Boiler Rentals
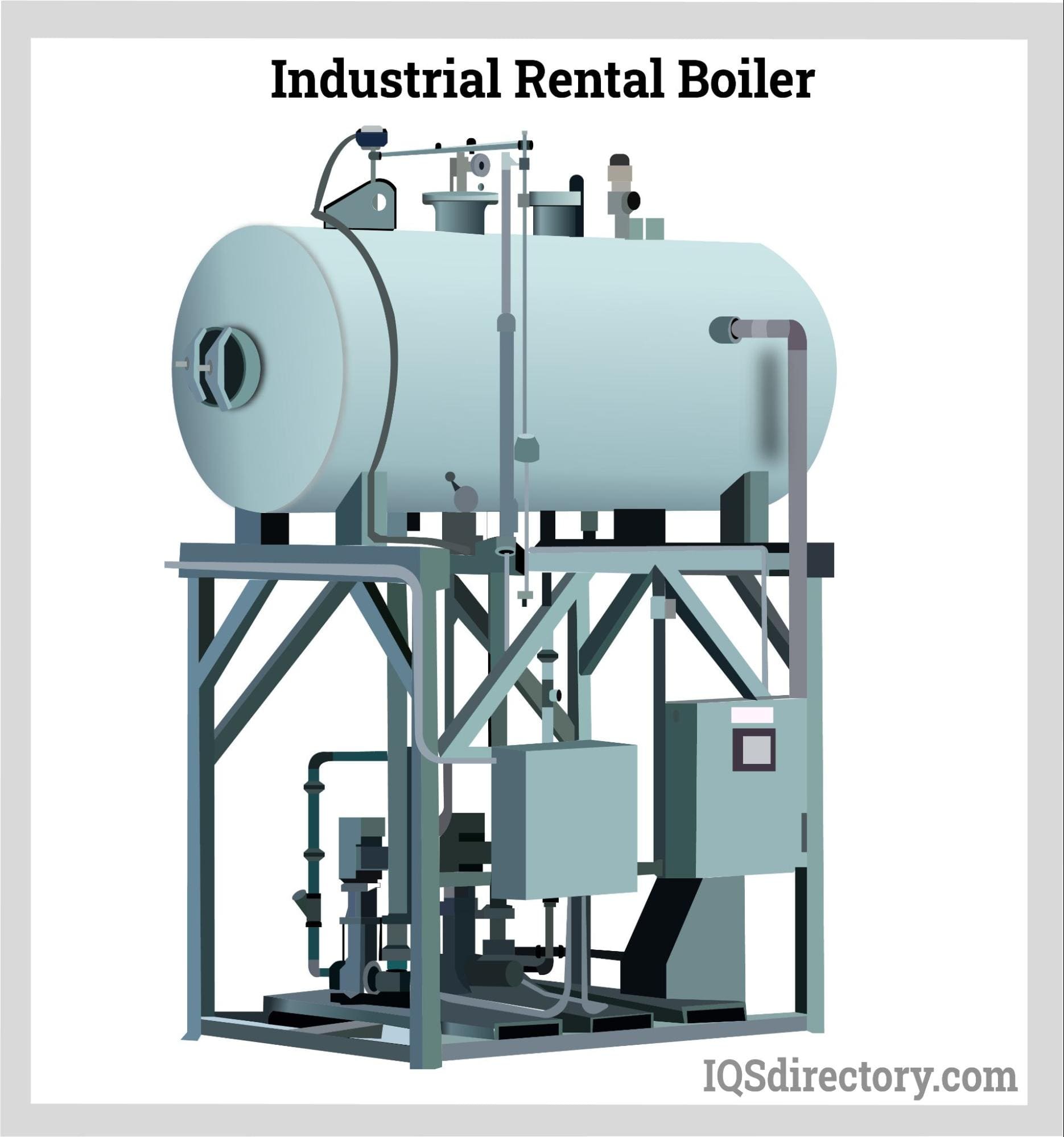
Boiler rental is a service that is offered by boiler manufacturers to assist customers in times of emergency, high usage, or as a cost effective permanent solution. Every type and size of boiler is available for rental from ones...
Please fill out the following form to submit a Request for Quote to any of the following companies listed on
This article contains everything you will need to know about water tube boilers and their use.
You will learn:
A water tube boiler features a network of tubes through which water flows and is heated by hot gases from a furnace or combustion chamber situated beneath the tubes. The fuel burned in the furnace generates gases that heat the metal tubes, which in turn heat the water. This heated water then rises to a steam drum, where saturated steam is expelled.
The fuel for a water tube boiler is natural gas, propane, coal, diesel fuel, or heating oil, which is burned in the combustion chamber or furnace to create hot gas to heat up the tubes and water. Old, conventional style boilers completed the process in reverse where the water was heated by a furnace using coal or wood. As the temperature of the water rose, it heated tubes that were immersed in it. The heating of the high volume of water made the boiler process time consuming and is the reason for the development of the water tube design where water is in the tubes
Traditional water boilers, which heated both the water and the pipes, occupied significant space and were quite cumbersome. To ensure these boilers were ready for heating or industrial use, designated staff had to start them up early each morning before the rest of the workers arrived.
The drawbacks of the previous design prompted engineers to explore the use of robust materials for tubes that would hold water and be heated to produce steam. This research resulted in the creation of the water tube boiler, which offers enhanced efficiency, higher steam output, and reduced fuel consumption. Furthermore, water tube boilers are safer, simpler to operate, and occupy less space.
In the early days of boiler use, numerous catastrophic failures occurred due to pressure part malfunctions in the steam section of boilers. The materials used in the construction of early boilers were inadequate to withstand the power they generated. Initially, municipal boilers were smaller and multiple units were needed to meet community demands. To address this issue, larger boilers capable of producing higher steam pressure were developed. However, the materials used in these larger boilers were still insufficient to handle the increased pressure.
Boilers are engineered to produce steam by heating water with a burner, leveraging water's remarkable heat transfer properties. In a traditional fire tube boiler, the tubes are submerged in a water-filled tank. A furnace heats the tube walls, which in turn heat the water, converting it into hot water and eventually steam. Despite water's excellent heat transfer capabilities, conventional boilers consume a significant amount of energy due to the lengthy process of heating the tubes through water's heat transfer.
Conventional boilers for industrial use require substantial space, often necessitating a dedicated boiler room due to their size. This spatial requirement restricts their application primarily to large industrial and manufacturing facilities.
Water tube boilers have gained popularity because of their efficient design, compact size, and low energy consumption. In this design, water is encased by hot gases from the combustion chamber or firebox. As these gases pass through the boiler, they heat the water in the tubes, generating steam that can be used for electricity, heating, and other power needs.
A water tube boiler consists of four main components: the water drum (or mud drum), the upper steam drum, water tubes, the furnace, and either a superheater or an economizer. The water tubes link the two drums, allowing water to circulate between them by convection. As the cooler water descends through the downcomer tube, the heated water rises to the top of the boiler.
The steam drum is responsible for collecting both steam and water, where they are then separated. This component is a large, elongated cylinder constructed from flat metal plates and situated at the top of the boiler. Water from the economizer enters the steam drum, where a scrubber or demister separates the steam from the water. The steam is then released from the steam drum to power various applications, while the separated water is recirculated back into the boiler via downcomers to be converted into steam again.
Cooler, denser water flows from the steam drum through large pipes called downcomers to the mud drums, or water distribution manifolds, located at the base of the boiler. This water movement can occur through natural circulation or be assisted by a multistage centrifugal pump. Typically, water tube boiler steam drums are equipped with at least six downcomers to ensure adequate water flow.
Located at the base of the boiler, mud drums collect sediment and impurities. Because of the substantial accumulation of material in the mud drum, regular cleaning is necessary to remove these deposits.
There are three primary types of steam drums: single steam drum, bi-steam drum, and multiple steam drums. The bi-steam drum design is employed for both power generation and steam production. Single steam drum boilers, commonly used in power plants, are capable of operating at higher pressures compared to the other steam drum types.
The economizer, also known as a flue gas heat recovery unit, is mounted on the stack of a water tube boiler. Its purpose is to capture and transfer heat to the boiler feed water, preheating it before it enters the boiler. This energy-saving device helps lower fuel consumption by reducing the amount of fuel required to heat the water in the boiler.
There are two main types of economizers: condensing and non-condensing. Condensing economizers are the most efficient of the two, but they require flue gases to be cooled below their condensation temperature, which can be challenging for boilers that use fuel oil. By cooling the flue gases to below this temperature, a condensing economizer allows water vapor in the gases to condense, thereby releasing latent heat that is transferred to the feed water.
Shell and tube economizers are the most widely used type, consisting of a shell with a series of internal tubes. In this design, flue gases pass through the shell while boiler water circulates through the tubes. Heat from the flue gases is transferred to the feed water through the tube walls.
Plate economizers feature a series of plates arranged in either a parallel or staggered configuration. Flue gases pass through channels between the plates, while feed water flows between the plates. The heat from the flue gases is transferred to the feed water through the plate surfaces.
The mud drum is positioned at the base of a water tube boiler and linked to the steam drum via tubes. It holds water and gathers impurities that settle at the bottom. These impurities are eliminated through a process called blowdown, which involves removing small quantities of water from the boiler to decrease impurity concentration.
Chemicals are introduced into the feed water for the steam drum and mud drum to prevent fouling and corrosion. The feed water enters the boiler from the economizer and flows into both the steam drum and the mud drum. As the water travels through the downcomers, it absorbs heat from the firebox and is delivered to the mud drum. Riser tubes then transport water or steam from the mud drum to the steam drum, maintaining continuous circulation of water and steam throughout the system.
Water tube boiler burners feature a short flame and a wide diameter. There are different types of burners, including single and multiple flame versions. A single flame burner can handle two types of liquid gas fuels, while a multiple flame burner is designed for just one type. These burners are equipped with a central ventilation system and a wind box to efficiently distribute combustion air.
The performance of a water tube burner is influenced by several key factors: the levels of oxygen and nitrogen concentration, the temperature of the combustion reaction, and the duration that nitrogen oxides (NOx) remain in the combustion environment. Nitrogen oxides, which include various forms of NOx, tend to form in higher quantities at temperatures exceeding 2800°F (1540°C). As these factors increase, so does the concentration of NOx emissions, necessitating measures to reduce one or more of these factors. The design of water tube boiler burners aims to mitigate the impact of these factors and minimize the formation of NOx.
Optimal performance of a water tube boiler burner hinges on achieving complete combustion and proper oxidation of the fuel, which relies on maintaining the correct fuel-to-air ratio. Adjusting this ratio and creating fuel-rich zones at the front of the flame helps minimize the conversion of nitrogen to NOx, thereby reducing its formation. The stoichiometric ratios are 10:1 for natural gas, 12:1 for oils, and 24:1 for liquefied petroleum gas (LPG).
In power plants, large water tube boilers are equipped with multiple burners, often numbering 20 or more, to generate sufficient energy to heat the tubes. The furnace or radiant section of the boiler is designed to accommodate the flames from these burners and absorb the heat they produce.
Burners are categorized based on their operating mechanism and the type of fuel they use. The primary types of burners include diesel, gas, and biomass burners. Diesel burners can utilize different forms of diesel fuel, such as fuel oil, kerosene, vegetable oil, and biodiesel. These fuels need to be pressurized prior to combustion in diesel burners.
Gas burners operate using fuels such as propane, butane, natural gas, hydrogen, and lighting gas. Unlike diesel fuels, gas fuels ignite more easily and do not require pressurization before combustion.
Biomass or pellet burners are eco-friendly burners and are used for heating and the production of hot water. The term biomass refers to the natural elements used to create boiler combustion, flames, and heat. Biomass includes pressed sawdust, bioethanol, forest waste, fruit peels, and pits. The unique nature of biomass fuels requires that it be stored in a tank close to the boiler.
The burner’s flame ignites within the furnace or radiant section of the boiler, generating radiant heat. This hot gas heats the water in the steam-generating tubes. The furnace walls consist of water-filled tubes or risers, which are heated through radiation or convection. The water in these risers is supplied from the mud drum at the base of the boiler. As the risers are positioned along the four walls of the furnace, this arrangement is known as a water wall.
The risers feature extensive contact areas designed to absorb heat efficiently. As they are exposed to the radiant heat within the furnace, the risers act as the evaporator section of the boiler, where the water inside them turns into steam.
Tubes in a water tube boiler play a crucial role in steam generation. Positioned within the furnace walls, these tubes hold the water that is heated to produce steam. Typically, water tube boiler tubes are seamless and constructed from carbon or alloy steel, suitable for medium to high-pressure applications. Common materials for these tubes include low-alloy steels with elements like chromium, nickel, molybdenum, and vanadium, as well as 9% to 12% chromium steels, austenitic stainless steels, austenitic heat-resisting steels, and nickel-base heat-resisting alloys.
Boilers are categorized based on their maximum operating temperature and pressure. The materials used for tubes in water tube boilers must meet several requirements, including resistance to oxidation and corrosion, fatigue strength, and resistance to creep and rupture. Among these factors, the thermal conductivity of the tube metals is particularly important, as it significantly impacts the performance of the water tube boiler.
The riser tubes within the furnace walls absorb heat from the furnace. In certain boilers, refractory cells are utilized, which consist of tubes equipped with welded studs and coated with refractory material to endure the intense heat. Most water tube boilers feature tubes joined together by fins or strips. These tubes are directly exposed to the furnace heat to facilitate steam generation.
The windbox plays a crucial role in the combustion process occurring around the burner. It encircles the burner and is equipped with fans that introduce air into the chamber. A damper on the burner controls and directs the airflow, as well as reduces noise. Airflow is monitored using instruments such as a pitot tube, airfoil, or flow restriction methods located in the duct system leading to the windbox.
Windboxes may also be positioned behind the water wall to supply additional air, helping to minimize air pulsation and ensure consistency. In coal-fired water tube boilers, there are primary and secondary air systems. The primary air system regulates the combustion of the fuel, while the secondary air system enhances combustion efficiency and supplies air to the windboxes.
Water tube boilers are categorized based on the type of fuel they use, which affects their operating costs. Over time, certain fuels have been phased out due to their environmental impact, a concern that has gained significant attention in the 21st century. The pursuit of environmentally friendly fuels has led to the creation of a variety of specially designed fuels in different forms.
Water tube boiler fuels are classified into four categories: solid, liquid, gas, and agricultural biomass. Fuel cost is a major expense in the operation of a water tube boiler. The most effective fuels release heat energy efficiently, providing the necessary heat for the tubes and risers.
Coal is the most widely used boiler fuel and has been utilized for centuries. It can be burned in its natural lump form or crushed to improve combustion efficiency. Although coal is being gradually phased out due to environmental concerns, it remains in use at large power plants. This brown or black combustible sedimentary rock varies depending on its mining location. Coal consists of carbon, hydrogen, nitrogen, and oxygen, with impurities such as ash, mercury, and sulfur.
Natural gas primarily consists of methane, along with varying amounts of ethane, propane, butane, and inert substances like nitrogen, carbon dioxide, and helium. It is the most commonly used fuel due to its low cost. Natural gas burns cleaner than oil, is readily available, and generates minimal greenhouse gas emissions, making it a more efficient option.
Liquid propane is similar to natural gas in that it is easy to use, economical, and is delivered for use in pressurized containers. As with natural gas, propane is cleaner than oil and costs less. It produces significantly fewer emissions than carbon energy sources and can be used in natural gas boilers. Propane is not recommended for industrial size boilers since it is not a sustainable source of fuel.
An oil fueled boiler functions like a gas boiler where the oil is ignited in the burner to produce the heat to warm the risers. Oil is more efficient than gas because all of the heat from the burning fuel is used with little waste. Unlike a gas boiler that receives its fuel from the main, oil fueled boilers have to have their fuel stored in tanks. Oil fueled boilers are not as environmentally friendly as other types of boilers but make better use of their fuel.
In oil-fired boilers, steam atomization is employed to blend the oil with air for more efficient combustion. This process involves injecting steam to break the oil into a fine mist, which then mixes with the air for easier ignition. As with most water tube boilers, the resulting flame is short and highly intense.
Oil-fired boilers utilize flue gas recirculation (FGR), a method that reintroduces flue gases from the combustion process back into the burner. This technique helps reduce NOx emissions and involves an air fan on the burner that directs flue gases into the air inlet mixing port. While FGR offers benefits such as improved fuel utilization and reduced toxic emissions, it can affect the boiler's overall efficiency.
The solid fuel category encompasses a variety of materials, including those explored for eco-friendly alternatives. This category traditionally includes coal and wood, which were among the first fuels used in boilers. Other solid fuels in this category include bagasse (pulp residue), municipal waste, refuse-derived fuel, tires, agricultural by-products, and various types of solid waste. Depending on the design of the water tube boiler, the steam capacity using solid fuels can range from 25,000 PPH to 500,000 PPH.
Biomass fuel systems use wood pellets or chips as a renewable energy source, generating steam through the combustion of organic materials. Although burning biomass does release carbon dioxide, the emissions are significantly lower compared to fossil fuels. Boilers designed for biomass fuel are generally larger than those for fossil fuels, as they require a bigger furnace to accommodate the increased volume of fuel and produce adequate heat.
A key component of biomass boilers is the feed hopper, designed to hold substantial amounts of biomass, which is then automatically supplied to the furnace. The use of biomass boilers has surged recently, particularly in sectors such as food and beverage, dairy, and meat processing. Wood pellets are commonly favored due to their ease of storage and handling in large quantities.
ASTM has set technical standards for fuel oil grades and given them six classifications or grades. Grade No. 1 is for domestic and small industrial burners while Grades No. 2 to Grade No. 6 are used in atomizing burners, commercial and industrial boilers, and burners with increased viscosity and boiling range.
aFuel Oil Grades | |||
---|---|---|---|
Grades | API Gravity | Density lb/gal | Heating Value Btu/gal |
1 | 38 to 45 | 6.950 to 6.675 | 137,000 to 132,900 |
2 | 30 to 38 | 7.296 to 6.960 | 141,800 to 137,000 |
4 | 20 to 28 | 7.787 to 7.396 | 148,000 to 143,100 |
5L | 17 to 22 | 7.940 to 7.686 | 150,000 to 149,400 |
5H | 14 to 18 | 8.080 to 7.890 | 152,000 to 149,400 |
6 | 8 to 15 | 8.448 to 8.053 | 155,900 to 151,300 |
Choosing the correct air-to-fuel ratio is crucial for optimizing boiler performance and preventing potential damage, regardless of the fuel type used. This ratio determines the appropriate amount of air needed to combust a specific type of fuel. Common fuels used in boilers include oil grades #2, #4, and #6, diesel, gasoline, natural gas, propane, coal, and wood. Maintaining a balanced air-to-fuel ratio is essential to avoid energy losses from excessive air or inefficient combustion, thus enhancing overall efficiency and performance.
Water tube boilers come in various types, including single pass vertical and bent tube designs. They are favored in industrial and utility settings due to their capability to handle design pressures up to 2000 psig, temperatures reaching 1000°F (537.78°C), and capacities of up to 500,000 pounds per hour (PPH).
Water tube boilers come in several types, including A Type, D Type, and O Type, named according to their shape. Other types include simple vertical, Stirling, and Babcock and Wilcox. Stirling boilers were developed during the first industrial revolution and later acquired by Babcock and Wilcox in 1906. Today, Babcock and Wilcox continues to build modern, technologically advanced boilers.
An A-type water tube boiler features two water drums connected by a shared header. In this design, evaporated water is transported upwards through risers into the steam drum and steam header. A-type boilers are known for their water-cooled furnace and vertical gas outlet, which reduce the boiler's footprint and allow for high steam capacity in a compact size. The triangular arrangement of the two water drums and the steam drum gives the A-type water tube boiler its name.
In an A-type water tube boiler, water fills the space between the drums, with the furnace positioned at the center. These boilers can be fired by coal or oil and feature multiple fire doors for stoking. Originally designed for battleships, A-type water tube boilers were created to deliver high power within a compact footprint.
D-type water tube boilers feature a large steam drum positioned at the top, connected to a mud drum at the bottom. Steam is generated in the tubes or risers and rises to the steam drum. The furnace includes water-filled tubes along its four walls, known as water walls. This design facilitates excellent water circulation, enabling rapid steam production and generation.
D-type water tube boilers are capable of generating steam at up to 1,000,000 PPH with pressures reaching 2000 psig. They are built for durability, endurance, and longevity, making them ideal for applications that require high-pressure superheated steam while maintaining a compact footprint.
In an O-type water tube boiler, the steam and mud drums are vertically aligned, one positioned above the other. They are connected by curved water pipes that form the shape of the letter "O." These boilers are fired by liquid burners, and the combustion chamber is situated between the curved convection tubes and the water wall tubes.
Similar to D type water tube boilers, O type water tube boilers are well-suited for conditions with limited space. Access to the O type boiler is available at both ends. These boilers are known for their durability and long service life. O type water tube boilers can achieve an output of up to 250,000 PPH with pressures reaching 900 psig.
Vertical water tube boilers differ from other types in that they are oriented vertically rather than horizontally. Historically, they were used to power vehicles such as early steam locomotives. In these boilers, water is heated within the cylindrical shell.
Fuel is placed onto the grate within the furnace of the vertical water tube boiler to generate hot gases that heat the vertical tubes. Ash residue from the fuel falls through the grate into an ash pit. The steam produced in the tubes is collected until it reaches a desired level and is then released to power machinery.
The firebox is tapered toward the top to facilitate the passage of steam to the top of the cylinder. The cross tubes are inclined to enhance their heat exposure and improve water circulation. An uptake tube extends from the top of the firebox to the boiler's chimney.
The Stirling boiler, a high-capacity bent tube boiler introduced in 1888 by Alan Stirling, can produce up to 50,000 kg/hr with pressures reaching 60 kgf per cubic meter. It is designed primarily for central power stations. This boiler features three steam drums positioned at the top and two mud drums located at the bottom. The steam and mud drums are interconnected by a network of bent tubes that are resistant to expansion under heat.
In keeping with 19th-century practices, the drum structure is encased in brickwork with a fire door at the base. A circulating tube links the steam drums, extending from the central drum, which gathers the steam. Positioned beneath the mud drums, the furnace heats the water contained in the mud drums. Steam from the steam drums is then converted into superheated or dry steam by a superheater.
The Stirling boiler is one example among many types of water tube boilers. As technology evolves, new designs and configurations are continually refined. However, all water tube boilers share the core principles of utilizing a fuel source, water, and tubes to produce steam.
Water tube boilers are widely utilized because they can manage both high pressure and temperature conditions effectively. Their exceptional efficiency in transforming fuel into valuable energy contributes to their broad application across various sectors. These boilers are favored for their dependable and secure operation.
Boilers primarily serve the purpose of generating power, which was why they were vital during the early days of the industrial revolution. The dependable performance of water tube boilers has solidified their role in power plants, where they generate steam to drive turbines and produce electricity.
The chemical and petrochemical sectors demand reliable power, flexibility to handle varying loads, and adherence to emission standards. Water tube boilers are capable of fulfilling these requirements due to their high efficiency and dependable operation. They are employed to generate steam for processes such as refining, distillation, and cracking.
Water tube boilers play a critical role in the pulp and paper industry by providing the necessary steam for drying paper, meeting energy needs, and cooking wood chips during the initial manufacturing phase in the digester. The steam generated ensures consistent heating, precise temperature control, and optimal efficiency throughout the process.
In the food and beverage industry, water tube boilers are essential for preparing food products consistently and efficiently. They produce large quantities of steam and hot water, which are crucial for mass production processes. The primary advantage of using water tube boilers is their capability to generate high volumes of steam and hot water, ensuring that food products are smooth, tender, and easily digestible. Additionally, these boilers contribute to maintaining the optimal environmental conditions within food processing facilities.
In the pharmaceutical sector, water tube boilers are subject to stringent demands, requiring precise temperature control for tasks such as drying, sterilizing, and purifying chemicals and equipment. A critical concern for all types of boilers in this industry is the generation of clean steam. Water tube boilers, with their advanced filtration systems, are particularly well-suited to provide the high-quality steam needed for pharmaceutical applications, ensuring both purity and efficiency in the production process.
In the textile industry, the primary requirement for water tube boilers is the ability to deliver rapid steam at temperatures of 265°F (129.4°C) for dyeing and finishing operations. Due to the variable demand in textile production, relying on fire tube boilers can be inefficient and expensive. Water tube boilers play a crucial role in the early stages of textile manufacturing, supplying the necessary energy for fabric pretreatment and facilitating precise heat control for printing processes.
For decades, water tube boilers have been a reliable choice for heating residential, industrial, and commercial spaces. Their widespread use in heating systems is due to their dependable performance and accurate temperature control. The even distribution of radiant heat from a water tube boiler ensures that buildings and work environments remain comfortably warm and conducive to productivity.
A flexible tube boiler, often referred to as a flex boiler, features a network of compact, curved tubes rather than the traditional long, straight tubes. Water flows through these smaller tubes and is heated by combustion gases. Because the tubes are smaller and more numerous, the flex boiler heats water more quickly. The design allows for greater surface area exposure to the hot gases, facilitating a faster conversion of water into steam.
The flexible tube boiler design offers several notable benefits. One of its key features is the arrangement where the fire is positioned outside the tubes while the water circulates inside. This design results in a low water volume and quick heating capabilities, allowing the boiler to reach 100 psi within ten minutes. The rapid heating reduces fuel consumption. Despite the bends in the tubing, the flexible tube boiler is resistant to thermal shock, as the tubing's flexibility helps mitigate the risk of damage from temperature fluctuations.
Flexible tube boilers are designed to reduce thermal stress while providing a rapid response in a compact and robust unit. Many models can achieve pressures of up to 500 psig or higher and maintain an efficiency rating of 90%. Their performance and reliability make them a preferred choice for institutions such as universities, hospitals, office buildings, and manufacturing facilities.
Water tube boilers are highly favored for their efficiency, as they experience minimal heat loss due to the direct interaction between water-filled tubes and combustion gases. This design allows them to quickly transform substantial amounts of fuel into valuable energy.
Boiler rental is a service that is offered by boiler manufacturers to assist customers in times of emergency, high usage, or as a cost effective permanent solution. Every type and size of boiler is available for rental from ones...
A high pressure boiler is a shell and tube heat exchanger that use boiled water to create steam or high pressure hot water. Using water filled tubes in a metal tank or enclosure, they create power by converting water into steam through thermal energy, which is used...
A steam boiler is a steam producing heating system. It creates energy by heating water to get steam. It is a heat exchanger that makes steam for outside usage and has a combustion chamber and water container. The several varieties of steam boilers include...
A conveyor oven is a continuous flow oven; it‘s an oven that is open on opposing sides and has a conveying system running from one end of the oven to the other. Designed like a batch oven, conveyor ovens have the additional benefit of keeping products moving while providing continuous and uniform heat...
A furnace is a direct fired device used to provide heat for industrial processes that require heat in excess of 400° C (752° F). Any industrial application that relies on heat to create a reaction or heat materials for production uses an industrial furnace...
A curing oven is thermal processing equipment used by thermal specialists to improve or enhance the strength and durability of materials. Many factory processes such as baking, drying, heating, cooking, and curing require...
An industrial oven is a device used to create extremely high temperatures to heat treat parts, condition metals, and cure metal coatings. Common functions for industrial ovens include drying, curing, testing, and coating of parts and products...
An infrared oven is an oven that heats objects or cooks food using infrared radiation instead of conventional conduction or convection heating. People can use infrared ovens in commercial kitchens, homes, or...
A normal function of an industrial furnace is to heat treat metals for annealing, tempering, or carburizing and pre-treat materials for forging. Though metal is a common material to be treated using an industrial furnace, other materials are also...
Industrial ovens are thermal processing machines used as heating chambers for drying, curing, and baking of foods, parts, and components. The main industries that use industrial ovens are chemical and food processing and electronics manufacturing...