Aluminum Forging
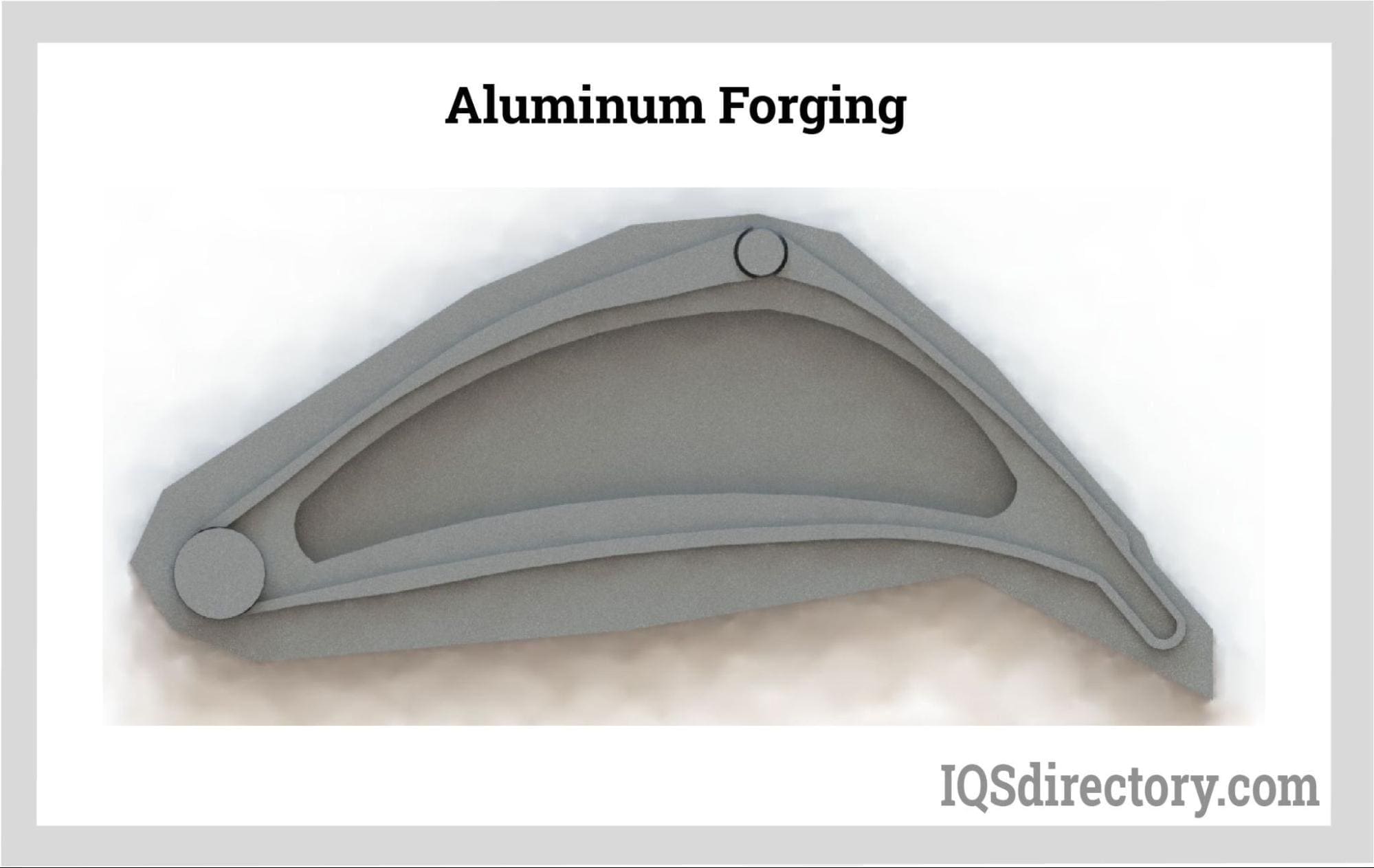
Aluminum forging is a method for processing aluminum alloys using pressure and heat to form high strength, durable products. The process of aluminum forging involves pressing, pounding, and...
Please fill out the following form to submit a Request for Quote to any of the following companies listed on
This article will take an in-depth look at open vs closed die forging.
The article will bring more detail on topics such as:
This chapter will discuss open and closed die forging, which are methods used for manufacturing products.
In this article, there are key terms that are typically used with open and closed die forging and it is necessary to understand their meaning.
Forging is a process in manufacturing that involves pressing, hammering, or rolling metal objects into various shapes or patterns.
Forged parts come in various shapes and sizes and these products include disks and blanks, hollows, forged rings, semi-closed dies, roller rings, bars, hubs, complex shapes, shafts, rotor shafts, eccentric shafts. The diagram below illustrates the steps of the process of forging. The processes will be discussed in greater detail in the other chapters.
The first step involves setting up the workpiece to the correct position on the lower die. The workpiece must be correctly inserted as it might be difficult to reverse the forging process once it is complete.
In this step, the upper die is dropped down onto the workpiece so that the desired shape or pattern can be made. This is possible because the workpiece will be in a very hot state, flexible enough to form the shape of the die. Heating the workpiece enables the workpiece to exhibit its elastic characteristic thereby requiring a lesser force to deform. A calculation and experiment are applied either by mechanical or electrical powering of the force.
Depending on the material type of the workpiece, the workpiece is allowed to cool down before releasing the upper die. The image below shows a forged part that can be used for various purposes.
The ram is part of the forging equipment that holds the upper die and allows it to move up and down, making strokes and forces that are needed for deforming the workpiece. The ram is mainly used to change the power source to a mechanical force.
A die is a special tool mainly used to cut materials into different shapes or profiles. They are used in most manufacturing industries with pressing and other machines. The workpiece is processed into final products when it is between the two dies (The lower and upper die or the top and bottom die). The diagram below shows the interaction of the dies and the workpiece before and after a force is applied.
Ingot refers to a metal block made from metals like gold, silver, steel, etc, and is usually in a shape such as a rectangular prism, cube, etc.
Grain flow is a commonly used term in open and closed die forging and it refers to the direction of flow in which metal grains will orient themselves and is caused by deformations during the forging process.
Flashing refers to the unwanted material that was not used to create a part during the forging process. This material usually overlaps and exceeds the required dimensions and is usually removed by machining after completing the forging process. The diagram below shows the flash formed when a force F is applied to the metal billet.
A hammer is an instrument that uses mechanical or electrical power to provide the force needed for shaping the heated or molten metal during the forging process. It provides strokes that shape the product and in most cases, it gets in touch with the workpiece for a very short time (Milliseconds) during the making process.
A press is a device used to apply pressure onto something to shape, flatten, or extract some oil, juice, or liquid from it.
An anvil is a heavy iron block with a flat top used for hammering, flattening, or other metal operations and can be used for forging as well.
A forging punch is a piece of metal that is used to create a hole or widen the existing hole during the forging process. Punchers come in different shapes, sizes, and material types depending on the application.
This chapter will discuss what is open die forging and what is closed die forging. It will also draw a comparison between the two as well as highlighting aspects to consider when choosing a forging process.
Open die forging is also referred to as flat die forging, blacksmith forging, Smith forging, and hand forging. In this forging, a hot forming process is involved where the metal or metal alloy is shaped by pressing or hammering between simple or flat contoured dies. It is the operator’s skill and the equipment type that determines the outcome or forms obtained hence the name blacksmith.
Nowadays, because of the availability of technology and advancement in technology, most open die forging equipment is now computer-controlled enabling the design and creation of complex forging and there is better dimensional control. In most cases, open die forgings are simple shapes like disks, shafts, rings, etc. The open die forging operations are mainly used when the parts involved are few or when the part is too big to be forged in closed dies. The process of open die forging is considered ideal and most appropriate to produce mechanical properties that can not be produced using closed die forging operations.
The open die process is classified as a heat forming process that uses convex and concave dies in its presses. They are also known as standard dies in presses. In this process, a variety of component sizes ranging from a few kilograms to over 300 tons can be produced. The process involves the creation of heat that will be applied to ensure that the material obtains enough plastic flow characteristics. This operation of heat will also help reduce the force required to make various shapes.
While the lower die supports the material, a series of strokes are applied to it from the upper die. A manipulator is used to change the positions of the material during phases of the strokes. This process allows the workpiece the freedom to change direction during the process. A force is applied in the direction of the upper die, and this direction is also known as the axial direction. For effective operation of this process, the axial direction can be changed or the workpiece itself can be rotated. Below are some of the most used operations in open die forging.
The upsetting operation involves working with the stock by referring to its axis in the vertical position. This position is held under the hammer of the forging press for effecting results. The operation works by increasing the cross-section of the stock while decreasing the axial length. Flat dies are the most used in upsetting because of their large cross-sectional area of the workpiece.
The cogging operation is known for effectively working with narrow dies. These narrow dies could be flat, V, convex, or concave. The repeated strokes elongate and reduce the ingot as it is sometimes rotated. The cogging operation changes the grain structure of the metal, consolidating the ingot defects like holes and porosity.
Drawing is used to make a shape having a length that is considered much greater than its cross-section. This is done by elongating the bloom or ingot or by reducing the section.
In these three operations, a cavity is formed by punching a force into heated steel. Although there is a displacement created without the removal of metal a blind cavity is created (piecing). In these cases, a solid punch is used to create a through-hole by extracting or removing in the form of slugs. (Punching). Trapping also creates a hole, usually done by hollow punching to remove the core of the central metal.
Hollow forging uses the method of lengthening and expanding the mandrel to produce hollow forms. The thickness of the walls is reduced and the operation of drawing increases lengths.
Closing in operations is used in hollow forging to reduce the section on portions. To reduce the area the piece is heated to forging temperatures. V tapered, formed, and curved dies are used to reduce the areas.
Ring forging operations produce rings from over a mandrel from pieced blanks. The ring wall is uniformly reduced by the rotation of the ring on the press strokes. This will also increase both the outside and inside diameters of the ring.
There are complex shapes that are best produced when these operations are combined. Such shapes range from simple to complex and they have a wide range of sizes.
Closed die forging is sometimes referred to as impression die forging. It is the process that occurs when two or more dies are used together to create complex-shaped parts through hammering or pressing of metal blanks using closed dies.
In closed die forging the hammer is dropped on the workpiece, causing the flow of the metal in the die cavities. This action is responsible for creating the outward appearance or shape of the product. The operation depends on the hammer part and in some cases, it may be dropped several times. This dropping of the hammer can also be done in a series of quick successions and the hammer makes contact with the workpiece for a short time which in most cases is in milliseconds.
As the hammer drops, there is a material that gets squeezed out the die cavities and is referred to as flashing. The flashing has a higher cooling rate as compared to the rest of the material. The flash is removed after the forging process and is usually stronger than the rest of the material. This post-removal of flashing is usually done by machining and finishing operations.
The main differences between open and closed die forging are tabled below:
Open Die Forging | Closed Die Forging |
---|---|
The method works by compressing the workpiece between the two flat dies | The method works by compressing the workpiece between the two impressed dies |
The cost of the die is low | The cost of the die is high |
The process is simple | The process is complex |
The is poor utilization of the material during the process | The is effective and conservative utilization of the material during the process |
Machining of the components is required after the process | No machining of the components is required after the process |
The products often come out with poor dimensions and irregularities | The products often come out with precise dimensions and low tolerances |
The process is mainly used for producing a few products | The process can be used for mass productions |
The process is appropriate when manufacturing simple products with less complexity | The process can be used for complex product |
The considerations when choosing between open and closed forging processes include:
One of the ways to choose the best forging process is to look at the precision of the products. This can be done by eye inspection and measuring and comparing the dimensions of the products and the actual metal piece one wants to copy. This can be measured using precision instruments like electronic calipers. The greater the tolerance value the poorer the forging process and vice versa is also true. Forging processes that use heat normally give better products compared to those that do not use heat. This is because heat allows the smooth operation of the molding process to happen. In the case of open and closed die forging both used heat for their processes however, other factors distinguish their products such as the material or metal used.
Metals have different mechanical and chemical properties that make them behave differently. The melting point for example is one property that distinguishes many metals from each other. Metals behave differently when exposed to heat. Some metals can be forged under high temperatures while others can be forged under low temperatures. Enough research needs to be done before using the material for forging.
The heating process involves some emissions into the atmosphere. Some metals release carbon into the atmosphere when heated which is a concern to environmentalists. If a material emits toxic gasses to the environment, it means there is a likelihood of increased expenses in trying to prevent it from polluting the environment and above all affecting the health of the one working with the metal.
The finalizing element in all this is the total cost because at the end of the day most of these forging processes are used for commercial gains. A lot of questions need to be asked and they also need to be answered. The pricing of things should be the last thing to be evaluated.
There are numerous machines available that perform both open and closed die forging, and they are important in today's society because they enable the production of a wide range of complex-shaped metal components used in various industries, offering versatility, efficiency, and precision in the forging process. Below, we examine some notable brands of machines used for both open and closed die forging.
The Ajax-CECO Bulldog 600 is a versatile forging machine capable of both open and closed die forging, featuring a robust construction, high forging capacity, and flexible control systems to produce a wide range of forged components.
SMS Group offers FRÖHLING Hydraulic Forging Presses, known for their ability to perform both open and closed die forging, with advanced hydraulic systems, customizable features, and precise control over the forging process.
Erie Press Systems' MultiForge™ machines are designed to perform both open and closed die forging, offering flexibility, high force output, and programmable settings to meet the requirements of various forging applications.
National Machinery's FORMAX Plus machines are capable of both open and closed die forging, featuring advanced servo-driven technology, quick tool change capabilities, and energy-efficient operation for enhanced productivity and precision.
LASCO manufactures FK Closed Die Forging Presses that excel in both open and closed die forging applications, with customizable features, precision controls, and high forging force, ensuring efficient production of forged components.
Please note that specific models, features, or components may have evolved since this latest update. It is advisable to consult the respective manufacturers or industry resources for the most up-to-date information on the latest models and capabilities of machines used for both open and closed die forging in the United States and Canada.
This chapter will discuss the applications and advantages of open and closed die forging.
There are many applications of open die forging but generally, the application of this forging type is classified according to the shapes of the products which are listed below.
Cylindrical shape products are commonly used in industries that prioritize extremely durable and strong products. An example is the aerospace industry, where products like rotors or propellers parts, flat bars, and landing gears are manufactured using open die forging. The military and automotive industries use parts forged and shaped for most of their equipment. Most products from open die forging are reliable, strong, and economical, making them an obvious choice for truck applications and automotive parts. Other examples include wheel spindles, axle beams, kingpins, shafts, torsion bars, idler arms, ball studs, steering arms, pitman arms, connecting rods, and transmission gears and shafts.
These forgings have a shape similar to a pancake and they appear like disks. They are used in aerospace, industrial, and military industries because they are reliable and bring safety to helicopters, commercial jets, piston-engine planes, spacecraft, and military aircraft. Examples of components include hubs, flats, discs, hexes, plates, and rounds. Upset forging can be used to create elongated parts such as screws, shafts, piston rods, and other parts used in public works, aerospace, and the automotive industry.
Hollow forgings are used to produce big parts like hollow tubes. They can be tapered hollow shapes, hollow cylinders, or straight cylinders. Hollow forgings can be used to produce rings, tubes, shafts, seamless rolled rings, or bearings. These are mainly used in the aerospace, military, automotive, and alternative energy industry.
Contour type forgings are greatly used for ring rolling applications to provide contours where they are needed. Rolled rings are strong and cost-effective. They have many applications from windmills, jet turbines, paper mills, jet engines, helicopter gearboxes, and other equipment exposed to stressful environments.
The advantages of open die forging include:
In open die forging there is enough space to work on the workpiece and the chances of void are closer to none.
Fatigue refers to the weakening of a material caused by repeated loading or stress being applied to it. This usually results in unfavorable conditions like bending and cracking. Open die forging products have better strength and can easily overcome fatigue.
The shapes created using open die forging methods have better microstructures mainly because they are bigger and last long.
Grain flow is an orientation of the direction of metal grains together with any inclusions such as deformation created by forging. It’s a method that is common in the forging of the crankshaft. The crankshaft is referred to as continuous grain flow forging because of the nature of the deformation steps.
Cost-saving refers to the savings that directly impact the company’s bottom line such as profits and losses. This can simply be referred to as the reduction in expenses. When comparing open die forging to closed die forging, this method had reduced expenses.
In this method of forging the operations involve simple operations like hammering and pressing which do not involve cutting and removing the materials meaning that most of the materials bought will be used for forging without any waste. In closed die forging some of the material is not used to create the product. Instead, it is removed as flashing.
Most shapes created have stronger bonds because of the method of manufacturing that they use, ie, they are compressed through pressing and hammering. These can withstand unfavorable conditions like high temperatures and other stresses involved making them stay for a longer time.
Some of the disadvantages of open die forging include:
In this method, a lot of space is left out, which gives the molten metal or heated metal enough room to spread unevenly towards the cavities of the dies. Because the molten or elastic metal has no confinement this may lead to irregular shapes, making it unsuitable for precision manufacturing/parts.
Since open die forging often produces irregular shapes, in most cases there post-machining is required to finish the product into the desired part. In a way, the method is expensive as it does not consume all of the material in most cases.
Open die forging has dies that do not close up during the process and this gives room for producing products that are irregular in shape. This makes it fit for the production of parts that do not necessarily have to be precise like supporting beams etc.
Because of the irregularities involved in open die forging, it is risky to do mass production as the level of irregularity may increase, leading to losses. It is effective for small quantities.
Closed die forging provides most metal components, particularly for industrial applications such as aerospace, electronics, agriculture, automotive, commercial, manufacturing, construction, hardware, semiconductor, and food processing industries.
Closed die forging components are common in the automotive and trucks industry. Examples of such components include steering arms, pitman arms, shafts, axle beams, torsion bars, idler arms, and ball studs. The examples are considered flame resistant and less resistant to corrosion.
Most closed die forging components are strong, tough, and economic which is essential in agriculture machinery and equipment. Most of the machinery used in agriculture is exposed to harsh and rigorous conditions such as rocky lands, which requires them to be strong enough.
The components are mainly used as engine and transmission components. Examples of such components include gears, shafts, spindles, tie rod ends, levers, cultivator shafts, and harrow teeth.
Most surgical and dental instruments are made through closed die forging. Common examples include pliers, sleds, hammers, garden tools, wrenches, sockets, wire rope clips, hooks, sockets, turnbuckles, and eye bolts. For electrical transmission and distribution lines, examples include suspension clamps, caps, brackets, and sockets are mainly forged to enhance strength, resistance to corrosion, and dependability.
In the valve and fitting, industry closed die forging components are widely used because they are created under high pressure and extreme force. This gives the components extra strength and toughness required in most valves. Commonly used components include heat and corrosion-resistant parts such as flanges, stems, elbow reducers, tees, valve bodies, saddlers, and other fittings.
Some of the advantages of closed die forging include:
Products made from closed die forging have excellent mechanical properties mainly because of the process they undergo. The pressing and hammering of an internal grain structure which has ideal properties like high strength and resistance to corrosion etc. The products from this forging type exhibit properties that make them for applications like precision instruments because of their toughness and strength.
The die forging operations produce shapes that have close tolerances and give a near-net shape. Near net shape refers to a shape that gives dimensional values close to the theoretical dimensions when measured. This is mainly because the workpiece is enclosed inside dies without room for flashing and there is no further machining required. Other small products can achieve tolerances of the order of +/- 0.3 mm, which will require no further machining or finishing thereby saving costs.
The forging creates near net shapes or net shapes. This means that the forging is close to the perfection or actual measurements that no extra work is required to be done after the process. Inside the dies is a design of the shape that the workpiece is expected to have. This shape is reproduced efficiently in the closed die forging processes.
Closed die forging operations use a wide range of material types from steel, brass, aluminum, iron, and other metal alloys. This makes the forging type applicable to many industries since most parts are material specific. In some forging processing, some materials cannot be used for the forging processes due to reasons like deformation in competencies, melting points, rate of cooling, costs, and other mechanical properties that may hinder them from being used as workpieces. In closed die forging these materials can be used with some slight changes in the system’s operation.
In these forging processes, there are no flashing materials involved after the process is complete making it a greener process as compared to other processes like open die forging or casting where further machining is done after the forging. Besides being environmentally friendly, the closed die forging processes promote favorable material budgets and some manufacturers prefer using it because of that.
Due to the precision machining involved, closed die forging provides a good surface finish. This has the advantage of saving costs related to machining. This is promoted because of the confined area to which the workpiece is exposed to. There is no room for flash materials.
Closed die forging involves the use of complex tools that require complex design. The tools have high pricing which makes this method expensive.
It is not the method to use especially when intending to produce irregular shapes because it is limited to dimensional manufacturing. Products with irregular shapes and structures will best be forged by the open die method.
Closed die forging is not suitable when manufacturing large products. It's suitable for small products.
Most of the products which are made from closed die forging are small compared to open die forging. Because they are small there is a probability of accidents as the hot workpieces can be easily flicked away in the wrong direction. Working with closed die forging equipment requires more cautiousness.
Both the open and closed die forging method uses heat for most of their operations. There are significant differences between the two, but there seems to be a balance on which method is the best because of what the other method can do and the other cannot do. From the outlined facts, it is evident that these forging methods complement each other and are best used depending on the type of application.
Aluminum forging is a method for processing aluminum alloys using pressure and heat to form high strength, durable products. The process of aluminum forging involves pressing, pounding, and...
Cold forging is a metal shaping & manufacturing process in which bar stock is inserted into a die and squeezed into a second closed die. The process, completed is at room temperature or below the...
Copper and brass forging is the deformation of copper and brass for the purpose of manufacturing complex and intricate shapes. The temperature at which copper and brass are forged is precision controlled and...
Forging is a metal working process that manipulates, shapes, deforms, and compresses metal to achieve a desired form, configuration, or appearance outlined by a metal processing design or diagram...
Rolled ring forging is a metal working process that involves punching a hole in a thick, solid, round metal piece to create a donut shape and then squeezing and pressuring the donut shape into a thin ring...
Forging steel is a manufacturing process used to shape steel by using localized compressive forces, which include hammering, pressing, and rolling. It is a widely used method for producing high quality steel products...
The ancient art of forging falls into two distinct categories – hot and cold where hot forging has been around for centuries while cold did not begin until the industrial revolution of the 19th Century. Though they are quite different ...
Aluminum casting is a method for producing high tolerance and high quality parts by inserting molten aluminum into a precisely designed and precision engineered die, mold, or form. It is an efficient process for the production of complex, intricate, detailed parts that exactly match the specifications of the original design...
Die casting is a high pressure metal casting process that forces molten metal into a mold. It produces dimensionally accurate precision metal parts that have a flawless smooth finish...
Sand casting is a manufacturing process in which liquid metal is poured into a sand mold, which contains a hollow cavity of the desired shape and then allowed to solidify. Casting is a manufacturing process in which...
Zinc die casting is a casting process where molten zinc is injected into a die cavity made of steel that has the shape, size, and dimensions of the part or component being produced. The finished cast zinc product has...
The casting process is an ancient art that goes back several thousand years to the beginning of written history. The archeological record has finds that document the use of the casting process over 6000 years ago around 3000 BC or BCE...