Canopies
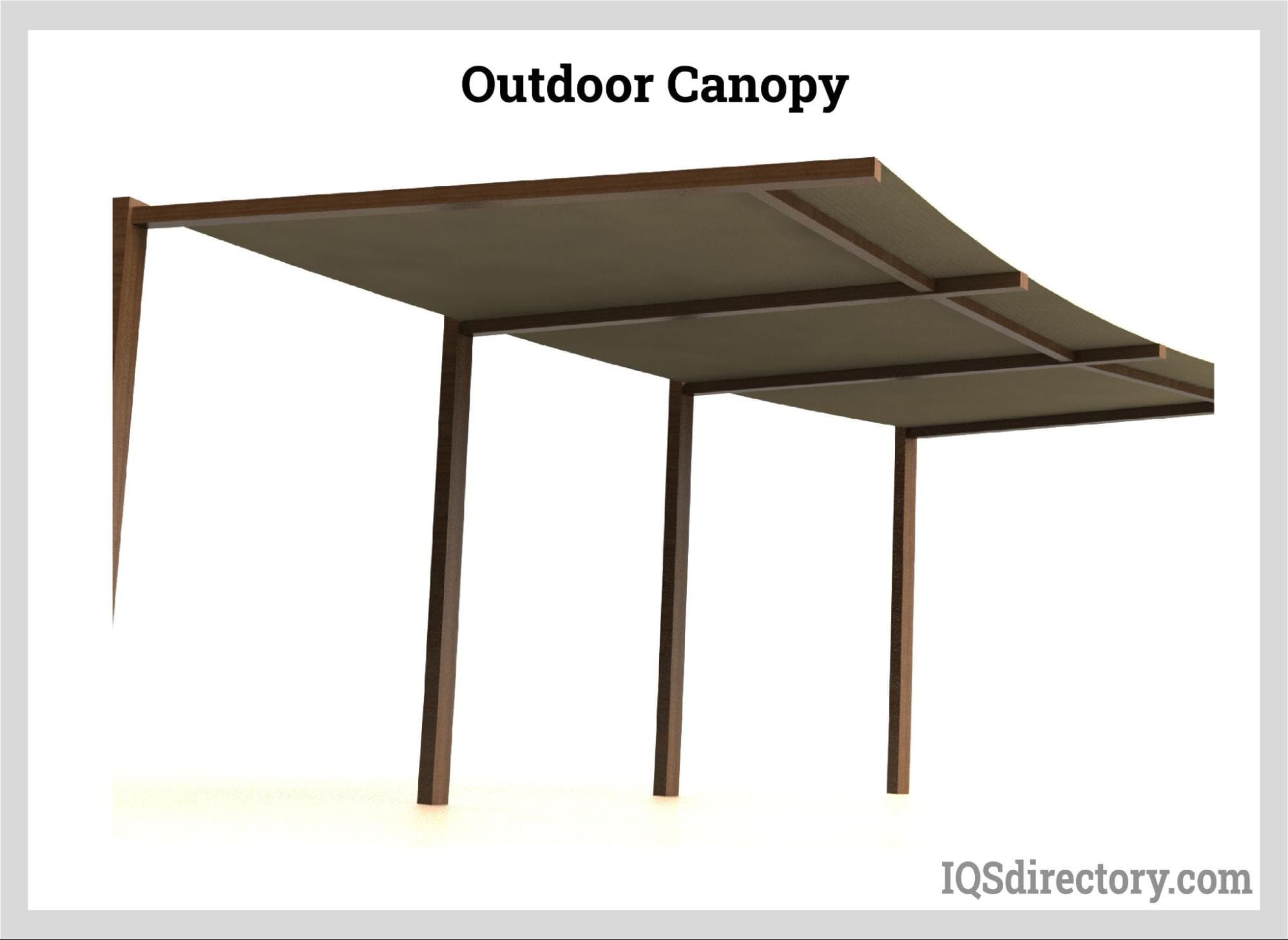
A canopy is a structure with a connected fabric or metal covering that can give shade or shelter from weather elements such as the sun, hail, snow, and rain. For example, a tent with no floor can be...
Please fill out the following form to submit a Request for Quote to any of the following companies listed on
This guide contains everything you need to know about contract sewing.
You will learn:
Contract sewing is a specialized industry that provides services to manufacturers for production of a wide range of products using highly skilled workers and technologically advanced sewing machines.The strength of the contract sewing industry is its ability to offer sewing services in the creation of soft goods for different industries including medical, military, apparel, aerospace and custom clothing.
The process of contract sewing is far more complex and complicated than producing goods on a traditional sewing machine. The main factor in the success of contract sewing is the amount of planning and preparation put into each customer’s project with a heavy emphasis on quality and efficiency.
An additional version of contract sewing is contract sewers that are individuals that contract their skills to contract sewing companies or manufacturers to complete small projects of 100 pieces or less. They are highly skilled in different sewing methods and are used for producing clothing and more complex items.
A major benefit of contract sewing is the wide range of materials and fabrics that are used to create their products, which include vinyl coated nylon, neoprene, Hypalon, canvas, anti-static materials, cotton, polyester, felt, plastic, webbing, and leather. The products that the industry produces are based on designs and creations submitted by their customers.
Contract sewing is a necessary industry used to support companies that do not specialize in sewing or needle work. The industry grew out of manufacturer‘s need to have items sewn for products they had designed but were unable to produce.
To fill the gap, manufacturers contract with sewing companies who serve as a supportive component in the completion and production of a variety of products. The specialized nature of sewing, as well as the technical aspects, has made contract sewing a vital part of the introduction and production of many of today‘s products.
The contract sewing industry offers services to companies that manufacture and produce items that require sewn fabrics as a part of their product line. Companies that use contract sewing are in an unrelated industry where sewing is only a small part of their production process.
The biggest reason that contract sewing has been so successful is its ability to take visions and ideas and turn them into reality. Industries that use contract sewing are not equipped to take their highly inventive ideas and make them a reality through their production processes.
An important benefit of contract sewing is its ability to produce large quantities of sewn products in short turnaround times, regardless of the size of the item to be produced. The first thought that comes to mind regarding contract sewing is clothing, which is only a part of what contract sewing does, as can be seen below.
Fabrics for the automotive industry have to be durable as well as UV and heat resistant since cars bake in the sun. Due to the nature of fabrics for car upholstery, a specially designed sewing machine is required with special attachments. The main concern with auto upholstery is the stitching, which has to be secure and long lasting. Also, the material and stitching have to fit into the overall design of the car.
The textiles used in cars add decoration and softness to seats and the interior but have a functional application. Unlike years ago, the types of materials used for car upholstery are no longer restricted to any one type of fabric and can include leathers, vinyl, cloth, and various types of sturdy fabrics.
The sewing of airbags is challenging since they have to be large enough to protect the occupants of the vehicle but small enough to fit in a limited space. The fabric for airbags is very dense and compact to be able to withstand the force of deployment. The heavily coated material is cut, sewn, and tested before being placed in a car.
Knee pads are made with reinforced stitching for extra protection. Included in their design is neoprene, nylon, and PVC to add strength and durability. Industrial style knee pads are made to protect workers from nails, broken glass, and various forms of debris. They must be designed for comfort but offer extra support to leg muscles and tendons.
Industrial aprons are made from high quality materials such as leather, cotton, polyester, rubber, and asbestos. They are designed to offer protection from water, chemicals, oil, and environments with hazardous materials. They can be sewn and produced to fit any type of conditions and come in a variety of types such as cobbler, no pocket, and bib as well as a variety of lengths.
A great deal of time, engineering, and effort are required to produce a piece of luggage. Much of today‘s luggage is made from heavy duty nylon fabrics. The texture and strength of the material requires automated stitching machines with the strength and endurance to produce secure and permanent stitches. Luggage sewing encompasses a wide range of products from duffle bags and sports bags to briefcases and messenger bags.
The core of an airplane seatbelt is its webbing with a buckle attached. The webbing comes in hundreds of different colors to meet the needs of each airline. The form, shape, and connectivity of an airplane seatbelt is governed by government regulations, which requires that every seatbelt be tested multiple times.
Though passengers may view an airplane seatbelt as a part of the process of flying, in reality, it is viewed as a crucial and essential safety device. They must be able to survive 16Gs of force to be acceptable for shipment.
HVSA wear is one of the more visible forms of safety wear and is found on highways, construction sites, and traffic patrols. The production and sewing of HVSA wear is determined by the American National Standards Institute, a private non-profit organization that oversees national standards.
There are three different categories for HVSA protective gear, which are O (off-road), R (roadway traffic control), and P (public safety). Each classification is graded by the reflective qualities of the material being used.
The production of uniforms involves the use of universal camouflage patterns (UCP) and operational camouflage patterns (OCP) using the sturdiest and most wear resistant materials. For the materials to be accepted for military use, the material has to pass a variety of tests, which rate its blending, brightness, contrast, and detection abilities. The final choice of OCP uses a variety of colors that include gray, artichoke, laurel green, American silver, grullo, and dark silver.
The main design factor for chair material is its ability to offer support and comfort. Chairs from the contract sewing industry are ergonomically designed with materials capable of withstanding the normal wear and tear of everyday use. A special feature of chair design is having an adjustable headrest and adjustable lumbar support. These chairs serve as seating for security and control rooms as well as public safety dispatch centers.
Industrial curtains have to be produced to the specifications and requirements of the customer‘s industry. They are made of a variety of materials that include PVC film, vinyl, banna, and parquet. Industrial curtains are designed, configured, and dimensionally compatible to meet the requirements of the application. They have headers with grommets and snaps made of long lasting and highly resilient material.
There are several reasons why manufacturers use industrial curtains, which include noise reduction, separation of production areas, safety, climate control, and avoidance of product contamination.
The aerospace industry makes wide use of contract sewing especially in the area of space suits that have to conform to very strict and demanding regulations. Space suits are made from various types of materials including synthetic polymers. The inner layer is made of nylon followed by a layer of spandex. Additional layers include urethane coated nylon for pressurization, a layer of Dacron, and a layer of Neoprene.
Other applications for contract sewing in the aerospace industry include insulation for aircraft piping, environmental containers, fuel and fluid bladders, and PVC bags. The items produced for the aerospace industry are mainly focused on safety and protection during emergencies and have to meet the highest possible quality standards.
Of the various industries, the medical industry depends on the contract sewing industry for the production of a wide variety of biocompatible items. Garments, organ holsters, and medical mesh for implants are a few of the products produced. The fabrics for the medical industry have to meet certain standards established by hospitals, which include being biocompatible, durable and able to withstand stressful wear, and incapable of fatal damage.
The long list of items produced by the contract sewing industry for medical use includes gauzes, bandages, blankets, and medical grade fabric supplies. The medical industry depends on the high standards and quality of the contract sewing industry to supply them with sterile and safe medical fabrics.
The contract sewing process is an industrial method for mass producing a wide range of products for commercial and industrial use. The production of these products requires the selection of components that are brought together and connected by sewing.
Contract sewing is a vital industry that supports large manufacturers in the planning, developing, designing, and perfecting of designs and procedures. The name, contract sewing, is a short definition of the process used to create sewn materials.
The purpose of the prototype and design phase of contract sewing is to define design flaws and develop methods for removing them. The basic premise of prototype and design is built on the idea that concepts and creations may look very good when generated on a computer but may not be practical in the production process. The errors and mistakes are caught prior to going into production, which saves time and money.
Unlike years ago when patterns were produced in print, modern contract and industrial sewing patterns are created on a computer using a computer aided design (CAD) based program. The patterns produced by CAD makes it possible to look inside a 3D representation of a garment to inspect every aspect of it and edit it by undoing or modifying the original but keeping the design in tact.
A 3D sample from CAD removes the need to create a physical sample for photo shoots or communication with buyers, which can be completed electronically. Instead of having a backroom of stored patterns, CAD makes it possible to store patterns online for future projects. Once the CAD rendering is completed, it is easily passed on to a pattern maker or technical designer who's responsible for production.
The instructions on a pattern are customized for each product since there is no one way to complete the process. As can be seen in the example below, the instructions for contract sewing are very brief. In most cases, no instructions are given and are left up to the contractor.
The electronic pattern process covers every aspect of the development of the product. For clothing, it displays the cuts for each of the different sizes as well as the methods for cutting. An important part of this part of the process is determining the consumption of the materials used for the production process, which has an influence on the final cost.
Once the pattern is approved, it is sent onto the pattern printer, which is a wide format printer similar to a plotter used for printing blueprints. This aspect of the process is not the same for all manufacturers. For some, the pattern is printed on a heavy material that will be used in the cutting process.
Once production develop is approved, the pattern is put through marking and grading to determine the yield. This helps determine how much fabric is needed for ribbons, lining, buttons, zippers, and such. When the fabric arrives, a pre production sample is made.
Prior to sending the fabric to production, it is inspected and preshrunk. Though this may not apply to all contract sewing projects, one aspect of the process is commonly used, which is the inspection and approval of the materials regardless of whether it is leather, polyester, vinyl, or some other type. It is important to ensure that the materials are in good condition for the production of a quality product.
The cutting process involves having the pattern lain out on the material to be cut. A very sharp saw-like cutting tool cuts through several layers of fabric following the guidelines found on the pattern. Though this process is used for the manufacture of cloth or clothing items, it may vary for heavier materials such as leather or vinyl.
Aside from the hand cutting method, a more efficient type of cutting is an automated high ply cutting system designed for cutting garments. The instructions for the cutting are completed on a computer that has developed the optimal way for cutting the fabric in a way that creates the least amount of waste. In CNC style, the instructions are downloaded into the automated cutter to guide it through each cut.
The process of sewing in contract or industrial sewing is quite different from a single person setting at a sewing machine. When something is being assembled, it is similar to what is done on an assembly line. Each person in the process does one part of the finished product, which is passed through a series of operations before being completed. The single part that a person performs can be sewing on a piece, adding a stitch or clip, or changing the positioning of the material.
The proper selection of the type of stitch depends on the design of the final product and the material that is going to be secured.
The single needle lockstitch is the most common mechanical stitch and creates a smooth seam that does not pucker. It uses one needle and two threads that lock together in the fabric.
Double needle lockstitches are like single needle lockstitches but use two needles that can create puckering.
Zigzag stitch is like the lockstitch but produces a back and forth zigzag pattern.
A cover stitch is a double or triple stitch used for hemming knit fabrics and seams that stretch. One side of the stitch displays two parallel lines, while the underside connects the parallel lines with a zig-zag pattern.
A bar tack is a series of closely formed stitches that reinforce garment areas that are subjected to stress or wear.
The box X stitch is a square box like stitch with a X in the middle and is commonly used for connecting straps or handles to fabric bags.
The mauser stitch is a flatlock stitch that is created by a specialized machine that forms threads into a flat, interlocking pattern. It is an incredibly durable and comfortable stitch when placed against the skin.
The post bed lockstitch is performed by industrial sewing machines in order to stitch heavy weight items like car seats, furniture, and sporting goods.
The blind stitch is an unseen stitch that is used in hems or for joining two pieces of fabric. It is hidden in the folds of the fabric and is only visible when the folded material is pulled apart.
The nine stitches listed above are only a sampling of the different types of stitches used by contract sewing companies. They use the proper type of stitch to fit the needs of the material and product. Stitch selection is related to the dynamics of the material and its use.
The contract sewing industry can transform any type of material into a component for another product or a final finished piece. The list of materials is endless and includes various forms of rubber, plastics, polyesters, and fabrics. An essential part of the sewing industry is choosing the right material for a project, which greatly affects the finished product.
There are several factors that contribute to the choice of materials for a project, which include strength, texture, type of product design, and the purpose of the product. The types of materials used for material operations are quite different from those chosen for a fashion show.
The division of materials is separated by natural materials and man made ones, where natural materials are taken from things from nature while man made materials are produced from chemicals and processing.
Cotton is a very common type of material that comes from a plant. It has been used to produce a variety of items for thousands of years. It is soft, breathable, and lightweight but durable.
As with cotton, linen comes from a plant and is a breathable material. It is an easy material to handle and work with as well as being durable. Linen can be used for upholstery, curtains, and projects that require a strong light material.
Jute is another material that comes from a plant (the bamboo plant). It is very stiff, study, and durable, which makes it ideal for floor decorations and certain types of upholstery.
Wool, another material that has a long history, comes from the hair of sheep. It is a heavy durable cloth that is excellent for projects that involve winter or cold weather.
Silk is a natural protein fiber that comes from the cocoons and webs of spiders and moths. The process of making silk can use any form of web or cocoon material but is generally taken from the ones produced by moths or caterpillars. Silk is a highly regarded fabric that is very soft and lightweight but extremely durable.
Polyester is a synthetic resin where polymers are mixed with the cellulose acetate ester, which is economical, has bright colors, and can be easily shaped. The manufacturing of polyester includes natural chemicals and synthetics. It is a very strong fiber that is highly resistant to stains.
Rayon is made from purified cellulose found in wood pulp. The natural part of rayon is enhanced with chemicals, which makes rayon semi-synthetic. A common form of rayon is viscose rayon that is like cotton. Rayon is a very versatile material that can be formatted, configured, and shaped into a wide variety of forms.
Fiberglass is a material that is made from woven glass fibers. It is lightweight, very durable and strong, weather resistant, and comes in a wide variety of textures. Fiberglass is a type of reinforced plastic that is blended with thin glass filaments.
Vinyl is made from a synthetic resin that contains polyvinyl chloride (PVC) that is tough, durable, and has exceptional flame retardant properties. It has been found to be the most versatile of plastic based materials, which can be easily shaped, configured, sewn, and fabricated. Vinyl is used to make a wide variety of products such as protective gear, shower curtains, and raincoats.
Acrylic fiber fabrics are made from the synthetic polymer acrylonitrile from petroleum based chemicals mixed with various monomers. Acrylics are known for their heat retention and not being breathable. It is used for the production of sports equipment such as tracksuits, hoodies, and athletic pants.
Canvas is a highly durable woven fabric that has multiple uses in the production of a variety of products. It is a cloth that is made from the weaving of either hemp, flax, cotton, or some type of yarn. Canvas is commonly thought of as the main fabric for producing tents, sails, bags, and sturdy cases.
Contract sewing is a vital part of several industries as a support for industrial products that are for commercial and industrial use. In many cases, contract sewing companies partner with a variety of producers to assist them in taking designs and concepts and making them a reality.
The basic function of the contract sewing industry is to help producers who do not specialize in sewing in making items and components that will help them in the completion of their production process. The many years of experience of sewing companies gives them the necessary tools to produce prototypes, offer suggestions for design improvements, and help in developing a production plan.
Many of the fabric components of aircraft are produced by the contract sewing industry. This includes seat belts, upholstery for the seats, carpeting, and the special pouches on the backs of the seats. Products and components for the aircraft industry are closely regulated by the Federal Aeronautics Administration (FAA), which has standards regarding safety and the protection of passengers and members of air crews.
Industries that handle a great deal of cash require money bags that are sturdy and able to take constant use. Bags for handling cash and coins come in a variety of sizes to fit the many types of money handling circumstances. They are designed with tight fitting heavy duty zippers with a locking mechanism. For the organization of cash, numbered security seals that can identify the location of the cash and when it is picked up can be added. The most important function of money handling bags is an assurance of security and safety.
The purpose of shipping bags is for direct delivery services. Much like bags for banks, delivery bags have to be secure, safe, and have a minimum risk factor. Delivery bags are made from extremely strong materials that are capable of keeping items safe as well as ensuring their proper delivery. The main purpose of delivery bags is for use by courier services.
Sewing services for the military have to take a completely different approach to their business model since the military has established standards for every item they purchase using a set of regulations referred to as MIL-STD. Unlike the products that are produced for private and public companies, the military has manufacturing directions and instructions to ensure the quality of the products produced.
There are a wide range of sewing projects for the military that include bags, parachutes, webbed safety harnesses, and medical aid kit bags. Each item has to be produced to exacting and demanding standards.
The most obvious use for the contract sewing industry is the production of clothing. Designers create and plan clothing items and handover the production of their creations to the contract sewing industry that produces prototypes and offers advice regarding design adjustments to enhance and streamline production.
A necessity in air filtration systems are the filters that capture the particulates and allow the clean air to pass through. Those fabric filter bags are produced by the contract sewing industry in a wide variety of sizes and fabrics that include polyester, polypropylene, mesh, nylon, and flannel. The bags are designed to capture airborne pollutants, trap waste, and keep the air and machines clear and clean.
In the marine industry, the contract sewing industry designs and produces protective coverings for boats and marine equipment. The durable materials are designed to protect equipment when they are moored or placed in storage. The materials thaT are used for marine applications are required to be marine grade fabrics. Since not all boats are the same, marine covers come in a variety of styles with a choice of accessories.
The sports and athletic industries rely on contract sewing to produce a wide variety of products that include golf bags, club covers, uniforms, protective gear, training outfits, and several other products. The unique nature of products for sport suppliers is the necessity of sewing team logos on the final products, something that is part of the original product design.
For the automotive industry, the focus of sewn products is for the interior of vehicles. Much like the aircraft industry, the United States Department of Transportation (USDOT) has specific standards that must be followed when producing components for automobile and truck interiors. The main concern is the use of materials that are non-toxic or dangerous.
The unique nature of products for the interior of cars and trucks is the portion of what is done to enhance vehicle interiors is not seen such as airbags that are made to meet strict requirements. Pouches, seat arms, and upholstery are all produced using the contract sewing industry.
Industrial sewing is far different than the types of sewing that is done at home. The equipment is the same type of machinery used in other industries and is just as sturdy and durable. The main difference between industrial sewing equipment and domestic, besides the price, is the type of precision, accuracy, and efficiency that is required by the contract sewing industry.
When a product is produced by industrial sewing, it has to have the appearance and feel of being professionally made with tight seams, clean cuts, and exceptionally tight and secure connections. Aside from these basic features, industrial sewing is much faster and reliable than machines made for domestic use.
Flat bed sewing is used for connecting flat pieces of fabric to create a professional seam. This type of sewing is very similar to what is done on a domestic machine. The main difference is how quickly it is completed with precision and in greater detail.
The bed for cylinder sewing is in a cylindrical shape, which is used for making parts of materials that need to be sewn in a circular fashion. The material goes over and under a column, which makes it easier to complete the stitching. The cylinders can be 5 cm to 20 cm in diameter.
Post sewing is for three dimensional sewing and allows for more space for creating specialty items. The bed is raised and projected such that the material can be shifted in more directions, which makes it possible to keep the material in the machine without the necessity of constantly adjusting it.
A free arm sewing machine is a type of cylinder sewing machine with the added feature of being able to remove the base. This type of sewing is not that unlike any other form of industrial machine since all machines have the ability to remove the base.
The bed extends out from the back of the machine as is seen in a cylindrical machine. The design is for working with items that have a tubular or pipe shape.
Feed off the arm machines are multi-functional with two or three needles to allow sewing to be completed by four threads. It produces two or three rows of chain lock stitches. Feed off the arm machines have a looper in place of a bobbin. The main advantage of this type of machine is its ability to sew heavy or folded fabrics.
There are several different types of feed mechanisms available for industrial and contract sewing. The type of feed mechanism has to fit the sewing operation and type of machine.
Walking Foot: the fabric is moved by feed dogs, teeth like ridges in the throat of the machine. They grip the fabric and gently move it through the machine. Feed dogs prevent slippage of slippery or padded fabrics.
As with any production industry, the contract sewing industry has standards from the International Organization for Standardizations (ISO), American Society for Testing and Materials (ASTM), the United States Military (MIL-STD), and the Occupational Safety and Health Administration (OSHA). ASTM and ISO standards are for product quality and performance, while OSHA standards are concerns for worker safety. MIL-STD standards cover the types of acceptable threads and textiles.
The main concern of the ISO for the contract sewing industry is found in ISO 9001:2008, which is a method of certifying the quality of product management systems. ISO 8239:1987 lists the standards for the sewing industry sewing machine needles and needle holders regarding tolerances and combinations of needles. The main concern is that the needles fit firmly.
The concern for OSHA is the risk factors for employee workstations in regard to the strain on the body due to the posture required to complete sewing operations. OSHA goes into detail regarding the type of chair, worktable, and pedals or mechanisms to operate a sewing machine.
OSHA does not refer to any specific piece of legislation except for the overall concern for worker safety and the requirements of management to provide a hazard free environment.
The ASTM goes into greater detail regarding various factors related to the sewing industry and has a set of precise standards. The standards for the ASTM cover thread, stitches, and seams. Also included in ASTM standards is a long list of standards regarding appropriate textiles for the sewing industry.
MIL-STD standards cover every aspect of the sewing process including a description of acceptable materials and the quality of the thread that can be used. The specifics of the standards cover seam design and positioning.
A canopy is a structure with a connected fabric or metal covering that can give shade or shelter from weather elements such as the sun, hail, snow, and rain. For example, a tent with no floor can be...
Cut and sew is a process for the manufacture of clothing where the design and pattern are printed on the raw cloth from which the garment is cut, ensuring full color, edge to edge print of the design and color...
A protective cover is a sewn fabric that is specifically designed and used for protecting equipment, people, surfaces, and enclosures. Protective covers provide protection from the elements, UV rays, dirt, dust, moisture, and...
A carrying case is a way of conveniently organizing and transporting a collection of similar or dissimilar items for future use. There is a type and kind of carrying case to fit every possible application from protecting and storing cell phones to cases for speaking systems and technical equipment...
Contract manufacturing is a business model in which a company hires a contract manufacturer to produce its products or components of its products. It is a strategic action widely adopted by companies to save extensive resources and...
A hard case is a type of carrying case that is made from molded plastic, aluminum, veneered or laminated wood, or different types of metals. They are the most secure and durable forms of carrying cases and...
A road case is a ruggedly built, highly functional protective container with varying wall thicknesses that is capable of withstanding the riggers and handling of shipping. They are designed to meet...
A tool case is a portable case designed to organize and protect tools and allow easy access and convenient availability. Standard tool cases can be used when working on a project. In addition, specialty and custom-designed tool cases are...
Cases designed to carry special valuables have been part of society throughout history back to the time of the Egyptians and before. Carrying cases are commonly found in any house stored in a garage, tucked away in a basement, or setting on a shelf...