Electric Actuators
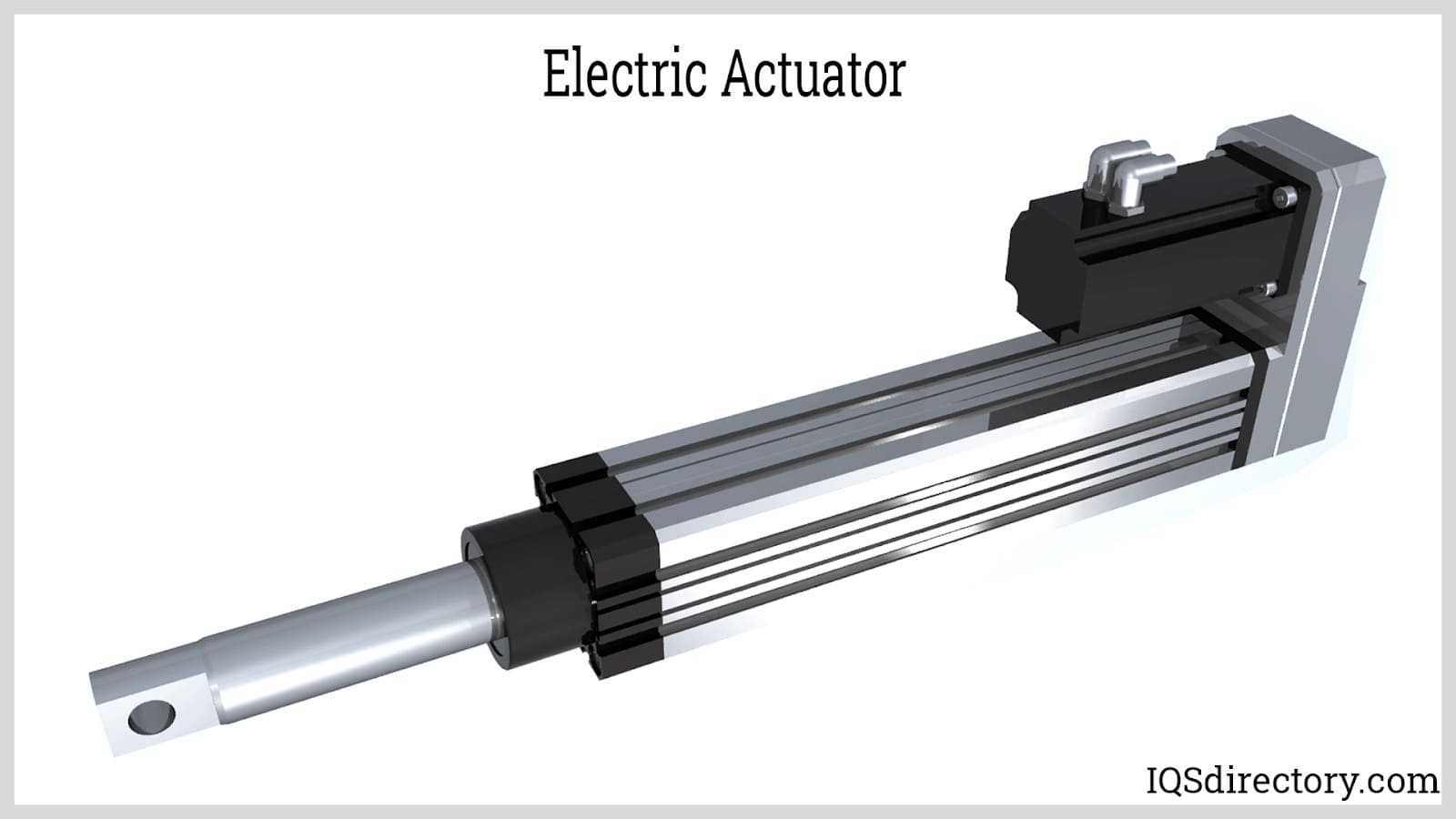
Electric actuators are devices capable of creating motion of a load, or an action that requires a force like clamping, making use of an electric motor to create the force that is necessary...
Please fill out the following form to submit a Request for Quote to any of the following companies listed on
This article will take an in-depth look at 12V linear actuators
The article will bring more detail on topics such as:
This chapter will discuss what 12V linear actuators are and how they work.
A linear actuator is a device that transforms rotational motion into push or pull linear motion, which can then be used to lift, lower, slide, or tilt machinery or materials. They offer effective, maintenance-free motion control that is clean and safe. 12 Volt linear actuators are powered by 12 Volt (Direct Current) DC voltage sources. Screw, wheel and handle, and cam are the three different kinds of linear actuators. The up and down motion of a screw winding and unwinding provides the motion in the screw type.
The force of a belt or chain that is fastened to a shaft causes the wheel and handle actuators to move. An eccentric circle is used to move a shaft in the cam type. The definition of a linear actuator varies depending on the industry. The widely used definition is a tool created to convert rotary force into linear motion. A linear shaft or other mechanism receives the initial force, which may come from an electrical motor or hand crank.
The miniature DC gear motor, which uses a screw-drive and gears to supply significant loads by releasing electromechanical motion, is the fundamental component of the 12V linear actuator. These powerful, simple-to-install, and suitably sized 12V DC actuators are quite handy. Two wires (one positive and one negative), mounting holes on either end, and internal limit switches make up each device. 12 volt linear actuators have stroke diameters ranging from 1 inch to 24 inches, and their maximum forces can be 15 lbs, 50 lbs, or 150 lbs. The majority of manufacturers create these linear actuators with specialized sizes, currents, and speeds in order to satisfy particular client needs.
In essence, an actuator that moves linearly in a straight line is called a linear actuator. Although an actuator's fundamental purpose remains the same, there are various methods for achieving motion. From wheelchair ramps, to toys, to technological equipment for spaceships, linear actuators are used in a variety of applications.
An actuator works in a pretty straightforward manner. Depending on the performance needed, a screw, such as a lead screw, ball screw, or roller screw, is used to generate motion by rotating either clockwise or counterclockwise, which causes a nut on the screw to move and provide linear motion. Roller screws work best for strong forces, whereas ball screws are best for quick, dynamic applications requiring precision alignment. The power to turn the screw comes from the motor, which is located above the actuator.
A DC motor serves as the power source. The voltage range for a typical motor is 12V DC. The polarity of the motor can be reversed using a switch on brush DC actuators, which causes the actuator to change its motion. Control electronics are necessary for servo motors and stepper motors in order to electrically control the direction of current within the motor. Rotor feedback is also required for BLDC and servo motor commutation utilizing a Hall effect sensor or encoder.
An actuator's control electronics may be externally accessible or integrated. The speed of the actuator determines how much force is applied. Since there is a relationship between speed and force, a gearbox that reduces the actuator's speed delivers more force. The length of the screw and shaft, which determines the actuator's stroke, is one of the fundamental differences between actuators.
The gears that connect the motor to the screw determine speed. Limit or micro switches, encoders, linear potentiometers, and LVDT transformers are a few of the devices used to end an actuator's stroke. The top and bottom microswitches on the shaft are activated by the up and down movement of the screw.
This chapter will discuss the design considerations for linear actuators and the considerations required when choosing linear actuators.
The duty cycle determines how frequently and for how long the actuator will operate. Since power is lost through heat, the duty cycle is determined by the actuator's temperature while it is in motion. By adhering to the duty cycle recommendations, you can prevent motor overheating and component damage in the actuator. There is variance in the duty cycles of actuators because they are not all created equally. Age, loading characteristics, and ambient temperature are all important variables to consider that might affect duty cycle motors.
Even though speed is crucial when choosing an actuator, it's also crucial to take the weight that needs to be moved into account. An actuator will move more slowly when a lot of force is needed to move a weight. An actuator measures speed in terms of distance traveled per second. By calculating the required duty cycle, you can get information that will assist you when choosing the suitable actuator for the job.
The different types or orientations of linear actuators which 12V linear actuators can be found in include:
The fundamental task of mechanical or electromechanical linear actuators is to translate rotating motion into linear motion. They perform the conversion utilizing one of the screw, wheel and handle, or cam types typically used in linear actuators.
An AC or DC motor provides the power for mechanical linear actuators. The ball screw, roller screw, or another type of screw design is used in mechanical linear actuators of the screw type. Driven straight ahead is a revolving screw-type shaft. The shaft is turned in the desired direction by a stator assembly.
A belt, chain, rack, or cable that is attached to the shaft is used in the wheel and handle variant. This kind of linear actuator employs a variety of guide systems, including recirculating bearings, cam roller guides, and plain bearings. They are typically housed because they have long strokes and high operating speeds. The eccentrically formed wheel that revolves in the cam variant generates linear motion. A shaft is moved by the generated thrust. Automobiles typically use this kind of linear motion.
A servo controller is a component of a servo linear actuator that continuously checks the actuator's state and compares desired and actual outcomes. When disparities are found, the actuator is turned on to make up for them. They are employed in automated and remote activities. An actuator that flips a switch or modifies the placement and focus of a lens is controlled by a servo linear actuator. Adjustments handled by servo linear actuators can range from moving tons of material to very minute adjustments of a fraction of an inch. A servo linear actuator's operation and output are both determined by the information it receives.
The controller evaluates the received data in comparison to the expected ideal circumstances. The data input is provided by a wide range of equipment, including various kinds of sensors. Because of its characteristics, servo linear actuators can be used in advanced automation, robotic control, beam steering applications, remote-controlled vehicles, marine applications, and aerospace manufacturing. Servo linear actuators are becoming increasingly commonplace and essential as a result of manufacturing's technological improvements.
Lead screw linear actuators are made to provide linear motion from rotary motor rotation. A lead screw actuator's thread profile and rolled thread structure provide great strength and efficiency. A lead screw actuator's nut must be constructed from low-friction materials or a lubricated metal.
With several motor types, including stepper motors, a lead screw actuator can be used for open loop control. Linear actuators powered by brushless DC motors are available in a variety of sizes and offer excellent speed efficiency at a reasonable price.
A threaded rod and a corresponding nut are part of the lead screw actuator's construction. The motor turns either the rod or the nut by mounting them directly, connecting them through gears or a belt, or both. The component that has to be moved is connected to the element that is not a part of the motor.
Electric linear actuators are machinery that convert electrical energy into mechanical energy to produce linear motion. This type of linear actuator is frequently used with valves that are powered by an outside source. Electric linear actuators often use single-phase, three-phase, AC, or DC motors as their actuation methods.
The same fundamental elements are found in the majority of electric linear actuators. In many instances, these parts consist of an electric motor, a screw, a nut, and gears. When the nut rotates along the screw in an electric actuator, it enables the conversion of electrical energy to mechanical energy. Electric rotary actuators spin from open to closure using butterfly, ball, and plug valves.
Similar to hydraulic linear actuators, pneumatic linear actuators move a piston using air pressure rather than a fluid. In a pneumatic linear actuator, the piston is housed inside a cylinder and is sufficiently large enough to create a tight seal against the cylinder walls. The piston must rise when pressurized air enters the cylinder housing. In a pneumatic linear actuator, the size of the piston and the pressure of the compressed gas determine how much force is applied.
The strength of the actuator rises when the piston is under more pressure. This procedure is clear-cut, easy to follow, and it is finished swiftly and effectively with pneumatic linear actuators. Pneumatic linear actuators can be utilized to make electrical and microprocessor components because they are not sensitive to magnetic force. They can function between -40°F and 250°F and are adaptive to environments with drastic temperature variations. They have no explosive or incendiary potential since they do not produce magnetic interference.
Ball screw actuators, also known as drive screws, turn rotary motion into mechanical energy by using a combination of a ball screw and ball nut. This produces mechanical linear motion. Due to their close production tolerances and the incompressibility of the ball bearings, they are extremely accurate and precise.
Ball screw actuators are extremely robust and can last 5,000 km at moderate loads and speeds or 3,000 km at high loads and speeds. The pitch of the actuator controls its speed. The screw lead, which establishes the linear travel of the ball nut per rotation of the screw, is the screw pitch multiplied by the quantity of threads.
Ball screw linear actuators with a lower screw lead create more linear thrust, whereas those with a higher screw pitch move a nut more axially and more quickly for a given screw rpm. Using a belt, direct, or worm gear drive, the ball bearings move in opposing, hardened rod tracks or grooves that are carved out inside the axially translating ball nut at a specific helix angle.
Ball screw linear actuators are employed in the manufacture of aircraft, missiles, and laboratory and medical apparatus. They can be found in dialysis machines and blood separation devices' pumps. They can withstand larger dynamic loads and transform a motor's torque into thrust.
The components of a hydraulic motor, including a cylinder, a piston, and an incompressible liquid that exerts uneven pressure on the piston, are shared by hydraulic linear actuators. Hydraulic linear actuators are typically used when a lot of force is required and applications that require the most mechanical energy from linear actuators use them. These linear actuators are used in the lifting mechanisms of machines that can lift tons of material.
There is a very good chance that the machinery contains a hydraulic linear actuator wherever significant lifting, or the transportation of huge goods, is required. A hydraulic linear actuator obtains its power from fluid. The actuator's movement can be adjusted by altering the fluid level. Different types of oils have been created for this purpose. Hydraulic linear actuators feature outstanding accuracy and dependability, just like all other linear actuators. They may be made to move like an arm to push and pull a machine's appendages since they are nimble and adaptive.
This chapter will discuss the applications and advantages of linear actuators inclusive of 12V linear actuators.
The following applications are suited for 12v linear actuators:
Other applications of linear actuators include:
The many applications for a linear actuator have increased workplace automation. It reduces production costs while streamlining manufacturing. For the best material handling, electric linear actuators have evolved into a crucial and essential instrument. Loads are moved from point A to point B via linear actuators. The capacity to halt the action mid-stroke is an additional feature of the electromechanical version. Industrial, high-speed, and micro models are a few of the other kinds of actuators used in material handling.
In order to lift, lower, slide, or tilt machines or materials, a linear actuator converts rotational motion into push or pull linear motion. They provide clean, safe, and effective motion control that doesn't require any maintenance. 12 Volt DC voltage sources are used to power 12 Volt linear actuators. The three different varieties of linear actuators are the screw, wheel and handle, and cam. The kind of screw is determined by the upward and downward motion of the screw winding and unwinding. Benefits, design considerations and applications need to be understood when choosing 12V linear actuators.
Electric actuators are devices capable of creating motion of a load, or an action that requires a force like clamping, making use of an electric motor to create the force that is necessary...
A linear actuator is a means for converting rotational motion into push or pull linear motion, which can be used for lifting, dropping, sliding, or tilting of machines or materials. They provide safe and clean...
High-precision, linear motion goods are essential components at the core of several items which are generally used in machine tools and equipment for manufacturing semiconductors. These items are utilized...
A linear actuator actuates, moves, in a linear, straight, line to complete or start a process. There are a variety of terms used to describe a linear actuator such as ram, piston, or activator. They are very common in...
Ball screws are mechanical linear actuators that consist of a screw shaft and a nut that contain a ball that rolls between their matching helical grooves. The primary function of ball screws is to convert rotational motion to linear motion. Ball nuts are used in...
A lead screw is a kind of mechanical linear actuator that converts rotational motion into linear motion. Its operation relies on the sliding of the screw shaft and the nut threads with no ball bearings between them. The screw shaft and the nut are directly moving against each other on...
Linear bearings are a type of bearing that "bear" or support the load of the carriage during its single-axis linear movement and provide a low friction sliding surface for the guide rails. In a linear guide, the carriage is the component that travels in a straight line, back and forth, along the length of the guide rail...
Linear Rails are ideal for moving items through a production process with great precision and as little friction as possible if creating, packing, and distributing products. Linear Rail is a type of gadget that...
Linear slides, also referred to as linear guides or linear-motion bearings, are types of bearings that allow smooth and near-frictionless motion in a single axis. Machine tools, robots, actuators, sensors, and other...
A roller table is a small, stiff, limited linear guide device with an integrated cross-roller guide. Electrical or mechanical drive systems are frequently used to move a roller table, making it easy to transfer heavy loads...