Belt Conveyors
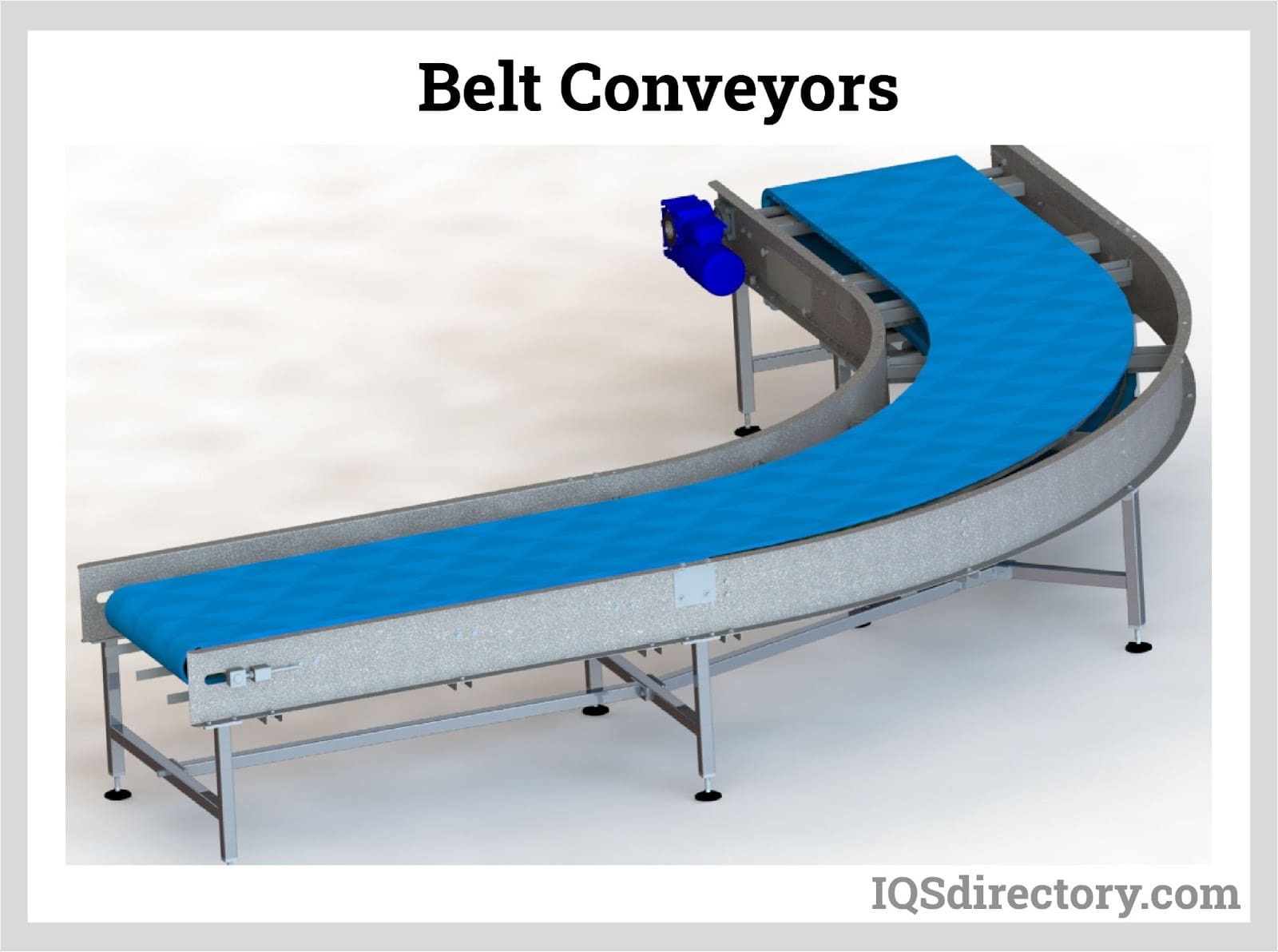
A central part of industrial or manufacturing operations is the supply chain that supports production with raw materials and moves products to customers. Every type of machine, implement, part, or component passes through and is handled by the supply chain. At the center of the supply chain is material handling, which is a vast network of specialists and equipment that ensure proper placement of parts and oversee inventory control.
At the heart of material handling operations is the equipment used to move and transport goods to consumers or production. The proper selection of equipment is critical to the efficient operation of the supply chain and material handling process. The correct types of equipment influence all aspects of a company‘s processes from the factors related to production to profit margins.
Material handling equipment is broken into categories depending on its function in relation to its position in the supply chain. The various functions include transportation, positioning, load formation, and retrieval. In modern technological material handling, various forms of highly engineered and well-designed software systems are included as material handling tools.
The category of transportation, in material handling, includes a wide range of tools and equipment that are designed for the efficient movement of goods, supplies, and materials. Included in this group are hoists, cranes, and conveyors that transport materials inside a facility between processing applications, production areas, and packing or assembly locations. These processes are also facilitated by forklifts, dollies, hand trucks, and pallet jacks that have more direct contact with material movement.
The success of an assembly or manufacturing process depends a great deal on how rapidly raw materials are fed to the processing location. The method that is used is determined by the product being produced and where the required component will need to be delivered. Modern manufacturing relies on technological devices such as automated robotic techniques and various forms of feeders that are engineered to perfectly position components for insertion into the product.
When people define or think of material handling, they usually envision the shipping and receiving department where materials are received and prepared for shipping. This aspect of material handling is one of the more crucial parts and uses a variety of tools, equipment, and machines that streamline and simplify various aspects of the process.
A necessary part of shipping and handling are side-loaders, pallet trucks, walkie stackers, order pickers and locators, and platform trucks such as dollies or hand trucks. Movable roller conveyors, designed to be flexibly located and positioned, are used for loading and unloading of trucks.
A specialized form of material handling is the process of handling bulk materials that requires equipment designed to move chips, cereals, gravel, sand, and other types of granular or powdered substances. Each form of bulk material handling equipment is specifically designed to handle a certain type of material and includes stackers, hoppers, grain and bucket elevators, belt and screw conveyors, and rotary car dumpers.
Every manufacturing, industrial, and commercial operation has a method for storing its raw materials and keeping a close watch on what is on hand and what is required. A central part of storage is warehousing, which is a closely managed and supervised part of a company‘s assets.
Warehousing includes a well-defined and organized process for material placement and retrieval. The placement process includes the positioning of materials in bins, on shelves, and in cabinets with labels and precisely defined categorizations. Of the many material handling functions, warehousing is the most difficult and requires planning and preparation using the right tools to fit the items to be stored.
If all of the other factors for warehousing are properly in place, then the retrieval of the stored items by forklift, pallet jack, dolly, or hand cart can easily be achieved. Modern methods of warehousing use sophisticated computer software to locate and allocate inventory for disbursement.
Though material handling may seem like a simple method for collecting, storing, and retrieving goods, in actuality, it is a complex, complicated, and well-organized automated process that uses specially designed equipment to ensure the smooth and flawless movement of a company‘s assets.
Bulk material equipment and systems are manufactured according to the task that each unit is supposed to accomplish, but most systems incorporate the same general components and features. A full system generally features:
An unloading station. The system must have an access point where materials can be discharged into the system. This portion of the system can take many forms, ranging from railcar unloading stations to a simple bag dumping station.
A conveying system. Most often bulk material handling systems utilize pneumatic conveyors, but other systems use screw conveyors, bucket elevators, or drag chain conveyors. Many systems use a combination of two or more of these different conveyors.
Material storage equipment. From huge storage silos to small bins or hoppers, a bulk material handling system should have a location where materials are stored until they are needed for processing.
Batching equipment. In order to utilize bulk materials efficiently, batching equipment is used to accurately dispense bulk materials for processing and for packaging.
A filling or packaging station. Once the bulk materials have been processed, the system needs a method for offloading the final product for packaging, shipment, or sale.
While practically all bulk material systems incorporate these main kinds of equipment, each system may use slightly different variations of the equipment and incorporate additional components to fit the specific needs of the application at hand. For example, in a food processing facility, a bulk material handling system would most likely use large storage silos instead of smaller storage bins, since they often handle such large quantities of grains, powders, and other materials.
This sort of facility would also include mixing equipment in addition to the equipment above to thoroughly combine ingredients. Additionally, some systems are designed to better transport and handle materials comprised of very small particles, while others efficiently convey larger granules. These systems can be highly customized to fit the specific requirements of a given task or process.
There are a number of considerations that have to be made when bulk material equipment or systems are being installed. Not all equipment is made for use with all types of material, and the consistency of the material will greatly affect the quality of the final product. Some factors that should be considered during equipment selection are:
• Bulk density • Average particle size • Particle properties • Environmental effects • Material base
Experts recommend conducting extensive material tests before purchasing equipment so that the necessary processing qualities can be understood. For example, some particle densities actually change at different stages of the material handling process, so it should not be assumed that each piece of equipment will function efficiently at the same density level. Pneumatic conveyors are the backbone of most bulk material handling systems, so these considerations are incredibly important for determining which kind of pneumatic conveyor will transport specific bulk solids most effectively. Abrasive materials cannot be transported in the same way that a sticky material would be transported, for example. Some materials may transport more effectively using dense phase conveying, while others are effectively transported with dilute phase conveying methods. While these considerations are most vital for conveying systems, they do also affect other handling components, but to a lesser extent. Particle size and cohesion affect how materials can be combined together and can affect how the material is dispensed. Which means that material properties should also be considered for batching equipment, mixers, and material feeders.
Granulated and dry bulk materials such as grain, powdered chemicals, sugar, flour and
dry cereal require specialized conveying, mixing and processing systems. These bulk material handling and powder bulk handling systems are designed for the integrated
industrial mixing, conveying, measuring and packaging of delicate, friable, sticky or free-flowing solids. Unlike parts, equipment and other products which are conveyed through
fabrication, assembly and packaging by belt and chain conveyors, bulk solids and powdered solids require a closed screw conveyor, flexible screw conveyor or pneumatic conveyor system
which prevents caking, packing, liquefying, contamination and agglomeration. Industrial mixers, dryers, pulverizers and vibratory feeders are integrated into bulk material handling systems
for complete processing.
Belt conveyors are a type of conveyor system, which are systems that move, or convey, different types of materials from one point to another and/or through various stages of processing. Conveyor systems in general use a number of different means to move goods and materials. These different means include floor chain conveyors, overhead chain conveyors and more. Belt conveyors, which are the most widely used type of conveyor system, use a wide polymer or rubber belt wrapped around two or more uni-directional pulleys that rotate it, in order to convey goods and parts of all shapes and sizes. They are used in a variety of industries, including industrial manufacturing, retail manufacturing, pharmaceuticals, food and beverage processing, defense, paper, aerospace and automotive.
Learn more about belt conveyors.
Bulk bag equipment is a type of process equipment used to hold and transport bulk bags.
Bulk bags are industrial fabric containers used to store and transport dry, flowable materials. Examples include: plastic granules, grain, fertilizer and sand.
Bulk bag handling is an important part of many applications, including some pneumatic conveying projects. Bulk bag equipment can be found in a wide range of facilities, including: greenhouses, commercial agriculture facilities, commercial food distribution facilities, pharmaceutical production centers, manufacturing facilities and more. Learn more about bulk bag equipments.
The term "industrial dryers" refers in general to dryers used for manufacturing, industrial or large-scale commercial purposes.
Industrial dryers can used to dry clothes and linens, as they are laundromats and hotels, but their range of applications is much wider than that. Rather, they are essential in many different industries including: agriculture, food processing, manufacturing, pharmaceuticals, pollution control, water treatment and paper and pulp. These industries count on industrial dryers to dry materials that come in contact with fertilizers, grains, chemicals, refuse, dairy products, minerals, papers, plastics and more.
Industrial dryers work using three main methods: air drying, infrared drying and spray drying. The first, air drying, is the most common. Air dryers work by bringing materials in direct contact with hot air, so that any moisture evaporates and diffuses into the air. Next, infrared dryers dry solid materials using electromagnetic radiation on a certain part of the wavelength. Finally, spray dryers work using jets of hot steam that cause moisture to flash dry and evaporate.
Industrial dryers come in a wide variety of makes and models. However, many share certain characteristics. For example, they are usually made from stainless steel. Learn more by contacting an industrial dryer manufacturing today.
Industrial dryers are used for removing moisture from substances, products or materials in a business or manufacturing capacity. Industrial dryers are often specialized or custom built for specific applications. They tend to be much larger than dryers found in a home or small business and usually don't dry laundry unless used in a laundromat or hotel.
The term "industrial dryers" is a general reference that applies to dryers no matter what their particular method of drying is: air, infrared or spray drying. Because of the variety, there is no single design or model of industrial dryer, though there are some shared characteristics. Many dryers are made from stainless steel because it is strong, sanitary and corrosion resistant. They are often cylindrical tanks or rectangular boxes with multiple intake and output valves, connections, openings, gauges and controls. Some may be continuous - able to dry a constant flow of materials - and utilize a conveyor belt while others work in batches. The capacity depends on the kind of dryer and the material that will be dried. Certain dryers can dry over 25,000 pounds an hour while others can be built to hold only one cubic foot. Dryers are essential for the pharmaceutical, food processing, manufacturing, agricultural, pollution control, water treatment and paper industries and have multiple functions when working with chemicals, dairy products, fertilizers, grains, minerals, paper, plastics, refuse and more.
Most industrial dryers are bolted or welded together, depending on the importance of the seams, the anticipated product and any motion the dryer will endure. The three main methods of drying encompass a variety of models that carry out the task in different ways. Air dryers are the most common industrial dryers. They bring materials into direct contact with hot air, which causes moisture to evaporate and diffuse into the air, leaving behind a dry product. Flash dryers, freeze dryers, fluid bed dryers and rotary dryers all fit in this category, though their designs vary. Flash dryers use a short, intense burst of heat to dry materials almost instantly while freeze drying uses cold air and vacuums to freeze moisture and sublimate it away. Fluid bed dryers shoot steam up through a perforated plate in order to cause the solid material to behave like a fluid; rotary dryers are large drums that dry products as they turn and tumble the material through the hot air contained inside. Infrared dryers rely on electromagnetic radiation from a certain segment of the wavelength to dry solid materials quickly and without overheating them because the wavelength can be matched to the absorption rate of the product to maximize energy and resources. Spray drying introduces the material to jets of hot steam, which causes the moisture to flash dry and evaporate.
Learn more about dryers.
Mixers and blenders are, just as their name implies, industrial mixing and blending equipment, respectively. Mixers and blenders are used in agriculture, food processing, mining and pharmaceuticals, among others. In these industries, they're used to create products like cosmetics, baking ingredients, fertilizer compounds, pet food and more.
It's important that products achieve a consistency that is up to industry standards. That's why mixers and blenders are equipped with precision speed controls and their internal temperatures and the radial reach of their mix components are carefully regulated.
Mixers and blenders can work with wet material or dry material, depending on their configuration. Those that deal with wet matter must be more powerful because wet materials generally result in heavier substances that still must be mixed at very high speeds. No matter the nature of material with which a machine is working, it must come with a seal that keeps dust and other particles from getting into the facility air. A great asset of mixers is the fact that you can easily remove their components for cleaning. Also, you can equip them with different attachments for unique material batches.
Common mixer/blender types include: auger mixers, high capacity mixers and ribbon blenders.
One of the most common types of mixers in a bulk material handling system is an auger mixer. An auger mixer is a powerful piece of equipment that has the capacity to quickly mix and blend bulk materials into a smooth consistency. Most auger mixers stand vertically in a facility on a sturdy metal frame. The auger is powered by an external electric motor that turns the auger rapidly through the bulk material. Depending on the desired consistency, the auger attachment may be changed. A long auger will create a more even blend throughout the tank, while a short one will produce more fine contents on the bottom. Some auger attachments are built with a diameter that is almost as wide as the diameter of the inside of the tank. Materials are loaded through an opening in the top and then extracted after mixing via a pneumatic conveyor or a discharge door in the bottom of the mixing tank. Most auger mixers are constructed using stainless steel so that they can be thoroughly cleaned between uses. This prevents cross-contamination and material buildup that could be harmful to the equipment or the mixture itself. The head of the auger can be removed for cleaning outside of the tank or to add a different attachment.
The shape of the auger's sharp blades move material on either side of it up the center and then down the walls of the tank. This continual cycling motion is what makes the auger mixer so effective. Some smaller auger mixers actually run horizontally. An access door allows the operator to open the top of the mixer and dump bulk materials in, and then the machine can be turned on to mix materials once the door has been closed. Doors on a horizontal auger mixer are usually made of transparent fiberglass so that the person operating the machine can monitor the change in the material's consistency.
Large bulk material handling systems are built to handle high volumes of bulk material on a daily basis, and these systems need mixers that have a capacity to match their batch sizes. Large bulk handling systems are very costly, so they are most efficient when they can frequently process high volumes around the clock. To mix these batches, industrial facilities use one or several high capacity mixers. A high capacity mixer is usually built with a large central auger that churns material, much like a regular auger mixer. However, the difference is that the power put out by the auger and the sheer size of the mixing tank itself is much greater. A high capacity mixer looks more like a storage silo, with a hatch at the top to add materials to the tank. After mixing, materials can then be discharged into bulk bags or bins using the door at the bottom of the tank. A pneumatic conveying system can also be fitted to the top or side of the mixer to pull materials out once the batch is mixed. A high capacity mixer for industrial use can be built with well over 1000 cubic feet of capacity. A quality high capacity mixer can process large volumes of material without compromising the consistency and precision of the mixture.
Powerful variable speed motors turn the mixing mechanism and push through heavy materials to evenly blend them. A high degree of control over the exact speed of the mixer enables workers to mix batches with the exact same texture every time. Sensors and instruments attached to the mixer input information to the control unit and display important stats to operators in the facility. This information is used to optimize efficiency and maximize batch output. Performance issues can also quickly be identified and addressed with this information. High capacity mixers are used in industries and applications where high volume production is very important. This includes cosmetics, food processing, pharmaceuticals, and more. If you are handling bulk materials for use in a cosmetic product, for example, you need a large batch all at once otherwise, the cost of the product will be greater than the revenue from the final product. Learn more about mixers.
A ribbon blender is a high-speed mixing unit for bulk material handling facilities. It is similar to an auger mixer, except the unit is usually built with smaller dimensions. The ribbon or auger in the machine is designed in a helical pattern that enables that machine to mix materials homogeneously and completely discharge a batch when the process is complete. Ribbon blenders come in vertical and horizontal mounting options, and the type and size of the machine is chosen based on the materials being processed and the space limitations of the bulk handling facility. The ribbon in the blender is set in a U-shaped trough. The screwing motion caused by the ribbon pulls material through this trough and then lifts it up, slowly forming a pile. After they have been picked up, materials blend by falling together into this pile. Once the blending process is finished, materials can be discharged from the ribbon blender by opening the door on the bottom of the tank. This door is opened using a lever or automated controls. The blender remains on as the door is opened, and materials fall through to a bin below as they are pushed by the ribbon to the center of the tank where the opening is. After the machine has been turned off, the access door can be opened and all of the parts can be cleaned.
Like most bulk material handling equipment, ribbon blenders are often constructed using stainless steel. Not only is this material strong and highly resistant to corrosion, but it is also very easy to clean. In some facilities, cross-contamination of ingredients is a major concern, so machines are all cleaned between batches. Ribbon blenders are used in many industries; from food to pharmaceuticals to cosmetics. Because of their balanced blending abilities and consistent mixing quality, ribbon blenders are an excellent choice for many bulk material handling facilities. The range of sizes created by blender manufacturers makes it possible for both small and large plants to utilize the efficiency of a ribbon blender in whatever space they have available. Learn more about blenders.
View a full list of Mixing & Blending Equipment Manufacturers
Palletizers are materials handling machines used for the loading and unloading of pallets before and after shipping as well as during storage.
Pallet loads are frequently used for mass shipping and distribution as a convenient means of consolidating many smaller units into one larger, more easily handled unit.
Many manufacturing and distribution plants use automated palletizers, palletizing systems and robotic palletizers for pallet loading and unloading. Automated conveyor palletizers may be low-level palletizers, which load packaged units from a floor level, or they may be high level palletizers, which move packaged units on an elevated platform. Palletizing Machines may be designed to handle a single type of product, such as bag palletizers, case palletizers, drum palletizers and bottle palletizers, or they may handle several different types of packages. Large-scale distribution centers and manufacturing facilities that handle incoming shipments often use depalletizers to unload packaged units, and palletizing equipment accessories such as pallet dispensers and load transfer stations are used to assist in managing both pallets and loads. Palletizers can also be referred to as case pickers; the terms "case picking" and "palletizing" are used interchangeably by some professionals, though case picking often refers strictly to the picking of individual products by warehouse staff in distribution operations. Learn more about palletizers.
A pneumatic conveying system involves the transfer of any bulk material of any kind from one place to another.
This process may involve the use of gas flow as the conveying medium but air is one of the most frequently used. A properly designed conveying system should be efficient, practical, and economical for transporting bulk materials from one point to another or to multiple destinations.
Pneumatic conveying equipment is a critical system and is mainly applied for the transfer of dry bulk materials and powder materials along a pipeline which is fully enclosed. The force used in that movement is as an effect of the combination of pressure differential and the flow of various gases in the tubes such as nitrogen. The system‘s essential elements include a feeder, an air mover, a dust collection system, a termination vessel and a belt conveyor, among other components.
It is also critical to notice that the system transfers material like cement, flour, sand, minerals, and food products among other substances. It is a requirement that granular materials are to be dry. Materials in paste or slurry are unsuitable and may cause complications in the system. Learn more about pneumatic conveyors.
Screw conveyor systems are mechanisms responsible for rotating or moving a variety of fluid, solid, and granulated materials from one process to the next.
In other words, they transfer materials.
Screw conveyors are also known as auger conveyors, helix conveyors, worm conveyors or flexible screw conveyors. Learn more about screw conveyors.
Vibratory feeders, also known as vibratory conveyors or vibratory bowl feeders, are bulk handling equipment used to to convey and sort materials. They consist of a vibrating unit, a bowl and a variable amplitude control box. Usually, they are also connected to a conveyor track. They are a favorite for use with sticky or delicate materials because they can convey them with liquefying them or causing them damage. Vibratory feeders convey and sort materials using vibrations and movement. The vibrations comes from the drive, which is installed underneath the bowl.
Vibratory feeders are generally simple in design and easy to run for extended periods of time. However, they do vary greatly from model to model. For example, some are built with troughs that sift material, while others have vibrating or trommel screens to convey and sort bulk products simultaneously.
Vibratory feeders are generally divided into two main categories: vibratory bowl feeders and vibratory conveyors. Bowl feeders used more for parts than for bulk material. They align products before packaging so that they are discharged into the package in the right positions. Vibratory conveyors, on the other hand, are used primarily to feed material from one point to another.
Learn more about vibratory feeders.
Weighing systems and scales are incredibly important to bulk material handling applications in many different industries. These include agriculture, food processing, pharmaceuticals, mining and oil and gas, among others. They are so important because they ensure that bulk material handlers accurately weigh and package their products.
Scales and other weighing systems range greatly in terms of size and configuration. Some are quite small and can measure products down to the gram. Others are large enough to weigh entire loaded pallets or loaded trailers. They weigh loads using a variety of mechanisms, such as load cells, springs, balances or hydraulics. In addition, they may have either digital or analog displays.
Some common scale types include: platform scales, hanging scales and bench scales. Platform scales, also known as floor scales, are level with the floor. Usually, they come with a large platform on which large bulk loads can be weighed. Next, hanging scales, suspend loads in the air. They gauge weight based on the amount of gravitational force a load exerts. Finally, bench scales weigh mostly small and medium sized loads. They stand several inches or a few feet off of the ground, which makes loading and unloading easier. They are portable.
Load cells are used in bulk material handling systems to gauge the weight and force of a load of bulk material. The purpose of this ability is to test mechanical systems and monitor their output during production times. Load cells are particularly important for maintaining the accuracy of the industrial scales that are used to weight bulk products. Compression and tension are the most common force measurements made using load cells. Many load cells are built with an internal strain gauge, a small device that can measure how much strain is put on an object using electrical signals. Force gauges do the same thing but for push-pull testing or measurement of flow.
The flow of liquid or viscous bulk materials can be measured by pressure sensors. This is useful to determine the rate and force of flow through a bulk system for optimization and efficiency purposes. Digital load cells are the most popular and the most easy way to access the information that sensors pick up during operation. In food processing facilities, load cells play an important role in measuring ingredients before they are entered into a mixture. This precision is critical to the on-going quality of a product. Perhaps the most important function of a load cell is to determine the exact weight of loads, like a loaded pallet. When bulk processors ship their goods, they need to know the precise weight for logistics and billing reasons. Load cells provide readings that are accurate within 0.25%, which is extremely precise for applications where a single load may weigh several tons.
So how exactly does a load cell work? A load cell is designed to convert mechanical stress into electrical energy. Information is received in this way and sent to a data collection system in the device. This is then turned into an output or reading that an operator can see as an item is placed on a scale or material runs through a tube. Analog load cells still exists, but they have been largely surpassed by digital load cells because they are more accurate and easier to read. In applications where a load cell is used to shut off equipment, the cell is designed to sound an alarm when a predetermined event or set of criteria is observed. Load cells can be fitted with multiple gauges. The more gauges, the more sensitive the cell will be to changes and the more accurate its measurements will be. Necessary accuracy, type of force, and response time are among the most important factors that must be considered when a cell is being designed for an application.
Load cells are used in equipment at bulk material handling facilities in mining, food processing, pharmaceuticals, oil & gas, agriculture, and other industries. Although a load cell is very small, it has a huge impact on the efficiency and cost-effectiveness of major operations. Some manufacturers specialize in load cell production and work with industry experts to create devices that perform specifically for certain materials or applications. Others are more general and can be used in many different bulk handling capacities. Learn more about load cells.
Bulk material handlers in all industries rely on scales to weigh their products and accurately determine quantities during packaging, before shipping, or before storage in a facility. Many bulk products are sold or distributed based on weight, so it is important that precise information is available. Scales can be small enough to measure tiny objects, but typically in bulk material handling applications, they are at least large enough to weigh a loaded pallet. Some industrial scales are large enough to weigh an entire loaded trailer or shipping container. Scales are made in many different forms, including: bench scales, hanging scales, and platform scales. A bench scale is raised up off of the ground by several inches or a few feet and may even be moved around a facility as needed. The raised stance of the scale makes it easier to load and unload small to medium sized loads. A platform scale or floor scale is level with the floor and typically has a large platform for weighing large bulk loads. A forklift or other vehicle can be used to move the weight directly onto and off of the scale. A hanging scale suspends loads in the air and gauges their weight based on the amount of gravitational force that they exert.
Scales can have either digital or analog readings. While a scale with a meter and a needle that displays the weight of a load may be accurate, it is not as precise or as easy to read as a digital scale. Digital scales show decimals and make it possible to be highly precise during the weighing of bulk products. In any bulk operation, the most important consideration when investing in an industrial scale is the maximum weight that it is able to measure. Scales can range from a capacity of just a few grams to over 80,000 pounds. Knowing the needs of your application and choosing a scale accordingly will prevent technical errors and allow for the accuracy that your system needs. When bulk products are weighed on a scale, they are usually on a pallet or loaded into some kind of container. The weight of the container or pallet itself can be inputted into the scale so that the only material being measured is the bulk material. If distributors are being charged by weight, it is important that a bulk handler does not also charge them for the weight of the container. To determine the weight of a load, scales are built with hydraulics, balances, springs, or load cells. In more complex scales, a combination of these devices is used.
In most industries, scales are subject to regulatory standards that have been established by the National Institute of Science and Technology. These standards ensure worker safety and accuracy for the measurement of bulk goods. In a bulk material handling system, scales can be placed near other equipment and loaded manually by workers, or they can be loaded and unloaded intermittently by automated machines. In these instances, the machines receive information from the scale that tells them when the load has reached the required weight. Bulk material handling systems in agriculture, food processing, pharmaceuticals, and more all use industrial scales to weigh products before they are packaged or shipped. Sometimes it is necessary to use scales to weigh small quantities that are then added to a larger mixture in a processing plant. Again, accuracy is key to maintain consistency and quality across bulk products in applications like these.
Learn more about scales.
Weighing and batching equipment are integrated into bulk material handling systems to ensure that the appropriate quantity of material is utilized, packaged, or shipped. A weigh batching systems can be used to accurately fill containers like bags, drums, or bottles so that each container is filled with the exact same amount of material, or they can be used to ensure that an appropriate amount of materials is added into a batch being mixed. These systems provide accuracy and repeatability in bulk material handling systems. There are several types of weigh batching systems that are used in bulk material handling, and they use what are known as either gain-in-weight or loss-in-weight principles.
With a gain-in-weight batching system, a volumetric feeder is used to feed the material into a weighing hopper. As material is added, the weighing hopper continuously takes weight measurements, and the feeders continue to release material until a set weight is reached within the hopper which triggers a mechanism that signals the feeders to stop. Many applications require that several different materials be added into the batch. In this case, each material is added to the weigh hopper one at a time. Once the set weight for an ingredient is reached that feeder is switched off and the next ingredient feeder is switched on until the next set weight is reached. This process continues until all ingredients have been added. This results in the hopper containing several layers, one for each ingredient since they were added individually. The sensitive automated controls in this weighing system prepare bulk materials for the next stage of the process by carefully controlling the release of substances.
In a loss-in-weight batching system, multiple ingredients are fed into a collection hopper using highly controlled feeders. Each of the ingredient feeders is equipped with a weighing sensor, such as a load cell, to carefully measure the weight of the material within the feeder. As the feeders release material into a hopper, the system tracks how much of the ingredient is released by tracking how much weight was lost in the feeder. This is important in applications where smaller weights are at play and where more exact weight measurements are necessary. Additionally, batch mixing times are reduced down the line because these materials are introduced into the hopper all together instead of one by one, resulting in a blended mixture.
Within these two types of weigh batching systems there is a wide variety of machinery. Machines vary in sizes and can be purchased to reflect the availability of floorspace in a commercial or industrial facility. Because industrial technology has advanced so much in recent years with the development of better digital control and sensors, bulk material weigh batching systems can be more precise than ever before. Full control and display units can be installed in a facility so that operators can monitor efficiency and output. Changes can now be made at the touch of a button, a feature which is especially convenient for suppliers who process high volumes of material for many industries on a daily basis.