Basics of Wire Mesh
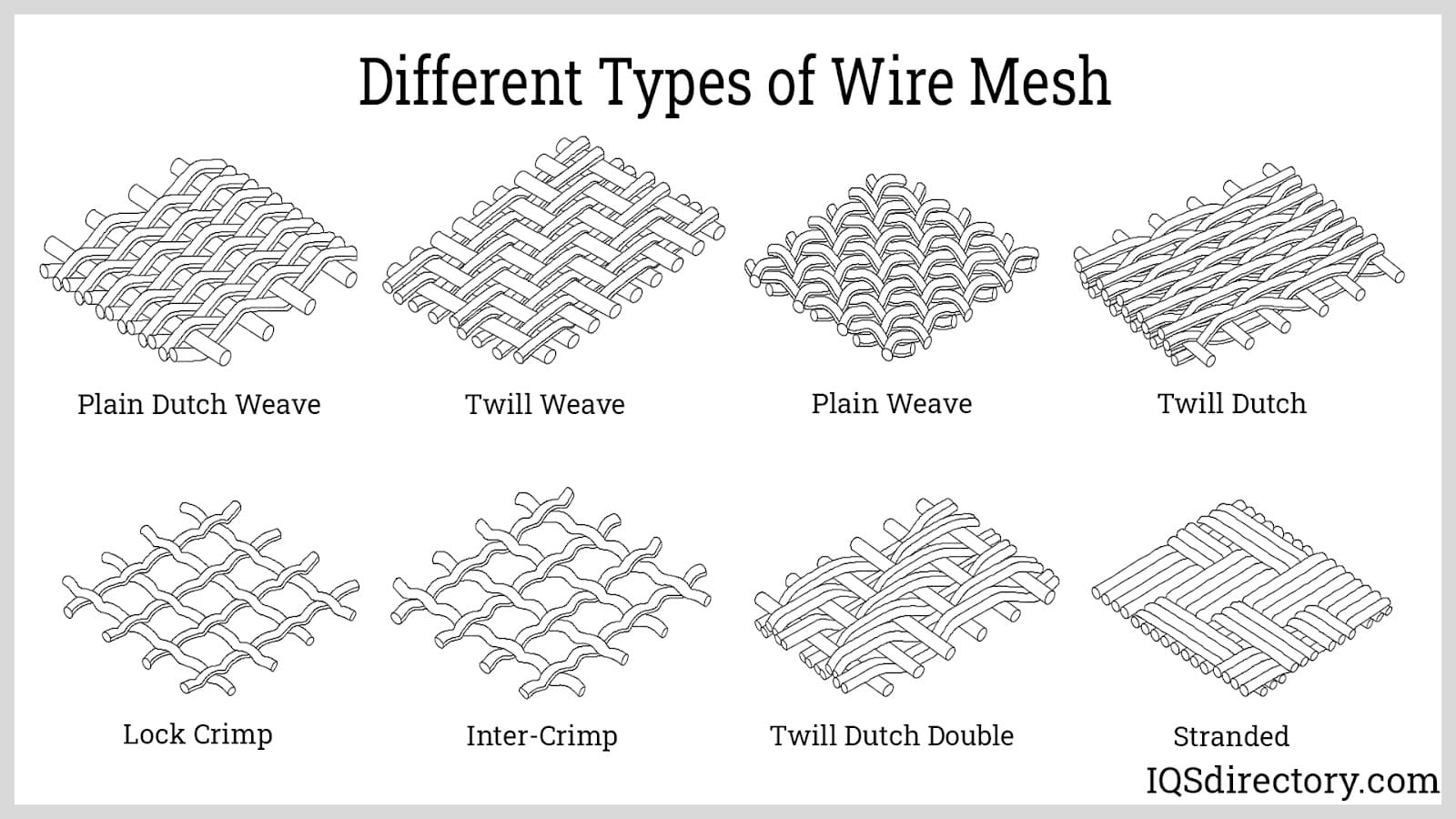
Wire mesh is created by intertwining, weaving, or welding wires of various thicknesses to form evenly spaced parallel rows and intersecting columns. It is also referred to as wire fabric, wire cloth, or...
Please fill out the following form to submit a Request for Quote to any of the following companies listed on
This article provides a detailed look at wire cloth.
You will learn:
Wire cloth is a woven or knitted fabric made from metal wires, commonly used in industrial applications like filtration, sieving, and as a barrier to control the flow of substances.
Wire cloth is available in a range of mesh sizes and wire diameters, making it versatile for various applications. It's commonly used for filtering solids from liquids or gases, protecting machinery and equipment, and separating materials based on particle size. Depending on the application's specific needs, wire cloth can be crafted from different metals, including stainless steel, brass, copper, or other alloys.
These terms are often used interchangeably based on the context and the particular application of wire cloth.
This term is commonly used to describe wire cloth, referring to a woven or welded fabric made from metallic wires.
Wire cloth, commonly referred to as wire screen, is frequently used as a screen or sieve in a wide range of industrial applications.
The term "wire fabric" emphasizes the textile-like qualities of wire cloth, as it is created by weaving or welding wires together.
This term is commonly used to refer to wire cloth when it's utilized for fencing or animal containment, highlighting the material's net-like structure.
Wire cloth, often called a wire grille, is frequently used in architectural and decorative applications, such as grilles for doors and windows.
Wire mesh and metal cloth are produced using a range of different base materials:
Metal and alloy wires are produced through a wire drawing process. In this process, a metal rod or larger wire is drawn through a series of progressively smaller dies to decrease its diameter and create a finer wire.
Although the process resembles metal extrusion, in wire drawing, the metal is pulled rather than pushed, which helps to minimize the reduction in area or diameter. Excessive reductions can cause the wire to yield. Typically, industrial wire drawing achieves area reductions between 15% and 45%.
Wire drawing imparts a great amount of cold work and strain hardening. The cold work can produce high carbon steel wire with extremely high strengths of 580 Ksi (4000 MPa).
Metal wire is commonly round in cross-section, but it can also be manufactured in various shapes. After drawing, wire can be rolled with smooth rollers to create flat wire with rounded edges. Using contoured rollers, wire can be shaped into square, rectangular, oval, hexagonal, or triangular cross-sections.
Metal sheets and foils can be used to create mesh or screen-like materials. Metal sheets are made by cold rolling, where an alloy is pressed between steel rolls to thin and shape the metal. While hot rolling can achieve annealing or recrystallization during the reduction process, it typically results in a surface finish and tolerance that are not as refined as those from cold rolling. Depending on the alloy and the extent of reduction, intermediate annealing steps may be necessary.
Metal sheets and foils can be slit into narrow ribbons or flat wire-like shapes. Additionally, metal sheets can be perforated and expanded to create nonwoven metal fabrics, such as mesh or screens.
Metal or metallic fibers are defined as any manufactured fibers made entirely from metal or alloys, including metal-coated plastic fibers and plastic-coated metal fibers. These metallic fibers serve as a raw material for producing wire or metal cloth.
Metallic fibers are finer than most metal wires. Metallic fibers typically have diameters ranging from 1 to 100 microns (0.00004 to 0.004 inches). American Wire Gauge (AWG) sizes range from 40 to 0000 (4/0 or “four aught”) gauge (0.0031 to 0.46 inches).
Metallic fibers are produced through various methods, including:
Thousands of wires are packed into a tube, which is then drawn through a die. The tube is subsequently removed by acid etching, leaving behind metallic fibers. This process produces octagonal fibers with diameters as small as 200 nanometers.
Fibers as fine as 14 microns are created through a foil shaving process. In this method, steel wool is formed by cutting wire, and the resulting fibers feature a triangular cross-section. This unique shape enhances the cutting and cleaning efficiency of the steel wool.
The machining process can create fibers as small as 10 microns with remarkable stability.
Molten metal is poured onto a cooled, spinning copper roll, which produces fibers ranging from 40 to 250 microns.
Carbon or polymer fibers can be coated with metal through various techniques, including electrodeposition, electroplating, and thin film deposition methods such as PVD or evaporation.
In many industrial applications, wire is utilized as monofilament to create or weld wire cloth materials. Wires can be twisted together to form strands or multiple wire bundles.
Strands are also combined to create wire rope, a structural component used to support suspension bridges. In certain architectural applications, wire cloth made from strands and/or wire is utilized where enhanced strength or the appearance of strength is needed.
Metallic fibers can be utilized directly to create metal cloth or twisted into metallic yarns. This yarn is then woven to produce metal fabrics with a finer weave compared to traditional wire cloth. Metallic fiber textiles are effective for filtering finer micron particles. Additionally, they are employed in various applications such as electrical cables, fuel cell electrodes, fire protection systems, high-temperature insulation, EMI/EMC shielding, and composite reinforcement.
Blends or hybrid weaves incorporate one metal wire or metal fiber interlaced with non-metallic fibers, yarns, strands, or monofilaments. These weaves are employed in specialized applications where neither metal nor synthetic fibers alone are adequate. The non-metallic components can include natural fibers like cotton and silk, as well as glass fibers, ceramic fibers, carbon fibers, and synthetic materials such as polyamide (nylon), polyester, polytetrafluoroethylene (PTFE), and polyetheretherketone (PEEK).
Aluminum is among the lightest structural metals, with a density that is 35% lower than that of steel. It boasts high ductility, making it easy to shape and form.
Aluminum offers better corrosion resistance compared to steel, particularly when anodized. However, it does not match the corrosion resistance of stainless steel. Additionally, aluminum is softer and more susceptible to abrasion and wear.
Aluminum is valuable for architectural and aerospace applications, but its alloy is not suitable for filtration or screening of powders or solids.
Copper boasts excellent electrical and thermal conductivity, with only silver surpassing it among pure metals. This superior conductivity makes copper ideal for conductive braids, electrodes, and various electrical and shielding applications. However, its softness and lower tensile strength can restrict its use in filtering and screening applications.
Copper possesses antimicrobial and anti-fouling properties, making it increasingly valuable in hospitals and medical devices. These properties help ensure that surfaces contacted by patients and healthcare professionals are safer and more hygienic.
In seawater, copper wire mesh screens are resistant to fouling and will not accumulate barnacles or marine growth. Copper root barrier screens are designed to prevent tree roots from penetrating beneath sidewalks and pavement. The roots will encounter the screen and cease to grow further.
Copper can be treated to develop attractive patina colors, making it ideal for consumer product designs and architectural applications.
Brass is an alloy composed of copper and zinc, with zinc enhancing the strength of copper. Compared to pure copper, brass is easier to cast, machine, and work with. Brass is categorized into high and low brass based on zinc content, with high brass containing more than 33% zinc. The terms "high brass" and "low brass" originate from the era when shotgun shells were made from paper.
Bronze is an alloy composed primarily of copper combined with tin, silicon, aluminum, lead, chromium, zirconium, and other metals. These alloying elements enhance the metal’s strength and give it specific properties based on the elements used. Compared to pure copper, bronze can be easier to work with due to its improved machinability and versatility.
Phosphor bronzes are composed of tin and a small amount of phosphorus, which enhances their properties. These bronzes are particularly well-suited for weaving into very fine mesh screens due to their strength and resistance to cold working. Compared to brass, phosphor bronze offers superior durability and is commonly used to manufacture fine Fourdrinier wire screens for papermaking.
Bronze can be treated to develop stunning patina colors, enhancing its appeal for consumer products and architectural designs.
Galvanized steel is coated with zinc to safeguard the underlying steel wire. This coating process is achieved through methods such as electrogalvanization or molten zinc dipping. Zinc dipping provides a thicker coating, offering extended protection for the steel. Galvanized steel can be used to create woven wire cloth. However, welded wire cloth cannot be manufactured with galvanized steel wire due to:
Welded wire mesh is usually galvanized after welding to overcome these problems.
Nickel and nickel alloys have outstanding high temperature strength and oxidation resistance properties even at red hot temperatures. Nickel alloys also have excellent corrosion resistance in acid and chemical environments where other metals fail. Nickel alloy mesh, filters, and strainers are used in chemical process and aerospace applications. InconelⓇ and HastelloyⓇ are common nickel based alloys.
Monel is an alloy composed of copper and nickel, renowned for its exceptional corrosion resistance. It retains some of the antimicrobial properties of copper. Due to its durability and resistance to harsh environments, Monel wire mesh and nickel materials are frequently utilized in food processing application.
Stainless steel is an iron alloy containing at least 10.5% chromium. When the alloy is cut or ground, it quickly forms a protective oxide film. This passive chromium oxide layer helps prevent further corrosion. Additionally, the inclusion of nickel in stainless steel stabilizes the austenite phase, enhancing its ductility and formability. Nickel also contributes to improved corrosion resistance.
Austenitic stainless steel alloys must contain at least 12% chromium and low carbon levels to ensure passivity and corrosion resistance after welding. Common welding grades include 304L, 316L, and Columbium-stabilized 347 stainless steels. The 304L grade, also known as 18-8 stainless steel, comprises approximately 18% chromium and 8% nickel. The 316L grade contains higher nickel levels (10–12%) and includes molybdenum (2–3%), making it more suitable for environments with chlorides, such as saltwater.
Stainless steel wire cloth and metal mesh are used in various applications, including chemical processing filters and strainers. They are also employed in architectural fabrics to diffuse light and add decorative elements.
Low carbon steel is highly malleable and cannot be hardened through heat treatment. In contrast, high carbon and alloy steels can be hardened to achieve high levels of strength and hardness. High carbon steel, in particular, can be drawn through dies to produce extremely strong wire.
Titanium offers superior corrosion resistance compared to stainless steel and is significantly lighter, with a density that is only 60% of steel’s. Its exceptional fatigue strength and high strength-to-weight ratio make titanium and its alloys highly valuable for aerospace applications.
Titanium's exceptional corrosion resistance makes it ideal for chemical process applications where stainless steels are inadequate. It performs well in environments with seawater and other chloride salt solutions, hypochlorite, wet chlorine, nitric acid, and even fuming acids.
Titanium offers superior biocompatibility compared to stainless steel. Therefore, a woven titanium mesh is a preferable option for implant applications.
Here are some common uses for different types of wire cloth:
The two major construction types of wire cloth, metal cloth, and wire mesh are:
Woven metal cloth is created by interlacing two or more sets of wire, usually at right angles. The warp wires or yarns run parallel to the length of the cloth, while the perpendicular or crosswise wires, known as weft, fill the gaps between the warp wires. When metal fiber yarn is used instead of traditional wires, the resulting metal cloth features a fiber-like texture and a higher fiber density, closely resembling conventional synthetic fiber cloth. In contrast, woven wire mesh presents a coarser, more open appearance.
Nonwoven wire cloth is produced through various methods, including knitting, stitch bonding, welding, expanding (via punching and stretching), perforating, electroforming, chemical milling, photochemical etching, and laying metallic fibers into a felt mat.
Welded wire cloth, also known as welded wire mesh, is a type of nonwoven metal mesh where wires are joined by welding. In this mesh, one set of wires runs either perpendicular or at an angle to another set. The welds are created at the intersections where the wires cross. Compared to woven wire cloth, welded wire mesh offers greater strength and durability. A particle or object can push through a woven screen by shifting the wires apart. However, with welded wire cloth, the openings cannot be expanded without breaking the welds. This makes welded wire cloth ideal for applications involving high pressure or conditions that could damage a woven mesh.
Metal wires and fibers can be joined using solid-state welding or diffusion bonding techniques. Initially, the wire is woven, knitted, braided, or arranged into a nonwoven batt. This metal mesh or fabric is then placed into a furnace with a controlled atmosphere to prevent oxidation during sintering. During the sintering process, surface energy facilitates diffusion, leading to the rearrangement of metal atoms.
In braided metal or wire cloth, strands, yarns, or wires are interwoven in an alternating zigzag pattern. The three-strand braid is particularly common and is often used to create ropes. Various complex braid patterns are employed in industrial applications. Compared to woven fabric, braided cloth offers greater flexibility and stretchability.
After braiding, metal strands are frequently flattened or calendered. Braiding is employed to create metal ropes, cords, flexible conductive straps, and protective sleeving.
Protective sleeving is commonly woven into a tubular form. Braided metal fiber sleeving, in particular, is utilized as an outer layer for hoses, data cables, and electrical cables. It offers critical protection by providing cut resistance, abrasion resistance, and shielding against electromagnetic interference (EMI) and radio frequency interference (RFI).
Braided copper conductors, or copper braids, are utilized to link conductive electrical power components in scenarios where movement occurs between the conducting parts. This type of copper can withstand repeated flexing without becoming work-hardened or breaking. Additionally, braided copper is commonly used for flexible grounding straps, offering durability and flexibility for various applications.
Knitted metal cloth is made by interlacing loops of wire or yarn to create its structure. This method gives the cloth greater flexibility and stretch compared to woven fabrics, as the loops can slide against each other. The main types of knitting processes used in creating such fabrics include warp knitting, weft knitting, and stitch bonding.
Stitch bonding is employed to create high-strength industrial textiles and composite reinforcements used in aircraft and wind turbine applications. This process involves joining or stitching together multiple fabric layers with a knitting thread, resulting in stitch-bonded fabrics that offer enhanced durability and performance.
Metal wires or fibers can be arranged to create a nonwoven metal fiber batt or mat. Since the fibers are not bonded together, nonwoven metal fiber mats are commonly stabilized using needle punching. In this process, a barbed or forked needle repeatedly penetrates the nonwoven metal fiber web and then withdraws, causing mechanical entanglement. Needle plates, equipped with over 100 needles per inch, punch the fiber batts at a rate of 2,000 strokes per minute.
The metal cloth products mentioned above begin with metal wire or metallic fibers that are woven or processed into a mesh or fabric. Expanded metal, perforated metal, and chemically milled mesh all start with sheet metal as their raw material.
Expanded metal is produced by cutting small slits into a metal sheet and then stretching the material to create openings. This process typically results in diamond-shaped openings in the metal. One of the advantages of expanded metal is that it generates minimal to no scrap during manufacturing.
Perforated metal is created by punching holes into metal sheets using a steel or carbide punch and die set on a high-speed punch press. This method, known as punching and blanking, is a cost-effective way to quickly produce holes in metal sheets and plates. The punched-out material, known as the plug, is considered waste or scrap. Compared to expanded metal, woven wire mesh, and welded wire cloth, perforated sheet metal has a thinner profile, offering a more streamlined appearance.
Chemical milling and electroforming are ideal for creating extremely fine mesh or products with very small hole sizes.
When the wire diameter of wire cloth or the hole size of perforated metal becomes too small, manufacturing these products through weaving and punching becomes challenging. Extremely fine wires and punches are prone to breaking easily during production.
Chemically milled mesh is created by applying a masking material to sheet metal. This masking can be selectively applied using screen printing or photolithography techniques. Areas not covered by the masking material are then etched away or removed using an acid bath. Chemical milling allows for the creation of intricate patterns, including holes, slots, star-shaped openings, and various perforations.
Electroformed mesh is produced through the electrochemical deposition of mesh material onto a conductive pattern, mold, or mandrel. Once the deposition is complete, the pattern or mold is removed using methods such as melting, etching, or chemical dissolution. This process allows for the creation of mesh openings as small as 5 microns.
Electroforming utilizes distinct raw materials and chemicals for electro deposition or electroplating, setting it apart from other metal mesh or cloth products. The process involves ionic aqueous solutions or dissolved salts from the metal being deposited, which are essential for the electroplating process.
Electroforming achieves greater detail in metal patterns compared to chemical milling, etching, stamping, or machining. This method provides exceptional edge precision, with edges nearly free of burrs and typically exhibiting a variance of less than 0.5 microns.
Molds or patterns are frequently created using photolithography techniques. Because electroformed parts utilize a reproducible mold or pattern, they can consistently replicate highly detailed and complex mesh patterns. Electroforming enables the production of intricate shapes that are difficult or impossible to achieve with other manufacturing methods.
Woven wire cloth is available in a range of standard weaves, with many metal cloth manufacturers offering proprietary designs as well. Additionally, custom weaves can be created to fulfill the specific requirements of both demanding industrial applications and architectural projects with unique aesthetic needs.
The four most common wire cloth weaves are:
In plain weave or square weave, parallel warp wires alternate between running under and over the cross, fill, or shute wires. This interlacing pattern creates a basic and widely used type of wire cloth weave.
Dutch weave, also known as plain Dutch weave, resembles the plain weave pattern but features a notable difference: the warp wires have a significantly larger diameter than the weft or cross wires. Additionally, the weft wires are tightly packed together. This combination results in a dense, high-quality material that excels in filtration applications.
Twill weaves feature a pattern where two adjacent warp wires pass under the fill or weft wires, followed by two adjacent weft wires passing under the warp wires. This pattern allows twill weaves to handle larger wire diameters while maintaining a specific mesh size. Compared to plain weaves with the same wire diameter, twill weaves offer greater flexibility.
Dutch twill weaves integrate both twill and Dutch weave patterns.
Here are a few of the less common weaves:
Broad and oblong weaves feature rectangular openings. They are often referred to as off-count mesh due to the uneven mesh count in the parallel warp and crosswise shute directions. Broad weaves have a lower number of warp wires, while oblong weaves have fewer shute or weft wires.
Optimized weaves enhance filtration efficiency by increasing the number of warp or weft wires until they make contact. This results in smaller apertures and improved flow rates.
Reversed Dutch twill weaves and reversed plain Dutch weaves are types of reversed weaves. Reversed plain Dutch weaves feature a higher number of warp wires and fewer shute or weft wires. These weaves offer greater strength, making them suitable for demanding applications where backwashing, filter cake removal, and cleaning processes exert mechanical stress on the wire weave.
Stranded weave consists of multiple strands of wire for each warp and shute wire. Its surface resembles the appearance of Parkay wood flooring.
5-heddle weaves, also known as 5-shed twill weaves, feature warp wires that pass over four shute wires and under one shute wire. These weaves have a smooth surface on one side, which makes it easier to remove filter cakes from the smooth surface of 5-heddle weaves.
3D and volumetric weaves employ specialized proprietary weaving technology to create a mesh with a three-dimensional structure. These weaves offer significantly higher volume porosity compared to conventional media of the same wire diameter, making them ideal for filtration applications. Additionally, they can help reduce pressure loss in filtering processes.
Multi-layer wire mesh laminates consist of several mesh layers bonded together using methods such as sewing, welding, sintering, fastening, or adhesive bonding. A finer mesh cloth can be attached to the top of a larger diameter wire mesh screen. The larger screen provides support for the finer mesh during filtration processes, preventing it from bowing or breaking.
Ribbon weaves, or cable weaves, involve warp metal ribbons or flattened wires interwoven with round shute or weft wires. These weaves are particularly effective for facade and wall cladding applications where security, privacy, light diffusion, and protection from wind and sunlight are required.
Cable mesh consists of stranded wire woven into a square or diamond pattern. The intersection points can be secured using ferrules, cross clips, bolts, interweaving, or welding.
Spiral weaves are created using wires that are crimped or formed into a spiral shape. The V-shaped wires are threaded or woven in a spiral pattern, interlocking with each other. This technique is commonly used for manufacturing endless process belts and chain link fencing. Spiral woven belts can feature interconnected spiral wires along with additional "shute" rods. Hexagonal wire netting, or "poultry netting," is also produced through a spiral winding process, where wires are twisted at intervals, shifted forward, and then twisted in the opposite direction. Additionally, spiral weaves are employed in architectural applications for light diffusion and decorative facades.
Specialized weaves are created by combining two standard weave patterns.
A wide range of proprietary and custom weave and woven metal cloth types can be developed by varying the weaving patterns, wire sizes, wire shapes, and wire materials.
Woven wire cloth can utilize either crimped or non-crimped wire. The crimping process introduces bends, undulations, or kinks into the wires, which helps interlock the parallel and crosswise wires. Crimped wire features a wave-like or sawtooth profile. Typically, the crimping is done prior to the weaving process.
Crimping reduces wire movement, ensuring more consistent and accurate openings. A sharp point or awl can penetrate non-crimped wire mesh more easily than crimped mesh.
Various crimping methods can be employed, including:
Without crimping or pre-crimping, the wires remain free to move. This results in wire cloth that may offer greater flexibility or adaptability compared to crimped or welded mesh.
Pre-crimped wire is typically used for coarser diameter or gauge wire cloth. This type of mesh is more rigid compared to non-crimped mesh.
Lock crimp features a precise crimp shape that securely "locks" the wires at their intersection points, holding them tightly in place.
Intercrimp, intermediate crimp, or multiple crimp wire cloth features more frequent crimps, with wire intersections occurring at every 3rd, 5th, 7th, etc., crimp. This type of mesh has additional bends or corrugations between intersections. Intercrimping enhances rigidity and accuracy, particularly when weaving large opening wire mesh with fine wire gauges.
Flat top mesh utilizes downward crimps or corrugations that alternate between the warp and shute wires, resulting in a flatter surface with fewer undulations.
The most common characteristics used to specify metal cloth or wire mesh include metal alloy types, mesh count, wire diameter, percent open area, and weave type.
The significance of specific specifications varies depending on the intended industrial application. For example:
The diameter of round wire or the width of flat wire or ribbon is a crucial specification for wire cloth. Although some manufacturers may use "wire gauge" to indicate wire size, this can be confusing due to the variety of gauge systems available. To avoid confusion, wire diameter should be specified using a precise numerical value in inches or microns.
Mesh size, wire count, or mesh count refers to the number of wires per unit length, typically measured in linear inches, and is determined from the center of one wire to the center of the next. For wire mesh cloth with large openings, the specification is based on the distance between adjacent wires, such as 1-inch mesh, 2-inch mesh, or ⅝-inch mesh.
The percent open area of wire mesh cloth is determined from the width or dimension (W1) of the openings between adjacent parallel wires. For mesh with square openings, the opening area is calculated as W1 × W1. For meshes with rectangular openings, the area is calculated using W1 × W2.
The percent open area is calculated by dividing open area by the total area of the wire cloth. In summary:
The opening size of wire cloth, mesh, or screen refers to the dimension between two adjacent wires, measured from edge to edge. This differs from mesh size, which is measured from the center of one wire to the center of the next. Wire cloth openings range from 20 microns to 5 inches. Electroformed mesh can have standard catalog openings as small as 5 microns. For finer mesh, sieves, screens, and wire cloth, the opening size is specified in microns.
The shape of the openings is an important specification for decorative and architectural applications. It can also be a key factor in applications where wire cloth screens are used to produce elongated particles in powders or granular materials. Opening shapes include:
How is mesh size utilized in industry?
Wire cloth can be categorized into two primary application fields:
Architectural applications encompass:
Industrial applications include:
When choosing a supplier for wire cloth, it's important to consider their secondary processing capabilities. Wire cloth requires different forming and fabricating techniques compared to sheet metal. If your application involves fabricating components from wire cloth, selecting a vendor with expertise in processing, treating, cutting, forming, and joining wire cloth would be advantageous.
Value-added processes that can be applied after weaving or welding include:
Wire mesh is created by intertwining, weaving, or welding wires of various thicknesses to form evenly spaced parallel rows and intersecting columns. It is also referred to as wire fabric, wire cloth, or...
Hardware cloth is a woven mesh constructed by interlacing wires of different sizes to create a metal fabric used in applications such as animal cages, fencing, strainers, and filtering screens. The distinctions between the various types of hardware cloth include...
The term "wire mesh" refers to two- or three-dimensional structures made from two or more metallic wires interconnected through various techniques. Wire mesh products are utilized in a diverse array of applications, including...
Welded wire mesh consists of wires that are welded at their intersections. The size of the openings varies depending on the type of wire used and the intended function of the mesh. Regardless of its dimensions or wire type, welded wire mesh is durable and permanent.......
Expanded metal is a type of sheet metal mesh created by stretching a slitted sheet of malleable metal. The slits are aligned perpendicular to the stretching direction. This process results in an array of holes along the slits, forming a mesh structure....
Perforated aluminum is made by manually or mechanically punching an aluminum sheet using CNC (computerized numerical control) technology to create a range of shapes and patterns in various sizes....
Perforated metals are sheets of metal with decorative shapes and holes punched or stamped into their surface for both practical and aesthetic purposes. The perforation process produces a variety of geometric patterns and designs....
Perforated metal refers to sheet metal that has been stamped, fabricated, or punched to create patterns of holes, slots, and various decorative shapes. The perforation process can utilize a wide range of metals, including steel, aluminum, stainless steel, copper, and titanium....
Perforated stainless steel is cut, punched, or stamped to create a precise pattern of holes or apertures. It serves both functional purposes, such as filtration or ventilation, and aesthetic purposes, such as architectural accents...
Perforated metals are sheets that have had decorative shapes and holes punched or stamped into their surface for both practical and aesthetic purposes. The perforation process creates various geometric patterns and designs...
Wire baskets are constructed from wires that are either woven or welded together to form a basket shape. They can also be described as containers made using an openwork pattern of metal...
Wire shaping is a versatile process that involves creating a variety of dimensions, forms, and textures. The technique of bending and shaping wire to produce functional items is referred to as custom wire forms...
Wire forming is a process that involves applying force to alter the contour of wire through techniques such as bending, swaging, piercing, chamfering, shearing, and others. These techniques can create a wide range of shapes, forms, and configurations...
A wire handle is affixed to a bucket, pail, or other containers to facilitate lifting and transport. These handles are constructed from durable and sturdy metals, designed to support the weight of several pounds...
A wire rack is a flat wire structure used for storing and displaying a variety of products, typically in retail settings. The bottom surface, which supports the items, is composed of multiple latticed or interwoven metal strands...