EDM Machining
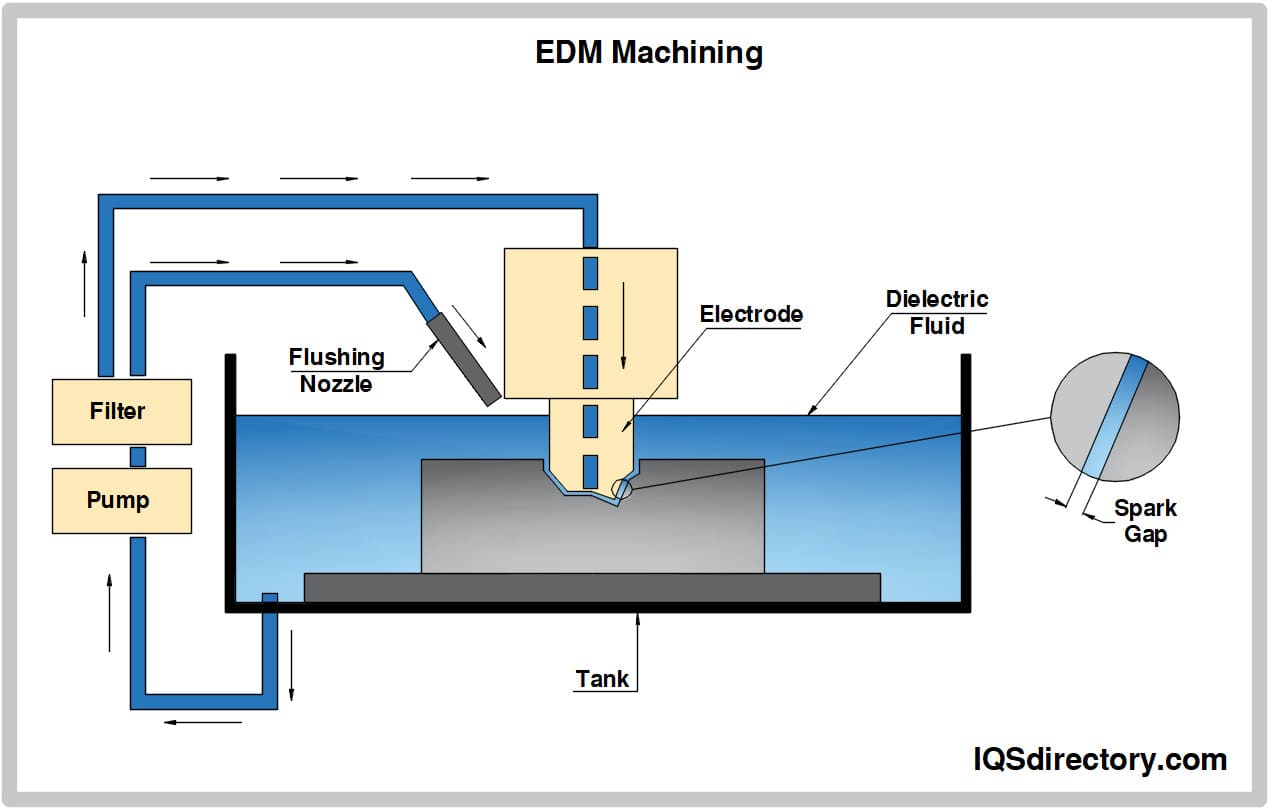
EDM machining is a contemporary machining method based on the removal of material from a part using thermal energy. The material is removed by local melting or vaporizing small areas on the surface of the part being machined...
Please fill out the following form to submit a Request for Quote to any of the following companies listed on
This article will give a detailed discussion on wire electrical discharge machining (EDM)
It is expected that after reading, one should understand;
A method of precision machining called electrical discharge machining (EDM) removes material from a workpiece using thermal energy rather than mechanical force. A thin, single-strand metal wire and deionized water used to conduct electricity are used in the electrical discharge machining method known as wire electrical discharge machining (EDM) to cut through metal while preventing rust. In wire EDM, the tool electrode is a metallic wire, typically constructed of brass or layered copper. To cut or shape a workpiece, utilize the metallic wire. The thin electrode wire travels along a predetermined route. Although smaller and larger diameters are available, the typical electrode diameters range from 0.004 inches to 0.012 inches (0.10mm to 0.30mm). The wire is coiled between two spools so that the active portion of the wire is continually changing. This design prevents the wire from eroding to the point where it breaks.
Wire electrical discharge machining (EDM) can machine parts resistant to conventional machining methods as long as they are electrically conductive. Typically, non-ferrous metals like steel, titanium, super alloys, brass, and many others fall into this category. EDM produces relatively small chips and a precise cut line by melting or vaporizing the material rather than cutting it. EDM is widely accepted in the industry and has a wide range of applications since it is extremely adaptable, can cut strong metals, and takes up only a small amount of space.
One of the most successful and economical ways to accurately process conductive and hard materials is wire EDM. This technique allows complicated structures to be swiftly and readily sliced while achieving high tolerances. It is also a no-impact cutting technique, allowing for the distortion-free machining of hard, brittle, and delicate materials.
The material is cut, trimmed, and removed from the workpiece during the wire EDM process. Wire EDM machining generates an electrical current discharge between the wire or electrode and the conductive workpiece. Material is removed from the workpiece, and the electrode as the spark jumps across the gap. Hard conductive materials can be easily machined with wire EDM because of the intrinsic characteristics of the technique. A non-conductive fluid or dielectric is also employed to prevent the sparking from shorting out. The dielectric then removes the waste material, and the procedure resumes.
A hole in the workpiece is required before beginning wire machining, or one can start from the edge. Every discharge on the area being machined leaves a crater in the workpiece and an imprint on the tool. It is possible to create parts with taper or various profiles at the top and bottom, thanks to the wire's ability to be inclined. The electrode and workpiece never make contact mechanically. Depending on the accuracy and surface polish required, a part may be cut, roughed, and skimmed. On a single cut, the wire should go through a solid component before dropping a slug or piece of scrap. This design will provide acceptable precision for some tasks, but skimming is usually required.
Potential difference is used in wire EDM, which is pulsed onto the electrode and workpiece. As a result, electrons from the negative electrode flow toward the positive workpiece and strike the deionized water molecules. The number of ions and electrons between the workpiece and the electrode rises due to the electrons' conversion of the molecules into ions. An electric current is produced when the ions go toward the workpiece, and the electrons move toward the electrode.
The temperature rises to almost 10,000°C when the electric current passes between the workpiece and the electrode. The material farthest from the workpiece is melted and vaporized by extreme heat. The molten material is transported or flushed away by the moving dielectric fluid after the current stops. The cutting parameters and speed significantly impact the wire EDM process's accuracy. The wire may move slightly or bend at higher speeds, reducing accuracy overall. Therefore, keeping lesser power and speed guarantees the highest possible precision. Tolerances of up to +/- 0.0002 inches are possible with lesser power and speed, whereas tolerances of +/- 0.001 inches are possible with greater speeds.
The diameter of EDM wire varies from 0.0008 to 0.013 inches. Smaller wires require lower power settings and cutting more slowly. A 0.010-inch diameter plain brass wire is used in more than 80% of EDM work. One should select a wire suitable for the material they want to machine.
An important factor in deciding if a design is appropriate for wire EDM is part geometry. It also affects how challenging it will be to manufacture the component itself. Designers must first determine whether wire EDM can be used to manufacture the features. Not all geometries work well with EDM and can cause issues with wire erosion, surface finishes (due to variations in material thickness), and even the level of tolerance that can be achieved. Engineers and designers must consider geometry as early in the design process as possible when designing a part for manufacturability.
The requirements for the surface finish should be carefully considered when designing a product for wire EDM machining. Surface finishes created by wire EDM can have an accuracy of up to 3 microinches. Only some components, though, need to be extremely accurate. Only a small percentage of parts require such a high level of precision and polish; thus, designers should consider the minimum and maximum tolerance variations when engineering an object. The establishment of minimal specifications will significantly impact the final product's expenses.
Cost optimization, project lead time reduction, and the finished part's repeatability requirements all play a significant role in design. For example, the greater the surface polishes in wire EDM, the narrower the tolerance. However, the cost will increase because the part will require more time to cut overall. In addition, the type of material or part height may impact machining precision. Taller pieces require greater force to remove material, but precision and surface polish will also be impacted; therefore, these factors must be considered.
When assessing a project design, the designer should question the client regarding the material selection. Another choice that needs to be carefully considered is the choice of the right conductive material to meet the part design specifications and be suitable for wire EDM. Selecting the right material conducive to wire EDM machining can reduce the cost of the finished product if material hardness, dimensional accuracy, and tight tolerances are required. Each component of the part design must be assessed and optimized for proper functional performance and the lowest possible product cost for wire EDM design to be most effective.
The time factor in manufacturing is another important consideration when designing a part for the best manufacturability. Since EDM machining takes longer, customer orders frequently call for a quick turnaround.
The entire process is focused on wire EDM programming. The numerical control program directs how the machine tool is processed. The program's correctness directly impacts the processing shape and accuracy. The CNC program should be checked and verified to ensure it is correct after the programming is finished and before the official cutting process. The wire EDM machine tool's numerical control system offers a program verification technique. The program is examined for syntax mistakes and compliance with the pattern processing contour.
The wire EDM machine's various components interact to shape material appropriately. These parts work in tandem with one another and are all necessary for the machine to function.
The wire serves as the cathode, and the workpiece as the anode of the machine's electrodes. When cutting with wire EDM, the servo motor controls the wire electrode to ensure that it never comes into contact with the workpiece.
The wire running system regulates the speed and tension of the electrode wire feed, the electrode wire's reciprocal feeding, and the electrode wire coiling on the wire drum without overlapping.
The wire serves as the electrode to create the electrical discharge. Therefore, the workpiece's thickness and form directly impact the wire's diameter.
The workpiece is supported and held by the work table. Two stepper motors regulate their movement. Relative movement between the working table and cathode wire completes wire EDM machining. The high-speed feed wire cut EDM machine's working table has X and Y axis slides and uses a priceless linear guideway and priceless ball screw as its moving parts. Since the XY cross structure has been in use for many years, its mechanical rigidity and controllability have been established and widely accepted. Today, its production and design processes are well-advanced and frequently used for many machine tools.
High-precision stepper motors with strong coupling and programming instructions are essential components of CNC systems. In addition, CNC tools manage the entire wire EDM machining process. Controlling the entire procedure entails being able to handle the cutting process automatically and sequence the wire path.
The tank used for the wire-cut EDM technique must contain dielectric fluid. With the help of this liquid, the workpiece's minute particles are kept from adhering to the wire electrode. Deionized water is the most used medium since it cools the process and produces a workpiece with a smooth surface.
The power supply unit sends pulses between 100V and 300V to the wire electrode and the workpiece. The electrical charges that flow through the wire electrode to interact with the workpiece are also controlled in frequency and intensity. Therefore, a highly-developed power supply unit is required to deliver the right kind and quality charges during wire EDM machining.
The working solution (deionized water) is drawn out of the tank by a pump, passed through a filter to remove impurities, then directed into separate up and down nozzles before returning via a filter next to the tank. If the working solution and filter impact cutting quality, they must be changed.
Due to their high conducting qualities, brass is the most popular material for EDM wires. It is a copper and zinc alloy, and the wire cuts more quickly the more zinc there is in the alloy. There should be a balance, though, as brass wire's corrosion rate is decreased when the zinc concentration exceeds 40%.
As the name suggests, these are produced by coating the surface of the wire with pure zinc or zinc oxide. Manufacturers use zinc-coated wires because they increase machining speed.
The first wire to be used in wire EDM was copper. At the time, copper seemed a sensible option for an EDM electrode due to its accessibility and high conductivity. Still, copper's slow cutting speed and low tensile force quickly became apparent as generators got more powerful. As a result, this wire is rarely advised, except for older equipment that calls for the use of copper wire.
Wires with a greater zinc content can be produced with the diffusion annealing process. It entails applying layers of pure zinc coating to wires. These wires can process various materials and are excellent for mass manufacturing.
Wires made of molybdenum have a very high tensile strength. Molybdenum wire is a somewhat poor electrode material due to its extremely high melting and vaporization temperatures. However, moly wire helps maintain great wall straightness and reduces the frequency of wire breaks typical with many small and fine brass wires due to its high tensile strength.
This kind of wire contains a core made of carbon steel, which provides great strength and fracture resistance, and is covered in a thick layer of zinc-rich, diffusion-annealed brass, which improves cutting performance.
When attempting to address a challenging application, tungsten wire is frequently one of the last options considered. Sometimes this wire is the only option for an EDM issue, despite being very expensive, cutting poorly, and difficult to deal with. It is the least effective wire electrode in cutting performance, with even greater melting and vaporization temperatures than moly. Of all EDM wires, however, tungsten wire has the highest tensile strength. This quality enables it to define and sharply carve very small, straight-walled details.
It's crucial to specify the tensile strength of EDM wire. The machine's wire drive feed mechanism, which comprises a wire tensioner, roller guides, and upper and lower feed contacts, stretches the wire even when it does not come into contact with the part during cutting (where the electric current is applied). The wire has tension preloaded on it, which may be changed to perform various cutting procedures. The wire's capacity to withstand stress during cutting depends on its tensile strength. The easier it is to break, the lesser the tensile strength.
Angles can be cut in a wire that has reduced tensile strength without breaking. The U-V axis wire guides can be moved or offset to create massive tapers, and angle cuts up to 45°. When employing the U-V axis to manage the perpendicularity of vertical walls for cutting precisely, the stronger wire can be stretched more tightly. Lower wire tension for roughing allows the machine to cut faster without breaking the wire. For skim cuts, slower speeds and less power are used to achieve the best surface finish and precision.
Since there is no real way to rate fracture resistance, it could be more accurate to refer to an EDM wire's fracture resistance as wire toughness or resilience. This alternate reference is because the wire can withstand the spark gap's extraordinarily dynamic environment.
Conductivity gauges a substance's electrical current-carrying capacity. More power can be transmitted to the workpiece during EDM if the wire's conductivity is higher. Increased cutting speeds are frequently the result of more efficient conductivity.
For quick vaporization, a low wire melting temperature will work best. Then, instead of polluting the gap with resolidified chips, the wire surface should evaporate and swiftly transform into gases.
Tensile strength is frequently confused with hardness. A wire's elasticity or capacity for extension, elasticity, or capacity for extension is referred to as its hardness or temper. EDM wires fall into one of two categories here: soft or hard. A strong wire will thread better than a softer wire on closed-guide machines, but a soft wire will taper-cut better. Additionally, a hard wire will offer the most reliable auto-threading performance.
After the correct material has been selected for the workpiece and the right wire has been selected according to the guidelines given, a machinist can follow the following steps;
Wire holes must be processed before online cutting to process closed holes and some punches. Therefore, the threaded hole's location should match the starting point for the machining operation defined during programming.
Choose the right clamping technique to establish the workpiece's position based on the workpiece's size, form, and processing requirements. One can select specialized or self-designed fixtures to clamp the workpiece if the clamping techniques for plate parts, rotating parts, and block components differ. The workpiece needs to be adjusted after being clamped. In general, it is to examine the clamping of the workpiece for perpendicularity and flatness and to rectify the axial parallelism between the machine tool and the workpiece reference plane.
The wire electrode needs to be precisely positioned to the cutting coordinate starting location before wire EDM operation. The adjustment techniques include automatic alignment, the spark method, and visual inspection. Contact sensing, automated edge finding, and automatic center finding are all features shared by modern CNC wire-cutting machine tools. As a result, they are extremely practical for situating electrode wires and have good alignment accuracy. However, various machines are operated differently.
The entire procedure is focused on wire EDM programming. The CNC software directs how the machine tool is processed. The program's correctness directly impacts the accuracy and shape of the machining. The automatic programming method is primarily used in production.
The CNC program must be examined and validated for accuracy after programming and before any formal cutting. Program verification techniques are provided by the wire EDM machine tool's numerical control system. One can start the machining process and wait for it to finish if the CNC program is accurate.
The tool returns to its starting location after finishing. The finished workpiece can then be freed from the clamps by the machinist.
Wire EDM and conventional EDM use the same principles, with wire EDM being an improved version. The two differ in the ways below:
Traditional EDM electrodes must have a variety of forms. Therefore, before beginning the machining process, manufacturers must develop and form them, which takes time. The wire EDM machine, on the other hand, is ready to use as soon as the wire is in place. It is, therefore, suitable for projects that must be finished fast.
The wire is used as the electrode in wire EDM machining. They are, therefore, more accurate than traditional EDM. For instance, they can cut at a thickness of roughly 0.004 inches thanks to the wire electrode. In addition, unlike conventional EDM, which is better suited for more severe cuts, they are more accurate, making them more suited for machining items with complicated shapes and designs.
As was already mentioned, a thin, heated wire is utilized as the electrode in wire EDM cutting. In contrast, traditional EDM generates electrical charges using electrodes made of highly conductive metals like copper or graphite. Their various sizes and shapes impact the smoothness of the electrodes. For instance, the smoothest surface is produced by a circular electrode. Next comes a diamond, square, and triangle shape. The electrode creates a mold when put into the workpiece, creating a "negative" impression of its shape.
Since wire EDM machining is flexible and can cut ferrous and non-ferrous metals, many industries use it. Furthermore, its employment is not constrained by size or shape because it can handle both long and incredibly microscopic parts. However, because the wire electrode thickness affects how a wire EDM machine is used, conventional EDM may be able to deal with tougher and thicker materials.
A good wire EDM machine possesses several key characteristics that contribute to its effectiveness and efficiency. First and foremost, precision and accuracy are paramount. The machine should be capable of achieving tight tolerances and maintaining consistent dimensional accuracy throughout the machining process. Additionally, a high level of repeatability is essential, ensuring that the machine can consistently reproduce the same shapes and features. Speed and cutting efficiency are also crucial factors, as a good wire EDM machine should be able to execute the machining process quickly without sacrificing quality. The machine's stability and rigidity play a significant role in achieving these objectives, enabling it to withstand the forces generated during the EDM process while minimizing vibrations and maintaining precise positioning. Finally, advanced control systems and software, including CAD/CAM integration and adaptive machining capabilities, enhance the machine's versatility, ease of use, and overall performance.
Based on these traits, here are five manufacturers of wire EDM machines that were recognized for their popularity and reputation in North America:
Mitsubishi Electric is a well-established manufacturer of wire EDM machines known for their precision, reliability, and advanced technology. Their machines often feature high-speed cutting capabilities, superior surface finish, and excellent accuracy. Mitsubishi Electric is also recognized for its user-friendly CNC controls and software, allowing for efficient programming and operation.
Mitsubishi Electric's MV series of wire EDM machines, such as the MV1200S and MV2400R, in particular,have been well-received in the market. They incorporate advanced technologies like non-contact cylindrical drive systems and intelligent automatic wire threading, which enhance productivity and reliability.
Makino is another prominent manufacturer in the wire EDM machine market. Their machines are highly regarded for their stability, durability, and exceptional performance. Makino's wire EDM machines often incorporate advanced control systems, high-speed machining capabilities, and intelligent automation features. They are known for their ability to achieve tight tolerances and maintain superior accuracy in complex machining applications.
Makino's popular wire EDM machines include the U6 H.E.A.T. Extreme. The U6 H.E.A.T. Extreme utilizes high-energy applied technology to achieve efficient and precise machining results. This wire EDM machine is sought after for its ability to handle intricate shapes, maintain tight tolerances, and deliver superior surface finishes.
Sodick is renowned for its precision wire EDM machines. Their machines are appreciated for their exceptional cutting speed, accuracy, and surface finish quality. Sodick utilizes innovative technologies, such as linear motor drives, to achieve high levels of responsiveness and productivity. They are also recognized for their advanced control systems and intuitive software interfaces, enhancing user convenience and efficiency.
Sodick's AG series, including models like AG400L and AG600L, have gained popularity in the wire EDM market. In addition to their typical benefits, the AG series machines also feature intelligent control systems, advanced wire threading capabilities, and user-friendly software interfaces. Customers are attracted to Sodick's wire EDM machines for their reliability, productivity, and ability to handle complex machining applications.
GF Machining Solutions offers a wide range of wire EDM machines designed for various applications. Their machines are favored for their precision, versatility, and reliability. GF Machining Solutions incorporates intelligent features such as automatic wire threading, adaptive machining, and advanced tooling options. Their machines often provide high cutting speeds, optimized energy efficiency, and advanced automation capabilities.
GF Machining Solutions' AgieCharmilles CUT series, such as the CUT E350 and CUT P550, are widely recognized in the market. As noted, these machines offer versatility, precision, and advanced automation features. Additionally, the AgieCharmilles CUT series machines incorporate intelligent features like automatic wire changing, collision protection systems, and advanced tooling options. Customers are attracted to GF Machining Solutions' wire EDM machines for their performance, flexibility, and ability to optimize productivity.
Fanuc is a well-known manufacturer of CNC machines, including wire EDM machines. Fanuc emphasizes user-friendly interfaces and intuitive programming, allowing operators to easily set up and control the machining process. Their machines are also recognized for their accuracy, efficiency, and long-term reliability.
Fanuc's Alpha C600iA is a popular wire EDM machine known for its robust construction, stability, and traditional reliability. It offers excellent cutting performance, high precision, and user-friendly operation. Fanuc’s Alpha C600iA emphasizes the integration of their CNC control systems with their wire EDM machines, allowing for seamless programming, monitoring, and control. The Alpha C600iA is favored by customers for its accuracy, durability, and ease of use.
It's important to note that the right machine will depend on your specific requirements such as the level of repeatability provided, the level of accuracy and cutting speed required, and your budget. Additionally, it's advisable to consult industry reports, review market trends, and reach out to industry experts or suppliers in the wire EDM machine market before making any selection.
Due to its intrinsic characteristics, the wire EDM technique is perfect for elaborate designs, complicated geometries, and components that call for geometric angles that are impossible to produce using conventional production processes.
The automobile sector prefers the wire EDM cutting process over conventional techniques because it ensures precise molding and drilling of even larger parts. In addition, the materials are more enduring and durable due to the EDM process, a feature the automotive industry cherishes.
The medical sector significantly relies on wire EDM services because it outperforms conventional production techniques. Medical equipment needs pieces that are specifically designed, small, and precise. For example, consider that the hand instruments used by doctors and surgeons to produce straight, precise edges during the manufacturing process are necessary for the equipment to be useful during operations.
Manufacturing companies also use wire EDM services for dental and orthodontic equipment. Dental equipment frequently needs to operate with the same precision as medical equipment. For the microscopic components that make up braces, wire EDM is frequently employed.
Wire EDM cutting services are also frequently utilized in aerospace technology. This process creates parts for the engine, fuel system, landing gear, and other high-stress, high-temperature systems because these parts can survive the extreme heat and pressure required to keep the technology running.
Many molds, including punch dies, squeeze dies, powder metallurgy molds, bend molds, and plastic molds, are machined using wire-cut EDM. Wire EDM can easily cut terrace dies, punch plates, stripper plates, and other materials by modifying different compensation values.
EDM machining is a contemporary machining method based on the removal of material from a part using thermal energy. The material is removed by local melting or vaporizing small areas on the surface of the part being machined...
Sinker Electrical Discharge Machining (EDM) is a metal machining process used to create molds, dies, and parts using electrical sparks to erode material from a workpiece. It is preferred over other machining processes due to...
The normal functioning of CNC machines is done along the three Z, X, and Y axes. The five axes machines have two more axes accessible, which are namely A and B. The addition of the two extra axes makes it easy to cut complex and intricate parts...
CNC machining is an electromechanical process that manipulates tools around three to five axes, with high precision and accuracy, cutting away excess material to produce parts and components. The initial designs to be machined by CNC machining are created in CAD...
The CNC process was developed in the 1950‘s and took a leap forward in the 1980‘s with the addition of computerization. Unlike other production processes, CNC begins with a rendering by a computer, which creates a two or three dimensional representation of the part to be produced...
G-code is the name of a plain text language that is used to guide and direct CNC machines. For most modern CNC machines, it isn‘t necessary to know the meaning of G-codes since CAD and CAM software is translated into G or M codes to instruct a CNC machine on how to complete a process...
Computer numerical control (CNC) is a fundamental part of modern manufacturing. The majority of machines operate using instructions and guidelines that have been downloaded using a CNC program controller...
Water jet cutting is a manufacturing process that uses high pressure jets of water provided by pressurizing pumps that deliver a supersonic stream of water to cut and shape various types of materials. The water in water jet cutting is...
Machining is a manufacturing process used to produce products, parts, and designs by removing layers from a workpiece. There are several types of machining that include the use of a power driven set of machining tools to chip, cut, and grind to alter a workpiece to meet specific requirements...
The CNC process, computer numerical control, is a method of manufacturing where programmed software directs the operation of factory tools and machinery. It is designed to manage a wide range of complex machines from grinders and lathes to mills and routers...