Vacuum Pumps
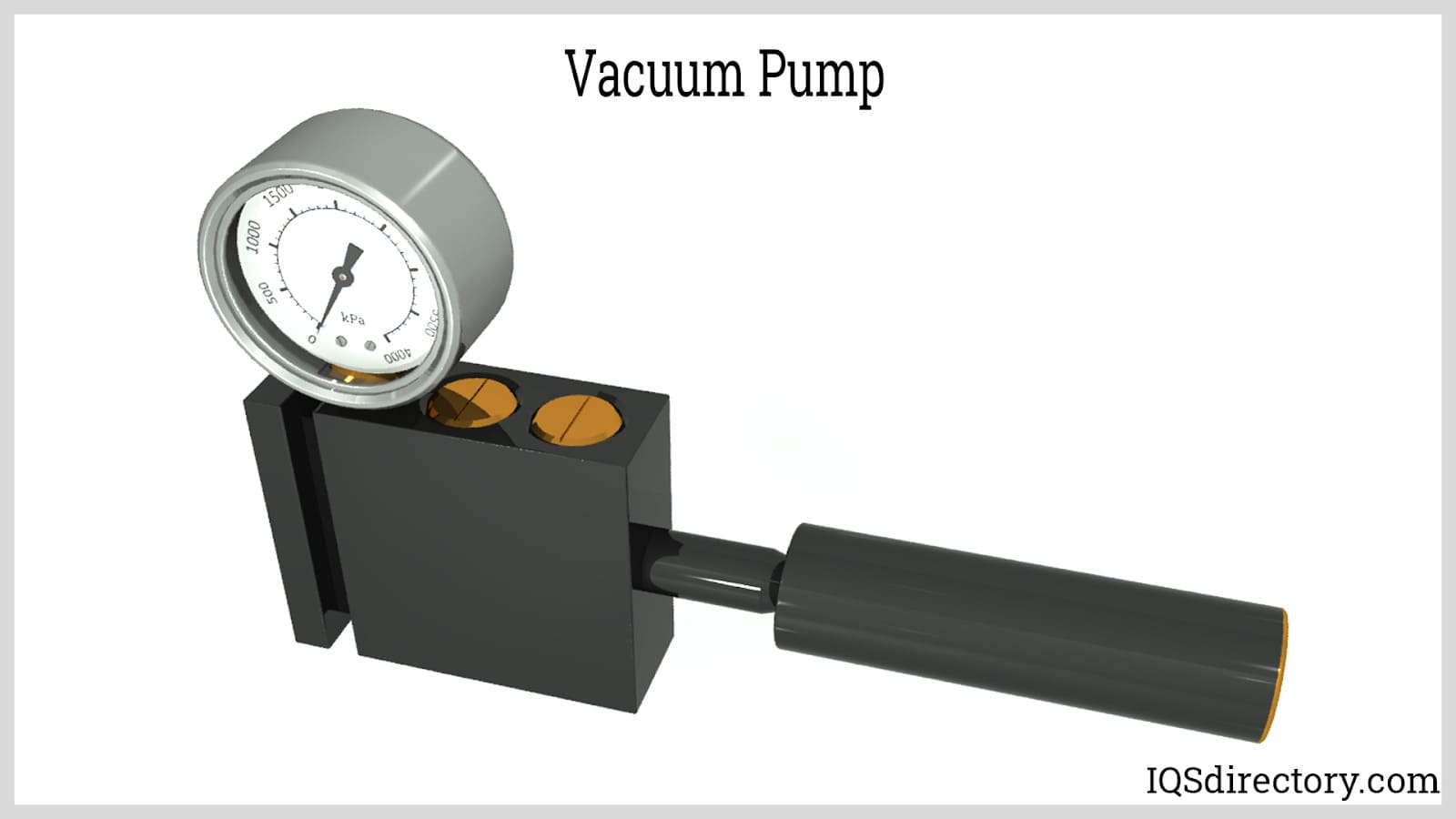
A vacuum pump is a piece of equipment capable of generating a partial vacuum or a low-pressure space by drawing gas molecules out of a sealed chamber. A vacuum is a relative state at which the chamber pressure has...
Please fill out the following form to submit a Request for Quote to any of the following companies listed on
This article will take an in-depth look at rotary vane vacuum pumps.
The article will bring more detail on topics such as:
This chapter will discuss what rotary vane vacuum pumps are, their design, and how they function.
Rotary vane vacuum pumps are vacuum pumps that generate low-pressure zones by rotating the moving parts against the pump casing. The mating surfaces of the rotor and the housing have very small clearances that are covered with self-lubricating or low friction materials like graphite, PEEK (polyether ether ketone), or PTFE (polytetrafluoroethylene).
The narrow clearance prevents fluid leakage to the low pressure side. Rotary vacuum pumps offer lower pulsing delivery than reciprocating versions, resulting in a more continuous flow. However, they are not suitable for handling fluids contaminated by abrasive media because the narrow clearances between the housing and the rotor can be eroded. Rotary vacuum pumps are categorized based on the rotor design.
The most popular form of positive displacement vacuum pump is the rotary vane vacuum pump. The vanes in this pump are inserted radially into a circular rotor. The rotor is positioned eccentrically with relation to the stator housing. The eccentricity is referred to as the pump stroke. As it gets closer to the discharge, the individual chambers divided by the vanes get smaller and smaller. The vanes are free to move radially, pressing on the housing mostly due to centrifugal force while the rotor turns. When the rotor is not in motion, a spring energizes or holds the vanes in place.
Rotary vane vacuum pumps are a type of positive displacement pump. This means that they constantly evacuate chambers and generate a vacuum without requiring infinite expansion by closing off, exhausting, and re-expanding one of their sections. Rotary vane pumps, aside from being positive displacement pumps, can be constructed as dry pumps or oil-sealed pumps. In a nutshell, dry pumps operate without the usage of any liquid.
Wet pumps use a fluid seal/lubrication to work, while dry pumps depend on internal dimensional tolerance to make a vacuum. Following that, oil-sealed pumps are a sort of wet pump (a pump that employs fluid to create a seal) that uses oil to generate a seal. Furthermore, many rotary vane vacuum pumps are built with a direct drive. Every rotary vane vacuum pump is built using the same basic components.
There will be changes in components depending on the design, size, or model. The following are some common components found in both oil-lubricated and dry-running pumps.
Rotor – The rotor is normally wound with copper, while some variants use a cylindrical or "caged" rotor constructed of solid conductors. The rotor is the revolving part of this electrical engine, regardless of design, but it requires energy to turn. The stator is the coiled layout's stationary component. It carries electrical current and wraps around the interior surfaces of the motor's housing. As basic as this arrangement of copper conductors appears to be, the technical concepts underlying the technique are a little more complicated.
Blades and Vanes – These are wide blades attached to a rotating wheel or axis. The vanes maintain a tight seal against the pumping chamber's wall, preventing fluid from flowing back across the pump.
Oil Sump – The engine oil necessary for sealing is stored in the oil sump. An oil pump extracts the oil from it and conveys it into the engine block's oil channels via the oil filter. The oil then returns to the oil sump via the sealing points.
Cylindrical Housing – Often made of die-cast aluminum. It is the outer part of a pump. It houses the compressor inside.
Suction Flange – Suction flanges are used to connect a suction tube onto a hydraulic tank. They form a seal to prevent fluids from leaking and pollutants from entering the tank. Suction flanges also allow access to the suction element without draining the tank.
Motor – An electric motor is a machine that converts electrical energy (AC or DC) into mechanical energy. Most electric motors generate force in the form of torque imparted to the motor's shaft by interacting between the magnetic field of the motor and electric current in a wire winding.
Float Valve – A float senses variations in elevation on the oil free surface and opens or closes a valve in response.
Oil Separator Elements and Filters – Oil separator elements are inserted directly into the vacuum pump's exhaust box. They are also utilized to collect oil mist from the lubricating process.
Oil Separator Housing – Houses the oil separating elements and oil sump.
Oil – the lubricating/sealing fluid
Pressure Regulating Valve - A pressure lowering regulator is a control valve that lowers a fluid or gas input pressure to the desired value at its output. It is a normally-open valve that is put ahead of pressure-sensitive equipment.
Motor Fan - The fan, also known as the impeller, is the disk-shaped component with fins that generates suction in a vacuum cleaner. It is always fitted directly on the shaft of the Suction Motor, causing it to spin at a rapid rate. The actions of centrifugal force acting on the spinning air in the fan produce suction.
Exhaust Silencer - They are made of steel and lined with aluminum to protect from heat. Also called mufflers, they are used mainly to dissipate the noisy sounds created by the vacuum pump.
Rotary vane vacuum pumps are a type of Vacuum pump. A vacuum pump is a piece of machinery that may create a partial vacuum or a low-pressure environment by sucking gas molecules out of a sealed chamber. A vacuum is a relative condition in which the chamber pressure is lower than that of the surrounding atmosphere or systems. This is distinct from an absolute vacuum, which has a pressure of 0 Pa absolute and is entirely bereft of gas molecules.
There are various levels of vacuum that can be produced. It can be anything from a low vacuum with a range of 1 to 0.03 bars of absolute pressure to an exceedingly high vacuum with a pressure of one billionth of a Pascal. Vacuum cleaners, vacuum grippers, incandescent bulbs, vacuum furnaces, sandblasting, painting, and negative pressure ventilation are all examples of low and medium vacuum. For laboratory applications like particle reactors and accelerators, higher vacuum systems are used.
There are two types of partial vacuum generators. The first is through gas transfer or gas feeding, while the second is through entrapment. Gas transfer vacuum pumps remove gasses mechanically using momentum transfer or positive displacement. To draw and eject flow, positive displacement vacuum pumps use chambers that sequentially contract and expand with check or non-return valves. Momentum transfer pumps operate by accelerating gasses, leaving a low-pressure zone in their wake. Entrapment vacuum pumps, on the other hand, use numerous processes to capture gas molecules, such as sublimation, condensation ionization , adsorption, and so on.
The narrow clearance prevents fluid leakage to the low pressure side. Rotary vacuum pumps offer lower pulsing delivery than reciprocating versions, resulting in a more continuous flow. However, they are not suitable for handling fluids contaminated by abrasive media because the narrow clearances between the housing and the rotor can be eroded. Rotary vacuum pumps are categorized based on the rotor design.
The most popular form of positive displacement vacuum pump is the rotary vane vacuum pump. The vanes in this pump are inserted radially into a circular rotor. The rotor is positioned eccentrically with relation to the stator housing. The eccentricity is referred to as the pump stroke. As it gets closer to the discharge, the individual chambers divided by the vanes get smaller and smaller. The vanes are free to move radially, pressing on the housing mostly due to centrifugal force while the rotor turns. When the rotor is not in motion, a spring energizes or holds the vanes in place.
Rotary vane vacuum pumps may differ in a variety of ways. Their material compositions, on the other hand, are usually relatively standardized. Rotary vane vacuum pumps have several parts composed of various materials, such as:
Cast Iron - Cast iron is a broad category of ferrous alloys comprising between 1% and 3% silicone and 2% to 4% carbon, with a core of approximately 95% iron by weight. While several casting procedures are used to make cast iron parts, they all follow the same basic process of heating, molding, cooling, and ejecting.
It has good casting attributes and is available in huge quantities, therefore produced in a mass scale. Tools needed for the casting process are comparatively cheap and inexpensive. Hence this results in the low cost of vacuum pumps. It can be made into any complex form and size without using expensive machining operations. Cast iron has 3 to 5 times more compression strength in comparison to steel. Good machinability in gray cast iron is a bonus. Its outstanding damping or anti-vibration properties make it useful in vacuum pumps. Cast iron is outstandingly resistant to wear. It’s also durable and resistant to deformation.
Ductile Iron – Also known as ductile cast iron or nodular cast iron is a type of graphite-rich cast iron. While most variations of cast iron are tensile weak and brittle, ductile iron possesses much more impact and fatigue resistance, because of its nodular graphite additions.
Ductile iron may be cast and machined easily. Its strength to weight ratio is excellent. Ductile iron is much cheaper than steel. Ductile iron gives a designer an exceptional combination of cheap manufacturing, toughness, and reliability.
Steel - Steel is a metal alloy composed of iron, carbon, and other elements. These elements include molybdenum, tungsten, chromium, nickel, silicon manganese, and, among others. Steel is the most important engineering metal by far. It has a high tensile strength at a reasonable cost, making it an excellent choice for vacuum pump construction.
Steel is probably the most popular material among producers because of its durability. Properly processed and plated steel will not decay, distort, split, crack, or catch fire. Wherever and whenever it is utilized, it delivers great structural integrity, resistance to weather, and long-term strength.
Steel’s flexibility is just as important whether the vacuum pump requires machining, welding, or painting. The wide variations of steel products available show that its design flexibility is boundless. Vacuum pumps are a testament to its flexibility.
Carbon Graphite - Carbon graphite is a material used for replacement and specialty components because it offers high-temperature capabilities, wear resistance, self-lubricating qualities, and the ability to be utilized with corrosive materials when properly prepared.
Carbon graphite devices are usually composed of two materials: powders and binders. Natural or synthetic graphite, carbon black, petroleum coke, or other types of carbon are used to make powders. Coal tar pitch is a popular binder in carbon graphite compounds.
Carbon graphite and graphite parts are self-lubricating and will not seize or gall while in use. Furthermore, because carbon graphite is dimensionally solid, temperature variations will not distort the portion. Pushrods and vanes are frequently made of carbon graphite and graphite parts.
Polyetheretherketone (PEEK) - is a semi-crystalline engineering thermoplastic with good performance. This stiff opaque (gray) material has a one-of-a-kind combination of mechanical characteristics, chemical resistance, wear, fatigue, and creep resistance, as well as extraordinarily high temperature resistance, reaching 260°C (480°F). The polymer belongs to the polyketone family of polymers, of which PEEK is the most frequently utilized and mass-produced.
PEEK has excellent tensile characteristics. Tensile strength of 29000 psi may be attained when strengthened with carbon fibers, with outstanding characteristics retained at 299°C. The polymer also has a high creep resistance. When paired with flexural and tensile qualities, it provides a great balance of qualities where the material must sustain strong loadings for extended periods of time at high temperatures without permanent deformations.
Its flexibility modulus at extremely high temperatures can be enhanced further using glass or carbon reinforcing. (Reinforcement also improves creep and fatigue resistance, polymer thermal conductivity, and heat distortion temperature). It has crystallinity which provides great resistance to a wide range of liquids as well as superior fatigue performance.
The functioning of rotary vane vacuum pumps is as follows:
The operation of a rotary vane is based on the principle of increasing pressure by decreasing volume. The blades rotate within the cylinder, and the presence of a thin layer of oil in the cylinder means that there is almost no wear. The oil lubrication is produced by differential pressure in the housing. Pipes connecting the housing aid in this endeavor. The rotor is eccentrically positioned within the housing. The blades are pressed against the housing wall by centrifugal force, resulting in three chambers that collect the air. When the first chamber opens, air enters the compressor chamber via the suction flange.
The following vane closes the first chamber then opens the second as the rotor rotates. This is the position at which the blades are the furthest apart, allowing for the most air volume. The oil and gas mixture is then squeezed using volume reduction and blown in the oil separator housing. Some pump designs incorporate exit valves to prevent air backflow once maximum pressure is attained or the pump is shut off. Gas and oil are divided from one another in the oil separator housing by a procedure.
The oil is redirected to the oil sump. This technique can remove 95-98 percent of the oil content from the air. To eliminate any leftover oil particles, the remaining gas and oil combination is passed through fine filter components. These particles will then be reintroduced into the pump's oil circuit through a float valve. Now that the gas is nearly oil-free, it can be evacuated by the air exit or via pipes or hoses.
Drying running pumps, like lubricated pumps, operate on the pressure rise by volume reduction concept. In these pumps, dry graphite vanes brush against the surface of the housing cylinder, forming a graphite coating that protects the pump from wear. These pumps, like their lubricated counterparts, must filter the compressed air after it has been blown out to eliminate any particulates. Furthermore, with this sort of pump, the air is frequently passed via a cooler to lower the exhaust's temperature.
Manufacturers list several distinct sorts of specifications to define rotary vane vacuum pumps and systems. The ultimate operational vacuum and pumping speed are the most critical specifications to consider for rotary vane vacuum pumps.
Ultimate (Maximum) Operating Vacuum – The vacuum pump's ultimate pressure is the lowest pressure that it can produce (usually within a set time). Buyers should take note of the conditions or assumptions used to calculate this figure, as manufacturers may provide this grade based on assumptions that are unrealistic under regular operating settings (e.g. leaving the pressure of the condensable gasses like water vapor).
Pumping Speed - The volumetric rate at which gas is drained from the vacuum chamber is measured in m3/s, ft3/min (cfm), L/min, or gal/min (gpm). The highest achievable pumping speed of a pump (across its whole pressure range) is referred to as its rated pumping speed always, and manufacturer-specified pumping speeds are often attributed to STP (standard temperature and pressure). Pumping speed must be matched to the application's requirements, which are determined by the system's desorption, chamber volume, and process gas loads. Depending on the design and application, rotary vane pumps have pumping rates ranging from 1 to 650 cfm (cubic ft per minute).
Note: The pump's speed is rarely the same as the true pumping speed in the device's chamber. When comparing performance parameters to the application’s needs, rated pumping speeds are often determined under the same parameters as the ultimate pressure.
Rotary vane vacuum pumps are usually powered by either alternating current (AC) or direct current (DC).
AC power is the most usual supply for rotary vane vacuum pumps and systems. Single phase AC motors are well known and are commonly cheaper than three phase AC motors, however they are also less efficient (for equivalent horsepower) and bigger.
DC power supplies use DC current from a battery or power supply.
The pumping speed and vacuum level are key factors to consider. They have an impact on all of the other aspects. The following are examples of typical classifications and ranges:
There are two factors to consider while determining the appropriate pumping speed:
Depending on the desired pump down time and vacuum level, a combination of vacuum pump technologies may be required.
Pumps that operate in the medium and rough vacuum regions are known as fore vacuum pumps. These pumps work by compressing gas and then expelling them into the atmosphere. Food packaging, heat treatment, and freeze drying are examples of applications.
High and ultra-high vacuum pumps, such as diffusion and turbopumps pumps, work solely in tandem with a fore vacuum pump and use the molecular transfer mechanism. Metallurgy, coating, and analytical applications are possible.
The different types of rotary vane vacuum pumps include:
The typical lubricated rotary vane pump is a single-stage pump with a closed-loop oil-circulation system. The construction is robust and compact. 50,000 hours is the average life. The pump rotor is eccentrically positioned in the pump's cylinder. Inlet gets contained between the rotor and vane segments when the pump rotor revolves. This causes an increase in cell volumes on the inlet's port side, resulting in a vacuum.
Because the rotor is eccentric to the pump chamber, the volume between the vanes, rotor, and housing reduces, causing the rotor’s spin to increase. As the revolution proceeds, the air is compressed and expelled into the exhaust box.
These vacuum pumps use the tried-and-true rotary vane technology. There is no need for operating fluid because the rotor vanes self-lubricate. The compression takes place during a fully dry operation.
Perfectly coordinated materials, specific graphite vanes/blades in the compression chamber, efficient heat discharge, and high-tech and accurate production ensure a continuously high vacuum level in continuous operation.
When the vacuum pump is turned off, an optional non-return valve prohibits air from entering the vacuum chamber. The unit is powered by an integrated motor with a high efficiency rating.
The compressor variant operates practically pulsation-free and without the use of any oil. A strong cooling fan removes heat from the motor and pump.
A liquid-ring pump uses positive-displacement rotation. They are commonly employed as vacuum pumps, but they can also be utilized as gas compressors. A liquid-ring pump works similarly to a rotary vane pump, except that the vanes are an inherent component of the rotor and churn a revolving ring of liquid that forms a compression-chamber seal. The rotor is the only moving portion, hence they are naturally low-friction. The shaft seals are the only places where sliding friction exists. Induction motors are commonly used to power liquid-ring pumps.
By rotating a vaned impeller eccentrically in a cylindrical housing, the liquid-ring pump compresses gas. Liquid (typically water) is delivered into the pump, where it creates a rotating cylindrical ring on the inside of the casing due to centrifugal acceleration. This liquid ring forms a series of seals between the impeller's vanes, forming compression chambers. The eccentricity of the geometric axis of the casing and the impeller's axis of rotation causes a cyclic fluctuation in the volume encompassed by the vanes and the ring.
Gas, usually air, is pulled into the pump via an inlet port at the casing's end. The gas is contained in the compression chambers created by the impeller's vanes and the liquid ring. The compression induced by the impeller's rotation compresses the gasses, which flows to the discharge port at the casing's end.
On pump discharge, compressed gas retains a small amount of working liquid, which is normally removed in a vapor–liquid separator.
This chapter will discuss the applications and benefits of rotary vane vacuum pumps.
Because a rotary vane vacuum pump is very simple in design, they are frequently ineffective for producing high vacuums. Nonetheless, they are widely used in a variety of situations that necessitate the generation of an artificially evacuated environment or vacuum. Some of these include the use of electron microscopy, the manufacture and design of electronics such as superconductors, and the use of certain types of analytical apparatus. These types of environments frequently necessitate the existence of vacuum pumps since they must be devoid of minute airborne pollutants of air particles in general. In addition, rotary vane vacuum pumps are often utilized in healthcare to deliver suction during surgical procedures.
Firstly, liquid ring vacuum pumps have a rotary as well as vanes that revolve around an enclosure. Because they are sealed by a ring of water, they are known as liquid vane pumps rather than rotary vane pumps. This ring assists them in compressing air and preventing it from returning to an evacuated area. Following that, both pumps that require oil as a sealant or lubricant and dry vacuum pumps have spinning blades.
Rotary vane vacuum pumps are some of the most prevalent types of vacuum pumps. In truth, most vacuum pumps have spinning vanes, blades, paddles, or impellers of some kind that propel shuttle gas in and out of an enclosure, and any vacuum pump with any of these components is a rotary vacuum pump.
The presence of low vapor pressure oil is the first drawback. Because the rotary vane vacuum pump can’t function without oil, it must be regularly monitored, refilled, and changed. This also exposes the vacuum pump to contamination from high vapor pressure gasses, reducing its performance and damaging its components.
Installing traps and filters before the vacuum pump’s intake prevents pollutants from entering the vacuum pump chamber. This reduces the risk of contamination of the oil in the vacuum pump.
Furthermore, the rotary vane pump discharges oil and water mist into the environment through its exhaust. One rotary vane vacuum pump can smoke up an enclosed space to the point that it becomes a health danger over time. This precludes the use of rotary vane pumps in clean rooms, close surroundings, or indoor conditions.
Oil mist emissions can be reduced by attaching an exhaust filter or an oil mist eliminator to the vacuum pump's exhaust. This simple measure reduces emissions by 99.95 percent.
The maintenance of rotary vane vacuum pumps considers:
Because rotary vane pumps use oil in greater volume, it is critical to change the oil on a regular basis to keep the pump working. General recommendation is that oil should be changed every six months, however this may be necessary earlier or later depending on how frequently the pump is operated and what process gasses pass through it. The color of the oil is an easy indicator that an oil change is needed. The new oil is clear. The oil's color darkens when the pump is utilized. When the color reaches amber hues, it's time to replace the oil. Oil color must never be allowed to reach shades of black or dark red, since this may cause pump failure and a whole overhaul.
Performance oil is triple refined to the maximum level of purity after being treated without contamination or dilution. It is not suggested to use low viscosity oils because they will reduce pump speed, ultimate vacuum, and ultimately the pump's lifetime.
Wearable elements such as gaskets, O-rings, and seals must be replaced on a regular basis in every rotary vane pump. Without this, the pump's sealing capability deteriorates and its performance begins to deteriorate. The frequency of clean and overhaul is determined by the size of the pump. Larger vacuum pumps having pumping speeds of 40 m3/h-1 and higher necessitate annual clean and overhaul maintenance. Smaller pumps having pumping speeds of up to 28 m3/h-1 can run for two years before requiring a clean and overhaul.
Rotary vane pumps are based on the revolving vanes, also called blades, technology. Because the vanes are moving materials that are exposed to process gasses, they must be replaced on a regular basis. Vanes replacement is recommended in conjunction with clean & overhaul maintenance and is necessary once every three years for bigger vacuum pumps (40 m3/h-1 and above) and once every four years for smaller vacuum pumps (up to 28m³/h-1).
Another key maintenance consideration is maintaining a rotary vane vacuum pump as cool. Heat, in fact, is the one thing that can destroy a motor quicker than anything else. If the pump is operated in a confined space, using a fan can keep it cool. The issue is that when the engine gets too hot, it reduces the oil’s viscosity. When this happens, the pump's ability to create a vacuum is no longer efficient.
Solids and liquids entering a rotary vane vacuum pump can cause failure if the filter is unable to complete its job. As a result, much like the oil, the filter should be changed according to the manufacturer's instructions.
Vacuum pumps generate low-pressure zones by rotating the moving parts against the pump casing. The most popular form of positive displacement vacuum pump is the rotary vane vacuum pump. Rotary vane pumps, aside from being positive displacement pumps, can be constructed as dry pumps or oil-sealed pumps. In a nutshell, dry pumps operate without the usage of any liquid.
Wet pumps use a fluid seal/lubrication to work, while dry pumps depend on internal dimensional tolerance to make a vacuum. Rotary vane vacuum pumps may differ in a variety of ways. Their material compositions, on the other hand, are usually relatively standardized.
They are widely used in a variety of situations that necessitate the generation of an artificially evacuated environment or vacuum. Some of these include the use of electron microscopy, the manufacture and design of electronics such as superconductors, and the use of certain types of analytical apparatus.
A vacuum pump is a piece of equipment capable of generating a partial vacuum or a low-pressure space by drawing gas molecules out of a sealed chamber. A vacuum is a relative state at which the chamber pressure has...
A ball valve is a shut-off valve that allows or obstructs the flow of liquids and gases in a piping system by rotating the ball having a bore inside the valve for 90°. The ball is mounted against two seats and has a stem that connects it to the operating and control mechanism that rotates the ball...
A butterfly valve is a quarter-turn rotational motion device that utilizes a rotary disc to allow, obstruct, or control the flow of fluids in a piping system. It features a rotating disc that is situated on the passageway of the flowing media...
A check valve is a safety device designed to allow fluids and gases to flow in one direction. Under pressure, fluids enter the valve at the inlet and exit through the outlet. Uninterrupted flow continues until the pressure drops, or the pump is shut down...
A PVC or polyvinyl chloride ball valve is a plastic on and off valve that has a rotary ball with a bore where turning the ball a quarter turn can stop the flow of a fluid. They are highly durable, cost effective and can be...
A spring check valve is a valve that ensures unidirectional flow and prevents reverse flow. They have a single inlet and outlet and must be placed in proper orientation to function correctly. On the side of a spring check valve, and all...