Aluminum Forging
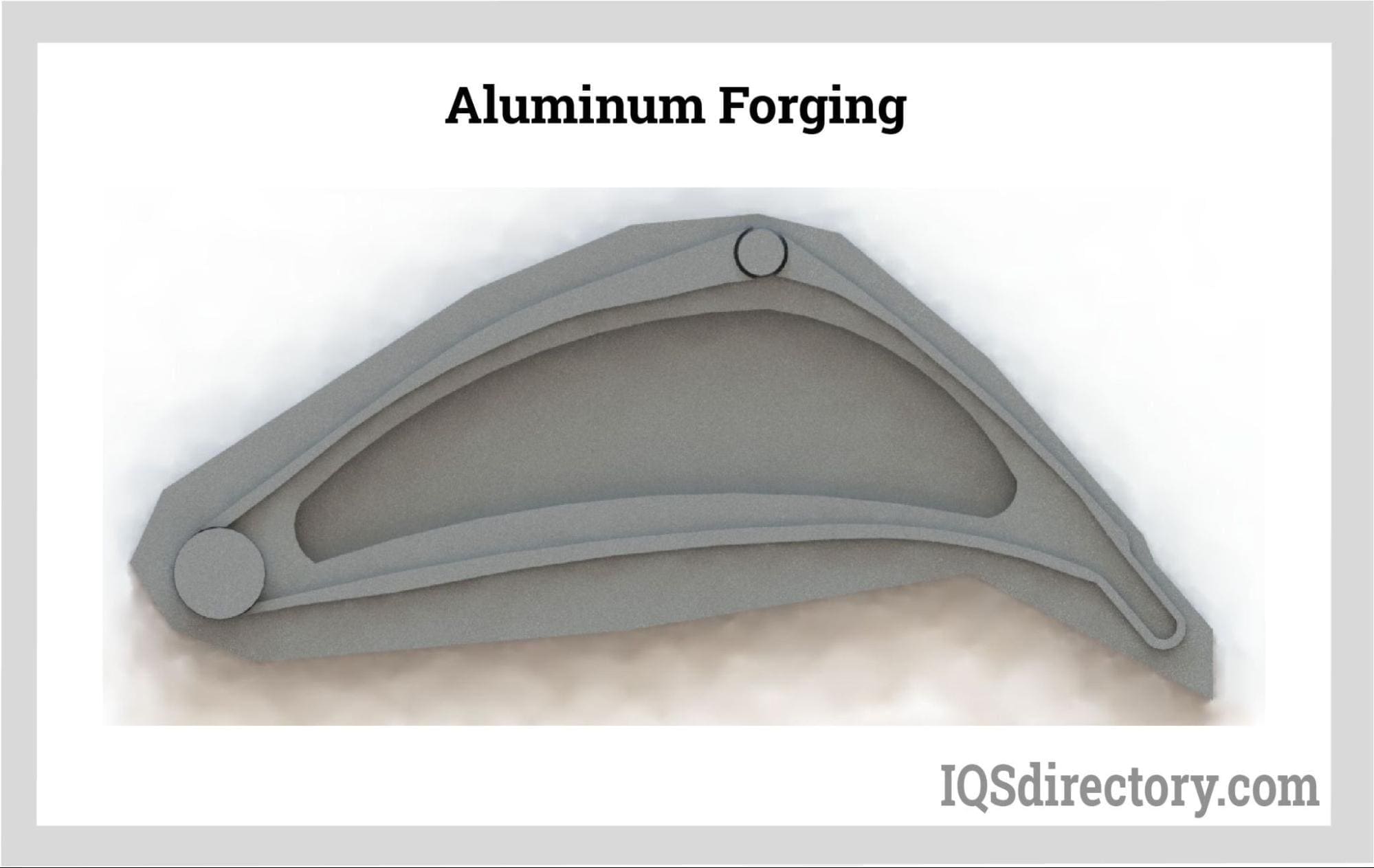
Aluminum forging is a method for processing aluminum alloys using pressure and heat to form high strength, durable products. The process of aluminum forging involves pressing, pounding, and...
Please fill out the following form to submit a Request for Quote to any of the following companies listed on
This article takes an in-depth look at rolled ring forging.
You will learn more about topics such as:
Rolled ring forging is a metalworking process that begins with a circular preformed piece of metal that has been upset and pierced to form a doughnut-like shape. The temperature of the doughnut shape (torus) is heated to a point above the recrystallization temperature and placed over a mandrel or idler.
The idler moves the pierced doughnut shape toward a drive roller that evenly, continuously, and uniformly rotates to reduce the wall thickness of the torus while increasing its inner and outer diameters. The results of the process are a seamless rolled ring.
Using the rolled ring forging process, the seamless metal rings can have varying sizes and are manufactured for use as parts of machine tools, turbines, pipes, and pressure vessels. Rolled ring forging significantly affects the mechanical properties of the material being shaped while allowing it to maintain its grain structure.
The rolled ring forging process produces workpieces with improved densities and aligned grain flows. Their weight can be from a few pounds up to thousands of pounds, and they come in diameters ranging from a couple of inches to over twenty feet. Configurations from rolled ring forging include washer-like parts and cylindrical shapes. Wall-thickness-to-height ratios range from 1:16 up to 16:1, with larger proportions being achievable with special processing.
The most common cross-sectional shape for rolled ring forged pieces is rectangular. Shape tooling is used to produce complex, custom shapes with unique contours on the ID and OD.
Rolled ring forging is an open die forging process that forges a workpiece that has been cut, weighed, and rounded such that upsetting will achieve the desired structural integrity and directional grain flow. Open die forging processes repeatedly work the workpiece, increasing its strength and improving its resistance to fatigue while eliminating voids.
Rolled ring forging is recognized for its reduced material cost, versatility, and the exceptional quality of the finished products. It produces flat washers and cylinders two feet high, with an outside diameter of several feet weighing over six tons. In addition, the grain structure of the metal being processed is retained since the metal is not liquified.
The lack of waste and the versatility of sizes makes rolled ring forging an ideal method for metal forming. Any type of metal can be shaped using the process, including stainless steel, aluminum, nickel alloys, and all forms of steel. The main type of rolled ring forging is seamless rolled ring forging, which produces rolled rings with added strength and fatigue resistance not found in welded rings or torch cut rings.
The first step in the rolled ring forging process is to take a billet, normally a cylinder, and upset it. The function of upsetting is to prepare the workpiece by deforming it to the necessary diameter, height, and shape, all of which increases its cross section. This deforming process places the workpiece under a great deal of pressure that is applied horizontally by a hydraulic press. The necessary force is applied in the direction of the workpiece’s length axis, increasing the area of the cross section.
The dies for upsetting compress the workpiece at its plastic deformation temperature and allow it to spread beyond the press. It is an open die process where the cylinder is pressed by an upper and lower die and can be completed either hot or cold.
When a workpiece is heated for upsetting, changes occur in a metal's grain structure, which happens any time a metal is heated. When it is heated beyond its austenite stage, there will be a change in the grain structure. In the austenite phase, there is a transition from body centered crystal lattice to the face centered cubic crystal lattice, which is the austenite phase where metals are ductile and soft, making them easy to shape.
Upsetting is a common forging method that is used to shape and form multiple pieces quickly and efficiently. It is used to form the heads of bolts as part of cold forging. Upsetting machines have a ram that moves in a horizontal direction against a workpiece. The results of the horizontal strokes are an increase in the volume and shape of the workpiece.
In seamless rolled ring forging, the center of the workpiece has to be removed. There are various names used to describe this part of the process, which include punching and shearing. Its purpose is to create a hole in the middle of the workpiece. The distance between the die and punch is determined by the thickness and strength of the workpiece, parameters that also govern the load or pressure at the cutting edge of the tool or the point of pressure.
The result of piercing is the creation of a round doughnut shape. Piercing does not drill into the workpiece but creates an opening through its middle by forcing a punch that radically displaces the metal, leaving a thin web at the bottom of the pierced opening. It is classified as a forging process due to the fact that it does not drill or grind the surface of the workpiece.
There are multiple forms of piercing, including lancing, shaving, cut-off, and parting-off. The method that is used for the preparation of a workpiece for rolled ring forging is referred to as punching since it punches through the middle of the billet. The portion that is removed is scrap that is used to form other billets.
The overall purpose of shearing, beyond its use in rolled ring forging, is to trim and remove the unwanted portions of metals in preparation for further processing. It is a cold working process that uses various types of tools. In the case of rolled ring forging, the shearing tool is a punch that completes the piercing process by removing the web at the bottom of the pierced hole.
In order for the workpiece or doughnut shape to fit smoothly over the mandrel or idler, the surface of the ID has to be smooth and even free of obstructions. The shearing tool, in a single stroke, travels the length of the pierced hole and punches out the bottom web. The result is a completed hole that goes through the workpiece to prepare it for the rolled ring forging process.
The piercing and shearing processes create a hole in the workpiece such that it can be placed over the mandrel, a blunt end rod used to shape the hole of the doughnut. Mandrels, known as saddles or idlers, are made of steel or medium carbon steel and have sufficient strength and durability to apply the necessary force and withstand the stress created by pressuring the workpiece.
Prior to being placed over the mandrel, the workpiece is heated to a point just below its recrystallization temperature. It is then rotated in a series of small steps used to forge the ring to its final dimensions and shape. The mandrel, saddle, or idler forces the doughnut-shaped workpiece against the drive roller, the force of which increases its ID and OD to match the design of the final part.
The shaping process begins with the slow, incremental rotation of the preformed doughnut shape by the main roller. As the doughnut turns, the mandrel applies pressure against the interior of the doughnut and presses it against the main roller. The rotation and pressure increase the inner and outer diameter of the workpiece and make its walls thinner.
In the diagram below, the main roller is to the left of the yellow workpiece with the mandrel inside the workpiece to the right of the main roller pressing the ring of the workpiece against the main roller. The overall process takes place slowly and with precision in order to reach the proper dimensions and form.
As the mandrel and main roller increase the diameter of the workpiece and thin its walls, the axial rollers reduce the height of the workpiece’s cross section. The rotation of the workpiece by the main roller and mandrel as well as the motion of the axial rollers, happens at a continuous gradual rate allowing the workpiece to retain its grain formation.
Axial rollers are vertically displaced, taper rollers that are mounted horizontally across from the mandrel and main roller. They are designed to squeeze and control the height of the workpiece as it is slowly rotated by idler and main roller. The motion of the idler and axial rollers changes and creates the desired cross-sectional shape.
The rotation and forming of the workpiece continue until the desired dimensions are achieved. This particular process is referred to as seamless rolled ring forging since the shaping and forming of the final part does not include cutting, welding, or forging. The piece remains as a solid single metal piece throughout the process.
Final completed pieces from seamless rolled ring forging are used for components and parts for power plants, chemical plants, freighters, cargo ships, and windmills.
The various methods for rolled ring forging are classified according to how the ring is rolled, which can be radial, radial axial, horizontal, or vertical. The different rolling methods deform the workpiece in a unique way to achieve a particular shape and grain structure. Additionally, the different methods are capable of producing different ring profiles such as flanges, sheaves, and anti-friction rings.
Radial axial ring rolling is the classic form of rolled ring forming and involves the main roll rotating as the mandrel squeezes the workpiece and runs idle due to the friction on the contact surface. The axial rollers rotate at an inverse rate and withdraw as the diameter of the ring increases. As the diameter increases, the upper conical axial roller slides toward the lower axial lower, which causes height reduction in the ring. Guide rollers touch the outer diameter of the ring to keep it circular.
The radial axial rolled ring process requires precision control of all three sets of rollers to ensure the quality and performance of the final product. Control of radial axial rolled ring forging involves the use of a closed loop system with a single point laser distance measuring tool.
Radial rolled ring forging, known as hot radial rolled ring (HRRR) forging, is a rolled ring forging process used to produce medium scale bearing rings. During the process, the HRRR mill’s main roller produces the necessary rotation and linear feed as the mandrel creates passive rotation. Guide rollers are positioned at the exit side of the main roller with a signal roller placed at the opposite side of the guide roller. The determination of the end of the rolled ring process is when the outer diameter of the ring touches the guide roller.
During the rolling process, the wall of the ring is compressed radially as the metal expands tangentially, regardless of the axial direction not being limited by a roller. The radial rolled ring process is best suited for rectangular cross sections, grooved shapes, and ten shaped rings.
The typical conventional method for rolled ring forming is completed on a horizontal rolled ring forging machine with a radial and axial ring rolling mill. The vertical version of a rolled ring forging machine has a pair of main rollers, a mandrel, and multiple restraining rollers. The main rollers axles are inclined at 20o to 30o from the horizontal and are motor driven. The mandrel is idle driven by the ring being formed and is mounted on the lifting frame, which is lifted by a hydraulic control to press the ring. The restraining rollers are positioned to meet the parameters of the rings diameter and to ensure its roundness.
Horizontal rolled ring forming is the traditional type of rolled ring forming that is most commonly used. The workpiece moves in a radial direction with a mandrel placed on the inner side of the ring to press the ring wall. Axial rollers, positioned on the upper and lower or bottom and top of the ring, determine the height of the ring. Centering rollers assist in maintaining the smoothness of the ring and its roundness and are idling rollers driven by the movement of the forged ring.
There are many machines available to perform rolled ring forging, and they are important in today's society because rolled ring forging allows for the efficient production of high-strength, seamless, and near-net-shape rings used in critical applications such as aerospace, energy, and automotive industries. Below, we discuss many notable brands of machines used for rolled ring forging:
SMS Group offers the RAW series of machines for rolled ring forging, known for their advanced automation, precise control systems, and high throughput capabilities, allowing for efficient and precise production of rolled rings.
Siempelkamp specializes in the production of RingRoller machines, which are designed for rolled ring forging, featuring advanced hydraulic systems, CNC controls, and the ability to handle a wide range of ring sizes and materials.
Ajax-CECO offers the RRG (Rolled Ring Generator), a versatile machine designed for rolled ring forging, featuring advanced control systems, high forming force, and customizable options for various ring sizes and materials.
Forging Equipment Solutions offers ring rolling machines for rolled ring forging, featuring advanced controls, robust construction, and the ability to produce high-quality rolled rings with precision and efficiency.
Scot Forge provides ring rolling mills for rolled ring forging, offering precise control, efficient material utilization, and the ability to produce seamless and symmetrical rings with excellent mechanical properties.
Please note that specific models, features, or components may have evolved since this update. It is advisable to consult the respective manufacturers or industry resources for the most up-to-date information on the latest models and capabilities of machines used for rolled ring forging in the United States and Canada.
The seamless rolled ring forging process offers the choice of several different types of materials, including carbon steel, stainless steel, alloyed steel, waspaloy, Inconel, and Hastelloy X. The rolled ring forging process is a quick and inexpensive method for shaping products with excellent ductility, impact, and fatigue resistance.
The choice of metals being used for a project depends on its final use. Each type of metal has characteristics and properties that can be applied to specific groups of applications depending on the strength and endurance that is required.
Carbon steel is used for applications that do not require the strength and cost of stainless steel. The rolled ring forging process enhances the strength of the steel, which makes it more durable. The results of rolled ring forging of carbon steel forces porosity from the metal and creates a consistent grain flow. Unlike other ring manufacturing processes, the rolled ring process forms carbon steel to meet exacting tolerances to provide high quality performance.
Alloy steels are made from a combination of metals that bind together to form an extremely strong form of steel. The quality, strength, and endurance of alloy steel depend on how the alloys are mixed. Different quantities of carbon are added to enhance the strength of steel. As the amount of carbon increases, steel becomes harder and more difficult to work. It is always added to when it is important to increase tensile strength.
The common metals that are combined with steel include:
The grades of alloy steel that are commonly used for rolled ring forming are:
The weight of rolled rings from alloy steel vary from ten pounds up to several thousand pounds. The variations in weight include different diameters and ring thicknesses. There are several post processing procedures that can be performed in alloy steel that enhance its endurance and life span.
Stainless steel is an obvious choice for use in rolled ring forging due to its exceptional strength, corrosion resistance, ability to be recycled, and long lifespan. Of the many selections of metals, stainless steel is the most popular and widely used.
Stainless steel is an iron based alloy made up of at least 10% chromium. The special properties of stainless steel are due to the chromium rich oxide film it has on its surface. The term stainless steel is a generic description of an assemblage of metal grades, with each having a different combination of alloys.
Common grades of stainless steels used for rolled ring forging include A 182 and several three and four hundred grades. Aside from the strength and endurance of stainless steel, finished rolled ring forged products have an exceptionally pleasing aesthetic appearance.
The many positive properties of aluminum alloys make them ideal for seamless rolled ring forging. The tensile strength, toughness, and fatigue strength for which aluminum is famous can easily be used to shape aluminum with internal structure and circumferential grain flow. An added benefit of aluminum is its superior surface finish, which is exceptionally smooth.
Pure aluminum is rarely used for production unless corrosion resistance is more important than strength. To increase the hardness and endurance of aluminum, various alloys are added, which are used in the rolled ring forging process.
Rolled ring forging aluminum alloy grades include:
Titanium is lighter than steel but has an exceptional strength-to-weight ratio with corrosion resistance. It is a silvery-white metal protected by an oxide covering, enabling it to withstand acids and chemicals. In addition, the strength of titanium makes it capable of resisting erosion and metal fatigue. Though titanium has an excellent strength-to-weight ratio, it is much lighter and less dense than alloy steel.
The formability of titanium is improved by rolled ring forging, which decreases its tendency to spring back and reduces the risk of structural defects.
Hastelloy X is an austenitic nickel based alloy made from nickel, chromium, and iron with a small amount of cobalt. It has exceptional strength at high temperatures and is corrosion-resistant. The use of Hastelloy X is due to its heat, oxidation, and chloride corrosion resistance, as well as its resistance to reducing and carburizing conditions.
Hastelloy X is used for rolled ring forging because of its ductility and ability to be cold worked. In addition, it can be easily machined in its annealed form.
Inconel is an austenitic nickel chromium alloy that is resistant to oxidation and maintains its structural integrity at extremely high temperatures and in severe environments, and has wear and corrosion resistance. Inconel has high tolerances, which makes it ideal for a variety of specialized industries that require precision and accuracy.
Seamless rolled forged rings are widely used in a variety of industries and are the foundation of critical machines and equipment. While other metal-forming processes weaken metals during processing, seamless rolled rings are sturdy and tough since they are formed from a solid piece of metal. They are designed to withstand corrosion, high temperatures, and hostile and harsh environments.
The precision manufacturing process used to produce seamless rolled rings produces products with high tolerances capable of meeting any specifications. Every completed component precisely fits its application.
A major factor in the harvesting of oil is transporting it through pipes. There is a limitation on the length of a pipe before it needs to be connected to the next length of pipe. The fear of connecting pipes is the tendency of the connections to leak. It is for this reason that seamless rolled forged rings are used to make the connections. Made to exacting specifications, seamless rolled forged rings guarantee durability and no leaks.
The fracking process places a great deal of stress on the parts and connectors related to hydraulic fracturing. Seamless rolled rings have the durability and strength to withstand the stress since they do not crack, corrode, or fail at high temperatures. Their long lifespan offers dependability and reliability during the fracking process.
The safety and welfare of passengers and pilots depend on gearboxes that play a significant part in flight operations. Using exceptionally durable metals and alloys, gearboxes are manufactured using the seamless rolled ring forging process, which creates high-functioning, long-lasting gearboxes.
Flight operations depend on materials that are precision engineered to avoid mechanical failures. Gearboxes for jet engines and helicopters have a tremendous amount of stress placed on them. Seamless rolled ring forging produces gears and bearings that are lightweight to meet aircraft requirements but strong and resilient for dependability.
Every aspect of a wind turbine has some form of seamless rolled ring forged parts. They are an essential part of wind turbine construction. The accuracy, precision, and strength of seamless rolled ring forged parts makes them an ideal choice for keeping wind turbines running and productive.
The main shaft of a wind turbine is designed to withstand the constant changes in axial and radial loads. Seamless rolled rings serve as bearings to assist the shaft in handling the varying loads.
Wind turbines produce and endure constant wear and tear, which is the reason that seamless rolled ring bearings capable of withstanding the stress are used to prevent breakdowns and lost energy.
Other wind turbine parts made using seamless rolled ring forging technology include flanges that connect sections of the tower, gears, and couplings that assist in withstanding the torque between the gearbox and the generator.
Several parts of vehicles have to endure high loads and stress, which necessitates the use of components capable of enduring and withstanding the conditions in order to keep a vehicle running. Seamless rolled ring forged components and parts can be found in every part of trucks and cars. Crankshafts, camshafts, clutches, braking systems, gears, and couplings are all made using seamless rolled ring forging. These high-quality parts are capable of withstanding the constant wear, pressure, and tearing that is common in the daily use of a vehicle. They are lighter and more versatile as well as resistant to the continual torque.
The types of rolled ring forging are divided by the types of metals used in the process and consist of three basic types, which are stainless steel, alloy steel, and carbon steel. Although these metals are used as a general description of the types of rolled ring forging, they are representative of a wide range of other metals that are forged using the rolled ring process. Strength and toughness are two qualities that are necessary for metals shaped in rolled ring forging due to the stress placed on the workpiece.
A necessary component of every modern manufacturing process is the production of strong and durable products. Parts with long lifespans are required by every customer. Seamless rolled ring forging is a forging process that produces strong components and parts that are guaranteed to last through all conditions.
Seamless rolled ring forging can be used to produce a wide assortment of bearings, gears, couplings, and connectors using a variety of durable metals. The seamless nature of the process is a major factor in the strength and endurance of the components produced.
The popularity of rolled ring forging is due to the incredible strength that rolled ring forged parts possess. In conditions where other parts may fail, rolled ring forged parts can endure and perform, even if the temperature is extremely high. For this reason, they are found in jet engines, windmills, paper mills, and oil refineries.
The high temperatures used in rolled ring forging mean that the process's grain patterns give the final products exceptional strength and resistance.
The complexity of the rolled ring forging process may give the impression that the cost of the final product is excessively high. In actuality, the opposite is the case. The parts and components produced by rolled ring forging are competitively priced in comparison to other forging and fabrication methods. Unlike seamless rolled ring forging, other forging processes involve a great deal of handling and machining, which increases their cost.
In addition, low tooling costs and fast set up times assist in reducing production costs. Since workpieces are made from a single piece of metal, there is little waste, which makes production efficient.
Seamless rolled ring forged parts can be produced using any form of metal, from high tensile strength stainless steel to various copper alloys. This particular characteristic gives customers and producers the ability to choose the precise material to fit the application where the part will be used.
The manufacturing process of seamless rolled ring forging processes metals near or at their recrystallization point during configuration and formation. The steps in the process and how metals are handled makes the final product capable of withstanding and enduring high temperature environments.
Aluminum forging is a method for processing aluminum alloys using pressure and heat to form high strength, durable products. The process of aluminum forging involves pressing, pounding, and...
Cold forging is a metal shaping & manufacturing process in which bar stock is inserted into a die and squeezed into a second closed die. The process, completed is at room temperature or below the...
Copper and brass forging is the deformation of copper and brass for the purpose of manufacturing complex and intricate shapes. The temperature at which copper and brass are forged is precision controlled and...
Forging is a metal working process that manipulates, shapes, deforms, and compresses metal to achieve a desired form, configuration, or appearance outlined by a metal processing design or diagram...
In this article, there are key terms that are typically used with open and closed die forging and it is necessary to understand their meaning. Forging is a process in manufacturing that involves pressing, hammering, or...
Forging steel is a manufacturing process used to shape steel by using localized compressive forces, which include hammering, pressing, and rolling. It is a widely used method for producing high quality steel products...
The ancient art of forging falls into two distinct categories – hot and cold where hot forging has been around for centuries while cold did not begin until the industrial revolution of the 19th Century. Though they are quite different ...
Aluminum casting is a method for producing high tolerance and high quality parts by inserting molten aluminum into a precisely designed and precision engineered die, mold, or form. It is an efficient process for the production of complex, intricate, detailed parts that exactly match the specifications of the original design...
Die casting is a high pressure metal casting process that forces molten metal into a mold. It produces dimensionally accurate precision metal parts that have a flawless smooth finish...
Sand casting is a manufacturing process in which liquid metal is poured into a sand mold, which contains a hollow cavity of the desired shape and then allowed to solidify. Casting is a manufacturing process in which...
Zinc die casting is a casting process where molten zinc is injected into a die cavity made of steel that has the shape, size, and dimensions of the part or component being produced. The finished cast zinc product has...
The casting process is an ancient art that goes back several thousand years to the beginning of written history. The archeological record has finds that document the use of the casting process over 6000 years ago around 3000 BC or BCE...