Eyelets
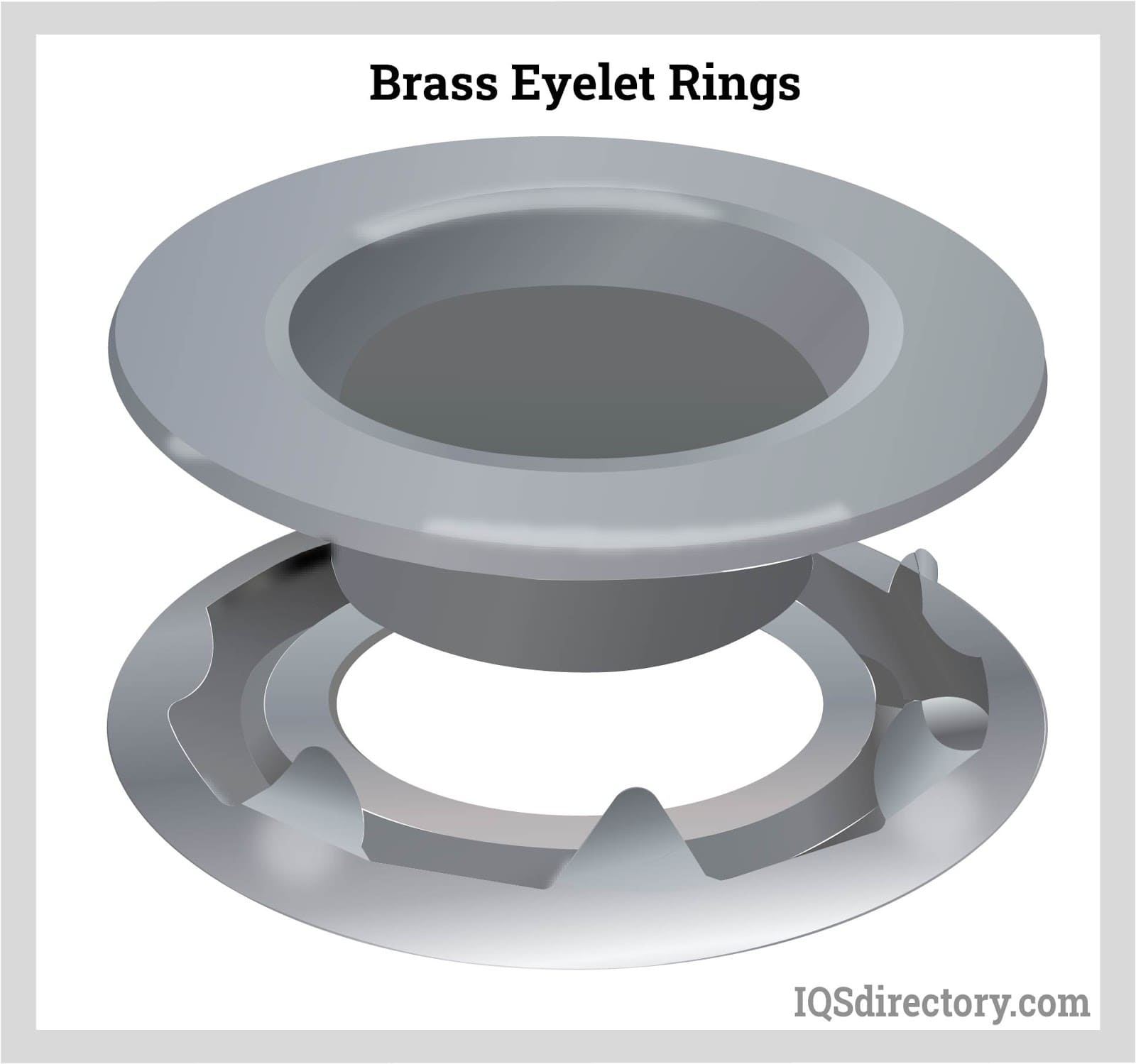
An eyelet is a ring made of metal, rubber, or plastic with flanges, used to reinforce holes punched in thin fabrics. It serves as a smaller alternative to a grommet, which is larger and designed for heavier-duty materials.
Please fill out the following form to submit a Request for Quote to any of the following companies listed on
This is the best information for die stamping on the internet.
Here is what you will learn:
Die stamping is a cold forming process that begins with a strip of metal, known as a blank or tool steel. Through the use of one or multiple dies, this method cuts and shapes the metal to achieve a desired shape or profile. The force applied to the blank alters its geometry, inducing stress that renders the workpiece suitable for bending or shaping into intricate forms. Parts produced through this method can vary greatly in size, from exceptionally small to extremely large, depending on the specific application.
Die stamping, also referred to as pressing, encompasses various techniques such as punching, blanking, piercing, coining, and several other operations. Precision in design is essential to ensure each punch achieves optimal quality.
Dies used in die stamping are specialized tools tailored to produce specific designs, ranging from simple everyday items to intricate computer components. They can be designed for single-function operations or as part of a sequential series of functions performed in stages.
(These three processes will be further explained below in Chapter 3: Production Methods).
Stamping dies serve two primary functions: cutting and forming, with some dies capable of performing a combination of these functions. Each operation is intended to either separate the material or shape it through plastic deformation.
Forming dies compress metals into precise shapes, functioning akin to stencils.
Bending forms shapes such as L, U, or V, using plastic deformation that stresses the material below its tensile strength along a single axis.
Flanging involves bending the workpiece along a curved axis, with two primary types: stretching and shrinking. Tension and compression are typical in the flanging process, influenced by the length of the tab. It can create curves or corners and involves a straightforward downward movement of the press.
Drawing is a metal forming process that displaces the surface of the workpiece to conform to another shape while maintaining the same surface area. The reshaped metal retains its original thickness. The direction of drawing is crucial as it determines how the part can be manipulated, cut, and ejected.
A variation of drawing is deep drawing. It is non-directional, meaning the direction can be up, down, or vertical.
Tension and thinning increase the surface area of the workpiece, resulting in a smooth surface ideal for painting and finishing. Dies apply high-pressure binding to control the metal flow. Stretched metals are typically resistant to dents in most cases.
A pattern is created by applying intense pressure to the workpiece, thereby reducing the metal's thickness.
Ironing is like coining. Its purpose is to reduce the wall thickness of the workpiece by squeezing it at a depth that is 30% of the workpiece‘s thickness. Ironing unifies wall thickness and increases its drawn vessel length.
Below is a description of cutting dies: Cutting, also referred to as shearing, involves separating a piece of metal by applying force until the metal fails.
Blanking removes a portion of a metal strip along a specific contour line or shape. Simply put, it involves cutting out one part of the strip from another. The cut-out part becomes the workpiece, while the remaining material is considered scrap, as illustrated in this diagram.
Shearing results in a linear cut and is typically used for creating parallel cuts, although it can also accommodate angled cuts. The diagram below illustrates a parallel cut.
Piercing is akin to blanking in process. The distinction lies in blanking where the punched-out piece becomes the usable part, whereas in piercing, the removed piece is scrap, leaving behind the desired part. The dimensions of the punch dictate both the size of the removed part and the resulting hole. Below is a basic diagram illustrating this process.
During the die stamping process, excess material around a form, known as flash, is trimmed away to achieve the desired profile by cutting along the perimeter edge of the form.
Notching can be used to assist in the bending or cornering processes. It is performed on the outside of the workpiece to create a specific profile.
The twelve dies described here are just a small sample of the many available options. Consulting with a die stamping manufacturer can offer you a comprehensive selection of various die types.
When selecting a die stamping method, considerations such as cost, time, and required geometric tolerances play crucial roles. Below, we describe the three common production types: line, transfer, and progressive.
Line dies are employed for low-volume part production or for very large parts that cannot fit on a single press. The workpiece progresses from station to station, with each station adding a single feature. Combination dies, on the other hand, execute multiple operations in a single stroke during pressing.
Transfer dies operate similarly to line dies, but they synchronize multiple dies together. Parts are evenly spaced on a single press, known as pitch, and are automatically moved between presses on side-by-side rails or manually. Once a cycle completes, the workpiece is gripped and transferred to the next die.
Progressive die stamping has several dies that are activated together. The metal strip, as seen below, is fed through, producing a continuous stream of parts. The stress on the metal is distributed evenly over multiple operations. The equal distance between them is called the progression.
Compound die stamping involves feeding strips of steel through a compound die, which cuts or punches out a part in one stroke. A knock-out mechanism ejects the part, and the steel strip continues through the die. This rapid process can produce parts within seconds, achieving rates exceeding 1000 per hour, thereby reducing labor costs and lead times.
Compound die stamping eliminates the necessity for multiple dies, which can inflate stamping costs. By using a single die, this process ensures consistent accuracy, flatness, and dimensional stability. The preference for compound die stamping stems from its capacity to decrease expenses and minimize waste, addressing critical concerns in contemporary manufacturing practices.
Regardless of the production process, die stamping requires the use of lubricants for:
When punching dies exert force against a metal strip, friction can lead to scratches, burning of the piece, or damage to the die itself. To mitigate these issues, a lubricant is applied to form a protective layer on the metal workpiece. This helps reduce damage to the die and lowers defect rates during the stamping process.
The three methods for applying lubricant are drip, spray, and roller.
Manufacturers use lubricants made from plant, animal, and mineral oils in addition to graphite, soap, and acrylic ones. Modern lubricants are synthetic and do not contain any oil.
There are four main types of die stamping presses: mechanical, hydraulic, servo, and pneumatic, named according to the force-generating mechanism they employ. Each type is categorized into C-frame and straight side varieties, where C-frame presses feature three open sides, while straight side presses have two. The ram or slide, where the upper die is mounted to apply force, can have single or double connectors.
The image below shows a straight side press, equipped with four to eight guideways. These guideways enable it to manage off-centered loads effectively while safeguarding against deflections.
Stamping press manufacturers utilize specific terminology to describe the operation of their equipment, with individual companies often employing proprietary terms. Below is a comprehensive diagram listing all the terms associated with a die stamping press.
Below are selected stamping terms from Sutherland Presses Auto Stamping based in Malibu, CA. For a complete list of their die stamping terminology, please visit their website at https://www.sutherlandpresses.com/news/press-terminology
When communicating with a die casting company, it's advantageous to be familiar with the vocabulary to understand the terminology used.
Hydraulic and pneumatic die stamping presses are widely used, with mechanical presses remaining the cornerstone of the industry. Each type of press employs a distinct method to achieve similar functions with varying types of force. Some models integrate both hydraulic and pneumatic methods. Motor presses represent a recent advancement under evaluation and exploration by major manufacturers.
A pneumatic press utilizes air pressure to drive the downward stroke of the ram, while springs facilitate its upward movement. When activated by the controller, air fills the cylinder, expanding to generate pressure. At the end of the cycle, the air is released, allowing the ram to return to its starting position at the top.
Hydraulic presses provide force using static pressure over a finite and small area. They use pressurized incompressible fluid in a cylinder or cylinders to drive the ram. They are used for metal forming, shallow stretching, and bending. There are three parts to a hydraulic press: machine, power system, and control system.
Until recently, the primary method to increase tonnage was by constructing larger motors. However, press manufacturers have now replaced motors, clutches, and flywheels with servomotors. These servomotors provide precise energy delivery at specific locations, enhancing control over the ram.
Servo presses enable operators to program the dwell time at the bottom of each stroke, ensuring the workpiece settles perfectly before forming. This capability significantly extends the lifespan of the die. Additionally, programming the dwell allows for advanced in-die functions, such as pre-heating the metal before forming. This pre-heating prevents tough materials like stainless steel from tearing during deep draws. Moreover, programmable functions facilitate the use of water-soluble lubricants instead of oil-based lubricants, eliminating the time-consuming and environmentally problematic oil-removal step in subsequent processes. These features make servo forming a compelling alternative to mechanical presses.
All mechanical presses produce force by stored energy from a flywheel. Punches can be 5 mm up to 500 mm at stroke speeds of 20 to 1500 spm. They are categorized by their type of drive, which can be single gear, double gear, double action, linked, or eccentric geared.
Energy stored in the flywheel is discharged using one of the drive types. As the flywheel completes each rotation, it gradually loses energy, reducing its speed by 10 to 15 percent per turn. This lost energy is replenished by an electric motor.
Tonnage – They can vary in size from 20 tons to 1600 tons with the ability to supply substantial force.
Press Energy Chart | |
---|---|
Press Type: Flywheel (Direct drive) | |
SPM | In.-Tons of Energy |
5 | 5 |
10 | 19 |
15 | 43 |
20 | 76 |
25 | 119 |
30 | 171 |
35 | 285 |
40 | 285 |
45 | 285 |
50 | 285 |
There is a wide range of die stamping machines available across the United States and Canada. These machines are indispensable in modern society, playing a pivotal role in manufacturing industries by facilitating the mass production of precise metal components used in diverse products like automotive parts, electronics, and appliances. Below, we explore several popular die stamping machines, highlighting their unique features and characteristics that contribute to their widespread adoption.
Features: Bliss C Series presses are known for their robust construction and high precision.
They provide a broad spectrum of tonnage capacities tailored to diverse die stamping applications. Bliss Presses' C Series presses feature advanced control systems aimed at enhancing productivity and user-friendliness.
Features: The E2 Series of Komatsu Presses has gained acclaim for its energy efficiency and environmentally friendly design. These machines incorporate advanced servo technology, enabling fast and precise stamping operations. The press controls in the E2 Series are user-friendly and provide extensive monitoring and diagnostics capabilities.
Features: The P2H Series of Minster Presses are celebrated for their exceptional precision and productivity. They integrate advanced servo-driven technology to enhance control during the stamping process. Minster Presses are highly regarded for their durability and minimal maintenance needs.
Features: The Seyi M1 Series presses are recognized for their versatility and efficiency in die stamping operations. They offer customizable features tailored to meet specific production requirements.
The M1 Series presses feature intuitive interfaces and enhanced safety measures to optimize the operator experience.
Features: The AIDA NC1 Series presses are renowned for their high-speed capabilities and precision. They incorporate state-of-the-art technology to deliver consistent and reliable stamping performance. The NC1 Series provides a variety of tonnage options to meet diverse metal stamping needs.
Keep in mind that advancements in technology and changes in the market often bring about the introduction of new machines or updates to existing models. For the latest information on the leading die stamping machines available in the United States and Canada, it is advisable to refer to industry publications, visit manufacturers' websites, and consult with industry experts or suppliers in the field.
When selecting a metal for die stamping, several factors should be taken into account, such as its mechanical properties, lubrication requirements, press speed and capacity, magnetic attributes, and the type of steel used in die construction. Die stamping utilizes both ferrous and nonferrous metals, with aluminum being particularly favored for its strength, lightweight nature, and resistance to corrosion.
Two primary considerations must be evaluated when selecting a metal: ductility and tensile strength. Ductility is critical as it determines a metal's ability to be shaped and formed without cracking, tearing, or breaking. Tensile strength, on the other hand, measures a metal's resistance to breaking under tension and pressure. These factors are essential criteria for assessing a metal's suitability for die stamping.
Tensile testing is a straightforward method used to determine how a sample responds under tension, revealing its breaking point when subjected to external forces. These tests provide designers and developers with material analysis reports to predict how a metal will perform in its intended application. The diagram below illustrates the testing process. Tensile strength reports typically include values in megapascals (MPa). For instance, 1090 mild steel has a yield strength of 247 MPa and ultimate tensile strength of 841 MPa, with a density of 7.58. In contrast, aluminum exhibits a yield strength of 241 MPa and ultimate tensile strength of 300 MPa, with a density of 2.7.
Benefits include:
Ductility describes a metal's capacity to deform without fracturing, as depicted in the diagram below.
Four factors contribute to determining a metal's ductility: elongation percentage, tensile strength, yield strength, and hardness.
Elongation percentage measures how much a metal can stretch within a specified distance, typically two inches. For example, a metal with a 38% elongation can stretch 38% of its original length before fracturing when elongated over two inches.
Tensile strength refers to the maximum stress a metal can endure. A higher tensile strength indicates greater ability to withstand stress.
This measure quantifies the force required to shape and deform a metal. When a metal undergoes deformation, it experiences two stages: elastic and plastic. Elastic deformation occurs when it bends under its own weight, whereas plastic deformation involves permanent changes to the metal during processing.
The hardness of a metal is determined using the Rockwell hardness scale, which measures its resistance to penetration by applying weight until the metal surface yields.
Various metals can be utilized in the stamping process, categorized as either ferrous or nonferrous. Ferrous metals contain iron, while nonferrous metals do not. Steel exemplifies a ferrous metal, derived from iron ore, whereas aluminum, devoid of iron, originates from raw aluminum. In general, ferrous metals are magnetic, whereas nonferrous metals are not, with a few exceptions.
Because nonferrous metals lack iron, they are resistant to rust and oxidation. Nonferrous metals commonly used in stamping include aluminum, bronze, brass, gold, silver, tin, and copper. Among these, aluminum is preferred for its strength, lightweight properties, and corrosion resistance.
Of the ferrous metals, steel is the most used in stamping due to its strength and durability.
Because nonferrous metals lack iron, they are resistant to rust and oxidation. Nonferrous metals commonly used in stamping include aluminum, bronze, brass, gold, silver, tin, and copper. Among these, aluminum is preferred for its strength, lightweight properties, and corrosion resistance.
Stainless steel is another type of steel used in stamping, classified as a ferrous metal. The composition of alloys, primarily chromium and nickel, in stainless steel determines its grade. Each grade possesses specific properties and characteristics that make it suitable for diverse applications. For instance, stainless steel grade 316 is ideal for marine applications, whereas grade 304 is preferred for chemical and food processing industries.
Typical grades of stainless steel used for stamping are 301, 302, 304 & 304L, 316 & 316L, 321, 410, and 18-8.
Aluminum, a nonferrous metal utilized in stamping, is valued for its lightweight nature, strength, and resistance to rust and corrosion. Typically, aluminum is alloyed with other metals to enhance its strength and augment specific properties and characteristics.
Aluminum's excellent formability makes it an ideal metal for stamping, as it can be shaped and molded into virtually any configuration.
Copper, similar to aluminum, is a nonferrous metal known for its ease of forming and ability to be shaped into seamless components. It is low maintenance, highly resistant to corrosion, and naturally hygienic, making it suitable for medical, food, and beverage applications. While pure copper is used in stamping, it is often alloyed to improve its durability and strength. Its high ductility makes it well-suited for the stamping process.
Brass is an alloy of copper and zinc, with the proportions of each metal defining its grade and ductility. It features a smooth, silky surface that is easily shaped, resistant to corrosion, and has excellent conductivity. Additionally, brass is chosen for its attractive appearance and superior aesthetic value.
C26000 is among the most widely favored grades of brass, largely owing to its remarkable corrosion resistance. The hardness of brass correlates directly with its zinc content percentage.
Specialty metals encompass a wide range of materials crafted to endure severe environmental conditions without corroding, degrading, or becoming brittle. This category includes diverse titanium and nickel-based alloys. Their extensive variety makes it challenging to generalize their characteristics, as they are specifically engineered to meet precise operational conditions.
Specialty metals commonly share two key attributes: corrosion resistance and heat resistance. Engineering these metals involves enhancing the base material's strength, durability, and resilience against impact and physical damage.
Microstamping involves manufacturing parts that are nearly imperceptible to the naked eye, typically measuring fractions of a millimeter in size. The production of these micro-stamped parts demands highly precise technical procedures with strict tolerances and exceptionally accurate dimensions. These miniature components are created through processes such as line, transfer, or progressive die stamping, where they are pressure-formed at microscopic scales and may include even smaller integrated elements.
Process - Parts are formed in one stroke of the stamping press.
Technical requirements - Dies are specially designed for a single operation.
Lead times – The complex nature of producing dies takes months to produce and configure.
Equipment – Presses and other equipment are the same as in regular die stamping.
Metals – Beryllium copper, phosphor bronze, and brass. The tensile strength of metals has to be precision controlled to ensure quality and proper performance.
The microstamping industry continually encounters new challenges in designing and producing increasingly smaller and more precise parts. Below are some recent advancements in this field.
Rivetless Nutplate – Fastener for use in the aerospace industry.
Micro lumbar retractor – Micro Lumbar Discectomy at 1.57 in (40 mm).
Micro USB Breakout Board – Breakout board with USB Micro-B connector.
One challenge with the die stamping process is its inflexibility. Once a die is cast or a product is produced, there is limited room for reverse engineering or process corrections. However, new auto simulation software enables designers to conduct simulations in a seamless process, minimizing iterations and validating designs before they proceed to manufacturing.
Simulation software is designed to compute the stages of the die stamping process, aiding developers in anticipating potential flaws and errors in designs, including those outlined below.
Tensile failure can occur due to excessive stitching of metal, resulting in deformation like smiling or elongation caused by stretching the metal to its maximum threshold.
a tear or rip caused by too much stretching; happens after necking.
A geometric alteration in a part occurring at the conclusion of the forming process can illustrate the effects of springback, as depicted in the image below.
a result of excessive cold working or strain hardening.
AutoForm and Stamping Simulation technology have the capability to forecast and rectify intricate die stamping issues. The image below illustrates a solution for addressing a springback problem.
Examining the entire process, engineers can simulate each operation, such as drawing, flanging, or coining.
Formed parts – The software provides an image of the completed part for close evaluation and determination of any flaws.
An eyelet is a ring made of metal, rubber, or plastic with flanges, used to reinforce holes punched in thin fabrics. It serves as a smaller alternative to a grommet, which is larger and designed for heavier-duty materials.
A fastener is a mechanical tool, either non-permanent or permanent, that securely connects or affixes two surfaces or objects together. Non-permanent fasteners can be removed without causing damage to the joined materials.
A metal bracket serves as a fastener or connector specifically crafted to securely hold two pieces or objects together. They are utilized for supporting shelves, stabilizing equipment, fastening uprights, or adding decorative accents. Metal brackets are available with various features...
Shim Definition: A shim is a material used to fill gaps or adjust spaces. For example, construction shims are commonly used in window and door jamb installations. Shims can be made from readily available materials, particularly when...
Metal stamping is a cold-working process that converts sheets of metal into predefined shapes using specialized tooling. This process utilizes a punch's stroke to induce a structural change in the metal sheet.
A metal washer is a small, flat piece of metal with a central hole, employed as a spacer, shock absorber, or to distribute the load of a fastener. The hole in the center of a metal washer accommodates a bolt or screw for secure fastening.
The metal stamping process originated during the industrial revolution as a method of cold forming to manufacture bicycle frames and handlebars. Starting in Germany, it has evolved into a critical component of modern industry, used extensively for producing parts and components across various sectors.
A self-drilling screw is a tool designed with features similar to a drill bit or cutting tool. As the name suggests, self-drilling screws can function as fasteners without the need for a pilot hole.
Bolts are mechanical devices utilized for assembling and fastening objects, commonly paired with a corresponding nut. They are intended to be installed into aligned unthreaded holes across multiple parts.
Contract manufacturing is a business model where a company engages a contract manufacturer to produce its products or components. This strategic approach is widely adopted by companies to conserve significant resources and...
Precision sheet metal fabrication is a widely used manufacturing process involving cutting, bending, and assembling metal workpieces through machining. Numerous operations are involved in creating a final sheet metal product...
Sheet metal fabrication involves transforming metals into thin, flat sheets that are subsequently cut and bent into various shapes. Various metals such as brass, steel, copper, tin, titanium, aluminum, and others can be utilized in sheet metal production.
Stainless steel can be shaped using traditional forming and shaping techniques. Austenitic stainless steel, in particular, can be rolled, spun, deep drawn, cold forged, hot forged, or textured under force and stress.
Secondary manufacturing processes, also known as fabrication, refine products from primary processes to produce metal parts or structures ready for end-use. These processes involve reshaping and joining semi-finished metal products.