EDM Machining
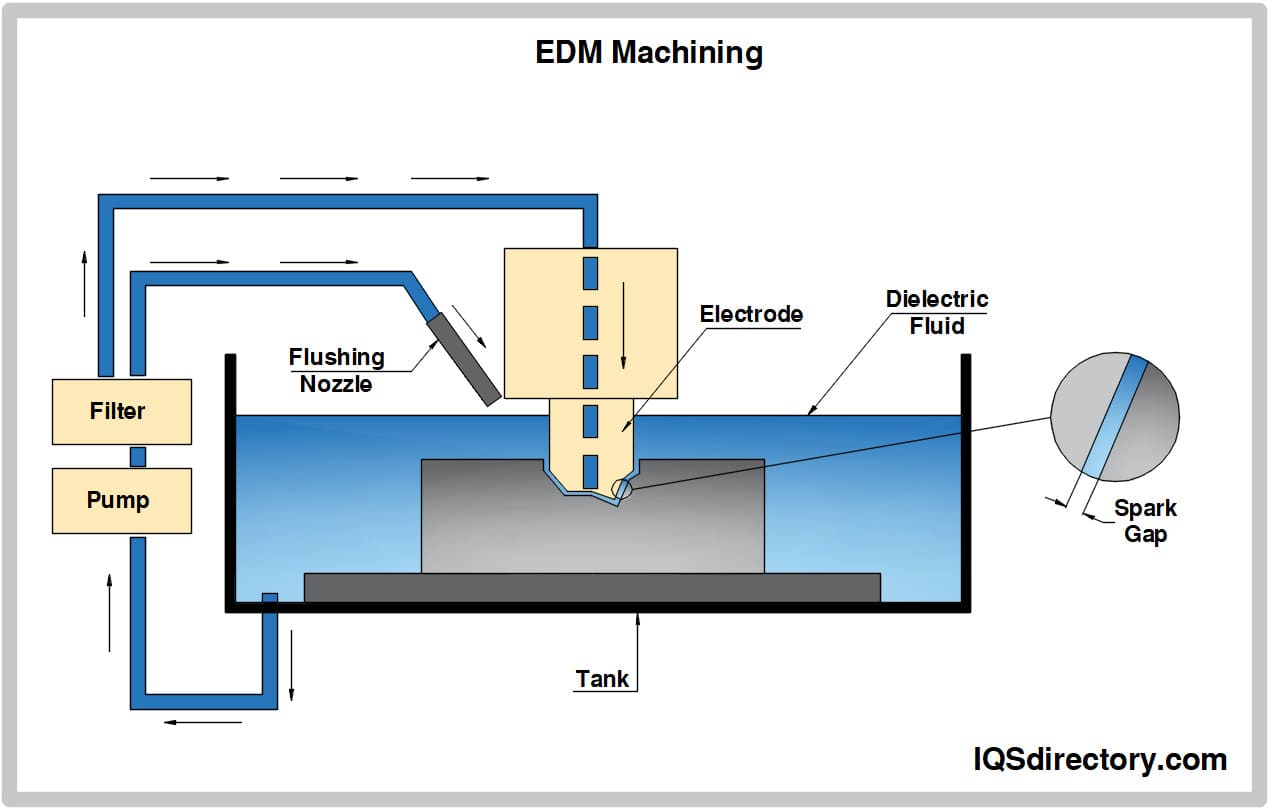
EDM machining is a contemporary machining method based on the removal of material from a part using thermal energy. The material is removed by local melting or vaporizing small areas on the surface of the part being machined...
Please fill out the following form to submit a Request for Quote to any of the following companies listed on
This article contains everything you need to know about sinker EDMs and their use.
You will learn.
Sinker Electrical Discharge Machining (EDM) is a metal machining process used to create molds, dies, and parts using electrical sparks to erode material from a workpiece. It is preferred over other machining processes due to its ability to produce complex shapes with a high degree of accuracy and repeatability.
The sinker EDM process gets its name from how it sinks into a workpiece as it erodes the material. The process is sometimes referred to as burning as it creates micro sized craters to shape and form the workpiece. The workpiece has to be electrically conductive or a ferrous alloy to be able to be shaped by sinker EDM.
The sinker EDM process is used by manufacturers due to its ability to cut extremely tiny pieces with exceptional tolerances. It is often used to produce detailed products that are too delicate to be produced using any other process. Sinker EDM is used to produce prototypes for customers to examine and for engineers to adjust for other means of processing.
The first step in the Sinker EDM process is to design the electrode. The electrode is typically made of copper or graphite and is shaped to match the desired shape of the workpiece. The electrode is mounted on the machine's electrode holder and connected to the power supply. The choice of electrode design has a major impact on the number of electrodes needed, the rate of metal removal, the surface finish, and the running stability. To enhance the efficiency of the process, multiple electrodes can be used with each electrode creating its own spark and only one electrode sparking at any one time.
Included in electrode design is choosing the type of electrode, which includes staged, pieced, and partial area electrodes. Each of the types are differentiated by the number of electrodes, the material used to produce them, and how much cutting they perform.
A dielectric fluid is used in the EDM process to act as a coolant and an electrical insulator. During the EDM process, the dielectric fluid circulates around the electrode and workpiece to prevent arcing and to remove the eroded material. It helps control the temperature of the machining area to prevent thermal expansion.
The types of dielectric fluids are made from petroleum based liquids or synthetic oils with some water based fluids also being available. Dielectric fluids are formulated to have high electrical resistance and low viscosity with the ability to insulate the electrical discharge and flow freely around the workpiece. Some types of dielectric fluids contain additives to improve their cooling and lubricating properties.
The dielectric fluid is a highly critical part of the sinker EDM process since it flushes away the bits of burnt metal and electrode from the work area into the filtration system.
There are specifications that are required regarding the workpiece that have to be followed to ensure the success of the sinker EDM process. The material that is chosen must be electrically conductive but does not have to be machinable. A critical aspect of the preparation of the workpiece is to ensure that it is sufficiently cleaned with contaminates, dust, particles, and other materials removed. Any unwanted materials can interfere with the reaction between the workpiece and the electrode and may damage the electrode. In addition, the reaction between the workpiece and the electrode will be more efficient and unhampered.
The initial preparation of the workpiece involves submerging it in a vat of deionized water or a non-conductive lubricant, which removes the molten material that is cut from the workpiece and pulled away from the electrode. The fluid into which the workpiece is placed is kept in constant motion to cool the removed particles and move them away from the electrode and workpiece. In addition, the deionized water or non-conductive lubricant helps control the discharge between the workpiece and electrode.
During sinker EDM, the fluid is closely monitored to ensure its purity, which is a crucial factor in regard to the success of the process. In addition, as with most machining processes, the temperature of the fluid is checked such that it is constant and stable.
The electrode is carefully positioned over the workpiece where an electrical discharge will occur in a voltage gap between the workpiece and the electrode. It is essential that the electrode not touch the workpiece, which would cause the electrode to be welded to the workpiece and damage the electrode and the workpiece. When properly positioned, the heat from the discharge vaporizes small particles from the workpiece that are washed away with the flow of the dielectric fluid.
During sinker EDM machining, the electrode is positioned such that it never comes in contact with the workpiece. It is close enough for the spark to melt material but is not so close that it touches the workpiece. This aspect of the process removes the need for cutting pressure, which is part of the unique nature of sinker EDM.
Since the electrode is the essential part of the sinker EDM process, it is carefully positioned within the dielectric fluid and in close approximation to the workpiece. They have a reverse shape of the features they create and are made of various materials with copper and graphite being the most common. The process of positioning the electrode is slow and continues until electric breakdown begins and sparks jump across the spark gap.
The power supply sends a high-voltage electrical discharge between the electrode and the workpiece. This creates a spark that erodes the workpiece material and shapes it according to the electrode's geometry. When the electrode gets close to the workpiece, an electrical sparks jumps between it and the workpiece. The spark generates temperatures as high as 8000°C up to 12000°C (14,432°F up to 21,632°F), which erodes the metal in the shape of the electrode.
Spark energy is a combination of amperage, voltage, and on-time. With each spark pulse, the electrical current increases until it reaches its set level. Before this can happen, the gap voltage has to create an ionization path. As the current flow begins, the voltage drops until it reaches a working level. The working level of the voltage is set by the controls of the sinker EDM process and determines the width of the spark gap between the workpiece and the electrode. As the voltage increases, the size of the gap increases.
As the on-time and amperage increase, more heat is produced with each discharge from the electrode. A faster burn rate increases the amount of heat, which can cause larger particles to be removed from the workpiece, pieces that are referred to as swarf. With the presence of swarf, the EDM machine sparks in the same place repeatedly damaging the workpiece and its finish.
The spark is controlled by adjusting the pulse duration, current, and other parameters of the power supply. The workpiece is eroded in a controlled manner, removing minute particles of material. The dielectric fluid circulates around the machining area to remove the eroded material and prevent arcing. This circulation is critical in removing swarf and its negative effects.
Initially, the process of a sinker EDM was controlled by operators that closely monitored the process and were trained to make adjustments when complications occurred. The speed of modern manufacturing and the advent of CNC machining has led to the development of adaptive monitoring and control, which reads the conditions of the spark and changes the readings into digital signals that are read by the sinker EDM’s controller.
Since swarf is a problem in the voltage gap, the monitoring system checks for contaminants and makes adjustments that do not affect the overburn or integrity of the surface of the workpiece. Changes in the gap voltage, increasing the off time, and changing the jump cycle assists in the adjustments that are necessary due to contamination.
The progress of the process is monitored by the adaptive controller that switches on and off as needed in accordance to the electrode size, material removal rate, contamination, and the desired surface finish. The adaptive controller adjusts the machining parameters as needed to ensure that the process proceeds smoothly.
The adaptive control system has a long list of parameters that it uses to oversee the sinker EDM process. It responds to changes quickly without the need for manual intervention and can operate within a wide production range.
Sinker EDM produces very smooth, even, mirror-like finishes, which may require extra processing depending on the parameters of the part being produced. Finishing enhances the appearance and durability of the part as well as meets the dictates of its design.
Sinker EDM can be used to shape the hardest and most difficult metals as long as they are conductive. The process results in very low distortion and no residual stress. The initial EDM process was discovered in 1943 when electrodes were submerged in a dielectric fluid to make controlled erosion possible. The process was developed to replace etching tools that did not have sufficient power to cut through metals.
Small hole EDM uses a small hollow diameter spinning electrode made of brass to form and shape the workpiece. The process of small hole EDMs is similar to drilling but has the advantages of EDM machining. Known as EDM drilling or EDM micro hole drilling, small hole EDM machining requires very little force and is ideal for making delicate precision parts.
As with all forms of EDM processes, small hole EDM machining can be used on any ferrous metal regardless of its hardness. The brass tube channels electricity to make different size holes. Small hole EDMs are used to place minute holes in the workpiece, even when the workpiece has inclined faces or difficult to reach positions.
Conventional Sinker EDM, known as die sinking EDM, uses an electrode made of copper or graphite shaped to the desired profile of the part being machined. Once the electrode is powered, it is lowered into dielectric fluid where sparks are discharged to erode the material from the workpiece to form the desired shape.
The process of conventional sinker EDMs allows for accurate replication of precision parts without concerns for deflection with tolerances of +/- 0.0003 inch. The exceptional level of precision provided by conventional sinker EDM has made it the go to method for the creation of prototypes and intricate small parts.
Orbital Sinker EDM is a variation of conventional sinker EDM that uses a specially designed electrode that rotates and orbits around the workpiece during machining. It creates a larger discharge area and reduces electrode wear to allow for faster and more precision machining.
The process of orbiting sinker EDMs is used for roughing and finishing a workpiece to save time on polishing. They have an orbiting head that moves the electrode around the center of the workpiece that allows for more precision control. The size of the burn is adjusted in accordance with the size of the electrode. The use of an orbiting sinker EDM eliminates the need for extra electrodes to perform the same function.
The electrode for an orbiting sinker EDM provides flusher conditions and eliminates tapering on cavity walls. The process can easily be controlled to achieve the desired size of the holes. Orbiting sinker EDMs makes it possible to perform Z axis burns to Z depths such that it is possible to remove tapers that are caused by secondary discharge. In addition, the orbiting motion produces a vacuum that draws in more of the dielectric fluid into the gap, which forces out particles for a cleaner finish.
Ram EDM produces its spark along a formed electrode instead of a wire. A servo system prevents the ram electrode from touching the workpiece. The process has the same capabilities as wire sinker EDM and is able to form parts with exceptional precision and intricacy. Ram EDM allows for a wider range of machining operations, including the production of more complex shapes and features.
With wire or small hole EDM, material is removed along a simple line or at a single point. Ram EDM makes it possible to remove material to form three dimensional shapes with the electrode being a negative image of the completed workpiece. The electrodes for ram EDM are CNC machined to create the negative image. Normally made of brass, the Ram electrode is capable of machining hard metals like tungsten carbide and Inconel.
Multiple electrode sinker EDM is able to machine several areas of the workpiece at the same time. Each of the areas being machined has the same shape, accuracy, and finished surface. It is a faster time saving process that reduces the amount of set up time, lowers the amount of necessary energy, but can have inaccuracies and produce rough finishes.
The use of the multiple electrode sinker EDM process increases the efficiency and precision of the process. The multiple channels allow for better flushing of debris and cooling, which helps speed up cutting and reduces the wear on electrodes. The use of multiple electrode sinker EDM is ideal for complex and precision applications and produces high quality finishes.
The development of multiple electrode sinker EDM was in regard to the high demand for increased material removal rates, better surface finishes, and a decrease in energy consumption since single electrodes require a great deal of energy. Since a multiple electrode sinker EDM can process several areas at the same time, the machining process takes less time and speeds up rough machining, regardless of the extra set up time.
Pulse Power Sinker EDM is a process that uses advanced pulse generators to control the discharge energy for longer periods of time and improve machining accuracy and surface finish. It is used for materials that are difficult to machine using conventional Sinker EDM processes.
The on time pulse of energy applied is extended with pulse power sinker EDM. With a longer pulse, more material is removed from the workpiece. It produces larger and broader holes than those created by short time pulses. Additionally, more heat sinks into the workpiece and spreads, which means more area of the workpiece will be affected with the affected area being deeper.
Each variation of Sinker EDM has advantages and limitations. The selection of the best process depends on the specific application and desired results. All metal working manufacturers provide guidance and expertise in regard to determining the best process.
The sinker EDM process is ideal for cutting holes into hardened materials. In some instances, a small pilot hole can be drilled into the workpiece after which a wire EDM is fed through the hole to complete the hole forming process. For blind hole applications and larger holes, this process does not work and requires the use of a specialized hole making electrode called a “hole popper”.
Using a continuous flow of dielectric fluid, a rotating conductive tube drills a large hole in a workpiece. The flow of dielectric fluid flushes the cut as the tube removes material. The process is capable of creating accurate and precise holes in the hardest materials.
The wire EDM was perfected in the 1960s as a method for making dies from hardened steel. The process uses a thin wire that moves in a controlled pattern like a woodworker’s scroll saw. As the wire continuously moves and erodes the workpiece, wire from a spool is fed into the discharge area to be able to provide a fresh discharge path.
The “cheese cutter” method has to pass through the workpiece to make a two dimensional cut in a three dimensional part. With modern sinker EDM machines, the movement of the wire along the XY plane is programmed by CNC coding.
A significant aspect of all forms of EDM machines is their ability to process any material that is conductive, which allows for shaping of depths that are hard to achieve using any other cutting method. When selecting an EDM machine, there are several factors to consider that begin with the desired design.
EDM machines are known for delivering exceptional precision cuts in any form of conductive material. The best sinker EDM machine for a project is determined by the material to be cut, the desired precision of the cut, and the required surface finish. The various types of sinker EDM machines are widely known for cutting blind holes and cavities in molds and dies.
The Mitsubishi MX600 is the latest development in sinker EDM machines. It has a granite base that isolates the workpiece and reduces floating capacitance. The improved cutting speed of the MX600 produces ultra fine surface finishes due to its nano-FS circuit that cuts finishes as low as 1.4 µ without any special tooling. The main basic feature is the auto feed of wire for wires being as small as 0.0008 inch (0.02032 mm).
Dielectric oil fluid eliminates cobalt depletion in carbide machining and rust on iron based machining. The guideways have linear motion with extra long linear guide bearings to eliminate guide waving.
ONA has a wide selection of sinker EDM machines with each machine designed to meet the needs of any manufacturing condition. The ONA IRIS T7 reduces erosion time by 50% with a 200% production efficiency and can handle workpieces weighing 28 tons (25000 kg). It is a three axis system with a reinforced C axis that provides stability in erosion. The touch screen interface makes the programming of cuts easy and efficient.
Makino sinker EDM machines come with a large touch screen interface that can be controlled like a smart phone making it possible for operators of all skill levels to operate the machine with limited training. The erosion rate for Makino sinker EDM machines is increased by an improvement in flushing and debris removal with a four times faster Z axis jump rate and an acceleration rate that is 30 times faster than previous technologies. These advancements have reduced the number of electrodes, lowered costs, and produced more uniform finishes.
EDM wire machines by Fanuc are referred to by the proprietary name of Robocut, a name that is used for three types of designs, which include models for small, medium, all around, and large part cutting machines. Robocut machines come with a compensation factory calibrated grid that allows for pitch correction of the worktable. As with several models of EDM machines, Robocut machines come with automatic wire threading software that rethreads wire in ten seconds. Key components of the Robocut design is the advanced user interface and an economy mode that allows for energy and wire use savings.
Sodick sinker EDM machines have a linear motor for vibration free operation and no backlash, which makes it possible to have high cutting accuracy with exceptionally fine finishes. They offer several types of sinker EDM machines with a variety of XYZ travel ranges that include ones that are a little over a foot to ones capable of traveling several feet. The core technologies of Sodick sinker EDMs are the power supply unit, discharge unit, the linear motor, motion controllers, and the fine ceramic components.
Material selection is an important consideration in sinker EDM, since the type of material being machined has an impact on the success and outcome of the process. There are several factors that need to be considered when selecting a material for sinker EDM machining. The key factor in the process is the conductivity of the workpiece that is being shaped.
Only metals with conductivity can be used in the sinker EDM process. Other materials, such as ceramics, can have conductive metals included in their processing such that they can be shaped by sinker EDM. The process of sinker EDM includes the easy flow of electricity to create the electrical discharge. A conductive workpiece completes the electrical circuit created by the sinker EDM machine and allows current to pass through it. Untreated ceramics and plastics are unable to conduct electricity and cannot be processed by sinker EDM.
All conductive materials can be machined using the sinker EDM process. The range of metals includes all forms of metal and graphite, which is a non-conductive material used for producing electrodes. Materials such as ceramics and some plastics can be used for the process when they have conductive metals added to their structure. The EDM process necessitates the use of conductive since it involves creating an electric circuit that is completed by the conductive metal of the workpiece.
The melting point of a metal is an important consideration that impacts the amount of energy required to melt the metal and the rate of the erosion process. Higher melting points require more energy and longer cycle times. The sinker EDM process is not affected by the hardness of a metal but its thermal properties determine its machinability. There is a wide range of melting points for metals, which is determined by the metal’s composition and purity. These aspects of metals are important considerations in regard to the selection process.
The melting temperature of a workpiece determines how the sinker EDM machine performs and is measured by the metal removal rate (MRR), which is affected by a metal’s melting point and thermal conductivity. Of the various metals used for sinker EDM machining, tungsten carbide has an extremely high melting point.
The melting point of a metal affects the production process and determines the types of machines that can be used. Higher melting points of metals require equipment to work harder and use more energy. In addition, the melting point plays a pivotal role in the speed of the EDM process in regard to material removal and electrode wear.
Melting Point of Various Workable Metals | ||
---|---|---|
Metal | F° Melting Point | C° Melting Point |
Aluminum (6061-T6) | 1080° - 1200° | 582° - 649° |
Inconel (718) | 2300° - 2437° | 1260° - 1336° |
Stainless Steel (410) | 2700° - 2790° | 1482° - 1532° |
Tool Steel (06) | 2732° | 1500° |
Titanium (Ti-6AL-4V) | 3000° | 1649° |
Tungsten Carbide (K-68) | 6054° | 3360° |
Machinability refers to how easy a metal can be shaped and cut. Metals that can be cut easily require less energy and can be deformed to achieve the desired shape. Machinable metals produce better parts with tighter tolerances and exceptional surface finishes. They can be produced quicker, require less tool wear, have a longer useful life, and save on machine shop assets.
In the sinker EDM process, there is a trade off between strong metals and weak ones in regard to machinability and performance. Since every design defines certain parameters and the use of different metals, designers have to determine which metal to use against the amount of machining required to produce the final product. Harder metals with low machinability take more time to process, shape, and form. In addition, they wear out tools and require constant adjustments.
When sinker EDM is used to produce dies, the metals to be processed are very dense and hard and require a great deal of energy to process. Such metals required for the manufacture of dies have to be very hard due to the nature of their function. Essentially, as with the manufacture of dies, certain processes necessitate the use of very hard metals that have low machinability. The sinker EDM process, in those cases, is necessary since it can produce products with minute details and tight tolerances.
The surface finishes produced by sinker EDM processing are different from those found with other material removal processes. The texture is random, and the multiple passes creates a nearly mirror quality. Although the surface finish influences the appearance of a part, it is also important in applications where parts slide over one another. The sinker EDM process creates micron (µ) sized holes across the workpiece, which is different from cutting tools that leave a directional lay.
To achieve the most accurate finish, most parts require multiple passes with the first pass being the rough cut, which removes the slug. This initial or rough cut involves a hotter, more intense process. The second cut is the finish cut that defines the geometry of the part while the final cut, surface finish cut, is a very fine cut that produces an extraordinarily fine smooth surface.
Since any form of metal can be processed using sinker EDM, the desired parameters for the surface are established during the initial planning of a part, which includes the proper metal. The selection of the metal plays a factor in the amount of time involved in creating the finish since certain metals require more processing
One of the main reasons for using sinker EDM is the types of finishes that it produces that require very little after secondary processing. Sinker EDM is unaffected by the hardness of a material, which makes the selection of type of metal easier.
The rule for using sinker EDM as a method of processing is that the metal be electrically conductive, which limits the choice of metals to ferrous metals and aluminum. With this as the criteria, it would seem that copper would be the ideal metal since it is so highly conductive. Although copper is used for sinker EDM machining, it is not necessarily the first choice since the process heats copper so quickly and requires constant control.
All forms of steel are machined by the sinker EDM process. They are used for their toughness, strength, durability, and resilience. Alloy steels have elements added to improve their properties including chromium, cobalt, columbium, molybdenum, manganese, nickel, titanium, tungsten, silicon, and vanadium. The various alloys change the properties of steel and add desirable characteristics.
Copper is the perfect choice for the sinker EDM process since it has such high conductivity. The use of copper restricts the process due to copper heating quickly and passing the heat through the metal, which requires that the process be slowed and carefully controlled. Sinker EDM works with copper components that have thin walls without warping or distorting the walls.
Tungsten carbide is a difficult metal to machine since it has high hardness and melting point and is brittle, which makes sinker EDM the perfect method for machining it. The heat that is generated is conducted differentially due to the structure of tungsten carbide.
Electrodes for tungsten carbide are made of copper using negative electrode polarity, which produces very low surface roughness. When machining tungsten carbide, using sinker EDM, the removal rate is very slow due to the nature of the metal. Small intricate and complex geometries can be produced using the process.
Titanium has exceptional strength to weight ratio, corrosion resistance, and the ability to withstand high temperatures. Due to its biocompatible properties, it is widely used for medical implants. The high hardness of titanium makes it difficult to machine using conventional machining methods. As with tungsten carbide, it is machined using copper electrodes with pulse on and off time.
Nickel will alloy with several different different metals including chromium, iron, molybdenum, and copper. The wide variety of alloys makes it possible for nickel to have several different properties and characteristics, such as resistance to corrosion, high temperature scaling and strength, exceptional shape memory, and low coefficient expansion. It can be combined with a single metal and combinations of metals, like nickel chromium and molybdenum and nickel chromium and cobalt.
A common use of nickel alloys is in high stress applications since they can continue to function in the hottest and harshest conditions. Regardless of the exceptional strength of nickel alloys,they are easy to work and form without becoming brittle, a factor that adds substantially to metals like iron, which is brittle, and copper, which is soft and ductile. Combined with nickel, iron and copper become stronger, more resilient, and long lasting. When copper is combined with nickel, the resulting alloy can last over thirty years.
A key aspect of nickel's strength is its melting temperature, which is about 1455°C (2651°F), a factor that gives it stability when exposed to high temperatures. In addition, nickel has a low density and controlled thermal expansion and conductivity, characteristics that make nickel effective as a heat resistant material.
Aluminum is an extremely abundant metal that is used in a wide assortment of applications and products. Its natural resistance to oxidation, corrosion, and rust makes it a highly durable metal. Aluminum is seldom used in its pure form and is normally alloyed with other metals to improve its properties. It is well suited for work with sinker EDM due to its ability to be shaped into intricate and complex shapes.
The list of metals above are a small sampling of the metals that are processed by sinker EDM machining. In essence, any metal that is conductive can be machined and shaped using the process. It is up to the manufacturer and customer to determine the best metal to fit an application.
The parts of the sinker EDM process include the worktable, electrode, tank, dielectric fluid, servo control system, control panel, filtration system, and a power source. The central part of the process is the workpiece that is made of a conductive metal and capable of completing an electrical circuit. The dielectric fluid is deionized water or a non-conductive lubricating oil. The various components work together to form and shape the workpiece to create the final product.
The worktable is the part of the machine that holds the workpiece in place and secure during the machining process. It can be moved in the X, Y, and Z axes to allow for precise positioning of the workpiece with some versions of worktables having positioning for A and B axes. Worktables come in several forms depending on the requirements of the EDM machine. They can have multiple axis settings and are designed to be unaffected by dielectric water or oils. The internal structure of sinker EDM worktables is isolated from the electric current produced by the process.
The five axis design of sinker EDM worktables makes it possible for creating precision cuts with exceptional tolerances. The workpiece can be continuously rotated allowing the electrode to remain in one position. An essential aspect of the worktable is proper positioning of the electrode such that it does not get too close and leaves sufficient space for the discharge gap.
The tank is filled with the dielectric fluid that is deionized water or non-conductive oil. The sinker EDM process takes place in the tank, which is an exceptionally sturdy container that is capable of withstanding the stress of the sinker EDM process. In essence, the tank is the central point of the process since it contains the dielectric fluid, the worktable, the workpiece, and the electrodes that shape the workpiece.
An essential aspect of the tank is the flow of the dielectric fluid such that the particles from the cutting process are removed from the electrode and the workpiece. Although all tanks serve the same purpose, each tank is designed in a unique way to ensure the constant flow, with some tanks having a special mechanism to increase the rate of the flow.
Since dielectric fluids are neutral and non-acidic, there is little concern for damage to the tank from its contents. What is important is that the tank be tightly sealed along its seams to prevent leaks, which can be damaging to the process. Specially designed tanks are connected to a reservoir of dielectric fluid that allows the fluid to be taken from the tank, filtered, and returned to the tank. This particular method ensures the purity of the dielectric fluid and its flow.
Control of the arc of the electrode determines the quality of the surface of the workpiece. This involves uniform power and energy from the power supply, which supplies the current and voltage to create the arc. Current for the process is controlled electronically from the power supply while the voltage across the arc is dependent on the gap distance, which is regulated mechanically. The control of the electronic and mechanical functions of the system are referred to as the EDM servo motor system.
The power supply creates the duration of the arcs, which can last for 1 microsecond up to 250 microseconds. Since the sinker EDM system is very slow, faster pulses are more desirable with the frequency of arcs being in the tens of kHz for efficient machining speeds.
The voltage of the power supply is set high enough to initiate the sparking process with over 100V being sufficient but not too extreme. The speed of the pulse, the current, and the duration of the arc are controlled by the power supply. In some cases, switching the polarity off the workpiece and the electrode electronically avoids the need to manually manipulate the process.
The electrode is a specially shaped tool made of conductive material, such as copper or graphite. It creates the desired shape and is connected to the power supply. At the initiation of the process, it is lowered with the workpiece into the dielectric fluid in the tank. The electrode produces a non-contact sparking that removes material from the workpiece.
The servo control system is responsible for controlling the movement of the electrode, the worktable, and the spark discharge gap. It has a gap sensor that measures the voltage from each machining pulse. Its precision motor and feedback sensors ensure that the electrode moves in the correct direction and speed. The servo control system determines optimum spacing between the electrical discharge electrode and the workpiece.
The filtration system removes debris and particles from the dielectric fluid to ensure that the machining process is clean and efficient. During the sinker EDM process, sparks create minute holes in the workpiece that are removed as waste material that could interfere with the process. The filtration system captures the waste material.
The control panel is the interface between the operator and the machine. It allows the operator to input the machining parameters and monitor the progress of the machining process.
Each component of a Sinker EDM machine is essential to the overall performance and accuracy of the process. Manufacturers provide guidance and training regarding the use of sinker EDM machines. They design and produce equipment that perfectly fits the needs of their customers.
Aside from the simple linear cutting types of sinker EDM machines, there are multi axis machines capable of adding shapes and tapers on the bottom, top, and sides of a workpiece. These multi axis machines make the production process go faster and increase efficiency.
High-speed sinker EDM machining speeds up the process by increasing the rate of flushing and debris removal using a Z axis cycle rate that is faster. Since most EDM machining is slow and takes time, any method that speeds up the process helps to bring EDM machining inline with modern manufacturing methods. The introduction of high-speed sinker EDM makes it capable of competing with traditional milling methods.
Part of the advancements in high-speed sinker EDM is the introduction of automatic tool changers, which make it possible for machines to operate unattended as electrodes can be changed every 30 seconds. In addition, upgrades to sinker EDM tanks allows for quicker drainage of dielectric fluid, a factor that reduces cycle times.
High-Speed Sinker EDM machines use advanced technologies such as high-frequency generators, advanced servo systems, and high-speed spindles to improve machining speed and precision. The various innovations are an effort to make sinker EDM a more acceptable machining method for a wider range of manufacturers.
At the center of making sinker EDM machining more acceptable is speed. It may be interpreted that these enhancements require sacrifices of other features of the process. Regardless of the speed at which high-speed sinker EDM operates, it still has the same precision and accuracy that has made it popular.
Typical sinker EDM processing is a three axis approach to shaping the workpiece. It is an efficient method that produces precision cuts with extraordinary accuracy. The addition of the fourth axis increases the movement of the electrode and its ability to make a wider range of cuts, which lowers the cycle time.
The three axis method of sinker EDM machining is linear, a factor that limits the movement of the electrode. A fourth axis adds rotary movement to the process and allows the workpiece to be cut along the B axis. This particular feature is common in computer numerical control (CNC) machining and is one of the reasons for the success of CNC machining. As new innovations are added to sinker EDM machining, it is being incorporated into the CNC process.
The fourth axis of four-axis sinker EDM machines adds to the standard three-axis motion control, which makes it possible to perform more complex and precise machining operations. The fourth axis is used to control the angle and position of the electrode during machining, which is useful for complex shapes and intricate designs. The axis process makes it easy to reposition the electrode to make multiple cuts with the pattern.
As four axis sinker EDMs add additional movement to the electrode, five axis sinker EDMs further increase the motion of the electrode in order to produce more complex designs. The increase in the number of axes closely relates to enhancing the speed of the process and decreasing cycle times.
While four axis sinker EDMs add rotational motion to the process, five axis EDMs make it possible to turn the workpiece such that it can be shaped on all its sides. Features that are added at the top of the workpiece can be engineered to shape all sides without the need to delay machining in order to reposition the electrode or workpiece. This additional positioning involves the worktable since it is manipulated to accommodate the additional motion.
Essentially, the five axis process increases the efficiency of EDM machining and increases the speed, which is a vital factor in increasing its use. Most CNC machines are capable of five axis machining, a factor that was part of their initial design. By adding this feature to sinker EDMs, they can easily combine with the CNC process.
Automated sinker EDM machines are a complex and intricate form of EDM machine with robotic features that enhance the performance of the sinker EDM process. An articulated robot, a robot with several joints to perform multiple motions, adds and removes electrodes and workpieces and forms their layout. The size of the robot is determined by the weight and configuration of the workpiece.
The integration of robotics and automation has greatly advanced the importance of the sinker EDM process and allows it to produce more complex and consistent components in greater quantities. Precision control is used to position electrodes and removes human error, while improving part quality. Higher volumes of parts can be produced without affecting the quality of parts.
The use of the automated sinker EDM process helps tooling achieve quicker offline setup and increases the accuracy and efficiency of the system. Included in the system is control of the dielectric tank, which has to be configured to comply with the parameters of the system. The main feature of automated sinker EDM machining is automated electrode and parts changing with the long term effect being lower costs and higher productivity.
The process for an automated sinker EDM is computer programmed, a factor that increases repeatability and reduces lead times. Once a process is proven, it can easily be reproduced without making adjustments to the system. Part quality increases, labor costs lower, and profitability increases.
As with several other aspects of the improvements in sinker EDM processing, automated sinker EDM machines increase the efficiency of the process, which helps increase its speed. From the beginning of the process to the final product, every aspect of machining is closely controlled and programmed.
Micro Sinker EDM machines are designed to produce extremely small and precise parts. These machines use advanced technologies such as ultra-fine wire and high-precision servo systems to achieve very high accuracy and surface finish quality. Micro scale processes are capable of making cuts down to the micron (µ) level, one millionth of a meter or micrometer.
As a specialized form of sinker EDM, micro sinker EDM is capable of creating features that are the size of 10 µ (0.0004 inch). The electrodes used for the process are also very small in order to cut miniature holes, slots, and shapes.
Sinker EDM is used with CNC machining when a very small feature is necessary in a fragile section of a component. Wire is constantly fed into the dielectric fluid in a CNC code controlled machine and guided by upper and lower diamond guides that control the wire as they are fed instructions from the CNC machine controller. The multiple axis movement of the CNC sinker EDM makes it possible to program intricate, precision cuts for delicate shapes.
The enhanced capabilities of sinker EDM machining is further improved with the technology of a CNC machine. The choice of sinker EDM technology with CNC machines is due to the inability of CNC milling and cutting tools to make the highly precise cuts available with a sinker EDM.
As with all forms of production equipment, there are regulations and standards regarding the use of sinker EDM machines. In the United States, they are subject to the oversight of the Occupational Safety and Health Administration (OSHA), the National Fire Protection Association (NFPA), the Environmental Protection Agency (EPA). Other laws covering their use are enacted by state and local authorities as well as international organizations.
The main concern with sinker EDM processing are the toxic and dangerous fumes and materials that are released during the process, which demands significant oversight and control. There are specific stipulations in regard to measures that have to be taken to ensure the safety of workers and the manufacturing environment. Part of the safety protocols are in regard to filters and ventilation while others are in regard to the performance of the process. In addition, workers are required to wear protective coverings that are outlined by manufacturers in the machine’s safety manual.
OSHA has a number of regulations that apply to Sinker EDM machines and operators. For example, OSHA's General Industry Standard 1910.212 requires that machinery and equipment be guarded to protect workers from hazards such as moving parts, electrical hazards, and flying debris.
The NFPA has a set of standards that apply to the use of Sinker EDM machines in manufacturing environments. These standards include requirements for electrical safety, fire prevention, and hazardous materials handling.
The EPA regulates the disposal of waste materials generated by the Sinker EDM process. This includes regulations governing the disposal of spent electrode materials, cutting fluids, and other waste materials.
State and local governments may have their own regulations that apply to the use of Sinker EDM machines. For example, some states may require permits or licenses to operate Sinker EDM machines, or may have regulations governing the disposal of hazardous waste materials.
The ISO is a world recognized organization that has developed standards regarding a wide variety of manufacturing processes. EDM machining is covered under ISO 28881:2022 for machine tools, safety, and electro discharge machines. Since the majority of sinker EDM machines are manufactured outside the United States, manufacturers and users work vigorously to comply with ISO standards for the safety of their products and workers.
ANSI standard B11.27-2020 outlines the requirements for electro discharge machines. It includes safety requirements and risk reduction measures and is applicable to all die sinking, drilling, CNC sinking, and wire cutting machines. Unlike ISO standards that address requirements for manufacturers, ANSI B11 provides standards for suppliers and users. It is examined and updated yearly as the use of sinker EDM machines is rapidly rising.
The sinker EDM process is ideal for producing small intricate parts with exceptional tolerances. Sinker EDM machines can be programmed to produce a wide variety of shapes regardless of their complexity in any form of conductive metal. Its introduction has dramatically changed the capabilities of parts manufacturers and producers.
The use of sinker EDM processing is due to its ability to create complex and intricate parts that cannot be completed using other manufacturing methods. Hard and difficult to work metals can easily be formed and shaped using the process. Its accuracy ensures that molds and dies have the proper proportions and form in order to produce high tolerance components and parts.
There are several ways to define the versatility of sinker EDM. As with all forms of EDM processing, sinker EDM can shape any form of conductive metal regardless of its density or hardness. This aspect of the process is one of the reasons for its wide use since sinker EDM can easily shape metals that cannot be machined using traditional methods.
The number of configurations, forms, and shapes that can be produced using sinker EDM is endless and includes extremely complex and intricate shapes formed from some of the hardest metals. It is used to produce dies and molds that are required to have the highest tolerances for part and component production.
The consistency of the sinker EDM process is in regard to its accuracy since every part, regardless of its complexity, is produced with a smooth even finish and high tolerance. The EDM process is known for its ability to adhere to the stipulations of a parts design due to its process programming and the lack of stress on the workpiece.
This fact plays a major part in the repeatability of sinker EDM machining. Once the parameters for a workpiece is programmed into a sinker EDM machine, it adheres closely to its programming in a manner such that every part is exactly the same in regard to their dimensions and specifications. The types of accuracy and detail found in sinker EDM machining is difficult to find in any other machining process.
With traditional milling and cutting processes, a sharp tool cuts and shapes the workpiece by scraping against the surface of the workpiece. Specially manufactured tools made of hardened metals are used for the process, which enables them to cut deeply into a workpiece. Although the tools are well designed and manufactured, over time they endure wear and have to be replaced.
One of the positive aspects of sinker EDM is the electrode, which is the tool used to burn away the surface of the workpiece to achieve the desired shape. Unlike sharp cutting tools that dig into a workpiece, the electrode for sinker EDM does not make contact with the workpiece but uses an electrical spark that evaporates small particles from the workpiece in order to achieve the desired shape. The electrode, made of graphite or copper, does not endure any form of wear but is electrically charged. Although there is an initial cost in producing the electrode, it continues to function and perform the EDM process until it is replaced.
Since sinker EDM does not cut into the workpiece, it does not stress the workpiece. The use of the EDM process is based on the idea that the workpiece is shaped, formed, and configured without producing residual stress that comes from bending, drawing, rolling and cutting the workpiece.
The sinker EDM process is performed in a dielectric fluid using a tool that does not make contact with the workpiece, a factor that eliminates the likelihood of any stress, which comes from deformation that is not uniform. Sinker EDM electrodes cut and shape metal in controlled and monitored conditions where the cutting tool and workpiece work together to reach the desired shape and design.
The results of the sinker EDM process are parts that remain stable and do not warp or lose their shape during use. This aspect of the process is critical for applications where machined parts are part of an assembly. This is due to the absence of mechanical force being used during machining.
The superior finish of sinker EDM machining is achieved through several cycles of the electrode passing over the workpiece. The first cycle is a rough cut that is done at high speed, which is followed by two to three finishing or skimming passes that produce a mirror finish that cannot be achieved by any other machining method.
The unique nature of sinker EDM finishes is their random texture, which is different from the directionality of conventional removal methods. The key to the exceptional finishes is the multiple passes that can only be done using sinker EDM machining since conventional methods stress the workpiece and leave marks due to tooling.
The finishes from sinker EDM machining produces parts with fine surface finishes, which eliminates the need for additional finishing operations. This aspect of the process is a necessity for certain applications especially when parts are required to pass over each other. Since the electrode does not touch the workpiece, its surface is not marred by cuts or abrasions.
Regardless of the cost of sinker EDM machining, manufacturers depend on the process to produce complex and intricate designs, shapes, and configurations. The slow precision of the sinker EDM machining process is capable of reproducing any computer rendering in the most precise detail. Products and parts are produced with tolerances of 0.0001 in (0.00254 mm), a factor that is not possible with any other form of machining.
Sinker EDM machining is widely used to create blind holes and cavities in irregular shapes using tools shaped like the cavities, which is the reason for sinker EDM being able to manufacture such complex shapes. In addition, holes can be drilled into a workpiece at acute angles to the surface, a capability that is not possible with conventional methods.
The wide use of sinker EDM is for products that require high precision and have complex geometries with intricate details. The process is capable of meeting such specifications with accuracy and efficiency. Using sinker EDM, engineers and designers have more flexibility to create innovative high-performance products.
Since its introduction, sinker EDM technology has provided designers and engineers with a tool that can meet the needs of several industries. It has become exceptionally useful for the aerospace industry due to the necessity of aerospace parts being precision crafted and meticulously shaped. This is also true for the medical industry where errors and flaws in medical devices can be dangerous.
In a case study conducted by a leading aerospace component manufacturer, Sinker EDM was used to produce critical components for jet engines. By using Sinker EDM, the manufacturer was able to produce complex parts with tight tolerances and high precision, which resulted in improved performance and reliability of the final product. Additionally, the use of Sinker EDM allowed the manufacturer to reduce lead times and costs associated with traditional machining methods.
In a case study conducted by a medical implant manufacturer, Sinker EDM was used to produce orthopedic implants made of titanium. The manufacturer was able to produce intricate designs with high precision, which resulted in improved implant fit and patient outcomes. Additionally, the use of Sinker EDM allowed the manufacturer to reduce the time and cost associated with traditional machining methods.
In a case study conducted by an electronics component manufacturer, Sinker EDM was used to produce components for microelectronics. The manufacturer was able to produce small, intricate parts with high precision, which resulted in improved performance and reliability of the final product. Additionally, the use of Sinker EDM allowed the manufacturer to reduce lead times and costs associated with traditional machining methods.
In a case study conducted by a tool and die manufacturer, Sinker EDM was used to produce complex dies for stamping operations. The manufacturer was able to produce intricate designs with high precision, which resulted in improved tool life and reduced maintenance costs. Additionally, the use of Sinker EDM allowed the manufacturer to reduce the time and cost associated with traditional machining methods.
In a case study conducted by an automotive component manufacturer, Sinker EDM was used to produce gears for high-performance applications. The manufacturer was able to produce complex gears with tight tolerances and high precision, which resulted in improved performance and durability of the final product. Additionally, the use of Sinker EDM allowed the manufacturer to reduce lead times and costs associated with traditional machining methods.
Sinker EDM machining is capable of producing high precision parts from conductive materials. Since its introduction, more and more manufacturers have found the value of sinker EDM as a highly accurate manufacturing process that produces a wide assortment of complex parts.
Sinker EDM is widely used in the manufacturing of molds and dies for injection molding and stamping. The process allows for the creation of complex shapes with high precision and repeatability, which is essential for producing high-quality molded and stamped parts. Additionally, Sinker EDM can be used to create molds and dies from hard-to-machine materials, such as titanium and Inconel, which are often required for demanding applications.
Sinker EDM is also used extensively in the aerospace and defense industries for creating critical components for jet engines, missiles, and other applications. The process is ideal for producing complex, high-precision parts with tight tolerances, such as turbine blades, compressor vanes, and fuel nozzles. Additionally, Sinker EDM can be used to produce parts from exotic materials, such as nickel-based alloys, which are commonly used in the aerospace and defense industries.
Sinker EDM is used in medical device manufacturing for creating surgical tools and implants. The process allows for the creation of small, intricate parts with high precision and repeatability, which is essential for producing high-quality medical devices. Additionally, Sinker EDM can be used to create parts from biocompatible materials, such as titanium, which are often required for medical applications.
Sinker EDM is used in the automotive industry for producing gears, crankshafts, and other components. The process allows for the creation of complex, high-precision parts with tight tolerances, which is essential for producing high-performance automotive components. Additionally, Sinker EDM can be used to produce parts from hard-to-machine materials, such as hardened steel and titanium, which are often required for demanding automotive applications.
Sinker EDM is used in the electronics industry for creating components for circuit boards and other applications. The process allows for the creation of small, intricate parts with high precision and repeatability, which is essential for producing high-quality electronic components. Additionally, Sinker EDM can be used to create parts from a wide range of materials, including copper, tungsten, and molybdenum, which are commonly used in the electronics industry.
Sinker EDM is used extensively in tool and die manufacturing. The process allows for the creation of complex shapes with high precision and repeatability, which is essential for producing high-quality tools and dies. Additionally, Sinker EDM can be used to create tools and dies from a wide range of materials, including hardened steel, which is often required for demanding tool and die applications.
Sinker EDM is used in jewelry manufacturing for creating intricate designs and patterns. The process allows for the creation of small, intricate parts with high precision and repeatability, which is essential for producing high-quality jewelry. Additionally, Sinker EDM can be used to create parts from a wide range of materials, including precious metals and gemstones, which are commonly used in jewelry manufacturing.
Sinker EDM is also used in the production of consumer products, such as eyeglass frames, watches, and writing instruments. The process allows for the creation of small, intricate parts with high precision and repeatability, which is essential for producing high-quality consumer products. Additionally, Sinker EDM can be used to create parts from a wide range of materials, including stainless steel, aluminum, and plastic, which are commonly used in consumer product manufacturing.
Aside from its many advantages, sinker EDM has limitations to what it can produce. Additionally, sinker EDM machines are expensive to purchase and maintain. It is a slow process that is unable to produce high volumes of parts. With all its accuracy and precision, the use of sinker EDM has significant drawbacks that require careful consideration when choosing it as a process.
The recast layer forms when molten metal from the cutting process cools and hardens on the surface of the part contaminating the surface. A finished EDM workpiece will have several layers of globules of metal and electrode particles. A second layer, the recast layer, is the layer that has altered the metallurgical structure of the workpiece.
The recast layer creates tensile stress in the part that can lead to cracks. There are several processes that are used to remove the recast layer to ensure the quality of the part.
The low material removal rate is one of the disadvantages of the sinker EDM process, a factor that engineers are working to resolve. The slow sparking to remove particles from a workpiece is time consuming and adds to the expense of the final product. Unlike conventional machining that rapidly removes surface materials, the sparking cycles in sinker EDM take time, making material removal slow. What can happen in minutes with conventional machining can take several minutes and more with sinker EDM machining, which influences turn around times and on time deliveries.
With sinker EDM, the electrode has the shape of the final product and is pressed slowly into the workpiece. This aspect of the process significantly slows the production process since the die cannot touch the workpiece. As the electrode creates sparks along the workpiece, it erodes away particles, a time consuming and highly controlled process.
The selection of materials used for sinker EDM machining are limited to ones that have electrical conductivity, which eliminates plastics, ceramics, and other materials that are not conductive. This aspect of the process restricts the types of products and parts that can be produced. Much of modern manufacturing has shifted its focus to the use of heavy duty plastics for a wide range of applications, which is less expensive and more flexible than sinker EDM machining of heavier materials.
Many of the products that are created using sinker EDM machining are designed for heavy use applications that require precision manufactured components that lighter materials are unable to fulfill and meet. Conductive metals are expensive and require a great deal of time to machine, which are factors that producers evaluate when making the choice of machining processes.
The initial cost of using sinker EDM as a machining method is in regard to the tool or die that is used to produce a part or component. These aspects of the process are partly due to how dies are manufactured, which is the CNC machining of graphite, copper, or tungsten that are produced with exceptional tolerances to meet the precision of the sinker EDM process. For finer surface finishes, roughing and finishing tools are created, which adds to the expense of the process.
Since sinker EDM is used to produce complex and intricate designs, the dies and tooling have to be of the highest precision, a factor that further increases the expense of the process. The conductive metals are heavy duty materials capable of enduring the sinker EDM process and their final use. In the majority of cases, only large machining organizations are capable of meeting the required costs of the sinker EDM process. All of the various factors, tooling, time, and complexity, add to the cost of the manufactured part or component, which makes choosing sinker EDM as a solution for part production a critical decision.
The sinker EDM process is considered to be hazardous due to its toxic emissions, debris, and electrode materials, issues that are related to recycling, reuse, and non-degradable materials. During the erosion process, sinker EDM produces smoke and fumes, the amount of which is determined by the type of dielectric fluid and its viscosity. Synthetic dielectric fluids produce non-specific aliphatic hydrocarbons, aerosols, and benzene.
Sinker EDM is a cutting process that requires a reaction between the workpiece and the electrode. As with all forms of reactions, there are negative impacts that can damage the environment and harm workers. The sinker EDM process produces significant amounts of toxic materials that can cause damage and harm, a factor that further influences choosing it as a manufacturing method.
Aside from the gases that are produced by sinker EDM, volatile particles are released from the workpiece into the air that cool to form dangerous carcinogenic substances. To protect workers, there is a required depth at which a workpiece is to be submerged in the dielectric fluid to prevent particles from being released into the atmosphere. In addition, to keep work areas safe and clean, filters and special ventilation systems are necessary to collect the dangerous particles and isolate work areas.
Aside from the precision, accuracy, and positive aspects of sinker EDM, there are negative factors that have to be carefully monitored and considered. Sinker EDM manufacturers work diligently to ensure that their use of the sinker EDM process is safe for the environment and their employees.
EDM machining is a contemporary machining method based on the removal of material from a part using thermal energy. The material is removed by local melting or vaporizing small areas on the surface of the part being machined...
A method of precision machining called electrical discharge machining (EDM) removes material from a workpiece using thermal energy rather than mechanical force. A thin, single-strand metal wire and deionized water used to...
The normal functioning of CNC machines is done along the three Z, X, and Y axes. The five axes machines have two more axes accessible, which are namely A and B. The addition of the two extra axes makes it easy to cut complex and intricate parts...
CNC machining is an electromechanical process that manipulates tools around three to five axes, with high precision and accuracy, cutting away excess material to produce parts and components. The initial designs to be machined by CNC machining are created in CAD...
The CNC process was developed in the 1950‘s and took a leap forward in the 1980‘s with the addition of computerization. Unlike other production processes, CNC begins with a rendering by a computer, which creates a two or three dimensional representation of the part to be produced...
G-code is the name of a plain text language that is used to guide and direct CNC machines. For most modern CNC machines, it isn‘t necessary to know the meaning of G-codes since CAD and CAM software is translated into G or M codes to instruct a CNC machine on how to complete a process...
Computer numerical control (CNC) is a fundamental part of modern manufacturing. The majority of machines operate using instructions and guidelines that have been downloaded using a CNC program controller...
Water jet cutting is a manufacturing process that uses high pressure jets of water provided by pressurizing pumps that deliver a supersonic stream of water to cut and shape various types of materials. The water in water jet cutting is...
Machining is a manufacturing process used to produce products, parts, and designs by removing layers from a workpiece. There are several types of machining that include the use of a power driven set of machining tools to chip, cut, and grind to alter a workpiece to meet specific requirements...
The CNC process, computer numerical control, is a method of manufacturing where programmed software directs the operation of factory tools and machinery. It is designed to manage a wide range of complex machines from grinders and lathes to mills and routers...