Linear Rails
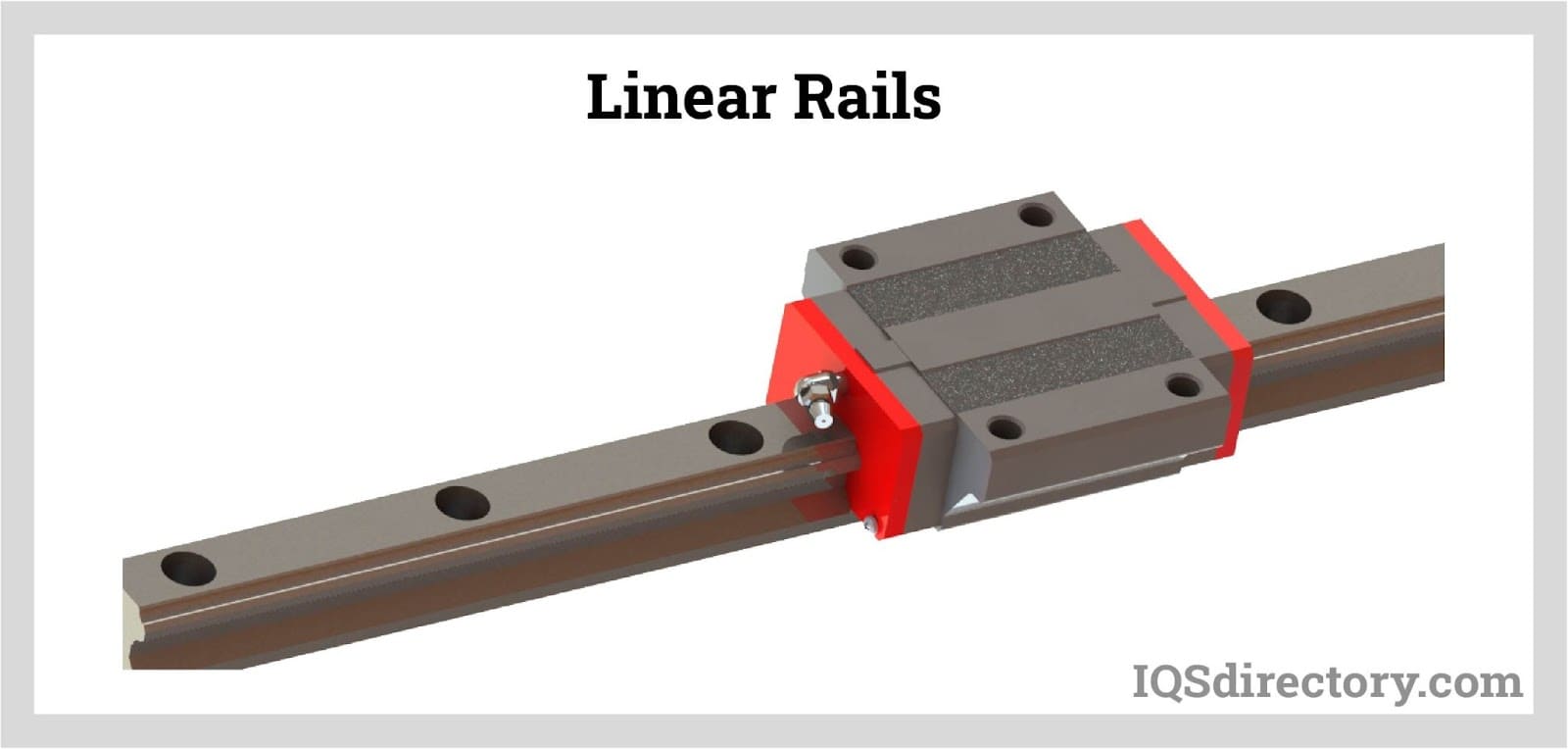
Linear Rails are ideal for moving items through a production process with great precision and as little friction as possible if creating, packing, and distributing products. Linear Rail is a type of gadget that...
Please fill out the following form to submit a Request for Quote to any of the following companies listed on
This guide provides in-depth insights into linear slides. Read further to learn more about:
Linear slides, also known as linear motion slides or linear motion guides, are essential mechanical components designed to facilitate precise and controlled linear motion in various industrial and mechanical systems. These devices serve as the backbone for achieving smooth and stable movement of objects or tools along a defined path. Machine tools, robots, actuators, sensors, and other mechanical equipment often require moving components in a straight line in any of the three-dimensional axes. While in contact with another object, free translational motion is always countered by friction, the force exerted by two bodies moving against each other’s direction of motion. The amount of frictional force exerted is governed by the load acting on the surface in contact and the surface property known as the coefficient of friction.
For minimal power consumption, reduced tool wear, and lower heat generation, low friction and high precision are essential qualities. A linear slide is just one part of linear motion systems, which also include power screws, actuated cylinders, linear motors, and rack and pinion mechanisms. Linear slides specifically handle motion guidance, while other components are responsible for power transmission.
The main component of linear slides is the bearing, which can be either a rolling-element, plain surface bearing, or magnetic bearing. A rolling-element uses balls or rollers to minimize the area of contact into against the rubbing surfaces. The surfaces where these elements roll are called races. Rolling element bearings that utilize rolling balls are called ball bearings, while the ones using rollers are roller bearings. Ball bearings reduce contact to a small point. In theory, the area of contact can be reduced to an infinitely small point provided that the surfaces can resist the infinitely high contact stress produced. In practice, the ball and race surfaces deform slightly, creating a finite area of contact. A small area of contact limits ball bearings from carrying heavy loads. To counter the high contact stresses produced, the number of balls in contact is increased. This is done by adding more rows of balls and races.
Roller bearings are rolling elements designed to support loads and reduce friction. They operate by using rolling elements that keep moving parts apart from the bearings. Unlike spherical ball elements, which make point contact, rollers create a line contact with the race surfaces. This line contact is effectively a rectangular area due to the deformation of the rollers, providing a larger contact area compared to ball bearings of the same size. Consequently, roller bearings can handle higher loads with reduced contact stresses.
Plain surface bearings use sliding surfaces instead of rolling elements to support a load and allow motion. Plain surface bearings utilize materials and finishes with a low coefficient of friction and lubrication. Some plain surface bearings are made from composite materials such as PTFE and graphite with a metal backing. This type is called dry lubrication. This allows no metal-to-metal contact between the sliding surfaces and provides heat dissipation characteristics from the metal backing. As PTFE and graphite bearings are abraded, the worn-off particles become a lubricating layer. A similar property is seen in plastic plain bearings, however, they lack heat dissipating properties and act as thermal insulators.
Plain surface bearings can employ fluids such as pressurized air or lubricants to support the loads exerted between surfaces. The term hydrostatic lubrication refers to the use of pressurized liquid lubricants, while aerostatic lubrication involves compressed air. For linear motion systems, dried air is often preferred due to its cleanliness. Hydrostatic bearings offer nearly frictionless movement, which is ideal for extremely precise machinery. However, one drawback is the high cost of the auxiliary equipment needed to generate the pressurized fluids.
Magnetic bearings, similar to hydrostatic lubrication, offer nearly frictionless movement by either repelling or attracting the moving component. Unlike hydrostatic bearings that rely on pressurized fluids for levitation, magnetic bearings use electromagnetic forces to achieve this effect. They are capable of handling significant loads, which makes them suitable for heavy-duty applications. However, their use can be constrained by potential interference with other equipment and higher energy requirements.
This section explores the fundamental elements of linear slide systems. It covers the slide mechanisms and the necessary components for both actuation and positional regulation. Depending on the specific application and the manufacturer, there may be additional specialized parts, such as air bearings and positioners, among others.
The most common among the three main classifications are rolling element bearings. In comparison with lubricated and magnetic bearings, rolling elements are more robust and highly versatile. They work better in both dynamic and static conditions. Also, their performance and service life can be easily predicted by industry best practices and standards. Hydrostatic and magnetic bearings are only used in a narrow range of applications, mostly in laboratories and specialized instruments.
Rolling element bearings used in linear slides can be classified according to rolling element recirculation. For configurations without recirculation, the distance covered by the linear slide is limited to the length of the rolling element row. The rolling elements rotate but do not travel completely with the carriage. Non-recirculating rolling elements move only at half the carriage's speed and thus cover only half the distance. For recirculating rolling elements, the race has a return path designed into the carriage. The rolling elements recirculate by traveling the looped path within the carriage. The enables both the rollers and carriage to travel together along the guide rail. Rolling elements for recirculating linear slides are ball bearings.
Carriage: The carriage is the moving part guided by the bearings. It is the part that supports the tool, instrument, or sub-assembly that requires linear movement. Their linear movement is mostly limited within the X-Y plane. Carriages moving in the Z direction employ power screws or screw drives. A drive unit is usually coupled to the carriage. This provides the necessary force or torque to set the carriage in motion.
Guide Rail: These are stationary surfaces that the gliding surfaces of plain bearings or the rolling elements slide against. Guide rails for plain surface bearings are basically flat surfaces with or without lubrication. They can also be cylindrical in shape, often called a shaft or journal. For rolling element bearings, the races are designed to balance the covered area of contact with the magnitude of contact stress. Since this is more evident in ball bearings, its race profile is designed to be classified into two: circular arch and gothic arch.
Circular and gothic arches both have two races that contain the ball bearings. The races only contact the ball in circular arches at two points; for gothic arches, contact is at four points. Initial intuition dictates that gothic arches are better since it can support heavier loads. However, an effect called differential slip causes negative consequences for gothic arches. Differential slip is caused by the different rolling diameters occurring in curved races. This results in different rolling speeds creating sliding friction. Differential slip is more evident on gothic arches since there is a larger difference between the effective rolling diameters. Therefore, a circular arch is preferred over a gothic arch. Gothic arch is generally used for small systems that need higher load ratings than similarly sized circular arc races.
The construction of roller guides includes linear rails with rollers, a moving component, and a mounting bracket. The raw materials for roller guides are aluminum or cast iron, which is why they can support heavy loads. In conditions where there is the potential for rust or corrosion, stainless steel is used to make the roller guides. The distance between their rails determines their capacity and needs to be increased as the weight of the application increases.
The rolling motion of roller guides removes the need for lubrication that is necessary with sliding motion linear slides.
End Cap:The end cap serves as a protective cover at the end of the linear slide assembly. It prevents contaminants, such as dust and debris, from entering the slide system, which could damage the bearings and guide rails. End caps also help maintain the integrity of the linear slide by sealing the ends.
Bellows and Covers: Linear slides operating in harsh environments or exposed to potentially damaging elements may feature bellows or protective covers. Bellows are accordion-like flexible enclosures that shield the slide from contaminants and debris while allowing for linear motion. Protective covers can be rigid or flexible and serve a similar purpose in safeguarding the slide's components.
There are numerous combinations of bearings, including recirculating and non-recirculating designs, contact types, raceway profiles, drive mechanisms, and precision controls, each tailored to specific applications. Certain combinations are particularly notable for their simplicity, load capacity, rigidity, or versatility. These are constantly being developed to match their intended purposes. Listed below are some of the commonly used linear slides in the market.
Dovetail Slides: These are linear slides that employ plain surface bearings that rely on a low coefficient of friction and lubrication. Their names originate from dovetail-shaped protrusions that fit into identical negative geometry. The protrusion is usually on the stationary rail or base while the negative is constructed into the carriage. This configuration is sometimes referred to as a dovetail table. Dovetail slides are robust and can withstand both radial and lateral loads. These are typically used for large machine tools such as lathes, shapers, and milling machines.
Boxway Slides: Like the dovetail slides, boxway slides are plain surface bearings. But instead of a dovetail-shaped protrusion, these have a square gib with flanges at the top forming a T shape. They can handle heavier loads than dovetail slides due to the larger projected surface area in contact between the carriage and the rail.
Sleeve Bearing Slides: This type uses cylindrical surfaces instead of mating tongue and groove geometry. These surfaces are called bushings and journals. The bushing is like a hollow cylinder constructed into the carriage, while the journal is a long shaft that acts as the guide rail mounted on the base. Advantages of using sleeve bearing slides are its simple construction and its ability to handle loads applied in any direction. However, they are not as strong as dovetail and boxway slides and can only be used for light to medium load applications.
The bushings can also be classified according to their form, which can be closed or open. Closed bushings have a shaft that is supported only at the ends, while open bushings allow shaft supports directly underneath. Having support underneath the shaft eliminates deflection from carrying high loads.
Linear Ball Slides: This is one of the most common types of rolling element slides. Linear ball slides are similar to linear ball bushings, but a runner block is used instead of bushings. The runner block can also be constructed with a return path for recirculation. Linear ball slides are better than linear bushings since they offer better versatility and load capacity. Since the races sit directly on the base, there is guide rail deflection. Also, several design variations are available for the race profiles that can favor either load capacity or compactness.
Crossed Roller Slides: As the name suggests, this type utilizes rollers that are oriented at 45° and 135° relative to the horizontal. The rollers can be arranged into a single row with 90° alternating orientations, or into multiple rows where each row is oriented perpendicular relative to the other rows. This type has better load capacity than similarly sized ball slides due to the larger contact area inherent to roller bearings.
Ball Screw: This is a special type of linear slide that combines ball bearings with power screws. A typical power screw drive has an Acme profile that engages the nut integrated into the carriage through sliding contact. A ball screw further lowers friction by introducing balls as rolling element bearings. The nut is constructed to have a return path for recirculation.
A linear slide serves to guide the movement of a machine tool or instrument but does not provide the force needed for this motion. Instead, a drive unit, which can be mechanical or electromagnetic, supplies the necessary force. Basic linear slides often rely on manual actuation, which can be accomplished through methods like pushing, pulling, or using devices such as a hand crank leadscrew. The following are various types of powered drive units commonly used with linear slides.
Belt Drive: In this type, the carriage is attached to both ends of a toothed belt. A toothed or timing belt is used instead of a flat or V-belt to prevent slippage. This toothed belt is wrapped around two pulleys located at the ends of the guide rails. One pulley is connected to a motor known as the drive end, while the other pulley is only for providing tension known as the tail end.
Pneumatic Systems: Pneumatic systems are piston and cylinder assemblies where compressed air is supplied on one or both ends. Introducing compressed air causes increased pressure inside the cylinder, moving the piston. A rod is attached to one side of the piston and is extended or retracted according to the piston‘s action. A pneumatic cylinder can be classified as single-acting or double-acting. A single-acting cylinder has only one inlet port. One stroke is pneumatically powered, while the return stroke is caused by other countering forces, such as spring force. In a double-acting cylinder, there is one inlet port at both ends of the cylinder. This makes the return stroke pneumatically powered also. The simplest pneumatic actuators have the tool or part of the carriage attached to the end of the rod. However, this requires an overall length twice that of the stroke. The rod is then replaced with other modes of coupling such as cables, bands, and magnets. Pneumatic systems have high operating speeds. Also, since there are no mounted electrical components, they are suited for explosion-proof devices. However, unlike the other types, the carriage cannot stop at an intermediate position. The travel is only from end-to-end positions.
While the previous chapter focused on machines responsible for carriage actuation, it’s equally important to consider the devices that monitor these movements. Actuation can be either manually controlled by an operator or automated. To facilitate this, sensors are required to provide feedback signals that the controller uses to activate, deactivate, or adjust the force generated by the drive units. The following are some common sensors employed in linear slide systems.
Linear slides offer numerous benefits across various applications, such as in manufacturing, automation, and precision machinery. Below are some of the primary advantages and benefits associated with using linear slides:
Linear Rails are ideal for moving items through a production process with great precision and as little friction as possible if creating, packing, and distributing products. Linear Rail is a type of gadget that...
A roller table is a small, stiff, limited linear guide device with an integrated cross-roller guide. Electrical or mechanical drive systems are frequently used to move a roller table, making it easy to transfer heavy loads...
A linear actuator is a device that transforms rotational motion into push or pull linear motion, which can then be used to lift, lower, slide, or tilt machinery or materials. They offer effective, maintenance-free motion control...
Ball screws are mechanical linear actuators that consist of a screw shaft and a nut that contain a ball that rolls between their matching helical grooves. The primary function of ball screws is to convert rotational motion to linear motion. Ball nuts are used in...
Electric actuators are devices capable of creating motion of a load, or an action that requires a force like clamping, making use of an electric motor to create the force that is necessary...
A lead screw is a kind of mechanical linear actuator that converts rotational motion into linear motion. Its operation relies on the sliding of the screw shaft and the nut threads with no ball bearings between them. The screw shaft and the nut are directly moving against each other on...
A linear actuator is a means for converting rotational motion into push or pull linear motion, which can be used for lifting, dropping, sliding, or tilting of machines or materials. They provide safe and clean...
Linear bearings are a type of bearing that "bear" or support the load of the carriage during its single-axis linear movement and provide a low friction sliding surface for the guide rails. In a linear guide, the carriage is the component that travels in a straight line, back and forth, along the length of the guide rail...
High-precision, linear motion goods are essential components at the core of several items which are generally used in machine tools and equipment for manufacturing semiconductors. These items are utilized...
A linear actuator actuates, moves, in a linear, straight, line to complete or start a process. There are a variety of terms used to describe a linear actuator such as ram, piston, or activator. They are very common in...