Air Pollution Control Equipment
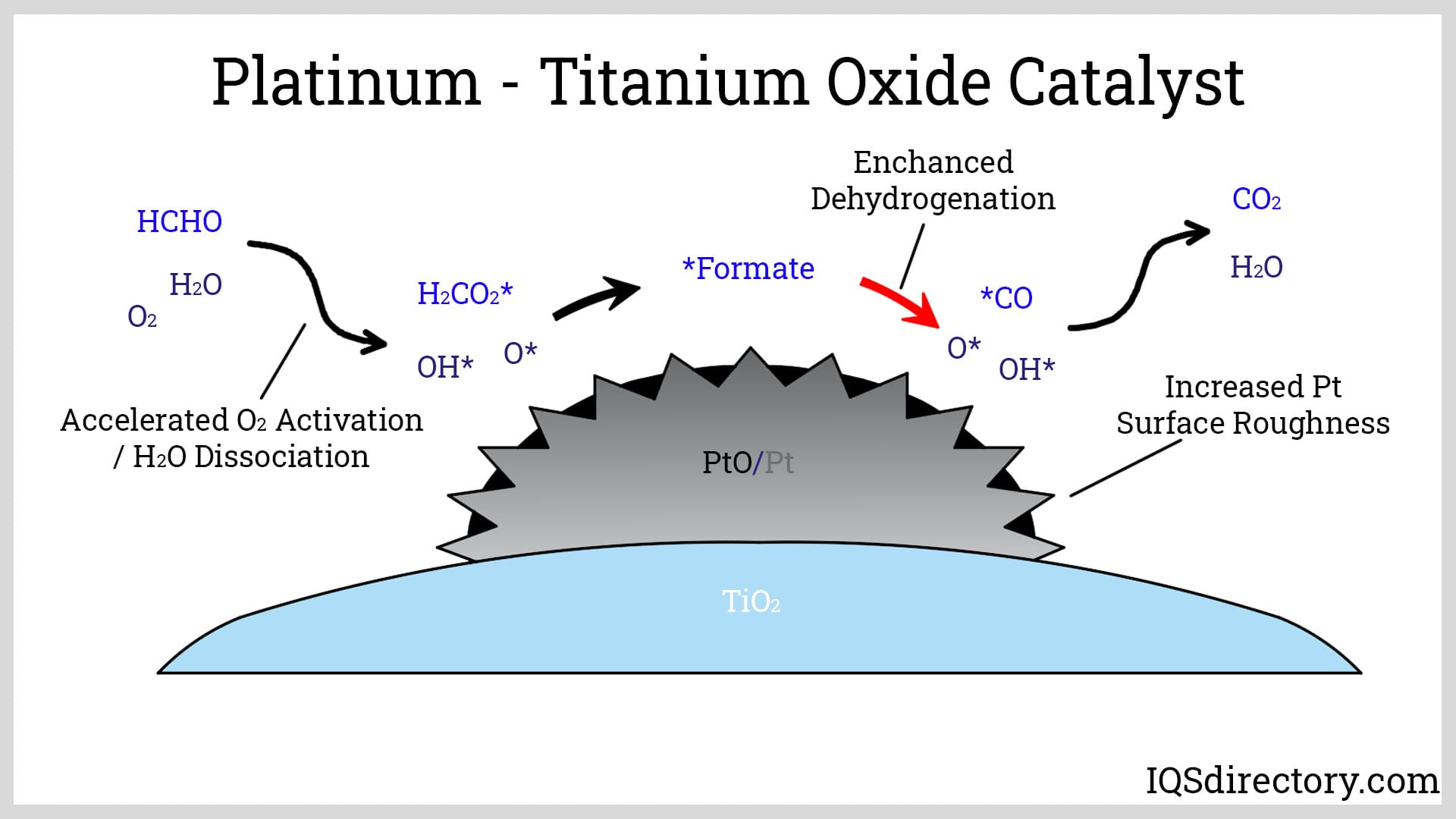
The term "air pollution" is used so frequently that many of us believe we have a complete understanding of its meaning. Scientists and environmentalists have made so many predictions of the negative effects...
Please fill out the following form to submit a Request for Quote to any of the following companies listed on
This article will provide industry insights on oxidizers.
Read further to learn more about:
Oxidizers, also known as incinerators, are devices used to process waste gases or plant emissions containing harmful pollutants by thermally breaking them down into simpler, stable compounds. They function like burners or reactors, where the preheated waste gas is oxidized at temperatures reaching up to 1832°F (1,000°C).
Waste gases containing volatile organic compounds (VOCs), organic hazardous air pollutants (HAPs), or odors are burned to produce carbon dioxide and water vapor. These gases may also include non-organic pollutants such as halogenated and sulfuric compounds. The combustion process generates acid gases, which can contribute to smog and acid rain. Similar to scrubbers, oxidizers eliminate harmful compounds and release cleaner air or vapors.
The US Environmental Protection Agency (EPA) regulates the emission of harmful compounds under the Clean Air Act (CAA). The EPA mandates that industrial facilities install pollution control systems to comply with the emission limits outlined in the CAA. Industries that must adhere to these regulations include oil refineries, coal-fired and gas power plants, chemical plants, cement plants, steel mills, and glass factories.
Air pollutants are substances suspended in the atmosphere that can harm human health, the environment, and property. They are categorized into three types: hazardous air pollutants, criteria air pollutants, and greenhouse gases. Among these, hazardous air pollutants are the most dangerous, as even at low concentrations, they can cause severe health issues or even death. To address this, industries have been developing and implementing technologies to remove hazardous pollutants and transform them into less harmful compounds.
Thermal oxidizers decompose organic or hydrocarbon-based hazardous air pollutants (HAPs) and volatile organic compounds (VOCs) into carbon dioxide and water. The process begins by directing the waste gas stream into the combustion chamber, where air is typically introduced via a forced draft fan. This air is controlled to ensure that the combustible compounds are fully burned. Additionally, the air helps to dilute the waste gas stream to safe levels.
To ensure safe operation, the concentration of combustible gas in the combustion chamber should not exceed 25% of the lower explosive limit (LEL). However, with proper upstream monitoring, excursions up to 50% of the LEL may be permitted.
A pilot burner or igniter starts the combustion of the fuel gas in the thermal oxidizer burner. The thermal oxidizer is then heated to its specified operating temperature. Depending on the amount of combustible material in the waste gas stream, the incoming waste gas may release enough heat to sustain the process. If the combustion is not self-sustaining, additional auxiliary fuel is introduced to maintain the required chamber temperatures.
The amount of auxiliary fuel required can differ among various types of oxidizers. For instance, catalytic oxidizers utilize catalyst media to facilitate the reaction. A catalyst speeds up a chemical reaction without being consumed in the process. This allows catalytic oxidizers to operate at lower temperatures compared to thermal oxidizers, resulting in reduced fuel consumption.
Another method to maintain chamber temperatures while minimizing the use of auxiliary fuel is to utilize the heat from the exhaust gases. After combustion, the exhaust gases carry significant heat energy that would otherwise be wasted if released directly. Heat exchangers capture and transfer this heat from the exhaust air stream to the incoming air stream. This preheated air requires less energy to ignite when entering the chamber. Additionally, ceramic media within the combustion chamber, as seen in regenerative thermal oxidizers (RTOs), can also preheat the air. The ceramic media absorbs heat from previous reactions and transfers it to the incoming gas stream.
The exhaust gasses are released into the atmosphere through a stack. A stack is usually constructed to create a means of discharging hot flue gas to an atmospheric chamber. Along the stack are a series of probes for taking samples. The samples are processed by emissions monitoring systems.
If the waste gas stream contains acid-forming compounds and particulate matter, additional downstream equipment may be necessary. Wet scrubbers are commonly used to remove acid gases.
A wet scrubber introduces a scrubbing liquid into the waste gas stream. The contact is made by spraying the scrubbing liquid down into the waste gas flowing from the bottom of the scrubbing vessel. Common equipment used to remove particulate matter are cyclones and electrostatic precipitators.
In cyclone separators, the gas stream is introduced tangentially to the inner walls of the cyclone. This causes the gas to change direction and swirl around the chamber. Centrifugal force then causes the particles to be separated from the gas, with the particles collecting at the bottom of the conical section of the separator.
Wet electrostatic precipitators (WESP) are a particulate matter control method that uses an intense electric field to charge and capture particles and droplets onto a collection surface. A discharge electrode gives particles in a gas stream a negative charge as the gas flows through the collection section. With a negative charge, the particles are attracted to the grounded surface of the collection electrode. WESPs operate at low pressure drop and have over 90% collection removal efficiency.
The key factors in oxidizer design are temperature, residence time, and turbulence.
Air-polluting compounds in waste gasses ignite at different temperatures. To accommodate this, the combustion, or oxidation, chamber is kept at temperatures exceeding 1600°F (870°C). Thermocouples monitor the temperature as controls modulate the gas burner. The process temperatures are high enough to ensure high levels of VOC destruction.
Operating temperatures in oxidizers can vary depending on the type and concentration of VOCs. Higher temperatures generally result in greater destruction and removal efficiency (DRE) of the oxidized compounds. To achieve the desired DRE, the thermal oxidation process must exceed the autoignition temperature of the substances involved.
Residence time refers to the duration that waste gases remain in the combustion chamber. For various VOCs, the required destruction and removal efficiency (DRE) must be achieved within a residence time of approximately 0.1 to 1 second. While increasing residence time can allow for lower chamber temperatures, it is important to balance this with considerations of capital and operating costs.
Shorter residence times necessitate higher chamber temperatures. If residence time is reduced without raising the chamber temperature, the destruction and removal efficiency (DRE) is significantly compromised, leading to unburned VOCs. Typically, VOC destruction efficiencies reach 99.9% with residence times of no more than one second and chamber temperatures ranging from 1650 to 2190°F (900 to 1200°C).
Turbulence enhances the efficiency of a thermal oxidizer by ensuring that all VOCs in the waste gas stream are fully burned. Chaotic fluid flow improves mixing and mass distribution, preventing gases from accumulating in stagnant areas. Many thermal oxidizer designs incorporate specific chamber geometries to promote turbulence and optimize the combustion process.
Thermal oxidation is a widely used method for controlling VOC emissions. Alternative methods include adsorption, absorption, condensation, membrane filtration, and catalytic oxidation. Thermal and catalytic oxidation are especially preferred for their high effectiveness in treating gaseous pollutants and achieving high removal efficiencies.
Thermal oxidizers primarily rely on combustion for the oxidation process. The three main types are direct-fired, regenerative, and recuperative thermal oxidizers, each differing in their methods of heat utilization and recovery. Additionally, there are flameless thermal oxidizers and enclosed vapor combustion units, which provide alternative approaches for managing and treating waste gases.
The firing chamber typically operates from 1400°F to 2200°F (760–1204°C) with an airflow rate of 500 cu ft up to 50,000 cu ft (14.2 to 1416 cu m) per minute, with the DFTO designed for the necessary residence time to achieve the required DRE. Once the DFTO processes the emissions, safe air and water vapor are released from the chamber. DFTOs have an efficiency rate for hydrocarbon destruction of as high as 99.9999% and achieve emission compliance with the least amount of capital investment.
The process starts by heating the incoming waste gasses across ceramic heat recovery media. The gas temperature is then raised from ambient to near combustion temperatures. As most of the heat is absorbed by the incoming gasses, the ceramic bed becomes cooler, resulting in less heat transfer. The control valves then redirect the intake flow to another ceramic bed that has been previously heated. The cool ceramic bed undergoes a heating phase from the exhaust gasses, preparing it for another heating phase.
Regenerative thermal oxidizers have thermal efficiencies of around 92-95%, with destruction removal efficiencies of more than 95%. This results in less auxiliary fuel consumption and less heat released into the atmosphere.
The heat exchangers can be either plate or shell-and-tube heat exchangers. Thermal oxidizers with plate heat exchangers require lower investment and have higher thermal efficiency at lower operating temperatures. However, at higher operating temperatures, shell-and-tube heat exchangers are preferred. Thermal efficiencies of thermal recuperative oxidizers range from 50% to 80%.
Catalytic oxidizers function similarly to thermal oxidizers but include a catalyst bed that accelerates the reaction rate of VOCs at a given temperature. This allows catalytic oxidizers to achieve removal efficiencies comparable to thermal oxidizers, but at lower temperatures. However, this process comes with the drawback of requiring additional maintenance and replacement of the catalyst media, which can degrade or sinter over time. Additionally, some catalysts can become deactivated in the presence of certain compounds or catalyst poisons, such as sulfides and halides.
In a catalytic oxidizer, the air and waste gas stream are drawn in and can be preheated using either regenerative or recuperative methods. Regenerative catalytic oxidizers use alternating ceramic beds for heat recovery, while recuperative catalytic oxidizers utilize heat exchangers. After preheating, the stream is ignited and heated in the combustion chamber. Unlike thermal oxidizers, the primary function of this initial heating is not to destroy all VOCs but to raise the temperature to approximately 392 to 932°F (200–500°C) to initiate the catalytic reaction. The heated gases then pass through the catalyst bed, where they are further broken down, achieving a destruction removal efficiency of over 95%.
The primary destruction of VOCs in a catalytic oxidizer occurs when they contact the catalyst. As the stream flows through the catalyst bed, VOCs are adsorbed onto the catalyst's surface, which contains active sites with a high affinity for atoms like oxygen and hydrogen. At these active sites, VOC compounds more easily break the bonds between their atoms, as these bonds are attracted to the catalyst. New, more stable bonds form, resulting in the reaction products. This process releases the VOCs from the catalyst, freeing up the active sites. Consequently, less heat is needed to facilitate oxidation compared to thermal oxidizers.
The choice of catalyst in a catalytic oxidizer depends largely on the specific VOCs and contaminants present in the waste gas stream. Catalysts can be selective, efficiently facilitating reactions for certain compounds while being less effective for others. To enhance overall performance, some systems use combinations of catalysts to achieve a synergistic effect. Catalysts are generally classified into two categories: metal oxides and noble metals.
Catalyst systems can also be categorized according to their method of contacting the gas stream. The catalyst must have a shape and distribution that can maximize the contact of the active sites to the VOCs in the stream, especially if the VOC concentration is small and the gas mixture flow rate is high. The methods of enabling catalyst contact are enumerated below.
When air pollution regulations were first introduced, identifying an effective system for controlling gaseous emissions was challenging. However, advancements in technology and process development have significantly improved these systems. Today, there are a variety of options available that are designed to meet regulatory requirements.
When choosing a direct thermal oxidizer, considerations include capital investment, operational costs, and safety. Direct thermal oxidizers are typically used for processes that involve:
Recuperative thermal oxidizers have higher capital costs than DFTOs but lower fuel consumption. They are good for processes with high VOC levels, small air flow rates, and batch-type cycling. They are typically used with processes that have:
Direct catalytic oxidizers share a similar design with direct thermal oxidizers but use catalysts to lower the operating temperature. They are employed in processes that involve:
The advantages of recuperative catalytic oxidizers include reduced fuel consumption and cost-effective construction materials. They are not suitable for systems with catalyst poisons but are used in processes involving:
Regenerative thermal oxidizers offer lower capital and operational costs, higher airflow, low VOC concentrations, and thermal effectiveness ranging from 92% to 95%. They are suitable for processes with:
The term "air pollution" is used so frequently that many of us believe we have a complete understanding of its meaning. Scientists and environmentalists have made so many predictions of the negative effects...
An air scrubber is an air purification system that removes particulate matter from the air through the use of moisture or by cooling or filtering the airstream as it enters the scrubber...
Any unwanted particle present in the air that pollutes the environment and adversely affects the health of living organisms is called air pollution. These particles can be poisonous and may lead to many serious health issues such as...
Air filters are devices used to remove airborne particles, pollutants, and microorganisms hazardous to health and the ecosystem. In industrial facilities, air filters preserve the quality of products and materials and protect critical equipment from damage...
A baghouse is a pollution control device that uses tubes, envelopes, or cartridges to remove, capture, and separate dirt, particulate matter, and dust from the air of a manufacturing or processing facility. The main components of a baghouse are the media or bags used to filter the particles from the air as it passes through the system...
A central vacuum system is a cleaning mechanism that is built into a building for ease of use, access, and maintenance. Vacuum and pressure are created by a centrally located motor to remove dirt, dust, and debris...
A dust collection system is a system that removes particulate contaminants from the air in production facilities, workshops, and industrial complexes. The system cleans air by forcing it through a series of airtight filters...
Explosion-proof vacuums are vacuum systems that use compressed air, electricity, and cyclonic motion to prevent the ignition of gasses or vapors and operate at temperatures that will not ignite a possibly flammable atmosphere. Replacing motors with...
A HEPA filter is a high efficiency pleated air filter capable of capturing extremely small particulate matter down to particles that are the size of a micron (µ), or a micrometer, which is 1/1000th of a meter...
An industrial vacuum cleaner is a heavy duty piece of cleaning equipment designed to remove debris, industrial waste, construction refuse, and matter that remains after a manufacturing process or construction project...
A jet dust collector is a suction filtration unit that pulls dust ladened air into a filtration system that collects particulate matter and releases clean air. The filters of jet dust collectors are cleaned by compressed air that uses...
During the Industrial Revolution, when companies began producing high volumes of industrial waste like fine dust, wood dust, and other particles, an American, in 1852, S.T. Jones, applied for the first dust collector patents, a single bag filter...
Vacuum cleaners use suction to collect dirt, dust, waste products from industrial processes, and other debris for disposal, recycling, or reuse. They are mainly used for building maintenance and cleaning of industrial space...