Expansion Joints
Introduction
This article will provide a detailed discussion regarding expansion joints.
It is expected that after reading this article, one should better understand:
- Expansion Joints, What They Are, How They Work, Common Materials Used in Expansion Joints, and Considerations in Selecting an Appropriate Expansion Joint
- How Expansion Joints Are Manufactured
- Types of Expansion Joints
- Benefits and Applications of Expansion Joints
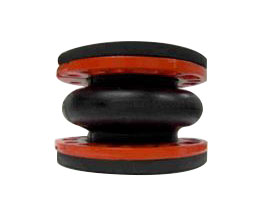
Need to order expansion Joints? Order online or call Mercer Gasket & Shim at: Phone: (800) 210-5000
Chapter One: Overview of Expansion Joints
Expansion joints, as their name suggests are meant to allow for movement. Expansion joints are used to absorb the movement of pipes, ducts, and other components of a pipeline resulting from thermal and mechanical vibrations. These vibrations are often the result of different temperature conditions. Expansion joints are designed to expand when the temperature rises and shrink when the temperature is reduced in order to securely reinforce the piping systems they support. Sometimes mechanical components can also be used with the allowance for turning and linear motion.
An expansion joint is a connection between any two structures that permits movement of the structures during expansion and contraction. Expansion is the process of becoming larger, or expanding in size or scope, from an increase in temperature. During expansion, the average kinetic energy of the atoms increases, causing them to vibrate more quickly, as a material’s temperature increases. This causes the matter to expand. A plumbing system uses expansion joints to absorb such shock and vibration.
Expansion joints also have benefits like noise reduction and misalignment compensation. Usually an expansion joint just allows for the connected structures or pipes to expand or contract. Some expansion joints, however, are additionally made to accommodate exterior thermal expansion in extremely hot environments where temperature changes from the surrounding environment can affect a piping system.
Standard materials for expansion joints include metal (usually aluminum), rubber, and braided material. Braiding is the mechanical intertwining of three or more yarns so that no two threads are wrapped around one another. Since the braids are continuous, the load may be distributed equally throughout the structure. Braids can be made from either fiber or stainless steel. These adaptable connectors are made of stainless steel bands that have been braided and corrugated and are wrapped around a rubber or elastomer hose.
Additionally, they can be utilized to adjust for misalignment, lessen noise, and relieve anchor tension. They serve as an interface between two pipes, and aid in dampening movement. Due to their use, expansion joints take on unique shapes. Expansion joints are crucial because they can be employed in situations where there is a risk of structural damage due to the expansion or contraction of plumbing pipes, machinery equipment and even hydraulic and pneumatic systems. An expansion joint, for instance, can effectively retain its seal and position when there is movement between the two surfaces.
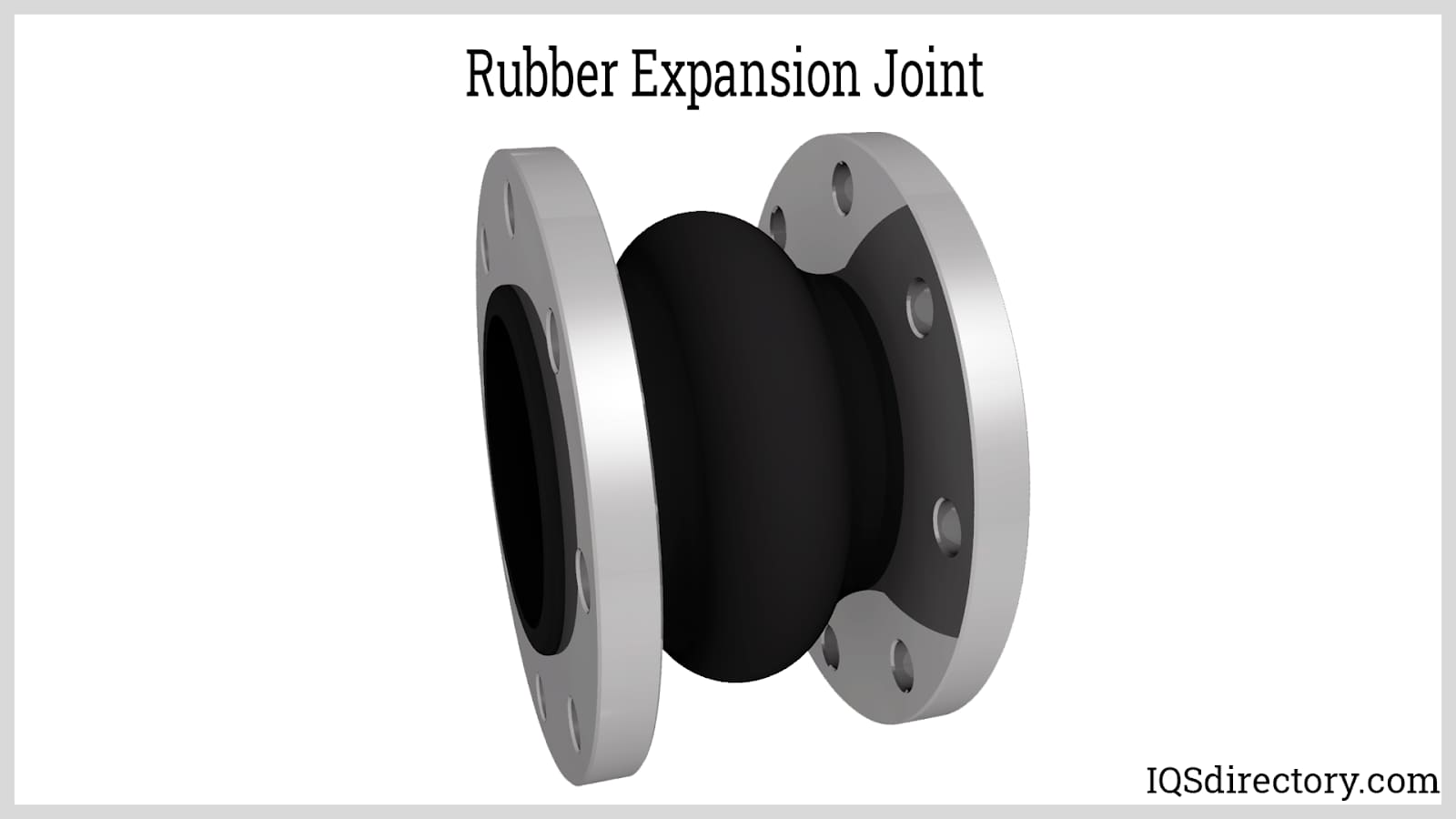
How They Work
Metal expansion joints serve as compensatory components for thermal expansion and relative movement in pipes, containers, and machinery. Depending on the application, they may have one or more metal bellows, connectors at both ends, and tie rods. Bellows are pliable components that dampen pipe system motions. The bellows' construction calls for them to be composed of either rubber or metal, which can stretch during expansion and constrict into a heap during contraction. Metal expansion joints compress to account for movement and relieve pressure on the pipe as the pipe’s temperature rises. Metallic bellows can be made from various materials, including nickel alloys and stainless steel.
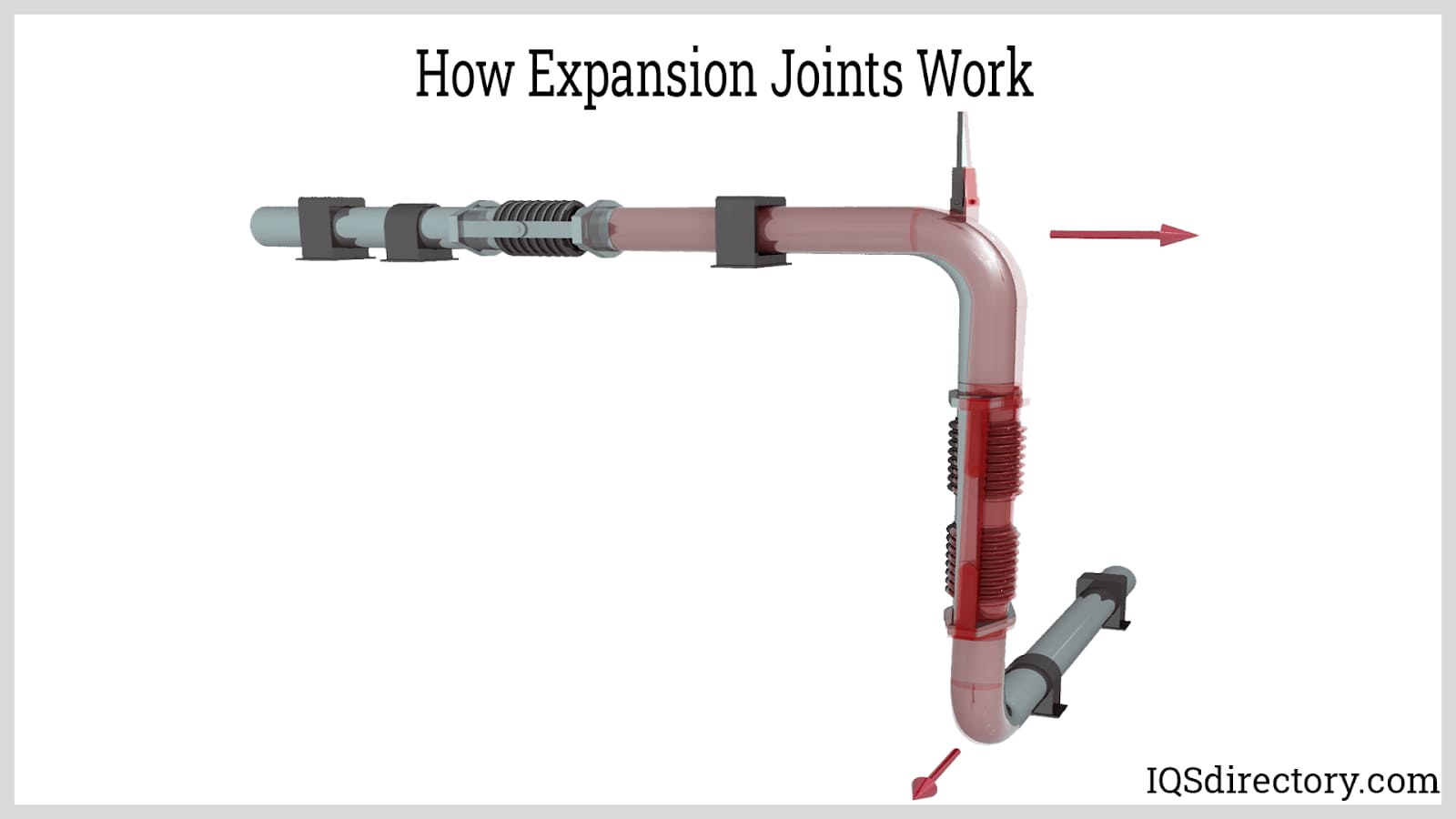
Expansion joints are used in various industries that produce energy, paper, chemicals, water treatment, oil, and gas. Expansion joints can be employed whenever pipelines and thermal or vibrational motions occur.
Common Materials Used in Expansion Joints
Metal
Metal expansion joints are useful in applications with much thermal expansion. As the pipe's temperature rises, the metal expansion joint contracts to account for the movement, relieving pressure on the anchors and the pipe.
Rubber
Rubber has excellent vibration and shock wave absorption and can be utilized for thermal expansion. To safeguard equipment like pumps, this expansion joint is perfect for reducing the transfer of noise and vibration from other equipment. Additionally, they serve as shock absorbers to lessen the damage brought on by seismic events and pressure surges.
Braided Stainless Steel
Technically speaking, braided stainless steel hoses with flexible or metal liners are more of a flexible connector than an expansion joint. As a result, they perform effectively in applications needing vibration dampening or pipe misalignments in high-pressure and high- temperature environments.
Factors to Consider When Selecting an Expansion Joint
Given that expansion joints are frequently used in potentially demanding processes, such as those found in the steel, power, pulp and paper, mining, and chemical industries, proper selection, installation, and maintenance are essential for ensuring reliability and maximizing performance while obtaining the longest service life.
Pipe Size (in.) | Std Face-to-Face (in.) | Axial Com-pression (in.) | Lateral Deflection (in.) | Angular Rotation (deg.) | Torsional Rotation (deg.) | Std Working Pres. (psi) | Min. Burst Pres. (psi) | Vacuum Rating (in. Hg) |
---|---|---|---|---|---|---|---|---|
2 | 6 | 3/4 | 1/2 | 14.5 | 3 | 165 | 660 | 30 |
2 1/2 | 6 | 3/4 | 1/2 | 11.5 | 3 | 165 | 660 | 30 |
View the full data table here
Application Field
The area of application is, of course, the very first factor to take into account when selecting an expansion joint. Many industries use expansion joints. Therefore, knowing where the expansion joint will be used is the first choice stage. Some uses include plumbing, piping and construction.
In piping systems and when fluids are being pumped, the pipes may expand due to the pressure of the fluid or the surrounding temperature. A plumbing system has expansion joints built to absorb shock and vibration. Additionally, they lessen system operation noise.
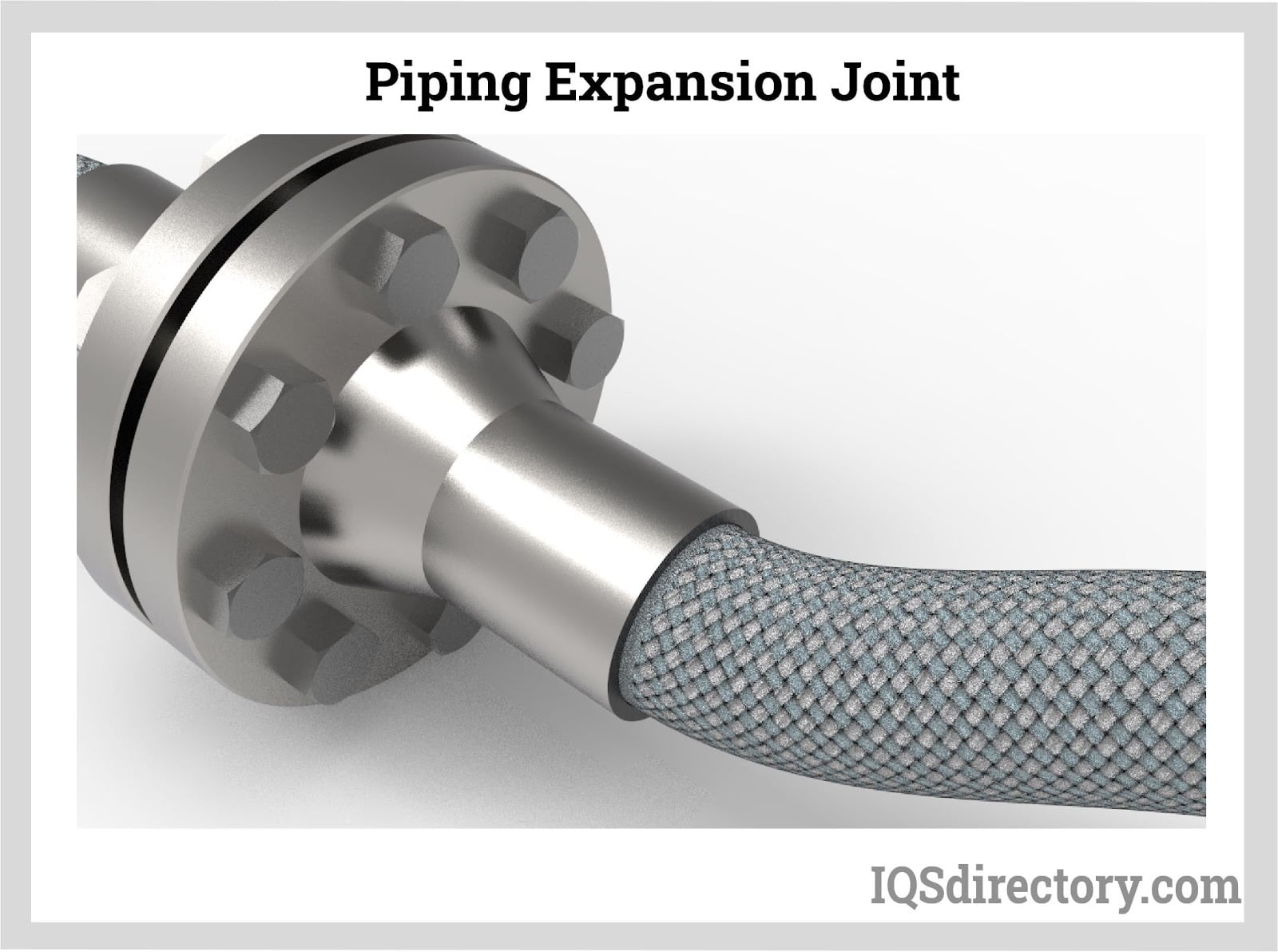
An expansion joint in building construction is a mid-structure separation intended to reduce stress on building materials brought on by building movement. Main factors that cause movement in buildings at expansion joints include: temperature fluctuations that produce thermal expansion and contraction, seismic sway brought on by wind occurrences, dynamic load bending, and direct force bending
Piping Scheme
Before addressing the expansion junction, one must verify that nearby pipes and equipment adhere to good, solid piping engineering techniques. In essence, for the expansion joint to work properly, the placement and design of the anchors, guides, and supports are critical. Pipe anchors are typically used to secure pipes to a location and prevent them from moving. To allow pipe movement in one direction while preventing motion in other directions, a pipe guide is used. The purpose of pipe support is to transmit the weight from a pipe to the supporting structures.
Placement
The expansion joint's position is critical for best performance. Early planning will result in a location that enables appropriate movement allowances, sufficient ambient cooling, and simple accessibility.
Joint Motion
Since axial, lateral, and angular pipe movement and vibration are absorbed by expansion joints and pump flexible connectors, considerable thought should be given to appropriately calculating those movements. These basic movements must be considered and built into the expansion joint to ensure a long life. More stress placed on an expansion joint might result in an unexpected failure, and certain designs are better suited to manage specific movements than others.
Expansion joints used in construction projects may need to have the ability to move horizontally, vertically, or have a multidirectional movement capability; they must also be able to provide both shear movement as they may be required to rub against other joints and items, and protection from any degradation caused by this type of harmful interaction.
Media Flow
Many design elements are based on the air or liquid that passes through the expansion joint. Important add-ons like flow liners or insulation provide further defense against contaminating or abrasive media. The medium passing through the piping system is one of the most crucial deciding criteria for choosing a suitable material. Condensation inside an expansion joint might lead to a chemical attack on the employed materials or framework. If the proper support materials are not used, the turbulent flow might result in flutter and will reduce the lifespan of the expansion joints.
Material Examination
It is advised that expansion joints meet criteria for material certification to ensure that they meet requirements for the pumped fluid. The examination procedure must include material choice. Selecting a defective tube material is dangerous and might result in expensive replacement costs or downtime.
Temperature
The examination of the application's needs should take into account the significance of accurate temperature data. The internal and external ambient temperatures determine the appropriate materials, insulating components, and frame design. The expansion joint or flexible connector must be able to support the system while operating at its highest pressure at temperature.
Pressure
What fabric or reinforcements should be utilized for the design of the expansion joint is frequently determined by the design pressure. Compared to reinforced fiberglass fabric, reinforced molded rubber expansion joints and metal bellows can withstand substantially higher pressures. However, if not handled, pulsations or pressure changes might reduce life. Therefore, pulsing or shock pressure should be examined when connectors are used at discharge.
Installation
Many expansion joints can be sent already fully constructed, where they can simply be inserted between duct flanges and fastened in place. However, due to transportation restrictions, larger sizes frequently need to be sent in sections and built on location. It's crucial to consider any barriers or interferences next to the expansion joint in either scenario. The mounting flanges' positioning and accessibility are crucial for an effective installation and for future maintenance or replacement.
Finish Type
Various finishes and materials are conceivable on an expansion joint. When choosing an expansion joint, consider the color, powder coating, and stainless steel or brass caps, among other factors.
Maintenance of Expansion Joints
Although a properly sized, designed, and fitted expansion joint shouldn't need any maintenance, a routine inspection program is strongly advised. Any problems, such as leaks, corrosion, or blisters and fractures in rubber expansion joints, can be found through inspections. While looking for wear indicators does not ensure that damage won't happen, doing so greatly lowers the overall potential of harm.
Ready to take the next step in exploring Mercer Gasket & Shim's high-quality expansion joints? Download our expansion joint data sheet today to learn more about our products and how they can meet the unique needs of your application. With detailed technical specifications and customization options, this data sheet is the perfect resource for engineers and procurement professionals. Don't miss out on the opportunity to see how Mercer Gasket & Shim can help you achieve your industrial goals.
Click the link to download our expansion joint data sheet now!
Chapter Two: How Expansion Joints are Manufactured
Tube to Bellow Construction
Making the corrugated tube or tubes is the initial stage in producing metal bellows. First, precision shearing is used to cut the coil or sheet stock to the required size. Next, the sheets are coiled into tubes after being sheared. To fit over the dies used to manufacture bellows, care must be given to ensure that the tubes are properly round. After rolling, each tube is longitudinally seam-welded on an automatic seam welder. This process is crucial to the creation of the bellows.
Forming Technique
There are various ways to corrugate the tube; mechanical die-forming and hydroforming are the most popular methods. On the bellows forming machine, the tube is positioned over the die. A metal forming technique called hydroforming uses pressurized liquid medium to create specific workpiece shapes out of tubular or sheet metal. A hollow aluminum tube is put into a negative mold that mimics the desired bellow's shape in order to hydroform aluminum or other metals into bellows. The aluminum tube is then filled with fluid at extremely high pressure by high-pressure hydraulic pumps, which forces it to expand until it fits the mold. After that, the hydroformed bellow is taken out of the mold. The machine is programmed to create the correct engineered diameter of bellows corrugation and to ensure that the overall joint was also made in the correct shape. The additional components of the joint are created during the shaping process.
Re-Rolling Process
The shape of the produced metal bellows is completed and cold worked to the precise geometry established by the design engineer during the secondary phase of re-rolling. Any metalworking procedure known as cold work involves plastically deforming the alloy below its recrystallization temperature. Coldworking makes the bellows strong and ensures they have good dimension control properties as well. Unfortunately, some dishonest expansion joint manufacturers omit this step and compress the bellows to size in a press, lowering the bellows' final performance capabilities.
Welding
On multi-ply bellows, a continuous series of overlapping spot welds join the tubes at the bellows' neck. This procedure is known as roll seam welding. First, the bellows are constructed, then welded to the other manufactured components of the junction.
Chapter Three: Types of Expansion Joints
Get a free catalog to understand your options with the help of the form below:
Axial Expansion Joints
The length of the expansion joint will either lengthen or compress as a result of absorbing axial movement, which is viewed as elongation or compression of the pipe system along its longitudinal axis. Axial expansion joints are made to accommodate longitudinal extension and compression movements. If axial expansion joints in a piping system are built without restraint bars, the pipeline will need fixed points and the right anchors to counteract the reaction forces produced by the bellows. A free length is the length of an expansion joint when it is neutral. Axial expansion joints should be fitted under pre-tense conditions, known as cold pull, to achieve more cycle life. An axial expansion joint in axial compensation absorbs the thermal expansion of a straight line section between two fixed points. The pipeline length that needs to be compensated is determined by the distance between two fixed points, which also establishes the required axial movement of the expansion joint. Larger motions can also be obtained by pre-tensioning or putting many expansion joints on the pipe section. Axial expansion joints that absorb significant movements can comprise one, two, or several bellows in one unit. Axial expansion joints can absorb slight lateral and angular deflections and installation tolerances, depending on the nominal diameter and length. However, the principal purpose of axial expansion joints should be only based on recommended usage; otherwise, their service life may be significantly impacted.
Types of Axial Expansion Joints
Single Expansion Joints
Single expansion joints have bellows components, end connectors such as pipe ends, flanges, weld necks, and additional optional features like collars, liners, and coverings. Depending on the movement of the pipe, the bellows may deflect in any direction or plane. Single expansion joints are a practical design choice, but they require that the piping coordinate align with the direction of the bellows unit's movements. It is unreasonable to anticipate that the pipe expansion joint will regulate pipe movement. The piping must be steered and restrained so that movement will occur if the piping analysis reveals that the pipe expansion joint must accept axial compression.
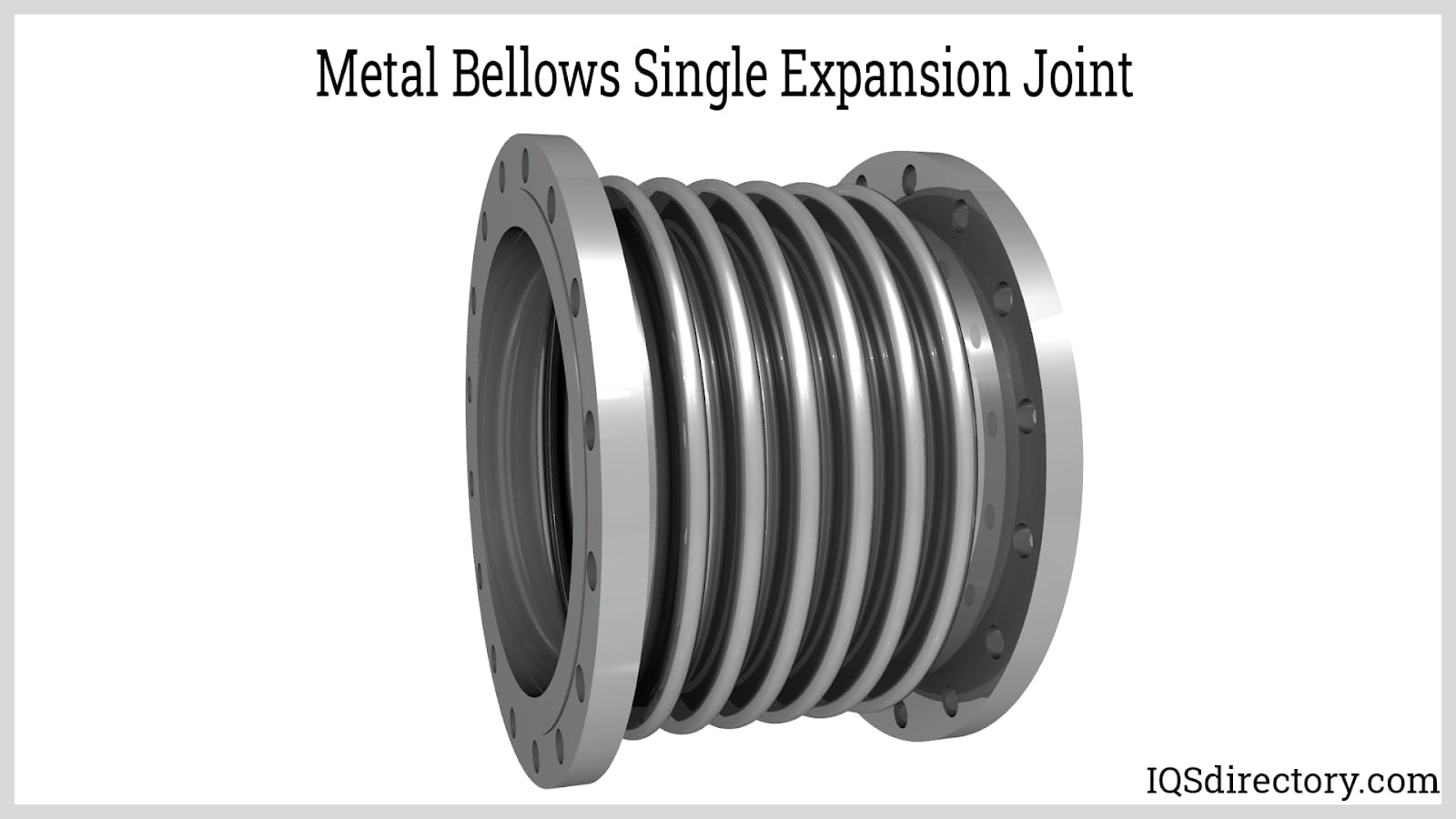
Elbow Pressure Balanced Expansion Joints
Elbow pressure balanced expansion joints are the types of pressure balanced expansion joints used when pressure thrust pressures on machinery or piping become intolerable to the point that the direction of the pipe system also changes. By using elbow pressure balanced expansion joints, the pipe system only receives the spring rate force required to move the expansion joint since the pressure thrust force (the force produced by the expansion joint as a result of internal pressure) is internally balanced within the expansion joint. The word spring rate force refers to the amount of flexibility of a bellows. It is typically used to describe the amount of force needed to move the bellows through a certain movement. As a result, fewer supporting structures are required because the load on the guides and anchor points is reduced. This makes it possible to utilize lighter guides, which can result in significant savings, especially when performing structural and foundation work is impractical. Pipe guides are used to allow pipe movement in one direction while preventing motion in other directions. Elbow pressure balanced expansion joints are the best option for pipe systems because this feature prevents pressure thrust loads from operating on flanges and linked machinery like turbines.
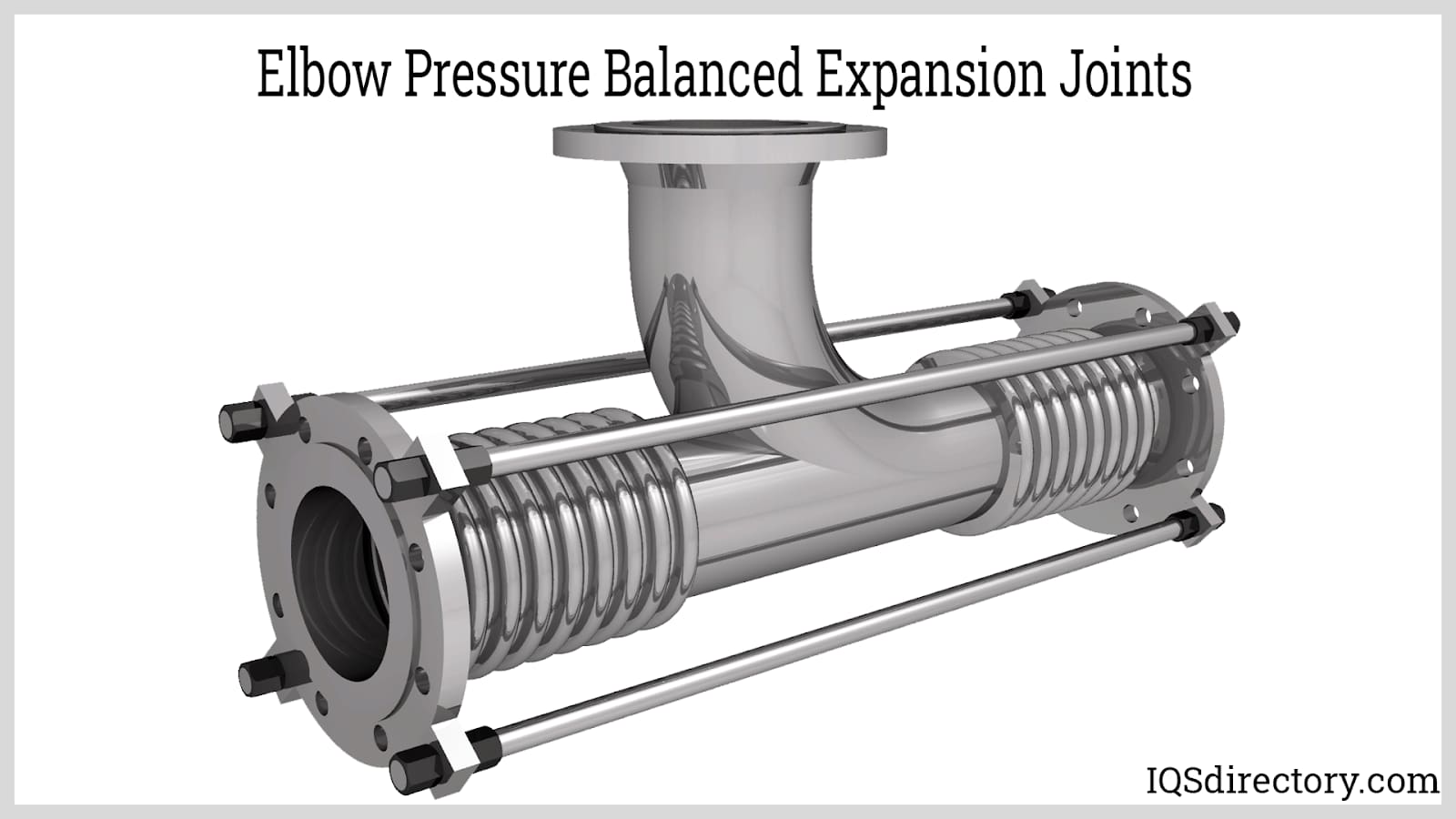
Externally Pressurized Expansion Joints
In contrast to a traditional expansion joint, an externally pressurized expansion joint receives pressure from the outside of the bellows part. Due to the wiggling movement caused by the longer bellows, conventional expansion joints with internally-pressurized bellows cannot support substantial axial movements. However, large axial movements are possible because of the distinctive design of externally-pressurized expansion joints, which may be required when space is an issue. Media passes via the expansion joint and contacts the bellows' outside rather than its interior. This external pressurization enables a longer structure and a larger stroke by eliminating pressure instability as a design constraint.
Toroidal Expansion Joints
Toroidal convolutions, which are circular tubes wrapped around pipe ends or weld ends and feature a gap at the inside diameter to allow for axial stroke while absorbing changes in pipeline expansion or contraction, make up a toroidal expansion joint- a metallic assembly. The bellows' convolutions are what give it its flexibility. The majority of toroidal bellows are manufactured hydraulically under high pressure. Others are free-form, like a balloon being blown up. Toroidal dye cavities may be produced using more precise convolution forms. Toroidal expansion joint pressure-resistance is significant due to this high-forming pressure. Due to the pressure load on the convolution side wall, bellows shaped like a "U" experience bending stress. While the toroid contains only membrane stress, this generally defines the maximum pressure that may be contained. Deflection is minimal because of the toroidal form. Although allowed pressures are lower with "U" shaped convolutions, more deflection can be accomplished.
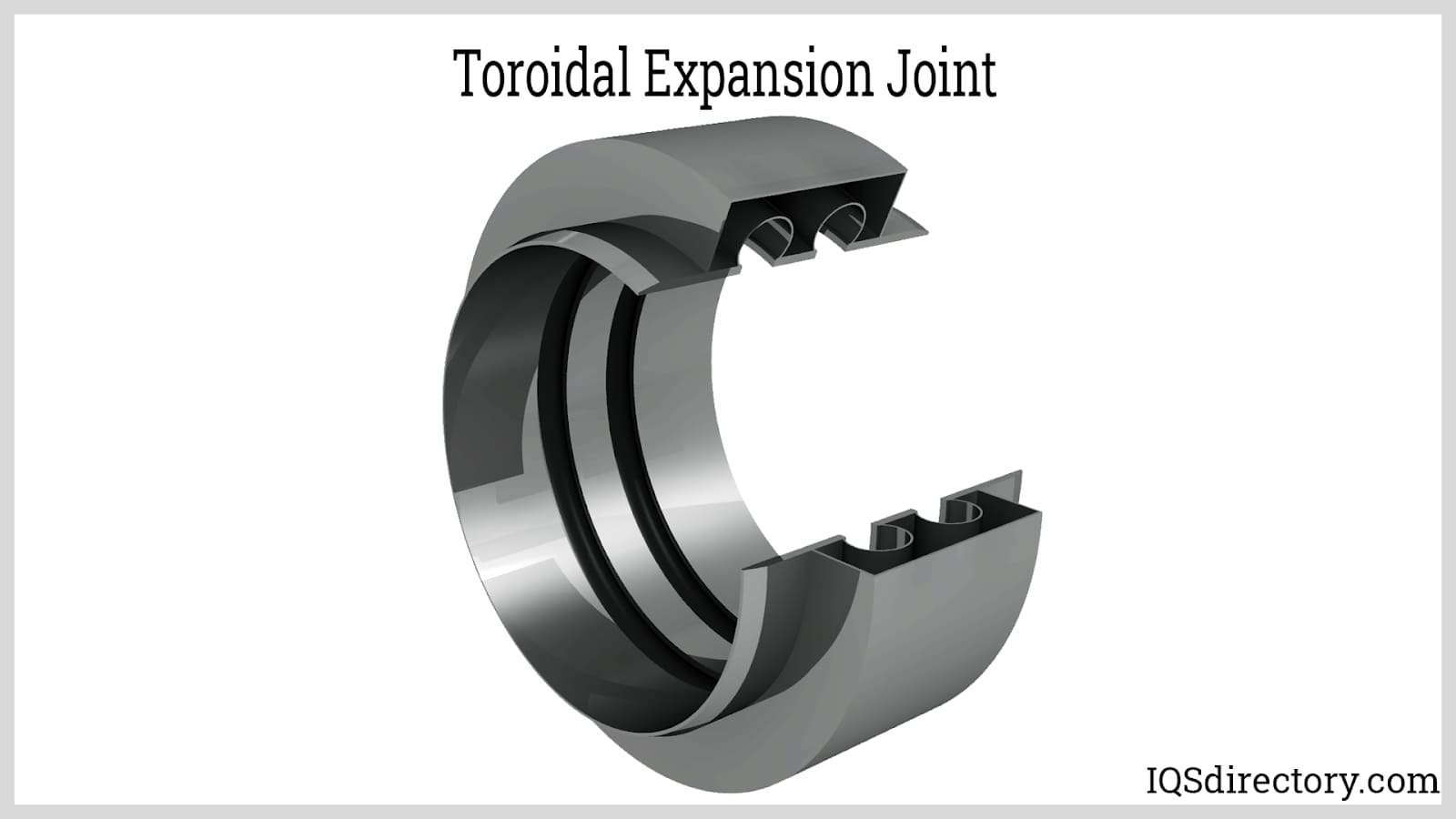
Slip Type Expansion Joints
Tubular piping expansion joints come in the slip kind. Sleeve expansion joint or sleeve compensator are other names for it. Slip-type pipe expansion joints are used when the main issue is a significant axial movement. The material choice must consider the high temperatures and pressures that the joint will be exposed to. Lines with multiple axial motions are best suited for slip-type expansion joints. Slip joints are parallel to the piping system and contract as the pipe enters them. A sleeve that inserts into the shell enables an expansion. Sealing materials are wrapped around the sleeve inside the shell to stop leaks through the slip joint.
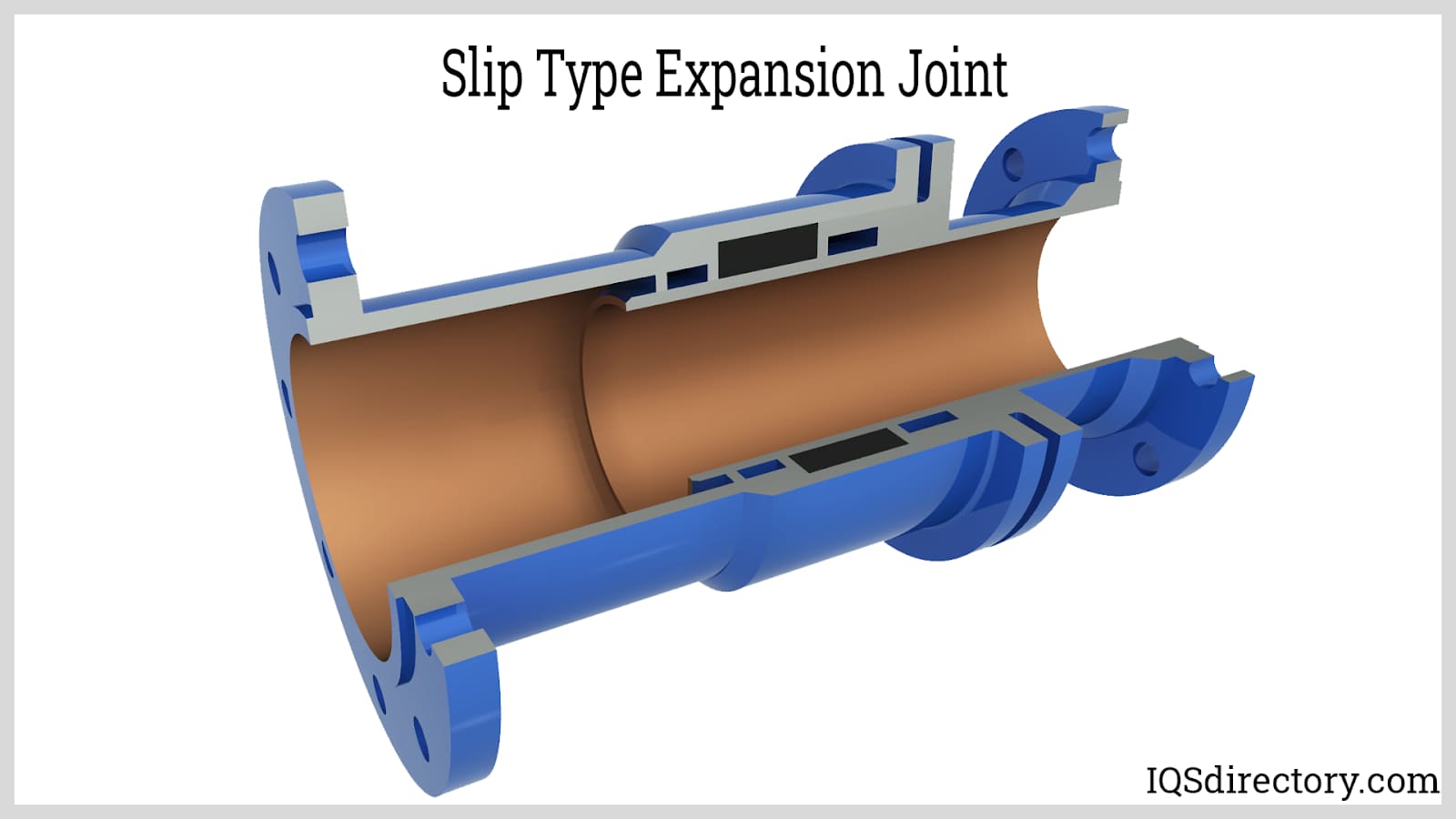
Unfortunately, slip type expansion joints have several significant drawbacks. They cannot tolerate rotational rotation or lateral offset since these conditions would lead to packing distortion, binding, galling, and possibly leaking. Therefore, suitable pipe guides and slide expansion joints are typically employed to ensure alignment. They are frequently utilized in civic water supply pipelines and district heating systems. The inner sleeve can become trapped inside the shell due to any lateral or angular movements, which reduces its capacity to withstand thermal stress. To avoid leaks, the packing material must be periodically maintained and replaced.
Angular Expansion Joints
Axial expansion Joints can extend and compress in the pipeline axis, but angular expansion joints only permit angular motions. A set of hinges moves the angular expansion joints in an angular rotation in one or more planes. Angular expansion joints can be produced with various end connections, such as welding ends, welded flanges, loose flanges, or combinations thereof, depending on client needs. Angular expansion joints are typically furnished with either hinges or gimbals. Angular expansion joints are just components of an expansion system, as opposed to axial and universal expansion joints, which are designed to compensate for movements independently. In contrast to axial expansion joints, angular expansion joints do not place any unique requirements on pipe supports or guides. Even swing hangers work well enough with angular expansion joints.
Both lengthy pipe sections of district heating systems and short boiler and turbine room pipelines can be compensated in one or more planes using angular expansion joints. One should also investigate the possibilities of installing linked universal or pressure-balanced expansion joints for installations with very little available space. A specified static system comprises two to three angular expansion joints. The function depends on the bellows' capacity to rotate, and the proper angular rotation which is specified in technical data sheets. Installation of angular expansion joints typically includes pre-stressing (this is done before commissioning to ensure functionality). In addition, the installation temperature is taken into account during pre-stressing.
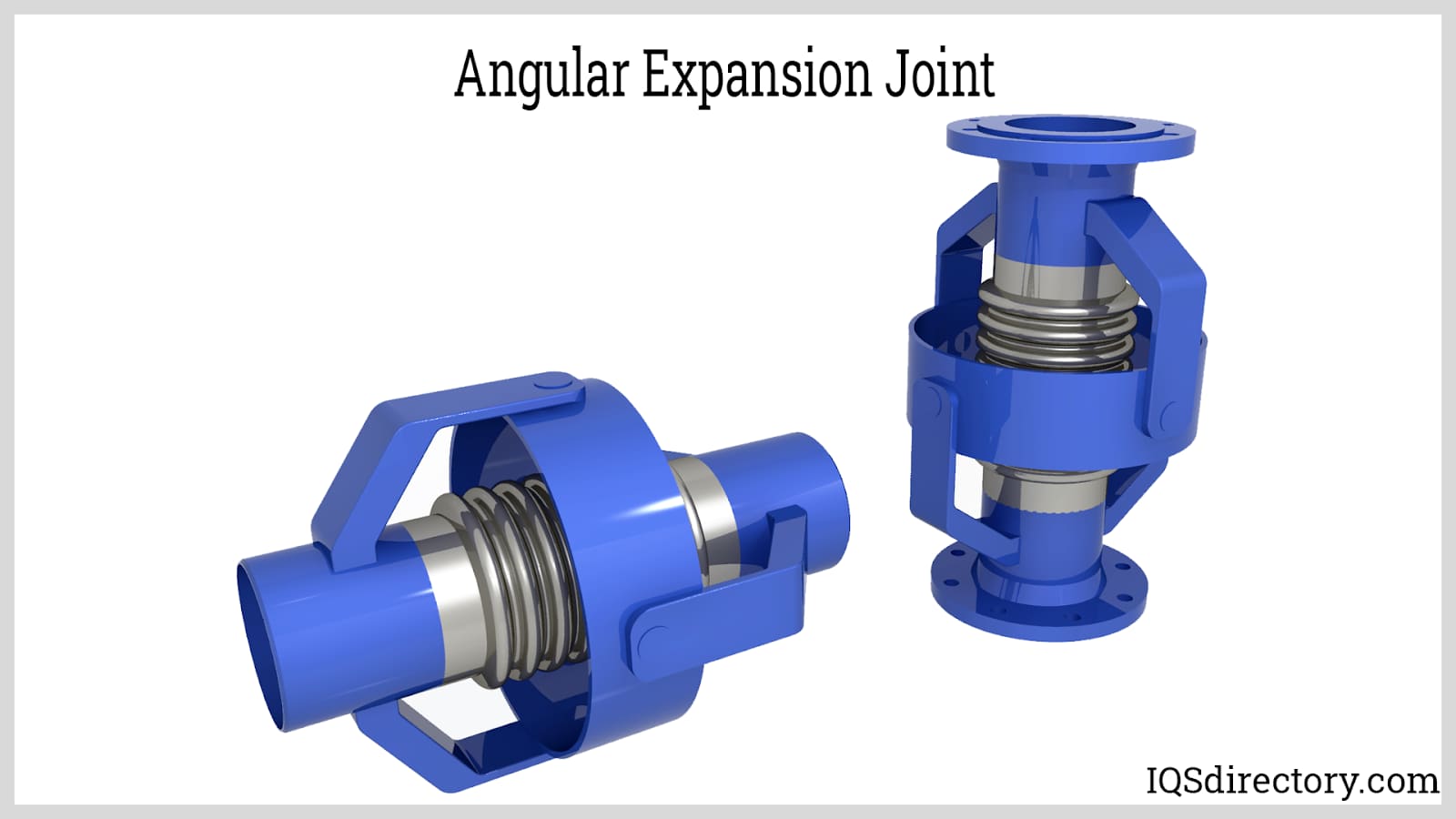
Two or even three angular expansion joints are necessary for the angular adjustment of thermal expansion. A large range of combinations is available when using angular expansion joints in so-called two- or three-hinge systems. While multi-plane three-hinged systems for absorbing thermal expansion in three axial directions require at least two gimbal expansion joints that are angularly flexible on all sides, single-plane, three-hinged systems can get by with just one-sided angularly flexible expansion joints.
Types of Angular Joints
Hinged Expansion Joints
Hinged expansion joints are metallic assemblies that may rotate in a single plane to accommodate changes brought on by pipework's thermal expansion or contraction. They contain hinges secured to the ends of the expansion joint with two pins and permit angular movement in a single plane while limiting pressure thrust and preventing axial deflection of the expansion joint during either extension or compression.
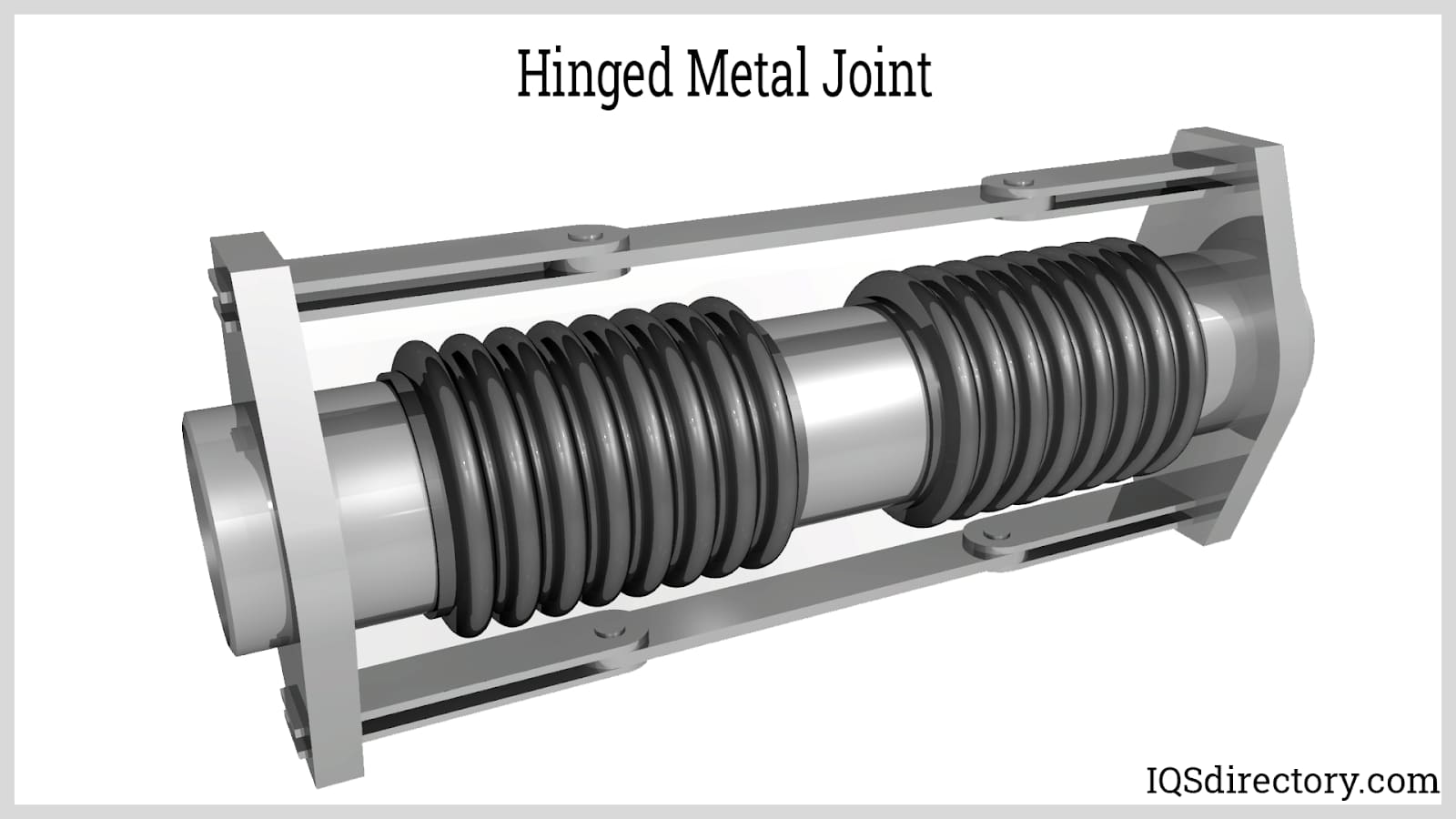
The hinges of each hinged expansion joint utilized in piping systems only allow for pure angular rotation. Hinged expansion joints work as a pair to counteract lateral deflection. The advantages of hinged expansion joints are their typical compact size and sturdy construction.
Gimbal Type Expansion Joints
Gimbal-type expansion joints allow angular rotation in any plane using two pairs of hinges attached to a single floating gimbal ring. A double-gimbal expansion joint is made up of two single gimbal expansion joints, which are connected by an intermediate pipe. The capacity to absorb a significant lateral movement in either plane at each end benefits this configuration. However, the gimbals at each end of the bellows prevent the universal joint from absorbing the intermediate pipe's thermal expansion, so the adjacent piping must accept it.
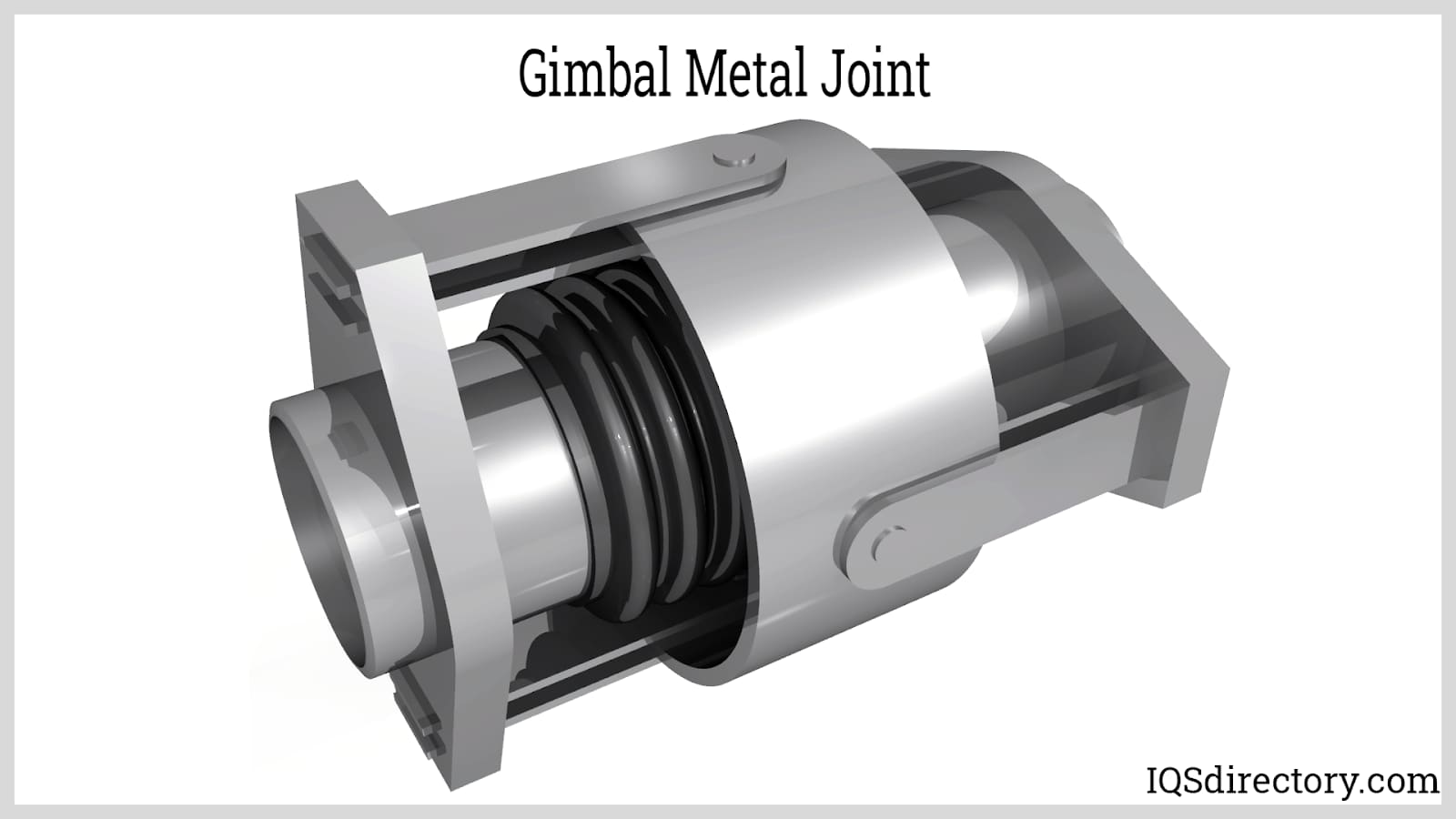
Lateral Expansion Joints
Lateral expansion joints are utilized for lateral deflection absorption. When two pipe sections expand in distinct directions, expansion joints can move in all directions simultaneously. The outer tie rods, often a part of the lateral expansion joint, allow it to absorb pressure thrusts and movements in all lateral directions. The operation of a lateral expansion joint is analogous to that of a hinged expansion joint. It makes use of the bellows' angular rotational capability. The bellows' capacity to rotate in an angular direction and their center-to-center distance enable lateral movement. The movement is greater the farther apart the bellows are from one another.
Contrary to unanchored axial and universal expansion joints, tie rods absorb the axial compressive force generated by internal pressure in lateral expansion joints, preventing them from loading nearby pipe support expansion joints with an angle.
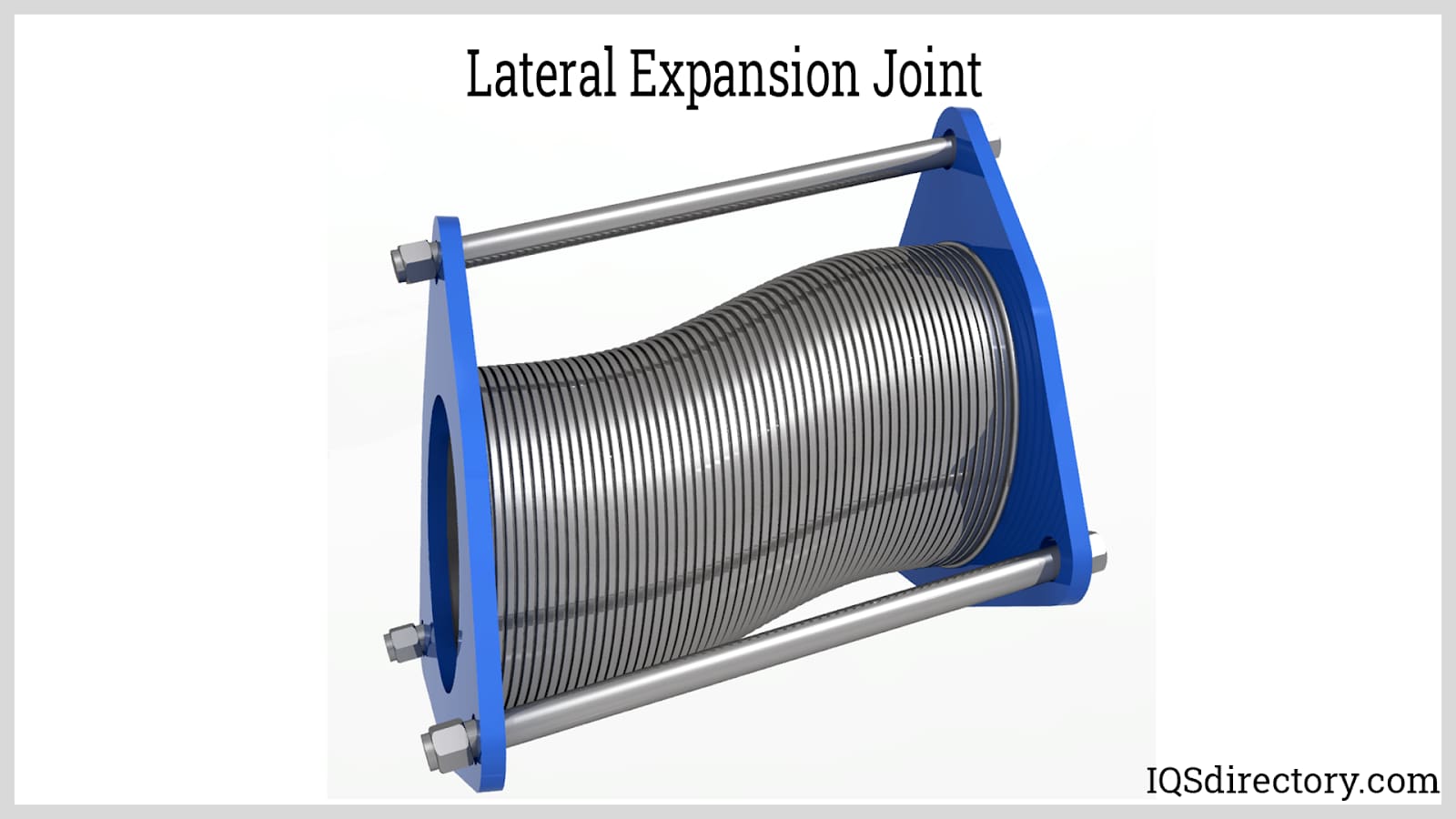
In single-plane or multi-plane pipe systems, lateral compensation is also related to a 90° flow redirection. Typically, lateral expansion joints are inserted in the system's already-existing right-angle redirections. The desired lateral movement and a small, unavoidable axial movement that originates from the expansion joint itself make up the movement of a lateral expansion joint.
Lower displacement forces of the expansion joint are also a result of a larger center-to-center distance. In contrast to single-hinged expansion joints, lateral expansion joints are separate expansion systems. They have two pins. Pre-stressing of 50% is typically used while installing lateral expansion joints. After the expansion joint is fitted, the pipe system as a whole is pre-stressed to achieve this installation.
Simple lateral expansion joints provide a far greater expansion absorption than axial expansion joints when used for lateral movements in one plane. Two pipe sections expanding in opposite directions are absorbed by lateral expansion joints simultaneously moving in all planes.
Types of Lateral Expansion Joints
Pressure-Balanced Expansion Joints
Pressure-balanced expansion joints can accommodate axial and lateral motions where anchoring the pipe system is impossible or unfeasible due to structural or financial reasons. The internal pressure force is not transmitted through these joints to the anchor points, nearby machinery, or nearby structures. Fix points are typically unnecessary; only guides can guarantee that thermal expansion is converted into a regulated movement. Therefore, where pipe systems are coupled with turbines, pumps, valves, or other equipment that cannot handle pressure thrust loads, pressure-balanced expansion joints can provide considerable benefits.
Thick Wall Expansion Joints
Thick wall expansion joints are distinguished by their thick ply structure and high coiled profile. They can be produced in any specific shape, including circular, oval, and square. Heat exchangers, furnaces, and blast furnace pipe work typically require thick wall expansion joints.
Rectangular Metal-Pipe Expansion Joints
Like circular pipe expansion joints, rectangular pipe expansion joints withstand axial, lateral, and angular movement. Therefore, knowing the direction of the lateral and angular movements is essential for designing rectangular bellows. In addition, the rectangular bellows must be constructed for longitudinal bending stresses, unlike circular bellows where the pressure stress is a circumferential membrane stress.
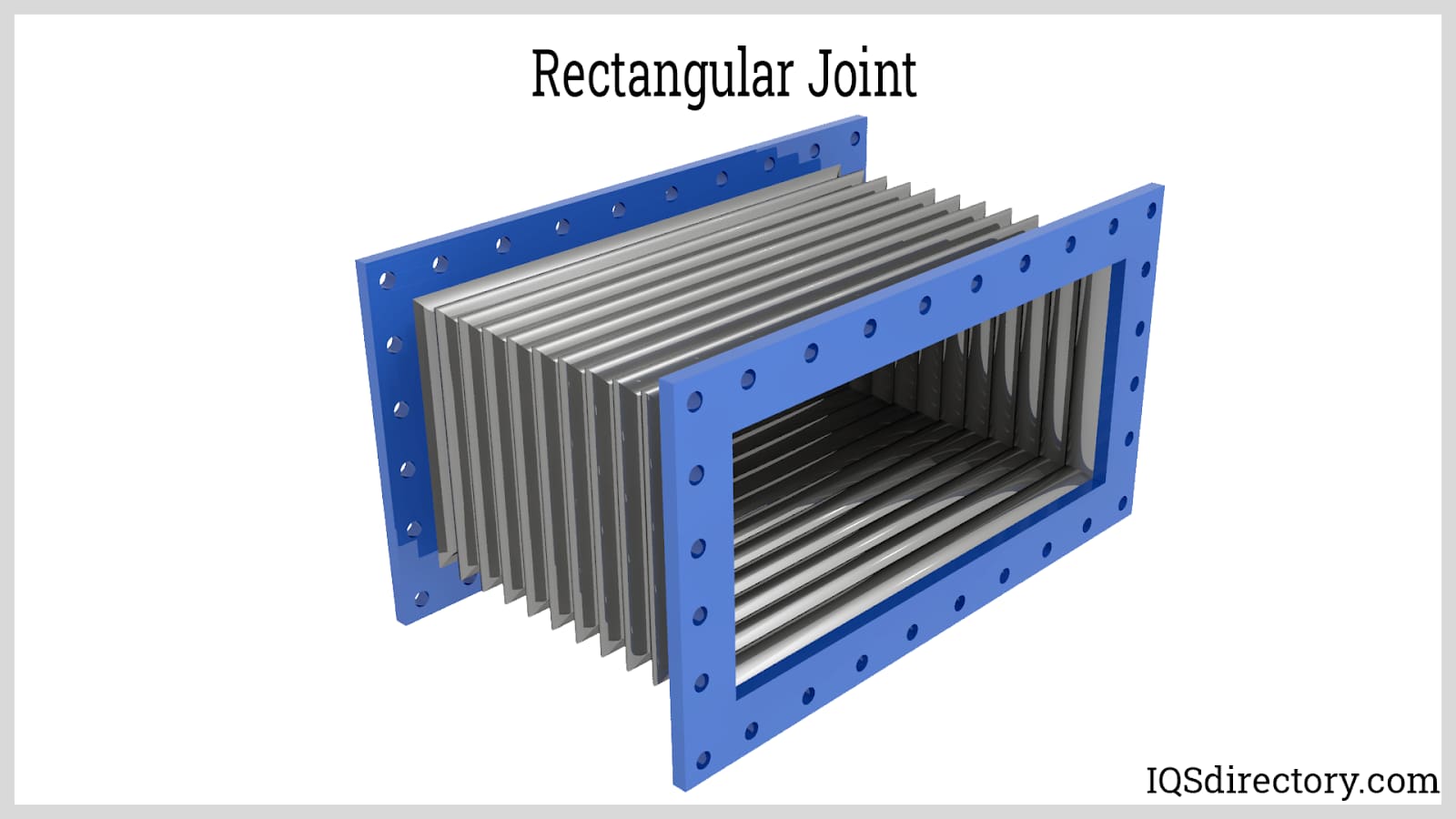
Rectangular metal-pipe expansion joints absorb all of the motions in any one length of piping, regardless of accessories like liners and caps, but they are mostly employed to absorb axial movements. Therefore, they can only be utilized in piping systems that have anchors and pipe alignment guides that are properly built since they do not restrain pressure thrust. Hence suitable anchors and guides must be provided.
The Universal Expansion Joint
The universal expansion joint can absorb axial movements, angular, and lateral movements. It comprises two metal bellows joined together by a pipe in the middle and connectors on either side. The universal expansion joint, a special axial expansion joint, loads the adjacent pipe supports with the axial compressive force brought on by internal pressure and has only a modest amount of pressure resistance for stability reasons. Therefore, the universal expansion joint is typically utilized at low pressure to compensate for significant axial and lateral movements.
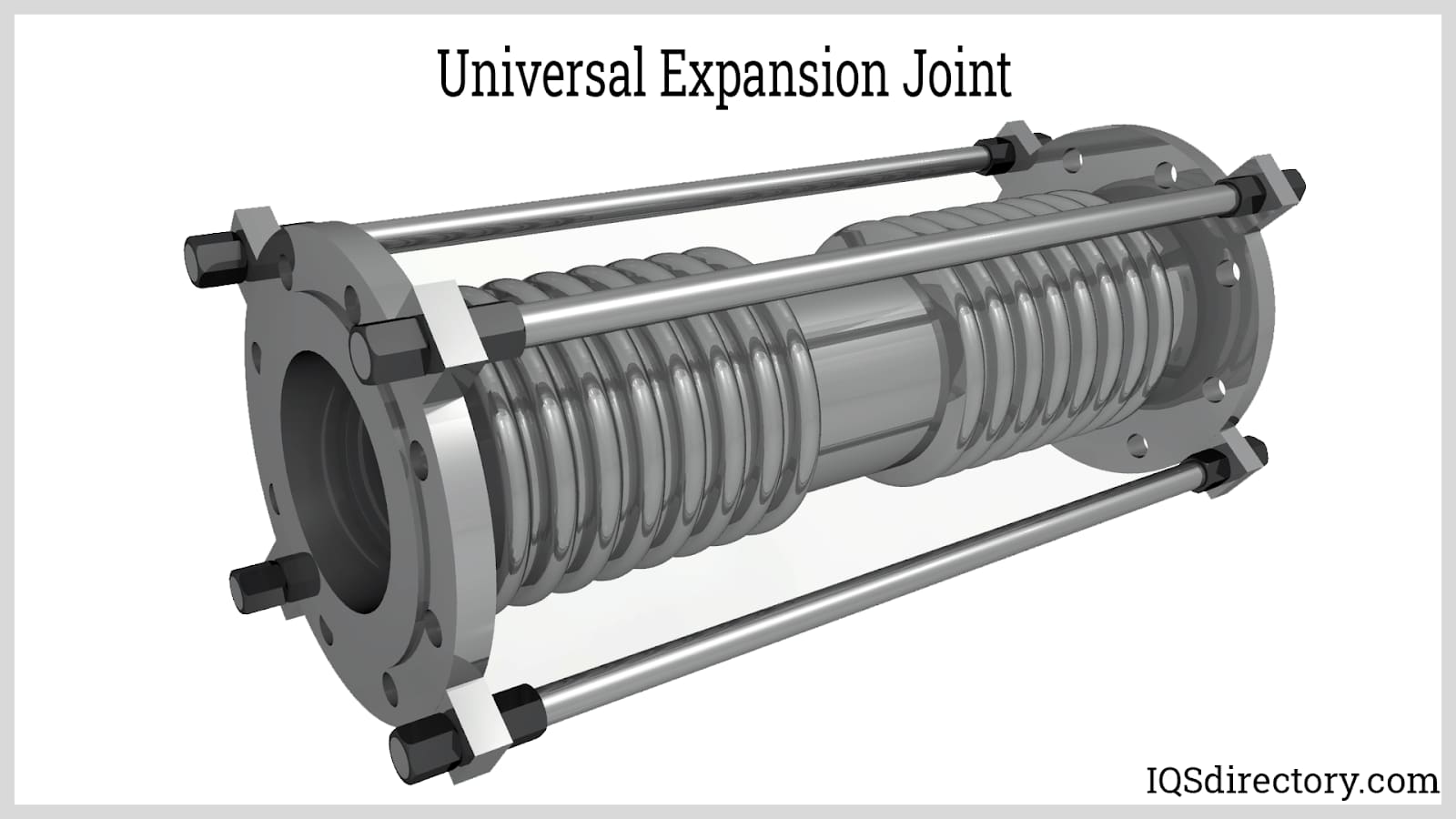
A connecting pipe or center spool connects two bellows that make up a universal expansion joint. Limiting or full thrust tie rods are typically employed depending on the service conditions. Tie rods or limit rods balance out movement between the bellows and stabilize the middle pipe connection. Tie rods are required where it is necessary to absorb full pressure thrust and other externally applied loads. Typically, universal expansion joints are made in multi-plane plumbing configurations, absorbing axial, lateral, and angular movement combinations. As a result, they are incredibly well-suited to absorbing significant lateral motion. In addition, any increase in the length of the center pipe spool results in a proportional increase in the permitted lateral deflection, allowing for a wide range in the amount of lateral displacement.
Refractory-Lined Expansion Joints
Expansion joints with refractory lining are built to endure harsh conditions and are utilized in applications involving extremely high temperatures and pressures. Depending on the temperature, pressure, movement, and flow medium conditions, refractory-lined expansion joints may be hinged, in-line pressure balanced, gimbal, or tied-universal. The metallic expansion joint bellows must lower the temperature of the pipe wall.
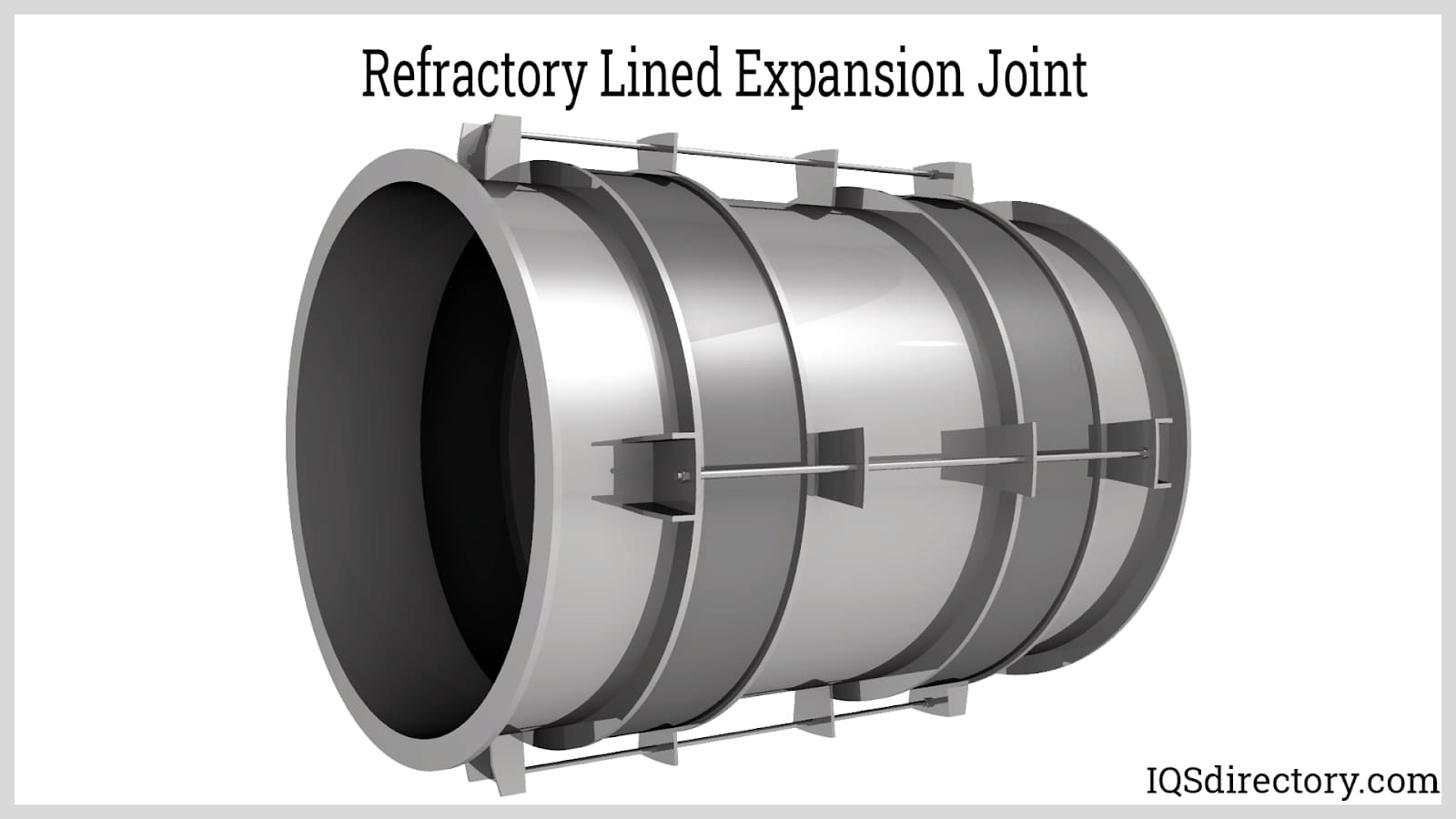
The working lining of a refractory lining is typically followed by a backup or safety layer that comes into contact with the contents of the furnace.
Chapter Four: Benefits and Applications of Expansion Joints
Benefits of Expansion Joints
- Expansion joints and bellows are employed in plumbing systems. They are constructed from add-ons like tie rods, coverings, and flow liners. Although the metal bellows are constrained to control the pressure, they behave like springs. The movement of the connecting pipes is crucial for optimum flow.
- Thermal expansion would result in severe strains if expansion joints were omitted from piping systems. Thermal expansion may generate a great deal of pressure, which may cause pipes to bend and the welds to shatter.
- An expansion joint is created using more than a coil, sometimes referred to as convolution or corrugation. Their grooves are made to withstand the intense pressure of the entire piping system. The bellows assembly is positioned so that it can move in accordance with the associated piping's thermal movement.
- Metal bellows and bellows expansion joints absorb a pipe's thermal expansion in piping systems.
- Pipeline expansion joints are more effective than substitutes, such as pipe bends and loops, due to their improved effectiveness in absorbing larger movements, higher capacity to conserve space, and superior economic efficiency.
- Expansion joints are simple in both form and operation in that they can be directly installed where needed.
Applications of Expansion Joints
- Since power production uses high pressure and temperature, expansion joints are used to assist when pipes expand.
- Co-generation systems producing both electricity and heat simultaneously use expansion joints where the industry faces heat changes.
- In chemical transportation from one place to another, expansion joints are needed to absorb shocks and vibrations.
- Expansion joints are used in transportation of cryogenic gasses. Cryogenics is the study and the production of very low temperatures.
- Expansion joints are used for vessels under pressure and heat exchangers. Vessels under pressure face chances of shaking and that shock must be absorbed by expansion joints.
- Heat exchanging may also lead to the expansion and contraction of pipes which need expansion joints to compensate for this.
- Expansion joints are used in construction and bridges to allow for shock absorption when heavy vehicles are passing.
- Pharmaceutical production utilizes some use of expansion joints in their main robotic plants. Expansion joints are used in hydraulic and pneumatic pipes in pharmaceutical production plants.
- Water treatment plants need a lot of expansion joints to absorb the shock from high flow rate.