AC Motors
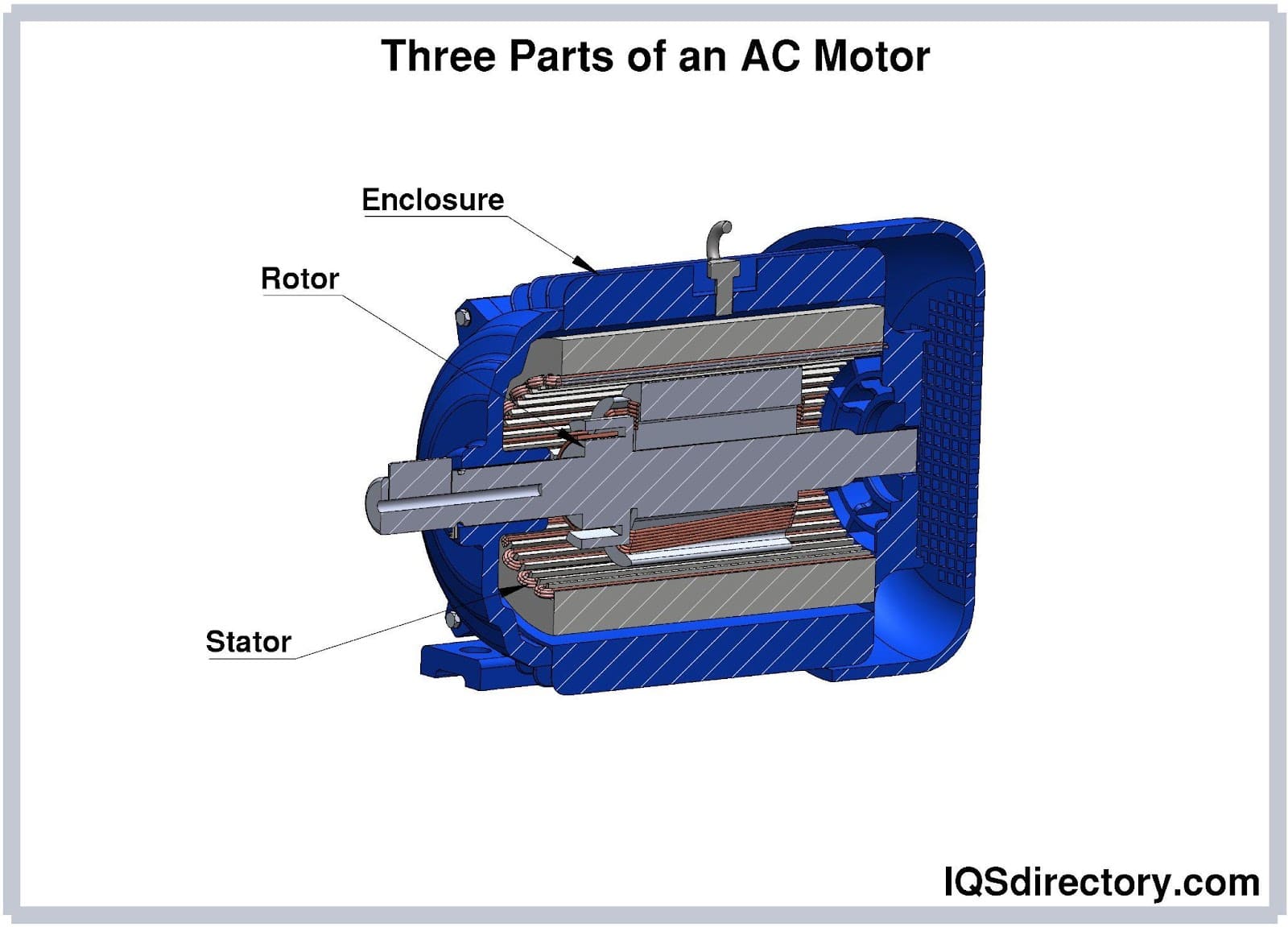
An AC motor is an electric motor that uses alternating current to produce mechanical energy using magnetism blended with alternating current. The structure of an AC motor includes coils that produce a rotating...
Please fill out the following form to submit a Request for Quote to any of the following companies listed on
This article will take an in-depth look at hydraulic motors.
The article will bring more detail on topics such as:
This chapter will discuss what hydraulic motors are, their nomenclature, how they work and how they differ from hydraulic pumps.
Hydraulic motors are rotary or mechanical actuators that operate by converting hydraulic pressure or fluid energy into torque and angular displacement.
The most relevant nomenclature used in hydraulic motors include:
Motor displacement is the volume of fluid required to turn on the motor’s motor output shaft through one revolution. Cubic inches and cubic centimeters per revolution are the common units that are used for motor displacement. Depending on the type of motor used and application, the displacement may be a fixed or variable quantity. In a fixed displacement motor the torque is constant. The speed of the motor can be varied when controlling the amount of input flow that gets into the motor. Variable torque and speed can be obtained if the motor used is a variable displacement motor.
The torque output of a motor can be expressed either in foot-pounds or inch-pounds. It’s a function of the pressure in a system and the motor displacement. The specific pressure drops in a motor can be evaluated based on motor torque ratings given by the manufacturer.
Starting torque is the ability of a hydraulic motor to make a load start moving. The starting torque indicates the amount of torque that a hydraulic motor can develop to make a load start turning. It can be expressed as a fraction or percentage of the theoretical torque. The starting torque for piston, vane, and common gear motors is usually between 70% to 80% of the theoretical value.
Braking torque is the torque required to make a stationary load start rotating or turning. It requires more torque to make a load start moving than to keep the load moving.
Running torque is the torque associated with either the motor or the motor’s load. When referring to the load, it shows the torque that keeps rotating. When referring to a motor it shows the actual torque a motor creates to keep the load turning. For common vane, piston, and gear motors, the running torque is approximately 90% of the theoretical value.
Mechanical efficiency measures the effectiveness found in a machine or a mechanical system. This can be obtained from different variables and in hydraulic motors, torque usually is used. In hydraulic motors, mechanical efficiency refers to the ratio of the actual torque to be delivered to the theoretical torque.
Slippage refers to the fluid that passes through the motor’s internal parts without performing the intended work.
Hydraulic motors work by converting hydraulic pressure or fluid energy into torque and angular displacement. Some components operate inside these motors to develop the required. Below is a list of the key components that are used in most hydraulic motors and their corresponding functions
The stator operates by exerting a force on the piston, and this creates a tangential component that makes the piston and the rotor rotate.
In hydraulic motors, the rotor is the part that rotates after being triggered by a mechanism inside the motor. These mechanisms differ depending on the type of motor, for example in a gear-type hydraulic motor, the rotor starts rotating after meshing of the gears and fluid flow. In a vane type hydraulic motor, the rotor is triggered by the pressing of the vanes.
A driveshaft (also known as a propeller) is part of a hydraulic motor that is responsible for delivering or transferring the torque created inside the motor to the outside environment where it can be used for lifting loads and other applications. Most driveshafts are made of metals and have gear teeth on their ends.
Hydraulic motors operate by manipulation of the flow of fluid inside the motor. Directional control valves are designed to control fluid flow inside the motor. In most hydraulic and pneumatic systems these valves allow the fluids such as oil, water, air to flow from into different parts according to the control patterns and mechanisms of the system.
Hydraulic motors have a casing that protects and contains the components. They are made of different materials such as stainless steel, titanium, cast iron, low carbon steel, nickel, etc. Cases come in various shapes according to the arrangements of the components inside the motor.
A piston rod is a bar that is machined precisely and used to transmit a force created in a hydraulic or pneumatic system to a machine’s component performing the work. In hydraulic motors, piston rods are mainly used in piston-type motors to produce a turning movement.
Hydraulic motors use fluids to transmit energy from one point to another. Most hydraulic motors use water-based, petroleum-based, and synthetic fluids. The widely used is petroleum-based which is also known as mineral-based. This mineral-based product comes in many forms depending on the additives used and the quality of the crude oil used. Common fluid additives include anti-corrosion agents, demulsifiers, extreme pressure agents, rust, oxidation inhibitors, and defoamants.
Water-based fluids are mainly used for fire resistance applications because of the high-water content. When using these fluids high temperatures should be avoided because they result in the evaporation of water. They must be monitored carefully because if the water evaporates, lubrication challenges are likely to arise.
Synthetic-based lubricants are also known as man-made lubricates. They have excellent properties, and the challenge is that they are more expensive.
Bearings are mechanical components that enable the rotation of parts by reducing friction and holding the load. In hydraulic motors the bearing is mainly used on the driveshaft to enable smooth and efficient rotation of the shaft. Many types of bearings are used on rotating shafts and the choice of one depends on many factors such as shaft speed, amount of load, the direction of the load, type of fluid used, etc.
It is important to know and understand how hydraulic pumps and motors differ from each other. Hydraulic pumps and motors operate similarly to each other to such an extent that some people do not know the differences. Some use the word pump when in effect they are talking about a motor and vice versa.
Some of the differences between hydraulic motors and hydraulic pumps include:
Hydraulic motors can operate in either direction. Hydraulic motors have mechanisms that allow them to rotate in either direction (negative or positive rotation) are required to have positive and negative rotation, which is why their internal structure is symmetrical, and hydraulic pumps generally rotate in a single direction, so that requirement is not necessary.
For example, in a vane motor, the blades can only be arranged in a radial manner. It can not be inclined like a vane pump, because this will cause the blades to be broken when reversing. The distribution plate in the axial plunger motor is supposed to have a symmetrical design, in that case, the axial plunger of the pump is not; the gear motor should have a separate leakage tube.
This chapter will discuss the classes and types of hydraulic motors.
Hydraulic motors are generally classified according to two classes namely the low speed and high torque (LSHT) and high-speed low torque (HSLT).
Low-speed high torque (LSHT) motors are sometimes called high torque low RPM (revs per minute) motors and are designed to cater to heavy loads and equipment moving at a slower speed. These motors are characterized by speeds ranging from 0.1rpm to about 1000rpm. They provide high torque or power which operates at a slower speed. Some of the applications of LSHT motors include moving of gates, doors, lifts, etc. LSHT motors are used in environments and systems where the machinery is supposed to lift considerable weight in an environment that is smooth, controlled, and safe.
Their low speeds ensure that the heavy objects are controlled and will follow a path of motion precisely. These motors are very useful in today’s workplaces and industries such as public buildings, aircraft, conveyors, robotic feeding mechanisms and manipulators, textile machines, mining machinery, metalworking machines, agriculture machines, food industries and other transportation systems. They are useful and take a big part in mechanization and automation processes.
The advantages of using low-speed high torque (LSHT) motors include:
High-speed low torque (HSLT) hydraulic motors are sometimes referred to as high revs per minute (RPM) motors are designed to operate at high speeds ranging from 1 000 rpm to 14 000 rpm. They are used when the load is light because they have a low torque range. They can be used for applications in the utility, earthmoving, forestry, material handling etc.
The advantages of using high-speed low torque (HSLT) motors include:
The different types of hydraulic motors include:
In this gear type, the hydraulic motor is made of two gears which are called the driven gear and the idle gear. The driven gear is connected to the output shaft usually by means of a key. Inside the motor is high pressure oil which flows into the sides around the gear tips and flows into the motor housing exiting through the outlet port. In the process, the gears mesh, and this will not allow oil coming from the outlet to flow back into the inlet side.
A small amount of this oil is used for lubrication of the gears. This oil is bled through the bearings (hydrodynamic), and the oil enters through the pressure side of the gears. The spur gears are popularly used in these types of hydraulic motors. If the gears are not manufactured to standards, they may become subject to vibration and may be noisy during the operation of the motor.
The features of external gear hydraulic motors include:
Internal gear motors have similar features and characteristics to external gear motors. The smooth operation of the gears characterizes the motors as compared to external gears where they are subjected to vibration causing noisy situations. They have one external gear that is used to mesh with the circumference of a larger gear. Internal gears are found in two versions namely the gerotor motor (mainly used in mobile systems and hydraulic technologies) and the gerotor motor.
In these gear motors a crescent vane is used to separate the discharge volume from the inlet volume between the two gears. When the hydraulic fluid enters through the inlet volume it causes the pressure to increase causing the volume to expand and this results in the gears rotating. The fluid will be forced out as the gears continue to rotate.
The features of internal gear hydraulic motors include:
Hydraulic motors operate by creating an imbalance due to pressure which results in the rotation of the shaft. In vane motors, this imbalance is a result of the difference when the vane area is exposed to hydraulic pressure. Vane motors have a hydraulic balance which prevents the rotor from sideloading the shaft. The pressure difference develops the torque as the oil from the pump is forced to go through the motor.
Vane motors are usually made of a cartridge configuration of a motor housing. Their design is like that of a vane pump. They are characterized by two-port plates that separate the outlet and inlet ports as they put in between them the cam and rotor ring. Inside the cylindrical case of a vane motor is a ring mounted. This ring is made up of radial slots where there are sliding vanes. The vanes operate by pressing inside, against the wall of the cylindrical case. The ring rotates when the vanes are spring forced against the wall due to centrifugal force.
The features of vane hydraulic motors include:
The radial-piston type hydraulic motor operates by transforming the energy created by the fluid pressure into mechanical energy (rotation). There is a directional valve, which is a fixed and central part of the configuration, it has two lines for fluid flow where one is for draining and another for fluid intake. The rotor is for turning in the directional valve which is fitted with radial bores. This will cause the free-floating pistons to operate.
The pistons which are in contact with the track that is fixed and rotated by the rotor produce a reciprocating motion with respect to the rotor. To keep the motor’s torque at a constant rate, they usually install an odd number of cylinders.
When the hydraulic fluid, that is pressurized by the pump, gets into the bores it presses the pistons against the stator usually for half a revolution. In the following half revolution, the fluid is delivered into the draining line connected to the directional valve. If the motor is operating under pressure loading on the motor piston, the stator will exert stress on the piston, and this will make the pistons and the rotor rotate. When this happens the output shaft of the motor is driven. Most of these systems are fitted with rollers which reduce the losses caused by piston friction on the track.
The features of radial piston hydraulic motors include:
Axial piston-type hydraulic motors are also known as barrel motors. In these motors the plate of the drive shaft is positioned at an angle with respect to the barrel of the motor, the intake of fluid in the cylinders results in the movement of the pistons, causing the drive to rotate. In each cylinder, there is 1 phase of output and of intake per rotation. The piston operates when it is applied to the inclined plate with a force proportional to the pressure. This force reduces the angle and creates a force that makes the plate rotate.
The direction of rotation of the drive shaft is associated with the angle of inclination of the plate of the drive shaft with respect to the axis on the barrel. In other assemblies which have axial pistons, they can change this inclination. If this axis can be changed, it means that the speed can/will be varied for a constant rate of flow, and in this case, a motor with two flow directions is created.
The features of axial piston motors include:
This chapter will discuss the applications of the various types of hydraulic motors.
The various applications of hydraulic motors are detailed below.
The applications of external gear motors include:
The applications of internal gear motors include:
The applications of vane hydraulic motors include:
The applications of radial piston hydraulic motors include:
The applications of axial piston hydraulic motors include:
When choosing a hydraulic motor to use there are factors that one needs to consider when designing an efficient system. The motor used should match the system requirement and if it does not this might affect the whole system. Below is a list of some of the factors and questions to consider.
Load requirements are very important when choosing a motor to use because that is the system’s goal. It is advised for the designer of the system to start by noting how big or small the load is. When the load requirements have been identified then one can design other requirements of the system.
There are different types of motors, and these motors operate differently depending on the application. Choosing the motor type has a lot to do with understating the ratings and specifications written on the motor by the manufacturer.
For example, if a motor is designed to operate at high speeds and the designer chooses to use it for slower speed applications, this will stress the motor. When such a scenario occurs, it means the motor’s life cycle may be reduced. It is important to match the load requirement with the motor ratings.
Motors operate at different displacements, some are fixed, and some can be adjusted. This will only depend on the application. Knowing the application will help on which motor to choose. What is the operating pressure and flow? In hydraulic motors, high operating pressures give a higher force which in turn results in high torque.
Leakage is defined as the escape of a fluid from a system through a gap such as a hole or crack. The higher the likelihood of leakage potential the riskier the motor. If a motor has high leakage potential, it means that the motor cannot be used for lifting sensitive material as it may fail easily.
There are many applications that hydraulic motors can be used for. These motors are made of different materials meaning they respond differently to operating conditions. Some are strong enough to withstand vibrations and harsh conditions and these are mainly used for industrial applications.
Motor designs come in various ways. Some operate with large tolerances and can be used for multi-purposes whereas some motors are discrete in terms of their operating pressure, speeds, temperatures, and knowing this information will assist in system designing and motor selection.
Controls on a motor can be mechanical or electronic. This depends on what the user wants after considering other factors like power consumption and automation advantages.
Some motor types can be very efficient and yet require a lot of maintenance. Some, if they are not properly maintained their life cycle is reduced. Axial piston motors, for example, require more maintenance routines as compared to gear motors.
Knowing the expected life of a motor and the bearing to be used can help to plan with regard to application and maintenance. There are some complicated machines where it does not make sense to fit a motor type that has a short life span. There are many bearings that can be used for the rotor and shaft. These will depend on the forces and torque produced because bearings are used according to the force that acts on their surface area.
Before one can choose a type of motor to use, they need to gather installation information as well. This is because other motor types require a lot of expertise and are complicated to install. It is essential to talk with professionals about the other costs that are involved before purchasing a hydraulic motor.
A closed-loop in a hydraulic system is also known as a hydrostatic drive and is commonly found in mobile systems and industrial machines such as conveyors. In a closed-loop, the fluid flows directly from the pump to the motor and then returns to the pump without entering a reservoir. The fluid flow determined the speed of the motor. In an open loop, the fluid flows from the motor to the pump through a reservoir. Before choosing the right motor for the system it is essential to understand the loop that will operate in the specific hydraulic system.
Many contaminants may affect the operation of the motor, and this depends on where the motor is going to be used. Contaminants that could be hazardous to the motor could involve things like dirt, dust, chemicals, or anything that may enter and affect the operation of the motor. Some motors should not be exposed to water as this may result in rusting. Sometimes contaminations may lead to leakages, cracking, unwanted vibrations, etc.
Some motors work according to international standards, some according to workshop standards, some according to other engineering approvals. When choosing a motor, these should be considered because failing to do so may result in a dangerous situation especially if engineering standards are not followed correctly.
Maintenance is important to keep the motor running perfectly. Below is a list of some of the things to consider when maintaining hydraulic motors.
Hydraulic motors play a vital role in the engineering and automation of many systems in our everyday lives. Although some of them are complex, most of these motors use simple operating principles which are easy to understand and are user-friendly.
An AC motor is an electric motor that uses alternating current to produce mechanical energy using magnetism blended with alternating current. The structure of an AC motor includes coils that produce a rotating...
A DC motor or direct current motor is an electrical machine that transforms electrical energy into mechanical energy by creating a magnetic field that is powered by direct current. When a DC motor is powered, a magnetic field is created...
An electric motor is an electric machine that converts electrical energy to mechanical energy. Most electric motors work via the interaction of the motor magnetic field and electrical current in a wound wire to...
A hydraulic cylinder is a tube that produces linear actuation utilizing hydraulic pressure. Basically, the pressure of a hydraulic fluid forces a piston to move in either a pushing or pulling motion...