Linear Rails
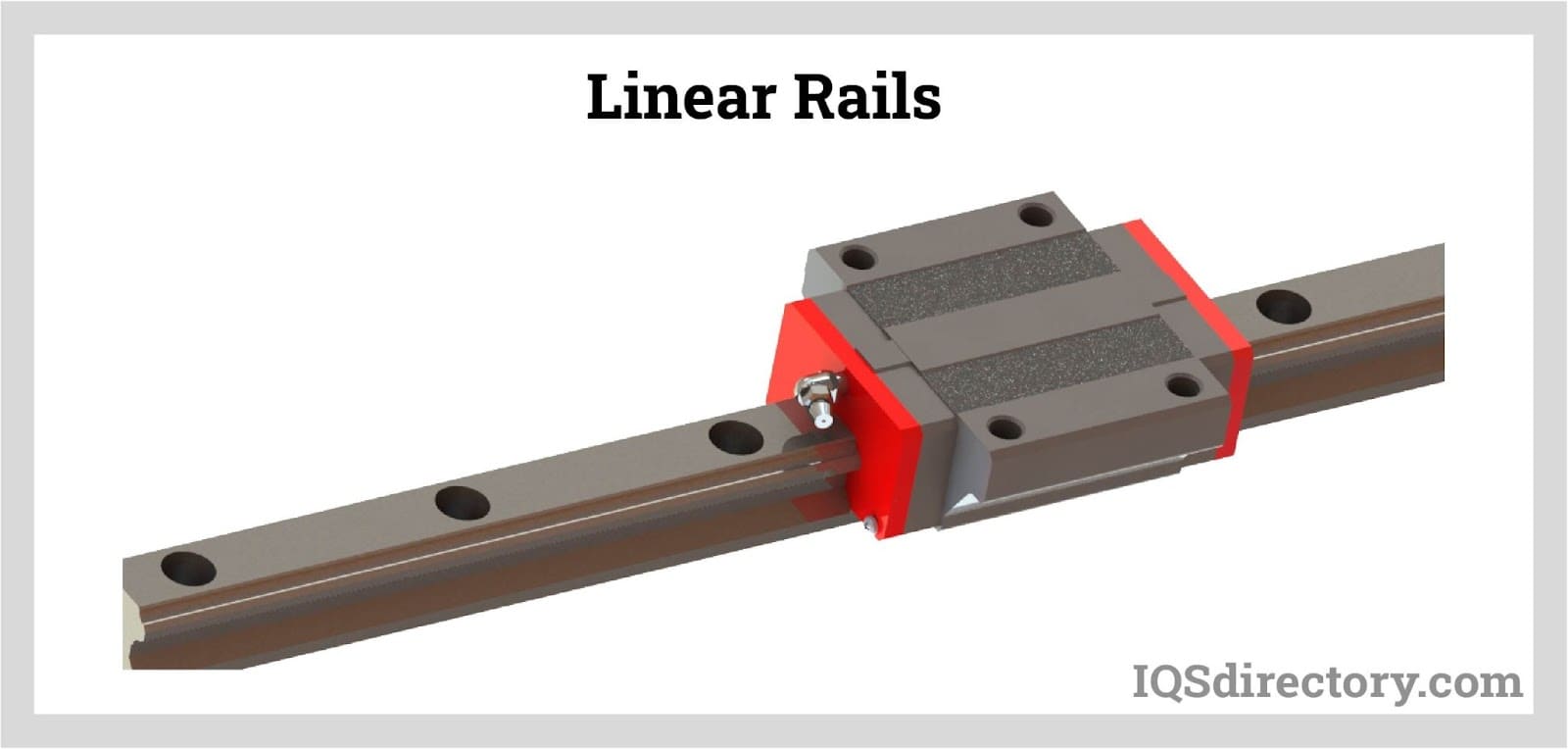
Linear Rails are ideal for moving items through a production process with great precision and as little friction as possible if creating, packing, and distributing products. Linear Rail is a type of gadget that...
Please fill out the following form to submit a Request for Quote to any of the following companies listed on
This article will provide a detailed discussion on roller tables.
It is expected that after reading this feature, one should understand:
A roller table is a small, stiff, limited linear guide device with an integrated cross-roller guide. Electrical or mechanical drive systems are frequently used to move a roller table, making it easy to transfer heavy loads. Positioning stages, described as motorized linear slides with precision rail sets supporting heavy loads with minimum friction, are a synonym for roller tables. Crossed roller bearings, as opposed to the more common ball bearings, are used in roller tables to deliver precise linear motion with low friction and great load-support rigidity. Roller tables provide a highly accurate linear guiding mechanism and are easily mounted with bolts. They are made up of a linear base and an affixed moving carriage.
Roller tables have roller slides with single or many axes, tables, and shafts to maximize direction and control. The size of the intended usage, the material, the weight capacity, and the degree of mobility all go into the design of roller tables. A roller table can be mounted in various ways for multi-axis linear position and motion in the X, XY, or XYZ configurations. Users can stop the table from sliding using shock absorbers or rubber bumpers and employ stroke adjustments for precise alignment. In addition, air-bearing slides for roller tables can be placed when pressured air is controlled between the platform and the base to reduce system errors.
Roller tables are machinery using mechanical or drive systems to easily move huge weights. Roller tables are well-suited for optical measuring devices, electronics assembly machines, and other applications due to their high-precision and low-friction performance. In addition, roller tables are used in various applications, including industrial automation equipment, fiber optic systems, semiconductors, precision instruments, communications equipment, surface grinders, tool grinders, assembly fixtures, and material handling.
One can move roller tables manually with a micrometer, a motor, or a combination of the three. Typically, a lead screw supported by cylindrical bearings is used as the driving mechanism in roller tables to move the carriage. Roller tables are straightforward linear motion devices with a fixed base and a moving carriage. A motorized linear slide is made by attaching the screw to the stationary base and the nut assembly to the moving carriage. The nut and carriage move linearly along the screw as it revolves. A hand wheel or electric motor turns the screw. A driving system for roller tables allows for accurate, controlled placement along a linear axis.
Alternative driving methods, such as linear motors, pneumatic cylinders, and hydraulic cylinders, may be employed instead of lead screws. For example, in a table with a linear motor, the linear motor moves the carriage directly along the slide. The slides are made up of a base with a secure locking mechanism and a movable platform that one may move manually. Roller tables can support big loads since they have two or more slides. When employing hydraulic and pneumatic cylinders with roller tables, the slide base is where the cylinder body is mounted, and the carriage is where the cylinder rod is attached.
A roller table converts a motor's rotational motion into a straight line, making it a linear actuator. Linear actuators travel forward and backward, while conventional electric motors rotate in a circle. Roller tables can slide, tip, and lift objects at a button push, thanks to the push-and-pull motion. They employ various linear bearing techniques to decrease friction, stick-slip, and energy consumption while guiding their slide. Roller tables can be equipped with a roller cage to help avoid slips while moving and balancing loads. In addition, shields and covers are sometimes installed to prevent dust from entering the sliding base and platform and impeding mobility.
A moving carriage attached to a linear base makes up a roller table. The carriage houses the cylindrical or roller bearings that provide low-friction travel between the platform or table and the linear rails. In roller tables, cylindrical bearings are most frequently utilized since they produce the least mechanical noise. Roller tables are made to be extremely accurate and support huge loads when being pushed, pulled, or positioned. Tables with crossed linear rails, heavy-duty, and low profiles are common. Roller tables can have a single axis, or several axes, with shafts and tables to maximize direction and control by using roller slides.
Numerous types of automated machinery benefit from the smooth, accurate linear motion and positioning provided by roller tables. Steel roller table assemblies have a straight line accuracy of 0.0008 inches per inch of travel. Meanwhile, some aluminum/stainless steel roller table assemblies have a straight line accuracy of 0.0000040 inches per inch of travel. A roller table’s capacity to transport loads varies from a few pounds to more than 2600 lbs (1180 kg).
Additional Specifications to Consider:
The rollers are enclosed in a cage, which may be made of plastic or metal, to control their motion. By preventing roller-to-roller contact, the cage lowers friction and saves the rollers from wearing down too quickly.
Traditional metal cages are held in position by tabs on the carriage that slide into notches on the top and bottom of the rollers. This design limits how closely a roller can be positioned together, which limits the load-carrying capacity of the crossed roller bearing, even if it is less expensive to construct. Metal cages are available in stainless steel, a superior option for high-temperature, wash-down, and medical applications where corrosion is unacceptable. Metal is also more suited for applications that require a controlled environment, cleanroom, or vacuum, as cages constructed of resins tend to release a gaseous vapor and may create other harmful conditions.
Resin cages, however, allow rollers to be positioned more closely, increasing the contact area between 30% and 58% over metal cages, allowing for more rollers per inch and up to a 250% increase in load capacity.
Ultimately, what roller table to choose depends on the setting and field of use. The type, pace, and material used to build the table would all be determined by this use. Therefore, understanding where one will utilize a roller table is necessary before choosing one.
The potential for cage creep is crucial when selecting a roller table. Cage creep is where a cage can, over time, drift from its longitudinal center because it floats between the bearing's rails, especially in situations where the slide is mounted vertically or if the linear bearing only performs partial strokes. Additionally, shock and vibration can cause cage creep.
Cage creep can limit slide motion since an off-centered cage will run into a rail end stop and be forced to slip until it recenters itself again once the bearing executes its next full stroke. Cage creep ensures the retainer, rollers, and slideway will sustain damage when skidding into the end stop. Cage creep also indicates that the rollers are slipping rather than rolling, which causes metal-on-metal rubbing and wear.
Fortunately, roller tables often feature anti-creep mechanisms that hold the rollers between the two V-grooved slideway rails to prevent retainers from slipping. The rails can therefore be mounted in any direction. Such anti-creep devices lower maintenance costs and downtime.
The term "allowable load" refers to the maximum weight an object may have while still performing a smooth rolling motion on a contact surface and whose elastic deformation of the raceway and rolling parts added together is minimal. Therefore, if extremely smooth rolling motion and high accuracy are required, employ applied load within the permissible load range.
Choosing a supplier with experience relating to various roller tables is always wise. This experience would facilitate better advice for a roller table that best suits a particular use. Additionally, a provider should stock a range of roller tables in various sizes and makeups to allow users better selection for their specific needs.
The amount of accessible space required for an application is a critical consideration that often restricts the selection of a crossed roller bearing over a recirculating ball bushing. Because only the bushing moves with a recirculating ball bushing, the shaft needs to be only as long as the necessary travel. In contrast, the rail assembly and accessible space must be twice as long as the application's journey length with a crossed roller bearing because the two rails move in opposing directions. However, when the bearing uses plastic cages, the cage can be shorter for a given weight, allowing the stroke length to be longer on a given rail.
If precision is crucial, selecting bearings with a margin of excess load capacity is crucial. This margin is because rollers and rails can deform when they are close to their load limitations, which can change the accuracy—sometimes irreversibly. Roller slide tables are often produced with preload to make them appropriate for high-precision applications and to remove distance between the rollers and guides. Their mounting surface's flatness and parallelism are also precisely machined.
When thinking about a roller table, one should examine the operating velocity or how much material it can move along in a specific timeframe.
A roller table’s platform contains roller bearings that enable minimal friction between the table, or platform, and the linear rails. Most roller tables employ bearings, and cylindrical bearings make the least mechanical noise.
Aluminum is a material that is frequently used to make roller table components because it can bear the force of enormous loads while maintaining its structural integrity. In situations where corrosion resistance is a crucial component of operations, stainless steel is also frequently employed. Roller tables occasionally also feature plastic in their manufacturing. Based on the table's usage, tables can be custom constructed on size, weight capacity, flexibility of movement, and material.
The platform contains roller bearings that enable minimal friction between the table or platform and the linear rails. Most devices employ bearings, and cylindrical bearings make the least mechanical noise. Roller tables can be constructed with different mechanisms, such as: recirculating linear bearings, non-recirculating linear bearings, linear ball bearings, flat-type roller bearings, and crossed roller bearings.
A table can be equipped with roller cages to help balance loads and avoid slippage while being moved. For some applications, linear slides can have coverings or shields to prevent dust and debris from getting inside the sliding mechanism and impeding motion. To ensure the roller table performs at its best, the slides will likely need to be dismantled and cleaned sometimes.
The stud roller system and resin retainers are included in the new varieties of roller tables. The stud roller system is built on a novel idea that completely prevents roller cage sliding while it is in use. Use of this system is permitted in all directions and positions. The developed, integrated stud roller mechanism allows use in all orientations, supports extremely rapid acceleration and deceleration, and eliminates slippage inside the product. A smooth and silent motion is provided by the ideal design of the R-retainers and the roller racetrack.
A roller table comprises two linear bearings, a one-piece base, and a one-piece table.
A driving system of this kind transforms rotating motion into exact linear movements. The screw and nut are the two main components. Actuators using ball or lead screws operate similarly to power screws. The other component is linearly moved when the screw or nut is rotated. Because of its strong design, high driving force, and absence of backlash, ball screws are chosen.
This drive consists of a pinion attached to a linear gear that transforms rotation into linear motion to function. The carriage mounts the pinion, which is powered by a motor. The carriage moves along the rack when the pinion is rotated. In contrast to ball screw and belt drives, the rack allows for the installation of several carriages because each pinion's rotation is independent of the others.
In contrast to conventional motors, a linear motor has a stator and rotor arrangement that is not a continuous loop. Instead, it operates on the same principles as rotary induction motors. The electromagnet on the carriage creates an electromagnetic force that pulls and attracts the permanent magnets mounted on the guide rail. The thrust force is produced by electrically powering the electromagnet. The prior drive units mechanize shaft power but ultimately rely on rotational motors. With no intermediate mechanical components, a linear motor has superior positioning precision since there is less backlash and elastic deformation. Additionally, fewer moving components mean less maintenance and wear.
Piston and cylinder assemblies in pneumatic systems have compressed air supplied to one or both ends. Compressed air is introduced, increasing the pressure inside the cylinder and moving the piston. The motion of the piston controls the extension or contraction of a rod fastened to one of its sides. Two types of pneumatic cylinders exist: single-acting and double-acting. One inlet port is all that a single-acting cylinder has. Pneumatic power is employed for one stroke, while opposing forces like spring force are responsible for the return stroke. An inlet port is found at either end of a double-acting cylinder. As a result, the return stroke now has pneumatic power as well.
Part of the carriage is fastened to the end of the rod in the simplest pneumatic actuators. But for this, the entire length must be twice as long as the stroke. The rod is then changed for alternative coupling mechanisms like cables, bands, and magnets. Pneumatic systems operate at quick speeds and with less accuracy. Additionally, they are appropriate for explosion-proof equipment because there are no mounted electrical components. In contrast to the other varieties, the carriage cannot halt in a middle position. Only end-to-end positions are traversed.
This drive uses almost the same principle as a lead screw, but it is based on the higher precision of a micrometer screw gauge. It usually comes with a lock nut on the side to lock the distances that need to be covered. Once the distance is reached, the table then stops.
The roller tables use different bearings to slide the carriage on top of the base. Here are some of the examples of slide bearings used:
Needle roller bearings have a V-shaped carriage track that forms a 90° angle. On either side of the V-profile, there is a row of cylindrical or needle rollers.
The cylindrical or needle rollers in flat-type roller bearings are positioned in the cage on their horizontal axes. The rollers' axes run parallel to the direction of linear motion.
Slide tables with ball bearings are the most typical kind of linear slide. Ball bearing table slides, which are supported by ball bearings housed in the linear base and have self-lubricating characteristics that promote reliability, provide smooth, precise motion along a single-axis linear design. Recirculating linear ball bearings allow the carriage to move over the length of the guide rail because the balls continuously move in a looped raceway inside the bearing. No matter how long it is, it may move any distance inside the guiding rail. Raceways in recirculating linear bearings are typically numerous.
Metal balls are attached to the cage in linear ball bearings that do not recirculate. The track geometry of the mating grooves between the bearing and the guide rail can be either circular or gothic arch.
Crossed roller bearings offer more precision, stiffness, and weight-bearing capacity for linear motion than frequently used friction-reducing components like ball bearings. Unlike ball bearings, roller tables with crossed roller bearings can also better withstand moment loads, radial forces, or tilting loads. In addition, due to the ability to replace multiple ball bearings with a single crossed roller bearing, ball bearing space is conserved, resulting in a reduction in material costs. Crossed roller bearings are used for high-precision linear motion applications requiring smooth and reasonably quick linear movements. Greater control, load capacity, and precision are all benefits of crossed roller linear rails. In roller table applications, the rails can be crossed at a 45° angle between the base and the carriage.
Heavy-duty crossing roller tables offer good weight-carrying capacity and high precision. Heavy goods and cartons are lifted using heavy-duty roller tables. Most tables have accuracy ranges between 0.0001" and 0.00008" per inch of travel straight line precision, which offer outstanding load-carrying capabilities.
Heavy-duty roller tables are utilized in conjunction with an anti-creep system for vertical applications and applications involving significant acceleration or deceleration forces. Heavy-duty roller tables are usually mechanically driven since they are used for heavy loads. The image below shows a heavy-duty roller table driven by a ball screw. The rail and roller cage design avoids roller cage migration or slippage in high-speed and vertical applications. They include couplings that are fastened together for connections, hex-shaft axles for added capacity and strength, and different curves such as 30, 45, 60, and 90 degrees.
These roller tables can support heavy loads while offering improved control and precision. In addition to other options for application design, crossed-linear roller tables are available in steel construction. Aluminum-crossed roller tables come with both metric and inch mounting holes. One should consider anti-creep tables in situations with strong acceleration, deceleration, or vertical applications. In high vertical applications and at high speeds, roller cage slippage or migration is addressed by the roller cage and rail design. These tables come preloaded and ready for a factory to install. They use crossed roller bearings to deliver exceptionally precise linear motion with comparatively little friction.
High-precision slide tables with adjustable preloading are low-profile roller tables. Low-profile tables can be created using both ball and crossing rollers. Low-profile tables provide linear support and guidance with excellent repeatability and low friction while being extremely precise and accurate. When comparing same-sized tables, crossed roller tables may withstand heavier loads than ball-bearing tables. The rollers are at a 45-degree angle, allowing them to withstand stress in all directions. The low-profile roller table is frequently driven by a pneumatic system.
Roller tables function well under the majority of running speeds and under all kinds of load scenarios. As a result, roller tables are used in the following applications and many others:
Robots' ability to execute an ever-increasing variety of activities presents machine designers with various motion requirements, such as the ability to handle heavy or light loads and complete complex tasks in a smaller area. In addition to their stiffness, smooth motion, and precision, roller tables come in various sizes and constructions to match different rotating motors.
For shafts, roller tables offer precise, fluid linear motion.
The little mechanisms or articulating arms that place and hold objects in the lab can accommodate numerous roller tables. Additionally, they are particularly desirable for indexing tables found in blood centrifuges due to their high precision.
The semiconductor industry needs roller tables to provide the micron-scale accuracy needed for pick-and-place systems and silicon wafer-handling machinery. Additionally, they can be set up for cleanroom settings.
There is plenty of equipment used in the military and aerospace industries that uses precise linear motion to move items. For example, because of their high load capacity, high precision, and rigidity, ball and cylindrical roller bearings in roller tables are ideal for airline seat adjustment systems.
Spindles for food processors and slicers must be precise, long-lasting, and spotless. Crossed roller tables can provide stiffness, precision, and load capacity without contaminating the food products when used with food-grade greases.
Linear Rails are ideal for moving items through a production process with great precision and as little friction as possible if creating, packing, and distributing products. Linear Rail is a type of gadget that...
Linear slides, also referred to as linear guides or linear-motion bearings, are types of bearings that allow smooth and near-frictionless motion in a single axis. Machine tools, robots, actuators, sensors, and other mechanical equipment often require moving components in a straight line in any of the three-dimensional axes...
A linear actuator is a device that transforms rotational motion into push or pull linear motion, which can then be used to lift, lower, slide, or tilt machinery or materials. They offer effective, maintenance-free motion control...
Ball screws are mechanical linear actuators that consist of a screw shaft and a nut that contain a ball that rolls between their matching helical grooves. The primary function of ball screws is to convert rotational motion to linear motion. Ball nuts are used in...
Electric actuators are devices capable of creating motion of a load, or an action that requires a force like clamping, making use of an electric motor to create the force that is necessary...
A lead screw is a kind of mechanical linear actuator that converts rotational motion into linear motion. Its operation relies on the sliding of the screw shaft and the nut threads with no ball bearings between them. The screw shaft and the nut are directly moving against each other on...
A linear actuator is a means for converting rotational motion into push or pull linear motion, which can be used for lifting, dropping, sliding, or tilting of machines or materials. They provide safe and clean...
Linear bearings are a type of bearing that "bear" or support the load of the carriage during its single-axis linear movement and provide a low friction sliding surface for the guide rails. In a linear guide, the carriage is the component that travels in a straight line, back and forth, along the length of the guide rail...
High-precision, linear motion goods are essential components at the core of several items which are generally used in machine tools and equipment for manufacturing semiconductors. These items are utilized...
A linear actuator actuates, moves, in a linear, straight, line to complete or start a process. There are a variety of terms used to describe a linear actuator such as ram, piston, or activator. They are very common in...