Types of Metal Finishing
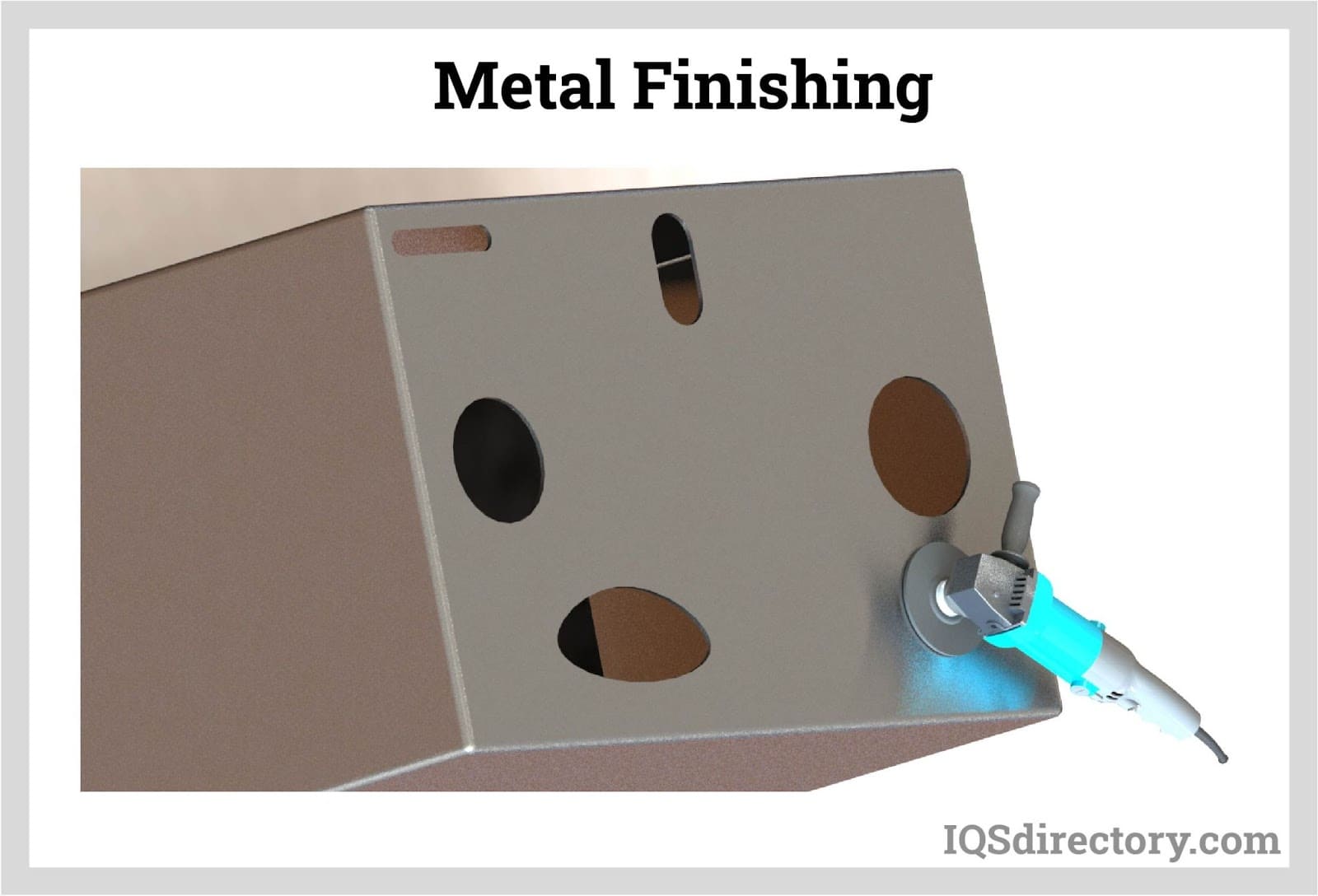
Metal finishing describes various procedures or processes that can be as simple as buffering to adding a special type of coat to the substrate. Included in the description of metal finishing are a number of cleaning...
Please fill out the following form to submit a Request for Quote to any of the following companies listed on
This article is an in depth study of electroless nickel plating and its uses.
You will learn:
And much more…
Electroless nickel plating (ENP) is a surface finishing process that places a nickel alloy coating using chemical reduction. In the process, nickel ions are reduced to metallic nickel using a chemical reduction agent such as sodium hydrophosphite. ENP is used to provide corrosion resistance to salt water, carbon dioxide, oxygen, and hydrogen sulfide. The process of electroless nickel plating creates an even, smooth, uniform thick coating across the substrate including slots, holes, and the inside walls of tubing.
The success of electroless plating is dependent on proper preparation of the surface since uneven, rough surfaces with burrs and cold shuts can cause either bonding issues or build up that would exacerbate the issue. The purpose of the process is to provide protection from wear, abrasion, corrosion, and enhancement to the performance of surfaces. It is a highly efficient and cost effective method for applying a strong, high quality finish.
For a successful plating process, there are a set of preparations that have to be completed to make a surface viable for coating. The texture and cleanliness of the surface as well as its pretreatment are critical and essential aspects of the process.
The surface to be plated must be cleaned thoroughly to remove any dirt, oil, or other contaminants that could interfere with adhesion of the electroless nickel layer. The surface is cleaned with different chemicals to remove grease, fingerprints, cooling oils, and other materials left over from the machining process.
After cleaning, the surface is activated by dipping it in an acidic solution, which removes any oxide layer and exposes a fresh metal surface. This is important for proper adhesion of the electroless nickel layer.
Depending on the substrate material, pre-treatment may be necessary to improve adhesion and corrosion resistance. The process can involve applying a zincate or palladium catalyst to the surface.
With electroless nickel plating, the substrate is then immersed in a plating solution that contains a source of nickel ions, a reducing agent, and other additives. The reducing agent reacts with the nickel ions to deposit a layer of nickel on the surface of the substrate.
After plating, the part may be rinsed and dried, and subjected to post-treatment to improve adhesion, corrosion resistance, and other properties. This can involve baking, passivation, or applying a topcoat or sealer.
There are numerous machines available to produce electroless nickel plating, which are important in today's society as they enable the deposition of uniform, corrosion-resistant, and wear-resistant nickel coatings on various substrates, providing enhanced protection, durability, and performance in industries such as automotive, aerospace, electronics, and manufacturing. Below, we discuss many leading brands of machines available in the United States and Canada used to perform electroless nickel plating, along with specific models and their unique abilities, features, or capabilities:
Features: SIFCO Applied Surface Concepts offers a range of equipment for electroless nickel plating, including tank systems and portable systems. SIFCO Process® Equipment allows for controlled and precise deposition of electroless nickel coatings on various substrates and features adjustable parameters for bath composition, temperature, and agitation for optimal plating results. This equipment incorporates advanced filtration and solution circulation systems for consistent plating quality. SIFCO Applied Surface Concepts' equipment is designed for ease of use, reliability, and productivity.
Features: The Techni EN-BM Series is a line of electroless nickel plating machines from Technic Inc. offering automated processing capabilities for consistent and repeatable plating results.
These machines feature advanced controls for precise control over plating parameters such as solution flow, temperature, and immersion time and incorporate filtration and agitation systems to maintain solution quality and uniform coating distribution. The Techni EN-BM Series supports easy maintenance and efficient production processes.
Features: The Miralloy Series by C. Uyemura is a range of electroless nickel plating equipment.
This series offers customizable solutions for various electroless nickel plating applications and requirements and features advanced control systems for accurate monitoring and adjustment of plating parameters. The Miralloy Series incorporates filtration and purification systems for consistent and high-quality plating results and supports efficient material utilization and cost-effective operations.
Features: Sharretts Plating Company provides custom-built electroless nickel plating systems tailored to specific customer needs. Their systems offer precise control over bath composition, temperature, and other process variables. Their equipment incorporates robust agitation systems for uniform coating deposition and features advanced control panels and monitoring systems for efficient operation and quality assurance. Sharretts Plating Company's custom systems are designed for durability, flexibility, and optimized plating performance.
Features: The Auto Catalyst 2000 Series by Metal Chem is an electroless nickel plating equipment line. It offers automated processing for high-volume electroless nickel plating applications. This equipment features advanced control systems for precise regulation of plating parameters and incorporates integrated filtration and solution management systems for consistent plating quality. The Auto Catalyst 2000 Series supports efficient production and streamlined operations.
Please note that specific model availability and features may vary, so it is advisable to contact the manufacturers or their authorized distributors for the most up-to-date information on the models that suit your requirements.
One of the attributes of nickel plating is the number of methods that can be used to complete the process. Each of the methods uses the name plating with each type having different uses and purposes. Regardless of the method, they are all intended to enhance and improve the properties of nickel and its resistance to corrosion and rust.
Electroplating is a process of depositing a metal coating onto a metal object using electrical current. In this process, the object to be plated is connected to the negative pole of a direct current power supply, while the metal to be plated is connected to the positive pole. An electrolyte solution containing ions of the metal to be plated is used as a medium for the metal ions to travel and adhere to the object. Unlike electroless plating, electroplating requires an electrical current and a conductive object to be plated.
Brush plating is a process of depositing a metal coating onto a localized area of a metal object using an electroplating solution and a brush. In this process, the brush is connected to the positive pole of a direct current power supply, while the metal to be plated is connected to the negative pole. The brush is then dipped into an electroplating solution containing ions of the metal to be plated, and the metal ions are brushed onto the localized area of the object. Brush plating is typically used for repairing localized areas of a metal object, rather than coating an entire object.
Hard chrome plating is a type of electroplating that involves depositing a thick layer of chromium onto a metal object to provide corrosion and wear resistance. Unlike electroless nickel plating, hard chrome plating requires an electrical current to be applied to the object being plated, and the plating process produces a hard, highly reflective surface that is highly resistant to wear and abrasion. However, the use of hexavalent chromium in the plating process has led to environmental and health concerns, and alternative plating methods are being developed.
Compared to these processes, electroless nickel plating does not require an electrical current to be applied to the object being plated, as the plating process relies on a chemical reduction reaction. This means that the coating can be applied uniformly to complex shapes and non-conductive materials. Additionally, electroless nickel plating can provide a uniform thickness of coating even in areas that are difficult to reach, and can also provide superior corrosion and wear resistance. Overall, however, the choice of plating process depends on the specific application and the desired properties of the coating.
Sulfamate nickel plating is an electro-plating process that uses nickel sulfamate to produce a purer and denser structure. The sulfamate method creates a high tensile strength machinable coating. It has a high level of corrosion resistance and is capable of performing at temperatures up to 1400o C (2552o F). A sulfamate nickel coating has a dull appearance and is used to repair worn parts.
Electroless nickel plating is a method for depositing a nickel alloy by chemical reduction, without the use of electric current. Most electroless nickel plating uses nickel phosphorus with a 2% to 14% phosphorus content. As the quantity of phosphorus increases, the plating material offers greater corrosion protection. The variations in electroless nickel plating are determined by the amount of phosphorus used.
This variation contains a high percentage of phosphorus in the plating solution and results in a coating with excellent corrosion resistance, wear resistance, and non-magnetic properties. It is commonly used in the aerospace, automotive, and electronics industries.
This variation contains a lower percentage of phosphorus than high phosphorus electroless nickel and results in a coating with good wear resistance and moderate corrosion resistance. It is commonly used in the automotive and electronics industries.
This variation contains a very low percentage of phosphorus and results in a coating with excellent brightness, solderability, and electrical conductivity. It is commonly used in the electronics industry.
These coatings contain nanoparticles or other materials dispersed within the plating solution, resulting in coatings with enhanced properties such as wear resistance, corrosion resistance, and electrical conductivity. These coatings are used in a variety of industries, including aerospace, automotive, and electronics.
This variation contains polytetrafluoroethylene (PTFE) particles dispersed within the plating solution and results in a coating with excellent non-stick and low-friction properties. It is commonly used in the food processing, medical, and semiconductor industries.
This variation contains boron nitride particles dispersed within the plating solution and results in a coating with excellent lubricity and wear resistance. It is commonly used in the aerospace, automotive, and electronics industries.
This variation contains tungsten carbide particles dispersed within the plating solution and results in a coating with excellent wear resistance and hardness. It is commonly used in the oil and gas, aerospace, and automotive industries.
This variation contains a proprietary mixture of nickel and other materials that create a black coating with a matte finish. It is commonly used in the firearms industry for aesthetic purposes, as well as in the electronics and automotive industries.
This variation contains silicon carbide particles dispersed within the plating solution and results in a coating with excellent wear resistance, hardness, and thermal conductivity. It is commonly used in the automotive, aerospace, and defense industries.
This variation involves plating a layer of electroless nickel followed by a layer of gold. This creates a coating with the corrosion resistance and electrical conductivity of electroless nickel, as well as the aesthetic appeal and corrosion resistance of gold. It is commonly used in the electronics and jewelry industries.
This variation involves plating a layer of electroless nickel followed by a layer of cobalt. This creates a coating with high hardness, wear resistance, and magnetic properties. It is commonly used in the electronics and automotive industries.
Each of these variations has specific applications based on their unique properties. For example, high phosphorus electroless nickel is often used in aerospace applications due to its excellent corrosion resistance, while electroless nickel-PTFE coatings are commonly used in the food processing industry due to their non-stick properties.
Electroless nickel plating on plastic is used to add wear protection, increase surface hardness, create electrical conductivity, or for improving a part’s appearance. Although the process began in the 1960s, it took a while to develop a process that created a strong enough bond between the nickel plating material and the plastic.
The problem for the plating process was resolved through the use of a chromic acid based etchant that was capable of preparing the surface of the plastic, which improved the plastic's adhesive properties. Once the process became viable, the automobile industry used electroless nickel plating of plastics to produce grilles, emblems, and light bezels.
The success of the plastic plating process is dependent on the proper molding of the plastic component. Molding relieves stress on a part and removes imperfections. For plastic to be plated, it has to be metallized to improve its adhesive properties, which is completed by electroless depositing of metal on the surface of the substrate.
Etchants, such as chromium trioxide or sulfuric acid, make it easier for the part to absorb liquids and produces microscopic holes for bonding of the deposited metal. After attempting different methods for treatment of the surface of the plastic material, it has been found that pre-etching improves the adhesive properties and relieves the surface layer strain of the plastic.
There are an endless number of benefits to the nickel plating process, which is the reason that it has been used for over 150 years. When nickel was originally discovered in the eighteenth century, it was named kupfernickel, which is German for “devil’s copper”. The strength, corrosion resistance, durability, and appearance of nickel made it popular.
It was in the middle of the first industrial revolution that nickel plating was invented by an Italian chemist. Near the end of the nineteenth century, a viable method for nickel plating was introduced and became the standard for the process.
Electroless nickel plating provides excellent corrosion resistance, protecting parts and components from rust and other types of corrosion. This is due to the formation of a protective layer on the surface of the part, which helps to prevent moisture and other corrosive substances from reaching the underlying metal.
Electroless nickel plating also provides excellent wear resistance, which helps to extend the life of parts and components that are subjected to high levels of wear and tear. The hardness and durability of the nickel coating make it resistant to scratches, abrasions, and other types of wear.
Electroless nickel plating allows for precise control over the thickness and uniformity of the coating, ensuring that parts and components are coated evenly and consistently. This helps to ensure that the coating provides optimal protection and performance.
Electroless nickel plating provides excellent adhesion to a wide range of materials, including metals, plastics, and ceramics. This means that parts and components can be coated without the need for additional primers or adhesives, saving time and reducing costs.
Electroless nickel plating can provide a smooth, uniform surface finish that is free of imperfections and defects. This can improve the appearance of parts and components, as well as improve their functionality and performance.
Electroless nickel plating provides excellent electrical conductivity, making it an ideal coating for electronic and telecommunications components. The coating can also be used to improve the conductivity of existing components, such as connectors and printed circuit boards.
Electroless nickel plating provides excellent resistance to many types of chemicals, making it an ideal coating for parts and components used in harsh chemical environments. This resistance helps to prevent damage to the part and prolongs its lifespan.
Electroless nickel plating can be engineered to have non-magnetic properties, making it an ideal coating for parts and components used in magnetic environments, such as MRI machines and other medical equipment.
Electroless nickel plating is a cost-effective solution for coating parts and components, especially when compared to other coating methods, such as electroplating or vacuum deposition. The process is relatively simple and requires minimal equipment, which helps to keep costs low.
These are just a few of the many benefits of electroless nickel plating. Other potential benefits may include improved heat resistance, increased hardness, and improved wear resistance at high temperatures.
Since its introduction, nickel electroless nickel plating has found a wide and expansive use in industrial applications. As the demand for more durable products has grown and customer awareness has improved, manufacturers have come to rely on electroless nickel plating to extend the life time of their products and enhance product appearance.
A manufacturer of aerospace components was experiencing corrosion and wear on aluminum parts used in landing gear systems. By using electroless nickel plating to provide a uniform, corrosion-resistant coating on the parts, the manufacturer was able to increase the lifespan of the components and reduce the need for costly replacements.
Electroless nickel plating is used extensively in the electronics industry to improve the performance and reliability of electronic components. One case study found that electroless nickel plating of printed circuit boards resulted in improved solderability and reduced defects, leading to improved product reliability and lower manufacturing costs.
An automotive parts supplier was experiencing corrosion and wear on cast iron brake components. By using electroless nickel plating to provide a uniform, wear-resistant coating on the parts, the supplier was able to improve the durability and reliability of the components, reducing the risk of costly recalls and warranty claims.
A medical device manufacturer was experiencing problems with the biocompatibility of stainless steel components used in implantable devices. By using electroless nickel plating to provide a biocompatible coating on the components, the manufacturer was able to improve the safety and effectiveness of the devices, reducing the risk of adverse reactions and improving patient outcomes.
Electroless nickel plating is used to coat equipment used in oil and gas exploration, such as drill bits and pipe connectors, to improve wear resistance and corrosion resistance. One case study found that electroless nickel plating of drill bits resulted in a significant increase in the bit's service life, leading to reduced downtime and lower maintenance costs.
Electroless nickel plating is used to coat a wide range of industrial and manufacturing equipment, such as molds, dies, and rollers, to improve wear resistance and corrosion resistance. One case study found that electroless nickel plating of a roller used in a paper mill resulted in improved wear resistance, leading to longer service life and reduced downtime.
Electroless nickel plating is used extensively in the chemical processing industry to improve the corrosion resistance of equipment used in harsh chemical environments. One case study found that electroless nickel plating of a heat exchanger resulted in improved corrosion resistance, leading to longer service life and reduced maintenance costs.
Electroless nickel plating is used to coat equipment used in food processing, such as blades and mixing bowls, to improve wear resistance and corrosion resistance. One case study found that electroless nickel plating of a mixing bowl used in a food processing plant resulted in improved wear resistance and reduced contamination, leading to improved product quality and reduced cleaning time.
Electroless nickel plating is used extensively in military and defense applications, such as firearms, to improve wear resistance and corrosion resistance. One case study found that electroless nickel plating of a firearm resulted in improved wear resistance and reduced friction, leading to improved accuracy and reliability.
These examples demonstrate the versatility and effectiveness of electroless nickel plating as a surface finishing technology. By providing a uniform, corrosion-resistant coating on a variety of substrates, electroless nickel plating can help to improve the performance and durability of a wide range of products.
The applications for parts that have been electroless nickel plated has expanded over the full spectrum of applications from the production of airplanes and automobiles to medical devices and dental implants. The strength and durability of metals protected by electroless nickel plating is constantly extending its use into new and more dynamic applications.
Electroless nickel plating is used in these industries to improve the wear resistance and corrosion resistance of engine components, such as pistons, valve bodies, and fuel injectors. It is also used to coat critical components of aircraft engines and landing gear to prevent corrosion and wear.
Electroless nickel plating is used to protect electronic components from corrosion and wear, as well as to enhance their electrical conductivity. It is commonly used to coat connectors, printed circuit boards, and microwave components.
Electroless nickel plating is used in medical and dental equipment to improve the biocompatibility of implants and instruments, as well as to provide a smooth and uniform surface finish. It is commonly used to coat surgical instruments, orthopedic implants, and dental tools.
Electroless nickel plating is used in the oil and gas industry to protect equipment from corrosion and wear in harsh environments, such as offshore drilling platforms and pipelines. It is commonly used to coat valves, pumps, and drill bits.
Electroless nickel plating is used in various industrial and manufacturing applications to improve the wear resistance and corrosion resistance of machinery and equipment. It is commonly used to coat gears, bearings, molds, and dies.
Electroless nickel plating is used to coat equipment used in chemical processing, such as tanks, valves, and pumps, to protect against corrosion and wear caused by harsh chemicals and high temperatures.
Electroless nickel plating is used to coat food processing equipment to prevent corrosion and wear caused by acidic and salty environments. It is commonly used to coat mixing blades, choppers, and conveyors.
Electroless nickel plating is used in military and defense applications to improve the wear resistance and corrosion resistance of equipment used in harsh environments, such as submarines, tanks, and aircraft.
Electroless nickel plating is used to coat mining equipment, such as drill bits and cutting tools, to improve their wear resistance and corrosion resistance in harsh mining environments.
Electroless nickel plating is used in renewable energy applications, such as solar and wind power, to coat components exposed to harsh outdoor environments. It is commonly used to coat connectors, gearboxes, and bearings.
Electroless nickel plating is used in the printing industry to coat printing rollers, gears, and other components to prevent wear and extend the life of the equipment.
Electroless nickel plating is used in the textile industry to coat parts of weaving and spinning machinery, as well as to coat parts of dyeing machines, to prevent wear and corrosion.
Electroless nickel plating is used on fasteners used in the aerospace industry to prevent corrosion and improve the durability of the parts.
Electroless nickel plating is used to coat firearms to protect them from rust and corrosion and to improve the appearance of the gun.
Electroless nickel plating is used on certain musical instruments, such as flutes and saxophones, to prevent corrosion and improve the sound quality.
Electroless nickel plating is used in the jewelry industry to coat pieces of jewelry, such as bracelets and rings, to improve their resistance to wear and corrosion.
Electroless nickel plating is used in the marine industry to coat propellers, valves, and other components that are exposed to saltwater and other harsh marine environments.
Electroless nickel plating can be used in the automotive industry for decorative purposes, such as coating wheels, trim, and other parts to improve their appearance.
Electroless nickel plating is a chemical process that requires strict oversight to ensure the safety of workers and the community. As regulations regarding pollution are ever increasing, more scrutiny is being given to all of the plating processes, especially those involving chemicals. In the United States, electroless nickel plating is subject to various laws and regulations, including those related to environmental protection and worker safety.
The Clean Water Act regulates the discharge of pollutants into navigable waters, including those that may be used in electroless nickel plating processes. This law is enforced by the Environmental Protection Agency (EPA).
The Resource Conservation and Recovery Act regulates the management and disposal of hazardous waste, including those generated by electroless nickel plating processes. This law is also enforced by the EPA.
OSHA regulations set standards for workplace safety, including those related to the handling of hazardous chemicals used in electroless nickel plating processes.
The Toxic Substances Control Act regulates the manufacture, import, and processing of chemicals, including those used in electroless nickel plating processes. This law is enforced by the EPA.
In addition to these national laws and regulations, there may be state or local regulations that apply to the use of electroless nickel plating. For example, some states have additional regulations related to hazardous waste management or workplace safety.
Internationally, there are also several organizations that may have authority over companies performing the process of electroless nickel plating elsewhere, including:
REACH (Registration, Evaluation, Authorization and Restriction of Chemicals) is a regulation of the European Union that regulates the use of chemicals in industry, including those used in electroless nickel plating processes.
The IARC is an intergovernmental agency that is part of the World Health Organization. It evaluates the carcinogenicity of various substances, including nickel and other chemicals used in electroless nickel plating.
The IEC is an international standards organization that sets standards for the electrical and electronics industries. It has developed standards for the use of electroless nickel plating in electronics applications.
It's important for companies performing their electroless nickel plating overseas to be aware of these laws and regulations and to comply with them to ensure the safety of workers and the environment.
Any chemical process has shortcomings that can be harmful and have an impact on the environment. Additionally, these processes tend to be expensive due to the types of chemicals used to initiate and complete the process. Each of these factors need to be considered by choosing electroless nickel plating as a manufacturing process.
Some of the chemicals used in the electroless nickel plating process, such as nickel and sodium hypophosphite, can be hazardous to human health if not handled properly. Proper safety precautions, such as wearing protective gear and working in a well-ventilated area, must be taken to prevent exposure to these chemicals.
The chemicals used in the electroless nickel plating process can also have negative impacts on the environment if not disposed of properly. Proper disposal methods must be used to prevent contamination of soil and water sources.
While electroless nickel plating is generally more cost-effective than other coating methods, such as electroplating or vacuum deposition, it can still be more expensive than other surface treatment options, such as painting or powder coating.
Electroless nickel plating can only be applied to a limited thickness, typically up to around 0.003 inches. If a thicker coating is required, other coating methods may need to be used.
Electroless nickel plating is generally only suitable for use on certain types of substrates, such as metals and some plastics. It may not be suitable for use on other materials, such as ceramics or glass.
Electroless nickel plating is a complex process that requires careful control of the plating solution and other factors, such as temperature and pH. This can make the process more difficult to implement than other coating methods, especially for smaller businesses with limited resources.
Proper surface preparation is crucial to the success of the electroless nickel plating process. Any contaminants or imperfections on the surface of the part can affect the adhesion and quality of the coating.
The future of electroless nickel plating appears promising. To begin with, as the technology continues to develop, new applications are constantly being discovered. Additionally, there are many favorable trends related to electroless nickel plating hinting to its importance in the future.
As industries such as aerospace, automotive, and defense continue to require higher levels of wear resistance in their components, electroless nickel plating may see increased demand due to its ability to improve wear resistance.
With the rise of additive manufacturing techniques such as 3D printing, there is a need for surface finishing processes that can coat complex geometries. Electroless nickel plating has the potential to be an ideal solution for this need.
The medical device industry is one of the fastest growing industries globally, and electroless nickel plating has already shown its potential in this area. With increasing demand for biocompatible coatings and the need for antimicrobial properties, electroless nickel plating may see further growth in this industry.
Researchers continue to develop new electroless nickel alloys with improved properties such as increased hardness, wear resistance, and corrosion resistance. As these alloys become more widely available, electroless nickel plating may see increased use in a wider range of applications.
Due to increasing environmental regulations, there is a push towards using more environmentally friendly coatings and plating processes. Electroless nickel plating, with its lower environmental impact compared to other plating processes, may see increased demand in industries that are sensitive to environmental concerns.
Renewable energy sources such as solar and wind power require a range of specialized components, many of which require coatings that provide high levels of wear and corrosion resistance. Electroless nickel plating has already been shown to be an effective coating for components used in wind turbines, and it has the potential to play a larger role in the renewable energy sector as the industry continues to grow.
As the field of nanotechnology continues to advance, there is a need for surface finishing techniques that can coat and protect structures at the nanoscale level. Electroless nickel plating has shown promise in this area, as it can be used to coat and protect nanomaterials, nanoparticles, and other structures at the nanoscale level. It may be used to provide additional functionality such as electrical conductivity, catalytic activity, and biocompatibility.
The biotechnology industry requires specialized coatings for a range of medical devices, such as orthopedic implants and cardiovascular stents. These coatings need to be biocompatible, antimicrobial, and wear-resistant. Electroless nickel plating has already been shown to be an effective coating for some medical devices, and it may see increased use in this industry as demand for biocompatible and antimicrobial coatings continues to grow.
Overall, electroless nickel plating may play an important role in a wide range of industries as new technologies emerge and new applications for the process are discovered. Its ability to provide wear and corrosion resistance, biocompatibility, and other important properties make it a versatile and useful technology for a range of applications.