Bungee Cords
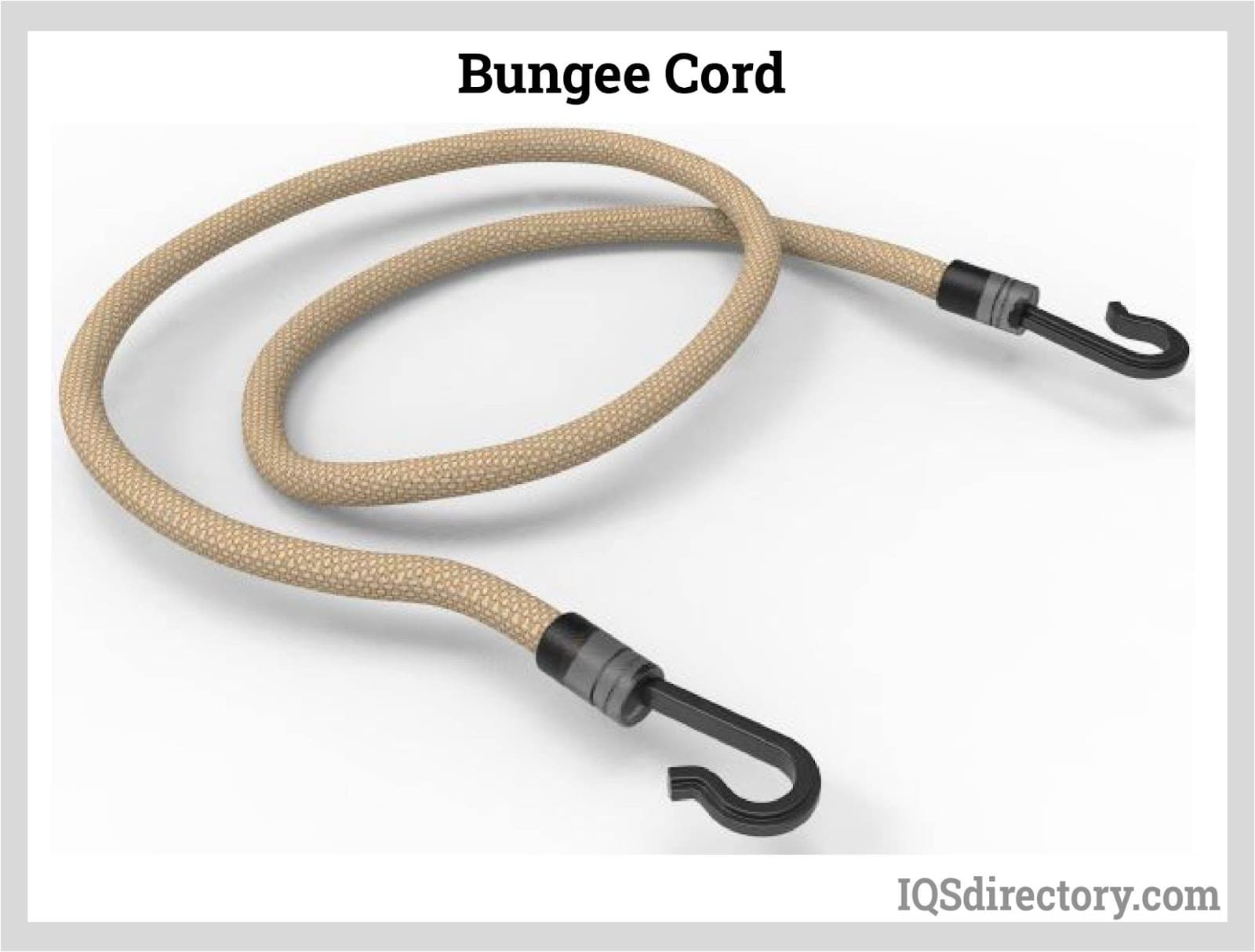
A bungee cord is a rope that is composed of two or more elastic strands coated with a woven fabric. It has hooks that are placed on both ends. A bungee cord is also known as shock cord and elastic cord...
Please fill out the following form to submit a Request for Quote to any of the following companies listed on
Here is everything on the internet you need to know about cordage.
You will learn:
Cordage is a series of intertwined fibers, strands, strings, or fabric that are joined by twisting or braiding to form a larger more formidable whole. The combination of the materials makes the final, larger strand stronger than its individual pieces. Cordage, also referred to as rope, is an ancient tool that has been used by sailors, farmers, and cattlemen for centuries. Its exceptional strength and versatility have made it an important method for securing, fastening, and hauling furniture and equipment.
Over the centuries, the design and processes used to produce cordage have gradually changed. The hemp, cotton, and thread of years ago has been replaced by synthetic materials, such as nylon and polypropylene, that are more durable.
The basic process of making cordage has not changed from its original form. When rope was made by hand, the strands of material were stretched for hundreds of yards, where one end of the strands were secured on hooks. To create rope, a wheel was turned that twisted the material into rope, a technique that was referred to as a "rope walk".
Over the years, the materials and methods of braiding or twisting rope has been modernized and mechanized with machines performing the functions of the "rope walk".
The two methods for creating rope are braiding and twisting. Though the final products look similar, there is a difference between the techniques.
Braided rope is produced by braiding together multiple strands that can be from eight or nine up to the hundreds. The three forms of the braiding process are hollow, solid, and double.
Twisted rope is made by twisting individual strands, which are twisted again into a larger, stronger rope. The main advantages of twisted rope is its low cost, ability to be stretched, and ease of splicing.
Rope manufacturing begins with fibers that are natural or synthetic. Natural fibers include hemp, sisal, cotton, flax, or jute. Though natural fibers do not have the resilience and strength of synthetic ones, they are still commonly used to make rope for ships and large hauling operations as well as household chores.
Synthetic fibers, which are stronger and more durable than natural fibers, are made from nylon, polyester, polypropylene, and aramid. Each of the synthetic fibers has characteristics and properties that make them more reliable since they can be used in hostile and harsh environments without being negatively affected.
Prior to feeding the fibers into the braiding or twisting equipment, they are lubricated and treated as well as cleaned. During this initial process, the fibers are straightened and spread apart by steel toothed combs. The process of combing creates a loose continuous ribbon of fibers referred to as a sliver.
The next step is to compress the sliver to prepare it for the twisting or braiding process. It is run through the rollers of a drawing machine that compresses the fibers. The finished material is wound onto a bobbin. At this point in the process, the yarn may be dyed to give it color.
The bobbins from the drawing process are placed on the creel. The ends of the yarn are fed through the holes in a plate to keep the strands apart and in proper relationship to each other. As they pass through the plate, they are fed into a compression tube that twists the strands before they are placed on a bobbin. In the simplified image below, the plate can be seen in the middle with the compression tube off to the left.
The bobbins from the forming machine are placed in a second braiding machine. When the yarn was braided in the forming machine, they were twisted in S and Z patterns. The Z pattern of twisting moves to the right, while the S pattern moves to the left. The different patterns are referred to as laid patterns. The difference in the patterns can be seen in the diagram below.
In the final braiding process, there may be eight strands, which consist of four S and four Z twisting patterns. One Z and one S are paired to make an individual strand. To make the final rope, the paired patterns are combined with other pairs to create a solid length of rope.
The rope cordage industry has taken the basic concept of the rope and developed a wide array of products that include common styles of rope to those that are specially produced for unusual and unique applications. Though it is common to think of rope as a simple strand of twisted fibers, in actuality, the type and design of rope is engineered for specific tasks.
One of the key factors for choosing a rope is to determine its working load limit and tensile strength, the amount of stress it can withstand before it breaks. The working load limit defines the amount of weight a rope can support.
Three strand twisted rope is the oldest form of rope and has been produced for centuries. It is a general purpose robe that can be used in several applications. Three strand rope is the easiest to splice and has excellent shock absorbency properties.
Solid braided rope is made from 9, 12, or 18 strands, which are braided using a lock stitch pattern. The construction of solid braided rope keeps the ends of the rope from unbraiding. It is very solid with or without a core.
Diamond braided rope can have 8 to 144 strands, depending how the rope will be used. The diamond name of diamond braided rope comes from the diamond pattern that is formed in the braiding process. The braid is formed by braiding the strands over and under in a circular pattern. The main characteristic of diamond braiding is its ability to firmly hold knots.
The double braid has a braid as the core with a second braid, like the core braid, braided over the outside. Over braids may be of similar material as the core braid or use a completely different one.
The initial use of rope was for the lifting and carrying of people and materials. Over the years, its usage has expanded into industrial applications. From the rapid growth of the rope and cordage industry, the Rope Access Trade Association (IRATA) and the Society of Professional Rope Technicians (SPRAT) have developed methods for training and certification for rope use and products.
Much of the work on bridges and buildings is inspected by remote devices with video cameras. Though this has proven to be a convenient method for doing inspections, it has been found that in-person inspections by technicians supplies more accurate information. High quality ropes are used to allow inspectors to move across surfaces and high altitude structures safely and easily.
There are varied uses for rope in the construction industry. One specific application is for specialized technicians attempting to reach inaccessible places on a project. Attaching workers to ropes and lowering them to hard to reach places is less expensive than constructing scaffolding and less time consuming as well as being a better method for utilizing resources. Highly trained specialists with advanced skills can safely reach inaccessible places in a short period of time.
Rope has been a standard part of rescue operations for centuries and provides access for rescuers to locations that may be otherwise inaccessible. Since rope is very dependable and does not conduct electricity as well as seldom being damaged by chemicals or water, it has proven to be one of the most reliable tools in rescue workers' assortment of options.
Though wire slings have become a very normal method for lifting heavy materials, it has been found that rope is just as reliable and a more economical solution to lifting operations. Rope slings have been engineered to be used with cranes, rigging, and other lifting mechanisms. They are safe, light weight, and highly reliable. Rope ensures the avoidance of injuries from snapping, recoiling, or dropping of loads from incorrect rigging.
The mining industry has used wire for underground operations for many years. The unfortunate outcome was wire rusting and developing fishhooks and kinks, which created unsafe conditions. Ropes and cordage have been accepted as a safer and stronger alternative to wire. The engineering expertise used to create ropes for mining makes them easier to see and longer lasting as well far more reliable.
The special quality of rope used for ocean work is its being pre-stretched to avoid it becoming elongated during use. Another unique feature, which would only apply to ocean work, is creating cordage or rope materials that are not susceptible to fish bites. One of the major problems of working on the ocean is salt water, which can cause any material to deteriorate. Rope designed for ocean work contains chemical protection that allows it to withstand the harsh conditions of being constantly in water.
As with other applications, rope has several uses for the military from securing equipment during troop movements to helping soldiers traverse rough terrain. Ropes can be used as a method for crossing rivers and other obstacles. For many years, it has played an important part of endurance training during basic training.
For as long as ships and boats have existed, ropes have been a staple tool. As with ropes used for work in the ocean, boating and shipping ropes have to be constructed of special materials that can withstand the harsh conditions and environment of the ocean. Cordage has been used to secure cargo, tighten hatches, and lift sails for centuries. Modern rope, made from synthetic materials, has the added feature of never unraveling and excellent elasticity.
Though much of the manual labor for agriculture production has been replaced by highly efficient machinery, there are still many applications that require the use of trope, which include loader wagon ropes, tedders, rakes, mowers, pulling ropes, poultry feeding systems, and feeding boxes. Unlike other industries, agriculture requires a different rope for each of the various applications, which are specially designed for tensile strength and endurance.
Industry relies on equipment and tools that are durable and long lasting. For this reason, rope has become an essential tool that has multiple applications and uses. In modern industrial operations, rope is used for sun protection systems, ascenders for wind tower operation, electrical tools, convertible top drives, deep drilling, helicopter operation, pipe access systems, and installation of components, to name a few. The list is very long and covers a wide spectrum of applications and processes.
Parachute cord, often referred to as paracord or 550, was originally designed for use as parachute lines. Recently, its use has expanded into other applications. It is made of 32 strands that are woven around a seven strand inner core and has a smooth outer finish. Paracord is made from nylon fibers that provide strength and endurance. Though it has been replaced by other materials for use with parachutes, it is still a staple tool for the military, which uses it for harnesses, rope bridges, and tree nets. The 550 name of paracord comes from its 550 lb. tensile strength.
For centuries, going back to ancient Egypt, rope has been made from natural materials such as plants and parts of animals. In the modern era, with the development of synthetic materials, rope has been made from nylon, polypropylene, Kevlar, and Vectran.
Hemp is a natural fiber made from the outer layer of the hemp plant. It is made by twisting together groups of fibers of the hemp plant into the form of a yarn, which is twisted with other yarn to form rope. Hemp rope is used for tying packages and securing various items and materials. It has become a staple for several industries from construction and sailing to communications and shipping.
Flax material is used for making hemp rope. It is strong, durable and a fine material for ropes. Flax ropes are stronger than those of cotton and jute, and also get stronger when wet. Flax is actually a plant which grows up-to 50 to 100 cm. When this plant is mature, it produces two colored flowers, white and blue. The fiber collected from the blue flowers is the finest one, but the fiber collected from the white flower is the strongest but a coarser one. Flax fiber is also used along with wool and cotton to produce clothing. Flax rope is actually a natural one so it is soft to handle, has resistance to friction burns and can be used in a variety of applications. Flax ropes are usually used in skipping ropes, gymnasium and in theaters etc.
Cotton rope is made from cotton yarn, which is twisted or braided into rope. Cotton ropes are soft, pliable, hold knots well, and are easy to handle. Cotton ropes are stretchy and flexible as compared to other natural fibers. However, cotton rope is not very durable and strong. It also has very low corrosion and heat resistance. Cotton ropes also lose their strength in sunlight. Cotton ropes are available in their original white color, with 3 or 4 strand configurations. Size range of cotton rope ranges from 4mm to 37mm. The largest size of cotton rope is known as elephant ropes. It is used for boating, horse halters and leads, camping equipment, towing, and securing materials for shipping.
Manila rope is made from natural fibers taken from the abaca banana plant. It is a form of hemp and is the strongest of the natural fibers. Manila rope is very durable, flexible, and resistant to damage from salt water. When manila rope gets wet, it shrinks. To overcome this disadvantage, it is soaked and dried before being sold.
Manila rope shrinks up-to 10-15% when it becomes wet therefore, if it gets wet while working, it should be dried thoroughly. Manila ropes are easy to handle and knot well. They have a poor resistance to acids and alkalis. Therefore, exposure to chemicals and water should be avoided. These ropes should be stored in a dry place to avoid any damage. Average available size of these ropes is 6mm to 50mm. Manila ropes are widely used in exercise climbing, art and craft, landscaping, outdoor decorations, swings and other farming work.
Sisal rope is made from the fibers of the agave sisalana plant that is found in Mexico. It has very stiff fibers that are excellent for making rope. In the production of sisal rope, the leaves of the plant are crushed to remove its fibers, a process that is known as decortication. Sisal rope is considered to be the most durable and long lasting of the fiber ropes since it is more resistant to rot than other fiber materials.
It is a strong fiber and just like manila, cordage oil is also applied to it to improve its water and friction resistance. Sisal is a leading material to make agricultural twines such as binder twine and baler twine. It has a great strength, durability, stretch ability, affinity for certain dyes, and its resistance to damage in salt water. All these qualities make sisal a best choice for rope making. Sisal material has a good grip and knotting ability as compared to other natural fibers. Sisal ropes can be damaged easily by exposure to weather. Sisal ropes are used for decorative and farming or gardening purposes.
The natural fibers for jute come from two varieties of jute plants, white and tossa. Tossa jute is soft, silky, and sturdier than white jute. Regardless, white jute is more often used to make rope. Jute is an edible plant that has been a food source in Asian countries for centuries. The fibers for jute rope come from the skin and stem of the jute plant that are removed by retting, a process that involves rotting the skin and stem in water. Industrial jute rope is treated with an oil that is referred to as jute batching oil.
Jute is a natural fiber which is eco-friendly and biodegradable. It is versatile in nature and can be reused easily. Its breaking strength is 20% less than that of manila, with a limited capacity to stretch. This less stretching and a good resistance to heat makes jute ropes sturdy and enduring. Jute can be damaged easily by moisture. It should be kept in dry places. Jute ropes are made from natural jute fiber and are available in 3 and 4 strands with Z and S twist directions. Jute ropes are widely used in towing, home gardens, steel wire ropes, transportation industry, and packing.
Polypropylene is the least expensive of the synthetic rope materials. It has excellent insulation characteristics and floats. Polyproplyene‘s resistance to rot and mildew makes it perfect for use in water applications. It is a polymer that is resistant to the effects of solvents, bases, and acids with a melting point of 170° C. Rope made from polypropylene is made from a continuous filament that is twisted or braided into rope.
These ropes retain their shape even if these are bent or flexed. Just like nylon ropes, these ropes are also rot proof and have a very good resistance to abrasion, acids, alkalis and other chemicals. Polypropylene ropes also show resistance to marine growth and mildews. When this rope is not in use, it is recommended to keep it away from sunlight to avoid any damage. It is a general purpose rope and comes in yellow color. It is used in mooring, dock and anchor lines. Polypropylene rope is also used in boat lines, trampolines, pool barriers, builder lines, public utility and for many household, farm, and industrial applications.
The benefits of polyester rope include its resistance to UV rays, heat, and abrasions, which makes it more expensive than other synthetic materials. Polyester has the same appearance as nylon and comes in very fine fibers. It has strength that is comparable to nylon, and does not stretch, which is minimized by pre-stretching. Polyester has a melting point of 240° C with low creep under load properties.
Polyester fiber has excellent resistance to chemicals, abrasion, and sunlight. It is also easy to splice even with nylon, stainless steel, or galvanized thimbles. Polyester rope is used for mooring, rigging, industrial plant use, fishing net and bolt sling along with hawser. It is also used in anchor lines, fender, and fender lines.
Kevlar has high strength, exceptional stiffness, toughness, and thermal stability. One of the qualities of Kevlar that makes it applicable for specialized applications is that it gets stronger at subzero temperatures. Since it doesn‘t stretch, it is the first choice for jobs that require stability. It is used for winch lines, mooring lines, and extreme temperature conditions.
Nylon is one of the strongest synthetic fibers with exceptional elasticity and abrasion resistance, which makes it long lasting. It is resistant to UV rays, rot, mildew, and chemicals. Since nylon rope is so durable, it has found use as towing lines, anchor lines, and pulleys. Nylon rope retains its flexibility regardless of the amount of use it gets, which makes it ideal for tie downs and knots.
Nylon rope is easy to handle, highly elastic and has a characteristic called memory. Memory of nylon rope means that when it is stretched, it returns back to its original position. Nylon rope is used in many applications because it is a trustworthy one. However, this rope is widely used in mooring lines, towing slings, fishing, utility ropes, safety lines and as industrial slings.
HMPE has exceptional strength but is lightweight with excellent flexibility and stability. It is capable of supporting heavy loads without any signs of wear or possible tears. Since HMPE ropes can float, they are much safer than other synthetic ropes. They have very low elongation and stretch properties, which makes them easy to handle during critical and hazardous times. HMPE ropes are 7 to 9 times stronger than steel, by weight, and 3 times stronger than polyester of equal weight with a high strength to weight ratio.
Vectran is made from a liquid crystal polymer (LCP) and has exceptional strength and rigidity with a tensile strength of 26 grams/denier, which makes it five times stronger than steel and ten times stronger than aluminum. It is resistant to abrasion, flex fatigue, and chemicals with an excellent thermal stability when exposed to cryogenics and high temperatures. For modern industrial use, Vectran is unaffected by radiation and microwave energy with minimal creeping and shrinkage.
Dacron rope is made from polypropylene and Dacron plastic fibers, which are twisted into strands and braided. Since it is made from the combination of two materials, it is often referred to as combination rope. Dacron rope is flexible as well as fracture, heat, abrasion, and ultraviolet ray resistant. It is used in applications where strong durable rope is required to withstand extreme weather conditions and high impact, which include sailing, climbing, workouts, and roof construction.
There are three main factors that determine the type of rope that is needed for a job, which are length, diameter, and workload strength. Each type of rope is specifically designed to perform a certain job and function. When deciding on a rope, it is important to consider these factors especially in situations where the rope will be used as a safety harness or work tool.
Each type of rope, synthetic or natural fiber, has a breaking strength and safe working load limit. The standard used to determine natural rope strength is the breaking strength of manila rope, which is used to compare all other natural fiber ropes. Synthetic ropes have comparison factors that are also compared against manila rope. To determine the breaking strength of manila rope, the circumference of the rope is multiplied by 900 lbs.
The two factors used to determine rope strength are its tensile strength and working load strength. Though these terms may be used interchangeably, they actually refer to two different qualities of rope strength.
The choice of the diameter of a rope is determined by how maneuverable it is, the ease of handling it, and comfort and safety. Thicker rope is normally the first choice since it has greater strength. Larger diameter rope distributes pressure creating a sustainable bondage. The problem with increasing the diameter of rope is that it gets stiffer as it increases, which can be a complication for certain jobs.
To determine the length of rope, a common method is to pull out four full arm lengths of rope from armpit to fingertip and multiply it by four. This method has been used for centuries and can give a good approximation of the length of rope needed for a particular job. For industrial applications, the process involves more precise calculations using calibrated measuring devices.
The main factors in choosing a length of rope is the number of obstacles the rope will have to traverse and its flexibility. Longer ropes tend to be heavier, have a larger diameter, and are stiffer, which makes extending them to their full length an involved process. Most engineers use mathematical calculations in choosing the right rope for the application.
The work life of a rope is very much dependent on how it is maintained. Each type of rope and their fibers have to be treated according to their specifications and guidelines. Certain general parameters can serve as guidelines for enhancing rope usage.
The first step in ensuring the longevity of any tool is regular inspections. Though rope may be viewed as a common or secondary tool, it still requires the same considerations as any other tool and should be thoroughly inspected prior to being used. This will guarantee the safety of workers and operations. In the case of safety operations such as construction work, military operations, and search and rescue, inspection of tools, especially ropes, is a common practice.
The working load of a rope should never be exceeded and is normally provided in the product description. All work for a rope must be a straight pull and not from the side or on an angle since those operations can severely impact a rope's work load limit.
Hooks, links, or shackles need to be appropriate for the fibers of the rope and its size. They must be properly installed and have the same working load as the rope. Misaligned components that do not match the workload can severely damage a rope and undermine its usefulness.
Shock loads involve rapidly pulling or jerking on a load or allowing it to free fall, which increases the amount of force placed on a rope and can cause it to overload and exceed its working load limit. Applying a shock load to a rope can radically exceed the ropes design and specifications.
All types of rope, even it is abrasion resistant, can be damaged by rough edges, sharp surfaces, and corners. If a rope is attached to a hoist, winch, or drum, it is important that the surface of the equipment be smooth, clean, and free of harmful materials such as metal filings, wood chips, or dust. Devices that wind rope must rotate smoothly and be the correct size for the rope.
Synthetic ropes can lose 50% of their strength if stored in temperatures that exceed 140° F. When a rope is being wound or winched, it may slip or surge, which will cause friction and overheating, which leads to a loss of tensile strength.
The major use of ropes is for lifting and pulling. A part of these operations includes tying and bending of ropes. The fiber content, material, and design of a rope determine how easily these operations can be performed. Ropes can lose half their strength when they are constantly knotted and bent. In most cases, the best preventative is to check the manufacturer‘s specifications.
Regardless of the type of rope, they should be stored in a clean and dry location out of direct sunlight and extreme heat as well as off the floor on a rack or shelf. To offer the right conditions, the storage place should have proper ventilation. For best results, avoid storing rope on concrete or dirt floors as well as away from chemicals.
When preparing to store a rope, it should be coiled properly. The best method is to coil it around a reel, which can be handheld or on wheels. Proper coiling of rope allows the fibers to rest properly and avoids the possibility of any ambient stress. Using a reel can prevent damaging entanglements.
Sharp bends in a rope decreases its strength and can lead to damage or failure. When a component is added, the bending radius should be more than three times the rope‘s diameter. For the best results, the ratio of the component to the rope‘s diameter should be 5 to 1. Thimbles are designed at a 3 to 1 ratio.
Rope is normally shipped on reels for ease of transit and protection. It is important to take care when removing a new rope from its reel. For best results, the reel should be mounted on a pipe for free movement and should never be unreeled while lying on the ground or in a stationary position.
The ends of ropes can be protected by being knotted to avoid unraveling. In some cases, this cannot be avoided. Such damage can easily be repaired by removing the damaged end and sealing or knotting it. When the middle of a rope is damaged, it should be immediately put out of use. Regardless of any efforts to repair it, the tensile and load strength of the rope will be diminished.
Any tool that is used for industrial or manufacturing purposes has an oversight organization for the protection of workers and to guarantee quality. In the case of rope, these organizations include the American Society for Mechanical Engineers (ASME), International Organization for Standards (ISO), the American Cordage Institute, Rope Access Trade Association (IRATA), the Society of Professional Rope Technicians (SPRAT), and the American Society for Testing and Materials (ASTM).
The ISO has three standards for rope that were established in 2010.
ASME volume B30.30 describes the proper construction, selection, installation, attachment, testing, inspection, maintenance, repair, use, and replacement of wire rope, hybrid rope and synthetic fiber rope for lifting operations. B30.30 is a subsection of B30 and is written for owners, users, employers, and producers of rope products.
The ASTM‘s standards specify the properties for ropes for rescue systems and the methods that should be used to test them. It outlines the drop test designed to simulate the worst possible conditions for rope usage.
The American Cordage Institute is an association of manufacturers, producers, and suppliers that has developed standards for fiber rope. It includes a description of all rope products, raw materials, machinery, and suppliers. The American Cordage Institute develops standards and practice for proper manufacturing of fiber rope and their use.
The IRATA provides recommendations and guidance for the safe use of rope. It trains experts regarding rope practices and provides an outline and description of proper rope use. One of the main concerns of the IRATA is the use of ropes when working at heights or in hazardous conditions.
The SPRAT was founded in the early 90s due to the concern regarding the growing amount of work being completed at dangerous heights. The original focus of the organization was on rescue operations. As the use of rope has expanded into construction and manufacturing, the SPRAT has broadened its view to include any operations that involve working at extreme heights. It has a set of standards and legislation to assist companies regarding rope access operations.
A bungee cord is a rope that is composed of two or more elastic strands coated with a woven fabric. It has hooks that are placed on both ends. A bungee cord is also known as shock cord and elastic cord...
Rope is a collection of strands, fibers, piles and yarns joined together to form a strong and a large structure. These strands or fibers are either twisted or braided with one another to give high tensile strength to the rope...
An aircraft cable is a style of highly durable cable that is used for aircraft flight controls and other applications and is differentiated from normal cables by its diameter, stranding, and wires, which provide...
Electric hoists are material handling equipment used for lifting, lowering, and transporting materials and products. They are powered by an electric motor and have a controller to adjust the lifting parameters...
A gantry crane is an overhead crane that has an overhead beam supported by freestanding legs and moves on wheels, a track, or rail system carrying a bridge, trolley, and hoist. Workshops, warehouses, freight yards, railroads, and shipyards use gantry cranes as their lifting solution as a variation of overhead or bridge cranes...
A jib crane is a lifting device with an arm or boom that extends off the main body of the crane to provide extra reach and has a lattice design to lower the weight added to a load. The design of jib cranes allows them to work...
An overhead crane is a type of heavy duty machinery that is capable of moving extremely heavy loads and equipment from one location to another in a safe and precise manner using the overhead space of a manufacturing facility. Due to the nature of the work they perform...
A push pull cable control is used for the transmission of multi directional precision control of mechanical motion. The many varieties of push pull cables or controls are adaptable to a wide range of applications and...
Stranded wire refers to thin bundled up wires that are compressed and covered up in insulating material. Stranded wires are more flexible thus making them very ideal for joining electronic circuit components in confined spaces where their bending...
Wire rope is a collection of metal strands that have been twisted and wound to form the shape of a helix with the purpose of supporting and lifting heavy loads and performing tasks that are too rigorous for standard wire...
A wire rope assembly is composed of wire rope and end fittings, terminals, or lanyards that are attached to various parts of the wire rope such that the assembly can be used to lift, hoist, and move loads. The various types of...
Wire rope is constructed of multiple strands of wire that are twisted and braided together to form a spiral design or helix. Once the separate wires are shaped into a solid form, they become a single wire with greater strength because...