Aluminum Forging
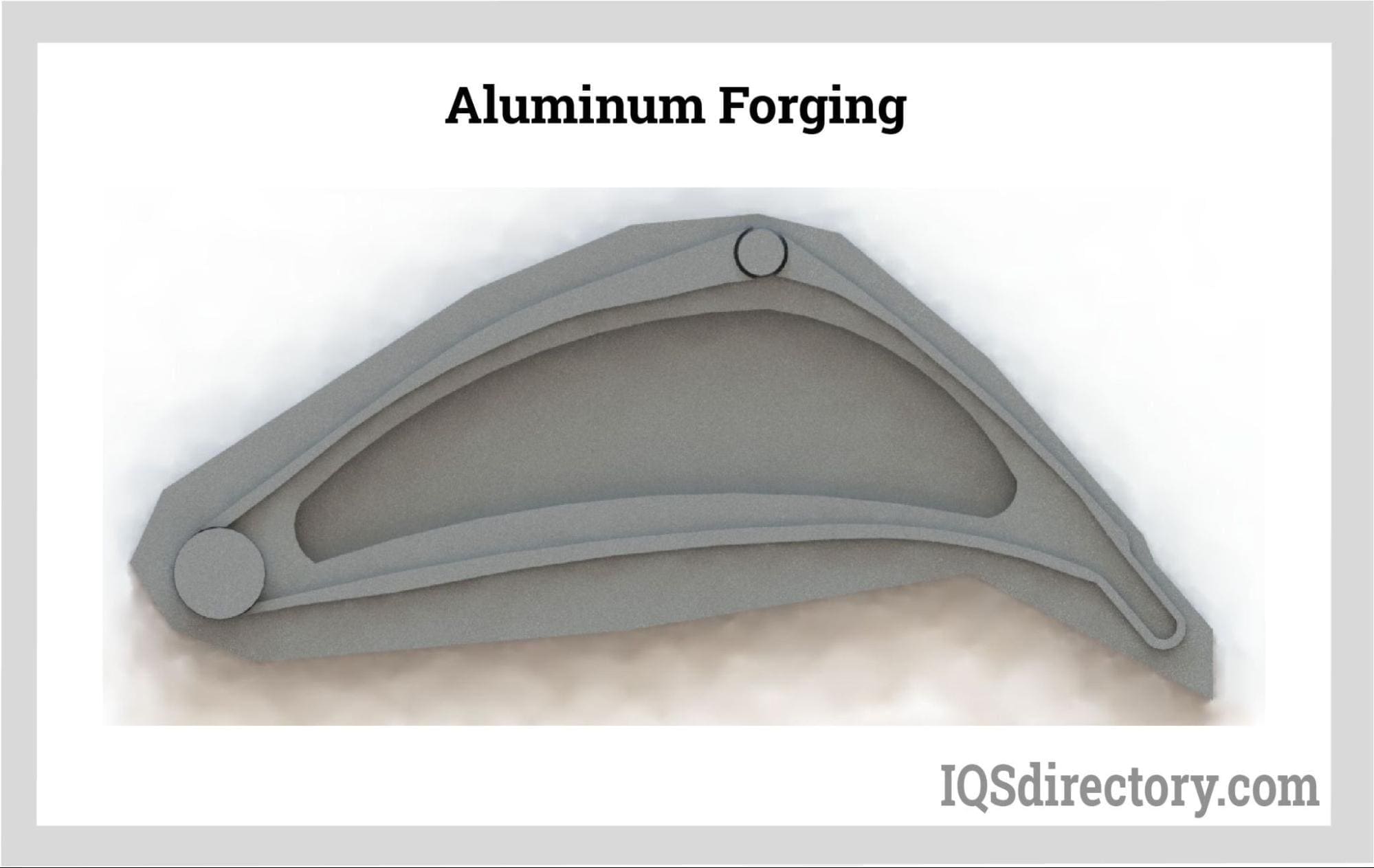
Aluminum forging is a method for processing aluminum alloys using pressure and heat to form high strength, durable products. The process of aluminum forging involves pressing, pounding, and...
Please fill out the following form to submit a Request for Quote to any of the following companies listed on
The content of this article provides detailed information about forging steel.
You will learn:
Forging steel is a manufacturing process used to shape steel by using localized compressive forces, which include hammering, pressing, and rolling. It is a widely used method for producing high quality steel products with exceptional tolerances. The steel for forging is produced by alloying iron and carbon, which is manufactured under controlled pressure to ensure proper ductility, fatigue strength, tensile strength, and outstanding grain structure.
The three distinct classifications for forging steel are cold, hot, and hardened, which are separated by their forming pressure and the temperature at which the process is completed. Forging steel is one of the methods used to shape and form steel and is distinctive in the properties it creates in forged steel, which are unlike those found in cast steel and include solidity, anisotropic, and consistency.
Forging steel makes the metal stronger for use in mechanical and industrial applications. Parts are more reliable with uniform composition and structure and preferred for high loads and stress. They are free of voids, pockets, and other defects that could lead to load failure.
All processes for forging steel take the same form, which is applying some form of force to a steel billet that is heated before processing or processed at room temperature. The temperature at which the forging is completed is dependent on the type of processing and can include dies, presses, rollers, and other methods used to apply pressure. The key in every method is the application of some form of force and the ductility of the billet.
As with all aspects of manufacturing, forging steel begins with a design or plan as to the shape of the final product. With die forging, the die is produced that has the desired shape. Rolling, pressing, and other forms of steel forging have a design in mind when applying force to the billet.
Billets are produced by hot rolling or extrusion and have a square or rectangular shape with uniform dimensions along their length. They have a smooth surface and are used to produce a number of different products. In preparation for the forging steel process, the raw billets are cut to lengths to match the dimensions of the design. The grades of steel billets are determined by the carbon content of the steel and its microstructure. They are carefully chosen such that they meet the needs and requirements specified in the design.
The temperature of the billet varies in accordance with the process being used to shape it. For some processes, the billet is heated to make it malleable for shaping such as die forging, which is a hot forging process. Cold forging does not heat the billet and shapes it at room temperature. Heating of the billet is the main differentiating factor between the various processes. When the billet is heated, it is easier to form since it becomes ductile and highly malleable. Cold forging requires more force and pressure for shaping the steel.
Forging steel processes are open die forging, closed die forging, roll forging, cold forging, and extrusion. The processes vary according to how force is applied, and the pressure placed on the billet to shape it into the form required by the design. Additionally, each of the methods is used to produce different products, which include structural parts like landing gear for aircraft, shafts for jet engines, and turbines. Forging steel is used to manufacture hand tools such as chisels, rivets, screws, and bolts.
A common after processing stage in forging steel is finishing, which can include grinding, removing flash, smoothing of surfaces, buffing, or other machining applications used to achieve the proper texture for the finished part. As with the different processes, finishing methods vary according to the method used to forge the steel.
A more aggressive form of finishing is shot blasting, which includes pummeling a forged part with metal beads, sand, or other forms of particles. It is used to achieve a better surface finish that is not possible with other finishing methods. The finished surface from shot blasting tends to be clearer and smoother.
Heat treatments are applied to forged parts to improve the mechanical properties of the metal, including its strength. Common forms of heat treatments are normalizing, quenching, annealing, tempering and hardening, and spheroidizing. The use of heat treatments is only included in the forging process when it is required and part of the design.
The final step in the forging process is one of the many forms of surface treatments, which can be as simple as cleaning the finished forging with water or oil or be as complex as zinc plating, galvanizing, electroplating, or painting. As with other stages of the process, the type of surface treatment is dependent on the requirements of the design of the forging.
An important aspect of steel forging is the selection of the type of alloyed steel to be used since the elements added to steel improve its physical and mechanical properties, which include its hardness, strength, toughness, high temperature performance, and its resistance to corrosion and wear. The types of alloys include boron, chromium, molybdenum, manganese, nickel, silicon, tungsten, and vanadium with lesser used ones being aluminum, cobalt, copper, lead, tin, titanium, and zirconium.
There are 57 different types of steel whose properties differ in accordance with the percentage of the elements mixed into the alloy and make up 1% to 50% of the composition of alloyed steel. In order to organize the many types of steel alloys, they are grouped by their elements and the percentage of the added alloys with high alloy steel having more than 8% of alloying elements while low alloy steel has less than 8%.
Carbon is the essential element in the creation of alloyed steel, which makes up 0.35% of steel. The addition of carbon to steel increases steel's hardness and strength as well as its hardenability. The down side of steel’s carbon content is that it increases steel's brittleness and reduces its ability to be welded due to the formation of martensite.
The three classifications of carbon steel are plain, low, and high with plain steel being iron with less than one percent of carbon and small amounts of manganese, phosphorus, sulfur, and silicon. Low alloy steel has a carbon content below 0.25% and is alloyed with nickel, chromium, molybdenum, manganese, and silicon to add strength and increase low temperature toughness.
High alloy steel is stainless steel, which has a 12% chromium content and high nickel content with the three basic types being martensitic, ferritic, and austenitic with ferrite having the highest chromium content between 12% up to 27% with small amounts of austenite alloys. The many special properties of stainless steel make an extremely popular steel alloy.
The SAE developed a numbering system to help define and identify the different types of carbon steel and steel alloys. The numbers for the SAE system have four digits with the first digit representing the general grouping of steels with the number 1 representing carbon steel. Plain carbon steel is represented by 10XX while resulfurized carbon steel is 11XX, and rephosphorized carbon steel being 12XX.
The second digit of the SAE numbering system represents the steel's major element with zero (0) indicating the absence of sulfur, which is essential for the machinability of steel. The final two digits of the four digit number system indicate the concentration of carbon. For additional precision, letters may be added between the second and third digits to indicate the presence of another element, like “L” standing for lead and “B” standing for boron. “H” may be added to the end of the SAE number to indicate hardenability.
First digit SAE designations:
Although the SAE/AISI system is widely accepted as a method for identifying steel alloys, there are several other methods producers use to classify steel including:
The key to the quality and performance of a steel alloy is partially related to how it is made with each method capable of providing an alloy with certain characteristics and properties. Regardless of the many advances in manufacturing, the steps for the production of steel alloys have changed very little.
The wide use of alloy steels is due to their low cost, availability, ease of processing, and mechanical properties. They are more responsive to heat and mechanical treatments and take on increased hardness, strength, ductility, corrosion resistance, and the ability to be welded after forging.
The selection of a steel alloy is a complex and difficult process that requires careful consideration and is an important part of the mechanical properties of a product.
The process of choosing a steel supplier can be tricky, time consuming, and difficult considering the many suppliers that are available. Although the internet can be helpful in researching a supplier, there are other factors to consider to ensure a successful selection.
In the initial process of selecting a steel supplier, it is important to obtain a sample of the steel a company produces to ensure it has the necessary quality for forging and a product. In the majority of cases, suppliers will have ISO certification to verify the quality of their product. Researching the background of a company and its rating is essential since some companies have inappropriate business practices.
Pricing is a key issue since it influences the cost of the final product. The majority of manufacturers have clear guidelines for their pricing and assist in providing a cost analysis that assists in determining the type of steel and how it aligns with the product to be produced. In very rare and unusual circumstances, a company may attempt to gouge a customer by fluctuating its costs and prices.
The central concept of modern business is customer service, which influences the relationship with the customer and the quality of their product. In many cases, customers will pay a higher price for steel when the provided customer service is exceptional. The foundation of manufacturing is customer service being available to assist a customer in all conditions and at all times. It is an aspect of business that differentiates a single sale from forming a lasting partnership and relationship.
In the steel supplier market, there is a tight circle of highly qualified suppliers that have a reputation for providing high quality products at a reasonable price. In many cases, the internet can provide superficial information regarding a company as well as its website. The best way of knowing the reliability of a supplier is contacting a company’s past customers. Although there may be negative comments regarding a supplier, it is best to look into how they responded to them.
In the initial negotiations with a supplier, it is necessary to stipulate how and when the steel will be delivered. The key is delivery and in what condition the steel is delivered. This aspect of the process can be the turning point in the selection of a supplier depending on the needs of an application. Also, the type of steel and steel alloy plays a major role in the determination of turnaround times since some alloys take longer to process.
Steel production is rapidly rising with millions of tons being produced every month. This rapid growth makes it more important to select a supplier that exactly meets your needs as a customer. Careful consideration and planning go a long way toward ensuring a successful and profitable collaboration.
Forging steel is a central part of the metal working industry and has been used for centuries to produce high tolerance quality products. The initial form of metal forging was a blacksmith with an anvil and a heated forge. Using a hammer, heated metal was placed on the anvil to be beaten and hammered into swords, cookware, battle shields, and other metal products. Over the centuries, forging steel has progressed through the addition of technological advancements and specialized equipment.
Open die forging involves deforming steel by placing it between dies that do not enclose the steel. The shape of the billet is changed by hammering or stamping it by a series of repetitions with each blow to the steel billet changing its shape. The workpiece is shaped between the top ram and a die that is placed on the bottom anvil. It is an imprecise forging method used for shaping simple forms. Once the process is completed, the forged piece requires a significant amount of machining.
Closed die forging, known as impression die forging, is used to produce small or medium components. It is a plastic deformation process that forces carbon steel between halves of a die. The process makes it possible to form intricate parts with complex geometries, the key to which is the shaping and forming of the die, a complicated machining process.
The bottom portion of the die for closed die forging is attached to an anvil. The hammer portion of the die drops repeatedly down on the die cavity to force the billet into the desired shape. Excess material, referred to as flash, from the multiple blows of the hammer, is squeezed out of the die and cools quickly, which prevents more flash from forming. Additionally, the flash acts as a barrier preventing other soft material from leaving the die causing the steel to fill the die.
Industrial closed die forging has the workpiece move through a series of dies with the first of the series used to distribute the metal and forming a rough shape of the workpiece. It is a fullering, edging, or bending impression. The die cavities after the first impression are referred to as blocking cavities, each of which resembles the configuration of the final product.
The forging load has to be precision set to ensure that the final product will have the correct form. If the load is too low, the carbon steel will not take the shape of the die. If the load is too high, the process will overstress the steel and lead to cracking and incorrect deformation.
Cold forging deforms steel below its recrystallization temperature or near room temperature. The low temperature of the steel makes the forging process more difficult and requires more energy and force. The steel billet, used in the process, is brittle and subject to cracking during forging. Cold forging pancakes the grains of the steel and elongates them making them stronger and more resilient.
The basis of cold forging is impacting the workpiece to plastically deform it, under compressive forces, where the workpiece is located between a die and a punch. It is a displacement process that takes the workpiece and forces it into a desired shape. Some of the techniques of cold forging are extrusion, coining, upsetting, and swaging, each of which can take place in the same stroke or separate strokes.
Roll forging or roll forming uses rollers to shape and form steel. Cylindrical or semi-cylindrical rollers with grooves for shaping are used to deform round or flat bar stock. As the bar stock passes between the rollers, its thickness is reduced as its length increases. Roll forming can be completed using cold or hot bar stock with hot bar stock being the preferred choice. For the heated process, the bar stock is heated sufficiently to make it malleable and ductile such that it can easily be formed. The grooves in the rollers have the precise shape geometry of the completed part and are what forges the workpiece to the correct dimensions.
A unique form of roll forging is ring forging, which involves ring rollers that decrease the dimensions of a ring of steel by squeezing it. The process is designed to remove the need for welding rings and forms perfectly shaped rings.
Drop forging uses impression dies and a heavy hammer to compress steel billets into designed shapes. A drop hammer that contains the upper die is a mechanical device that is powered by a pneumatic or hydraulic cylinder. The lower half of the die, as is found in open die forging, is attached to the anvil directly below the drop hammer. The steel billet is heated to a temperature that makes it malleable and placed in the lower die on the anvil.
The drop hammer, under great force, pounds the steel billet until it completely fills the lower die cavity. As the drop hammer strikes the die, flash is pushed outside the impression created by the die. A draft angle is added as part of the die to allow the release of the completed part.
Hot forging is one of the most common methods for forging steel and harkens back to the days of the blacksmith with his hammer and anvil. The use of hot forging reduces the amount of force that is necessary to shape and mold the workpiece. Heated steel has better flow, which makes it ideal for open and closed die forging. Additionally, the heating process anneals a workpiece and relieves its stress making it ready for further processing.
With hot forging, the workpiece is heated to a point above its recrystallization temperature. The process of recrystallization deforms grains of the crystal structure, which are replaced by stress free grains that grow until the original grains are gone. It is used in steel forging to eliminate the effects of strain hardening. The recrystallization temperature is one third to one half the melting point of the steel.
Hot forging makes it possible to precisely adjust the fine microstructure of the steel. The strength and durability of the metal can be clearly defined and is used in manufacturing processes with high loads, both static and dynamic, that place demands on products.
Heated die forging is a form of hot forging and is used to achieve closer tolerances to reduce machining and the cost of steel. The use of a heated die reduces the number of preforming and blocking processes, which further lowers the cost of processing and tooling. Ram speeds can be slower to reduce the necessary pressure to form the workpiece.
Using cold dies leads to uneven plastic flow of the heated steel, referred to as die chilling. To avoid die chilling, dies are heated using furnaces or other means to temperatures of 400o F to 500o F (205o C to 260°C), a process that depends on the type of equipment being used. The ideal method is to heat the die to the temperature of the workpiece, which is referred to as heated or hot die forging.
Die heating is an essential part of modern forging with electric infrared heating being the most efficient. It is more effective than gas or electric furnace die heating, direct flame heating, electric calrod radiant heating, and gas radiant heating. Infrared technology uniformly heats a die to prevent hot or cold spots. Since electric infrared heaters are mobile, they are able to heat the die in place to provide continuous heat.
The term steel is a general term used to describe a wide range of alloys produced by the combination of iron and carbon with other alloys. The history of steel began in the iron age when it was found that iron was stronger and harder than bronze. For thousands of years, the process of iron production was dependent on the raw ore used to produce iron and production methods.
Over the centuries, since the discovery of iron, processes were perfected in China, India, Sri Lanka, Turkey, and Europe. In 2000 BCE, forged iron had 0.8 % carbon added to form a hard brittle form of steel. Metallurgists in Egypt and China discovered that heating the brittle steel tempered it to make it less brittle. As with many modern processes, the dynamics of steel rapidly advanced during the first industrial revolution as hotter furnaces added carbon to make strong durable steel.
The main types of steel are low carbon steel, mild steel, carbon steel, and stainless steel. Mild steel comes in grades A36 and 1018 with 1018 being the purest form. Carbon steel has a carbon content of 0.4% up to 1.5% carbon. Stainless steel is distinguished by its 10.5% chromium and is available as martensitic and austenitic in hardened and non-hardened forms.
Alloy steel is used the most for the steel forging process. It is known for its strength, wear resistance, and toughness. Alloy steel is iron based steel that has been mixed with other elements to enhance and improve its physical properties. Common alloys are chromium, molybdenum, manganese, nickel, vanadium boron and silicon. The most common alloy steels used for forging steel are grades 4140, 4340, 6150, and 8620.
Alloy Steel 4140 is a chromium, molybdenum, and manganese steel with good strength, toughness, ductility, and resistance to fatigue, abrasion, and impact. It does not stress or creep at temperatures up to 1000°F (537.8°C). Alloy 4140 is available in leaded grades that have improved machinability but cannot be used for applications that include high temperatures, which lowers 4140’s ductility.
The process for making alloy steel 4140 includes placing the alloying elements in a furnace where they are melted and cooled. Once cooled, the completed steel is annealed several times. After being annealed, the steel is melted again to be poured into molds to be hot or cold worked.
Alloy 4340 is a nickel chromium molybdenum alloy that has exceptional toughness and strength as well as fatigue resistance. Heat treating of alloy 4340 increases its level of strength while maintaining its toughness, wear resistance, and level of fatigue strength. In addition, heat treatment gives the alloy atmospheric corrosion resistance.
High strength levels up to 150 KSI 0.2% PS can be achieved for alloy 4340 using proper heat treatment. Alloy 4340 is used in place of 4140 due to its higher strength and better hardenability as well as its exceptional impact resistance. A key aspect of the production of alloy 4340 is its heat treatment, which has to be carefully monitored to achieve the correct hardenability.
Alloy 6150 is a low alloy steel that contains carbon, small amounts of vanadium, and chromium and has excellent shock resistance and toughness when properly heat treated. The small quantity of vanadium in alloy 6150 differentiates it from alloy 5150 and gives it greater hardness. The characteristics of alloy 6150 include oil hardening, resistance to vibratory stress, medium hardness, and torque strength. It has low distortion properties and easily accepts heat treatment.
The main use of alloy 6150 is in the production of medium to large components that require high tensile strength and toughness. It is widely used for automobile parts such as crankshafts, steering knuckles, connecting rods, spindles, gears, and gear shafts. Alloy 6150 is forged at 1600°F up to 2150°F (870°C up to1175°C). For the best results, it is slow cooled and annealed to give it machinability.
Alloy 8620 is a nickel, chromium, and molybdenum steel alloy that has exceptional strength, which makes it wear resistant. The nickel content of alloy 8620 gives it good core toughness. It is forged at 1700°F(925°C) up to 2250°F (1230°C) and is air cooled after forging. Once cooled, alloy 8620 can easily be machined or heat treated. During hardening treatments, it is relatively flexible, which makes it possible to improve its core properties.
Since alloy 8620 has a low carbon content, it cannot be hardened by flame or induction hardening but is hardened through the use of nitriding. It is widely used in applications that require toughness and wear resistance. Typical uses for 8620 include gears, cranks, shafting, axles, bushings, pins, bolts, springs, hand tools, gears, and other machinery parts.
The short list of four steels above is only a sampling of the many steels that are formed by the steel forging process. When choosing a steel for forging, the first thing to be considered is the temperature at which the steel can be forged. Most types of steel can be forged at temperatures between 700°C up to 1300°C (1290°F up to 2300°F). The ductility of steel is determined by its carbon content and its alloying metals. Steels with a high carbon content tend to be less ductile and require extreme heat to change their grain structure.
Steel Alloys for Forging Steel | |
---|---|
AISI | Description |
4130 | Forged in a temperature range of between 1750°F (954°C) and 2200°F (1204°C), Alloy Steel 4130 contains chromium and molybdenum (as strengthening agents) and can be hardened by heat treatment. |
4140 | Forged at a temperature range of between 1700°F (926°C) and 1900°F (1038°C), this alloy steel has a high fatigue strength, toughness, torsional strength and a resistance to abrasion and impact. |
4330 | Forgeable in the temperature range between 1800°F (982°C) and 2200°F (1204°C), Alloy Steel 4330 is heat treatable, in which it has a good strength, toughness and a good fatigue strength. |
4340 | Forging is typically done between a temperature range of 1800 °F (982 °C) and 2250 °F (1232 °C). Alloy Steel 4340 is a heat treatable low alloy steel and is know for its toughness as well as for its ability to develop a high strength in heat treated conditions while still retaining a good fatigue strength. |
8620 | A common carburizing alloy steel and its is flexible during heat treatment. |
8630 | A lot more responsive to mechanical and heat treatments when compared to carbon steels, this alloy steel is alloyed with a number of elements including manganese, chromium, nickel, carbon, silicon and molybdenum. |
9310 | Forged at a temperature range of between 1700 °F (927 °C) and 2175 °F (1191 °C), this alloy steel contains molybdenum, nickel and chromium. |
Nitralloy 135 | Forged in a temperature range of between 2000 °F and and 2025 °F, this alloy steel has a moderate hardenability and is used in applications such as gears, bolts and crankshafts. |
Carbon Steel for Forging Steel | |
---|---|
AISI | Description |
1010 | A carbon steel with a 0.10% carbon content, alloy 1010 has low strength, which can be improved by quenching and tempering. Forging can be completed at 1800°F (982°C) up to 2300°F (1260°C). |
1018 | A low carbon steel, alloy 1018 has good ductility, toughness, and strength. Its temperature for forging is 2102°F up to 2336°F (1150°C up to 1280°C). |
1020 | With a combination of ductility and strength, alloy 1020 can be hardened and carburized. It can be forged at between 1800°F (982°C) up to 2300°F (1260°C). |
1026 | Alloy 1026 contains high iron content at 98.73% up to 99.18% with carbon content of 0.22% up to 0.28% and manganese at 0.6% up to 0.9% |
The steel forging industry has a set of unique terms that describe processes and the quality of forged pieces. The number of terms used in steel forging are endless and cover every aspect of the process. Here is a sampling of some of the terms that are representative of steel forging.
Backward Extrusion - Forcing a workpiece to flow in the opposite direction to the motion of a punch or die.
Blast Cleaning - Blast cleaning is a process that uses grit, sand, or shot for finishing and cleaning processed parts.
Board Hammer - Board hammering is a process for hardening the surface of a workpiece while leaving the core soft. The types of methods include carburizing, carbonitriding, cyaniding, and flame hardening.
Cold Shut - Cold shut is a surface defect where the metal being forged folds over on itself and occurs at the intersection of vertical and horizontal surfaces.
Compressive Strength - The maximum amount of pressure a metal can withstand without fracturing or becoming permanently deformed.
Descaling - The process of removing scales from a workpiece using wire brushes, water spray, and light blows.
Draft - Excess material on the side of a workpiece that is used to remove it from a die.
Drawing - Drawing is a forging process where metal stock has its cross section reduced and lengthened using flat dies.
Dye Penetrant Testing - Dye penetrant testing is an inspection and flaw detecting method that uses a liquid dye to identify flaws.
Elastic LImit - The stress a metal can withstand before being permanently deformed.
Electroslag Remelting (ESR) - It is a pre-forging process where steel is remelted through a layer of slag to give it better uniformity and improve its properties.
Finish Allowance - The finish allowance is the amount of stock that remains on the surface of a workpiece that is removed during finishing.
Heading - Heading is a forging process that creates heads on rods and wire ends.
Inclusions - Inclusions are nonmetallic particles that are present in ingots. Their shape and distribution can contribute to a metal’s directionality.
Lap - A lap is a metal defect that appears as a seam on the surface of a workpiece. It is caused by folding over or sharp corners.
Magnetic Particle Inspection (MPI) - MPI is a testing method that detects surface and subsurface breaks in magnetic metals, such as nickel, iron, and alloys.
Normalizing - Normalizing is a heat treatment that is used during forging where the workpiece is heated above its transformation temperature and then cooled.
Reduction in Area - The reduction in area is a measurement from a tensile ductility test, which is the difference between a workpiece’s original cross sectional area compared to its smallest cross section after testing.
Segregation - Segregation is a nonuniform distribution of alloying elements, which occurs during solidification.
Shrinkage - Shrinkage is the thermal contraction of metal after hot forging during the cooling period.
Superalloys - Alloys with an iron base, nickel base, or cobalt base are referred to as superalloys. They have high temperature mechanical properties and oxidation resistance.
Ultrasonic Testing - Ultrasonic waves are used to detect structural flaws.
Every steel forging company ensures that their processes and procedures are the most efficient and effective on the market. The many promises and sales pitches can make it difficult to find a forging company that meets the needs of a customer’s project. Experts in steel forging have a few tips to offer when making the choice of a steel forging provider.
In all industrial processes, cost is the first consideration. In the area of steel forging, the least expensive may not be the best choice. A broader view of a producer should include other factors beyond the cost.
This is one of the factors that is constantly emphasized during a sales pitch. In order to get a better view of real turnaround times, it is important to request information on recent orders regarding when they were placed and when they were completed or delivered. Included in turnaround times is how the final product will be delivered. Some companies have excellent turnaround times but seem to lack a system for delivery.
An aspect of turnaround times is the timeline for the forging of a steel part. Included in the timeline is the amount of time it will take to create tooling for the forging process. With unique or unusual parts, a considerable amount of time is necessary to create the dies, which adds to the amount of time to forge a part.
The complexity and size of a forging determines the forging process, die design, the forging company, and the cost of the forging. As parts become more complex, they require extra finishing and machining, which adds to the timeline and lengthens turnaround time.
Steel forging companies that have worked for several years and have developed a reputation have a better understanding of how to approach forgings with unique features and unusual requirements. During the development of a project, an experienced forging company can provide reliable data regarding turnaround times, tooling, and methods of delivery.
Highly qualified steel forging companies have been vetted, certified, and legally approved. The majority of reputable companies are International Organization for Standardization (ISO) certified, which requires that every company follow a specified set of guidelines in customer service and processing in order to receive a certification.
In modern industrial businesses, the factor that differentiates winning companies from run of the mill companies is customer service. This aspect of manufacturing processes has become the central factor in attracting customers and success. Pricing may be a factor in attracting customers, but customer service leads to lasting relationships and continued sales. The type of service, response to problems, and the ability to adapt to change are factors that build a reputation and ensure success.
As with any industry, steel forging has technological advances that have improved the processes of steel forging. In many respects, the dark and dusting steel forging operations of the past have been replaced with innovative processes and methods that are more efficient and produce high quality products. It is this aspect of the selection process that has to be carefully examined and is normally part of a factory tour or presentation.
Steel forging is a foundational process that is used to produce a wide range of highly durable products for large and small industries. Although the history of forging traces back thousands of years, it is still a primary source of high quality components and parts. No other metalworking process can compare with the desirable physical characteristics produced by forging at an exceptionally attractive cost.
The goal of forging steel is to change the grain structure of steel using percussive or compressive forces to produce components that are stronger, tougher, and more reliable. By compressing heated or cold steel, the steel undergoes metallurgical recrystallization that realigns the grain structure to produce exceptionally resilient and reliable parts.
Large capacity compressors are the core of ethylene plants. Forged parts are required to be resistant to the effects of hydrogen sulfide compounds and have the strength to withstand the effects of high pressure environments. Forged steel parts for high capacity compressors are used in petroleum and chemical plants.
A practice that has survived over the centuries is the shaping and forming of steel hand tools using forging. Pliers, hammers, sledges, wrenches, garden tools, sockets, hooks, turnbuckles and eye bolts are all produced using steel forging. Surgical and dental instruments and hardware for electrical applications such as pedestal caps, suspension clamps, sockets and brackets are forged for their strength, dependability and resistance to corrosion.
Much of the structure and framework of modern automobiles and trucks are dependent on the strength of components manufactured using steel forging. The dependency of the industry on forged parts is due to their strength, reliability and low cost. Forged components are used at points of shock and stress such as wheel spindles, kingpins, axle beams and shafts, torsion bars, ball studs, idler arms, pitman arms and steering arms.
Another essential application where forging steel is a necessity is in the powertrain, where connecting rods, transmission shafts and gears, differential gears, drive shafts, clutch hubs and universal joints are forged. Each of these components are produced using alloy or carbon steel due to its cost and reliability.
One of the greatest breakthroughs in the history of the world was the shaping of iron into plow shares. For many centuries, farmers had struggled with wooden plow shares that were not strong or durable enough to withstand constant use. With the introduction of iron plow shares, fashioned by blacksmiths, farmers could work for years without the fear of having to replace their equipment.
Forging steel provides the strength, toughness and cost effectiveness that is important to farmers. Engine and transmission components for heavy duty farm equipment are made of forgings that are subjected to impact and fatigue, such as gears, shafts, levers, spindles, and tie rod ends. Of all the industries listed here, forging has had the greatest impact on farming and the production of food.
The strength of forged steel is one of the reasons that it is used for the production of valves and fittings that have to endure the effects of high pressure applications. The superior mechanical properties and lack of porosity of forged steel makes it the ideal choice for critical components for the oil and gas industry. Key additional factors are the corrosion and heat resistance of steel when used for flanges, valve bodies and stems, tees, elbow reducers, saddles and other fittings. Oil field applications include the use of rock cutter bits and drilling hardware, which are all made of forged steel.
An interesting fact that is not generally known is that the original railroad tracks were made of wood, which could not endure the stress applied by steam engines. In an attempt to overcome the difficulty, the wood tracks were overlaid with iron to enhance their endurance. As would be expected, that concept also failed. With the advent of steel forging during the first industrial revolution, railroad tracks became the shape that they are today, made of highly durable alloy and carbon steel.
In the railroad industry, the use of forging steel has expanded into a wide range of components including anchor shackles, ball bearings, ball joints, beam clamps, bearings, blocks, bolts, clips, chain links, chain pullers, chain shackles, chain slings, chokers, clamps, claws, engine components and parts, and fasteners. The list continues into hundreds of parts, pieces, components, and features that keep the world’s railroads running.
A wide range of metals are used in the construction of ships. Out of all of the metals to choose, steel remains the most widely accepted. As with other industries, the strength of steel and its reliability make it the best choice for producing high quality components that are resistant to fatigue and capable of lasting the lifetime of a ship. Forging steel, with advanced technology, is the most dependable method for producing the various parts of ships.
Forged steel is an essential part of the construction of spacecraft and airplanes, which depend on steel's durability and strength. Unlike other industries that have little concern for the weight of steel forgings, a necessity for aerospace manufacturing is weight. Although steel is a heavy metal, it can be forged and compressed to meet the applications for aircraft construction. Cross rolled sheets and plates, turbine rings, bearing rings, fuselage structure, and rotor blades for helicopters are all produced using steel forging.
Steel forgings require the highest engineering skills and production control. It has been found that forging steel is superior to steel casting or bar stock machining because the natural grain flow of forged steel is made to conform to the shape of the products, making them superior in tensile and shear loads.
Aluminum forging is a method for processing aluminum alloys using pressure and heat to form high strength, durable products. The process of aluminum forging involves pressing, pounding, and...
Cold forging is a metal shaping & manufacturing process in which bar stock is inserted into a die and squeezed into a second closed die. The process, completed is at room temperature or below the...
Copper and brass forging is the deformation of copper and brass for the purpose of manufacturing complex and intricate shapes. The temperature at which copper and brass are forged is precision controlled and...
Forging is a metal working process that manipulates, shapes, deforms, and compresses metal to achieve a desired form, configuration, or appearance outlined by a metal processing design or diagram...
In this article, there are key terms that are typically used with open and closed die forging and it is necessary to understand their meaning. Forging is a process in manufacturing that involves pressing, hammering, or...
Rolled ring forging is a metal working process that involves punching a hole in a thick, solid, round metal piece to create a donut shape and then squeezing and pressuring the donut shape into a thin ring...
The ancient art of forging falls into two distinct categories – hot and cold where hot forging has been around for centuries while cold did not begin until the industrial revolution of the 19th Century. Though they are quite different ...
Aluminum casting is a method for producing high tolerance and high quality parts by inserting molten aluminum into a precisely designed and precision engineered die, mold, or form. It is an efficient process for the production of complex, intricate, detailed parts that exactly match the specifications of the original design...
Die casting is a high pressure metal casting process that forces molten metal into a mold. It produces dimensionally accurate precision metal parts that have a flawless smooth finish...
Sand casting is a manufacturing process in which liquid metal is poured into a sand mold, which contains a hollow cavity of the desired shape and then allowed to solidify. Casting is a manufacturing process in which...
Zinc die casting is a casting process where molten zinc is injected into a die cavity made of steel that has the shape, size, and dimensions of the part or component being produced. The finished cast zinc product has...
The casting process is an ancient art that goes back several thousand years to the beginning of written history. The archeological record has finds that document the use of the casting process over 6000 years ago around 3000 BC or BCE...