RTD Sensors
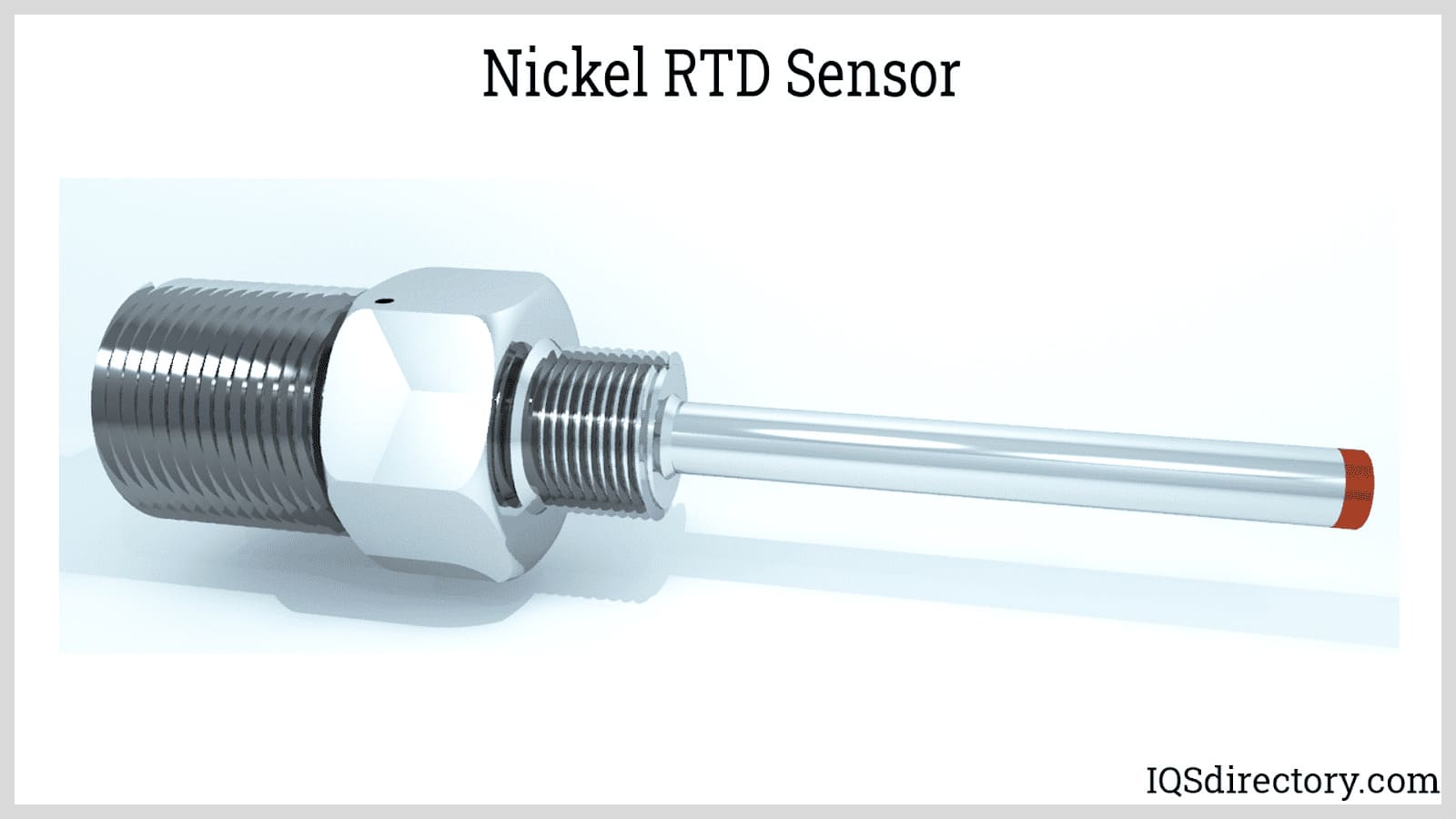
An RTD, resistance temperature detector, is a passive temperature sensing device that operates on the principle that the resistance of a metal changes as the temperature changes. The electrical current that passes through the element...
Please fill out the following form to submit a Request for Quote to any of the following companies listed on
This article will take an in-depth look at temperature sensors.
The article will bring more detail on topics such as:
This chapter will discuss what temperature sensors are, their uses, their components, and how they function.
Temperature sensors are devices that detect and measure coldness and heat and convert it into an electrical signal. Temperature sensors are utilized in our daily lives, be it in the form of domestic water heaters, thermometers, refrigerators, or microwaves. There is a wide range of applications of temperature sensors, including the geotechnical monitoring field.
A temperature sensor can also be defined as a simple instrument that measures the degree of coldness or hotness and then converts it into a readable unit. There are specialized temperature sensors used to measure the temperature of the boreholes, soil, huge concrete dams, or buildings.
Temperature sensors are devices designed for measuring the degree of coolness and hotness in an object. The voltage across the diode determines the working of a temperature meter. The change of temperature varies directly proportional to the diode’s resistance.
The cooler the temperature, the lesser the resistance will be and vice-versa. A measurement of the resistance across the diode is done, and the measurement is converted into units of temperature that are readable and displayed in numeric form over readout units. In the field of geotechnical monitoring, these temperature sensors are utilized in the measuring of internal temperatures of structures such as dams, bridges, power plants.
There are many different types of temperature sensors, but the most common way that is used in their categorization is based on the mode of connection that includes contact and non-contact temperature sensors. Examples of contact sensors include thermistors and thermocouples because their contact with the objects they measure is direct, whereas non-contact type temperature sensors measure the heat source’s radiation.
Such temperature meters are mostly used in hazardous environments such as thermal power plants or nuclear power plants. Temperature sensors are used to measure the hydration heat in mass concrete structures, in the field of geotechnical monitoring. They can also be utilized to monitor the migration of seepage or groundwater.
One area where they are commonly used is in curing concrete since the concrete has to be relatively warm to properly set and cure. The variations of seasons causes expansion or contraction of structures, bringing an overall change to their volume.
The working principle of a temperature sensor is the voltage across the terminals of the diode. If there is an increase in the voltage, the temperature also increases. This is followed by a drop in the voltage between the terminals of the transistor of base and emitter in a diode. There are also temperature sensors that work on the principle of stress change caused by changes in temperature.
In a vibrating wire temperature meter, dissimilar metals have different linear coefficients of expansion. It mainly consists of a magnetic stretched wire of high tensile strength with two ends fixed to any dissimilar metal so that any temperature change will directly affect the tension in the wire and its natural vibration frequency.
The dissimilar metal can be made from aluminum since it has a larger linear expansion coefficient than steel. When the conversion of the temperature signal into frequency occurs, the very same read-out unit that is used for other vibrating wire sensors can also be utilized in the monitoring of temperature also.
The specially built vibrating wire sensor is the one that senses the temperature change and then the temperature change is converted into an electrical signal which is then transmitted to the read out the unit as a frequency.
There are three types of components in temperature sensors. There are essential components of a temperature sensor including thermocouple or extension cables and wires, as well as the sensing elements. The following are examples of components which complete the sensor: insulating beads, connectors, connecting heads, and protecting tubes. There are also associated components that are necessary in the use of sensors like converters and controllers.
The detection circuit must offer an output in a usable format in order to use a temperature sensor in a control or compensation circuit. For analog circuits, usually, the output is resistance. The measurement must be converted to a digital format for processing by an MCU for digital control and compensation. Commonly, this is achieved by reading the measurement as a voltage by means of an analog-to-digital converter.
Semiconductor based sensors have a digital interface that makes communicating the temperature clearer to an MCU that is able to access thermocouples due to their voltage. RTDs and thermistors have the flexibility to provide voltage or resistance with ease. This gives engineers choices as to the methods of connecting the detector to the control or compensation system.
RTDs and thermistors output a variable resistance, which makes integrating them into an analog control or compensation circuit straightforward. If there is a requirement of a voltage output, the resistance can be converted easily to voltage by means of three additional resistors in a Wheatstone bridge configuration as shown in the figure below.
For non-linear sensors like thermocouples and thermistors, the output needs to go through a straightforward linearization. This can be implemented in a circuit that is simple for analog control and compensation. For control and compensation that is digitally based, the CPU can measure the adjusted temperature using a simple lookup table that reflects the temperature/resistance chart that is incorporated in the spec sheet of the sensor.
Engineers have many choices in designing a temperature detection circuit to prevent overheating or implement temperature control and/or compensation functionality. For extreme temperatures, thermocouples are mostly the ideal option. When there is a requirement for the greatest accuracy, platinum RTDs provide high precision. For PCB-based applications where installing an external sensor internally can be difficult, semiconductor-based sensors make the sensing of ambient temperature near sensitive electronics possible.
RTD elements are utilized in the manufacturing of temperature sensors. A resistance element is a component that senses temperature at the heart of a resistance thermometer or an RTD. They can’t be used in their bare form typically, but they may be built into a probe or assembly that enables them to withstand different conditions of their application. Each has a resistance value that is pre-specified at a known temperature which changes in a predictable fashion. In this way, by measuring the element’s resistance, that element’s temperature can be determined from calculations, tables, or instrumentation.
These elements are mass produced by automated equipment, which deposits a layer of platinum onto the ceramic substrate and utilizes photolithography in the etching of an electrical current path that corresponds to the value required in ohms. The elements have a smaller size than that of traditional wire wound elements and as a result have a response time that is fast and are suitable in more applications, while reducing the costs of the user at the same time.
Ceramic elements can be used to make temperature sensors. These elements are wound on either ceramic or glass former, or a helix of platinum wire can be semi-supported within a ceramic tube’s bores. This semi-supported type is capable of providing the widest temperature range of operation and, typically, the best stability. Although there are other usable metals, platinum is the most prevalent and widely used type with either ceramic or glass insulators.
The use of metals, aside from platinum, can lead to linearity at low temperatures and drift, which throws off temperature processing. The error corrections and adjustments necessary with other metals is why platinum is preferred.
Thermometrics can make an addition of lead wires to the elements of a temperature sensor as per specifications. The common additions are 20 AWG, Teflon coated nickel wire.
Glass (quartz) encased elements that are wire wound are available to meet the requirements of a user.
This chapter will discuss the different classes and types of temperature sensors as applied in control and compensation circuits and temperature sensor elements.
Temperature sensors are found in different types, sizes, and shapes. There are two main temperature sensors classes: contact temperature sensors and non-contact temperature sensors.
A few temperature meters are capable of measuring the degree of hotness or coldness in an object by being in direct contact with the object. These types of temperature sensors fall under the class of contact-type sensors. They can be utilized in the detection of liquids, solids, or gasses over a broad range of temperatures.
These types of temperature meters do not measure the temperature of an object while in direct contact; rather, they measure the degree of hotness or coldness from the radiation that is emitted by the heat source.
The contact and non-contact temperature sensors are divided further into the following mentioned types of temperature sensors.
This is known as the resistance thermometer and uses the resistance of the RTD element with temperature to measure the temperature. Different types of materials can be used to make the metal.
The materials include nickel, platinum, and copper. However, platinum is the most accurate and therefore the most expensive.
Thermocouple sensors have two wires made of different metals connected at two points. The voltage between the two wires reflects the change in temperature.
Although their accuracy may be slightly reduced to a degree that is lower than an RTD, they have a temperature range between -328°F to 3182 °F (-200 °C to 1750 °C) and are generally more cost-effective.
Thermocouples are separated into types, with each type being suitable for specific temperature conditions. The various classes of thermocouples are constructed to meet the needs of a specific application.
Thermocouple Types | |||||
---|---|---|---|---|---|
Thermocouple Type | Temperature Range (°C) | ||||
Short Term Use | Continuous Use | Class 1 Tolerance | Class 2 Tolerance | Class 3 Tolerance | |
Type E | -40 to 900 | 0 to 800 | -40 to 800 | -40 to 900 | -40 to 904 |
Type J | -180 to 800 | 0 to 750 | -40 to 750 | -40 to 750 | N/A |
Type K | -180 to 1300 | 0 to 1100 | -40 to 1000 | -40 to 1200 | -180 to 1300 |
Type N | -270 to 1300 | 0 to 1100 | -40 to 1000 | -40 to 1200 | -270 to 1304 |
Type R | -50 to 1700 | 0 to 1600 | 0 to 1600 | 0 to 1600 | N/A |
Type S | -50 to 1750 | 0 to 1600 | 0 to 1600 | 0 to 1600 | N/A |
Type T | -250 to 400 | -185 to 300 | -40 to 350 | -40 to 350 | -250 to 404 |
Type B | 0 to 1820 | 200 to 1700 | N/A | 600 to 1700 | 4 to 1820 |
Uses for Thermocouple Types:
Type E Thermocouples - Type E thermocouples have chromel, a nickel and chromium alloy, and constantan with a temperature range of -330°F to 1600°F (0°C to 870°C) and excellent EMF versus temperature values. They can be used in sub-zero temperatures and are used in inert environments but must be protected in sulfurous environments.
Type J Thermocouples - Type J thermocouples, like type K thermocouples, are a general-purpose thermocouple made of iron and constantan, with the iron leg being positive and the constantan leg being negative. They can be used exposed or unexposed with a protective tube being recommended. Type J thermocouples are used in vacuum, inert, and reducing environments. As with type K thermocouples, type J thermocouples have to be carefully calibrated and do not react well to noise.
Type K Thermocouples - Type K thermocouples are made of Chromel®–Alumel® with small percentages of manganese and silicone. They are a general purpose thermocouple with a temperature range of -328°F up to 2462°F (-200°C up to 1350°C). Type K thermocouples need to be carefully calibrated and have small output signals. They are used in an assortment of environments including water, mild chemicals, gasses, and dry conditions. Common industries that use type K thermocouples are hospitals and food preparation. Regardless of their wide temperature range, type K thermocouples are mostly used for temperatures over 1004°F (540°C).
Type N Thermocouples - Type N thermocouples have nicrosil, a nickel chromium alloy, and nisil, a nickel, silicon, and magnesium alloy. Their temperature range is from 32°F to 2300°F (650°C to 1260°C). Type N thermocouples are resistant to green rot and hysteresis and are used in refineries and the petrochemical industry.
Type R Thermocouples - Type R thermocouples are made of platinum and rhodium and are usable for temperatures up to 2700°F (1480°C). They have to be protected by a gas-tight ceramic tube and a secondary outer tube. Type R thermocouples have improved stability, an increased temperature range over Type S thermocouples, and are often used in place of Type S thermocouples. Applications for Type R are heat treating, control sensors, semiconductor industry, glass manufacturing, and ferrous and non-ferrous metals.
Type S Thermocouple - Type S thermocouples are used in high temperature applications in the BioTech and Pharmaceutical industries. They are also used for low temperature applications due to their accuracy and stability. Type S thermocouples have a temperature range of -58°F to 2700°F (980°C to 1450°C).
Type T Thermocouples - Type T thermocouples are made of copper and constantan with a temperature range of -330°F to 700°F (-200°C to 370°C). They are used in inert atmospheres and are resistant to decomposition even if there is moisture present. Type T thermocouples are used in food production and cryogenics.
Type B Thermocouple - Type B thermocouples are used for high temperature applications and have the highest temperature limit of the thermocouples with exceptional accuracy and stability. Their alloy combinations are platinum (6% Rhodium) and platinum (30% rhodium) with a temperature range of 2500°F to 3100°F (1370°C to 1700°C).
Type C Thermocouples - Type C thermocouples have tungsten and rhenium legs and are used with applications that require temperatures up to 4200°F (2315°C). They are used in hydrogen, inert, or vacuum atmospheres to prevent failure from oxidation. Type C thermocouples have protective sheaths made of molybdenum, tantalum, and inconel with insulators of alumina, hafina, and magnesium oxide.
This type of temperature sensor displays a change that is precise, predictable, and large in the alteration of different temperatures. With a change this large, it means that the reflection of the temperatures occurs rapidly and accurately.
This type of temperature sensor is the standard temperature sensor, particularly the mercury-filled glass tube. However, thermometers exist in several types. Glass thermometers can contain either ethanol or mercury, although nowadays the main liquid used in these thermometers is ethanol.
This type of thermometer consists of a connected gauge and stem. There is a spring attached to a rod on the tip of the sensor, leading up to the gauge’s needle. Inside the stems, the spring sits sensing the end.
When heat is applied on the sensing coil, there is a creation of movement in the coil, which causes the movement of the needle in the gauge – thus the temperature is displayed.
These types of thermometers work the same. Both have a bulb filled with either gas or liquid located inside the sensing end of the probe. When heat is applied, the gas expands or the liquid heats up, which signals the rod attached to move the needle to the measured temperature.
This type of thermometer utilizes a probe such as a thermocouple or an RTD. The temperature is measured by the probe (sensing end) and displayed as a digital reading.
These types of temperature sensors detect temperatures from a distance by measuring the amount of thermal radiation that is being emitted by a heat source or object.
These temperature sensors find their application in high temperatures or hazardous environments, where a safe distance must be maintained away from a particular body.
These temperature sensors are the most common type of non-contact temperature sensors. They are used in the following circumstances: when the target object is in motion (like within moving machinery on a conveyor belt); if the object is far away; if the surrounding environment is dangerous; or in extreme temperatures where a contact sensor is not suitable.
A thermistor is a temperature sensor that reacts to minute temperature changes. At very low temperatures, it provides high resistance. As the temperature increases, the resistance quickly drops. The glass coated NTC thermistor offers the highest accuracy. The smallest change in resistance per degrees of Celsius is immediately displayed.
Negative temperature coefficient thermistors require linearization due to their use of the exponential working principle, where the temperature range is between -58°F to 482°F (-50°C to 250°C). NTC thermistors also require linearization because of the size and speed involved.
The use of a NTC thermistor in a detection circuit requires the use of a small voltage to be passed across the thermistor. The temperature will be reflected by the thermistor’s resistance, which rapidly drops as the temperature increases.
For applications in the range of -40°F to 257°F (-40°C to 125°C), NTC thermistors provide an option that is less expensive than platinum RTDs, thermocouple sensors, and semiconductor based sensors. NTC’s fast changing resistance base makes them capable of providing superior accuracy, power efficiency, stability, reliability and responsiveness. They can easily be integrated into any system.
Semiconductor-based temperature sensors work with dual integrated circuits. They consist of two diodes that are similar, with voltage and temperature-sensitive current characteristics for measuring the changes in temperature effectively.
Semiconductor-based sensors give a linear output; however, they are less accurate at 1 to 5°C. These types of temperature sensors have the slowest responsiveness (5 to 6 seconds) across the narrowest temperature range (-94°F to 302°F or -70°C to 150°C).
This type of temperature sensor is used to measure the internal temperature in water or concrete structures. It exhibits a resolution of better than 0.1°C and its working is similar to that of a thermocouple temperature sensor.
Its temperature range is also high, ranging from -4°F to 176°F (-20°C to 80°C).
This chapter will discuss the applications and benefits of temperature sensors. It will also discuss temperature control using temperature sensors.
The function of temperature sensors is to measure temperature in many various applications and industries. Temperature sensors are all around us, present in both industrial settings and everyday life. The following are examples of the applications of temperature sensors:
Temperature sensors are utilized to monitor various environments and machinery, power plants, and manufacturing. Temperature sensors are used to measure water temperatures in reservoirs and boreholes. They can also be used to interpret temperature-related stress and changes in volume in dams. Temperature sensors are also utilized in the study of the temperature effect on other installed instruments.
Temperature sensors are utilized in science and biotech monitoring.
Temperature sensors are utilized in the monitoring of patients, in medical devices, in thermodilution, in humidifiers, gas analysis, cardiac catheters, ventilator flow tubes, and dialysis fluid temperature.
Temperature sensors are used for measuring inlet air temperature, exhaust gas, engine temperature, and oil temperature.
Temperature sensors are used in kitchen appliances (ovens, kettles, etc.) and also in white goods.
Temperature sensors are utilized in air conditioning devices and heating ventilation devices, either domesticated or commercial.
Temperature sensors are used in refrigerated vans and trucks.
The benefits of temperature sensors include:
There are some factors that must be considered when selecting a temperature sensor for a certain application. The following are factors that must be considered when opting for a temperature sensor:
Different types of temperature sensors are capable of measuring different ranges and might be more accurate within a certain range. It is important to make sure that the range of the temperature sensor is checked, and also the range of your application that is expected before purchasing. The temperature range of the temperature sensor is provided on the datasheet.
An application may require a certain degree of accuracy; be aware that the variance of thermocouples in long term stability is higher than that of thermistors and RTDs.
The type of temperature sensor selected is determined by the space available within the application. If there is limited space, a smaller device is required. How the temperature sensor will be connected to the application and how the temperature is going to be measured is determined by package style; therefore, package style is an important consideration.
A critical factor in the placement and choice of a temperature sensor is the conditions where it will be used. Humidity, vibrations, and other environmental factors radically affect the stability and accuracy of a temperature sensor. In addition, electrical noise affects its readings especially if the temperature changes are minute and small. Attention to the noise level where a temperature sensor is used ensures accurate measurements.
The conditions and environment where a temperature sensor is to be placed has to be closely examined to ensure optimum performance. Aside from the obvious structure of the temperature sensor, any connections, such as lead wires, have to be protected from hostile and unstable environments.
Various measures can be taken to protect a temperature sensor and its wiring from the conditions of the environment such as protective metal sheaths that are resistant to wear and corrosion. The use of sheathing increases the cost of a temperature sensor and affects its sensitivity. Additionally, certain sensor configurations have mounting considerations to ensure a solid thermal connection.
Temperature sensors are utilized in the effective control of temperature. Five keys to effective temperature control are discussed below:
The last decision made in the system design is often the selection of a temperature sensor. Typically, the decision is driven by the compatibility of the process controller of the system and often comes down to availability and cost. Unfortunately, the critical selection criteria that include sensor mass, operating temperature, signal strength, reading sensitivity, and operating ambient are overlooked frequently.
There are three types of sensors used in commercial temperature control: thermistors, thermocouples, and resistive thermal devices (RTDs). Each type of temperature sensor exhibits its own characteristics and various styles within each type are designed for specific temperature ranges, output signals and process compatibility based on the construction materials.
The sensor must be selected in such a way that it matches specific design application parameters. An important characteristic is the sensor mass, and it is important to consider it when making a final selection. Heavy sensor bodies offer a slower, dampened response to process changes, whereas a light sensor mass offers a quicker response to process temperature changes. Typically, if the temperature control is more exacting, the sensor will be lighter and will respond more quickly.
The location of the temperature sensor of the system is crucial, even though it might be obvious. In some situations, field installation of a temperature sensor is affected by physical obstacles that are responsible for the initial design location to be modified. When the placement of the temperature sensor in the correct location is difficult, there must be a consideration of compromises and alternatives.
However, the sensor’s position is the key to the success of every other part of the system. There must never be a compromise of the system efficiency for ease of sensor installation. Listed below are a few tips to avoid common pitfalls:
The goal of any temperature control system is to balance the heating and cooling capabilities of the system. If the energy balance is mismanaged, this may result in temperature instability. There are two basic types of controls, which are proportional output control and on/off output control.
The easiest type of control to understand is the on/off control. Its decision making on temperature deviation is based on the temperature setpoint of the system. At a temperature that is predetermined, either below or above the setpoint, there is an activation of the full capacity of the heating or cooling system by the system. The only way to stop further cooling or heating is by turning off the conditioning equipment. If the mass process is larger than the heating or cooling capacity and the temperature fluctuation that is allowed is wide, on/off control can be an ideal cost-effective control method.
However, there are some practical limitations with it. Because the capabilities of a system are often significantly higher than the load in different situations, only turning the cooling or heating equipment on and off is generally impractical.
One approach that can be used to enhance the capacity control of on/off control systems is the addition of different levels or stages of capacity to the cooling or heating system.
The process control can be more manageable by keeping all of the equipment subsystem functions predictable. With the advent of energy and management improvements, some energy-saving schemes can have a destabilizing effect on the temperature control of the process. As loads change, many new systems will automatically compensate several variables in response to this change.
The most commonly adjusted variables are supply fluid temperature, process fluid volume, and heating or cooling capacities. The adjustment of several subsystems such as supply temperatures, process pressures, and fluid flow will change the system’s characteristics, and these changes are capable of creating temperature instability and cause problems in control. For instance, consider a plant chiller system in which the rate of flow of the fluid of the process is changed.
The reduced rate of flow can change heat-transfer characteristics exponentially in some components of the system and heat exchangers. The loss of heat transfer may result in temperature instability at the critical point and can cause the malfunctioning of the compressor or other components.
Many of the proportional controllers fall into three design actions or types: (PID) proportional plus integral and derivative, (PI) proportional plus integral, and (P) proportional only. Engineers have been provided with more flexibility in their designs with technical advances in small process controllers.
The improvement of controllers has increased to such a degree that they are capable of often compensating for system design flaws and unruly characteristics. The simplest controllers are proportional controllers, and they are the basis for most small electronic devices. A proportional controller is able to work off a deviation of temperature and applies an output signal on the basis of a linear calculation in which a change in a given deviation results in a linear change in output.
A temperature sensor can also be defined as a simple instrument that measures the degree of coldness or hotness and then converts it into a readable unit. There are different types of temperature sensors, including thermocouples, thermistors, RTDs, etc. Each temperature sensor has its own unique characteristics, which makes it suitable in specific types of applications. However it is important to consider the temperature range, accuracy, size, and stability of a temperature sensor for optimal performance within a specific application.
An RTD, resistance temperature detector, is a passive temperature sensing device that operates on the principle that the resistance of a metal changes as the temperature changes. The electrical current that passes through the element...
A thermistor, a shortened version of the term thermal resistor, is a passive component whose resistance changes as the temperature in a system changes. Thus they serve as an inexpensive, accurate, and dynamic method for measuring temperature...
A thermocouple is a transducer that converts thermal energy into electrical energy and is constructed by joining wires made from dissimilar metals to form a junction. Voltage is produced when the temperature at the junction changes...
A thermowell is a pressure-tight vessel that safeguards and increases the lifespan of temperature sensors in processing plants in cases where a measuring sensor is not otherwise mechanically or chemically useful in...
A band heater is a heating device that clamps onto objects to provide external heat using radiant and conductive heating. The different mounting methods of band heaters makes it possible to secure them tightly and...
A cartridge heater is a cylindrical tubular heating device that provides concise and precise heating for various forms of materials, machinery, and equipment. Unlike an immersion heater, a cartridge heater is inserted into a hole in the item to be heated to furnish internal radiant heat...
Ceramic heaters are electric heaters that utilize a positive temperature coefficient (PTC) ceramic heating element and generate heat through the principle of resistive heating. Ceramic materials possess sufficient electrical resistance and...
Electric heating is produced by using a known resistance in an electric circuit. This placed resistance has very few free electrons in it so it does not conduct electric current easily through it. When there is resistance in...
A flexible heater is a heater made of material that can bend, stretch, and conform to a surface that requires heating. The various forms of flexible heaters include polyimide film, silicone rubber, tape...
A heating element is a material or device that directly converts electrical energy into heat or thermal energy through a principle known as Joule heating. Joule heating is the phenomenon where a conductor generates heat due to the flow of electric current...
An immersion heater is a fast, economical, and efficient method for heating liquids in tanks, vats, or equipment. Known as bayonet heaters, they have heating elements that can be directly inserted into a container of water, oil, or other material in order to heat the entire contents...
Infrared heating is a heating method used to warm surrounding bodies by infrared radiation. Thermal energy is transferred directly to a body with a lower temperature through electromagnetic waves in the infrared region...
Radiant heaters are systems that generate heat internally and then radiate it to the nearby objects and people. The sun is a basic example of a radiant heater. When we feel warm on our bodies on a sunny day...
The idea of an electric heater seems to be out of place in modern society since most buildings have a sophisticated central heating system. That may be true, but electric heaters can be a helpful way of saving energy while providing efficient heating...