Belt Conveyors
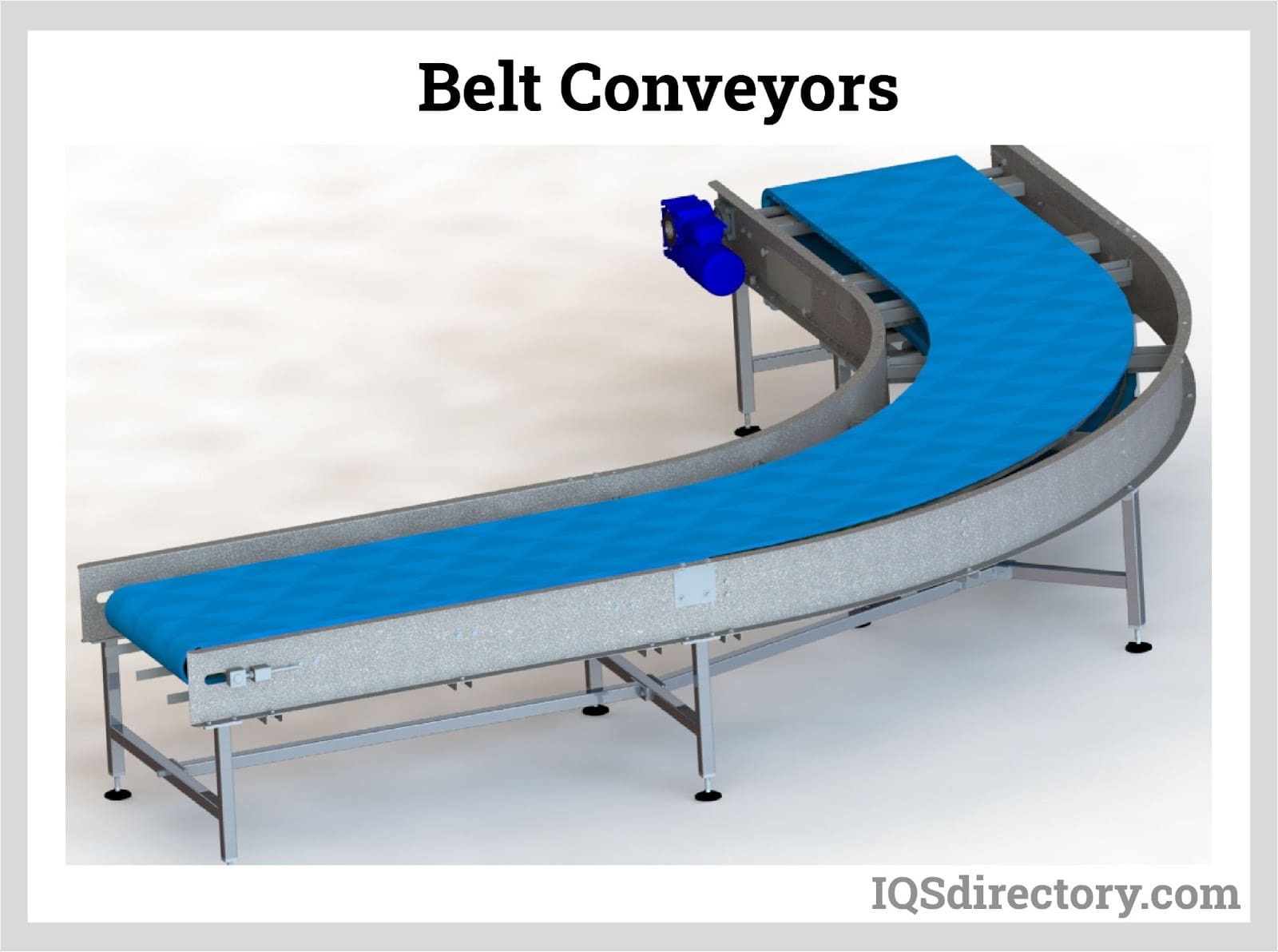
A belt conveyor is a system designed to transport or move physical items like materials, goods, even people from one point to another. Unlike other conveying means that employ chains, spirals, hydraulics, etc...
Please fill out the following form to submit a Request for Quote to any of the following companies listed on
The content of this article contains everything you need to know about overhead conveyors and their use.
You will learn:
An overhead conveyor is a material handling system designed to move parts, components, products, and supplies via a motorized chain mechanism suspended above the ground. This type of conveyor system optimizes space by using the vertical area and offers a highly efficient means of transporting loads of various shapes and sizes for tasks such as production, processing, storage, or placement. Overhead conveyors are less intrusive compared to other transport methods and are particularly useful for moving items through environments that are unsafe or restricted for human access, including ovens, paint booths, sintering processes, and chemical handling areas.
Overhead conveyors are classified based on their movement system, track design, and installation. Movement systems can be either manually operated by hand or motorized. The track types refer to the rails used to carry items like vessels and containers, which may range from basic I-beams to more advanced enclosed track designs.
The installation process for overhead conveyor systems requires precise planning and specialized expertise. While these systems can generally be installed in most locations, the unique characteristics of each site demand a custom approach. Factors like building structures, employee work areas, offices, and other facility features must be carefully considered before installation. This stage of the process is often the most complex, requiring significant time and preparation.
Overhead conveyors, like other industrial equipment, are available in various shapes and sizes to accommodate different manufacturing needs. They are utilized across diverse industries, from large-scale to smaller operations. The design of overhead conveyors also adapts to the types of items they transport, which can range from large automotive engines to small components undergoing processes such as heat treatment, painting, or coating.
When considering the various types of overhead conveyors, it is important to recognize that some are customized specifically for unique operations or manufacturing processes. This is particularly relevant for industries producing specialized or rare parts. Custom overhead conveyors are designed and engineered to meet specific needs, whereas generic models may need adjustments to accommodate unique conditions or requirements.
Despite advancements in technology, manually operated overhead conveyors still have their place, especially in specific applications where they are beneficial. While motorized conveyors offer greater efficiency, manual systems are useful for transferring workpieces between different stages of a process. These conveyors facilitate straightforward movement between processes, making them ideal for tasks where automated solutions may not be required.
Manual overhead conveyors can also be equipped with conveyor switches and turntables, allowing for changes in the direction of materials and enabling multiple conveyor tracks to operate simultaneously. These components facilitate the transfer of loads in various directions, optimizing space usage and enhancing both efficiency and productivity. Despite being powered by human effort, manual conveyors can support capacities comparable to motorized systems, handling loads of up to two tons (1814.37 kg).
Monorail overhead conveyors are designed for transporting goods over extended distances. These systems feature rails suspended from the ceiling, with power delivered through conductor lines housed within the rails. Monorail conveyors can adjust levels, allowing them to lower loads to work areas and move out of the way once loading or unloading is complete.
In monorail overhead conveyors, items are attached to fixtures that hang from the rail system. The beam and chain of these conveyors provide the necessary traction and load-bearing support to ensure smooth material handling. Depending on the application and load requirements, monorail conveyors can be either motorized or manually operated. Motorized versions often come equipped with start and stop controls, facilitating easy loading and unloading of items.
Basic monorail overhead conveyors are commonly used in dry cleaning and retail clothing stores to hang garments without causing wrinkles or damage. In manufacturing settings, these conveyors are employed for tasks such as batch painting, production line movement, and assembly processes. They can be loaded manually, with forklifts, cranes, lifting equipment, or robotics before transporting items for processing or assembly.
Monorail overhead conveyors are widely used because they offer various methods for material handling and help reduce production costs. Their design is versatile, especially for finishing applications, where some workpieces need to be exposed to multiple surfaces for thorough coverage. The flexibility of monorail conveyors allows for track configurations that enable workpieces to be returned for additional finishing as needed.
Power and free overhead conveyors consist of a motorized enclosed chain track positioned above a non-motorized track with trolleys. Simple mechanisms known as "pusher dogs" are inserted into the chain to engage with the trolleys, facilitating their movement between different locations. When the pusher dogs disengage, the trolleys stop. A single power and free overhead conveyor system can feature multiple conveyor lines, allowing for diversion and merging to sort and collect parts and materials efficiently.
In a power and free overhead conveyor system, the chain track continuously moves along the upper track, while the loads hang from the lower, free-moving track. This free track features a cast body, load-bearing wheels, and both front and rear flippers that interact with the pusher dogs to drive the track. Although the typical configuration has the load suspended below the track, there are also designs where the load is positioned above the track.
Power and free overhead conveyors, also referred to as accumulating overhead conveyors or birail conveyors, are designed to allow products to accumulate or gather between workstations. This capability provides enhanced flexibility for production processes, making them especially useful in operations like assembly lines.
An enclosed track overhead conveyor is designed to protect the chain drive and trolleys from contaminants by housing them in a sealed, box-like tube. Pendants hang through a slot at the bottom of the tube. The chain within this enclosed track moves in unison with the mechanism, maintaining both direction and spacing.
Enclosed track overhead conveyors are frequently used in painting processes where overspray could otherwise damage the conveyor system. They are also essential in applications involving lubricants or coatings to protect the track and trolleys. To ensure optimal performance, the conveyor system must remain free from debris, dust, dirt, and other contaminants that could disrupt its operation.
In various assembly and manufacturing environments, excessive noise can hinder efficiency and must be controlled. Enclosed overhead conveyor tracks are well-suited for these situations, as their covering helps to significantly reduce noise. Some designs even offer near-complete noise elimination.
A widely used type of overhead conveyor is the I-beam overhead conveyor. This system features an open track design with a chain-driven mechanism, where pendants are suspended from trolleys mounted on the I-beam. Like other overhead conveyor systems, I-beam conveyors support trolleys and their pendants, allowing materials to hang directly from them. The robust construction of I-beam overhead conveyors enables them to handle several hundred pounds of parts, equipment, trolleys, and components.
The I-beam overhead conveyor system offers significant flexibility, allowing the track to be bent horizontally and vertically. This adaptability makes it suitable for installation in various locations, even around obstacles. Unlike enclosed track systems, I-beam conveyors have exposed tracks, making inspection and lubrication straightforward. Some models feature torque arm drives with sensors to detect potential overloads. Additionally, take-up frames are included in many designs to prevent excessive stretching of the chain drive.
I-beam overhead conveyors are favored for their substantial load-bearing capacity, allowing them to support heavier loads on each pendant and trolley. The load capacities of the trolleys vary with the track size: 400 lbs (181.437 kg) for a 3 in (7.62 cm) track, 800 lbs (362.374 kg) for a 4 in (10.16 cm) track, and up to 2400 lbs (1088.62 kg) for a 6 in (15.24 cm) track.
Accumulating electric monorail conveyor systems feature individual powered carriers that operate independently along the track. Similar to other overhead conveyor systems, these electric monorail conveyors are mounted on ceiling-suspended tracks. However, unlike synchronized systems where all carriers move together, electric monorail conveyors are asynchronous, with each carrier functioning on its own power.
Accumulating electric monorail conveyor systems are used for various applications, such as transporting automobile bodies during assembly. These systems allow for the seamless movement of a vehicle from one workstation to another for adjustments and further processing. While similar to powered and free systems, electric monorail conveyors differ in that each carrier is powered by its own independent motor.
Known as an EMS system, motorized self-contained trolleys, or tractor drives, transport carriers along a rail system similar to other overhead conveyors. These tractors can operate individually or be combined in groups of two to four for handling heavier loads. A tractor load bar assembly links the tractor drive to its carrier. Power is supplied to the tractors through the track system, as is common with other monorail conveyors.
The seven types of overhead conveyors discussed represent just a portion of the various basic conveyor systems available. Given that most conveyor systems are tailored to specific requirements, it is impractical to cover every type and variation. Typically, manufacturers choose overhead conveyors for their efficiency, durability, and strength, utilizing them to optimize floor space, boost production, and enhance worker safety.
Overhead trolley conveyors are a cost effective and simple method for moving products, supplies, and other materials to various locations in a facility. As with all forms of conveyors, they take advantage of the overhead space and have straight runs, curves, and slopes.
The components of an overhead trolley conveyor include a single rail track, load bearing containers known as carriages, hangers with hooks, clamps, or stands, a tension method, trolleys on the track, and a drive system. Trolleys are secured to the drive method with hanging pendants that come in varying types to fit the loads and products being transported. Load bars, secured to two or more pendants, can be added to distribute the weight of heavy loads.
Overhead trolley conveyor systems are used in painting systems, cleaning parts, and coating, drying, and cooling processes. They are widely used in manufacturing for transporting parts, components, and assemblies between applications and processes. Overhead trolley conveyors can be used to deliver cases, cartons, and boxes.
Unlike other forms of overhead conveying systems, friction driven overhead trolley conveyors do not have a chain drive. Materials are moved along the system by rotating tubes that are powered by motors. Trolley wheels located at the top of the carrier sit at a canted angle, which allows the trolley carrier to move forward and backward. As the tube of a section of the conveyor turns, it drives the trolley wheels to move a load from one section of the system to the next. The movement of the tube and trolley wheels produces limited noise making transport quiet and efficient.
Each section of the chainless system has its own motor, which allows sections to speed up, slow down, or stop. When a part is present in a section, the motor shuts down to save energy. The system is floor mounted and bolted to the floor to provide a strong and sturdy mounting capable of moving a wide variety of loads.
Overhead conveyors are intricate systems used to transport materials, products, components, and parts in manufacturing and industrial settings. Each element of these systems is meticulously designed for optimal performance. Common components of an overhead conveyor system include a chain or cable drive, either enclosed or open track, a drive unit, a take-up unit, trolleys, carriers, and supports. These components are specifically engineered to cater to the unique requirements of different applications and operations.
Overhead conveyor chains come in various designs, each tailored to handle unit loads or bulk materials. Choosing the appropriate chain for an overhead conveyor depends on the specific application requirements, as well as the chain's durability and reliability. These chains feature a series of journal bearings, which include a shaft rotating within a support shell, and are interconnected by metal plates.
Overhead conveyor chains are available in various shapes, sizes, and designs, each tailored to address the specific requirements of a transport application. As a critical component of an overhead conveyor system, these chains are closely monitored for signs of wear and degradation. Key issues such as sprocket wear, chain slack, corrosion, and damage from heavy loads are carefully checked to ensure optimal performance.
The drive system in an overhead conveyor connects to the chain, propelling it along the conveyor's track. There are two primary drive types: caterpillar and sprocket. The type of drive affects both the chain and trolley speed and the rate at which materials are delivered to their destination.
Caterpillar Drives – Caterpillar drives are located at a high point of an overhead conveyor system to pull the chain. The drive has overload protection, a shear pin hub, and a current limiting method. A geared motor moves the caterpillar that moves the chain. The operation of a caterpillar drive is smooth, efficient, and quiet and installed on an enclosed track design.
The caterpillar of a caterpillar drive is a chain that has drive dogs that connect to the chain of the conveyor. Drive and take up sprockets move the drive chain and dogs that move the overhead conveyors chain drive.
Overhead conveyor tracks are categorized into I-beam and enclosed types, selected based on the application's requirements and conveyor use. I-beam tracks are popular for their strength and ability to support heavy loads and trolley wheels. Enclosed tracks vary in design, with some featuring a tubular structure and others having a rectangular or square cross-section.
Overhead conveyor tracks are constructed from robust steel to endure continuous operation. Their durability and reliability are significant factors in their widespread use, attributed to the high-quality materials used in their manufacture. This ensures that overhead conveyors maintain consistent performance and longevity.
Trolleys, which are linked to the chain drive, travel along the track to transport heavy loads. Each trolley features an attachment point for securing various types of load carriers. As the chain drive operates, it moves the trolleys along the track, carrying the overhead conveyor's load. The movement of the trolleys is regulated by the chain and drive system, allowing for controlled starting and stopping as needed.
Trolley designs are tailored to match the track type they are connected to, including configurations for tube enclosed tracks, I-beam tracks, and other enclosed track styles. Trolleys can be equipped with one to six wheels depending on the load requirements and weight they need to support. These wheels are
Take-up units in overhead conveyors are essential for maintaining proper tension on the chain drive and ensuring smooth operation. These units feature a roller turn or traction wheel design and address chain elongation caused by temperature fluctuations. Positioned near the drive, typically at a low point in the system, take-ups help manage the expansion and contraction of the chain.
Take-up units are positioned in various locations such as roller bank turns, traction wheel assemblies, or within spread track loops. They utilize different actuators like adjustable rods, counterweights, hydraulic or pneumatic cylinders, and springs, and are compatible with all track sizes. Essential for the efficient operation of overhead conveyors, take-ups help in maintaining chain tension and minimizing wear on trolleys and chains. By adjusting the chain length, take-ups reduce the need for frequent repairs or replacements.
Pendants in an overhead conveyor system are components that connect to the chain and support the loads being transported. Constructed from durable materials, these pendants are designed to handle the weight and operational stresses of the conveyor system. They attach to load pins on the chain, enabling materials to hang below the chain itself. Pendants are compatible with various tracks, brackets, chains, and other conveyor parts.
Spacing between pendants on an overhead conveyor chain differs based on the conveyor model and the type of materials being conveyed. To boost the load capacity, some items are supported by several pendants. Pendants come in various forms, including V-shaped, loading hooks, swivel fixtures, and double loading hooks, each suited for specific load needs.
Managing material movement and supply chains presents a significant challenge for industrial organizations, impacting both quotas and efficiency. To address this, automated systems for transporting raw materials, parts, and supplies have been developed. Modern automation has also revolutionized assembly processes, allowing products to be delivered to workstations, processed, and then seamlessly moved to the next station.
Overhead conveyors play a crucial role in optimizing product movement by utilizing vertical space that would otherwise remain idle. These chain-driven systems enable the safe and efficient transportation of items of various sizes and weights to different locations within a facility. As a result, overhead conveyors have become a cost-effective and efficient component of the supply chain.
One of the most common uses for overhead conveyors is painting, coating, and finishing. Overhead conveyors make it possible to handle multiple items, shapes, sizes, and loads to be processed. The use of overhead conveyors for finishing is because overhead conveyors prevent overspray and reduce the amount of dripping paint. Large items can be conveniently handled without the need to lift and move them. The problems associated with car doors and windows are eliminated by using overhead conveyors, which is the reason overhead conveyors have become a staple of auto assembly.
Henry Ford pioneered the assembly line for automobile production, significantly increasing the efficiency of producing Model T Fords daily. This method soon set the benchmark for the automotive industry and was adopted by other manufacturers. Originally, assembly lines were used in meatpacking plants before becoming a staple in automobile manufacturing.
Modern automobile manufacturing relies heavily on conveyor systems, with overhead conveyors being a key component. These systems are essential for tasks such as painting and coating, enhancing both safety and precision. Power and free overhead conveyors are used to transport vehicle frames and bodies along the assembly line, allowing workers to perform tasks without worrying about the continuous movement of the frames and bodies.
For years, forklifts have been a staple in warehousing for moving supplies, orders, and heavy equipment. They, along with pallet jacks, facilitate the quick picking and placing of items for packaging, storage, and shipping. Recently, as warehouses have embraced automation, conveyor systems have been integrated to reduce the need for manual item handling. These advancements have significantly improved picking efficiency and accuracy.
Overhead conveyors streamline the process of storing items by utilizing a computerized numbering system. This system minimizes errors, maintains precise counts, and helps prevent inventory losses. Overhead conveying systems are particularly useful in facilities with limited space or manpower.
Some materials, due to their unique shapes or designs, are not suitable for conventional conveying methods. Overhead conveyors, which carry items suspended beneath the chain and track, are well-suited for these types. This method is particularly advantageous for materials that have undergone processes like heat treatment or baking, which might damage other conveyor systems.
With the increasing reliance on robotics, there's a significant need for efficient component handling and positioning. Overhead conveyors are well-suited for integration with robotic systems, providing the required efficiency. Because robotics operate based on programmed actions, overhead conveyors can be configured to align seamlessly with these movements, allowing for smooth integration without major modifications.
In robotic systems, overhead conveyors handle various tasks such as loading cartons and parts, moving items between different conveyors, and supporting vision-based programming, commonly used in Automated Guided Vehicles (AGVs) and Autonomous Mobile Robots (AMRs). The integration of overhead conveyors with robotics continues to expand, offering versatile and evolving solutions as these technologies work together.
Upon closer inspection, it's clear that overhead conveyors have significantly impacted industrial operations and applications. Each year, advancements and new uses for this technology are explored by supply chain and assembly engineers. Overhead conveyor manufacturers often anticipate the challenge of developing innovative solutions for clients seeking novel ways to utilize this conveyor system for transporting products.
A major advantage of using overhead conveyors is their contribution to workplace safety. These systems move heavy loads overhead, reducing the need for manual handling by employees and thus decreasing the likelihood of injuries. By operating above the work area, overhead conveyors help prevent unnecessary interactions between workers and moving items. As the focus on ergonomic design and efficiency increases, overhead conveyors remain an essential tool for protecting workers and minimizing workplace accidents.
Each overhead conveyor system must be tailored to meet specific conditions and requirements, as no single system is universally applicable. Whether integrating an overhead conveyor into an existing setup or implementing one in a new location, careful design and engineering are essential. Precision calculations and planning ensure that the system operates smoothly and efficiently. In summary, every overhead conveyor system is customized to fit its unique environment and operational needs.
Overhead conveyors are effective labor-saving tools designed to eliminate the need for manual transport of essential items or materials. By automating the movement of goods, these systems reduce the risk of injuries, prevent production delays, and minimize the need for additional personnel. The automation provided by overhead conveyors not only enhances productivity but also contributes to cost savings by reducing the likelihood of operational disruptions and inefficiencies.
In many industrial settings, vertical space often remains underutilized due to its position within a facility and the requirement for specific equipment. Overhead conveyors efficiently use this vertical space, freeing up ground-level areas for various functions or reducing equipment congestion. This optimization of space enhances overall facility efficiency and functionality.
A belt conveyor is a system designed to transport or move physical items like materials, goods, even people from one point to another. Unlike other conveying means that employ chains, spirals, hydraulics, etc...
A bucket elevator or grain leg is used to move items in bulk. The usage of bucket elevators is widespread, notably in commercial agriculture and mining, and several specialized businesses manufacture bucket elevators and...
Processing equipment for holding and moving bulk bags is known as bulk bag equipment. This bulk bag equipment is typically used at the front end of the production process to hand off product to...
A conveyor system is a method for moving packages, products, supplies, parts, and equipment for production, shipping, or relocation. The different types of conveying systems include pneumatic, screw, belt, and roller. The construction of individual systems depends on the materials...
A conveyor belt is a material handling system designed to move supplies, materials, and components using an efficient and effortless process that saves on time, energy, and cost. The design of conveyor belts includes two motorized pulleys with the conveyor material looped over them...
Flat belts are power transmission belts that are flat and made of rubber, synthetic composites, or leather. They are used to transfer rotational power in industrial equipment and conveyor systems. Flat belts have a low profile with a positive grip, which...
A vertical conveyor is an engineered mechanical method for moving goods, products, supplies, parts, and components from a lower level to a higher level or from a higher level to a lower level. They are...
Vibratory conveyors are material-handling equipment used to transport fine to coarse-grained bulk materials. These vibratory conveyors are strong conveying equipment utilized for bulk commodities with fine to coarse graininess...
A machine guard is a mechanism whose role is to act as a safety barrier between a worker and machines used in manufacturing facilities, factories, plants, and warehouses. Furthermore machine guards keep vehicles out of certain areas...
A metal conveyor belt is a conveyor belt that uses metal in the form of flat sheets or woven wire mesh as its belt surface. The use of a metal surface enhances the ability of a conveyor to handle parts and...
Pneumatic conveying is a method for transferring bulk materials, like powders and granules, using compressed gas or air, from one processing center to another. Material is moved through an enclosed conveying line or tube using a combination of pressure differential and airflow from a blower or fan...
Screw conveyors, or auger conveyors, are industrial equipment used in transporting bulk quantities of granular solids (e.g., powder, grains, granules), semi-solids, liquids, and even non-flowing materials from one point to another...
A timing belt is made of rubber with hard teeth capable of interlocking with camshafts and crankshafts cogwheels. It is an integral component of an internal combustion engine responsible for...
A v-belt is a flexible machine element used to transmit power between a set of grooved pulleys or sheaves. They are characterized as belts having a trapezium cross-section...
Vacuum conveyors are suctioning machines that utilize air pressure in order to move materials through an enclosed pipeline. Vacuum conveyors have broad applications throughout the industrial and...