Cold Heading & Cold Forming
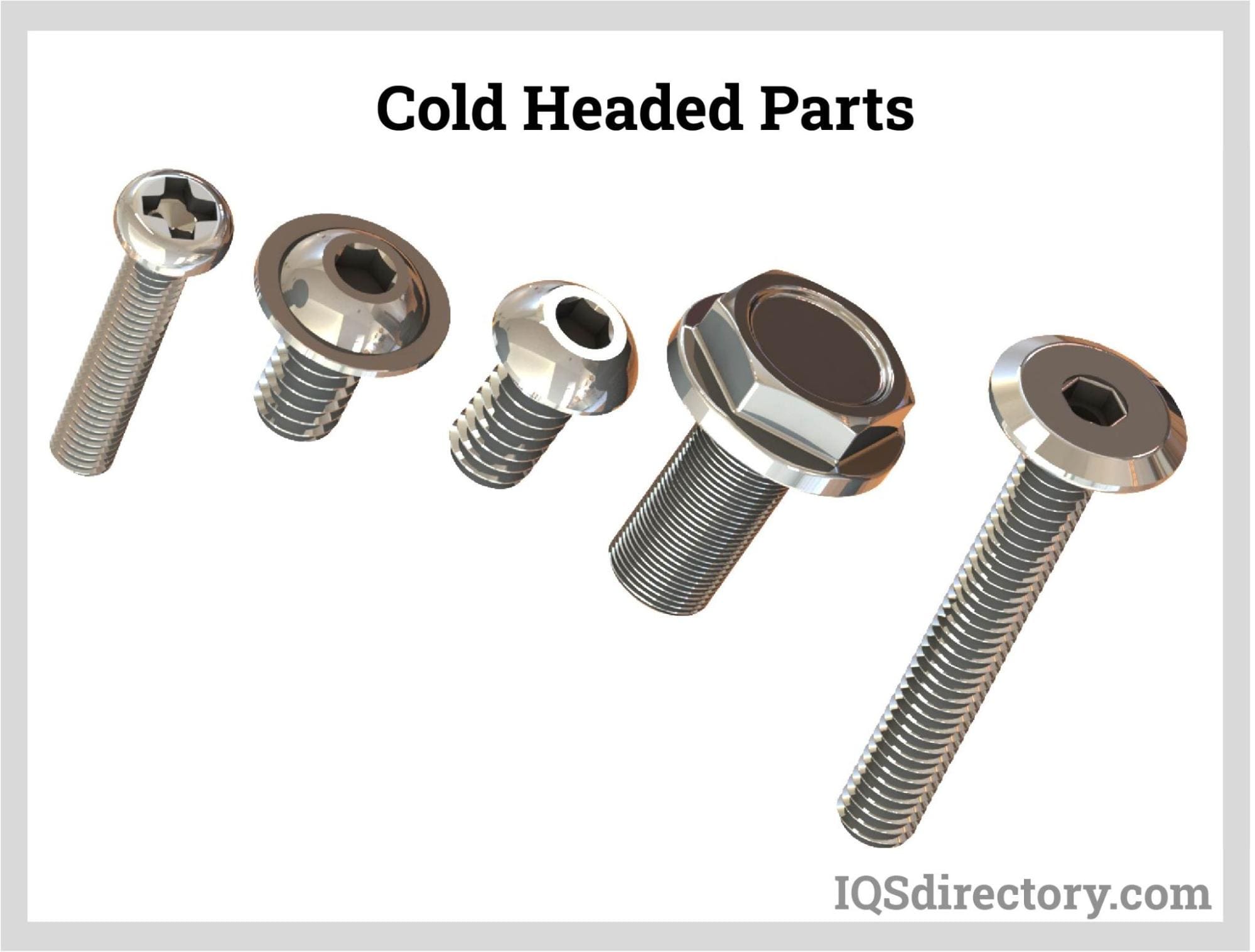
Metal forming is an essential stage in metal production, involving techniques that deform metals without reducing material or altering its mass. Its objective is to shape and transform raw metal by subjecting it to tension, compression, shearing, and pressure.
Since the advent of the first industrial revolution, various metal forming techniques have evolved. Starting with a plain sheet of metal, processes such as forging, rolling, extrusion, drawing, stamping, and others are employed to create durable metal products.
There are two primary methods for forming metals: hot and cold. Cold forming, also known as cold heading, occurs at or slightly above room temperature. It involves a sequential process using dies and hammers to gradually shape the workpiece into the desired form.
Die casting is a widely adopted method for shaping metals, involving heating metals to their melting point and pouring molten metal into molds. Typically, non-ferrous metals like copper, aluminum, zinc, magnesium, lead, tin, or bronze are used. Die casting offers the advantage of producing precise products and parts with extremely tight tolerances.
Expanded metal is a cold metal forming technique where metal is stretched and pulled, simultaneously pierced with a blade to create patterns in the sheet. This cost-effective process applies to aluminum, various steel types, and copper. Following processing, finishes and coatings can be applied for protection or aesthetic enhancement.
Forging, one of the oldest metal forming methods, involves subjecting a metal sheet to stress to induce deformation. This alters the metal's grain flow, shaping it to conform to the forging die. Positioned between cold and hot forging, the process may involve heating to facilitate shaping without melting the metal.
Grey iron casting, an ancient metal forming technique practiced for centuries, differs distinctly from forging. It derives its name from the gray hue resulting from graphite content in the metal. Various methods, including sand casting, are employed to produce grey iron castings, with sand casting being particularly prevalent.
Metal spinning is a cold metal forming technique where a flat metal disc is rotated at high speed to achieve desired shapes. Pressure is applied using specialized tools, known as spoons, which can range from a single tool to multiple tools depending on the complexity of the part's design.
Powder metallurgy is a long-standing metal forming method where metal is transformed into powder and then compacted in a die under high pressure. This compaction causes particles to interlock and conform to the die's shape. To enhance strength, the part is subsequently sintered by heating it close to its melting point.
Various processes are employed to shape metals into products like springs, wire forms, and wire mesh. Typically, these processes involve cold forming, though some methods may involve heating metals to increase their malleability.
Cold headed parts are products or stock shapes created using a specialized cold working process, which is part of a broader category known as cold forming. Unlike traditional methods involving heat, these techniques operate at ambient temperatures. Despite the term "cold," these metallurgical processes generally occur at room temperature using specialized machinery.
Learn more about cold headed parts.
Expanded metals are created from plate or sheet metal that undergoes perforation via a series of slits, cut along parallel lines, and then stretched into a mesh structure. This stretching can increase its width by up to ten times, depending on the length of cuts, width of metal between cuts, and amount of stretching applied. It is a lightweight and cost-effective alternative to solid plates and sheets, maintaining structural integrity without unraveling.
This versatile mesh is used to filter light, air, water, materials, sound, and views, commonly used in decking, fencing, screening, lath, and decorative purposes. Materials range from aluminum, steel, mild steel, carbon steel, stainless steel, copper, to plastics, offering various finishes to suit different designs. Perforation patterns can feature staggered lines for optimal open area when stretched, or evenly spaced fine lines. Typical designs reveal diamond-shaped holes, though other patterns are possible. Measurements are based on Long Way Diamond (LWD) and Short Way Diamond (SWD) specifications, tailored to specific application requirements.
Expanded metals differ from perforated metals, which are solid sheets with punched-out holes of specific designs and not stretched. Despite similarities in use, expanded sheets weigh less per inch and offer greater flexibility compared to perforated sheets of equal weight.
Learn more about expanded metals.
Metal spinning, also known as spin forming, is a cold metalworking process where a flat metal disc, fixed onto a lathe mandrel, spins at high speeds and is shaped using forming tools.
Using tools known as spoons, a metal spinner applies pressure to the rotating disc, known as a blank, to shape it over a mandrel. This can involve a single tool or multiple tools. The process ensures the finished product is free from wrinkles or warbling, emphasizing efficiency and cost-effectiveness. Typically, forming an average metal piece takes only five to ten minutes, with minimal metal waste generated per part.
Learn more about metal spinning.
Powder metallurgy produces solid metal parts used widely across industries including lawn and garden, computer electronics, hardware, and automotive sectors. These components are crafted from powdered metal, offering versatile applications.
Powder metal parts encompass magnetic assemblies, filtration systems, structural components, and automotive parts. Powder metal gears, characterized by their inherent porosity and noise-reducing properties, are well-suited for sintering processes. Bearings and bushings can be efficiently manufactured through sintering, though they may necessitate secondary sizing due to the precision required during fabrication.
Learn more about powder metal parts.
Roll formed parts are metal products shaped through a series of rollers in the roll forming process. Commonly roll formed metals include brass, steel, zinc, aluminum, and zirconium. These parts are appreciated for their uniformity, precision, structural strength, and cost-effective tooling. They are used across diverse industries including building construction, architecture, carpentry, commercial automotive, and home improvement sectors, in the fabrication of various commercial, consumer, and industrial products.
Common roll formed products used in carpentry and building construction include angle irons, aluminum angles, steel angles, metal channels, and metal trim. These angles are specifically engineered to provide dual-directional support and often include slots or holes for connecting components.
Learn more about roll forming.
Springs are essential components found in numerous devices, machines, and systems. They are elastic devices that exert a resistant force when compressed or stretched. Springs serve to store and absorb energy, as well as maintain the necessary force or tension within their intended applications.
Springs are utilized in various applications such as circuit breakers, solenoid valves, writing instruments, and electronics. They are categorized into four primary styles: compression springs, extension springs, torsion springs, and flat springs. A combination of a flat spring and a coil spring is commonly referred to as a constant force spring.
In addition to these main categories, springs are available in a diverse array of styles. Industrial springs are usually crafted from thick wire, whereas smaller springs can be made from thin, flexible wire. Some of these springs are too minuscule to be visible to the naked eye.
Learn more about springs.
Wire forms encompass a diverse array of shapes and components crafted through wire manipulation, involving techniques like cutting, bending, and heat treatment. Essential across various sectors, they cater to industries such as commercial retail—utilizing wire displays for product placement like point-of-purchase (POP) displays and wire grids—and industrial manufacturing, where they serve purposes ranging from wire racks and shelves in storage systems to protective wire guards for machinery.
Learn more about wire forms.
Wire mesh is a versatile industrial product created by weaving or welding interlocking metal wires into a mesh with uniformly spaced openings. It’s often used in filtering, screening, structural support, and protection across industrial, agricultural, and residential settings.
Industries such as petrochemical processing, screen printing, pharmaceuticals, and food and beverage processing carefully select wire mesh materials based on specific application needs. Different weave patterns, such as twilled square mesh, plain square mesh, plain Dutch weave, reverse plain weave, and twill Dutch weave, cater to diverse requirements. For example, plain square meshes, woven from equal gauge lateral and longitudinal wires, excel in fundamental mesh operations.
Learn more about wire mesh.