Aircraft Cables
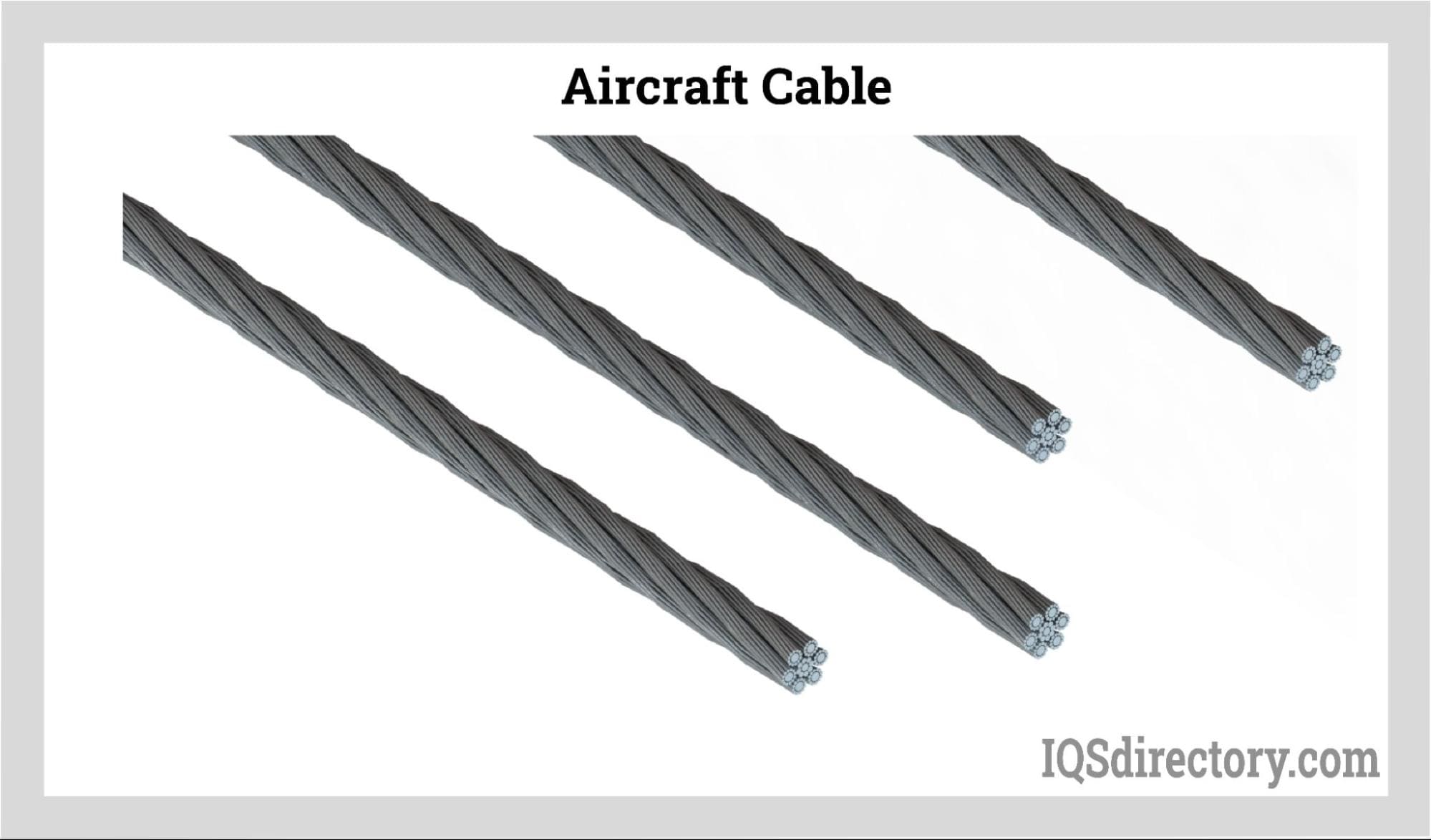
An aircraft cable is a style of highly durable cable that is used for aircraft flight controls and other applications and is differentiated from normal cables by its diameter, stranding, and wires, which provide...
Please fill out the following form to submit a Request for Quote to any of the following companies listed on
The article contains detailed information on wire rope assemblies and their use.
You will learn:
A wire rope assembly is composed of wire rope and end fittings, terminals, or lanyards that are attached to various parts of the wire rope such that the assembly can be used to lift, hoist, and move loads. The various types of assemblies are designed for a variety of lifting applications from small riggings that position parts for repair to support for suspension bridges.
The key to wire rope assemblies is the type of wire rope, which varies according to its construction and how its cables are combined. Although individual wires may not have the strength to hold a load, when the strands of wire are arranged and twisted together, they become a strong and formidable lifting tool capable of handling massive loads.
The different types of wire rope assemblies are designed for specific applications and are uniquely constructed to lift particular loads. Wire rope assemblies are resistant to heat and abrasion and offer high level performance in any type of conditions. A critical aspect of wire rope assemblies is selecting the correct assembly to fit the job since selecting an assembly with low load capacity can lead to application failure.
Wire rope is available in different strengths and metals each of which determines its load capacity. Manufactures provide clear and concise information regarding wire rope assemblies as well as in person assistance.
A push pull wire rope assembly or pull push wire rope assembly is a control device that sends smooth mechanical power to remote locations. They perform as throttle controls, latch releases, actuators, and clutch cables. All of the work of push pull wire rope assemblies is performed with less friction around corners and through small openings. The wire rope of a push pull wire rope assembly is encased in a polymer to allow for protection and smooth movement.
Single leg wire rope slings are a common type of wire rope assembly used for lifting and rigging applications. They are created by attaching a wire rope sling to a lifting hook or other attachment point and are used to lift heavy objects such as machinery or construction materials. Single leg wire rope slings can be made from a variety of wire rope materials, including galvanized or stainless steels.
Multi-leg wire rope slings are similar to single leg slings but have multiple legs or branches that attach to a single lifting point. The design allows for greater load distribution and can increase the overall lifting capacity of the assembly. Multi-leg wire rope slings can be made from a variety of materials and can be configured in different ways depending on the specific lifting application.
Wire rope lanyards are used to secure tools, equipment, or workers in elevated positions such as scaffolding or construction sites. They are typically made from galvanized or stainless steel wire rope, are designed to withstand heavy loads, and prevent equipment and tools from falling. Wire rope lanyards can be customized to fit specific lengths and attachment points, making them versatile and adaptable for different applications.
Cable railings are a type of wire rope assembly commonly used in residential and commercial construction sites. They are created by attaching horizontal or vertical wire ropes to a supporting frame or structure, providing a secure and durable railing system for balconies, stairs, and other elevated areas. Cable railings can be made from stainless steel or other materials and can be customized to fit specific design requirements.
Guy wire assemblies are used to provide stability and support for tall structures such as transmission towers or antenna masts. They are created by attaching wire ropes to anchor points on the ground and to the structure being supported, creating a tensioned system that helps to resist wind and other forces. Guy wire assemblies can be made from a variety of wire rope materials and are typically designed and installed by experienced professionals.
Wire rope tethers are a type of wire rope assembly used to secure or anchor equipment or other objects in place. They are commonly used in the marine and transportation industries, as well as in manufacturing and other applications. Wire rope tethers can be customized to fit specific lengths and attachment points, and are typically made from galvanized or stainless steel wire rope.
Control cables are used in various applications to transmit motion or force between two points. They are typically made from a combination of wire rope and flexible conduit, which protects the wire rope from external damage and helps to maintain its strength and flexibility. Control cables can be used in a wide range of applications, including industrial machinery, automotive systems, and marine equipment.
Winch lines are a type of wire rope assembly commonly used in the marine, construction, and transportation industries. They are designed to withstand high loads and provide reliable traction for winches and other pulling systems. Winch lines can be made from a variety of materials, including galvanized or stainless steel wire rope, and are typically configured with eye hooks or other attachment points.
Cane cables are a type of wire rope assembly used in the sugar cane harvesting industry. They are created by attaching wire rope to a harvesting machine or tractor and are used to pull the harvested cane from the fields to a processing facility. Cane cables are typically made from galvanized or stainless steel wire rope and are designed to withstand the harsh conditions of the sugar cane fields.
Wire rope sling assemblies are a versatile type of wire rope assembly used in lifting and rigging applications. They are created by forming wire rope into a sling configuration and attaching it to a lifting hook or other attachment point. Wire rope sling assemblies can be made in a wide range of configurations, including single leg, multi-leg, and endless slings, and can be customized to fit specific lifting requirements.
Wire rope hoists are used in various industrial and construction applications to lift and move heavy loads. They are typically powered by an electric motor and use wire rope to lift and lower the load. Wire rope hoists can be customized to fit specific lifting requirements and are available in a range of capacities and configurations.
Wire rope catenary systems are used in various applications, including overhead power transmission. They are created by hanging wire rope between two points and allowing it to sag under its own weight, creating a curved shape known as a catenary. Wire rope catenary systems are designed to withstand high loads and provide reliable support for overhead structures.
Each type of wire rope assembly is designed for specific applications and is created using specialized construction methods and materials. By understanding the different types of wire rope assemblies and their uses, users can select the right assembly for each application and ensure safe and efficient operations.
A wire rope assembly is a combination of wire rope and end fittings, terminals, and lanyards that are attached to wire rope to form a complete unit. End fittings, terminals, and lanyards are selected based on the intended use of the assembly. End fittings are located at each terminal connected to the wire rope, such as a piece of equipment or an object.
Hooks are used to connect the wire rope assembly to the load or anchor point. They come in various shapes and sizes, including eye hooks, clevis hooks, and grab hooks, and are often made from materials like alloy steel or stainless steel.
Eyelets are essentially loops that are formed at the end of a wire rope. They are used to create an attachment point or to pass the rope through itself to form a loop. Eyelets can be made from materials like aluminum, stainless steel, or carbon steel.
Wire rope assembly thimbles create a loop or eyelet to reinforce wire rope as it is looped. They prevent friction from fraying wire rope at its anchor point and enhance the service life of a wire rope assembly.
Thimbles are available in several sizes and strengths and come in light duty grade and heavy duty grade. Light duty grade thimbles are used in static applications where they won’t experience any significant load. Heavy duty grade thimbles have a thick coating and are used with applications that require the wire rope assembly to be frequently connected and disconnected.
The choice of a wire rope thimble is determined by the environment where it will be used. Stainless steel thimbles are used in corrosive environments and saltwater environments. Zinc plated steel, hot dipped galvanized steel, and grade 316 stainless steel are used to produce most wire rope assembly thimbles.
Sleeves, also known as ferrules, are used to terminate a wire rope by crimping the sleeve onto the rope. This creates a strong and durable attachment point that can be used for a variety of applications. Sleeves can be made from materials like copper, aluminum, or stainless steel.
Shackles are used to connect two wire rope assemblies or to attach a wire rope assembly to a load or anchor point. They come in various shapes and sizes, including D-shackles, bow shackles, and screw pin shackles, and are often made from materials like alloy steel or stainless steel.
The selection of end fittings, lanyards, and terminals depend on the application, the environment, and the requirements of the application. For example, a lifting sling may use a hook or shackle at one end to connect to the load and a thimble or sleeve at the other end to create a secure attachment point.
Wire rope cable railing assemblies may use eyelets or turnbuckles to tension the wire rope between posts. It is important to select end fittings that are appropriate for their intended use and are compatible with the wire rope. For the best results for wire rope performance, fittings should be installed correctly and securely to avoid safety hazards.
Wire rope grips are used to secure wire rope after it has been looped. This would apply to looping wire rope over a thimble. After the wire rope is passed through the thimble, the loose end is connected to the rest of the wire rope using a grip, which consists of a U shaped bolt that is threaded on both ends, a bracket that slips over the threaded ends, and two bolts to hold the grip in place.
Turnbuckles have two eye bolts at each end of a metal frame and are used to adjust tension and reduce slack on wire rope. The center of a turnbuckle is its metal frame that joins two threaded end fittings that take various shapes, such as hooks, jaws, and eyes.
Bodies of turnbuckles can be open or closed with open turnbuckles being the traditional type with the threads of the end fittings being visible. Closed turnbuckles or pipe turnbuckles encase the threads in a closed frame for a slimmer appearance. To tighten or loosen a turnbuckle, the body of the frame is turned.
A jam nut may be placed on the end of the threaded ends of the fittings, which is tightened to prevent the end fittings from unthreading or loosening.
Wire rope sockets are terminations that fit on the ends of wire rope as an anchoring system.
Wire rope socks are made of braided wire rope and have the shape of an open ended sleeve. They come in single eye, offset eye, and lace up styles made of galvanized steel wire and stainless steel wire. Wire rope socks are used to pull cables through and are referred to as pulling cables.
The process for making splices involves intertwining wire rope with wire rope. During the process, a wire rope has its strands opened in two parts, which are brought together by being looped in opposite directions to form an eye or loop at one end. Once looped, a metal sleeve is forcefully placed over the section that has been spliced to form a strong permanent connection. The forming process is an economical and efficient method for maximizing the use of wire rope.
A form of wire rope splicing that does not require a metal sleeve is a hand tucked splice, a process that uses tension in the wire rope to secure loose strands back into the body of the rope. The end of a wire rope with loose strands is bent backward along the rope body. The strands are tightly tucked back into the body to form a sling or eye. The strands are woven into the body to form a secure tight connection.
Wire rope ball fittings can be placed anywhere along the length of a wire rope. They come in a variety of sizes and diameters. Wire rope ball fittings have a round ball like section and a shank that is used to hold them in place. The shank can be placed on one side of the ball or on both sides. They are slid onto the wire rope through a hole located in the center of the ball and shank. Once positioned, the shank is forcely compressed to make a firm connection with the wire rope.
Strap forks are used with ball fittings. They have the shape of brackets with extended legs or straps that are longer than the base of the bracket. The length of the straps varies according to the design of the forks. Holes are placed at the top of the straps to accommodate the securing of loads. The hole at the base of the straps is placed over the ball of a ball fitting, which allows the strap forks to rotate or twist with loads. The movement protects the wire rope from friction.
The selection of the type of material used to construct a wire rope assembly is a critical aspect of its manufacture. The wrong material can lead to hazardous conditions and wire rope assembly failure. The primary materials used to produce wire rope assemblies are steel, stainless steel, galvanized steel, and bright steel. Knowing the difference between the various metals can ensure the successful use of a wire rope assembly.
Steel wire rope is the most common type of wire rope used in industrial applications due to its high strength and durability. It is made of high-carbon steel wires that are twisted together to form strands, which are then twisted together to form the rope. Steel wire ropes are used in applications such as construction, mining, oil and gas, and marine industries.
Stainless steel wire rope is corrosion-resistant and is often used in applications where the rope is exposed to harsh environments or chemicals. It is commonly used in marine, food processing, and pharmaceutical industries.
Galvanized steel wire rope has a protective coating of zinc, which provides corrosion resistance. It is commonly used in applications where the rope is exposed to outdoor environments or corrosive substances. It is used in construction, marine, and transportation industries.
Bright steel is made without a surface treatment or coating and is lubricated to protect the wire against corrosion. It is made of carbon steel and is capable of carrying the same loads as galvanized steel wire ropes. Bright steel wire rope assemblies are restricted from use in environments with high humidity, moisture, or harsh chemicals.
Bright steel wire rope is used with single part lines and in conditions where wire rope is required to resist cabling in a multipart system. The drawback to bright wire rope is the limitations created by its rotation resistant wire rope design, which requires special handling and use in special applications.
Since its invention by Wilhelm Albert at the beginning of the first industrial revolution, wire rope has become a mainstay in industrial applications that require lifting, hoisting, or securing of materials and goods. After its introduction, the use of wire rope assemblies rapidly grew due to its superior performance over hemp ropes and metal chains. Its wide use is due to its outstanding properties and characteristics.
Wire rope and wire rope assemblies are known for their high strength and durability, making them ideal for lifting and moving heavy objects. Wire rope is also resistant to abrasion and corrosion, ensuring a longer lifespan and reduced maintenance costs.
Wire rope assemblies are designed to support heavy loads, making them ideal for use in applications where heavy load capacity is required. By law, wire rope assemblies are marked with a safe working load (SWL) measurement. The lifting ability of wire rope assemblies is from one or two tons up to one hundred tons depending on their configuration, type of rope, and design.
Wire rope assemblies are designed with safety in mind. They are engineered to withstand high stress and heavy loads, and are rigorously tested to ensure they meet industry standards for safety and performance. Additionally, wire rope assemblies are often used in applications where worker safety is critical, such as in elevators or on construction sites.
Wire rope and wire rope assemblies can be used in a wide variety of applications and industries, making them a versatile and adaptable solution. From construction and mining to transportation and aerospace, wire rope assemblies can be tailored to meet the specific needs of each industry and application.
While wire rope assemblies may have a higher upfront cost than some other lifting and rigging solutions, they offer a longer lifespan and reduced maintenance costs over time. This makes wire rope assemblies a cost-effective solution for many applications, particularly those with high load capacity requirements.
Wire rope assemblies are often made from materials that are recyclable and have a lower environmental impact than other materials. Additionally, they are designed to use less energy for operations than other lifting and rigging solutions, making them a more sustainable choice for many industries.
The benefits of wire rope assemblies include strength, durability, load capacity, safety, versatility, cost-effectiveness, and environmental friendliness. Appropriate wire rope assemblies ensure safety, efficiency, and reliability while meeting sustainability goals. They are a critical part of a wide range of applications from lifting and moving heavy objects to providing safety and security in construction and transportation settings.
From its beginning as a replacement of metal chains and rope, wire rope assemblies have rapidly found a place in a wide assortment of industrial applications. Much of its popularity is due to its exceptional reliability and dependability. Regardless of whether it is holding a television tower in place under great stress or moving shipping grates, wire rope assemblies seldom fail and are capable of holding extreme weights of several tons without any signs of fatigue or stress.
Wire rope assemblies are commonly used in the transportation industry for various purposes. For example, in suspension bridges, wire rope assemblies are used to support the bridge deck and distribute the weight of traffic. They are also used in elevators to lift and lower the elevator cars. Cable cars use wire rope assemblies to support the car and ensure safety.
In the construction industry, wire rope assemblies are used in various applications such as crane cables, hoists, and cable railing systems. Crane cables are used to lift and move heavy objects on construction sites, while hoists are used to lift and lower workers or equipment. Cable railing systems provide safety and security on balconies, stairways, and elevated areas.
Wire rope assemblies are used as drilling lines due to their ability to withstand the pressure, stress, and temperatures of the drilling process. They are used in every aspect of drilling including deep water drilling at sea and ones on land. They provide unfailing support, stability, and precision controlled drilling.
Wire rope assemblies are often used in power transmission applications such as hoisting, towing, and conveyor systems due to their high strength, flexibility, and durability. They are commonly used in cranes, winches, and cable cars, where they transmit power over long distances and support heavy loads.
Wire rope assemblies are used in automotive construction for various applications, such as in the clutch and brake systems, suspension systems, and steering systems. They provide reliable and durable performance under high stress and heavy loads, making them an essential component in the safe and efficient operation of vehicles.
In the mining industry, wire rope slings are commonly used to lift and move heavy objects, such as ore or equipment. Wire rope slings are designed to be flexible and durable, making them ideal for use in harsh mining environments.
Wire rope assemblies are used in the forestry industry for various purposes, including logging and tree removal. For example, wire rope assemblies can be used to lift and move logs, or to pull trees down in a controlled manner.
In the manufacturing industry, wire rope assemblies are used for lifting and moving heavy objects, such as machinery or products on an assembly line. These assemblies are designed to provide stability and control, allowing workers to move objects with precision and safety.
Wire rope assemblies are commonly used in the marine industry for various applications, such as mooring lines, anchor chains, and winches. These assemblies are designed to withstand harsh marine environments and resist corrosion.
Wire rope assemblies are used in the agriculture industry for various purposes, such as for animal feeders and waterers, as well as for lifting and moving heavy equipment. As hinted at earlier, wire rope assemblies are also commonly used in sugar cane harvesting equipment such as cane haulage systems, winches, and elevators to ensure safe and efficient transportation and handling of the sugar cane.
In the food processing industry, wire rope assemblies are used for various applications such as hoisting and conveying food products, as well as supporting equipment such as conveyors, ovens, and mixers. Wire ropes used in food processing are typically made of stainless steel or galvanized steel to meet hygiene standards and resist corrosion.
Wire rope assemblies are used in the pharmaceutical industry for various applications such as lifting and moving equipment and materials, as well as supporting HVAC systems and other utility equipment. The wire ropes used in pharmaceuticals are usually made of stainless steel or synthetic materials to meet hygiene standards and resist contamination.
Wire rope assemblies are used in the aerospace industry for various applications such as control cables, landing gear, and wing rigging. The wire ropes used in aerospace are typically made of high-strength steel or synthetic materials that are lightweight and corrosion-resistant.
In the entertainment industry, wire rope assemblies are used for various applications such as stage rigging, suspension systems, and special effects. Wire ropes used in entertainment are usually made of synthetic materials such as nylon or polyester, which are lightweight and flexible, making them ideal for suspending loads and creating intricate rigging setups
Regular maintenance and inspection of wire rope assemblies is crucial to ensure their safe and reliable operation. Wire rope assemblies are subject to wear from repeated use, as well as environmental factors such as corrosion, UV exposure, and extreme temperatures. Without proper maintenance and inspection, they can fail, leading to costly downtime, property damage, and injury or loss of life.
Wire rope assemblies should be inspected on a regular basis to identify any signs of wear, damage, or other issues that could compromise their safety and performance. Inspections should be conducted by trained personnel using appropriate tools and equipment.
Wire rope assemblies should be cleaned regularly to remove dirt, debris, and other contaminants that can accelerate wear and corrosion. The cleaning method will depend on the type of assembly and the environment in which it is used.
Wire ropes should be lubricated regularly to reduce friction and wear, as well as protect against corrosion. The type and frequency of lubrication will depend on the type of assembly and the environment in which it is used.
Wire rope assemblies that show signs of wear, damage, or other issues should be replaced as soon as possible to avoid failure.
The strength and durability of wire rope assemblies gives the indication that they are so highly durable that they will never fail. Although this is a good premise upon which to choose a wire rope assembly, they are like any other tool that can wear out and fail over time. Due to the critical nature of their functionality, it is important to be aware of the types of failures wire rope assemblies can exhibit.
Wire rope assemblies can experience fatigue over time, especially if they are subjected to frequent bending, twisting, or other stressors. This can lead to wire breakage or other failures, which can be dangerous if the assembly is used to lift or move heavy objects. Proper inspection and maintenance can help to mitigate this issue.
Wire rope assemblies are susceptible to corrosion, especially if they are exposed to moisture or other environmental factors. This can weaken the wire rope and reduce its load capacity, making it less safe for use. Proper storage and handling, as well as regular cleaning and lubrication, can help to prevent corrosion.
Wire rope assemblies can also experience abrasion over time, especially if they are used to lift or move heavy objects or are subjected to other types of wear and tear. This can cause the outer layer of the wire rope to wear away, exposing the inner wires and reducing the assembly's strength. Regular inspection and replacement of worn wire rope can help to mitigate this issue.
Wire rope assemblies can be complex to install and maintain, requiring specialized tools and expertise. Improper installation or maintenance can lead to wire rope failure or other safety issues. It is important to work with experienced professionals who are trained in proper assembly installation and maintenance.
Some of the problems during installation include high stranding, improper seizing, twisting, and wavy rope. High stranding occurs at installation due to improper seizing of wire rope or maintaining seizing during wedge socket installation. Torque or twist and wavy rope can occur during installation and cause grooving problems or kinks.
Wire rope assemblies may not be compatible with all types of lifting and rigging equipment or machinery, which can limit their use in certain applications. Careful selection and testing of wire rope assemblies and related equipment can help to ensure compatibility and safety.
Wire rope assemblies can vary significantly in cost depending on their application, materials, and manufacturing process.
The inspection of wire breaks in a wire rope assembly should be completed by a certified American Society of Mechanical Engineers (ASME) inspector. Breaks on the outside of the wire rope assembly give a clue to the general condition of the assembly and whether it should be replaced.
Inspectors use various instruments to probe the strands of broken wire. Visible breaks on the surface of the wire rope and the connections are easy to see and examine. As with all forms of equipment, an inspection record must be maintained regarding the types of breaks, damage, and the amount of time between breaks. Replacement is advised when the number of breaks reaches ASME parameters or manufacturer specifications.
Diameter reduction is caused by abrasions, loss of core diameter, corrosion, and inner wire failure. The initial diameter of the wire rope compared to its present condition is the normal method for assessing diameter reduction. During the use of a wire rope, inspectors will periodically measure the diameter of wire rope in the same spot, which varies after its initial reduction at installation.
Shock loading is a common problem with wire rope assemblies, which is caused by a sudden release of tension followed by a sudden rebound from being overloaded. This type of damage is permanent and requires the replacement of the wire rope assembly.
Testing and certification of wire rope assemblies by an ASME inspector is a necessary procedure to ensure the safety and reliability of the assembly. Wire rope assemblies are subjected to high stresses and loads, which makes it important to know what forces they can withstand without failing.
Wire rope assemblies should be load tested to ensure that they can handle the expected loads and stresses that they will be subjected to during use. ASME inspectors have mechanisms and procedures they use to test the load capabilities of wire rope assemblies. Standard B30.30 rope standards and types of crane wire rope inspections are the guidelines that ASME inspectors use when examining and certifying wire rope assemblies. The various aspects of B30.30 covers Occupational Safety and Health Administration (OSHA) definitions such as rope structure distortion, broken wires, corrosion, deterioration, and environmental conditions.
Wire rope assemblies that have been load tested and found to meet the required standards are then certified as safe to use. Certification is completed by an ASME licensed inspector.
Wire rope assemblies are recertified at regular intervals to ensure that they continue to meet the required standards for safety and performance. The frequency of recertification depends on the type of assembly and the environment in which it is used.
Due to their importance in so many current applications, there are several parameters to consider as to the future use of wire rope assemblies.
Wire rope assemblies are typically made from steel or other metals, but advancements in material science could lead to new materials being used in wire rope assemblies. For example, high-strength synthetic fibers are becoming more widely used in industries like offshore oil and gas and aerospace. These materials have advantages over traditional steel wire rope, such as lower weight, increased flexibility, and resistance to corrosion and abrasion.
As automation continues to be integrated into industries like manufacturing and logistics, wire rope assemblies may be used in more automated systems. This could lead to wire rope assemblies being used for tasks that were previously done manually, such as lifting and moving heavy objects.
Safety is always a top priority in industries that use wire rope assemblies. Advances in technology, such as sensors and monitoring systems, could be used to detect wire rope damage or failure before it happens, reducing the risk of accidents. In addition, new safety features could be incorporated into wire rope assemblies, such as improved corrosion resistance, better fatigue resistance, and increased strength.
Wire rope assemblies are already a sustainable choice compared to other lifting and rigging options like chains and synthetic slings, but there is always room for improvement. For example, wire rope assemblies could be designed with eco-friendly materials like recycled steel or aluminum. In addition, the manufacturing process for wire rope assemblies could be optimized to reduce waste and energy consumption.
Artificial intelligence (AI) has the potential to revolutionize the way wire rope assemblies are used and maintained. One area where AI can be applied is in predictive maintenance. By analyzing data collected from wire rope assemblies, AI algorithms can identify patterns and predict when maintenance is required before failure occurs, allowing for more efficient and cost-effective maintenance schedules.
In the design process, AI can optimize wire rope assemblies for specific applications. By analyzing data on factors such as load, environment, and wear, AI algorithms can create optimized designs that maximize performance and durability while minimizing weight and cost. Finally, AI can be used to improve safety by identifying potential safety hazards and providing real-time alerts to operators. For example, sensors can be used to monitor the tension and stress on wire rope assemblies, and AI algorithms can analyze this data to detect potential issues and alert operators before a failure occurs.
Overall, these topics represent just a few areas where there is potential for significant improvements in wire rope assembly design and performance. As industries continue to evolve and new technologies are developed, we can expect to see new and innovative wire rope assembly designs emerge that meet the needs of a changing world.
An aircraft cable is a style of highly durable cable that is used for aircraft flight controls and other applications and is differentiated from normal cables by its diameter, stranding, and wires, which provide...
A push pull cable control is used for the transmission of multi directional precision control of mechanical motion. The many varieties of push pull cables or controls are adaptable to a wide range of applications and...
Stranded wire refers to thin bundled up wires that are compressed and covered up in insulating material. Stranded wires are more flexible thus making them very ideal for joining electronic circuit components in confined spaces where their bending...
Wire rope is a collection of metal strands that have been twisted and wound to form the shape of a helix with the purpose of supporting and lifting heavy loads and performing tasks that are too rigorous for standard wire...
Wire rope is constructed of multiple strands of wire that are twisted and braided together to form a spiral design or helix. Once the separate wires are shaped into a solid form, they become a single wire with greater strength because...
A bungee cord is a rope that is composed of two or more elastic strands coated with a woven fabric. It has hooks that are placed on both ends. A bungee cord is also known as shock cord and elastic cord...
Cordage is a series of intertwined fibers, strands, strings, or fabric that are joined by twisting or braiding to form a larger more formidable whole. The combination of the materials makes the final, larger strand stronger than its individual pieces...
Electric hoists are material handling equipment used for lifting, lowering, and transporting materials and products. They are powered by an electric motor and have a controller to adjust the lifting parameters...
A gantry crane is an overhead crane that has an overhead beam supported by freestanding legs and moves on wheels, a track, or rail system carrying a bridge, trolley, and hoist. Workshops, warehouses, freight yards, railroads, and shipyards use gantry cranes as their lifting solution as a variation of overhead or bridge cranes...
Rope is a collection of strands, fibers, piles and yarns joined together to form a strong and a large structure. These strands or fibers are either twisted or braided with one another to give high tensile strength to the rope...
A hydraulic lift is a device for moving objects using force created by pressure on a liquid inside a cylinder that moves a piston upward. Incompressible oil is pumped into the cylinder, which forces the piston upward. When a valve opens to release the oil, the piston lowers by gravitational force...
A jib crane is a lifting device with an arm or boom that extends off the main body of the crane to provide extra reach and has a lattice design to lower the weight added to a load. The design of jib cranes allows them to work...
A lift table is a platform capable of holding materials and raising, lowering, and adjusting them to any height to meet the needs of an application and the user’s requirements. Lift tables are supported by a strong, rigid, and stable base frame placed flat on the floor, in a pit, or equipped with casters or wheels...
An overhead crane is a type of heavy duty machinery that is capable of moving extremely heavy loads and equipment from one location to another in a safe and precise manner using the overhead space of a manufacturing facility. Due to the nature of the work they perform...
Scissor lifts are a type of manlift that is commonly used in construction and facility maintenance to raise employees and their tools to working heights. A power system and a control system make up the scissor lift...
A hydraulic system is based on Pascal‘s principle of fluid pressure, which hypothesizes that a change in pressure in a fluid is transmitted to all points of the fluid in all directions. With a hydraulic lift, an electrically powered pump pushes fluid into a cylinder at the base of a lifting jack system that lifts the platform up and down...