Hydraulic Cylinders
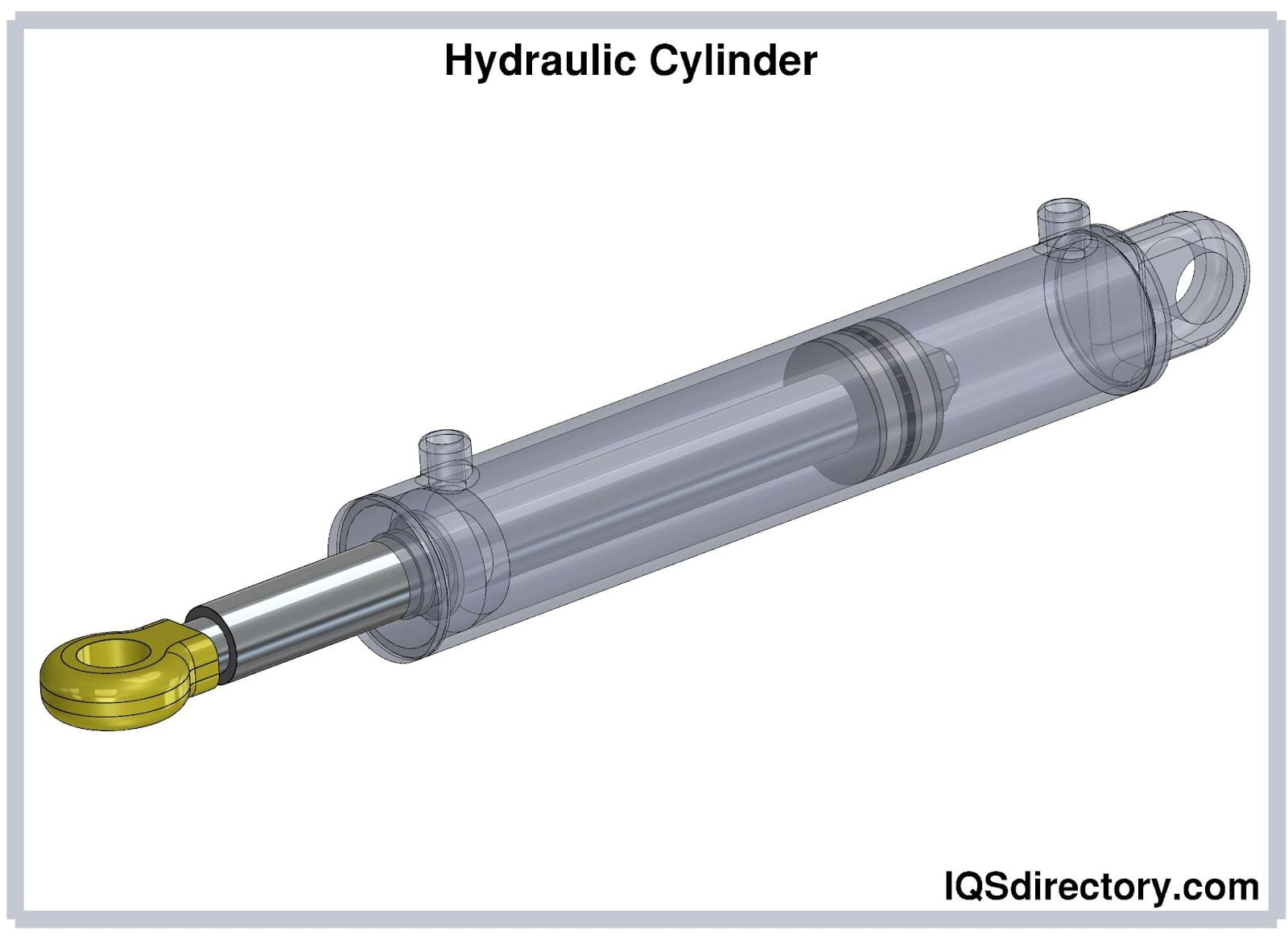
Hydraulic systems operate through the application of force and fluid dynamics. When pressure is applied to a fluid, typically oil, energy is transferred within the system. Control valves, either manual or automatic, regulate the fluid flow through tubes and hoses. This mechanism makes hydraulic systems highly powerful and efficient.
The first hydraulic equipment, the hydraulic press, was patented in 1795 by British inventor Joseph Bramah. Initially, hydraulic power was utilized in England for metal forging, machinery operation, elevator function, canal locks, and bridge section rotation. Despite these early developments, Harry Franklin Vickers, an American inventor, was later recognized as the "Father of Industrial Hydraulics" by ASME. Vickers' notable contributions include the balanced vane pump and the first hydraulic power steering system, significantly advancing mechanics, machining, and automotive technology.
Modern hydraulic equipment and systems are typically high-powered and heavy-duty, yet they remain versatile. Common examples include hydraulic presses, pumps, motors, cylinders, and lifts. A hydraulic press generates compressive forces, acting like a mechanical lever. Hydraulic pumps supply fluid to larger systems. Hydraulic motors convert hydraulic pressure and flow into torque and rotation, powering devices such as mixer drives, plastic injection machines, metal shredders, cranes, and military vehicles. Hydraulic cylinders provide unidirectional force, commonly used in engineering vehicles, construction equipment, and manufacturing machinery. Hydraulic lifts raise, lower, support, and move heavy objects or work surfaces.
Hydraulic equipment is extensively used in several industries such as material handling, construction, roofing, masonry, automotive, aviation, and manufacturing. It powers lifts, bulldozers, and cranes. In the automotive and aviation sectors, it is crucial for power transmission and braking systems. In manufacturing, hydraulic equipment aids in assembly and automation processes.
Hydraulic equipment relies on various supplies, including actuators, accumulators, filters, tubes, and valves, connected with seals, connections, and fittings. To ensure safe and efficient operation, manufacturers use materials that perform well under pressure, such as rubber, woven wire, stainless steel, cast iron, and brass. Unlike non-hydraulic equipment, which uses mechanical levers and gears, hydraulic equipment requires few or none, contributing to its widespread use.
For more information on hydraulic equipment and supplies, refer to the sections below, which offer detailed insights into various hydraulic components. To purchase any of these components, contact one of the listed manufacturers in the corresponding section. All IQS partners are experienced and reliable.
Hydraulic cylinders, also referred to as linear hydraulic motors, are mechanical devices designed to transform hydraulic energy derived from pressurized fluids into practical mechanical power. This mechanical force is subsequently harnessed to control the motions of machine attachments and linkages.
A hydraulic cylinder comprises several key components: a barrel, cap or base, head, piston, piston rod, seals, and seal glands. The barrel serves as the cylinder body, containing the hydraulic pressure. The cap encloses one end of the barrel and also serves for mounting, secured typically by bolts, tie rods, welding, or threading, with an o-ring used unless welded. At the opposite end, the head encloses the barrel, features a static seal, and attaches to the barrel via bolts, tie rods, or threading.
Hydraulic cylinder are used across diverse industries such as aerospace, agriculture, automotive, aviation, construction, machining, manufacturing, military, oil and gas, robotics, and waste removal. They are integral components in machinery ranging from spacecraft and aircraft to backhoes, snowplows, brakes, cranes, dump trucks, elevators, bulldozers, jacks, forklifts, lifts, power steering systems, material handling equipment, and robotic arms.
Learn more about hydraulic cylinders.
Hydraulic lift systems are employed to elevate, lower, support, and relocate heavy objects or work surfaces, such as platforms. Primarily used in industrial and manufacturing environments, they also serve private applications for accessibility. Various types of hydraulic lifts exist, including lift tables, scissor lifts, aerial lifts, platform lifts, vehicle lifts, and pallet lifts.
Lift tables position work materials ergonomically. Scissor lifts expand like an accordion from their crossed base, extending the platform to desired heights. Aerial lifts, a type of scissor lift, can reach up to fifty feet. Platform lifts, or elevated work platforms, are large. Vehicle lifts are robust for auto repair. Pallet lifts, or transformers, raise pallets in warehouses for handling and shipping.
Learn more about hydraulic lifts.
Hydraulic motors convert hydraulic pressure into rotational energy, powering construction equipment, recycling processes, wheel motors, self-driven cranes, excavators, agriculture, conveyor systems, dredging, and various industrial applications. As mechanical actuators, they are the rotary equivalent of hydraulic cylinders, delivering torque alongside rotational energy. Their wide-ranging applications span aerospace, agriculture, automotive, construction, forestry, manufacturing, marine, military, oil and energy, waste management, and recycling industries.
Types of hydraulic motors include gear and vane motors, gerotor motors, axial plunger motors, and radial piston motors, each offering distinct speed ranges and fluid distribution methods. Typically consisting of a reservoir, rotating machinery, and a pump, hydraulic motors operate on the principle of hydraulics: fluids, mostly incompressible, transmit force within closed systems. The pump pressurizes fluid from the reservoir into the system, where hydraulic motors harness this pressure to generate substantial power, surpassing many motors of similar size.
Learn more about hydraulic motors.
Hydraulic presses utilize hydraulic or fluid pressure to exert force on objects, offering greater efficiency than mechanical presses and pneumatic systems. They excel in clinching, molding, blanking, deep drawing, forging, punching, and metal forming tasks. They are also essential in compacting food and other consumables, as well as manufacturing ceramics, appliances, electrical and automotive parts, and even in aircraft construction.
Various types of hydraulic presses cater to different needs and applications. These include transfer presses, stamping presses, vacuum presses, platen presses, arbor presses, laminating presses, pneumatic presses, C-frame presses, H-frame presses, power presses, and press brakes.
Due to their involvement in heavy-duty applications and the need to withstand high shear forces, hydraulic presses are typically constructed from robust materials such as stainless steel. They can be configured with either single-station or multi-station designs. Single-station setups feature a single set of tools, while multi-station designs accommodate a variety of press operations with multiple tooling options.
Learn more about hydraulic presses.
Hydraulic pumps transform the power harnessed from pressurized fluids into practical mechanical energy. Serving as the heart of most hydraulic systems, these pumps are integral to a multitude of industries.
Every hydraulic pump is composed of a reservoir, tubes or hoses, and a cylinder. The reservoir contains the stationary fluid, while the tubes transport this fluid to the cylinder, the core component of the pump. Within the cylinder are two valves positioned at opposite ends, along with at least one piston or gear system. These valves are known as the intake valve and the outlet valve.
Valves in the hydraulic pump regulate fluid entry and exit from the cylinder, while the piston moves or compresses the fluid. As the piston retracts, the inlet valve opens, creating a vacuum that draws fluid from the reservoir. When the piston returns, the inlet valve closes, building pressure. The piston repeatedly opens and closes the valves at varying speeds, increasing pressure until the fluid is forced through the outlet valve. This process generates the necessary force and energy to operate the connected machinery.
Learn more about hydraulic pumps.
Hydraulic seals, integral to most hydraulic systems, are crucial for the efficient functioning of moving parts. Typically crafted from soft, flexible elastomers such as polymers, plastics, rubber, PTFE (Teflon), and polyurethane, these ring-shaped seals are designed to prevent or minimize fluid leakage within hydraulic or pneumatic systems. Their exceptional water and air sealing capabilities ensure optimal performance and reliability.
They serve a wide range of industries, including aerospace, agriculture, automotive, chemical processing, defense, food processing, marine products, medical and pharmaceutical development, nuclear power, pulp and paper, and waste disposal.
Hydraulic seals have diverse applications, including brake systems, clean rooms, conveyors, mixers, presses, valves, and test equipment, with their primary use in hydraulic cylinders. These cylinders, which provide unidirectional force through pressurized fluids like oil or water, are essential in agricultural and forestry vehicles, construction equipment, and similar machinery.
Learn more about hydraulic seals.
Hydraulic valves regulate the flow and pressure within hydraulic systems, ensuring safe and controlled fluid movement. They manage flow direction, rate, and pressure by opening, closing, or partially obstructing passageways, allowing for precise control of fluid dynamics.
Hydraulic valves are broadly categorized into directional control, pressure control, flow control, and proportional control valves. Specific types include pressure relief valves, pressure regulators, sequence valves, shuttle valves, check valves, counterbalance valves, cartridge valves, and auxiliary valves. The simplest and oldest type, check valves, prevent fluid flow in one direction.
Valves are available in various sizes and mounting styles, including subplate, pipeline, and flanged mounting. Valves meeting ISO standards are typically provided by reputable manufacturers. For more information, contact the top hydraulic equipment manufacturers listed below.
Learn more about hydraulic valves.