Rubber Bushings
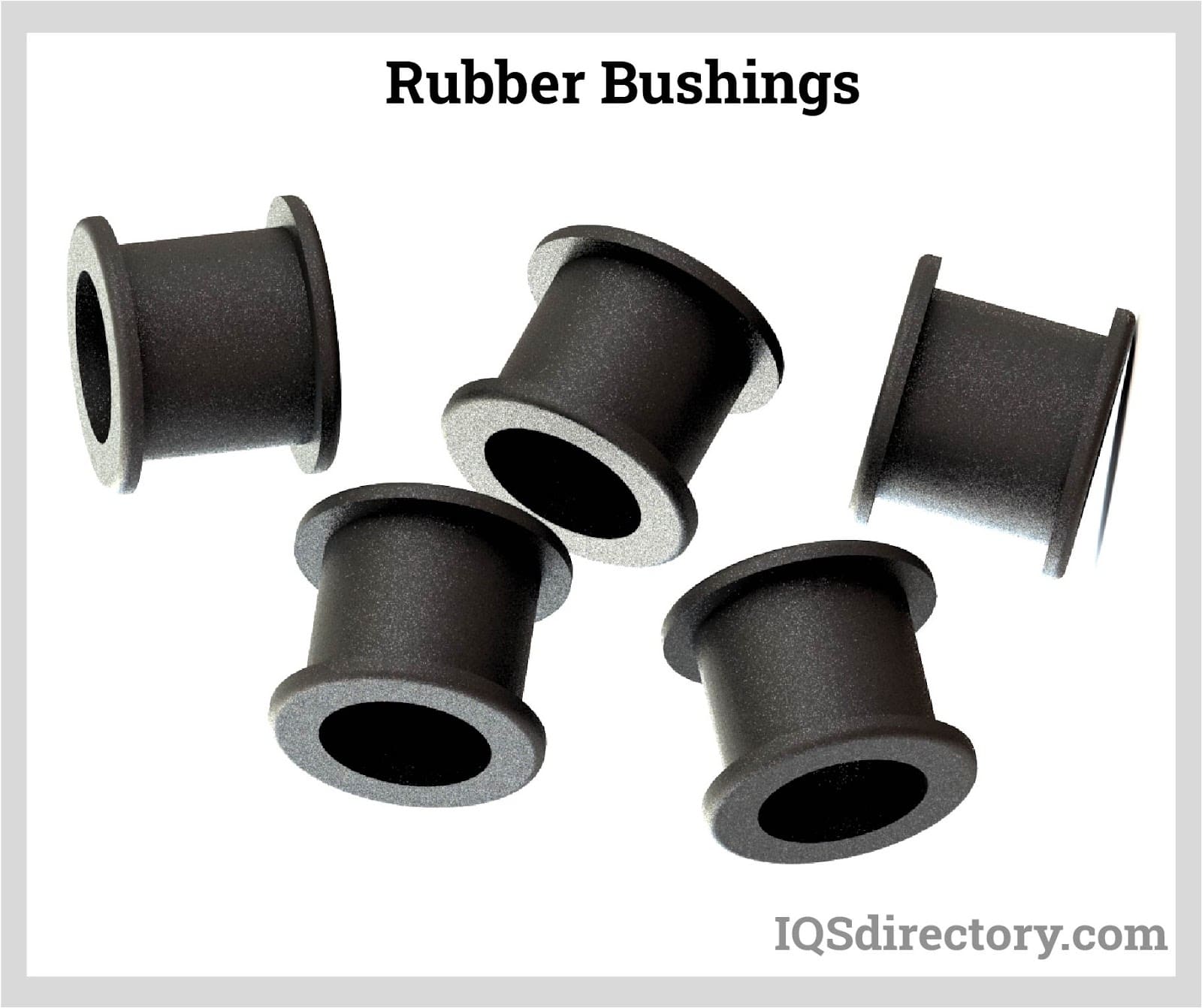
Since the first rubber product appeared on the market, there have been continuing innovations that have increased and broadened its use. The many benefits of rubber products include its durability, resilience, enhanced cycle life, and its flexibility to be molded and shaped into a wide array of forms and configurations. These multiple characteristics have made rubber the staple of several industries.
Aside from its natural properties, rubber can be combined with other materials to improve and increase its basic resilience. These combinations produce a variety of products that are stronger, more durable, and lasting. There is an endless list of the ways that rubber has been transformed and shaped. Some of those methods include extrusion and molding.
The extrusion process uses force to press rubber through a die profile to create a wide range of products from ones used for medical devices to others that serve as sealants and linings. As with all types of rubber processes, synthetic rubbers, such as silicone and viton, are used for specialized applications that require materials that are resistant to chemicals, heat, and weathering.
A very common and old method of shaping rubber is the use of molds, which place the rubber in a two part mold to produce intricate designs of complex and irregular shapes. For the molding process, rubber material is melted before being placed in the mold. Diaphragms and seals are made using this process because molds can be designed with dimensions that perfectly match the dimensions of their use in the final product.
One of the many uses of rubber is the manufacturing of rubber rollers, which are chemical resistant, shock absorbent, and wear resistant. In the printing industry, rubber rollers are used to apply ink to printing presses since they cannot be contaminated or damaged by the ink. A major function of rubber rollers is as drive rollers for converters and web machines.
A major concern for many products is protection from wear, friction, and weathering. In some cases, rubber is bonded to metals using various forms of adhesives to form a tight and secure connection as well as exceptional protection. The types of metals that bond easily with rubber include various grades of steel, some aluminum alloys, and polyamides. Aluminum alloys have become popular as materials for rubber bonding due to their light weight.
A very common use for rubber is rubber tubing, which is used in a wide array of machinery and vehicles as well as the medical and health fields. Much like rubber extrusion, rubber tubing is formed from rubber and its synthetic forms such as latex, neoprene, silicone, viton, and ethylene propylene diene monomer (EDPM). The resilience and flexibility of rubber tubing has made it ideal for several uses. Easy to manufacture and shape, rubber tubing is always the first choice for tubing applications.
It has always been known that rubber is excellent material for absorbing and withstanding shocks and vibration. It is used on the legs of machines that vibrate during operation and cushioning for other applications. The vibration absorption of rubber includes dampeners, bumpers, mounts, padding, and foam. The use of rubber to prevent vibrations in equipment extends the usefulness of the equipment and protects it from wear.
Rubber has become a common part of several forms of equipment as diaphragms to stop flow in a pipe or as material to support bumpers on cars. As a recyclable material, it has become an important part of multiple devices.
The rubber extrusion process allows different rubber materials to be shaped into useful products. Products like weatherstripping, rubber seals, rubber grommets, and rubber bushings are all results of the rubber extrusion process. Extruding involves pressing rubber through a die which shapes the rubber and cuts away material, leaving a rubber profile. The dies can be designed to produce almost any shape imaginable, so rubber extrusions can be custom made to satisfy a diverse range of requirements.
The properties of an individual finished product depend on the raw rubber stock used to make it, the extrusion process it underwent and any secondary processes. Since rubber exists in many unique forms, manufacturers are able further develop their products through raw material selection. For example, natural rubber, which is also called gum rubber, is sought after for its qualities of excellent acid and abrasion resistance.
Synthetic rubbers like silicone and viton, on the other hand, are frequently selected for applications in the healthcare and foodservice industries for their qualities of superior heat, chemical and weathering resistance. Another synthetic rubber, nitrile, is resistant to oils, while neoprene resists heat and butyl has low air flow permeability. In general, rubber extrusions are valued as sealants and gaskets because they offer such excellent flexibility, impermeability and resilience. Learn more about rubber extrusions.
The process of rubber molding involves shaping raw rubber materials into functional products. While some products can be made by other rubber shaping processes such as cell casting and extrusion, the molding process has its own features that set it apart. Products that are made through rubber molding are enclosed in a mold cavity instead of a die, and can thus be made into complex and irregular shapes.
Rubber molding is a operation in which raw melted rubber takes form inside a mold. Many kinds of complex rubber products, such as rubber diaphragms and rubber seals, are made this way, due to the ability of the rubber molding process to precisely design a product so it fits perfectly into a piece of equipment without the risk of any kind of leakage. Products that are made to protect equipment, such as rubber washers and rubber grommets, must also be designed with precision, and are thus manufactured by rubber molding. These products can also be produced through rubber extrusion. However, extruding machines have much more limited capabilities. An extruder only has control over the X and Y axes, and are thus much more suited for the production of simpler rubber products such as rubber baseboards or rubber sheets. Rubber molding allows from design control over three axes due to the process involving a molding cavity instead of a die. Learn more about rubber molding.
Rubber rollers are chemically resistant, shock absorbent cylindrical tubes that service many essential manufacturing applications. Commonly, rubber roller applications relate to material application, movement facilitation and material support and transportation. Examples of these applications include assembly line operation, grocery store checkout line operation, mail machine operation, consumer printer operation, industrial heat treat equipment operation, automatic car wash movement and boat trailer function. They're also commonly used as wheels and castors.
Rubber rollers are usually named after their function. To illustrate, let's quickly go over some rollers that fall under the application categories listed above. Two material application rollers are ink rollers and laminating rollers. Ink rollers, also called printing rollers, apply ink to paper and other materials; rollers may contain ink within themselves or they may be engraved with a pattern. Laminating rollers, made of heat resistant materials like silicone, are heated up to 500°F to laminate materials on both a small and large scale. An example a movement focused rubber roller is the rubber drive roller. Drive rollers, often used for converters and web machines, operate using integral shafts equipped with keyway that acts as a gear. Support and transportation rollers are quite common. Transportation rollers include guide rollers, grooved rollers and conveyor rollers. Guide rollers, or idler rollers, provide support to other roller systems like conveyors, but they do not actually move anything. Grooved rollers are called so because they have a grooved pattern, usually a spiral, U or V; grooved rollers are usually part of moving systems like belt driven conveyor systems. Incredibly common, conveyor rolls simply move, or convey, materials. Learn more about rubber rolls.
Rubber is bonded to metal using a variety of different adhesives. A metal substrate is sprayed with the bonding agent and then placed inside a mold. Rubber is then injected into the mold and allowed to cure, and once the rubber has solidified the part is complete. The process is used to fabricate products like rubber rollers, gaskets, seals, electrical cables, and engine mounts, and these kinds of products are utilized in the construction electric, medical, automotive, and aerospace industries.
The types of metal able to be bonded are quite varied. When rubber to metal bonding first began, steel of all grades was used most often. However, currently, aluminum alloys and polyamides have taken over as the most popular metal for bonding, because it is less expensive and more lightweight than steel, but it does not detract from seal strength or quality.
Other common metals used for rubber bonding include brass, beryllium, and copper. Rubber bonding may also be performed with non-metal materials, such as fabric, glass and a variety of plastics. Learn more about rubber to metal bonding.
Rubber Tubing is used in a wide range of industries in the transportation of liquids and gases. This tubing is made from a variety of materials such as latex, neoprene, natural rubber, silicone, viton, EPDM and other types. Since this product can be manufactured from a number of different materials this allows for manufacturers to make rubber tubing with specific applications in mind.
With their varying chemical compositions, rubber tubings' characteristics are quite diverse, which is advantageous for professionals who wish to engage tubing. Industries and applications including: food and beverage processing, medicine and surgery, commercial heating and cooling, lawn and garden care, petro-chemical extraction, sanitation and more. Flexible rubber tubing, for example, is ideal for beverage applications may that operate in very small or unconventional spaces, like bag in boxes. Surgical tubing is, of course, made to accommodate the requirements of a medical setting and the human body. Learn more about rubber tubing.
Vibration absorbers serve to prevent the inherent vibrations of operating machinery from damaging the components of the systems.
Vibration absorbers include a huge selection of components used to protect other components in a machine from the inevitable vibrations, shock, and impact of operating machinery. This encompasses everything including rubber pads and foams, air springs and spring dampeners, and sophisticated wire rope systems and negative-stiffness isolators.
Elastomeric rubber bumpers, or rubber mounts, are mounted between two pieces of machinery to prevent vibrations from transferring through metal-to-metal contact. Consistent contact between two rigid parts results in expedited deterioration and therefore higher maintenance, repair and replacement costs. In order for a mechanical system to be its most cost effective, it has to be operating at its highest output which can often be affected by the amount of vibration caused. Through vibration damping methods, machines can run at higher speeds, and as improved linear deceleration can be achieved, higher processing rates will result in higher outputs for the manufacturer. Learn more about vibration absorbers.