Stranded Wire, Braided Wire, and Wire Strands
Introduction
This article will take an in-depth look at stranded wires, braided wires, and wire strands.
The article will bring more understanding on topics such as:
- Principle of Stranded Wire, Braided Wire, and Wire Strands
- Types of Stranded Wire, Braided Wire, and Wire Strands
- Applications and Benefits of Stranded Wire, Braided Wire, and Wire Strands
- And Much More…
Chapter 1: Principle of Stranded Wire, Braided Wire, and Wire Strands
This chapter will discuss what stranded wires, braided wires and wire strands are, their construction, and how they function.
What is a Stranded Wire?
Stranded wire refers to thin bundled up wires that are compressed and covered up in insulating material. Stranded wires are more flexible thus making them very ideal for joining electronic circuit components in confined spaces where their bending and twisting capabilities can be put to use.
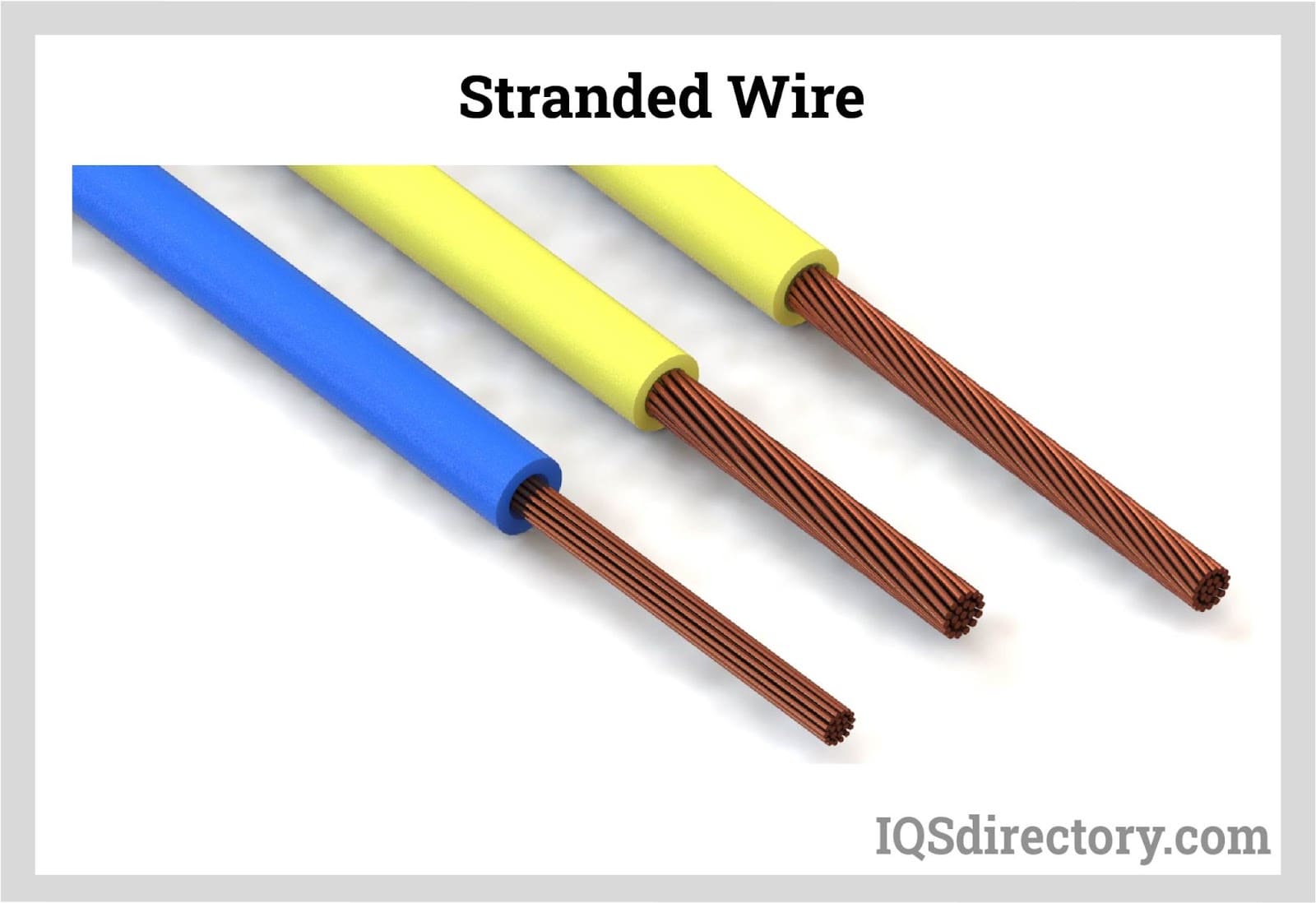
Unlike solid wires, stranded wires are very flexible and are malleable and cannot be broken easily.
What is a Braided Wire?
Braided wire is a jersey-like shielding built around a cable to shield the wiring from electromagnetic interference and to improve its mechanical strength.
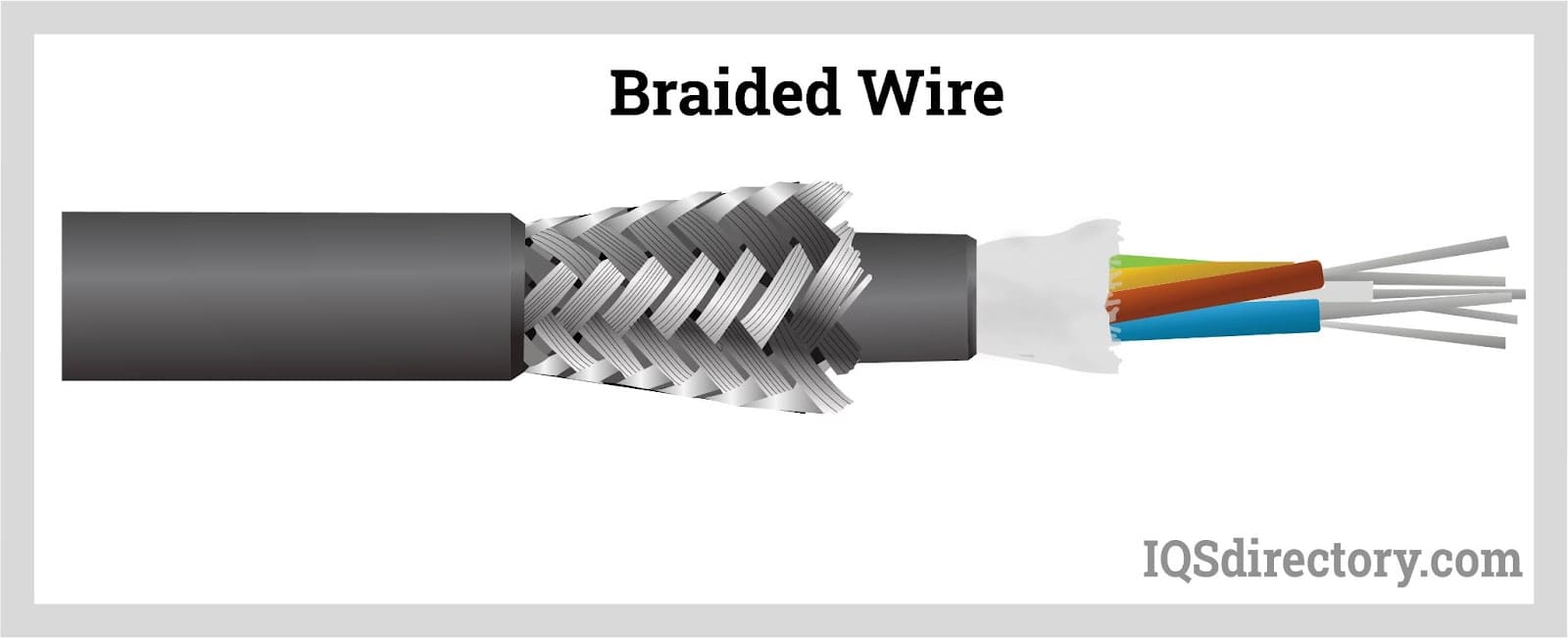
The shielding is made up of numerous tiny wires tightly woven in a standard mesh tabular formation around the conductor. In some designs, it can be flattened to achieve the desired width. A thin insulating layer covers the braid and other internal components of the cable.
What are Wire Strands?
A wire strand is when wires are wound up concentrically in a helix. The strands are wound around a central wire and then around the core.
Wire strands can be wound in varying numbers of configurations. The more the strand counts the more flexible the wire will be. The strands can be made from materials like stainless steel and some from precious metals like tungsten, gold, and silver.
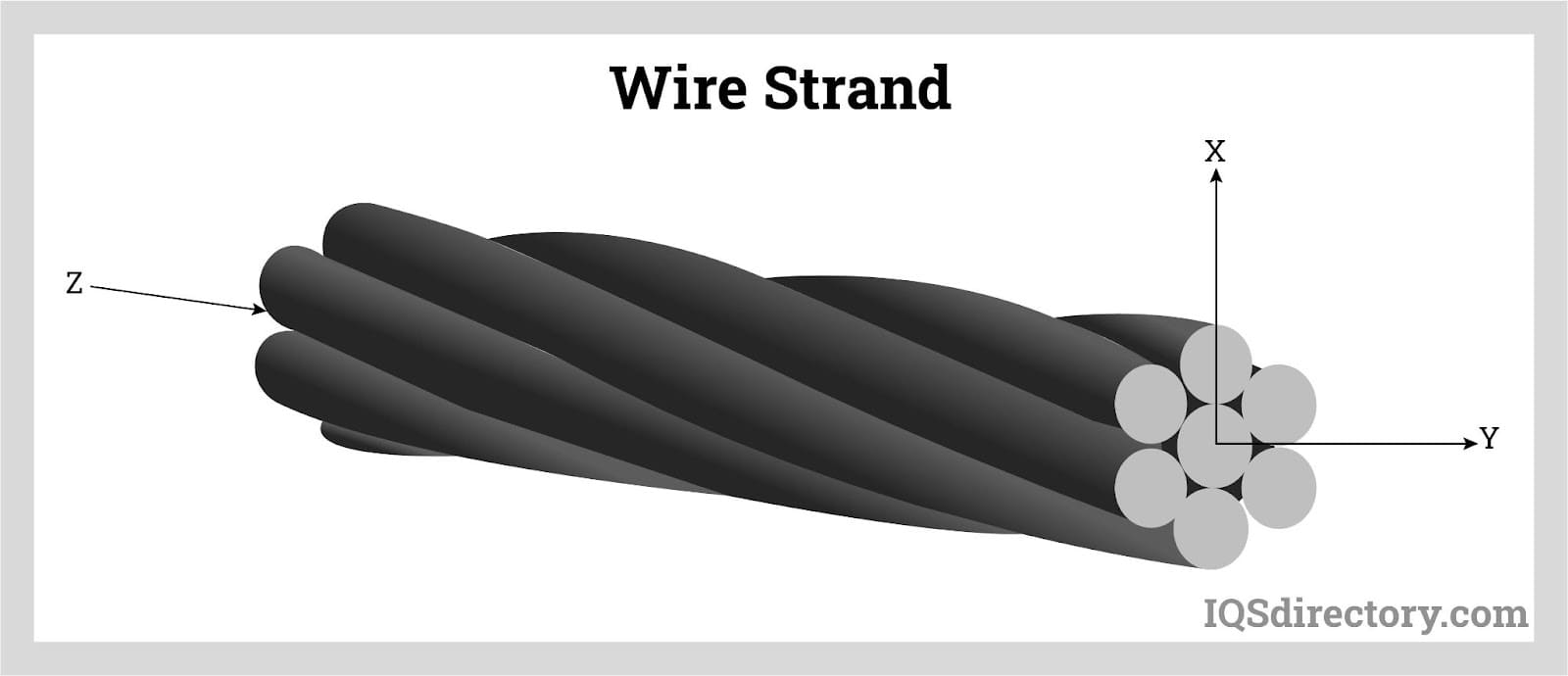
Functioning of Stranded Wire, Braided Wire, and Wire Strands
The functioning of these wires involves:
Stranded Wire
Stranded wires are commonly used as electrical conductors in transmission and distribution systems.
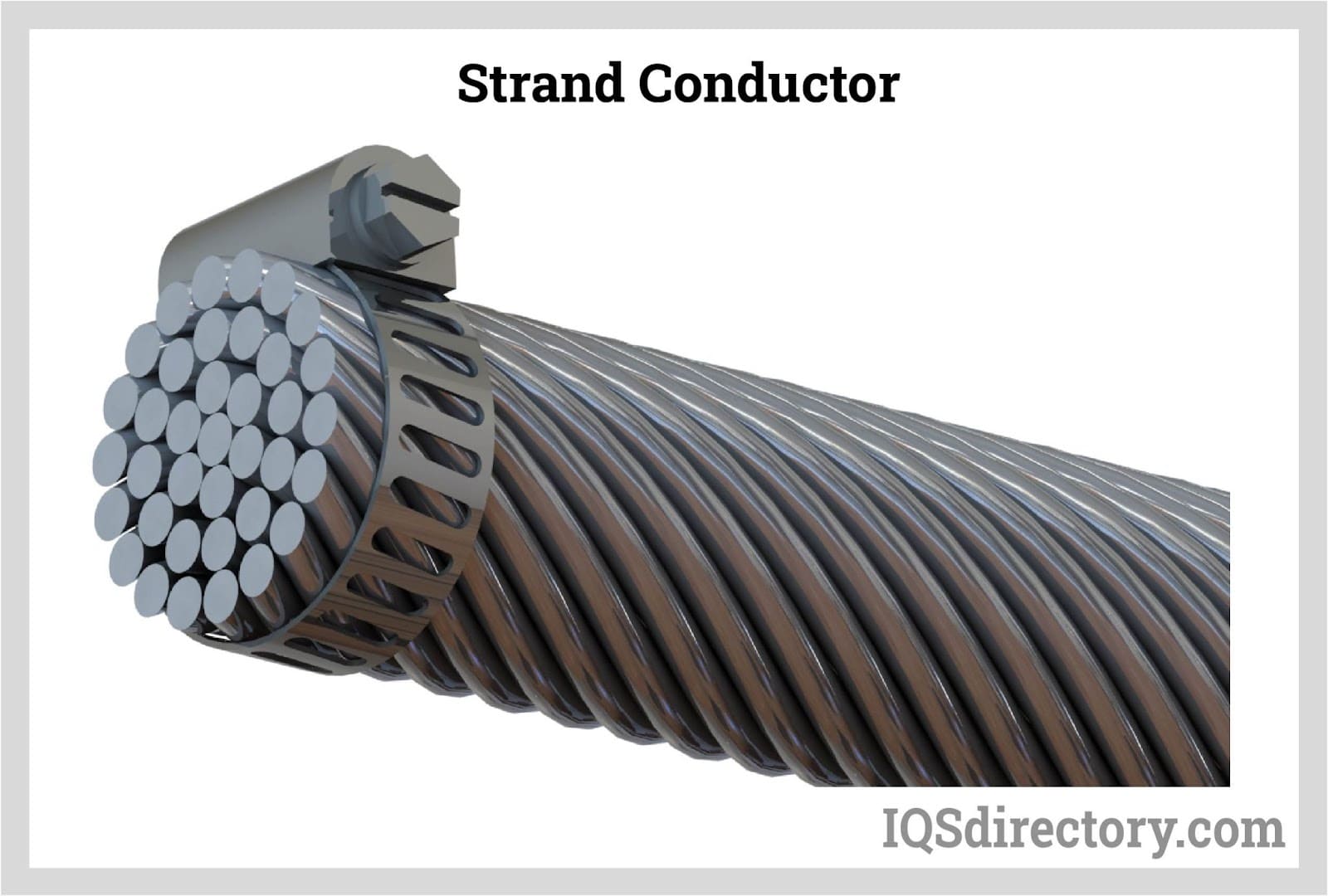
As shown in the diagram above, the center of the strand is made of a steel conducting material that contributes to the stranded conductor’s high tensile strength. Aluminum is used to make the external bundling wires and they aid in improving the conductivity of the wires. All this is done to make the whole conductor flexible.
A single solid conductor will not be as flexible as would be a stranded conductor and transportation would be challenging. Consider transporting a single conducting wire of 100m. A stranded conductor can be coiled and packed easily for transportation.
Facts on Stranded Conductors
The following are some known facts to be highlighted about stranded conducting wires.
- A stranded conductor is very flexible such that it can be coiled easily packed and be transported over a long distance.
- The flexibility of any conductor will increase with the number of strands.
- Stranded conductors are formed by winding the strands together in several layers.
- The several strands are laid one on top of the other in a helical format and this process is commonly known as stranding.
- For the stranding to hold, the successive layers are laid opposite the direction of the preceding layer. This means if the first strand is twisted in a clockwise fashion the strands of the following layer are twisted in an anticlockwise fashion and so on.
- The formula gives the total number of strands of any given conductor. N = 3 x2 - 3 x + 1, Where N refers to the total number of strands in the conductor
- The diameter of the conductor is calculated by using the following formula D = (2 x – 1)d, Where D refers to the diameter of the given conductor and d refers to the diameter of each strand.
Other common uses of stranded wires are AC line cords, computer peripherals wire connections, musical instruments, cables used in moving machinery, and equipment.
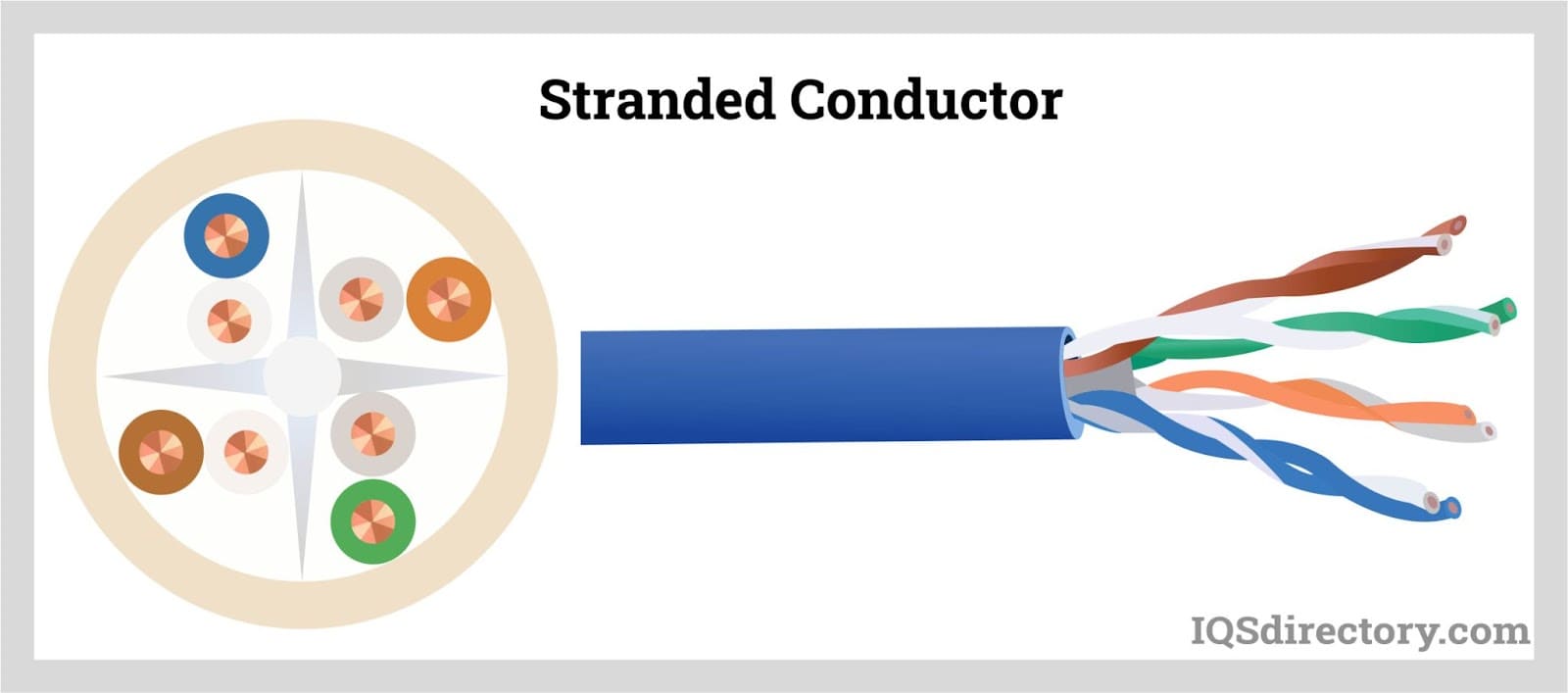
Braided Wire
Braided wires are commonly used as electromagnetic shielding and in noise reduction cables
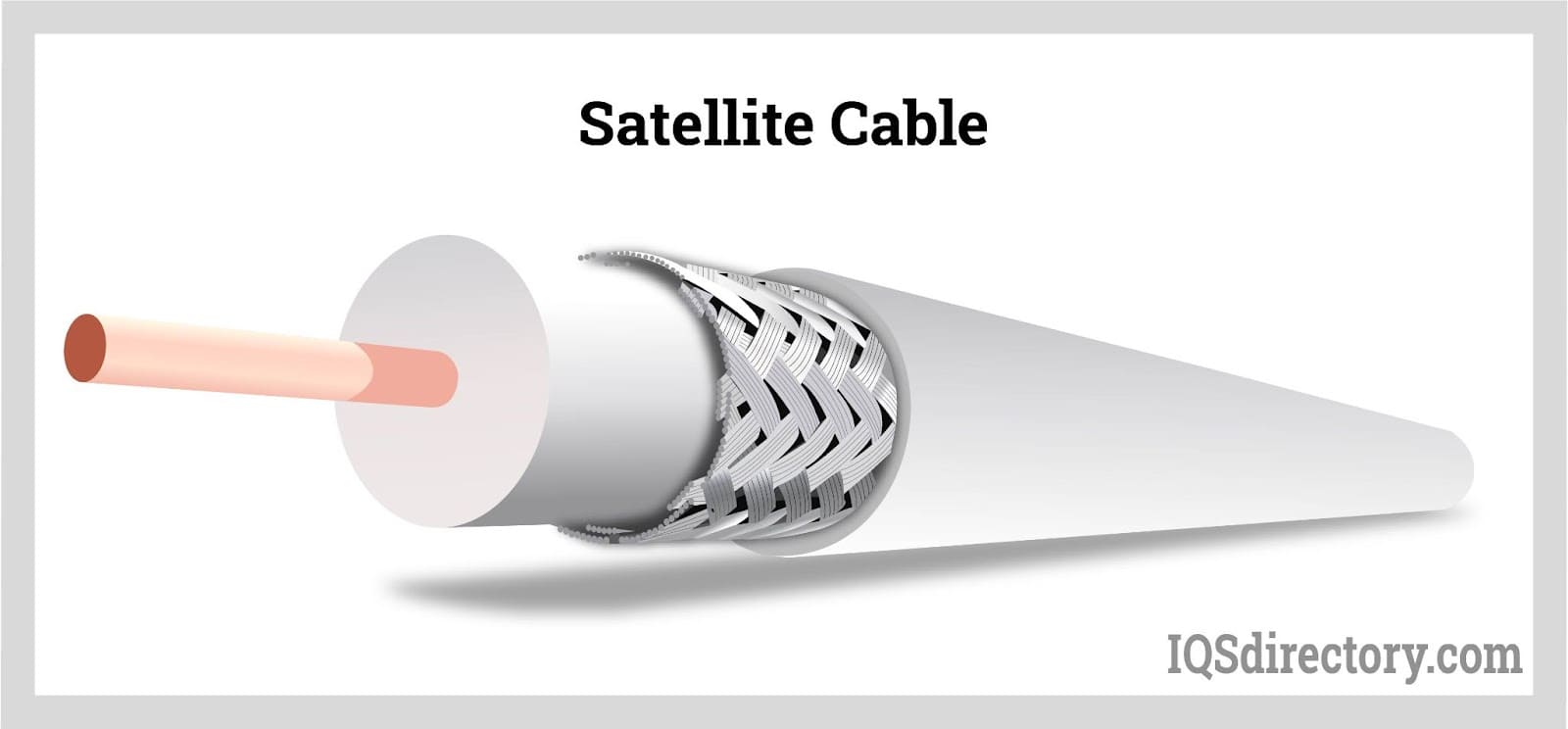
Braided cables are mostly used in satellite cable connections where their main property of shielding interference and countering electromagnetic interferences is put to use.
Wire Braid Manufacture
Wire braids are manufactured from copper, which can be bare or braided depending on the intended use. Silver- or nickel-plated copper are common viable options but tinned copper is mostly used because of its improved conductivity and its resistance to corrosion. The braided wire begins as multiple strands of thin and stretchy wire. The wires are then wound on rotating spools that rotate fast in round patterns around a core creating a weave and shaping the whole thing into a flexible and sturdy braid.
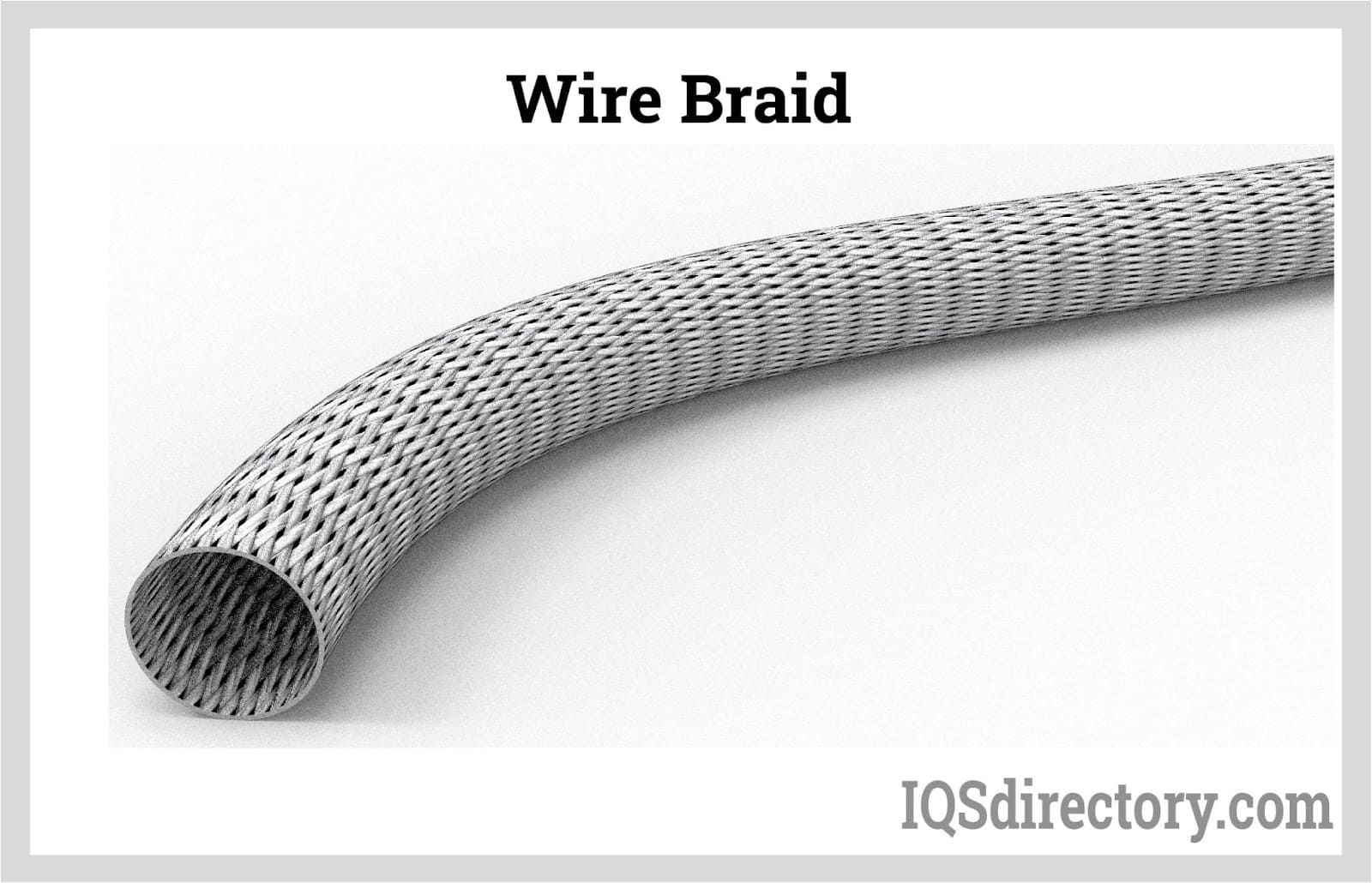
The size of the braid of wire depends on the number of carriers the machine has. Usually there are sixteen, twenty four or forty eight carriers in a machine. Individually each carrier has a bobbin which can take up as many as sixteen strands of wire. The construction is typically inscribed as three numbers (such as 24-4-36) where:
- 24 is the number of carriers
- 4 is the number of wires per carrier
- 36 is the AWG of each wire.
A plane braided wire starts as a round braid and is made flat by a force roller which will be on the capstan. A capstan is a huge roll that pulls the line through the braiding mechanism. A flat braid is as stretchy and strong as round braids, but it has a greater surface extent, which means it has less resistance when an electric current passes through it.
Wire Strands
The wire strands are wound up concentrically in a helix.
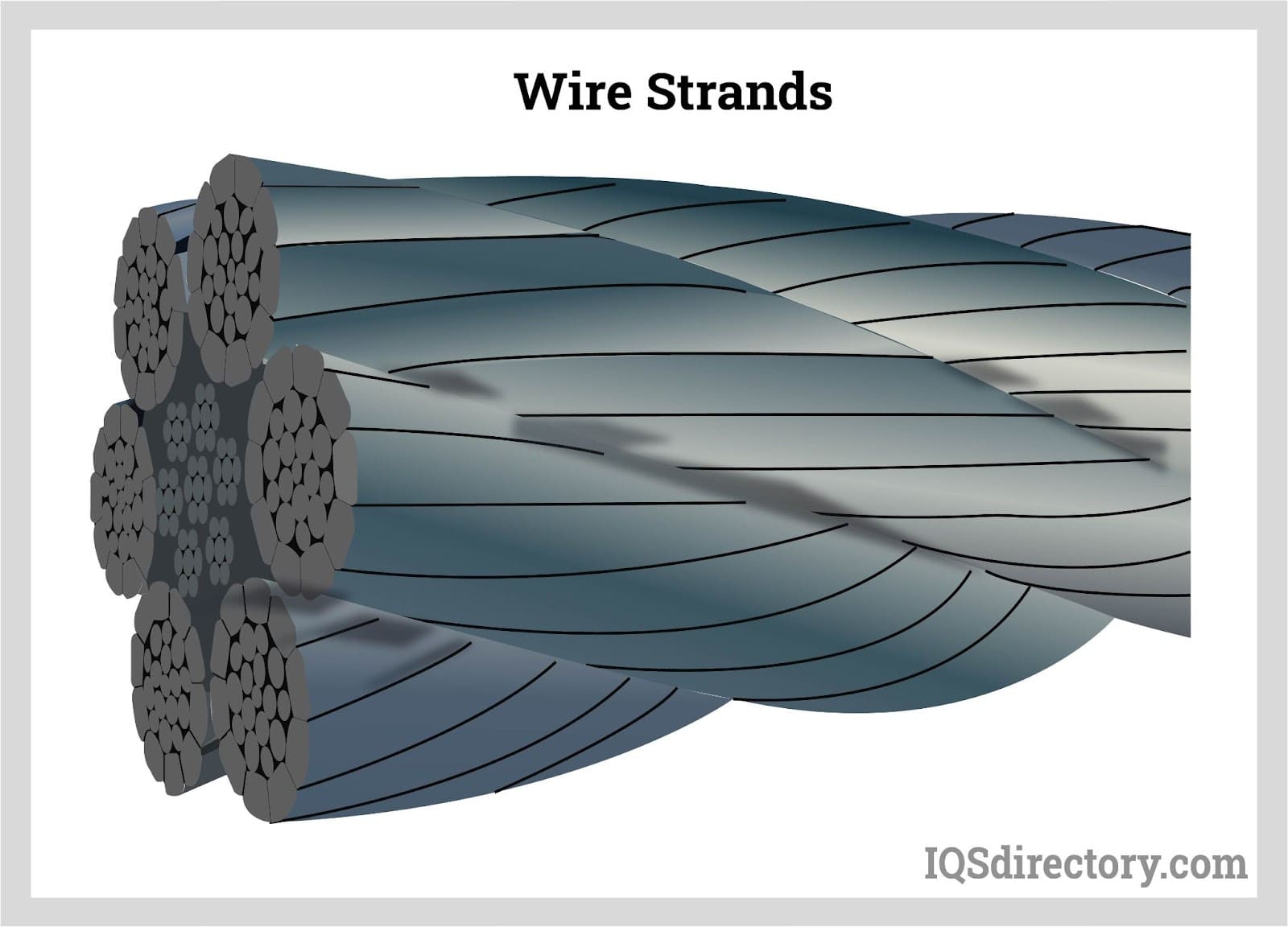
Manufacture of Wire Strands
Wire rope is made up of wires, wire wound strands, and a core in the middle. The wire centers are made in 2 unlike forms. The most frequently used is a wire cord of appropriate size to act as a core. It is known as an independent wire rope core and commonly referred to as IWRC.
The other type of wire core is called wire strand structure or WSC. It includes several wire strands and may have the same structure as the main line strands. A wire rope is composed of strands and each strand is composed of one or more pieces of wires.
Chapter 2: Types of Stranded Wire/Braided Wire/Wire Strands
This chapter will discuss the different types of stranded wire, braided wire, and wire strands.
Types of Stranded Wires
Though the numerous small strands of wire bundled together make a flexible conductor which can be used for various uses. The strands can be arranged into a variety of symmetrical arrangements to meet exact design necessities for any device or request. Common types of stranded wire include the following.
Concentric Strand
This is a common wire arrangement. Concentric stranded wire is a conducting material that consists of a middlemost wire encapsulated by one or more coatings of helically arranged wires. The conductors are organized in concentric circles and with each layer after the first one consisting of six wires more than the previous layer. Concentric stranded wire arrangements decrease the necessity for filler material. The wires are bunched together firmly to uphold the wire’s form and help increase conductivity.
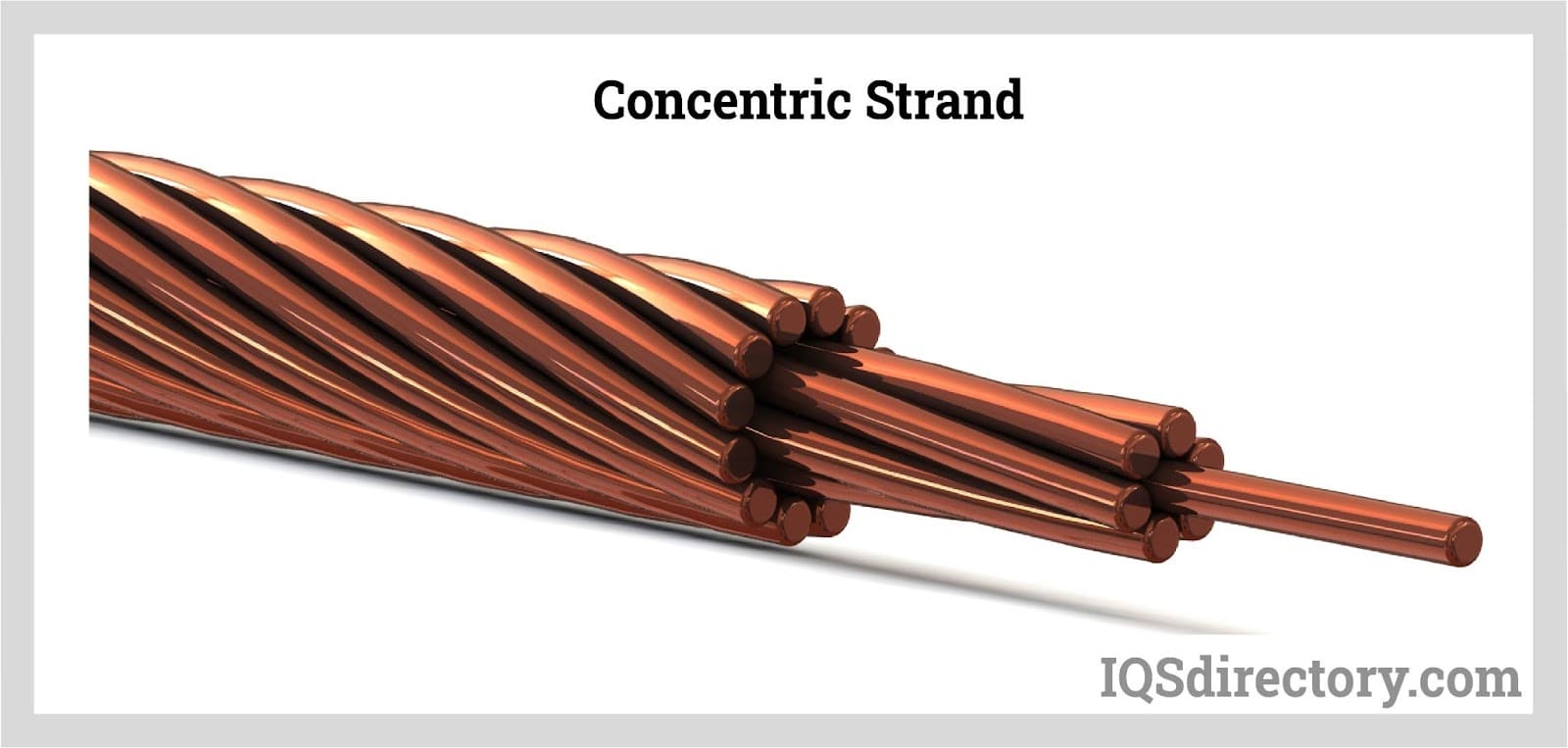
Bunch Strand
These stranded wire arrangements don`t have an exact geometry. The strands are bunched and some poised together in a similar direction. The alignment of wires is twisted together firmly to ensure they stay uniformly packed. The acceptance of bunched stranding entails their toughness and elasticity. The high malleability ensures them best for bending around constricted corners.
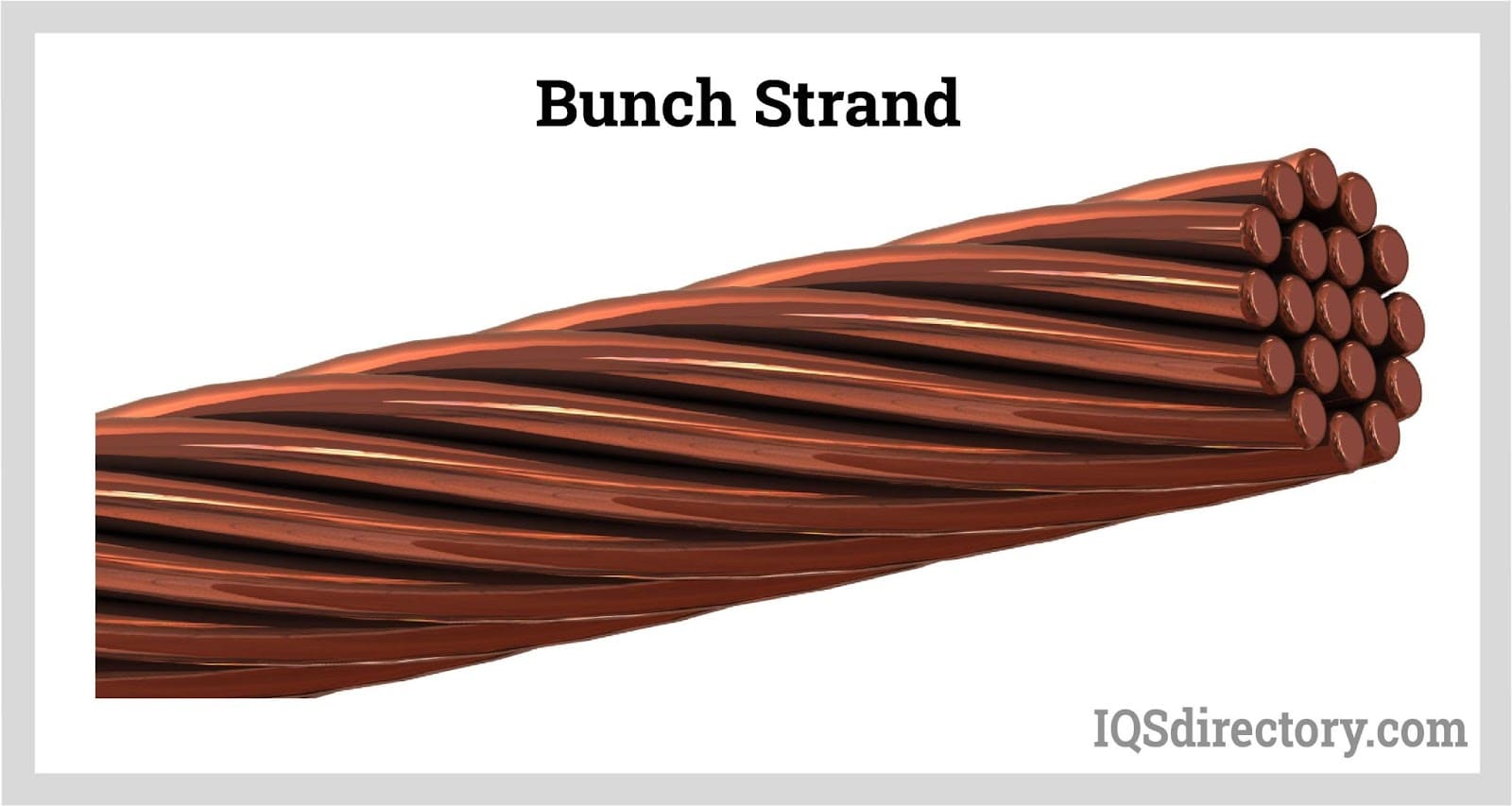
Rope Strand
Rope stranding sets wires together into numerous small bundles. Individually, each component strand is self-stranded and then organized into concentric rings to create a rope-like cable. The roping improves flexibility. This permits greater movement in use that requires frequent moving in multiple directions. Bigger gauge wire can be used with rope strands and it adds to the toughness and functionality of the wire.
Compact Conductor
A compact stranded conducting wire is often used where lesser diameter applications are needed. The separate strands of a bigger, round conductor are organized in layers in the same way. Once the bundle is set, they are compressed to take out all of the trilateral airspaces between the strands. The result is a much lesser finished conductor without airspaces and yet with the same extent of conductor cross section.
Braided Wires
The most common resources used for braided wire comprise tinned copper and silver-plated copper. Other materials that can be used are nickel-plated copper, gold-plated copper, pure silver, pure nickel, and gold alloys.
The electromagnetic waves range from signals bouncing to and from our phones, radio waves, and even natural sunlight. Data mediums require shielding to reduce data interrupts and losses. Specially woven metallic wires deflect the interferences so that data transfers are smooth.
Braided Wire and Foil Shielding Differences
Foil shielding is a metal tape used as a substitute for braided wire. This type of covering offers exceptional protection against high frequencies and is very cheap compared to braided shielding. Despite being cheap, it tends to fold and break because it lacks lattice reinforcement.
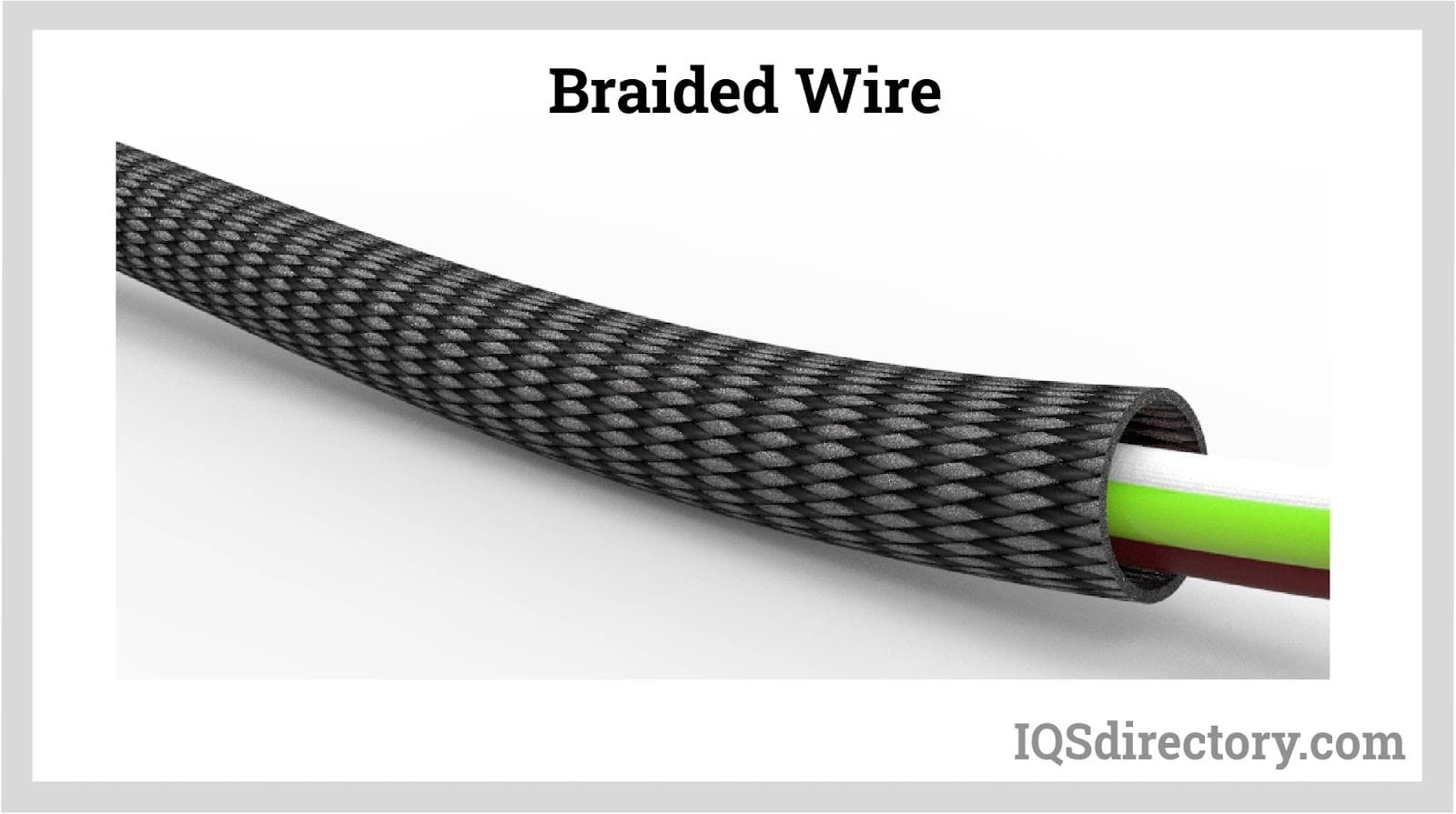
Wire Strands
The different wire strands include:
Wire and Cable Strand
Strands are the products of the stranding procedure, where wires or cables with a certain cross section are arranged and twisted together to create an electric conductor having a greater cross section. The objective is to improve mechanical properties in terms of flexibility, vibration resistance, and how easily it can be used in preparation for the following stranding or padding and sheathing process.
Layer length and the twisting direction depict the strand definition. There are two possible twist orders: left-hand and right-hand lays and are usually shown with S and Z respectively.
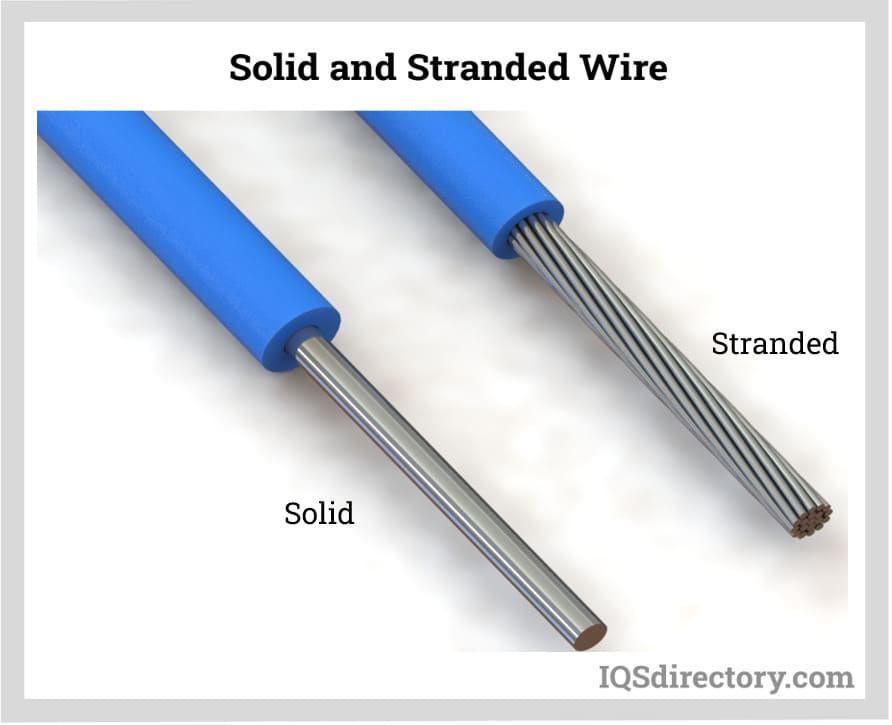
The strands can be separated into three different categories depending on their structure:
Bunched Strand
Bunched strands are packs manufactured in one phase with single wires or huddled multi-wires. The structure is uneven and the lay direction could be S or Z. This type of strand has the position of each of the individual wires not clearly defined. The exterior surface is irregular and the wire diameter and roundness are usually not accurate. This type of strand is not appropriate for a thin-wall lining process. This bunch is suitable for bendy or stretchy cords, building cables, and control cables.
Concentric Strand
This type of strand has a steady regular construction having a symmetric number of wires of (1 + 6 + 12 + 18 +24 + 30). The conducting material has 7, 19, 37, 61, or 91 wires. Concentric strands can be separated into two categories namely: True concentric types and the unilay types. True concentric kinds have different lay orders of the consecutive layers from inside to outer layers while unilay types have even lay directions. Common characteristics of all concentric conductors are the accuracy of the outer layer surface and the accuracy of the conductor’s diameter. This strand is mainly suitable for thin-wall insulation process that comprises of high-quality insulation materials.
Semi-Concentric Strand
In this type of strand, there is a regular arrangement but there is no symmetric number of wires (2 + 8 + 4; 3 + 9+ 16) as the concentric strand. The outside layers are regular about a central wire and the outside surface is regular. These strands are appropriate for thin-wall insulation.
Semi-concentric and concentric stranded conductors can be compressed with rollers or dies to get a very smooth exterior surface with the least conductor outer diameter, thereby reducing the insulation material to be used in the insulating process.
The term strand refers to the mean of an assembly of 7, 19, or 37 clusters or concentric strands in an even construction set. These are referenced as rope lay bunch stranded or rope lay concentric stranded.
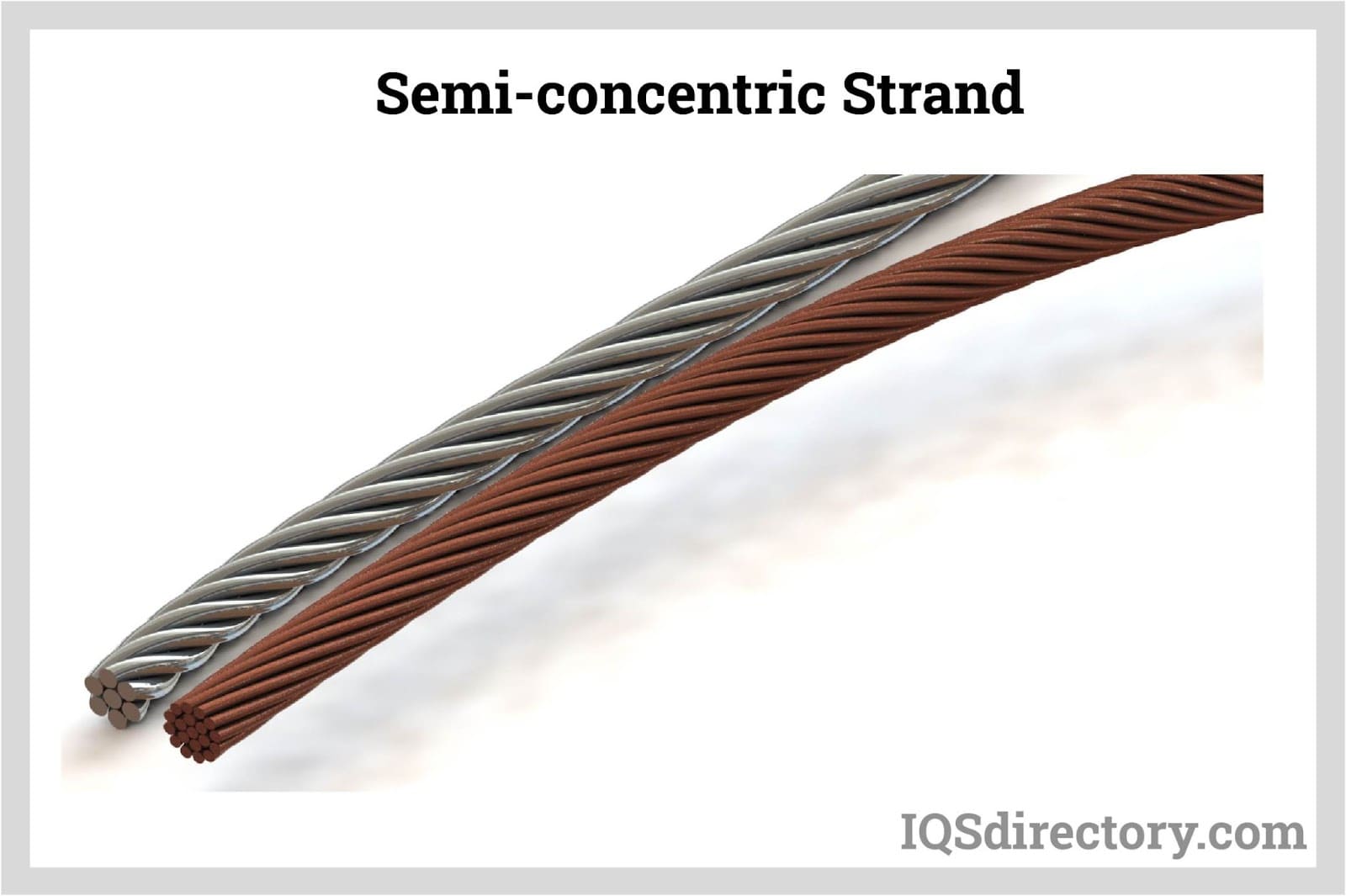
Stranded vs. Solid Wires-Key Differences
To differentiate stranded and solid wire the advantages and drawbacks of the two different types of wires must be looked at. An evaluation narrows down the adoptions based on how the specific wire attributes relate to their intended use and the project necessities. You must first consider your application’s requirements for climate resistance, flexibility, and toughness to splitting, severing, or failing. You then choose the most appropriate wire that will most closely meet the desired needs.
Some common differences of stranded wire and solid wire are as follows:
Current Carrying Capacity
Solid wire is denser and thicker, which means a lesser surface area for dissipation. The numerous and thinner wires in stranded wire have air gaps and larger surface area with each individual strand, translating to more transmission of current and dissipation. When selecting between solid and stranded wire for housing wiring setup, the solid wire will offer greater current capacity.
Routing Stranded Wires
Stranded wires provide a better elasticity, bendability, and flexibility, making them easier to go about around obstacles than solid wires would.
Stranded Wire Flexibility
Stranded wires are very flexible and can withstand a lot more vibration and bending without breaking or failing. Solid wires require more frequent changes than stranded wires in applications with significant shifting or vibrations.
Wire Cost
The production expenses of a solid wire are very low compared to stranded wire, making solid wire the most affordable option.
Relative Ease of Manufacturing
The single-core structure of solid wire makes it easier and much simpler to manufacture. Stranded wires desire a more complex and cumbersome manufacturing process of twisting the thinner wires together.
Solid and Stranded Wire Distance
For longer lengths, solid wires are a better selection because they have less electric current dissipation. Stranded wire will perform a lot better over minimum distances.
Superiority of Wire
When it comes to comparing stranded and solid wire in terms of superiority, it is difficult to determine which is better than the other. Each choice offers different advantages in particular circumstances.
Differences Between Braided Wiring and Foil Shielding
Foil shielding involves the use of metallic masking tape that can be made use of as a substitute for braided wiring. This kind of shielding offers exceptional protection against both high frequencies and other interfering signals and on top of that the associated costs are less than that of braided shielding.
The major drawback of this type of shielding is that it lacks a reinforcement of the lattice formation present in braided wiring and therefore the cables tend to fail as they cannot resist twisting and bending and cannot be laid down in a confined space.
Braided wire is handier and more adaptable as it plays a pivotal role in protecting the cable from both mechanical stress and EMI.
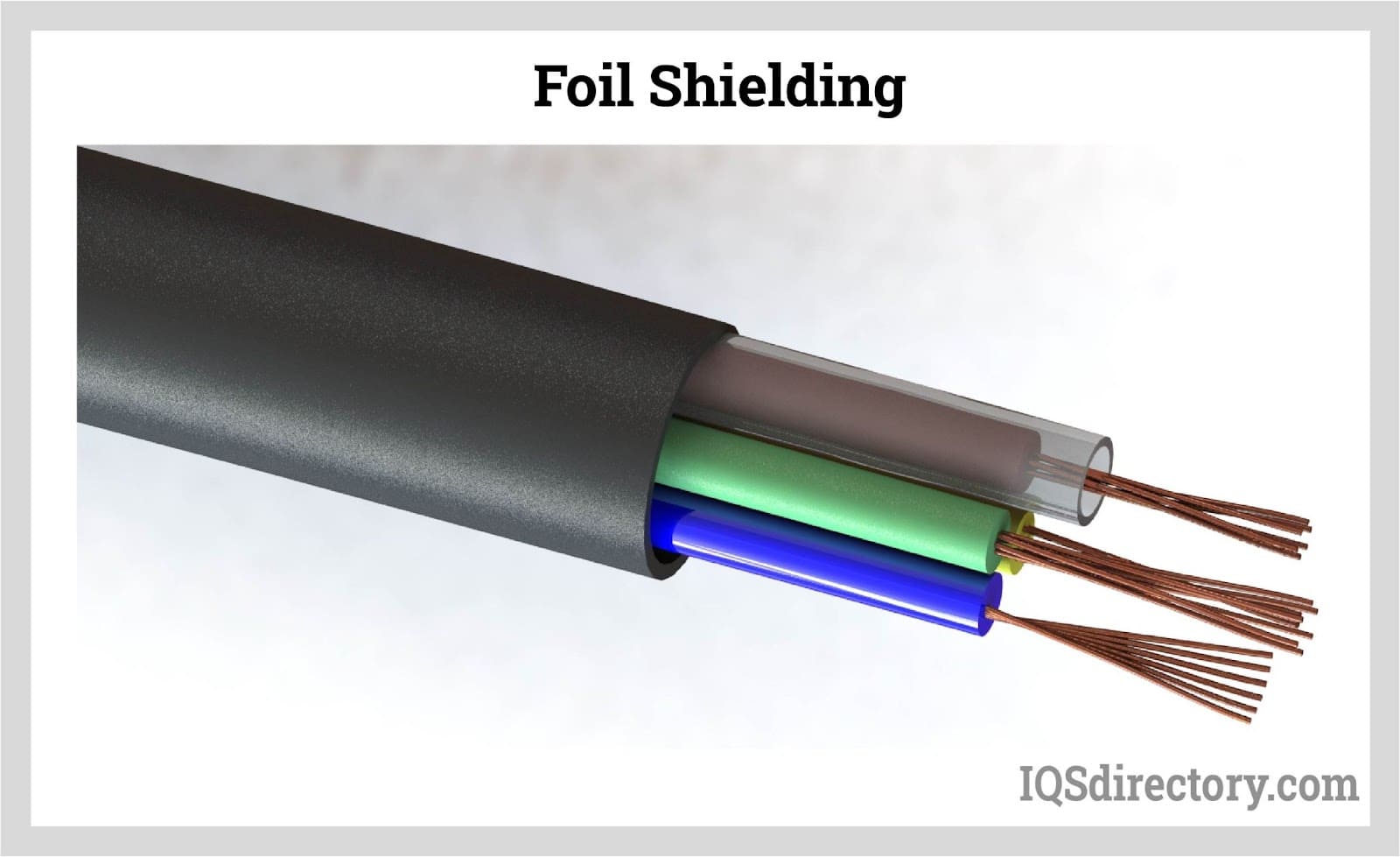
Braided wire only offers around 70 – 90% handling and furthermore adds bulk to the cable structure and this may not be best for applications that work with tight spaces or need 100% coverage. If you require a shielded cable but you are quite unsure which product to choose, consider doing a detailed background research on the task at hand because usually the consequences of selecting the wrong product are not worth the risk.
Leading Manufacturers and Suppliers
Chapter 3: Applications and Benefits of Stranded Wire, Braided Wire, and Wire Strands
This chapter will discuss the applications and benefits of stranded wire/braided wire/wire strands.
Applications of Stranded Cables
Those who need wiring for complicated and complex purposes such as circuit boards and any electronic devices will have to favor stranded wires as they will remain in place and safe even if it is twisted or made to fold when connecting to other electrical components.
Advantages of Using Braided Copper Wire
Copper wires can be of varying varieties ranging from stranded copper wire to braided copper wire. Each type has its own advantages and delimitations and it is imperative that you should weigh these correctly before buying any sort. You must research the kind of appliances these diversities can be used in. When you are working with a lot of flexibility the braided copper variety is better. This type is principally used for connecting parts of motor vehicles electronically for example the exhaust pipe. The braided copper wire is again used in the making of swinging doors and gates in locations where tall buildings have been built.
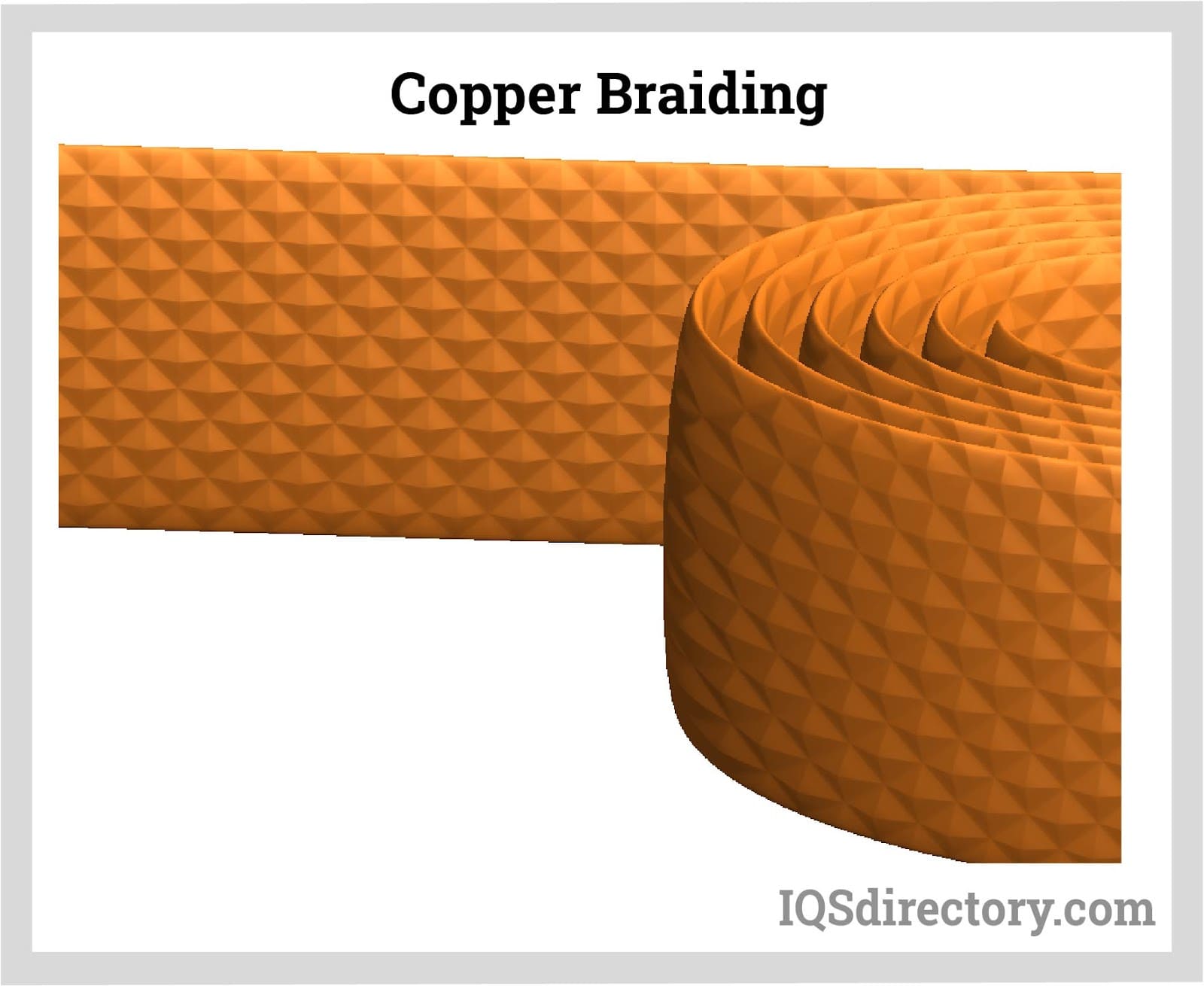
Braided Copper Wire vs. Solid Wire
- The solid copper wire is thicker compared to the braided one and the latter has a bunch of strands of copper which would have been twisted and braided together so as to create a whole wire. This is the reason why the braided sorts are more flexible and bendy as compared to the single solid wires. The solid wire is not easily moldable since it is rigid.
- Braided copper wire also has more resistance to corrosion and its malleability improves its resilience to wearing and tearing that is continuous. This is the reason why these bundles of copper wire strands are usually used for making electric cords and computer peripherals cables.
- The braided kinds are ideal for appliances which are used where there are a lot of vibrations. This makes such appliances tougher due to the braided wires that are flexible and strong.
- Unlike the usual copper cables, the braided types are easier to set up as they are made of many thin strands which would have been twisted.
Besides these numerous advantages that the braided wire offers, these wires are known to be more economical than cables like the coaxial cables. As they can both transmit electrical power efficiently, they have specific characteristics which make them appropriate for specific home or business purposes.
As the solid wires are better suitable for robust appliances and outdoor uses, the braided ones are better for electronic devices and circuit boards. Braided wires are suitable for robotics and motor vehicle applications because of their flexibility and strength. When purchasing this variety of copper cables it should be confirmed that the suppliers are legit and have a solid reputation.
You should only procure these conducting cables from companies that use top of the line raw materials and have been tested and safe to use in home appliances or in the industries. You can confirm the credentials of the dealers by checking for web reviews about the business organization and going through customer feedback on purchased products. This will enlighten you and give you an insight about which manufacturers you can work with to supply you with safe and relatively cheaper braided wires. Copper wires are still the most favored electric conductor when it comes to making electrical devices and appliances that require flexible and durable wiring.
Advantages and Disadvantages of Wire Strands
In dealing with reinforced and prestressed concrete bridges, the prestressing system is made up of a wire, strand and connecting parts, anchorage, force stressing jacks, corrosion resistance and ducting just to mention a few. The wire diameters usually range between 5 and 7 mm with a least tensile strength of around 1570 N/mm2 and are able to carry forces up to 45 KN. A strand is an assembly of numerous high strength steel wires twisted together. Anchorages are mechanisms used at all ends of the tendons and the resultant forces are transferred into the base concrete by an anchorage mechanism after being coursed through by the stressing jacks.
Solid vs. Stranded Cable
A solid cable is constructed with just one strand and sometimes the core of a wire that has non-conductive matter for insulation. This kind of cabling will be used for residential electrical wiring, wiring for laboratory breadboards, and other circumstances where wires are not required to be constantly moving about in the system.
Stranded cable is made up of a number of tiny gauge wires that are usually insulated and compressed with covering materials that cannot conduct electricity. This type of wiring is characteristically used in situations where the wire must be made to crawl about into cramped spaces and its strength will be put to use. It is yet again used in applications where there is substantial moving about, flexing, or vibrations of the working parts. Typical examples where such cabling is adopted include speaker wiring, headphone wires, and appliance cables, etc.
There are circumstances like the case of outdoor overhead electric cables and other heavy duty appliances where the cables are exposed to corrosive materials, back and forth movements, and extreme weather conditions. Engineers have settled for solid cables as they are best for such situations.
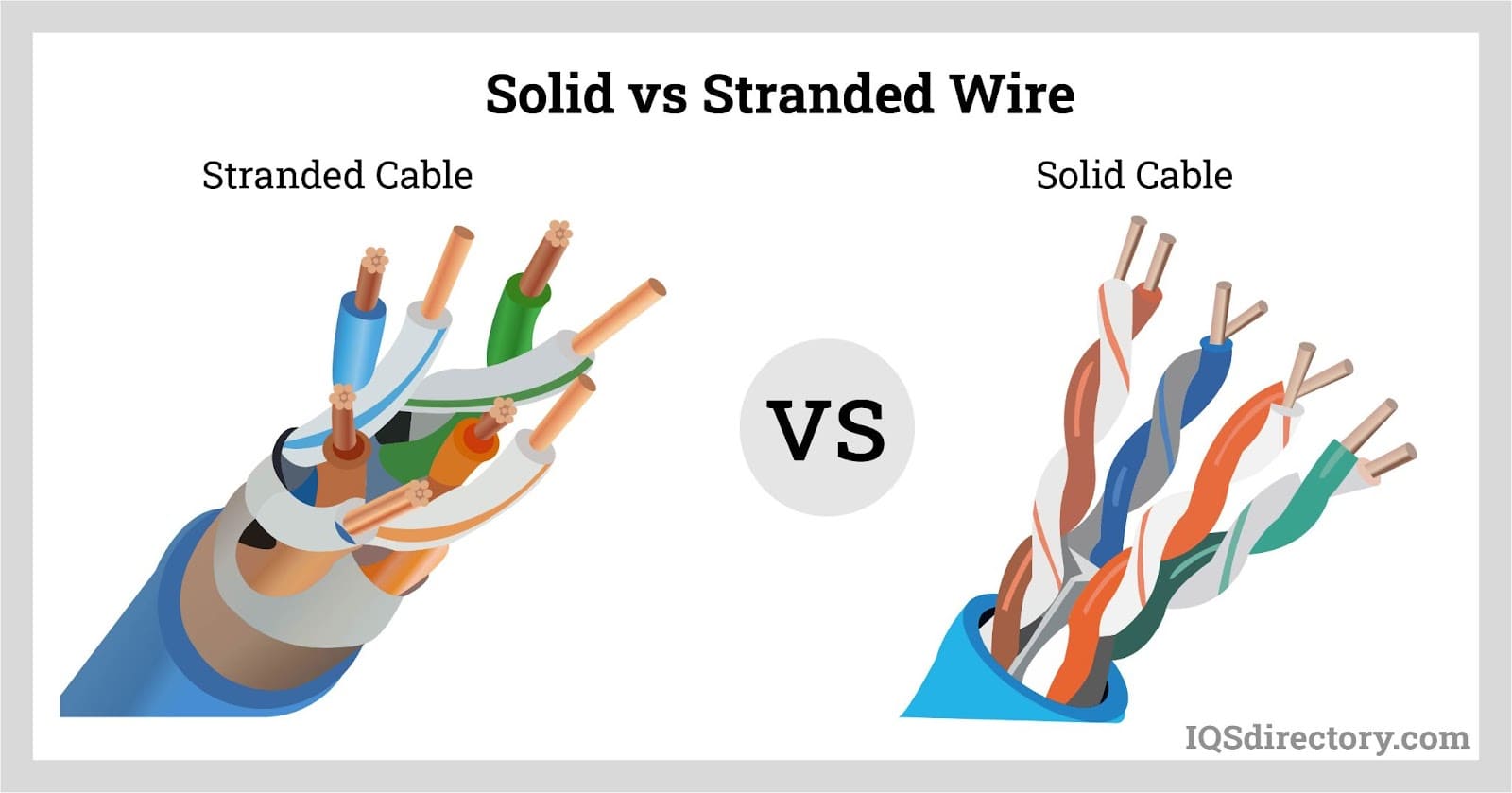
Benefits of Solid Cables
Solid cables are usually favored because they are usually more affordable than the stranded assortment and due to their relatively cheaper manufacturing costs. This type of cabling is simple and is very resistant to corrosion and mechanical wear and tear. Single but thick strands of cables are relatively quite resistant to occurring threats and very easy to produce. Solid cables have a much more compacted diameter in comparison to stranded cables. And this reduced extent does not lessen the current conductance ability of solid cables. To add in the fact that the solid cables are usually not as vulnerable to failure. This is as a result of deterioration and corrosion and it is easy to see why they are hoisted in high regard.
Disadvantages of Solid Cables
Though single solid cables have plenty of laudable features, they also have a number of drawbacks. One of the main challenges associated with solid cables is that they are commonly only sold in small volumes. Again, if there is continuous flexing or vibrations, the cable will eventually wear down and fail, creating the necessity for a replacement. Therefore, solid cables are usually not optimal for usage like robotics and vehicles requiring significant movement. If the cable happens to be bent into obdurate shapes, the solid cable will not have the suitable amount of fortitude and malleability to remain intact.
Benefits of Stranded Cables
Stranded cables are simpler to coarse in tight spaces in comparison to solid cables. They are also very extremely flexible and bendy. Stranded cables can resist a large amount of vibrations and back and forth flexing without wearing down and eventually failing. As a result, you will not have to change the stranded cables as frequently as will be required with solid cables.
Disadvantages of Stranded Cables
Stranded cables are good and all but are far from perfect. Their diameter is large yet they provide the same carrying capacity as solid wires. They are also a lot more expensive because their production costs are significantly higher than solid cables. The costs are relatively higher because of the complex manufacturing procedure that is needed to develop these complex wires. Stranded cables are very likely to fail as an effect of corrosion from capillary action. It is also worth pointing out that stranded cables are usually not best for preventing electronic disturbances. The air gaps between each wire amplify the “skin effect” made by the magnetic fields along the cable. Make sure you take each of the factors noted above into consideration before choosing either solid vs stranded cable for your household or business project.
Conclusion
In summary, there are various types of wiring used in the industries and home level appliances and some common types of wiring are stranded wires, braided wire, and wire strands.
Stranded wire refers to thin bundled up wires that are compressed and covered up in insulating material. Stranded wires are more flexible thus making them very ideal for joining electronic circuit components in confined spaces where their bending and twisting capabilities can be put to use.
Braided wire is a jersey-like shielding built around a cable to shield the wiring from electromagnetic interference and to improve its mechanical strength. The shielding is made up of numerous tiny wires tightly woven in a standard mesh tabular formation around the conductor. In some designs, it can be flattened to achieve the desired width.
A wire strand is when wires are wound up concentrically in a helix. The strands are wound around a central wire then around the core. Wire strands can be wound in varying numbers of configurations. The strands there are the more flexible the wire will be.
It is therefore imperative that a careful selection should be done depending on the job requirement and area of application.