Rubber Bushings
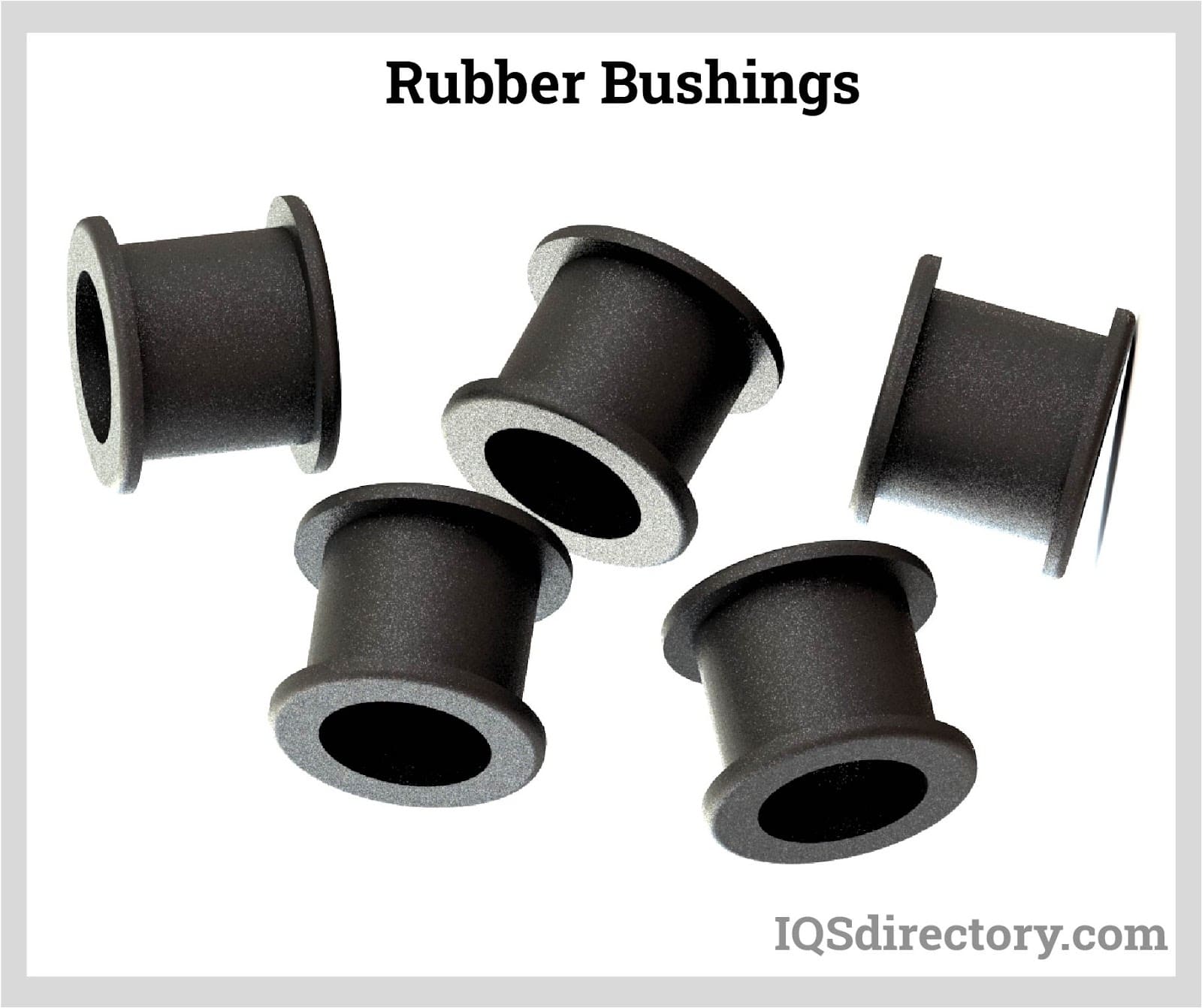
Rubber products have evolved since their inception, with ongoing innovations expanding their utility. Key advantages include durability, resilience, extended cycle life, and the ability to be molded into diverse forms, making rubber a cornerstone in various industries.
In addition to its inherent properties, rubber can be enhanced through combinations with other materials to bolster resilience. These blends result in stronger, more durable products with extended longevity. Rubber's versatility is evident in numerous transformation methods, such as extrusion and molding.
Extrusion involves applying pressure to force rubber through a die profile, crafting a diverse array of products from medical devices to sealants and linings. Synthetic rubbers like silicone and Viton are employed in specialized applications needing resistance to chemicals, heat, and weathering, aligning with various rubber processing methods.
Molding is a traditional and widely used method for shaping rubber, involving the use of two-part molds to create intricate designs and complex shapes. The process begins with melting the rubber material before it is placed into the mold. This method is ideal for manufacturing diaphragms and seals, as molds can be customized to precisely match the dimensions required for the final product.
Rubber serves diverse industrial roles, notably in manufacturing chemical-resistant, shock-absorbent, and wear-resistant rollers. In printing, these rollers ensure ink application without contamination or damage, crucial for printing presses. Additionally, rubber rollers function prominently as drive components in converters and web machines.
Ensuring durability against wear, friction, and weathering is a primary consideration for many products. Rubber is often bonded to metals using specialized adhesives to create a robust, protective seal. Compatible metals for such bonding include various steel grades, select aluminum alloys, and polyamides. Aluminum alloys are particularly favored for their lightweight properties in rubber bonding applications.
Rubber tubing is widely utilized across machinery, vehicles, and in medical and health sectors. Derived from rubber and synthetic variants like latex, neoprene, silicone, viton, and ethylene propylene diene monomer (EPDM), rubber tubing offers exceptional resilience and flexibility. Its ease of manufacturing and shaping makes rubber tubing the preferred choice for various tubing applications.
Rubber is widely recognized for its superior ability to absorb shocks and vibrations, making it indispensable for applications such as machine leg supports and cushioning. Its vibration-absorbing properties are utilized in dampeners, bumpers, mounts, padding, and foam, effectively prolonging equipment lifespan and safeguarding against wear.
Rubber is now integral to various equipment as diaphragms for flow control in pipes and as bumper support material in automotive applications. Its recyclable nature underscores its significant role across multiple devices.
The rubber extrusion process transforms various rubber materials into practical products such as weatherstripping, rubber seals, grommets, and bushings. This process involves pressing rubber through a die to shape it, creating custom profiles to meet diverse requirements. The properties of each product depend on the raw rubber used, the extrusion process, and any secondary treatments. Different types of rubber—such as natural rubber, valued for its acid and abrasion resistance, and synthetic rubbers like silicone and viton, known for superior heat, chemical, and weather resistance—are selected based on specific application needs. Overall, rubber extrusions are highly valued in industries requiring flexible, impermeable, and resilient sealants and gaskets.
Learn more about rubber extrusions.
Rubber molding shapes raw rubber into functional products, distinct from methods like cell casting and extrusion. It utilizes a mold cavity to create complex and irregular shapes, distinguishing it for its flexibility and precision in manufacturing various rubber goods.
Rubber molding is a process to shape melted raw rubber inside a mold to create precise, complex products like diaphragms and seals. This method ensures a perfect fit for equipment, minimizing leakage. Products like washers and grommets, crucial for equipment protection, require the precision of rubber molding, although they can also be produced through extrusion. Unlike extruders, which are limited to X and Y axes control, molding offers design flexibility across three axes, thanks to its mold cavity process.
Learn more about rubber molding.
Rubber rollers are durable, chemically resistant cylindrical tubes crucial for various manufacturing applications. They facilitate material application, movement, support, and transportation across diverse sectors such as assembly lines, grocery store checkouts, mail machines, consumer printers, industrial heat treat equipment, automatic car wash systems, boat trailers, and commonly serve as wheels and castors.
Rubber rollers are typically named based on their specific functions. For instance, ink rollers, also known as printing rollers, apply ink to various surfaces, either containing ink internally or engraved with patterns. Laminating rollers, constructed from heat-resistant materials like silicone, heat up to 500°F to laminate materials on both small and large scales.
Another type, the rubber drive roller, focuses on movement. Often used in converters and web machines, these rollers use integral shafts with keyways that act as gears.
Support and transportation rollers serve essential roles. Guide rollers, also known as idler rollers, support conveyor systems without directly moving materials. Grooved rollers feature spiral, U, or V patterns and are integral components of belt-driven conveyor systems. Conveyor rollers, widely used, simply convey materials along designated paths.
Learn more about rubber rolls.
Rubber is adhered to metal through a range of adhesives. Initially, a bonding agent is applied to a metal substrate, which is then placed into a mold. Rubber is subsequently injected into the mold and allowed to cure. Once solidified, the part is finished. This method is employed for manufacturing items such as rubber rollers, gaskets, seals, electrical cables, and engine mounts. These products find application across diverse industries including construction, electric, medical, automotive, and aerospace sectors.
Additional metals frequently utilized in rubber bonding include brass, beryllium, and copper. Moreover, bonding can extend to non-metal materials such as fabric, glass, and various plastics.
Learn more about rubber to metal bonding.
Rubber tubing serves diverse industries for transporting liquids and gases, fabricated from materials like latex, neoprene, natural rubber, silicone, viton, EPDM, and others. This versatility enables manufacturers to tailor tubing to specific industrial needs.
Rubber tubing's diverse chemical compositions offer significant advantages to professionals across various industries and applications, including food and beverage processing, medical and surgical settings, commercial heating and cooling, lawn and garden care, petrochemical extraction, sanitation, and more. For instance, flexible rubber tubing is well-suited for beverage applications in compact or unconventional spaces, such as bag-in-box systems. Conversely, surgical tubing is specifically designed to meet the stringent demands of medical environments and human anatomical requirements.
Learn more about rubber tubing.
Vibration absorbers mitigate the impact of machinery vibrations on system components, safeguarding against potential damage. They encompass a wide range of components such as rubber pads, foams, air springs, spring dampeners, wire rope systems, and negative-stiffness isolators, designed to protect machine components from vibrations, shock, and impact during operation.
Elastomeric rubber bumpers, also known as rubber mounts, are installed between machinery components to prevent vibrations from transferring through direct metal-to-metal contact. This reduces wear and tear, minimizing maintenance, repair, and replacement costs associated with frequent part deterioration. Effective vibration damping enhances mechanical efficiency, allowing machines to operate at higher speeds and achieve improved linear deceleration. This optimization can significantly increase processing rates and overall output for manufacturers, maximizing cost-effectiveness in mechanical systems.