Door Latches
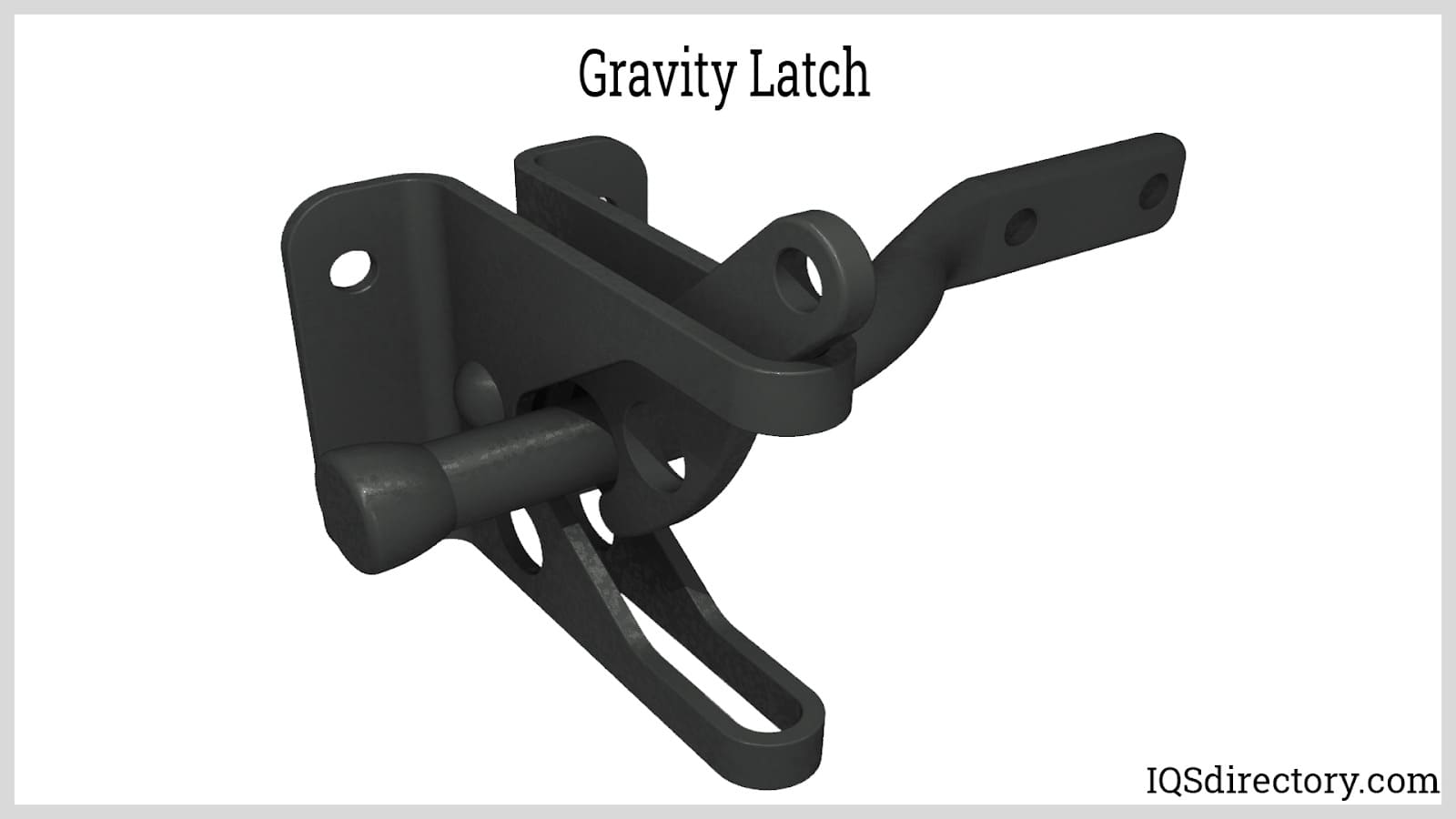
A door latch is a mechanical fastener that connects two surfaces or objects and provides a secure, safe, and strong connection. The latch portion of the mechanism is mounted on a flat surface such that when it meets a...
Please fill out the following form to submit a Request for Quote to any of the following companies listed on
This article will give an in-depth discussion about Gas Springs.
The article will bring more understanding about:
A gas spring is a hydro-pneumatic element that stores potential energy by compressing gas contained inside an enclosed cylinder sealed by a sliding piston.
A gas spring does not rely on elastic deformation. It is a closed system that does not require the introduction of any further gas to operate once charged with inert nitrogen gas and manufactured.
No matter where the gas spring is positioned, the pressure on all sides of the piston remains equal due to the size of the cross section of the rod that is small. The force (F) of a gas spring is equal to the pressure differential (P) between the internal environment pressure and the external environment pressure, acting on the cross-section area of the rod (A). The pressure differential ΔP must be taken in consideration for gas springs used in high pressure environments.
Gas springs can be understood in the following contexts:
It is the maximum magnitude of the distance traveled by the rod from closed length to extended length.
This is the magnitude of the total gas spring length that is measured from the center of one end fit to the center of the next end fit.
This is the total closed length that is measured from the center of one end fit to the center of the next end fit. During the times when there are no specified end fits, this measurement will refer to the length from rod end to the tube end.
This is the section of the tube that is grooved. The function of this feature is to retain the guide and seal the package and prevent the damaging of the seal package by the piston during extension.
Depending on the industry and application, gas springs can be referred to as gas props, gas struts or gas lifts. Gas springs or gas struts are typically used in supporting or counterbalancing dynamic masses. The term nitrogen gas springs is sometimes used to refer to gas springs because Nitrogen is the gas typically used inside the gas springs. Nitrogen is the preferred choice because it is inert and non flammable. Therefore, it would not react with the internal components.
Gas struts are typically used in vehicle suspension. They have a coil spring to support the vehicle’s weight and a shock absorber to absorb as well as dampen vibrations and shocks. A push or pull force is provided through the pressure that is applied to the spring. The gas strut supports the vehicle, absorbs the impact generated from surface inconsistencies, and aids in the wheel turning.
Gas springs that are damped are also referred to as gas dampers or gas shocks. This depends on the industry and application. The gas shocks support the dynamic masses while simultaneously controlling the motion of the system.
Dampers or ‘shocks’ use viscous friction to restrict motion. They usually work in conjunction with an external spring or in other cases moving masseslike panels and doors. A force that opposes the motion is generated by the dampers and the force is directly proportional to the moving mass’ velocity.
The basic difference between gas springs and coil springs is how they compress. A coil spring uses physical deformation to store energy while gas springs use pressurized gas. Some of the benefits of coil springs is their low cost, ability to be tuned, faster kick back time, and the elimination of any concerns regarding leaks or broken seals while gas springs have a smooth and silent operation and rely on internal pressure.
With gas springs, force increases exponentially as they are compressed with less force being necessary to compress them, initially. As a gas spring approaches the end of its stroke, the amount of compression force that is required increases. In operations where several springs are necessary, gas springs are used over coil springs because it takes fewer gas springs to do the same job as multiple coil springs. Since coil springs are physical mechanical devices, they do not operate smoothly and produce a certain amount of noise.
Gas springs possess greater force and require a much shorter stroke than coil springs, which is the reason that it requires fewer of them to perform a task. They are highly reliable, have excellent performance, and are very safe. In essence, gas springs provide lifting force at reduced speed.
The gas spring’s working principle is based on the use of nitrogen gas as an elastic medium together with oil such as transformer oil and turbine oil 50% each, for the sealing, lubrication, and transmission of pressure. During the compression stroke, the piston rod is introduced into the cylinder. This decreases the internal gas volume resulting in a proportional increase in pressure. This is a principle based on Boyle’s law. Consequently, when the rod is compressed, the force of a gas spring is at its maximum.
From the diagram above, when the piston is moved from the fully extended position P1 to the full compressed position P2, the pressure (represented by the solid line) rises, and the volume (represented by the dashed line) reduces.
The K-factor or gas spring progression, which is the difference between the two forces seen at the extreme rod positions labeled P1 and P2 respectively, is an important characteristic. Gas springs can achieve very low K-factors with a typical range of 1.05 to 1.8 as compared to mechanical springs. Gas springs are pressurized at the required force at P1, which is available immediately. Because of this reason, always take into account the P1 force when calculating the gas spring force at any given position: where F represents the gas spring force, k represents the spring constant in N/mm (change in force per unit compression), and X represents the deflection distance in mm.
On top of providing lubrication for the piston, seals and piston rod, oil in a gas spring also serves to control the velocity of the spring when the extension stroke ends. The oil serves to slow down the spring and prevents shock loading at the full extension reaching. This damping control helps to prevent rapid control extension that may result in the failure of the product, damage, or injury. By regulating the gas flow and oil through the piston, damping is achieved. Maximum damping is achieved when at the point where the piston reaches the internal column of oil near the full extension point, when mounted in the rod down position, which is the most preferred.
Factors affecting damping:
There are two ways in which the operating temperature affects damping. An increase in temperature results in an increase in the force within the spring, and the viscosity of the oil reduces. Consequently, the spring’s extension will speed up and less damping is achieved. At low temperatures, the opposite occurs, with the reduction in the extension force and increase in the viscosity of the oil; thus, the extension of the spring is at a lower rate, and high damping is achieved.
By definition, viscosity is the resistance to flow and shear of a fluid. Oil has a high viscosity, so an increase in temperature will decrease the viscosity of the fluid. This means that there will be an increase in the rate at which the fluid flows and a decrease in the fluid’s resistance to the objects passing through it (such as the piston of the gas spring). The higher the viscosity of the fluid, the greater the damping on the gas spring.
A high volume of the oil contained in the gas spring will cause the gas spring to hit the oil damping zone quickly and the extension speed will be lowered.
The temperature at which the liquid becomes semi-solid and loses its flow characteristics is the one that is referred to as the pour point. For a gas spring, when the pour point is reached, the oil effectively turns into a solid. As a consequence, the full stroke of the gas spring cannot be fully achieved, and damping will not occur.
The rate of extension and or compression is controlled by metering. This is achieved by altering piston orifice sizes to create restrictive flow paths through the piston. No matter which method is utilized, the purpose is to create a pressure drop across the piston to control the extension rate. A large piston orifice or a shorter flow path results in reduced pressure drop, reduced restriction of the flow path and increased speed of spring extension.
Another factor that affects spring performance is called the breakaway friction. This is experienced when a gas spring has been allowed to remain stationary for a period of time like a couple of hours. The lubrication flows away from the seals and the rubber is forced into the minute cracks and crevices that are within the metal, because of the pressure contained in the cylinder of the gas spring. When using the spring for the first time, it requires much force to overcome static friction. The rubber is also freed from the cracks and crevices.
A gas spring must not be used under any of the conditions listed below as that could result in an explosion of the spring or other malfunction that may cause a major accident or product trouble.
A gas spring consists of several parts, each being integral for the safe and successful operation of the component. The diagram below illustrates these components.
A rod comes in three forms: polished carbon, precision-ground, or stainless steel. The surface is given a treatment so as to improve wear and corrosion resistance. The length of the rod is always longer than the spring stroke though it will be less than the tube length.
There are a number of ways of treating carbon steel, which are salt bath, chrome plating, and nitriding. Chrome plated rods have chemical compliance issues because of their chromium content. Black nitrided rods are smoother and just as corrosion resistant as chromium rods.
Nitrotec surface layer treatment is a special rod treatment and has a number of advantages over the other methods that include:
A gas spring tube is made up of carbon, a powder-coated or stainless steel tube which can withstand high pressures. The gas spring’s longevity and burst pressure performance are affected by critical factors such as internal surface finish and tensile strength of the tube.
They are made out of plastic composite; the guide and seal package serve to provide a bearing surface for the rod and prohibits the escape of gas and ingress of contamination. Zinc, brass, or other materials in which a suitable bearing sleeve is incorporated, can also be used to manufacture guides used in gas springs. The standard used for seals is rubber.
The piston assembly is made out of zinc, aluminum, or plastic. The integrity of the piston to rod connection is critical, for factors involving safety and preventing the rod from being expelled from the spring. The rate of extension and compression of the gas spring is controlled by the piston assembly.
The sealing of the tube end of the gas spring is done by the end plug and it also attaches to the tube end fitting.
Nitrogen is used in gas springs because it is inert and non-flammable. It does not react with any of the components of the interior.
The types of gas springs are detailed below:
This type of gas spring features a rod that is attached to a piston within a sealed cylinder. The cylinder is filled with high pressure nitrogen which generates extended forces. These types of gas springs are reliable and have a compact structure, making them more useful in many lifting and counterbalancing applications.
In these types of gas springs, the piston rod can be locked at any position in its stroke. By triggering a plunger that links with the piston rod, the process is initiated. The rod starts to work as a compression gas spring upon pressing the plunger. When the plunger is released at any given point in the stroke, the rod gets locked in that position. Locking gas springs consists of the following components: piston rod, cylinder, piston valve, guide, seals, etc.
These types of gas springs are application specific, and they are designed to work in a variety of Industrial applications. They are available in a variety of materials such as EPDM, polyurethane, Viton, and other materials.
These types of gas springs come with an additional shroud mechanism around the rod. The gas spring is locked by this mechanism when it is fully extended.
Tension and traction gas springs apply some force or maintain the tension that helps to provide tension on the belt drive and mechanical assemblies. These springs operate in a way that is directly opposite to the way that compression gas springs operate. The springs come in a variety of sizes and stroke ranges, which aid in determining its force range and k factor. These types of springs are manufactured from stainless steel. They control the pulling and adjustment as per requirement.
These types of gas springs work best in corrosive environments. These gas springs come in a variety, such as compression and locking springs. Unlike micro gas springs, all types of stainless-steel gas springs feature a release valve. This valve helps during operation by releasing gas upon obtaining the correct force.
These types of gas springs help in the regulation of the speed and motion of the spring. They do this by using hydraulic oil. They are used in devices that move in a specified direction, such as doors, lids, and covers. Their load capacity ranges from 10 to 150lbs and they have various speed characteristics to meet the application requirements.
This chapter will discuss benefits and applications of gas springs.
Gas springs offer a wide range of benefits including: a higher force range of up to 12000N, a wide range of designs and dimensions, the cycle has no maximum, no external power supply is needed to use the gas springs, an opening angle of more than 90 degrees is possible, gas springs make no noise, and they are relatively cheaper. Below are more benefits of gas springs explained:
Gas springs require little or no maintenance at all compared to other types of springs like traditional coil springs. Gas springs consist of multiple parts like pistons, seals, and attachments. Since these parts are enclosed in a cylinder, maintaining a gas spring is easy. There is no need to be concerned with cleaning of the parts, nor to oil or lubricate them. Gas springs are easy to maintain because of the parts’ self-enclosed design.
Gas springs have a long life. They have a life span that is longer than other types of springs. Compared to other types of springs like coiled metal springs that use a purely mechanical method of operation, gas springs feature a cylinder that is filled with gas. The cylinder protects the gas springs from premature wear and tear. In traditional springs wearing and loss of ability to store energy is quick. Gas springs also deliver a high number of maximum strokes, approximately 100,000. They are financially sustainable because they don’t need to be replaced more often.
Many gas springs can be locked in place. There are locking and non-locking gas springs. Non-locking gas springs cannot be locked in place; therefore, you can choose a gas spring that offers the locking option. This is a benefit of gas springs as compared to traditional springs.
Ergonomics is another benefit of gas springs. They are more ergonomic compared to traditional springs. They deliver a smooth action when exposed to a compressive force. Retraction of the piston into the cylinder will simply occur. Because of this smooth action produced, gas springs are ergonomic. They can be used with certain types of furniture, including office chairs, due to their ergonomic design.
Gas springs offer a wide range of mounting options that include ball and socket, rod end, clevis, eyelet, threaded, tapered end, and bumper or rod end unattached.
The applications of the different gas springs include:
This chapter will discuss considerations when choosing gas springs as well as the installation considerations.
The following factors must be taken into consideration when selecting a gas spring:
They are many important performance specifications to consider when choosing a gas spring, including compressed length, absorber stroke, extended length, maximum force (P1), and maximum cycles per minute
Listed below are the important physical specifications that must be taken into consideration when opting for a gas spring:
This refers to the desired diameter of the housing cylinder
This refers to the desired diameter of the extending rod
The following are the different mounting choices that can be opted for:
This is a spherical bearing that allows for multi-axis rotation. A spherical bearing is a ball end (which is being referred to as the ball and socket) with an integral stud that is threaded.
These include mating fork mounts.
Mounting the cylinder side has a tapered end for snug fit into the mounting hole on a tapered end.
In this mounting, the ends have standard threads for mounting or accessory attachment.
In this type of mounting, the rod and the load are unattached, but the rod has a bumper on the end to engage moving load.
This refers to the type of material used to manufacture the gas spring. Common types of materials include aluminum, steel, stainless steel, and thermoplastic. If the gas spring is going to be used near saltwater or in food and medical applications, customers may opt for materials that are rust-inhibiting or UV coatings.
Knowing the weight and dimensions of the object to be moved is vital. The spring scale can be used to determine its weight for best results.
The range of motion of the body of the gas spring must not be limited; therefore, the body of the gas spring must fit within the assembly.
This refers to the range of the environment temperature under which the gas spring can operate.
The geometry and weight of the load must be known in order to determine the position where the gas spring can be mounted, the force that is required to counter-balance the load, and where any compromises can be made. When a gas spring is mounted with its center of gravity close to the pivot, its operation is easier to predict.
The gas spring’s long life is based on the correct lubrication of the seals. The correct orientation to install the spring is to have its rod directed downwards (see figure 2.1 below) or having the rod guide in a position that is lower with respect to the cylinder attachment.
In applications like car boots, the spring may rotate upwards between the fully open and fully closed position during the opening movement. Here also, focus on installing the spring with its rod directed downwards when it is in its fully closed position and compressed inside the cylinder.
These positions are recommended because they facilitate the lubrication of the guide and seals while delivering an excellent braking effect. The gas pressure is maintained by the rod surface. Therefore, the rod surface should not suffer any damage from blunt or abrasive objects or by any chemical substance that is corrosive.
When installing the spring, the seal must not be put under strain. This is achieved by aligning the lower and upper fittings. Maintenance of the alignment throughout the entire stroke is vital. Jointed attachments that allow alignment can be used. The machine to which the gas spring is applied may discharge vibrations onto seals through rigid connected attachments to the frame. A small clearance between the fixing screws and the attachments must be left out, use at least one joint attachment to fix the spring. Fixing the gas spring with smooth pins is recommended rather than using threaded bolts as thread crests.
During the application of the gas spring, make sure that the thrust force of the gas spring is greater than the pulling forces so as to ensure that the normal rod sliding speed is not exceeded. The normal operating temperature range is -30°C - +80°C. In particular, damp and cold environments may cause the creation of frost on the seals and compromise the duration of the gas spring.
The design and manufacturing of the gas spring was for it to lighten or counter-balance a heavy load for the operator or for the structure into which it is inserted. If it is put to any other use, this will need the designer or the manufacturer to carefully assess the use with regard to safety and durability of the spring.
The major factor in the failure of gas springs is the result of side loads being placed on the spring or rod. It is essential that nothing touches the sides of a gas spring, regardless of how minor. In some cases, a user will intentionally have force applied to the side of a gas spring to support another mechanism. The result of such behavior is early failure of the spring.
Additionally, twisting forces cannot be applied to the end connector of a gas spring. To avoid failure from twisting, a ball and socket connector is used to avoid any torque being applied to the connector.
Gas springs have a diversity of benefits over other types of springs due to their design and manufacture. They can be used in many applications including office furniture and industrial equipment. To choose the right gas spring for a particular application, one must know the specifications of the gas spring. Gas springs are long lasting as long as they are used under the correct specified conditions.
A door latch is a mechanical fastener that connects two surfaces or objects and provides a secure, safe, and strong connection. The latch portion of the mechanism is mounted on a flat surface such that when it meets a...
A gate latch is a locking mechanism that is used to secure gates on fences or stakes on truck beds using a metal bar and lever that is raised to open the latch and lowered to close it. Although they do not have...
Latches are mechanical components that allow the temporary joining of parts that are moving relative to each other. They are actuated to release the coupling and allow the two parts to separate. Latches are mostly seen on doors and enclosure...
A lock is a mechanism designed to connect an opening to its frame using a latch, solid cylinder, bolt, or some other form of a solid metal plunger that extends into the strike. They are metal devices that prevent entry or access for privacy, security, or...
A magnetic door latch is a type of latch that consists of a striking pad and a magnet and is used to keep doors and gates closed. Magnetic door latches are also known as magnetic door stops, magnetic door catches, and door magnets...
A rotary latch is a locking mechanism that secures openings such as doors, enclosures, cabinets, and panels so that they are locked and unable to accidentally open. They are referred to as slam latches since...
Rubber latches are latches made of rubber or are composed of rubber components. They are used in the automotive, aerospace, and medical equipment industries due to their flexibility, durability, and non-abrasive properties...
A spring latch is a mechanical device that is utilized in the joining of two separate components in order to prevent movement or opening. A spring latch is locked with a spring compression so that it will not be released...
A vibration absorber is a single degree of freedom (DOF) spring-mass system that eliminates or reduces the vibration of a harmonically excited system such as the rotation of engines, motors, generators, belts, etc...