Cold Heading & Cold Forming
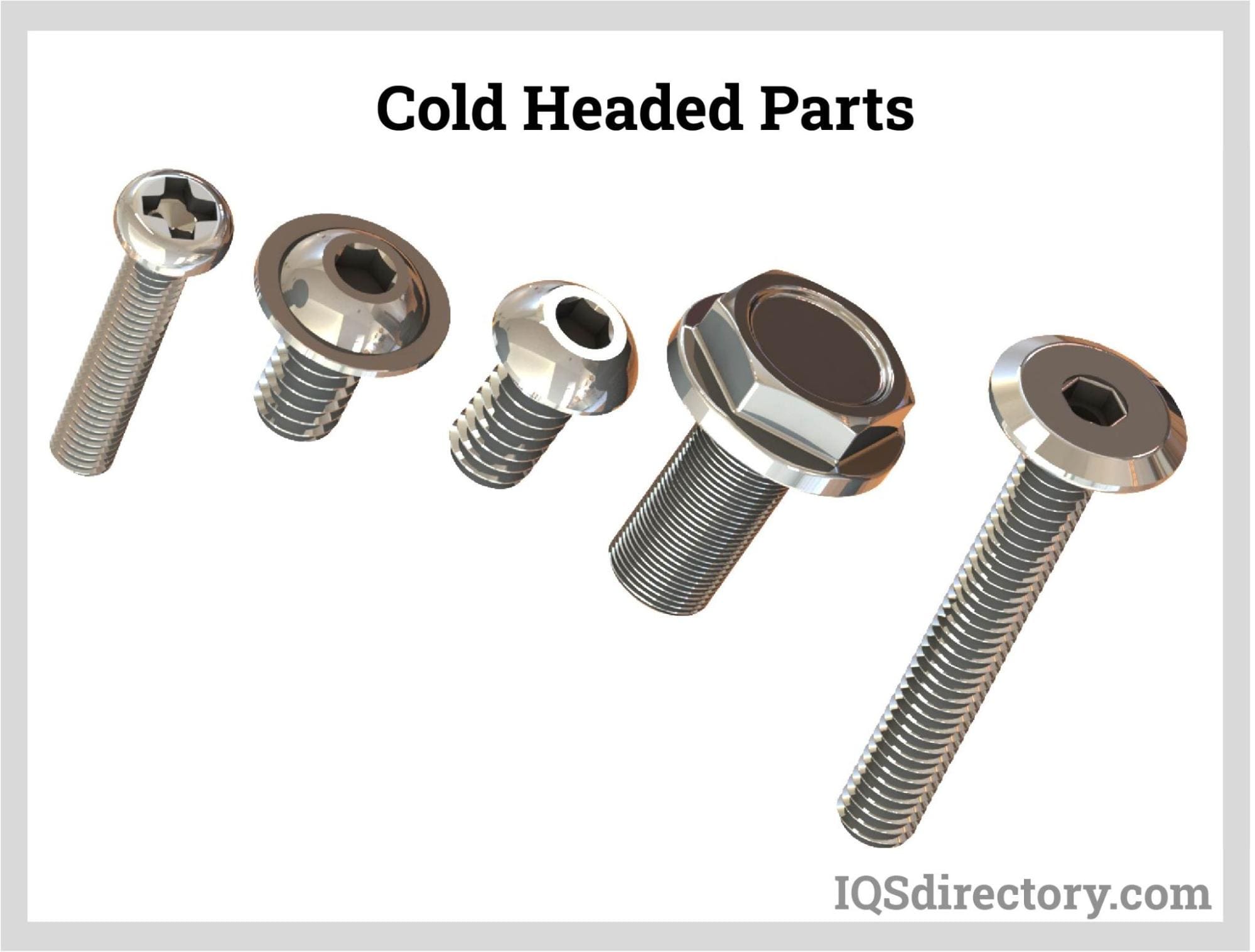
A necessary part of metal production is the forming process that is used to deform metals without removing material or changing its mass. The goal of metal forming is to take a raw piece of metal and shape, configure, and transform it by stressing it through tension, compression, shearing, and pressure.
Since the first industrial revolution, an assortment of metal forming methods have developed. Metal forming begins with a sheet of plain flat metal, which is subjected to forging, rolling, extrusion, drawing, stamping, and an assortment of other methods. Each process is designed to produce a long-lasting metal product.
There are two distinct methods for forming metals, which are hot and cold. The cold process, or cold heading, is completed at room temperature or a little above room temperature. The process of cold heading involves a series of steps that gradually shape the workpiece to the required shape through the use of dies and hammers.
A very popular method for shaping and forming metals is the use of dies, which involves the heating of metals to their melting point and pouring the molten metal into a mold. The majority of die casting is completed using non-ferrous metals such as copper, aluminum, zinc, magnesium, lead, tin, or bronze. The benefit of die casting is the precision of products and parts it produces that extremely close tolerances.
The expanded metal process is a form of cold metal forming where the metal is stretched and pulled. As it is deformed, it is pierced with a blade to create shapes and designs in the metal sheet. The process is less expensive than other methods and can be done on aluminum, various types of steel, and copper. Once the metal has been processed, finishes and coatings can be added for protection or aesthetic value.
One of the oldest forms of metal forming is forging, where a sheet of metal is placed under stress to cause deformation, which changes the grain flow of the metal and forces it to conform to the shape of the forging die. The forging process falls somewhere between cold and hot forging since the metal is not melted but may be heated to make the forging process easier.
Another ancient form of metal forming is grey iron casting, which has been practiced for hundreds of years and should not be confused with forging. Gray iron casting gets its name from the gray color of the metal caused by its graphite content. There are a variety of methods used to produce grey iron castings with sand casting being one of the more common methods.
Investment casting is a process for producing several parts in one casting. The process begins with the creation of a wax model of the part to be formed, which is turned into a mold. The mold is then filled with molten metal to form the final part. The multiple molds are connected by a sprue that is removed after the metal cools.
Metal spinning is a cold metal forming process where a flat metal piece is spun at high speed to be shaped and formed. As the metal spins, pressure is applied using a variety of tools called spoons. The methods of applying the pressure vary from a single tool to several depending on the design of the part.
The powder process of metal forming is another of those methods that has been around for centuries. The process involves the use of metal that has been made into a powder. The powder is fed into a die and placed under great pressure. As the pressure increases, particles are forced to interlock to conform to the shape of the die. To harden the part and increase its strength, it is sintered, a process of heating it just below its melting point.
Roll forming is a cold process where a sheet of metal is fed through a series of rollers that gradually reshape the sheet into a uniform shape. Several metals are capable of being rolled formed, which include zinc, brass, steel, and aluminum. It is a low-cost process that produces close tolerance parts.
There are several other types of processes that are used to shape and form metals to produce items such as springs, various wire forms, and wire mesh. The processes used to create these common items are normally cold forming though some methods may heat the metals to make them more pliable.
Cold headed parts are finished or stock shapes produced through a specialized process more broadly known as cold working. Although cold heading is a popular option, it is part of this larger group of manufacturing processes also referred to as cold forming. As the name would suggest, none of these techniques involve heat, but instead materials are processed and formed at ambient temperatures. While the name might imply that the temperature is further reduced for cold metallurgical processes, most are carried out with machines and materials left at room temperature.
Learn more about cold headed parts.
Expanded metals are made from plate or sheet metal that is perforated by a series of slits, cut along parallel lines, and then pulled or stretched into a mesh.
The resulting piece may be as much as ten times its original width, depending on the length of the cuts, width of the metal between the cuts, and the amount of stretching. It is a light weight, less expensive alternative to solid plates and sheets, and it will not unravel.
The mesh can be used to filter light, air, water, materials, sound, and the view. It is used for decking, fencing, screening, lath, or decoration. It can be made from aluminum, steel, mild steel, carbon steel, stainless steel, copper, or even plastics. A wide variety of finishes may be added, according to design.
The perforation lines may be staggered, which provides the greatest open area when stretched, or the fine lines may be evenly spaced. Typical metal mesh patterns reveal holes with diamond shapes, but other patterns may be produced, as well. Measurements are based on long way diamond (LWD) and short way diamond (SWD) specifications. The size and shape of the opening will be determined by the necessary requirements of the final application.
Standard expanded metals may be manufactured from different thickness of plate or sheet metal with a variety of opening sizes. The SWD bonds and LWD strands that divide the apertures are set at a uniform angle, offering increased rigidity with maximum flow. Because the metal remains a single piece, it provides much higher tensile strength than woven wire of equal weight.
By cold rolling the expanded sheets, they are flattened to create a smooth surface. This process can further extend the length of the piece by as much as five percent.
Perforated metals, not to be confused with expanded metals, are solid metal sheets that have holes of specific design punched out. The material is not stretched in any way. Their uses are similar, but the expanded sheets weigh less, inch for inch, and provide more flexibility.
Learn more about expanded metals.
Metal spinning, often called spin forming, is a cold metalworking process in which a flat metal disc affixed to a lathe mandrel is rotated at high speeds and formed by shaping tools.
A metal spinner applies pressure to the rotating disc, which is called a blank, using several tools, which are called spoons, to shape the metal over a mandrel. This pressure can be applied by a single tool or by multiple tools. The finished product should have no wrinkling or warble, and the process is quick and cost-effective. An average metal piece will take only five to ten minutes to be formed, and very little metal waste is produced per part. Learn more about metal spinning.
Numerous industries utilize solid metal parts made of powdered metal. Powdered metal components, which are made from powdered metal via powder metallurgy, can be found in applications spanning across industries such as lawn and garden, computer, electronics, hardware, and automotive.
More specifically, powder metal parts include magnetic assemblies, filtration systems, structural parts, and automobile components. Powder metal gears are inherently porous and they naturally reduce sound, making them a suitable component to the sintering process. Bearings and bushings can simply be produced by way of sintering, however, they may require a secondary sizing operation because their fabrication leaves little room for error. Learn more about powder metal parts.
Roll formed parts are metal products shaped by a series of rollers, during the process known as roll forming. Most metals can be roll formed, but the most commonly roll formed metals are brass, steel, zinc, aluminum and zirconium.
Roll formed parts are valued for many reasons, among them uniformity, accuracy, structural integrity and low tooling costs. They serve a myriad of industries, such as: building construction and architecture, carpentry, commercial automotives and home improvement. They‘re also used to fabricate a wide variety of commercial, consumer and industrial products.
Examples of common roll formed products for carpentry and building construction include: angle irons, aluminum angles, steel angles, metal channels and metal trim. Angles are designed to provide support in two directions, and frequently feature slots or holes for connecting parts. Learn more about roll forming.
Springs can be found as a necessary component in many devices, machines, and systems. A spring is an elastic device that applies a resistant force when compressed or stretched. Springs are used to store and absorb energy and maintain force or tension in the application for which it is designed.
Some of these applications include circuit breakers, solenoid valves, writing instruments, and electronics. Springs come in four main styles, which are compression springs, extension springs, torsion springs, and flat springs. The combination of a flat spring and a coil spring is known as a constant force spring.
Aside from these four major categories, springs can be found in a wide range of styles. Industrial springs are typically made from thick wire, while smaller springs can be made from wire that is flexible and thin. Some of these springs are too small to be seen by the naked eye. Learn more about springs.
Wire forms consist of various shapes and parts that have been fabricated through the manipulation of wire, which includes anything that alters the shape of the wire such as wire cutting, bending or heat treating. Vital to numerous applications, wire forms serve an extensive range of industries such as: commercial and retail, for wire displays used for product placement such as point of purchase (POP) displays and wire grids; industrial manufacturing, for wire racks and wire shelves that are used in storage systems as well as for wire guards as protective equipment for machinery.
Learn more about wire forms.
Wire mesh is an industrial product of weaved interlocking metal wires welded or sintered into a wire mesh with evenly spaced, uniform openings that is used as a material for a wide variety of filtering, screening, structuring and protecting in industrial, agricultural and residential applications.
In industries like petro-chemical processing, screen printing, pharmaceutical manufacturing and food and beverage processing select wire mesh materials on a case to case basis, depending on their application requirements. Some application require a specific weave pattern. The most common of these are are twilled square mesh weave, plain square mesh weave, plain dutch weave, reverse plain weave and twill dutch weave. Each weave pattern brings something different to the table. For instance, plain square meshes, which are made from shute wires or lateral wires and warp wires or longitudinal wires of equal gauge, are perfect for basic mesh operations. Learn more about wire mesh.