Canopies
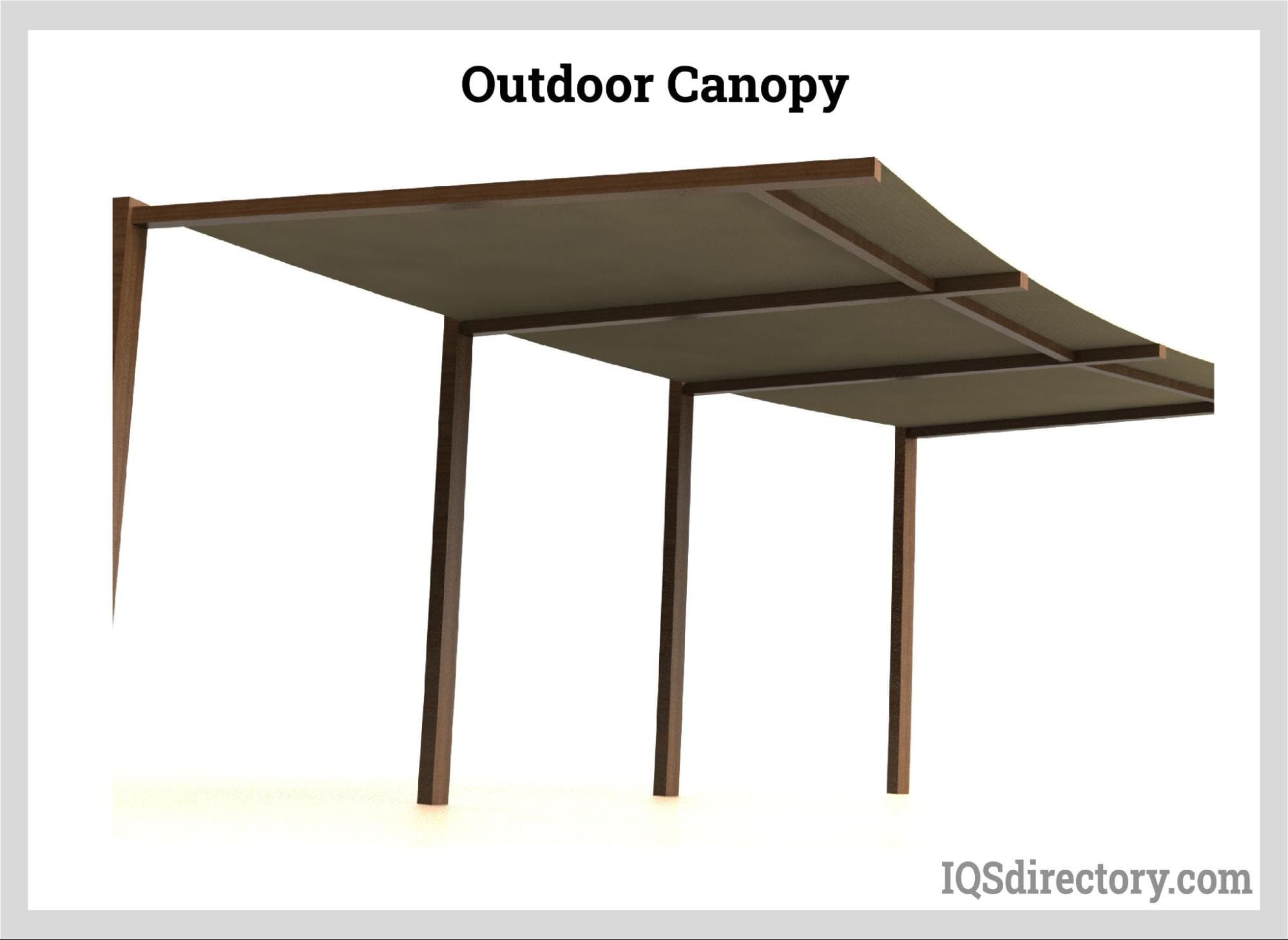
A canopy is a structure with a connected fabric or metal covering that can give shade or shelter from weather elements such as the sun, hail, snow, and rain. For example, a tent with no floor can be...
Please fill out the following form to submit a Request for Quote to any of the following companies listed on
This article shares important knowledge regarding the creation of protective covers, their use, and much more information on protective covers.
You will learn about:
A protective cover is a sewn fabric that is specifically designed and used for protecting equipment, people, surfaces, and enclosures. Protective covers provide protection from the elements, UV rays, dirt, dust, moisture, and harmful substances. The range of protective covers includes a wide spectrum of designs and sizes – from those used to cover small outboard motors, to others capable of covering a freight train with a semi-truck on it.
Protective covers are crafted to precisely fit the items that they are protecting. Depending on their intended use, there is a full assortment of different natural fabrics and certain forms of plastic used to create protective covers. They are very carefully manufactured to ensure tight seams using stitches and sewing techniques that guarantee a secure and uniform fit over for the items they protect.
In many cases, protective covers may also be custom made based on the environment where they will be used. All protective cover manufacturers, in fact, offer a method for customers to choose the fabrics they prefer based on such environmental factors, in addition to the items they will cover.
A wide assortment of high-performance and durable fabrics are used to produce protective covers. Although all fabrics have the same function, there are differences between how they are used. For example, some feature the chemical resistance required to fight ultraviolet rays, while others provide moisture protection.
The range of materials used to manufacture industrial protective covers includes cotton, canvas, and plastics such as polyvinyl chloride (PVC), polyethylene, and polypropylene. The types of fabrics used in the creation of protective covers are chosen based upon the application where they will be used.
Despite the fact that various protective covers are designed to serve a specific purpose, many covers do share many common characteristics. Some traits are listed below.
Canvas is a very popular covering material that is used by the military and in construction. Canvas is a material woven from cotton or linen that relies on their thickness and stiffness to provide strong support. The manufacturing of canvas involves tightly weaving yarn into a plain weave or basic textile weave. In weaving, there are two sets of yarns – warp yarns, which run lengthwise, and weft yarns, which run crosswise along the weave pattern. The warp threads are held steady as the weft threads cross over and under the warp. The fibers used in making canvas are thick and medium to heavy weight.
Cotton canvas is softer than linen canvas. It stretches very easily and is less expensive than linen canvas. When cotton canvas is produced by blending it with synthetic fibers, cotton becomes water resistant and viable for protection of equipment stored outdoors.
Cotton duck is a heavy, plain-woven cotton cloth that is sometimes referred to as just “duck.” As a woven material, duck cloth is categorized as a type of canvas but is sturdier and more resilient than typical canvas due to its tight weave. Cotton duck is tightly woven to be stronger and tougher than traditional canvas material and is waterproof, which makes it ideal as a covering material for many applications. The word “duck” does not refer to the waterfowl but to the pronunciation of the Dutch word for cloth, which is doek.
The production of cotton duck involves the weaving of two fabrics, using one for the warp and the other for the weft. There are different classifications of cotton duck that start at 1 (used as hammock, sandbag, or tent material) and go to 12 (used as light clothing material), with 1 being the heaviest and toughest version of the cloth.
PVC fabric is a synthetic vinyl that is easy to clean, flexible, and flame- and water- resistant. It is a chemically stable fabric that is exceptionally durable due to its molecular structure, which includes chlorine atoms attached to carbon chains. This configuration of atoms is what gives it its resistance to oxidation reactions, a factor that helps PVC fabric provide a long life of usefulness.
To enhance its performance, PVC fabric has plasticizers added to make it softer and more flexible. Because of these qualities, PVC fabric is easy to install, sew, cut, and shape, which makes it ideal for creating protective covers. The long useful life of PVC fabric is another factor to consider since it drastically lowers its cost over time when compared to other covering materials which may need to be replaced more frequently, and is one of the reasons that it is so widely used as a protective cover material.
Polyethylene fabric is woven material, or scrim, placed between two layers of plastic coating. It is a very low-cost fabric that is used for a wide variety of applications due to it being environmentally-friendly and recyclable. Polyethylene fabric is a thermoplastic made of crystalline structures from petroleum based plastics. It is referred to as an olefin fiber made from polyolefin that is similar to polypropylene.
Although polyethylene can be used alone, it is normally blended with other synthetic fibers or natural ones. As with other plastics, polyethylene comes in several densities, which include very low density, low density, linear low density, medium density, cross linked, high density, and ultra-high density. The various density levels are used to classify plastics in regards to what materials they may fold and what applications they may be used for.
Polyethylene fabrics are widely used in the manufacture of protective covers due to their strength, durability, and resistance to abrasions. A popular use of the fabric is protection for storage containers and CNC machines.
Polypropylene is a synthetic thermoplastic polymer made from petroleum that produces an exceptionally strong woven fabric known as polypropylene yarn. The strength of polypropylene is due to not having any active dyes that can alter the chemistry of a polymer. The result of having no dyes is a strong, fade- and stain-resistant fabric.
The process for manufacturing polypropylene fabric can be woven or nonwoven depending on how the fabric will be used. It is a very popular fabric due to its low cost, flexibility, light weight, durability, fire resistance, and moisture resistance. In its woven form, polypropylene is used for applications ranging from flood bags to transporting various agricultural products (fruits, vegetables, rice, and even flour) due to its extremely tight weave. In its unwoven form, PP is used regularly as an air, or liquid, filter material or as a wiping cloth due to its absorption capability.
Nylon was the first synthetic fiber and is a thermoplastic with impact- and abrasion- resistance. There are a wide range of types of nylons, with each type having different properties in regard to strength and wear resistance. The main quality of nylon that makes it so popular is its tensile strength, which is comparable to certain metals. Its high strength makes it ideal for producing protective coverings, with nylon 6 and 66 (based on the Denier rating scale used to measure the weight and thickness of threads in a fabric) being the most common types used.
Nylon is weather-resistant, unaffected by biological erosion, and features anti-bacterial and anti-mold properties, making it ideal for use as an outdoor protective covering. As with many of the other protective cover fabrics, nylon is lightweight as well as easy to handle and form.
Industrial sewing is a necessity for the creation of protective covers and other heavy duty fabric products. It provides a wide range of services that include sewing different materials, embroidery to decorate fabric materials, and embossing to stamp designs and images to cotton, canvas, PVC, vinyl, and nylon fabrics.
Any design, product, or covering can be created by industrial sewing due to the wide variety of specialized machines. It is this diversity that makes it possible for the industrial sewing industry to produce custom-designed protective covers to fit any machine, device, or piece of equipment. Below, we briefly discuss not only the machines used, but, additionally, some other important items to consider regarding the production of protective covers.
Industrial sewing machines that are used to make protective coverings are professional- grade machines designed to handle large-scale projects and the sewing of tougher fabrics than their household counterparts. They are capable of operating longer and are built of materials that are unlikely to break or need repair.
An industrial sewing machine can run for several hours without any need to replace its needle or other vital parts. Their main characteristic is their ability to handle high-volume jobs at exceptionally-high speeds through their ability to sew thousands of stitches in a short period of time.
When discussing industrial sewing machines, it is essential to understand that there is an endless number of types, designs, and configurations due to the nature of countless industrial sewing applications. Even in the specialized area of protective covers, there are several different machines designed to better create and manufacture a specific type of cover based on the specific type of material used.
In the case of protective coverings, the quality of the stitches is critical since coverings are placed in demanding conditions and the stitches are where environmental factors are most likely to affect a protective cover. Industrial sewing machines produce much tighter, more secure stitches than the typical household sewing machine and, as a result, afford commercially-produced protective covers with greater longevity.
Industrial sewing machines are also capable of producing a wider variety of stitches due to the nature of the fabrics that have to be stitched. The variety of stitches available makes it possible to refine and perfect their use in order to exactly meet the parameters of an industrial sewing project. Since there are so many types of stitches, industrial sewing machines are programmed with their stitches and patterns. To perform a particular stitch pattern, operators simply enter the type of stitch desired into the machine and guide the material through the machine.
There are so many factors involved in producing industrial stitches, including the number of threads and needles used, the type of seam, and the type of stitch required, that an official organization has been created to classify them in order to create conformity among industrial manufacturers of protective covers. This organization is known as the American Society of Testing and Materials (ASTM) and can explain more about their classification system through their website.
The choice of thread is another important factor when creating protective covers. A key factor in the selection of thread is its thickness, which affects its strength, diameter, type of sewing machine to use, and how visible it will be. Industrial threads for sewing protective covers are strong, smooth, and come in various thicknesses.
Threads are classified by their tex number, which is in reference to their mass in grams per 1000 meters of thread. If 1000 meters of thread weighs 25 grams, it has a tex number of 25. Higher tex numbers mean that the thread is thicker and stronger. Threads used for the manufacture of protective covers have a tex number greater than 69. When choosing a thread for making a protective cover, the tex size is one of the determining factors.
In addition to tex numbers, there are other systems used to classify threads. The Denier system, for example, is also commonly used to classify threads and refers to their weight in grams per 9000 meters of material; many manufacturers have ticket numbers that reference the Denier size. Thread sizes may also be classified by government size such as those established by the U.S. government.
Choosing the correct size of thread is another critical consideration for the fabrication of protective covers since it is also another standard used for meeting the specified requirements of a project. In the case of industrial threads, size is used to measure the number of threads woven into one square inch of fabric.
Another important factor related to the industrial sewing of protective covers is determining whether the process requires bonded or non-bonded thread. Non-bonded threads are minimally processed and are labeled as soft threads. They are uncoated, heat set, and conditioned before being wound. Non-bonded threads are used at slower processing speeds and are less expensive than bonded threads.
Bonded threads are used with high-speed, multi-directional sewing processes. They have a resin coating that prevents the plies of the thread from opening. Bonded thread has a smooth, even finish that keeps the threads together and is resistant to friction and abrasion. Bonded thread is more frequently selected for the stitching of heavy-duty protective covers.
The type of thread used for producing protective covers is, additionally, dependent on these factors:
The basic principle of industrial sewing machines is their needle system, which is determined by various characteristics including their size, length, point, and type of metal used to construct the needle. Needle systems for industrial sewing machines are specific so that the needle matches the machine.
Needle systems consist of two sets of numbers, with each set separated by an “X” that is printed on the front of the packaging and used to classify the type of needle inside. Printed with the needle system is the size of the needle and the type of point. The size of the needle has a numerical reference to its size and gauge and is presented in both European (metric) and American classifications (ie 90/14). Needle points are indicated by a letter or set of letters which describe the type of point of the needle. Larger needle sizes are thicker and stronger and are used with higher tex and Denier threads.
There are two common sizing systems, metric-based and US-based, with sizes for the metric system ranging from 35 to 250; these sizes refer to the size of the needle in hundredths of a millimeter. US sizes are from 6 to 28. Packages of needles have the metric and US sizes printed as NM metric size/US size. Larger needle sizes create larger holes in the material and allow for the use of larger diameter threads.
Needle points are designated by letters and indicate the point or tip of the needle. Different needle points determine the type and appearance of the hole created in the material as well as the type of stitch. There is a wide range of needle points, all of which are indicated by one or more letters.
A few of the needle points are:
Precise cutting is a critical aspect of the production of protective covers since it determines the size and fit of the cover for an application. The cutting process is dependent on the type of fabric, the cutting pattern required to produce the least amount of waste, and the types of cutting patterns provided by specific computer software.
Cutting machines used for the production of protective covers are very large and come in a variety of designs and sizes. Included in the types of cutting machines used for creating protective covers are multilayer machines, digital cutting machines, CO2 laser cutters, and die cutting machines.
Each of the aforementioned elements required in the protective cover creation process is completed with precision and accuracy to ensure the quality of the cover material and how it best fits to a specific application. Since these elements vary greatly among jobs, protective covers are essentially specially-designed based on such features.
Protective covers are used as a method for protecting inventory, assets, and machinery and are found in several industries and manufacturing operations. An essential part of protective equipment covers is how they are designed since they need to be specifically purposed and fabricated to give full protection to equipment.
Patterns are created by computer aided design (CAD) software using the parameters of the items to be protected and covered. A 3D rendering of the final design offers a conceptualization of the protective cover and its appearance. It is from this computer-generated perception that the material for the protective covering will be cut, sewn, and manufactured. Some of the items requiring such protection are listed below.
The technical nature of CNC machines requires that they be protected from liquids and potentially-harmful particulates. The natural inclination to protect such delicate equipment is to use shrink wrap fit comfortably over a CNC machine. Due to where CNC machines are located and the industrial environment they operate in, however, shrink wrap is not sturdy enough to offer the best protection.
For greater security and a more durable covering, CNC machines should be paired with a cover featuring material that conforms to the configuration of the CNC machine and one providing a zipper to open or close this protective layer around it. The material of the cover must be sturdy, durable, and abrasion resistant. The cover must be capable of withstanding the conditions of a harsh manufacturing environment.
Woodworking tools have to be protected from dirt, dust, and moisture when they are not in use. These factors can deteriorate woodworking tools and give them a shorter service life. Heavy-duty protective covers made of durable and breathable materials are designed to protect valuable woodworking tools and prevent any form of damage.
The breathability of protective covers prevents rust through the use of strong, coated, cotton duck material that blocks condensation and the accumulation of moisture. These versatile covers are used to cover saws, planes, sanders, drill presses, and lathes.
The function of a protective boat cover is to protect it from the build up of moisture and debris, as well as providing a barrier from UV rays. Boat covers help in maintaining the condition of a boat and increases its longevity. There are several varieties of boat covers, ranging from ones that only cover more critical portions of a boat to others that cover the whole boat. The majority of boat covers are made of one of the polymer fabrics which can better fit snuggly and uniformly over a boat.
Car covers have become very popular as a method for protecting the finish on a car in any climate. As cars are exposed to the elements over time, their exterior and interior begin to show wear and degradation. Car covers are a simple and easy-to-use solution which can provide exceptional protection, enhance and maintain the appearance of a car, and extend its useful life.
A basic concern for cars is rust, which is one of the prime reasons for having a protective car cover. A polymer-based car cover provides excellent moisture protection. As with boat covers, car covers are made from one of the polymers and are weatherproofed.
Equipment protective covers are, perhaps, the most unique types of protective covers due to the fact that a different cover is required for every type of situation and piece of equipment. These covers are designed to protect sensitive equipment from the elements and atmospheric conditions. Since every type of equipment or device is different, equipment protective covers have to be custom-engineered and designed using fabrics that fit their precise requirements and the specific environment where equipment is employed.
There are several necessary characteristics required for equipment protective covers, which include tear resistance, tensile strength, adhesion, being waterproof, low-temperature resistance, and resistance to decay, mildew, and acids. The strength and endurance of equipment protective covers is a necessity based on the conditions where they are typically employed and the value of the equipment normally covered. As a result, equipment protective covers are made from the most durable types of polyolefin fabrics.
The benefits of protective covers are a necessity for protecting and preventing damage to expensive equipment and tools. Dust, dirt, accumulated moisture, UV rays, and temperature changes can significantly harm and damage materials and equipment. Protective covers ensure that items are kept safe from these damaging elements so they may have a longer useful life. Below, we examine some of the protections and other positive features provided by protective covers.
Continuous exposure to the elements such as water and salt causes rust and corrosion, which reduces the strength of metals and makes machinery unserviceable. Additionally, UV rays from the sun damage plastics and composite parts by causing discoloration and cracking.
Heavy-duty protective covers are designed to block out the sun, keep moisture out, and form a permanent barrier against the environment. Their durability and strength provides a longer, healthier lifespan for materials and equipment.
Fluctuations in temperature can be severely damaging to equipment and machinery. Constant changes can cause expansion and contractions that can warp, crack, and damage materials. Extreme heat can be especially damaging to sensitive instruments and electronic components.
In many ways, a protective cover serves as a form of insulation that maintains equipment at a set temperature and diminishes the effects of temperature and climate changes.
Of the many potential hazards for machinery, particulates are the most damaging but the most difficult to see. These extremely small specks of material and dust can infiltrate electronic controls and instruments where they can etch, scratch, and damage control boards. A sufficient build up of these tiny particles can even become a fire hazard.
As a defense to potential particulate damage, a protective cover performs like housing for equipment and shuts out exterior conditions and potential harm.
When equipment is being transported, it is exposed to flying debris, moisture, road grime, and the elements. These uncontrolled conditions can cause severe harm and permanent damage to equipment, making robust, secure, and sealed coverings a necessity.
Placing equipment in storage has an enormous potential for permanently damaging equipment, whether it is in a warehouse or outside. Protective covers are a cost- effective, preventative solution to these risks made of lightweight, strong, flexible, and tightly-secured fabric.
All protective covers are made of fabrics designed to last. They are highly resilient, chemical resistant, and capable of preventing degradation, corrosion, wear, or the buildup of mildew.
The various synthetic fabrics used to manufacture protective covers can stretch to meet the demands of equipment but still retain their original strength.
One of the main functions of protective covers is to prevent water damage or the accumulation of water. In many cases, this aspect provides the fundamental reason for their use.
It can easily be said that there is a protective cover for every possible set of conditions, regardless of how severe or potentially-damaging the circumstances may be. It is this quality of protective covers that makes them such a vital and necessary tool. Protective covers are easy to use, easily cleaned, and exceptionally durable. They are a tool that can be continuously used for many years without tearing, rupturing, or cracking. Their resilience is what makes them the ideal solution for product protection.
A canopy is a structure with a connected fabric or metal covering that can give shade or shelter from weather elements such as the sun, hail, snow, and rain. For example, a tent with no floor can be...
Contract sewing is a specialized industry that provides services to manufacturers for production of a wide range of products using highly skilled workers and technologically advanced sewing machines. The strength of the contract sewing industry is its ability to perform any type of sewing services...
Cut and sew is a process for the manufacture of clothing where the design and pattern are printed on the raw cloth from which the garment is cut, ensuring full color, edge to edge print of the design and color...
A carrying case is a way of conveniently organizing and transporting a collection of similar or dissimilar items for future use. There is a type and kind of carrying case to fit every possible application from protecting and storing cell phones to cases for speaking systems and technical equipment...
Contract manufacturing is a business model in which a company hires a contract manufacturer to produce its products or components of its products. It is a strategic action widely adopted by companies to save extensive resources and...
A hard case is a type of carrying case that is made from molded plastic, aluminum, veneered or laminated wood, or different types of metals. They are the most secure and durable forms of carrying cases and...
A road case is a ruggedly built, highly functional protective container with varying wall thicknesses that is capable of withstanding the riggers and handling of shipping. They are designed to meet...
A tool case is a portable case designed to organize and protect tools and allow easy access and convenient availability. Standard tool cases can be used when working on a project. In addition, specialty and custom-designed tool cases are...
Cases designed to carry special valuables have been part of society throughout history back to the time of the Egyptians and before. Carrying cases are commonly found in any house stored in a garage, tucked away in a basement, or setting on a shelf...