Wire Baskets
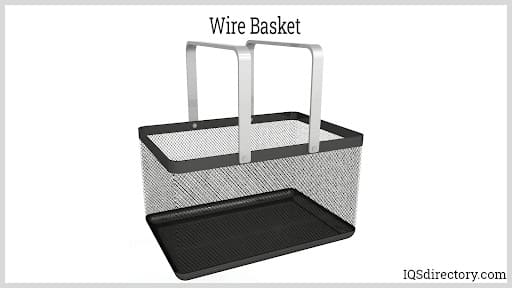
Wire baskets are made from a series of wires that are woven together or welded to form a shape of a basket. They can also be defined as containers that are made by use of an openwork pattern of metal...
Please fill out the following form to submit a Request for Quote to any of the following companies listed on
This article will take an in-depth look at wire racks.
The article will bring more detail on topics such as:
This chapter will discuss what wire racks are and their forming process.
A wire rack is a level wire form utilized to stock and exhibit a number of products, usually retail. The bottom surface on which such goods are stored is made of several latticed or interlaced metal strands. Although they’re similar to wire shelving, since they are both designed for taking full advantage of horizontal and vertical space, the term ‘wire rack’ more frequently refers to miniature units or ledges not made to stand alone.
Wire racks offer extra vertical storage as required for exhibition or storing of retail or commercial goods because they are frequently constructed with many tiers, or they are stackable. As an extra to promotional usage, industrial uses of wire racks are vast. For instance, drying and cooling racks are generally constructed of wire since it offers support yet maintains air flow to the products, for example baked goods.
While storing racks are mostly horizontal, cooling and displaying racks are at times to some extent tilted, allowing products or surplus products to slide forward. Other tilted units and wire racks regularly undergo wire bending to produce a curve or forward lip that will prevent products from sliding entirely off of the shelf.
Extra finishes such as painting, coating, threading heat treatment, and electro-polishing may be done during rack manufacturing to best suit a needed application. Caster wheels may also be installed to the bottom of each supporting bar in full rack units in order to maximize mobility.
Wire racks are made from wire forming. Wire forming is a process of acquiring a wire, from either a blank length or spooled coil, and bending it into definite forms. Wire forms are particularly flexible, enabling them to be changed into a vast variety of shapes and particular configurations.
Wire forms can be coiled, angled, bent, or cut in all different ways, making them perfect for customized projects. Whether formed into small springs for machinery pieces to big chains for carrying heavy objects, to wire racks for storing products for retail or commercial, wire forming is beneficial for multiple applications.
Wire racks require wires that are bent into particular shapes. There is an artistic way to bend the wire. The wire has to be bent outside its yield strength, but in the range of its tensile strength. In other means, the wire has to be bent to attain the needed angle without it breaking or letting it return to its initial shape.
As discussed before, wire forming describes the shaping of wires into a certain configuration. In this case, turning a piece of wire into an interwoven rack. This wire forming process is done by machines.
The wires can be bent up to 1 ½ inches in diameter. Using these machines allows bending of numerous wires in a short duration of time.
In the wire forming and assembly processes of wire racks, the optimum experience can be managed by:
The processes involved in wire forming for making wire racks include:
CNC bending is an abbreviation for "computer numerical controlled" bending. A modern day CNC wire bending machine, which is very common in today's production industries, is made up of a few critical components.
Together, these five critical components can create the most complicated forms and wire shapes. These components include:
The computer uploads the specifications to the CNC machine. Next, the wire forming CNC machine uses a system to uncoil the raw material from the spool and (using the robotic arm) force it via a number of opposing wheels (or servo-driven rollers) that are utilized to straighten the wire before the shaping and forming step.
Once a straight wire is fed between the straightening servo-driven rollers it is then pushed to an articulating head but through a number of pins and dies the head twists and spins around the straight wire while forming the wire in a number of pre-programmed bends. Once the piece is done to length, an automatic shearing blade is utilized to cut the wire off from the coil’s length and to the accurate desired size. This produces wires with the correct dimension and shape every time. Wire forming can bend a wire in any way: down, up, right, or left. It can bend a wire at any angle.
There are many types of wire benders available on the market, some of them are too limited in their scope and application. These 2D bending machines do not allow wire forming to be in anything other than a flat pattern. The more cutting-edge 3D benders offer an unlimited ability in wire bending in 3 dimensional space. These 3D Benders are much more preferred bending machines for wire forming requirements in the world over, enabling for complete adaptability in programming and design.
The earliest technique for wire forming is done by hand machines, which features a spindle and hand lever. Manual machines may be rotary die or drawn and have gears that increase the facilitated bending pressure.
Four-slide forming or stamping uses the identical process as a level stamping press with the inclusion of cams. Together with the cams, the system contains shafts, an electrically powered motor, a press, a die, and sliding gear. The process has four sliding gears which shape the wire from four sides. This amplifies the production speed.
About 3,500 easy wire forms may be made in an hour. The cam controls the movement of the four gears, which allows the process to have vertical movement, including punching, with a horizontal movement in numerous directions.
In the wire bending manner, the wire may be formed into countless configurations to shape anything. Diameters of 0.016 inches (0.41 mm) to 0.625 inches (1.59 cm) or 0.4 mm to 16 mm, maybe fashioned without a problem. Since the bend inside the wire is made before the wire is cut, the method has no waste or scrap and does not require secondary finishing.
In a hydraulic wire forming system, a hydraulic motor is utilized to energize the shaping rollers. A servo motor with CNC programming software sets the system to the needed configuration. Wire shapes are regularly cleared from the system when the finishing step of the operation is complete.
In the pneumatic process, wire is pushed into the straightening system then shaped to the needed shape and reduced pneumatically to the right length.
Welding joins the formed/shaped and bent wire together to form wire racks. It may mean different seam or spot welding procedures, such as metal inert gas (MIG) welding, tungsten inert gas (TIG) welding or electric resistance welding (ERW). ERW uses an electrical current and then applies mechanical pressure to weld wires.
TIG, MIG, and ERW apply inert gas to minimize any contamination. While tungsten inert gas welding is the best, it is much more multifaceted and requires a very capable operator as well as extended production times, so metal inert gas welding is frequently used instead. Weaving may also be utilized in order to produce wire forms like grids, screens, or guards.
Once they are wire formed and welded, they can be plated, coated, or painted. The need for finishing is dependent on the product type. Wire forming might not need finishing based on the product design. There are instances where grooves, cuts, heading, swaging, coining, and more after production modifications have to be made. The most important purpose is to confirm that sharp edges and burrs are modified and removed.
Consumers can still make more storage spaces even without renovating their buildings. This is possible with the usage of wire racks. Thus, wire racks may help tackle storage problems. Normally, racks are made to house many items. Books can be placed, shoes and kid’s toys on a rack. There are also rack types designed to carry heavyweight objects. Whatever the choice is, it’s always a good idea to choose a suitable wire rack for one’s needs. The following steps must be considered:
Determine the Needs – How is the rack planned to be used? Must it carry books, breadstuff, or retail products? Customer needs must be addressed in order to choose a wire rack that can suit the needs.
Size – Make sure to focus on the size. The wire rack must fit the space. Overall dimensions like height, width, and length must follow not only the items, but the available space also.
Design – If the wire rack is to be utilized as a decorative part, it may be good to purchase a rack with a fancy design.
Weight – The total weight of all items to be placed on a rack must not exceed the loading capacity, as this can lead to potentially hazardous and expensive mechanical failure.
Slit or Gap Size – slit between wires is of concern also when considering the best wire rack to buy, and must be smaller than the smallest product the rack will store to prevent such products from falling through or getting stuck.
These days, there are many wire racks available in the market. The key to choosing the perfect wire rack for a customer is to follow the suggestions mentioned above.
This chapter will discuss the various types of wire racks and wire rack materials.
The different types of wire racks include:
Literature stands hold all types of periodicals and hold products for sale or organizing the waiting room. Floor stands, with multiple level racks or modifiable tiered pockets, display lots of magazines, or folded brochures for simple recognition.
Unlike wooden racks having pockets, the wire frame construction helps with visibility from every direction. Countertop styles are easily smaller forms of the floor varieties, and have single and also multiple pocket designs. Table-top fixtures are used for providing takeaway literature material or for keeping service centers and doctor offices free from clutter. Rotating styles are also available in both countertop and floor versions.
These are the go-to wire racks for many retailers. Alluding to their high durability and affordability, these commercial wire racks provide lots of designs to cater for just about any type of product. Rotating spinner stands, have up to 72 wire pockets and are outstanding choices for providing greeting cards or postcards. On the other side, bulk bins keep and display stock that is difficult to store on shelves, like stuffed animals, beach balls, and pillows.
Racks with changeable slant shelving cater for bakery items, bottles, and much more. Most models feature rolling casters, which makes mobilizing the racks to and from very easy. Countertop forms are perfect for holding small products, including blister packs, souvenirs, keychains, and other trinkets usually related with the "impulse buy". Found at or near point of purchase checkout counters, these enticing wire racks often offer a substantial amount of proceeds for the retailer. Revolving racks are also useful for postcards.
Along with industry standard slat-wall, grid-wall fixtures are common retail store racks. They share the same design as slat-wall, but are cheaper and lighter. Grid-wall wire racks offer wall mounting or floor placement options. After choosing a wire rack, many add-ons, baskets, and hanging hooks to fully customize the floor layout and exploit the grid-wall's capability to highlight much merchandise.
Art display panels are grid-wall's counterparts. Having an alike wire frame design, these panels are very light and are the best option for outdoors art festivals, galleries, and trade shows. They hang mirrors, canvases, or other artwork fast and efficiently. The modular design enables for custom layouts, simply done with simple cotter pins which lock panels together. Both portable and affordable, this art display panel is compatible with grid-wall hanging accessories.
A wire cooling rack permits air to circulate fully around everything which is on it. This means that the baked good or pan will cool quicker than if simply placed on a trivet or a countertop. A hot pan will keep on baking everything inside it, so quicker cooling avoids over-baking.
Most recipes for cakes, cookies, or muffins instruct that the hot pan be placed directly on a cooling wire rack for a specific amount of duration for the first cooling phase. Then, after that time has elapsed, frequently the baked products are moved directly to the cooling wire rack to complete cooling. That final cooling process will keep off any amassing steam and condensation, so freshly baked goods won’t get soggy.
Usually, cooling wire racks are made of stainless steel wires which are made into meshed squares of crisscrossed wires or a number of straight, narrowly aligned parallel wires so that products to be cooled can simply be held without falling through, but permitting enough air to reach the base of the food, so it will not keep too much moisture. Some cooling racks have one layer while others might be multi-layers of two or three stackable rows to hold a batch of breads, cakes, cookies, or a number of pies at the one time. Cooling racks may be square, round, oval, or rectangular in shape. Roasting racks may also be utilized as cooling racks.
A garment or clothes rack is a rail used in stores to store pieces of clothing on display, like shirts and coats. Folding garment wire racks are simple to move or store, making them favorable for many retail applications in clothing stores.
Many different metals may be utilized for wire rack projects. The best metals to use will be based on the wire rack’s application. With this in mind, below is a small list of some of the best metals to use for wire rack projects:
As an austenitic alloy of stainless steel, grade 304 stainless steel has extremely high resistance to corrosion and has a high tensile strength of 621MPa (90ksi), making it perfect for sustaining heavier loads and mildly corrosive environments. Grade 304 stainless steel is also resistant to oxidation much better than iron or plain steel.
Grade 316 stainless steel is more resistant to corrosion than grade 304 stainless steel. In essence, 316 stainless steel is good at resisting chlorides, like salt, making this stainless steel grade perfect for applications having caustic conditions too hostile for grade 304 stainless steel.
Grade 434 stainless steel is a ferritic alloy of stainless steel and has outstanding resistance to pitting. Though less resistant to chemicals than grade 304 stainless steel is, grade 434 stainless steel remains superior at resisting corrosion, pitting, and oxidation than plain steel is.
A specialized coat to protect the real wire form from contact with harsh chemicals and elevated temperatures, polyester (triglycidyl isocyanurate) TGIC is a powder coating which is very resistant to chlorides and abrasions.
Like polyester TGIC powder coating, epoxy solid coating is strongly resistant to staining, marring, humidity, chipping, and many solvents to offer an excellent shield for metal wire forms.
Plastisol is a flexible coat material with characteristics which may vary depending on what plasticizer and procedures are utilized to apply it. It is especially suitable for shielding wire forms from exposure to chemicals.
Another alloy particularly formulated for usage in high temperature applications, grade 330 stainless steel can sustain prolonged exposure to high temperatures reaching 1,037°C (1,900°F).
This chapter will discuss the applications and benefits of wire racks. It will also discuss the maintenance involved with wire racks.
A perfect way for businesses to showcase informational materials about the products or services that they are involved with. A wire rack at the store entrance, on the counter, or inside the store, gives customers the choice of taking a pamphlet accessible on the wire rack. The pamphlet may contain marketing contents related to the businesses, or any important information the business owners feel is pertinent to the familiarity of the customer.
Wire racks differ with construction as some are rotational and circular on the stand and others are immovable, and the customer must go around the stands to get what they’re looking for. The dimensions of the wire rack rely on the dimensions of the brochures as some are A5, A4, while some are DL. The height of the stand is dependent on the amount of pockets and also how big they are. A wire rack with three ordinary pockets 1.25 inches deep could measure up to a height of 7 inches by a base radius of about 1.1 inches.
Some of the benefits of wire racks include:
Very Versatile – Wire racks may integrate panels that may be added or detached to reflect the situation or need. This implies not only will the grids simply work with the available space but fixed components can also be reorganized to reflect new or additional inventory.
This versatility further rationalizes efficiency, particularly when preparing for a professional show; the POP display pieces can be easily assembled and disassembled frequently.
Wire Rack Durability – Wire racks are very durable, and because only the highest quality wires are used when creating them, they maintain quality after extensive use. They won’t break or bend under the weight of products, making them a great solution for displaying mirrors, tools, and other heavy objects. They’re very light in weight, especially in contrast to their strength. This makes them easy to store and move as needs arise.
Beautiful Designs and Customization – A customized wire rack can integrate a variety of details and shapes if needed. Most often, the key advantage is that they offer sleek, open, streamlined designs that allow showcasing of products. In addition, new fittings can be formed to house any display item needed. Powder coating will also guarantee that the exact color will match customer needs. Manufacturers can work with customers to incorporate their vision to take full advantage of the different characteristics which make a wire rack a good choice.
Economics of Wire Racks – Wire racks provide excellent worth and high quality. Combined with durability, wire racks are an efficient investment.
Easy Product Access – Like shelving, wire racks are accessible from all four sides. This facet of customer psychology means if clients "connect" with an item, they’re very likely to purchase it.
Wire Racks are Portable – Wire racks, while still made from durable metals, are lighter than other storing options which enables them to be mounted easily on rolling casters when stacked to make them mobile. This increased movement can allow maximizing storage space, and changing the layout of the business or office as necessary.
Easy to Clean – A safe wire rack protects products from damage. The open design of wire racks prevents dust and debris from accumulating on the racks and can be wiped easily and disinfected when they become dirty.
Food Safe – In addition to easy cleaning, wire racks can be utilized for cold storage in butcheries and restaurants as the mesh permits optimal cold air flow around products for better quality products with longer shelf life. Wire racks may also be coated with antifungal and antimicrobial epoxy for better hygiene.
Picking the right wire forming product can maximize efficiency, reduce expenses from damaged equipment, and lower chances of employee injury.
Increased Efficiency – High quality wire forming products provide manufacturers with the right tools to finish operations fast and efficiently, boosting productivity.
Decreased Costs – High quality wire forms are made to last years of recurring usage without the risk of breaking. Broken products result in stoppage, which could increase costs and damage products.
One of the problems which can plague wire racks is that it may deteriorate. They can buckle and break when mishandled. Wire racks also rust, so it needs to be looked after. That includes understanding the advantages and disadvantages of each type. For example, chrome is vulnerable to rust, hence it is best used indoors. Stainless steel or Epoxy are better choices if working outdoors or have goods that need to be kept cool.
Wire racks are excellent options for storing small items and lightweight capacities, which implies that it might not be the right choice for high volume heavy products which need shelves.
Various maintenance steps are important for wire, which when done regularly can ensure better lifespan for wire racking units. These include:
Dust Daily – Whether it is a shop with or without air cons, dust will certainly accumulate over time. Dusty racks are not attractive to customers. This response will have repercussions which will hurt business economically. Regular dusting also avoids stale odors and makes a healthy environment for everyone.
Organized Display – An organized display of products changes the look of the whole store. Customers will find it easy to take what they need and will be impressed also by the outlet’s span and neat appearance.
Sanitize Often – Sanitisation is the requirement of the hour. During the day, the racks are used by the customers and employees, and they come in contact with many hands. The regular cleaning schedule should involve a proper wipe down of all racks inside the retail configuration. Use the best wipes, sprays, or disinfectant to disinfect the whole rack.
Doing Maintenance Checks – Most rack types tend to undergo wearing and tearing with time. A biannual service will guarantee that all the important pieces of the racking units are in a good shape for them to be strong enough to last many more years.
Wire racks are level wire forms for storing and showing a number of products, usually retail. Although they’re similar to wire shelving since they are both designed for taking full advantage of horizontal and vertical space, the term ‘wire rack’ more frequently refers to miniature units or those ledges not made to stand alone.
Wire racks come from wire forming which is a process of acquiring a wire, from either a blank length or spooled coil, and bending it into definite forms. Wire forms are particularly flexible, enabling them to be changed into a vast variety of shapes and particular configurations. They are applied mostly in retail to encourage consumers with impulse buying as they provide easy access to products.
Wire baskets are made from a series of wires that are woven together or welded to form a shape of a basket. They can also be defined as containers that are made by use of an openwork pattern of metal...
Wire shaping is a complex method that encompasses a wide range of dimensions, forms, and textures. The technique of creating a usable product by wire bending and shaping is known as custom wire forms...
Wire forming is a method for applying force to change the contour of wire by bending, swaging, piercing, chamfering, shearing, or other techniques. The various techniques for wire forming can produce any type of shape, form, or configuration...
A wire handle is attached to a bucket, pail, or other type of container to make it easy to lift the container and transport it. They are made of durable and sturdy metals capable of lifting several pounds...
Wire mesh is fabricated by the intertwining, weaving, or welding of wires of various thicknesses to create proportionally equal parallel rows and intersecting columns. Also known as wire fabric, wire cloth, or...
A coil spring is an elastic element made of metal or heavy plastic in the form of curls or ringlets of round wire or cord that is wrapped around a cylinder. The winding of a coil spring can be loose or tight in a helical shape depending on the application for which it is made...
Coil springs called compression springs can store mechanical energy when they are compressed. These open-coiled, helical springs provide resistance to compressive loading. When these springs are...
Contract manufacturing is a business model in which a company hires a contract manufacturer to produce its products or components of its products. It is a strategic action widely adopted by companies to save extensive resources and...
Extension springs are helical wound springs that are so closely coiled together to create initial tension in the coils. This initial tension creates resistance against the force applied to its ends for extension. The initial tension helps determine how closely and...
Hardware cloth is a woven mesh made by interlacing various sizes of wire to form a metal fabric that can be used for animal cages, fence material, strainers, and filtering screens. The differences between the various types of hardware cloth...
The phrase "wire mesh" describes two- or three-dimensional structures constructed of two or more metallic wires connected by various techniques. In a wide range of settings, wire mesh products are...
Springs are a flexible machine element that store mechanical energy when subjected to tensile, compressive, bending, or torsional forces. When the spring is deflected, it stores energy and at the same time exerts an opposing force...
A torsion spring is a mechanical device that stores and releases rotational energy. Each end of the torsion spring is connected to a mechanical component. As the spring is rotated around its axis on one end, the winding of the spring is tightened and stores potential energy...
Welded wire mesh is a series of wires that are welded where the individual wires cross. The openings of the mesh varies depending on the type of wire used and the function of the mesh. Regardless of size and wire, welded wire mesh is permanent and...
Wire cloth is a woven (or nonwoven) sheet or web material with a series of openings across the surface. Wire cloth is also known as: Metal Fabric or Metal Cloth; Wire Mesh, Metal Mesh, or Alloy Mesh...