Capacitive Touch Screen
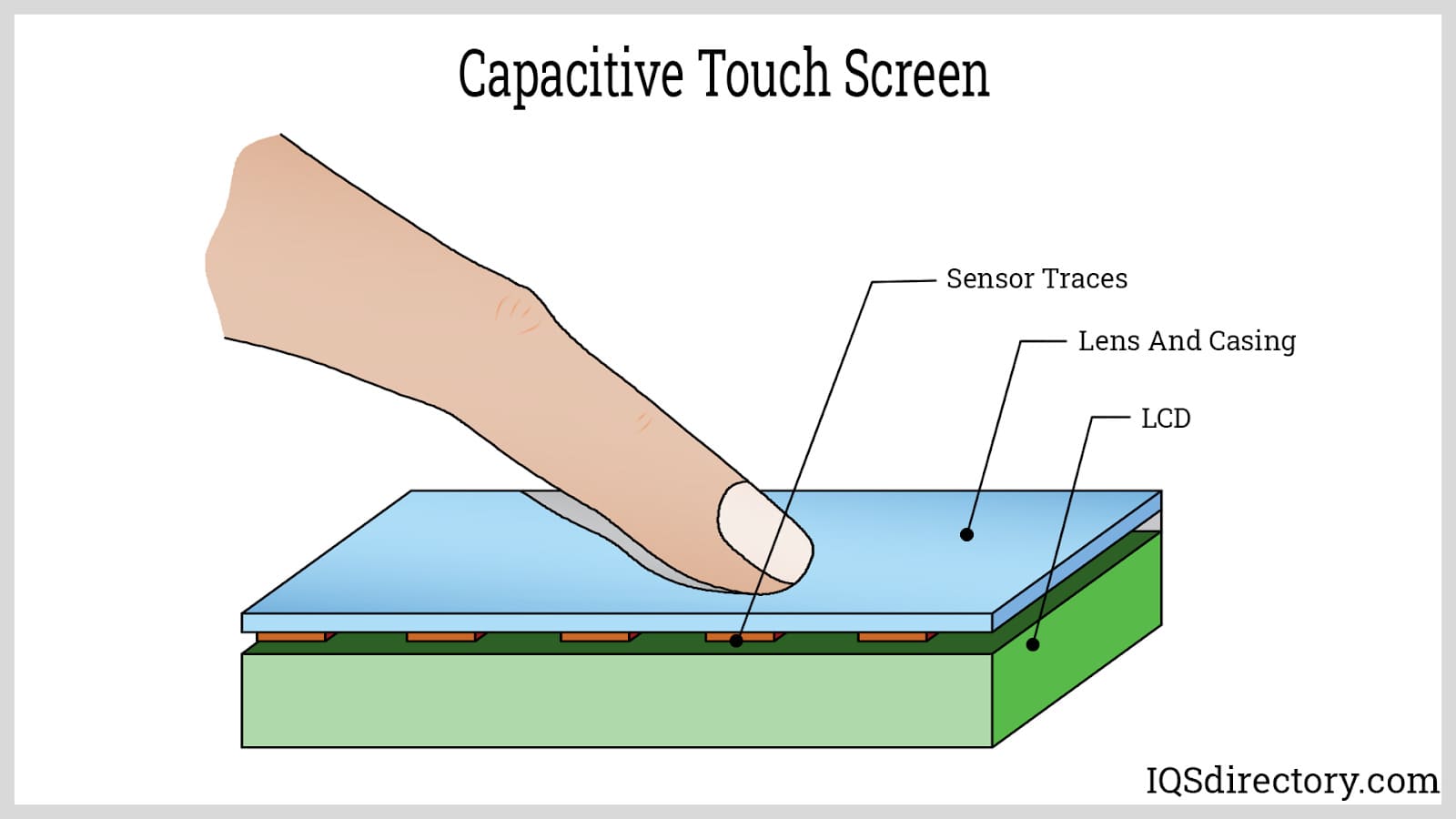
A device's display screen that uses finger pressure for interaction is called a capacitive touch screen. Handheld capacitive touch screen devices generally link to networks or computers using an architecture that can...
Please fill out the following form to submit a Request for Quote to any of the following companies listed on
This article will give a detailed discussion of flexible printed circuits.
It is expected that after reading this article, one should understand the following:
And much more…
Simply put, a flexible printed circuit (abbreviated FPC) has conductive traces on a thin, flexible substrate. "Flexible printed circuits." are circuit boards that can twist or bend. This claim makes it clear that they can be distinguished by flexible construction. It might feature surface-mount components like resistors and LEDs, and it typically has a connector or termination point for integrating with other parts. It's crucial to pick the appropriate substrate for the application because there are considerable differences between it and regular printed circuit board regarding design, production techniques, and functioning. Flexible substrates like polyimide are used to create flexible printed circuits since this property makes them unique. A PCB (printed circuit board) is composed of a flexible board with several wirings and connection pads placed on the flexible PCB's edge. It is created by laminating a copper foil with a resin substrate; the layers are attached with adhesive, heat, or pressure to create an integrated board. The conductive layers are encapsulating, insulating, and adhesive layers for effective insulation.
Applications requiring lightweight, compact, thin printed circuit boards with a high wiring density can benefit from flexible circuit boards. Flexible PCBs that can be three-dimensionally wired and reconfigured to fit applications and available space are necessary as companies attempt to to perform more functions with fewer employees. The improved heat dissipation of flexible printed circuits over printed circuit boards is another significant feature of these devices. This property allows for the electronics that use them to keep working well for a long time.
Flexible printed circuits and traditional printed circuit boards differ in several ways. It's crucial to note that even though they both perform a comparable electrical function, they differ noticeably in their mechanical and structural design. The first distinction between the two is that although a regular printed circuit board cannot be bent or twisted, a flexible printed circuit can. Due to this specific distinction, the two need to use various manufacturing processes, materials, and designs.
The requirements for printed circuit boards are primarily focused on thermal and chemical properties concerning adhesives. They don't flex, which is the main cause of this. The flexible printed circuit is different from this. Since it must bend, the chosen adhesive must permit bending for the application to succeed. For a glue designed for a flexible circuit, there must be a sizable degree of stretching. In short, a flexible printed circuit requires an adhesive with different thermal, mechanical, and chemical properties than a printed circuit board.
The base layer of a printed circuit board must be strong and typically reinforced with glass. In this instance, a class of flame retardant material formed of an epoxy resin and glass fabric composite is the most frequently utilized to produce it. The substance employed offers crucial stability and excellent mechanical and thermal resistance. However, it is rigid and cannot bend. On the other side, polyimide is mostly employed as the basic material for flexible circuits. This material has the advantage of having good flexibility, but it cannot offer mechanical support. Its dimensional stability also has some limitations.
The discussion then turns to copper film. There are two types of copper film. Electrodeposition is used for the first, and rolling and annealing are used for the second. The more flexible of the two, rolled and annealed, is ideal for a flexible printed circuit application. However, printed circuit boards are primarily produced using electro-deposited copper, although it has limited flexibility. Therefore, the performance of a flexible circuit greatly depends on the type of copper used.
Compared to rigid PCBs, flex PCB design necessitates a slightly different procedure. Here are some recommendations and things to keep in mind when considering a flex PCB.
One must ensure that the flexible PCB manufacturer they choose appropriately applies the most recent technology to anticipate material, movement, and thermal coefficient to construct resilient circuit boards. These are necessary to create a flexible PCB that the client requires.
In addition, the following are some other aspects to take into account when choosing a flexible PCB manufacturer. The manufacturer should provide assurances about the quality of the product. The purchaser must be confident that their purchase will be worthwhile because some products can be expensive. The manufacturer's circuit board should have a high-density design, quick communication lines, and good conductivity for improved thermal dissipation.
A manufacturer should be able to create whatever shape they need for flexible PCB construction. The majority of producers must comply with these fundamental criteria:
The bend radius characteristics are taken into account by producers of flexible circuits. Early in the design process, determine the bend radius to enable the design to tolerate any bends without damaging the copper. The bend radius suggests the minimal bend amount of the flex region. The bend radius should not contain bend radius elements like slots, cutouts, and mounting components.
The cover material chosen during a printed circuit board's fabrication significantly impacts its lifespan and overall performance. Therefore, it is crucial to choose cover materials that are appropriate for the circuit board's application. Make sure to consider quality while choosing the cover material. Quality is crucial whether users use flexible printed circuit boards for domestic or commercial purposes. The manufacturer must ensure that when choosing cover materials for printed circuit boards, the content is chosen based on proper performance, specifications, and the board's environment.
There is a step in the routing process known as "wire routing," or the path in electronic design. In the process of designing printed circuit boards, the route is a crucial phase. It's difficult to install the circuitry on a flexible PCB because the amount of strain applied to the board decreases as the bend radius increases. To achieve safety in the PCB design, the traces of installed components must pass via the low-stress areas. Trace routing aids in preventing short circuits and electrostatic discharge on the printed circuit board (PCB).
It doesn't concern features that may lead to discontinuities later, especially in a bending area. When one twists or stretches a flexible circuit, the pressure inside can cause breaks and cracks in the insulation or conductors. Again, it is better to eliminate beams and reduce the chance that copper circuits will get thin.
A layer-stacking strategy is critical on flexible PCBs because multiple layers are stacked on top of one another. The most flexible layers must be layered in the middle to prevent slipping.
Delamination, often referred to as "layer detachment," is a common issue in PCB production and use. The layers routinely demold, abruptly damaging the circuitry and occasionally even causing PCB collapse. Solder paste must be used to prevent delamination. When choosing a solder paste material, flexibility requirements must be considered. Features must be incorporated into the design to prevent delamination.
It is wise to avoid basing the adhesive width for flexible printed circuit boards on a drawing when designing them. Instead, designers should know that the description only needs to say how wide the flexible printed circuit board is and include some important dielectrics that affect impedance.
For their flexible printed circuit designs, designers need to create drawing packages. As a designer, one should not completely over-detail the non-critical aspects or elements of a drawing, even though it is necessary to specify some vital features. Find the correct balance of elements to make sure the costs are as low as possible.
Flexible printed circuits are made of a variety of materials. Copper is one of the primary materials used in flexible printed circuits as a conductor material. Other conductors that are employed include silver ink, Constantan°, and aluminum. Another material used in these specific circuits is polyimide. These components set flexible printed circuits apart from conventional printed circuit boards.
Flexible printed circuit production is procedural and is divided into stages. Flexible printed circuit manufacturers typically follow four steps, each of which includes a variety of procedures.
The initial phase is when the preservation of the base material is the main objective. Polyimide is the main material utilized for the flex circuit. Circuits should be kept as close to one another as feasible using the nesting method for proper polyimide utilization. The following procedures are part of the manufacturing process for flexible circuits:
Create cross-hatched ground areas if the electrical allotment is sufficient. In addition, lowering the weight of the circuit board helps the circuit's flexibility.
Following the initial stages, fabrication starts with an emphasis on the boards. The conductor width and spacing come first. 375 micrometers is the minimum conductor width needed for thin polymer films. The desired percentage of circuit current is carried by the nominally thick polymer films and the silver-based polymer films simultaneously. Depending on the design and application, the diameter of the holes on flexible PCBs might change.
Considering the edge distance is very important when making flex circuits. Here is where all design and construction efforts will finally start to pay off. A product fits flawlessly into its box or enclosure if the laminate layers are spaced properly. Filleting is a technique that allows manufacturers to divide the stress and multiply the pad's surface area. The designer must fillet the pads and land termination locations on their flexible circuits. Plating through holes is the best choice to make a solid solder junction.
Given that some flexible PCBs are harder than conventional PCBs, surface treatment is helpful in the manufacturing process to enhance the product's mechanical qualities. By employing plasma chemical vapor deposition, one can prepare the surface. Vacuum-assisted plasma deposition (PVD) is used for it. When utilized on an FR4 substrate (a specific flame-retardant epoxy), it increases dielectric strength and lengthens the product's lifespan.
In this case, a replacement plated through-hole can be made. Manufacturers prepare through-holes using copper.
The manufacturer can design small holes and a PCB architecture that is well-inclined to flexibility. Modern technology makes it possible to create holes as small as 30 micrometers.
After laminating the circuit layouts, manufacturers carry out the cutting and trimming process to precisely reduce the extra laminate material. It takes place before the final assembly of the product.
Manufacturers deal with cover layer and cover coating issues in this procedure. The cover serves as a solder mask and stops the solder from shorting out the traces. It guards against internal and external damage to the printed circuits. It stops circuits from becoming electrified externally.
Some typical cover layers utilized in the procedure are listed below:
Before the board can be put into service after the flexible circuit has been finished, some quality control is necessary. The following processes are carried out in this part.
Electrical test procedures are utilized on the circuit board to find shorts and openings. The test locates any short circuits or failed components that might occur during the production steps to guarantee product quality. After all procedures are finished and the product has undergone one last visual examination, electrical testing takes place. This testing ensures the effectiveness and dependability of the created goods. Additionally, it's crucial to check the boards’ connections, circuitry, and internal components for functionality. This check guarantees that there are no short circuits or bad contact points among the electronic components on the board.
Numerous flexible printed circuits are available. They typically follow a variety of configurations and standards. It's important to note that they are additionally divided into groups based on layers. Many flex circuit board types depend on configurations and layers.
These circuit boards have high-density connectors as one of their traits. Fundamentally, they produce a performance that is better than that of conventional flexible circuit boards. They have complex designs and construction, many components, and perform at a higher level as a result. Furthermore, high-density connectivity flexible printed circuit boards employ thinner substrates than more common substrates. By doing this, their performance and size are considerably enhanced.
The single-sided flex circuit is one of the fundamental varieties of flexible circuit boards based on layers. It is made of a single layer of polyimide film bonded to a thin copper sheet. Per precise design specifications, copper layers are etched to create the circuit pattern. In addition, the PCB is given a polyamide cover to protect it and enhance insulation.
These circuit boards are single-sided, as the name would imply; however, the copper sheet is accessible from both sides. It is a straightforward single-sided flex circuit, providing access to the conducting material from both sides. The single copper layer can be accessed twice thanks to specialized laser and processing methods.
The conductors on these specific circuit boards are double-layered, one on either side of the polyimide layer. On both sides of the substrate film, requirement-specific trace patterns can be generated using this type's two conductive layers. Copper-plated holes can be used to connect this.
This circuit combines double-sided and one-sided flexible circuits with intricate interconnections, shielding, and surface-mounted technologies in a multi-layered design. As a result, it is a good way to deal with inevitable crossovers, eliminate crosstalk, meet impedance specifications, add shielding, and have a high component density.
These particular printed circuit boards, as the name says, combine stiff and flexible printed circuit boards. The best qualities of stiff and flexible printed circuit boards are combined, and the resulting creation is connected using plated holes. This type is flexible in some applications but is ideal for higher components in inflexible areas. The benefit of hybrid circuits is that they enable designers to increase the functionality of circuits. It's crucial to emphasize how useful the stiff portions are for mounting various parts, such as connectors and chassis. On the other hand, flexible parts are utilized to guarantee vibration-free resistance.
By expanding the styles accessible for dash panels, “infotainment,” and other similar vehicle electronics, the automotive industry has benefited from flexible electronics. In addition, flexible electronics provide a wide variety of design options as opposed to having solely flat, boxy displays.
Additionally, flexible electronics enable more compact packaging that can fit into a small engine compartment as opposed to conventional rectangular prism-shaped boxes, which take up more room. Finally, it means that car designers don't have to think about the electronics package immediately. Instead, they can focus on making the car as fuel-efficient, comfortable, and aerodynamic as possible before trying to fit the electronics into the space they have.
Flexible circuits are utilized in computer peripherals on the moving print heads of printers to connect the signals to the moving arms and read/write heads of disk drives. Flexible circuits are used in consumer electronics like cameras, portable entertainment systems, calculators, and fitness trackers. Flexible printed circuits are used in manufacturing and medical equipment when numerous interconnections are required in a small box. Another notable example of flexible circuits is cellular phones.
With devices like fitness trackers, smartwatches, and tiny, real-time medical monitoring devices, flexible circuits are a big part of this growing industry.
Since every human body is slightly distinct in shape, flexible electronics are especially well adapted for this application. Instead of having to wear equipment too tightly to make sure it makes contact, sensors may now be able to conform to the skin's natural curves.
Flexible electronics research has recently concentrated on medical applications. In addition to step trackers and calorie counters, blood pressure monitors, oxygen monitors, glucose meters, and even blood alcohol meters are being developed using this technology.
A device's display screen that uses finger pressure for interaction is called a capacitive touch screen. Handheld capacitive touch screen devices generally link to networks or computers using an architecture that can...
A membrane keyboard is a type of keyboard technology found in many electronic gadgets and appliances. A keyboard, as we all know, is essential hardware that...
Membrane switches are a type of human-machine interface characterized by being constructed from several layers of plastic films or other flexible materials...
Die cutting is the mass fabrication of cut-out shapes by shearing a stock material such as paper and chipboard using tooling called a die. A die is a specialized tool used in manufacturing to cut or shape a material fitted into a press...
Kiss cutting is a method for cutting into a material where the upper layers are pierced, but the back layer is left intact. The term "kiss" refers to the way the blade touches the upper layers of the material and leaves a pattern or cut with a sufficient amount of force to leave an impression...
A name plate is a method for displaying the name of a person, logo, product, or mechanism and is made from a variety of materials to serve as a long term identifier...