Perforated Aluminum
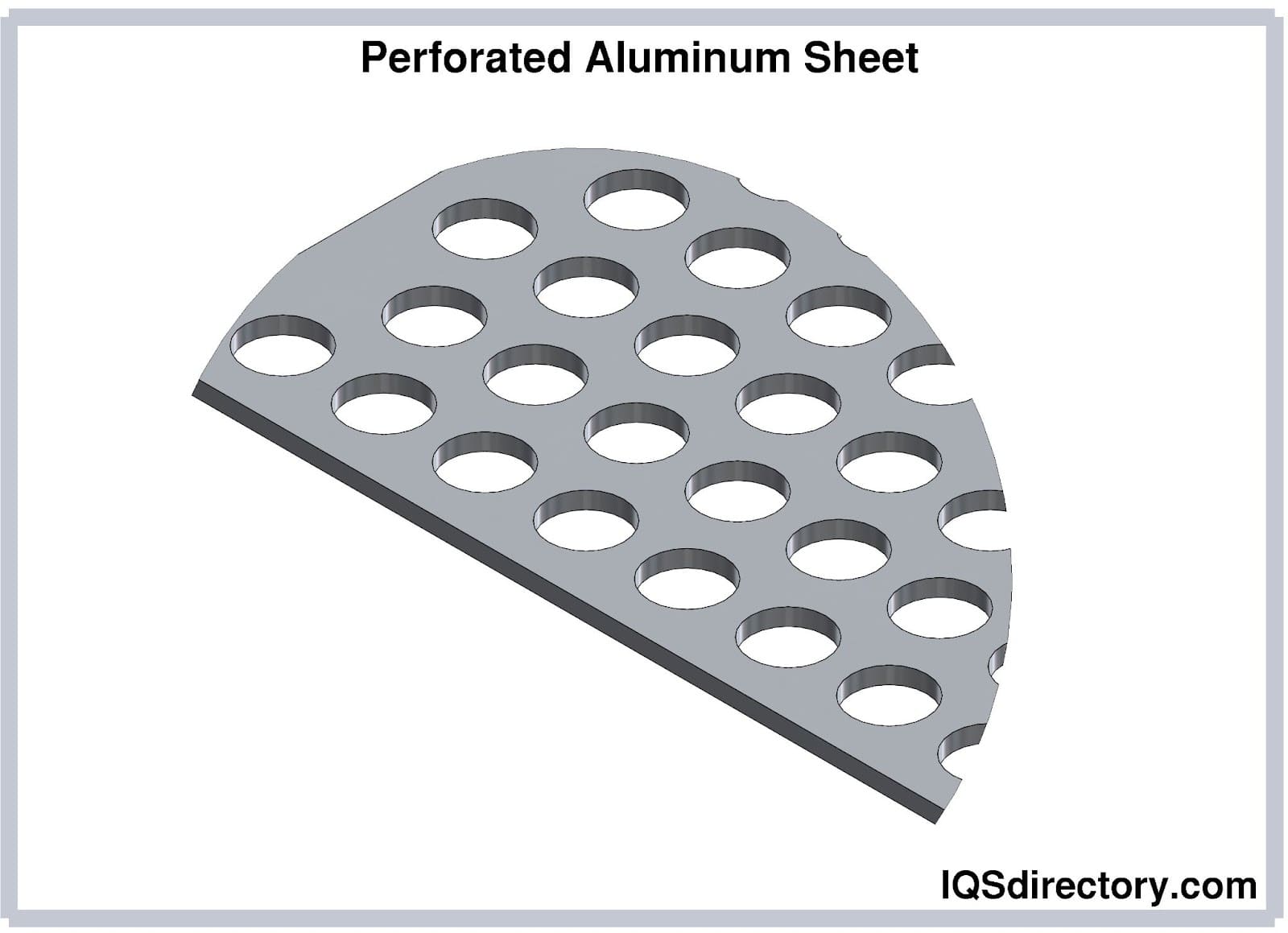
Perforated aluminum consists of an aluminum sheet which has been manually or mechanically pierced or punched using CNC (computerized numerical control) technology in order to produce shapes and patterns of various sizes...
Please fill out the following form to submit a Request for Quote to any of the following companies listed on
Below you will find the most complete information on perforated metals on the internet.
You will learn:
A perforated metal is a piece of sheet metal that has been stamped, fabricated, or punched to create a pattern of holes, slots, and various aesthetic shapes. A wide range of metals are used in the perforating metal process, which include steel, aluminum, stainless steel, copper, and titanium. Though the process of perforating enhances the appearance of metals, it has other useful effects such as protection and noise suppression.
The types of metals chosen for the perforation process depends on their size, gauge thickness, types of materials, and how they will be used. There are few limitations to the shapes that can be applied and include round holes, squares, slotted, and hexagonal, to name a few.
The process of perforating, which used to be extremely labor intensive, has been modernized and mechanized to meet present day standards. The three common methods of creating perforated panels are punch press, rotary pinned, and laser.
Each of the three methods has their benefits in the creation of different configurations, shapes, and forms.
The process of producing perforated metals begins with sheet metal that is thin and flat and can be cut, bent, shaped, or fabricated. The thickness of metals is measured in gauges with the higher gauge number signifying thinner metals.
The determination of the pattern depends on the intended use of the perforated metal, which comes in standard and custom designs as well as a variety of sizes, shapes, and arrangement of holes. The required strength, application, and how the holes are configured have an effect on the functionality and efficiency of the perforated metal.
Part of the decision process involves an examination of the hole and bar size. Bars are the spaces between the holes. The proper balance of the holes and bars is an essential factor that determines the strength of the perforated metal for its application. The larger the holes the narrower the bars. The general rule is that the thickness of the metal should not be greater than the size of the holes or the width of the bars. Following this guideline can avoid tool failure during processing.
All-across perforating presses quickly and accurately create the most number of punches per hit to as many as 1600 a stroke. It is the fastest, most efficient, and economical method of perforation. All-across perforating is normally used for large projects that require speed. It can be used for workpieces that are over 60 inches wide on material that is 0.002 inch thick to 0.25 inch thick. The all-across process is capable of making 600 strokes and thousands of holes per minute.
The XY axis punch functions much like a wide punch press with the exception that it moves across the sheet metal placing symmetrical holes section by section. This process can produce non-repetitive complex patterns.
Laser perforation is the most precise method for producing perforated metals. The laser process can produce intricate geometries with exacting dimensions. The process involves burning small holes consistently and accurately, leaving a reinforced ring around each cut. The two laser processes are CO2 and fiber. CO2 lasers use a gas based laser for cutting, while fiber lasers use a high powered laser with a specialized optical fiber with the laser placed in the fiber.
Plasma uses a gas fired out of a nozzle, which forms an electric arc between the gas and metal. The electric discharge heats the plasma so that it can cut through the metal. The plasma process is capable of cutting through any type of metal, regardless of its thickness and can cut at speeds up to 20 meters per minute.
Water jet cutting uses water, under high pressure, to cut patterns in metal. There are two forms of water jet cutting, pure water without any additives and abrasive that has some form of grit added. Water is forced through a nozzle to cut precision designs in metals. The delivery system for water jet cutting has robotic guidance to provide precise and accurate cuts. It is a cold cutting process that uses particles in the water to erode away material from metals.
Nibbling is a production process where the metal sheet is cut in stages using a punch. The process of a nibbling machine involves punching, cutting, and forming with exacting precision using an electrohydraulic motor. Nibbling machines are capable of performing a wide assortment of operations, which include punching, slot cutting, and the creation of rectangular patterns.
Once a sheet of metal has been perforated, it may require extra processing or value added processes. These methods may be used to enhance the workpiece or make it more applicable for its final use. All metal perforating companies offer an assortment of value added processes depending on their capabilities and standards. Two of those processes, welding and bending, are described below.
One of the most popular uses for perforated metals is as tubing for filters. The process for producing tubing is rather simple and involves the use of a machine that rolls sheets of perforated metal. The ends of the sheet are welded to form the tube.
Perforated metals are bent to different degrees depending on the application. Modern computer design software accurately creates the required angle that is reproduced on a hydraulic machine. Perforated sheets are bent by clamping the sheets between upper and lower dies that are capable of bending the sheets to angles of 120°.
There are numerous machines available to perform sheet metal perforation in the United States and Canada. These machines are essential in today's society as they enable efficient and precise production of perforated sheet metal, which finds applications in various forms like filtration systems, speaker grills, sunshades, electronic enclosures, and others. We examine many of these leading machines below.
Features:
Features:
Features:
Features:
Features:
Please note that the popularity of these machines is subject to changes based on advancements in technology, customer preferences, and market dynamics. Before making any purchasing decisions, it is recommended that you check the latest models and features available from the respective manufacturers.
The types of perforated sheet metals are determined by the shape of the punctures, which include round, rectangular, diamond shaped, hexagonal, slotted, and combinations, to name a few. The metal that is used to produce the perforation is critical to the type of shape that can be used.
Perforated metal types are determined by their patterns, which are limitless and come in a wide variety of sizes.
Round hole patterns can be staggered or straight lines. Staggered patterns place the holes out of alignment, while a straight line has holes arranged parallel and perpendicular to each other. There are three options for end margins, which include finished, unfinished, and blank. Finished margins are uniform and complete. Unfinished are not solid at the edge of the sheet. Round perforations with blank margins have holes that run to the edge of the sheet
Square hole perforations have a linear design that provides a modern look and a high percentage of open space. There are several varieties of square hole perforated metals with several different hole sizes and patterns. Square hole perforated metals can be staggered or in a straight line.
Slotted perforated metal has elongated holes with round or square ends and come in staggered or straight line patterns. The holes for the slotted pattern are punched using a slotted die. Perforated metals with a slotted pattern have an exceptional strength to weight ratio and allow for air, light, sound, and liquids to pass through. The holes for the die can vary in width and length.
Decorative perforated metals are used for architectural accents to provide an aesthetic appeal. They come in a wide variety of shapes and designs that are custom designed to fit the specifications of a building‘s plan. Decorative patterns are created by changing the shape of the pattern die, which provides the ability to enhance the appearance of the perforated metal and adapt it to any application.
Hexagonal, or honeycomb, perforated metal patterns have the highest amount of open space and are used in architectural designs that require steady airflow. Some of the many features of hexagonal perforated metals include aesthetic appeal, excellent strength to weight ratio, and ease of fabrication. Holes for the hexagonal pattern are arranged in a staggered configuration such that the midsection of one hole is in line with the edge of the adjacent hole. The hexagonal pattern is used in architectural applications that require load bearing, which includes roofs, facades, fences, steps, and walkways.
Perforated tubes are used for support, filtration, and cylinders to add strength and pressure resistance to the filter flow. Micron opening perforated metals filter coal, gravel, and ore. Perforated tubing is made from a variety of metals with carefully designed openings that are able to provide support. Holes are created to meet the specific needs of the application.
There are a wide variety of applications for perforated metals. They find use in industrial settings as well as homes and offices. From building construction and design to filtration units for pharmaceutical production, perforated metals have been an essential part of producing products and providing a pleasing appearance.
Filtration and exhaust systems use perforated tubes to trap dust and harmful particulates. Perforated tubes are preferred over other materials due to their resistance to pressure and ability to keep their shape under the constant pressure of filtration systems. The primary use of perforated metals for filtration purposes is as central cores to add support and trap contaminants.
The rungs of ladders are specially designed with upward facing embossing to prevent slippage and downward facing holes for drainage. The holes on ladder rungs are off set for safety and better traction. They come in a variety of widths, lengths, and materials such as galvanized steel, aluminum, and stainless steel.
Speaker grills are designed to protect sensitive instruments such as loudspeakers, listening devices, and telephones from contaminants without blocking sound. Materials used to produce speaker grills have to be vibration and weather resistant as well as able to withstand intensive wear. Speaker grills are made from expanded or perforated metals.
Perforated metal allows air to pass through the floor and walls of grain dryers to keep products fresh and safe. It is a form of ventilation system that provides a continuous flow of air so that grain can dry quickly and thoroughly. Grain bin flooring provides airflow to prevent germination of grain seeds and guard against bacterial growth.
The purpose of architectural perforated metals is to embellish construction projects and improve the appearance of existing structures. Perforated metals enhance the image of projects and are produced in a variety of sizes, materials, and perforations. The design and shape of perforations can be custom made to fit any application.
Architectural perforated metals can be configured to meet any set of requirements and are able to be installed horizontally or vertically depending on the specifications of the designer. They offer design flexibility and are aesthetically pleasing.
Perforated metal guards serve as covers for gutters to keep out leaves and large debris. Gutter guards have hundreds of tiny holes with a large space in between holes that provides for a large amount of solid surface. They fit flat on top of the gutter underneath the eaves and have a vertical step at the edge of the perforated panel to keep it securely in the gutter.
Another part of architectural design is backlit panels that highlight the structure of a surface making surrounding materials standout for dramatic effect. They have a minimal profile, conform to the area, and generate consistent radiance. Backlighting a perforated panel causes it to stand out to present a spectacular appearance and aesthetic appeal.
Perforated metal partitions can transform an ordinary space creating a distinct and extraordinary atmosphere. Aside from their aesthetic value, perforated partitions take large spaces and divide them to create separation but provide an open accessible feeling. Partitions can be configured, shaped, and designed to fit any space and dimensional requirements. They are flexible and lightweight, which makes them easy to relocate or move to storage.
Perforated metal fencing is determined by the size of the necessary panels, creation of panels that fit between the posts, precision produced paneling, and creating custom fit. The major benefit of perforated fencing is its aesthetic value since it adds beauty and appeal to what could be considered to be ordinary. Perforated fencing is manufactured with an environmental finish to protect against rust and flaking. The design of perforated fencing allows free flow of air but breaks up the current.
Sunshades or sunscreens serve several purposes. As the name implies, they provide protection from the rays of the sun. Aside from that initial purpose, they have more practical uses as well. Sunshades help in the reduction of energy costs from the use of air conditioning and lighting. Though they block the glare of the sun, they do allow its natural light to filter through providing a soothing light.
Much like perforated fences, sunshades restrict air flow causing a reduction in noise from wind and rain. They also provide extra privacy and eliminate intrusions. As a protective measure, sunshades protect a structure from weathering and harsh conditions, which helps avoid exterior repairs.
Electronic enclosures have to be constructed to meet specific requirements regarding electromagnetic (EMI) and radio frequency (RFI) interference. Much of the material stored in electronic enclosures is expensive, sensitive to interference, and not aesthetically pleasing. Perforated enclosures provide ventilation to keep equipment from overheating and protection from EMI and RFI interference. Since perforated panels are made from sturdy and durable materials, they are ideal for holding heavy cumbersome electronic devices.
Perforated metal handrail guards offer extra protection for railings, while adding an enhanced aesthetic appeal. Handrail guards are made from a variety of metals that include aluminum, stainless steel, and steel with a finish for protection against weathering and rust. Perforated handrails are preferable to pickets or rail designs since they allow for privacy but permit light and air to pass through. The main benefits of perforated metal panels are their durability, low maintenance, and decorative qualities.
From its beginnings as a protective covering for military use, perforated metals have progressed to become an essential part of several industries as decorative art, structural support, a part of filtration systems, and protective covering. The methods for producing perforated metals have improved and are much easier with the use of modern technology. The many innovations have made perforated metals more available.
Perforated metals for agriculture have several functions. Farm equipment is used for digging, planting, spraying, reaping, and threshing. Those processes produce dirt and dust that can foul engines. Perforated metals are used to protect machines from being damaged by debris as radiator grills, exhaust system guards, and metal screens.
For storage and protection of grain, bins and hoppers are lined with perforated metal to promote aeration for grain drying. Hammer mills that grind cornmeal, wheat flour, seeds, and pet food use perforated metal screens and components.
Air and water filtration are a necessary part of modern appliances to protect them from debris and keep them cool. Perforated metals keep appliances operating properly by ensuring the constant flow of light and air, holding filtration substrates, preventing overheating, and protecting against moisture build up. As an added benefit, perforated metals ensure safe operation of appliances.
Food production requires a high level of hygiene and sanitary environments as well as having materials that are able to withstand thermal conditions. Perforated metals are used for cleaning, heating, and steaming food. In rough cleaning and pre-cleaning processes, perforated metals provide a gentle environment for the removal of unwanted and undesirable materials from corn, grain, seed, maize, rice, and legume.
In the rough cleaning process, perforated metals are used to separate impurities and provide a convenient method for storing and drying processed food. Pre-cleaning prepares food for storage and improves its stability.
Perforated metals are used by the automotive industry because they add extra strength without increasing the weight of the vehicle. They are used for radiator and muffler guards to prevent debris from fouling the engine or exhaust system. At the same time that they are protecting the engine and exhaust seems, they allow for airflow to support engine components. Perforated metals installed on the exterior and interior of a car serve as a sound suppression system blocking the sounds of engine operation and exhaust noise.
Perforated metal store fixtures and displays are an attractive and clean method for displaying merchandise. Since there is constant continuous air flow, products always look fresh and new. An extra added feature of perforated displays is their flexibility allowing a store to rearrange and reconfigure the sales floor for different applications and products. Perforated metal displays are strong, sturdy, lightweight, permanent, long lasting, and easy to install and assemble.
The decorative qualities of perforated metals adds to the appearance and atmosphere of a store as well as offering brand promotion and visibility.
The medical industry requires materials that are exceptionally durable and functional. Perforated metals provide safe, precise, and effective support for medical procedures and services. They are used for autoclave and cadaver trays, test chambers, ventilation hoods, and test tube holders. Materials used to produce perforated equipment for the medical industry are chemical resistant, offer continuous filtration of gases and liquids, and rapidly adapt to radical temperature changes.
Heating, ventilation, and air conditioning systems use perforated metals for their ability to adapt to temperature changes but work smoothly with limited or no vibration. Perforated metals are ideal for distributing air flow evenly and suppressing HVAC system sounds. Diffusers made of perforated metals provide air flow that avoids cold floors, blasts of heat, and stale air.
A major problem with HVAC systems is fan noise, which can move through the system hoses into the duct work. Perforated metal works as a silencer in the ducting system to break up airflow and quell noise.
Industrial operations need receptacles for storage of equipment that meet industry requirements, are able to handle the weight of parts, and provide adequate ventilation. Perforated metals can be configured into baskets, storage units, and a wide variety of containers. They have the advantage of reduced weight making transportation easy as well as providing high visibility.
An important function for perforated metals in an industrial setting is a source of protection as barriers that do not block the ability to see what is beyond it and allow for consistent air flow for equipment that may become overheated.
Perforated metal sieves and filters are essential for washing, drying, baking, straining, and filtering in a variety of industrial processes. These unique processes require metals that are acid, corrosion, and wear resistant with the ability to be precise, strong, and durable.
The main use for perforated metals in the chemical industry is as filters and screens to remove contaminants and debris. Perforated metals are chosen by the chemical industry because of their resistance to chemicals and high temperatures.
Perforated metals in the construction industry have the dual purpose of offering a pleasant aesthetic appearance as well as structural support. Cladding made from perforated metals is used for lighting, ventilation, room and open space division, and as sunscreens. When ventilation and air flow are a necessity, perforated metals are used as ceiling material.
In conditions where there is a chance of slipping, perforated metals are used for flooring and stair treads. Though perforated materials are lightweight and easy to install, they have exceptional strength and endurance to perform under harsh conditions as well as serve as safety protection.
Partitions, fencing, paneling, ventilation grills, cable trays, and metal gates can all be fabricated from perforated metals but provide greater endurance, longevity, and wear than other materials.
A growing trend in the perforated metal industry is the incorporation of graphics, logos, and images in the metal panels to brand and identify a location. Though this has been used for many years, it is recently gaining greater popularity as an architectural tool and a method for creating an aesthetic design for buildings. The image is placed on a panel by computer programming. The computer rendering is fed into a perforating and fabricating machine that places the image in the perforated sheets.
There are very few limitations to the metals that can be used in the perforation process. In the early days, the number of metals was limited to ones that could be easily penetrated and fabricated. With the development of modern CNC processes and other technological advances, the spectrum of metals has grown into any form of metal that can be made into sheets.
The reddish appearance of copper makes it ideal for producing aesthetic perforated sheets. Since it is resistant to temperature changes and rust, it can be used for the exterior of buildings and as a means of protection. Copper is an excellent conductor of heat, which makes it ideal for perforated metals used in heating systems.
There are 15 different grades of stainless steel available to be fabricated into perforated metal sheets. The many qualities of stainless steel include superior strength but lightweight as well as being corrosion, rust, and bacterial resistant. Stainless steel perforated metals are found in all industries from medical and chemical use to auto manufacturing and mining.
Physically, chemically, and mechanically, aluminum has the same qualities or similar qualities as steel, copper, and lead. It can be easily shaped, formed, and fabricated using a variety of metal fabricating equipment. Aluminum is one third the weight of steel but has a comparable strength to weight ratio. Its lightweight, ductility, ability to withstand low temperature conditions, and corrosion resistance makes it ideal for perforated metal processing.
Monel is a nickel alloy that can withstand intense environments of heat and high pressure. It is a mixture of copper and nickel alloys with other alloys. The flexibility and adaptability of Monel makes it ideal for shaping and designing a wide range of perforated products. It has excellent performance and workability and can be hot and cold worked. Typical Monel has 68% nickel and 29% copper. The various grades of Monel are created by the addition of a third alloy.
The galvanizing process adds long life, durability, and excellent performance to steel. The manufacture of galvanized steel involves hot dipping steel in a galvanizing solution that coats the metal and protects it against abrasion, corrosion, and offers long term surface protection. The strength, endurance, and toughness of galvanized steel makes it perfect for the production of perforated sheets.
Titanium is one of the strongest and most durable metals. It has the same strength as steel but is less dense making it a good choice for configuring, shaping, and fabricating. Titanium has a natural resistance to rust and corrosion, a factor that increases its usefulness and longevity.
Brass has the appearance of gold and is an attractive metal for creating decorative perforated panels. It is normally used with heater and HVAC applications as well as electronics. Brass is an alloy of copper and zinc and comes in a wide range of versions depending on how its content is manipulated. The common way of identifying brass is by its zinc content, which can vary from 37% to 45%. The three outstanding qualities of brass are its durability, antibacterial properties, and aesthetic value.
Though perforated metals are valued for their aesthetic appeal, they have several benefits beyond their appearance. While they improve how an item may look, they have the extra ability of improving performance. Since they can easily adapt and change to meet a wide variety of applications, they have become an ever growing part of the manufacturing process.
Perforated metals serve many functions from lighting to appearance. One of their more useful functions is as a method for sound absorption. Perforated panels reduce unwanted noise by dispersing it. This benefit is ideal for work environments where loud annoying sounds can be irritating and uncomfortable. The porous and textured surface of perforated panels disperse sound waves and have indoor and outdoor use.
When a building needs to improve its ventilation, it uses perforated metal sun protection screens to improve airflow and increase shade. This method of protecting buildings results in decreased energy costs on heating, ventilation, and air conditioning. Statistically, perforated panels can lead to an estimated 30% to 45% savings.
The adaptability of perforated metals offers designers and architects a wide range of opportunities to enhance building construction that will last. Since perforated metals can be made specifically to fit any conditions, they can be uniquely made to give any structure a lasting and permanent impression. The manufacture and production of perforated panels create products that are stronger and more weather resistant than other materials for the same purpose.
One of the unique features of perforated panels is their ability to give the impression of privacy without a closed in feeling. Closed in walls and panels tend to cut off and isolate parts of a workspace. By installing perforated panels, a workspace is divided but still allows for airflow and visibility. The normal noises and echoes are deflected and absorbed by the panels creating a soothing and enjoyable atmosphere.
As the concern for sustainability and conservation grows, designers and architects are constantly searching for materials that will reduce environmental impact. The metals used for perforated panels are recyclable and reduce the need for the production of new metals for projects. Since they have a long usable life, perforated panels seldom need maintenance or suffer wear. These factors lead to the sustainability of the metals and increases their longevity.
In production processes, efficiency and quality are essential. Perforated components work smoothly in delivering and storing parts. The perforations allow for airflow and prevent materials from having any form of build up or collecting of debris. Most baskets, carts, and material handling equipment for production use are made of stainless steel, galvanized steel, or cold rolled steel.
Electrical components and appliances produce EMI and RFI radiation that needs to be contained and controlled. Perforated shielding provides a 99% attenuation of EMI and RFI radiation with a shielding effectiveness of 40 decibels, which is the minimum for applications. The shielding is very effective at 7 gigahertz.
The strength of perforated metals is measured by comparing them to solid metals, a concept that is referred to as the Equivalent Solid Material Concept. To help designers decide on what perforated materials to use, engineers perform a solid equivalent materials test.
The strongest pattern for perforated metals is round holes that are staggered at 60°, which provides strength and a wide range of open area. Using an engineering formula, design engineers calculate the strength of perforated material compared to solid material.
Perforated materials have different strengths depending on the direction of the loading. The yield strength of perforated materials is a function of the yield strength of solid materials. The determination of the strength of perforated materials is based on its thickness as it compares to a solid material.
An additional factor is the stiffness of perforated material, which is also calculated by comparison to solid materials. Using another formula, engineers decide on the necessary thickness of a perforated panel such that it provides the same stiffness as solid material.
The standards for perforated metals have been established to assist designers and engineers in selecting the correct product for their application. The standards for perforated metals have been created by the Industrial Perforators Association.
The width and length should follow the general standards for mill shearing, which should include any stretching of the material during perforation.
All metals that are used in the perforating process follow the U.S. Standard Gauge table.
Though 60° round is the standard pattern, there are variations, which include straight line and staggered using different shapes such as squares, slots, and a wide assortment of other choices.
Perforated metal patterns have a certain diameter with appropriate spacing with an open area where metal has been removed by the perforation process.
Staggered patterns are normally 45° or 60° and are used when panels are bent since it allows for bending dimensions to be easily reached. Straight patterns are rows and columns that are similar to a grid. It is unwise to use a straight pattern for bending.
Margins can be placed on all sides of a panel. It is typical to have margins on the side and not the top and bottom, which makes it easier for installation.
All perforated panels are delivered flat and normally flattened as part of the perforation process. Under special conditions, flatness requirements may need to be adjusted to meet specific design criteria.
Perforated aluminum consists of an aluminum sheet which has been manually or mechanically pierced or punched using CNC (computerized numerical control) technology in order to produce shapes and patterns of various sizes...
Perforated metals are sheets of metal that have had decorative shapes, and holes punched or stamped into their surface for practical or aesthetic purposes. The perforation of metal sheets takes several forms and includes a variety of geometrical patterns and designs...
Perforated stainless steel is cut, punched, or stamped to produce a precise pattern of holes or apertures. It is used for functional reasons, such as filtration or ventilation, and aesthetic ones, such as architectural accents...
Perforated metals are sheets of metal that have had decorative shapes, and holes punched or stamped into their surface for practical or aesthetic purposes. The perforation of metal sheets takes several forms and includes a variety of geometrical patterns and designs...
Wire mesh is fabricated by the intertwining, weaving, or welding of wires of various thicknesses to create proportionally equal parallel rows and intersecting columns. Also known as wire fabric, wire cloth, or...
Expanded metal is a sheet metal mesh. It is made by stretching a slitted sheet of malleable metal. The orientation of the slits is perpendicular to the direction of the stretch. The result of such stretching is an array of holes on the slits - to give a mesh form...
Hardware cloth is a woven mesh made by interlacing various sizes of wire to form a metal fabric that can be used for animal cages, fence material, strainers, and filtering screens. The differences between the various types of hardware cloth...
Metal grating is a metal product produced by perforating metal sheets or joining bars of metal to form a grid. They are a metal product that is widely used in various industries as stairs, platforms, scaffolding, and protective coverings...
The phrase "wire mesh" describes two- or three-dimensional structures constructed of two or more metallic wires connected by various techniques. In a wide range of settings, wire mesh products are...
Welded wire mesh is a series of wires that are welded where the individual wires cross. The openings of the mesh varies depending on the type of wire used and the function of the mesh. Regardless of size and wire, welded wire mesh is permanent and...
Wire cloth is a woven (or nonwoven) sheet or web material with a series of openings across the surface. Wire cloth is also known as: Metal Fabric or Metal Cloth; Wire Mesh, Metal Mesh, or Alloy Mesh...