Air Dryers
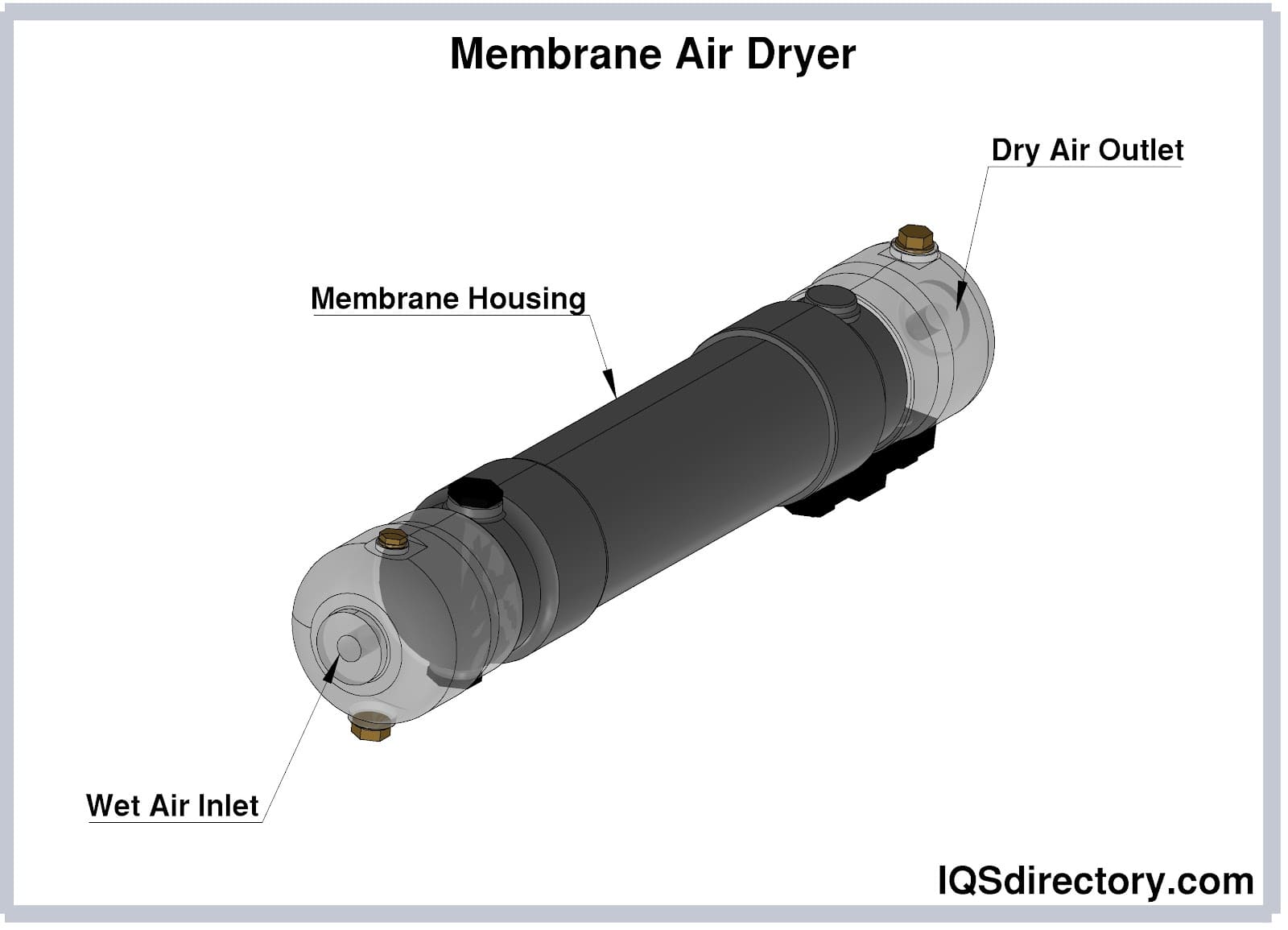
An air dryer is a system or piece of equipment that is used to remove moisture present in the air, particularly compressed air. Ambient air typically has a relative humidity of around 30 to 50%. Compressing air packs higher...
Please fill out the following form to submit a Request for Quote to any of the following companies listed on
This article takes an in-depth look at types of industrial dryers.
Read further and learn more about topics such as:
An industrial dryer is a high powered complex device designed to remove moisture from machinery, products, materials, food products, and mixtures. They are large rugged durable industrial pieces of equipment capable of drying high volumes of product efficiently with exceptional precision and control.
The descriptor, "industrial dryer", is a generic term used to describe a wide assortment of dryers each of which has a different and unique operating system. In the majority cases, industrial dryers are manufactured and configured to meet the needs of a specific product or manufacturing process. The types of dryers include freeze drying machines, chemical drying processes, air bar drying, continuous tray dryers, oven drying, and pan dryers.
Drying can be defined as the vaporization of absorbed moisture from wet materials. It is a heat and mass transfer process that is completed using a variety of mechanisms. The basis of the process is the transfer of heat from the material to be dried, which causes the absorbed water to vaporize that is transferred to and carried by the surrounding air or inert gas.
During the drying process, the humidity or moisture content of the surrounding air increases. The weight of the dried material decreases while the moisture free weight is constant. Some of the purposes of drying are:
Dryers are used in food, pharmaceutical, agricultural, sugar, pulp and paper, textiles, wood, metallurgical, metal fabrication, and automotive industries.
The difference between the various types of dryers is based on the mechanism used to remove moisture as well as the many different sizes and capacities. Small capacity industrial dryers are used for R&D and research laboratories, which remove a few grams of moisture. Large scale industrial dryers handle tons of wet feed per hour.
The many varieties of industrial dryers make choosing the right dryer with the appropriate type, size, and specifications for a given application a process that has to be carefully planned and considered. Each of the types of dryers offers capabilities and features that can affect the quality and performance of the final product.
Conductive heat transfer is a process where materials to be dried are heated through a board, object, or jacket. With convective heat transfer, the drying process is direct without the use of a board or coils. The two drying processes are classified as direct and indirect where conductive heating is indirect and convective heating is direct.
Direct dryers transfer heat to the material by convection. The heat transfer medium is forced to have direct contact with the material to be dried. A stream of hot air or inert gas serves as the heat transfer medium, which is blown or circulated around and within the material. This hot air carries and supplies latent heat to vaporize the absorbed moisture. The evaporated moisture is then picked up by the blown air.
Due to their efficiency, direct and continuous dryers are the most common configuration of dryers in industrial practice. Their heat transfer efficiencies are higher compared to indirect dryers. However, they have higher operating costs and may have increased energy losses.
The process of direct drying is further improved and enhanced with lifting flights that move the material over and through the stream of drying gasses. Lifting flights increase heat transfer and radially improve the drying process.
Air dryers are designed to remove moisture from ambient air, especially in compressed air. Ambient air has a moisture content of 30% to 50%. As air is compressed, the moisture content in a small quantity of air increases to 100%. High moisture content at manufacturing facilities can be damaging to sensitive equipment and machinery and can lead to process contamination, premature failure, wear, and corrosion, factors that necessitate the removal of the moisture content.
An air dryer absorbs moisture and impurities in ambient air to create a healthier and safer work space. In highly humid environments, air dryers help ensure uninterrupted operation and prevent downtimes. There are several methods used to dry air, which involve the manipulation of the temperature, increasing air pressure, and significantly compressing the air.
In one method of air drying, the temperature of the air is lowered after which it is reheated. In its cooled state, moisture is drained leaving moisture free air. With particulate absorption, moisture is absorbed by an absorbent material and discharged. A costly method involves compressing the air, lowering its temperature, draining condensation, and returning the air to its normal pressure.
Moisture build up is a natural result of filtering and compression processes, which cannot be prevented. The removal of the accumulated moisture is a necessity to avoid damage to the various processes. Air drying requires the selection of the best method for the application where the moisture is collecting. Air dryer manufacturers provide guidance and tools to safely and efficiently complete the process.
Conveyor dryers are a continuous drying system that moves products along a series of drying stations and are used as part of production or storage operations. Products are placed on the conveyor and pass through hot air zones that are precision controlled for accuracy and temperature. The conveyor belt is a form of mesh or web that allows warm air to be blown upward or downward at the product being dried. The normal design of a conveyor dryer is 60 feet long with three or more drying zones.
Certain designs of conveyor dryers allow for multiple passes where the fed products move from one belt to another via gravity. The number of passes is determined by the type of product being dried and can include two or three passes. A common use of multiple pass conveyor dryers is in vegetable dehydration.
The heated air in a conveyor dryer can be precision controlled and adjusted for air velocity, air temperature, and humidity. The multiple zones gently dry products using a constant feed rate and controlled temperatures. Turbine fans or nozzles blow heated air directly onto products to increase the rate of the drying process, a design that ensures complete removal of moisture. Any type of material, regardless of its viscosity, can be dried using a conveyor dryer.
The two key factors regarding food dryers are their ability to accurately control the temperature of the drying process, to avoid damaging the product, and the use of pure heat energy to avoid polluting the environment. All food dryers are designed with a stable heat source, powerful circulating fans, heat preservation, and efficient energy use of at least 90%.
Two common types of food dryers are multi-layer mesh belt continuous dryers and heat pump dryers. The multi-layer mesh belt dryer uses heat and air to increase the speed of the drying process and is used for drying massive quantities of food products. The belt for the process is made of strip pellet material that provides better ventilation, which is ideal for products that are unable to endure constant high temperatures.
Heat pump food dryers are a fast automated drying process for seafoods, bacon, fruits, tobacco leafs, and paper. They use forced ventilation to ensure that products dry evenly using a steam or electrical heat source. The successful use of a heat pump food dryer requires close attention to the temperature such that microorganisms are unable to grow and food products are not damaged. With a heat pump dryer, evenly spaced trays of food are placed in the dryer such that heat is uniformly exposed to the food.
Rolling bed dryers, known by the German acronym WB-T, are biomass dryers that are designed to dry large quantities of biomass. They combine bulk product flow with heat transfer and continuous movement for successful product drying. Rolling bed dryers consist of a large long cylindrical drum that is rotated on its vertical axis. Materials to be dried are placed in the drum and rolled along through the cylinder. The constant and continuous movement helps to evenly dry the material in a quick and economical way.
The process of rolling bed dryers combines the advantages of drum dryers and fluidized bed dryers to gently dry products at a low temperature. They are an energy efficient, homogeneous thorough drying solution that is used on biomass materials. Rolling bed dryers have a compact design for increased heat exchange, low exhaust temperatures, and reduced heat loss. The velocity of the drying air is adjusted to meet the needs of the material being dried. The process of rolling bed dryers makes use of the low temperature exhaust air.
Unlike more complex and intricate industrial dryers, the design of rolling bed dryers is simple and succinct, which makes their operation easy and uncomplicated. The perforated bed of rolling bed dryers allows for air flow over the material. The drying process is completed in the first stage of the cylinder and cooled through the final stages. Quick drying occurs due to the direct contact of the material with the hot blown air.
Indirect dryers transfer heat to the material by conduction. The heat transfer medium is separated from the material by a conductive partition. The material to be dried is contained inside a drying chamber and is heated from the chamber walls. The latent heat required to vaporize the absorbed moisture is transferred through the wall. The evaporated moisture is then carried up by the surrounding air. The surrounding or carrier air required by indirect dryers is much lower compared to direct dryers.
Indirect dryers are used in drying sensitive products, such as pharmaceutical products and combustible materials since the flow of air circulating the product is relatively low. These dryers prevent the risk of contamination during the process. They are also used in batch drying of relatively low production volumes.
The process environment for direct drying is tightly sealed and controlled, which is an advantage when working with potentially combustible materials. The fuel used to dry materials does not come in contact with the materials keeping dried objects from being covered with the fuel.
Since the fuel for drying is isolated from the materials being dried, lifting flights or circulating mechanisms are not needed by indirect dryers. Furnace exhaust from indirect drying is kept separate from the drying materials and process gasses eliminating the need to treat exiting gas.
Radiant dryers transfer heat by directly emitting electromagnetic waves to the material being dried. These electromagnetic waves carry thermal energy or heat that penetrates deep into the material. The absorbed heat is conducted to the moisture causing it to evaporate and combine with the surrounding air. Little heat is lost to the surrounding air, which makes the drying process contactless and low risk for contamination.
Like indirect dryers, radiant dryers do not require large airflow and may only need a small blower. They are cleaner and more environmentally friendly compared to convective and conductive dryers. Radiant dryers are used on adhesives, paints, and coatings on part surfaces.
Types of radiant dryers:
Microwave dryers use electromagnetic waves in the microwave region of 300 MHz to 300 GHz that penetrate beyond the surface of the material and use the molecules of the material to perform the drying process. Unlike hot air dryers, microwave dryers do not use heat as a part of the drying process but use energy that takes the form of heat due to its interaction with the molecules of the material being dried. In essence, the material heats itself using dipole rotation.
Dipolar rotation is caused by the electromagnetic waves of the microwave dryer that stress the molecules of the material and bring them into alignment from being in a relaxed state. Once the molecules are aligned, they return to the relaxed state from which they are aligned, over and over again. The constant change from relaxed state to alignment happens millions of times in seconds and results in the conversion of energy from stored energy to thermal energy, which rapidly dries the material.
A microwave dryer system consists of a microwave generator, applicator or wave guides, microwave unit, and a form of control system. Since microwave dryers are a non-contact and no heat drying system, they can be used in a wide variety drying applications from paper products to pharmaceuticals. Microwave dryers come in several forms from free standing dryers to large conveyor dryers with each form designed to meet specific drying needs.
Infrared dryers use electromagnetic radiation that has wavelengths that are longer than visible light and range between 0.78 µm and 1000 µm. It is a form of radiation that transfers thermal energy from a warm object to a cold object. The necessary heat level is reached on the surface of the material being dried where the infrared emission spectrum of the radiator matches the absorption level of the material.
The drying process for infrared dryers generates heat on the surface of a material that slowly moves to the inner parts of the material. They are a targeted material type dryer that is similar to microwave dryers and RF dryers. What distinguishes them from the other forms of electromagnetic wave dryers is their process of generating heat on the surface of a material.
Infrared dryers use high end infrared radiators as their heat source, which is highly efficient, low response time, supplies even heating, and has significantly low energy consumption provided in a compact package. The process used by infrared dryers does not rely on heated air or water to complete the drying process but uses radiation energy from a hot element in an infrared lamp to lower the temperature of the substrate. High power densities are produced in small areas, which is followed by rapid cool down times due to the lower thermal mass from the heating element.
The term batch dryer is a general descriptor that covers several versions of high volume dryers capable of efficiently drying large numbers of parts in one single cycle. Batch dryers can have conveyor systems where parts pass through on webbed belts that allow heated air to flow around the parts through the webs in the dryer. Other forms of batch dryers have a drying chamber with brackets to hold baskets of parts. It is form of dryer that is manually operated but has a control system that monitors the drying chamber.
Some forms of batch dryers have drying zones where parts pass through a series of heated areas to slowly and evenly dry parts. This type of dryer design is automated, which makes it possible for parts to be unloaded by robotic mechanisms, a characteristic that radically differentiates this form of batch dryer from other forms of drying processes.
Batch dryers process a fixed volume of material at a particular drying duration. A high volume, number, or quantity of materials passes through the drying chamber. The quantity is limited by the holding capacity of the dryer. The dried materials are unloaded automatically or manually to make room for the next batch. Batch dryers are used in relatively low production volumes. Typical forms of batch dryers are tray dryers, drum dryers, or rotary dryers.
A continuous dryer is designed to continually dry a constant flow of products, which may be grains, completed parts, pharmaceuticals, or various forms of food products. As with other forms of dryers, continuous dryers take several forms and can include transport chains, carts, rotary pumps, and conveyor belts. The drying process includes the movement of materials through a dryer chamber that has different zones that provide chemical and physical drying processes.
The first zone on a continuous dryer raises the temperature of the material to diffuse any moisture circulating around the product. As the product moves through other zones, the diffusion increases from the surfaces of products and into the air in the dryer. During the process, the temperature of each zone is carefully controlled to prevent damage to the product or material.
Continuous dryers are highly efficient and do not need to be cooled at the completion of a drying cycle. This is realized in production process savings since batches can be fed without having to change the controls of the dryer. Continuous dryers include gas burners, monitors for temperature and moisture, moisture outlets, recuperative burners, and a steering system with a control panel.
There are many benefits related to the use of continuous dryers that assist in the efficiency of a business. Continuous dryers have a very high throughput rate that makes it possible to process a high volume of material in a short time. The success of the process can be measured by the low moisture content of products at the end of the process, which makes it possible to immediately ship dried products.
The types of industrial batch dryers are the following:
Tray dryers consist of several trays, which contain the materials to be dried, stacked inside the drying chamber. Air is used as a heat transfer medium that is forced to move inside the chamber. Blowers facilitate air movement. The air gains thermal energy when it contacts the heating coils. The heated air is blown on top of the material, causing the moisture to diffuse and vaporize. A portion of the moisture-carrying air leaves through the ventilation duct, while the rest is recirculated in the chamber together with a stream of fresh, dry air. The temperature and velocity of the air may be adjusted depending on a given product and operational requirements.
Tray dryers are the simplest type of industrial dryers; they have inexpensive initial costs and consume less space. They are easy to operate and maintain. However, the drying time is typically long. They may not be suitable for powdered solids.
Vacuum dryers operate at a low (vacuum) pressure to hasten the vaporization of moisture or solvent absorbed by the material. The decrease in operating pressure depresses the boiling point of the absorbed liquid; hence, these dryers operate at a lower temperature than other industrial dryers.
The materials to be dried are loaded in trays. The dryer is equipped with a vacuum pump to reduce the pressure inside the chamber. Heat is transferred from the chamber walls to the material by conduction or radiation. Some vacuum dryers have a steam jacket. The vacuum pump draws the vapor; the vaporized solvent may be recovered by condensation and reused if necessary.
Vacuum dryers are used for heat-sensitive, hygroscopic, combustible, and granular products. They are used in food and pharmaceutical products to keep nutrients from degrading in high temperatures. They remove large quantities of moisture efficiently and have fast drying times.
Pan dryers are equipped with an agitator or a mill that stirs wet materials inside a jacketed vessel. The agitator or mill rotates slowly to increase the drying rate, which is moisture removed per unit time per unit area, to ensure uniform heat distribution and avoid products sticking to the walls. Pan dryers are operated at atmospheric or vacuum pressure and are used for drying heat-sensitive, viscous, and sticky products.
The process for pan dryers is designed to combine a set of drying operations in a single device without removing or exposing the product. It is a batch style dryer that has wet product automatically loaded, charged, into the top cylinder jacket as the agitator rotates. Once the product is dried, it is discharged by a pneumatically operated door. The cylinder and chamber of a pan dryer are able to meet the pressures and necessary compatibility requirements of the products to be dried.
Out of necessity, the components of a pan dryer are customized to meet the needs of the various products that it is designed to dry. Each pan dryer is constructed and tested to ensure that it meets the standards of the product it is drying. Scale up data and working capacity for each pan dryer is supplied to ensure compliance with client requirements.
Freeze-drying (or lyophilization) involves freezing the material to be dried and subjecting it under vacuum pressure. It is employed for products that drastically degrade or change at high temperatures. It preserves the material’s biological activity and chemical properties. It is used in food and pharmaceutical products to preserve their nutrient content and active ingredients. It is also used in biological specimens such as blood, tissues, and proteins. However, freeze-drying takes a long time to complete.
Freeze dryers consist of refrigeration equipment, a drying chamber, holding trays, and a vacuum pump. The sample is first frozen to at least its melting temperature to convert the moisture and solvent within the material into a solid phase. The vacuum pump is then activated to decrease the pressure inside the chamber. Heat transfer under low pressure causes the solidified moisture or solvent to transform into vapor. The vacuum pump draws the vapor sublimed off the material. The freeze dryer will continue to run to drive off the moisture or solvent bound to the material.
Bin dryers are a form of batch dryer that consist of a large cylindrical or rectangular drying chamber that has a wire mesh bottom. Air is drawn into the bottom portion of the dryer and blown up through the wire mesh over the product to be dried. The walls of a bin dryer are tightly sealed to prevent heated air from escaping the drying chamber. The door to the dryer that allows fresh air in to be heated is fully opened or partially open to regulate the level of circulation of heated air in the dryer.
The holding tank, referred to as a bin, has a perforated plate at its bottom. A fan blows air through a heater that circulates through the perforated plate vertically upward and over the product, causing it to dry. Material is arranged on shelves with the wettest heaviest material at the bottom. As the moisture carrying air moves upward, it exits out of the dryer. Ducting helps maintain air velocity and keeps fines in suspension until they fall to the bottom of the chamber and are removed. Bin dryers are used to dry agricultural and forest products such as wood, fruits, vegetables, grains, bamboo, and others. They lack a control system and are sometimes used as a pre-dryer.
In tunnel dryers, the materials to be dried are loaded in trays attached to a trolley. The trolleys enter at one and move slowly through the drying tunnel, wherein a stream of hot air or gas is blown. The material dries as it moves through the tunnel. The trays may move in either of the following directions with the air stream:
The settings of the heater zones and the trolley speed may be optimized according to the type and quantity of materials being loaded and final moisture or solvent content.
Tunnel dryers are considered as an enhancement to tray dryers. Materials continuously enter and exit throughout their operation. The material is steady on the trolley as it traverses the tunnel. Hence, these dryers are suitable for products sensitive to damage or deformation, such as automotive components, electronic parts, construction materials, glass materials, and large fruits, vegetables, and food products. Tunnel dryers are operationally efficient in processing materials requiring long drying times.
Rotary dryers consist of a slightly inclined metal cylinder with internal flights. The material is fed from the upper end of the cylinder. The cylinder slowly rotates to lift and cascade the product. Hot air or gas enters in a concurrent or countercurrent direction with the material. The agitation caused by the rotation and internal tumbling action results in rapid and uniform drying. The product is collected at the lower end of the cylinder.
Rotary dryers may be classified as direct-fired or indirect-fired. In direct-fired rotary dryers, the hot gas directly contacts the material inside the cylinder. High-temperature air may be used to roast food products. In indirect-fired rotary dryers, heat is conducted from the cylinder walls to the material being dried.
Rotary dryers are suitable for drying granular and non-sticky materials. They are commonly used in drying products from a crystallization process. They are suitable for drying salts, minerals, grains, nuts, and animal feeds.
In fluidized bed dryers, the wet material is fed to a vessel by a screw feeder. A stream of preheated air flows from the bottom of the vessel to keep the particles suspended or fluidized. This stream flows perpendicular to the direction of material travel. A horizontal air stream may be supplied to help in conveying the particles. The extensive contact of the particles and air results in a faster drying process. Moisture-carrying air exits at the top of the vessel. The particles carried over by this stream are separated by a cyclone separator or a bag filter. The dried products are collected at a point lower than the material inlet.
In vibrating fluidized bed dryers, vibration is added to enhance the fluidization of large-sized particles and sticky and sluggish feeds.
Fluidized bed dryers are used in powdered and granular products such as grains and cereals. Some fluidized bed dryers are designed and configured to enable batch drying.
Vacuum drying is a widely used form of drying process due to its efficiency and effectiveness in drying products and materials. The central part of a vacuum dryer is its enclosed drying chamber that is tightly connected by a condenser to a vacuum system. Various forms of heating methods are piped to a jacket that surrounds the vacuum dryer chamber.
As wet material enters the drying chamber, the vacuum system lowers the pressure in the drying chamber as the heated jacket transfers heat to the chamber. This indirect heating method protects the product and increases the efficiency of the drying process. During the drying process, evaporation causes the wet material to dry. The vapor that is created by the process is drawn through a vacuum stack or pulse filter to the condenser where it is returned to liquid form. It flows into a holding tank for reuse or disposal.
The removal of moisture in an agitated vacuum dryer is affected by the level of the vacuum, the accessibility to the surface of the material, and the efficiency of the heat transfer process of the jacket. The adjustment of these variables enhances the efficiency of the dryer. Agitator vacuum dryers are also used in drying heat and air-sensitive products. They are usually placed next to filtration equipment.
Spray drying is a quick and efficient process of directly transforming a slurry, suspension, or paste into fine dried powder form. The feed usually contains a high amount of moisture and must be transportable by a pump. It is used to produce soaps, detergents, milk, coffee, tea, salts, polymer resins, flavorings, extracts, pharmaceutical products, and others.
Spray drying involves the following stages:
It is the process of converting the feed into a mist of fine droplets to ensure fast drying. The feed is pumped continuously to an atomizer installed on top of the drying chamber. There are several techniques in atomizing the feed:
A hot gas stream is introduced either at the top or bottom of the drying vessel. The drying gas for solids in an aqueous solution is air. Nitrogen gas is used for organic or flammable solvents. The moisture or solvent is removed as the atomized feed is dispersed over the gas. The diameter of the drying vessel is large to prevent the particles from sticking on the vessel walls. The particles settle at the conical bottom of the vessel.
Drying takes place as quickly as a few seconds. Hence, spray dryers are used in drying thermally sensitive products which degrade when exposed at a substantial length of time.
A cyclone separator and a filter separate the particles from the drying gas.
With flash drying, wet material is fed into a stream of heated air that pushes it through a drying duct. The heat from the airstream dries the material as it passes through, after which it is separated by cyclones or bag filters. Scrubbers are used to perform a final cleaning in order to meet required emission standards.
Flash dryers dehydrate wet granular materials and laminate moisture. The high velocity gas stream keeps the particles of the wet material suspended as heat from the gas stream removes moisture or solvents. The cyclonic action separates the material from the gas stream. For the sake of energy efficiency, a portion of the exhaust gas is recirculated to the duct.
Flash drying is a continuous process that is heated directly or indirectly depending on its design. Materials are rapidly processed, which makes it possible to immediately package them for shipping as they exit the dryer. Flash drying can be adjusted from 340deg;F (170deg;C) to meet the needs of heat sensitive materials up to temperatures as high as 1100deg;F (600deg;C) for material that can not be damaged by exposure to high temperatures. The low residence time and flashing off of moisture results in evaporative cooling that makes it possible to use higher inlet temperatures without damaging the product
Drum dryers or roller dryers dehydrate liquid feed in order to produce powders, flakes, or granular materials. They consist of one or two internally heated drums that rotate about their axis. Steam is flowing inside the drum, and heat is conducted through the walls. The feed is sprayed onto the surface of the rotating drum or between the two rotating drums. A thin film of the liquid feed sticks and dries on the hot surface. The product's initial and final moisture contents determine its residence time on the drum surface. A scraper removes the dried particles once the desired moisture content is obtained.
In vacuum drum dryers, the drums are placed in a chamber with vacuum pressure. The low pressure inside the chamber decreases the boiling point of the moisture or solvent, causing it to evaporate at a lower temperature. Hence, vacuum drum dryers are suitable for drying heat-sensitive products.
Disc dryers consist of multiple vertical rotating discs mounted on a shaft contained in a horizontal cylinder. Heat is created on the shaft by steam or hot oil and conducted to the mounted discs. As the discs rotate, they provide indirect drying of the material. Wet feed, in the form of a slurry or sludge, enters the dryer at one end of the cylinder. Moisture or solvent from the feed evaporates as the material makes contact with the rotating discs as it is transported axially through the cylinder. Scrapers, located inside the cylinder, ensure uniform mixing and prevent the materials from sticking to the discs. Dried product is collected at the bottom of the cylinder at its opposite end.
The unique design of disc dryers ensures efficient heat transfer to the product for faster drying times. The gentle movement of the discs minimizes the possibility of damage to sensitive materials and assists in preserving their integrity. The key feature of a disc drying is the uniformity of the drying process due to the constant movement of the discs, which helps in avoiding uneven drying and the presence of moisture spots.
Disc drying has an advanced heat transfer mechanism that is energy efficient for the reduction of energy costs. Any type of material can be dried using a disc dryer and is used in a wide range of industries including pharmaceuticals, food processing, and the chemical industry.
The RAMCO hot air parts dryer is noted for its ability to quickly dry parts without the use of excessive heat. Its process elevator changes flow patterns that results in a dynamic drying mode for better coverage of part surfaces, increased evaporation, and faster processing times. Air for the RAMCO hot air dryer is electrically heated, continuously recirculated, and directed into the drying chamber using air knives. During the process, the elevator of the RAMCO hot air dryer moves the parts load in and out of the heated air stream. The RAMCO hot air parts dryer comes in standard models and can be customized to fit customer requirements.
NPH and PGH drying hoppers are designed for drying and dehumidification of plastic resins. They have a rail for hopper mounted heaters, slide gate shut off, and elongated sight glass. NPH and PGH drying hoppers are constructed of stainless steel and carbon steel with large access doors for easy clean out. The double wall construction of NPH and PGH drying hoppers ensures a tight seal, exceptional quality, and longevity of the dryer. Lifting lugs are available on most models, which also include 12 foot silicone hoses with clamps.
The 801D prevents spots on drying parts by using heated air to dry basket loads of parts. They have a stainless steel construction with digital timer and temperature controls. The 801D has a 29 gallon capacity with a 36x14x14 footprint. The drying process for the 801D includes the use of forced warm air that enters from the back of the dryer and passes over the baskets of parts for drying and passivation. The 801D is a large part stand alone dryer with casters that make it portable and easily maneuverable.
The FM-D-LH3025 hot air dryer is a front loading hot air dryer that uses vertical air flow for the drying process. Air enters the drying chamber at the top of the dryer and flows downward exiting through a grate at the bottom of the chamber. The design makes it possible to use drying racks or offers the ability to dry parts that are two feet tall. The downward air flow makes the drying process quicker and more efficient. Hanger rods, side wall brackets for multiple trays, and work rests are a standard feature on the FM-D-LH3025 hot air dryer. Vertical models of the FM-D-LH3025 hot air dryer have a wide chamber for high capacity loading.
One of the more difficult types of parts to dry are parts that are small and nested that cannot be dried using conventional hot air methods, especially if they have cups that can hold water. Spin dryers dry nested parts by spinning a basket of parts at a very high rate. The centrifugal force of the spinning causes the excess water to be thrown off while a turbine fan, below the spinning basket, sucks heated air from a heater mounted on the lid through the basket of parts. Using the process, in less than sixty seconds a basket load of parts is completely dried. The double action of the fan and centrifugal force ensures fast and efficient drying without scarring or damaging the parts.
Industrial dryers are a central part of the quality of products and need to be carefully chosen to match the needs of an application and product. Like all industrial equipment, industrial dryers are a substantial investment but, when chosen properly, can last for several decades with little need for maintenance.
Manufacturers and engineers have a clear concept of the type of dryer they require, which has been investigated, researched, and analyzed prior to the publishing of a RFP. The six criteria presented below are the factors that engineers consider before developing their RFP.
The size of the particles in the material and their density determines the amount of drying that will be required. Fine powders have different drying cycles than sludge. Large painted or coated parts have further unique drying needs.
The drying process can be further complicated by attempting to dry items of different sizes with different particulates in the same batch. The density of an item determines the speed at which it moves through the dryer and whether special types of conveyance are necessary.
The starting moisture percentage and the ending moisture percentage need to be calculated. This aspect of the assessment process can be completed by testing the weight differences between the wet and dry percentages of a material. The calculated water weight is used to determine the size of the dryer. This part of the process has to be the most precise since the slightest error can cause the water weight to change resulting in the selection of the wrong dryer.
Another distinction between materials is in regard to whether the water is surface water or absorbed, which significantly guides the drying process. Different methods of vaporizing are used for surface water compared to internal absorbed moisture. Whether the water is internal and absorbed or external and surface helps to decide if any pre-drying procedure is required.
Each type of material reacts differently in the presence of heat with some products having a chemical reaction at a certain temperature. Other materials may melt, burn, or explode when exposed to heat over an extended period or when the temperature reaches a certain level. This factor can be controlled by the heat source since heat sources can cause different reactions.
How an item reacts to heat determines if the dryer is large or small, the amount of time of heat exposure, and whether the heating method should be direct or indirect.
Material handling refers to how the substance to be dried will be placed in the dryer. Wet and sticky material may need to be forced through to prevent them from plugging or clogging the dryer. In those instances, nonstick surfaces or paddles can be built into the dryer with clean fittings to remove places for potential buildup.
Many modern products are extremely fragile and have to be handled with extreme care to avoid damage and waste. This type of situation demands a conveyance method that is non-abrasive and gentle. The reverse is true for coarse or gritty materials that can damage the surface of a dryer and shorten its lifespan.
As with every industrial operation, there are production limits to be met with each production run. The size of an industrial dryer has to meet the production amounts that are expected of a process. Included in this aspect of the selection process is whether the dryer will be running continuously as part of an assembly process or work with batches. Under sized dryers can slow down production and be overloaded with inappropriate demands.
Industrial dryers can be a separate mechanism that is used when needed. Conversely, they can be a central part of an assembly process and must be timed to the needs of the production operation. This part of the selection process determines where an industrial dryer will be located in relation to assembly and production needs.
Industrial dryers are a heavy duty piece of equipment that are an important part of production and product quality. As such, they are purchased using the same parameters as any other type of machinery, which includes their initial upfront cost and the expense of operating them.
Although there are industrial dryer options that are less expensive at first, they can be more costly during operation due to maintenance costs, being inappropriately matched to the needs of an operation, being less efficient, and having a shorter life span. These factors make operating a less expensive dryer more costly by increasing operating costs.
During the planning and research stages, engineers carefully examine the total investment in regard to the purchase of an industrial dryer including its efficiency, enhancement of product quality, and the cost of operation, which should match and exceed the needs of the operation. In essence, it is developing a perfect match between a dryer's abilities and production requirements.
An air dryer is a system or piece of equipment that is used to remove moisture present in the air, particularly compressed air. Ambient air typically has a relative humidity of around 30 to 50%. Compressing air packs higher...
A conveyor oven is a continuous flow oven; it‘s an oven that is open on opposing sides and has a conveying system running from one end of the oven to the other. Designed like a batch oven, conveyor ovens have the additional benefit of keeping products moving while providing continuous and uniform heat...
A curing oven is thermal processing equipment used by thermal specialists to improve or enhance the strength and durability of materials. Many factory processes such as baking, drying, heating, cooking, and curing require...
An industrial oven is a device used to create extremely high temperatures to heat treat parts, condition metals, and cure metal coatings. Common functions for industrial ovens include drying, curing, testing, and coating of parts and products...
An infrared oven is an oven that heats objects or cooks food using infrared radiation instead of conventional conduction or convection heating. People can use infrared ovens in commercial kitchens, homes, or...
Industrial ovens are thermal processing machines used as heating chambers for drying, curing, and baking of foods, parts, and components. The main industries that use industrial ovens are chemical and food processing and electronics manufacturing...