protection is an international standard that was developed by the International Electrotechnical Commission (ITC) under its standard 60529 and is a rating system regarding the amount of protection a load cell has against dust, dirt, solid objects, and liquids. The rating system consists of two IP numbers with the first number being the rating for solids and the second number being the rating for liquids. Solids are rated from zero to six while liquids are rated from zero to eight. In both cases, the higher number is the best rating or represents total protection.
The chart below outlines each of the different ratings and their meanings. The IP rating system is a general rule that load cell manufacturers adhere to in order to identify the quality and seal of their products.
Ingress Protection Rating Scale | |||
---|---|---|---|
1st Numeral | Degree of Protection | 2nd Numeral | Degree of Protection |
0 | No Protection At All Against Solid Objects | 0 | No Protection At All Against The Ingress Of Water |
1 | Protection Against Solid Objects Greater Than 50mm In Diameter | 1 | Protected Against Fallling Water Drops |
2 | Protection Against Solid Objects Greater Than 12.5mm In Diameter | 2 | Protected Against Fallling Water Drops At An Angle Of Up To 15° |
3 | Protection Against Solid Objects Greater Than 2.5mm In Diameter | 3 | Protected Against Sprayed Water Drops At An Angle Of Up To 60° |
4 | Protection Against Solid Objects Greater Than 1.0mm In Diameter | 4 | Protected Against The Splashing of Water From Any Direction |
5 | Protected Against The Ingress Of Dust In Such An Amount That It Will Not Interfere With The Operation Of The Equipment | 5 | Protected Against Water Jets From Any Direction |
6 | Total Protection Against The Ingress Of Any Dust | 6 | Protected Against Powerful Water Jets From Any Direction |
7 | Protected Against The Ingress Of Water When Temorary Immersed Of Between 0.15 m And 1 m | ||
8 | Prtected Against The Ingrss Of Water When Continuously Immersed To A Specified Depth |
Hermetic sealing is a process for creating an airtight seal and is done with plastics, epoxy resins, glass, metals, and ceramics. The first hermetic seal was an airtight glass tube referred to as the seal of Hermes, a messenger for the Greek gods. Hermetically sealed load cells are exceptionally reliable and durable. Aside from providing protection, hermetic sealing significantly extends the life of a load cell and removes the need to clean them.
As technology has grown and evolved, manufacturing and production have developed wider width machines in order to process a broader range of materials, resulting in a greater emphasis on tension control. Without accurate controls, distortions, errors, and flaws can appear in final products causing costly downtime.
In order to control and monitor tension and application weight, there has to be a precise, accurate, and constant measurement of production processes. These oversight devices and regulating systems must be placed in the production process and be preset with maximum and minimum levels.
Load cells are strategically placed in processes to take sequential measurements and convert their readings into electrical signals. The quality of those signals provides essential data regarding stability and the effectiveness of a process. The demands on production requirements are becoming greater, making load cells an essential inline component.
Before installing a load cell, it is important to test it using a multimeter and voltage source. To measure the resistance of a load cell’s input and output leads, the multimeter should be set at Ohms. The measurement values should be compared to the load cell’s calibration certificate to see how closely they match. Additionally, the load cell’s accuracy should be checked by measuring its millivolts signal from the input leads.
A digital multimeter is used to check a load cell’s resistance. It is connected between the positive and negative signal wires of the load cell. The output should be equal to the load cell’s datasheet. The test for input resistance is completed by checking the positive excitation wire and the negative excitation wire, which should be equal.
There are several reasons for fluctuations in load cell readings. Physical damage includes shock loading, broken cables, short circuits, and long term overloading. As with all types of devices, environmental conditions such as temperature variances, moisture, water ingress in a poorly sealed load cell, and corrosion can cause a load cell to provide flawed and erroneous readings.
The initial method for checking for fluctuations in a load cell is to inspect it for exterior damage. Such a visual inspection can provide a clue to the source of any fluctuations. The next step is to perform a zero balance check to see if the strain gauge has been deformed or damaged. In load cells that are not hermetically sealed, it is important to see if the insulation has been damaged or breached.
Once all exterior factors such as physical and environmental damage have been eliminated, the next step is to check for a short circuit in the load cell. A bridge resistance check is used for this test and will indicate if there is a short circuit.
A special condition known as zero drift is when the measurements of a load cell change radically under no load conditions. This can also happen when a load is present. There are numerous reasons for zero drift, which include mechanical errors, fluctuations in excitation voltage, and variations in temperature. To find the cause of zero drift, it is necessary to examine the entire system.
A key factor in a load cell's performance is its orientation. When improperly placed, load cells can give negative and inaccurate readings. The most obvious reason for this phenomenon is placing the load cell upside down, which can easily be prevented by examining the load cell’s arrow indicating its directionality. A tension load cell can be installed upside down and will supply erroneous and inaccurate readings.
It must always be kept in mind that weighing systems are delicate precision instruments that must be handled with care. If it is necessary to move them, all measures must be taken to avoid vibrations during transit. Load cells that are part of a greater system should be removed from the system and substituted with a placeholder until the new location is reached.
The accuracy class of a load is an indicator of its maximum capacity since the absolute measurement error is proportional to the load cell's maximum capacity. In accordance with the OIML and NIST, every load cell has a rated capacity, which is clearly indicated on its label. Placing loads on a load cell beyond its rated value overloads it and causes significant damage.
The first signs of overload damage are the types of readings from a load cell, which are inconsistent. When a load is removed, the load cell may not return to zero or there can be extremely dramatic changes in zero balance.
It may be assumed that simply placing weight beyond the capacity of a load cell is what causes overload issues. The causes of overload damage stretch beyond this obvious reason. In many cases, overloading can be caused by dropping an acceptable load onto the load cell system, creating an extreme, significant, and rapid change in the degree of weight in a very short time.
Although overload can be a significant problem, under certain conditions, load cells can endure and withstand overloads when they happen seldom or infrequently. Constant overloads are similar to continual impacts and cause permanent damage.
Overload problems are common in load cells with low maximum capacities and happen more often than is found in load cells with high capacities. Load cells with capacities under 50 kg can be damaged by small items falling on them such as light weight boxes or tools.
Since load cells are an important part of processes and operations, various types of protections are available to prevent load cell damage from overloads and are designed into load cells by engineers. Mechanical stops can be inserted into the mechanism of a load cell such that it limits the travel distance of a load. The deflection of the load cell is limited by a threaded screw, which is set at the load cell’s maximum capacity range.
Pretensioned springs are another form of overload protection. If the maximum load capacity is exceeded, a spring is compressed and applies force to serve as a mechanical stop. Additionally, the gap width on pretensioned springs is significantly wider, which makes setting the allowed load simpler and more reliable. Pretensioned springs also are excellent protection against pulse or dropped loads.
Load cells help measure physical quantity or mass and convert force or energy into another form, such as force, light, torque, or motion. They are used in mechanical testing, system monitoring, and as components in industrial scales. There are many common applications that use load cells, such as scales in the home and measuring devices for heavy industries.
Industries in which load cells are used include:
Load cells are part of security systems, electrical weighing scales, personal scales, thermometers, machines in the defense sector, industrial automation, submarine pressure sensing, and material testing.
Force sensors are transducers that transform mechanical input forces like weight, tension, compression, torque, strain, stress, or pressure into an electrical output signal whose value can be used to...
A load cell is a transducer which converts mechanical energy (tensile and compressive forces) into electrical signals. There are different transducer operating principles that can be utilized to convert forces...
A load pin is a sensor utilized to measure force or weight in various research, control, measurement and testing applications. The load pin force sensor converts a force into an electrical signal. The load pins provide...
A strain gauge, or strain gage, is a sensing device used for measuring strain experienced by an object. It is made from a long, thin piece of conductor bonded to an elastic backing material called a carrier...
A platform scale is a scale that measures the weight of objects loaded on a flat platform. The function of the platform is to transmit the weight of the object to the internal measuring device and to support the object during weighing...