Air Cooled Chillers
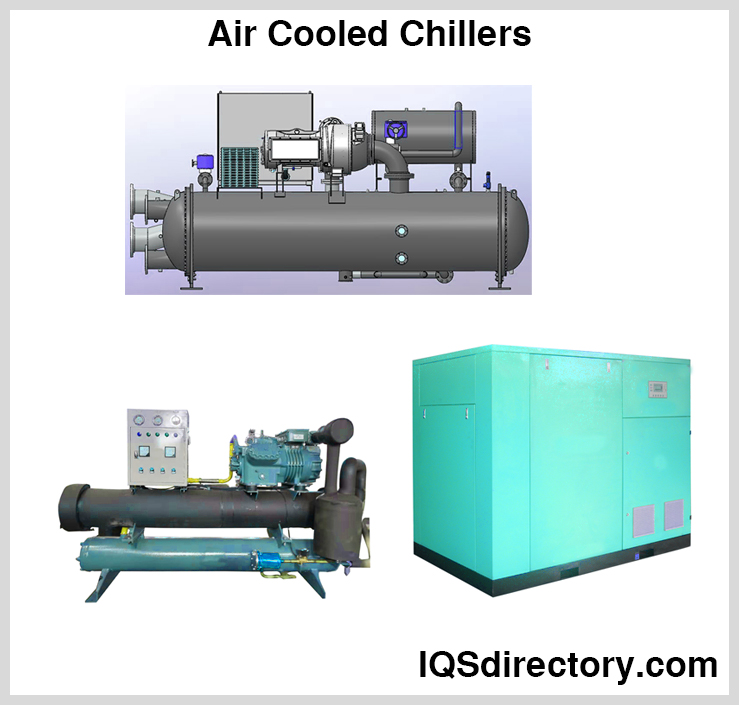
Air cooled chillers are refrigeration systems that cool fluids and work in tandem with the air handler system of a facility. Air cooled chillers are types of chillers that rely on the use of fans to reject heat outside the...
Please fill out the following form to submit a Request for Quote to any of the following companies listed on
Here is the most complete guide on the internet about
You will learn:
This article takes an in depth look at glycol chillers.
You will learn more about topics such as:
A glycol chiller is an industrial chiller system that uses a percentage of glycol mixed with water to create extremely low temperatures far beyond the freezing point of water. The two types of glycol are ethylene glycol based or propylene glycol based. The antifreeze nature of glycol ensures that the coolant remains in a fluid state in order to reach its low cooling points. In most chiller units, an ethylene or propylene glycol mixture with water is at a ratio of 60% to 40%.
By increasing the percentage of glycol, the antifreeze properties of the mixture are significantly improved, which is useful when rapid cooling is necessary. Glycol mixtures have enhanced heat transfer characteristics, a major part of the cooling process, which are useful when specific temperatures are important to the success of a production process.
Glycol industrial chillers send a glycol water coolant mixture through heat exchanger piping to have the heat in the coolant absorbed from industrial processes. The absorbed heat in the coolant passes through the glycol industrial chiller where it is cooled and sent out to absorb heat from the various industrial processes. The wide use of glycol industrial chillers is due to their consistency when protecting frozen foods and the production of food products.
Glycol is an organic compound belonging to the alcohol family and is referred to as antifreeze. The most significant aspect of glycol is its excellent heat transfer properties, making it ideal for cooling and chilling applications. Glycol mixtures used in industrial chillers are capable of removing large amounts of heat quickly. Heat is a normal byproduct of chemical reactions and has to be removed rapidly in order to maintain the stability of the reaction. In such instances, glycol industrial chillers are used due to their quick reaction and excellent heat transfer properties.
There are two types of glycol chillers, which are ethylene and propylene. Though both are glycol compounds, they cannot be mixed because they have different fluid, toxicity, and heat transfer properties that would prevent a system from working properly.
Ethylene glycol is an antifreeze used in industrial cooling units to protect against freezing and as a rust inhibitor. The percentage of ethylene glycol used in a glycol and water mixture is determined by the lowest outdoor ambient temperature and the temperature of the application loop. Ethylene glycol chillers are used for industrial applications because of its high flashpoint of 240o F. Due to its toxicity, ethylene glycol is not approved for food processing.
Propylene glycol has low toxicity and is a food grade antifreeze. It is safer than ethylene glycol and is biodegradable. Propylene chillers are used in the food industry or refrigeration systems where people may come in contact with it. Though propylene is a synthetic liquid, it is easily absorbed by water. The Food and Drug Administration has classified propylene glycol as being safe and can be used to absorb water and maintain moisture control for medicines and cosmetics as well as food.
Portable glycol chillers are small, compact, and self contained, with all of their components included in the unit. They have a capacity of 1 to 40 tons of cooling and are ideal for small loads or where special fluids, flows, pressure, or temperature are necessary. Due to the compact size of portable glycol industrial chillers, they can be used for test applications or positioned for temporary use.
A modular glycol industrial chiller system includes the use of multiple chillers linked together to form a complete chilling system. This form of glycol industrial chiller system is flexible with the ability to add extra chillers as needed. The design of the system guarantees constant cooling even during maintenance cycles.
Included in the features of modular glycol industrial chillers are oversized processing pumps and oversized glycol reservoirs that have extra ports to extend and add to the system. As new modules are phased in, the chilling system grows substantially. The configuration of modular chillers is commonly used for industries that cannot afford downtime since such downtime affects the quality of their products. Modular systems with multiple chillers make it possible to have a second or third chiller activate when one chiller malfunctions.
A special feature of modular glycol industrial chiller systems is their ability to cycle down and run only a portion of the system during low heat loads. This is a cost saving feature that provides greater control over the system. Although there is a single term in regard to modular glycol industrial chillers, they are available in several designs and configurations to meet the needs of various industrial requirements.
There are important factors that have to be considered when making the choice to use a glycol industrial chiller. The uniqueness of their performance and levels of efficiency they can achieve has made them a very popular source for cooling essential production processes.
Process cooling systems are essential to industrial applications since heat energy builds as materials are blended and mixed or where chemicals are combined. The use of a cooling system assists in holding materials at a stable temperature, which allows other manufacturing operations to continue.
A major benefit of a glycol industrial chiller is its ability to precisely control temperatures for cooling. The use of glycol in a chilling system prevents pipes from freezing because glycol is a form of antifreeze. Both types of glycol, ethylene and propylene, can be used in cooling systems, but not together since they have different properties.
Glycol is an excellent additive to a cooling system due to how well it interacts with water. As everyone knows, the freezing point of water is 32o F, which can obstruct or interfere with a cooling system or cause pipes to freeze. The addition of glycol dramatically lowers the freezing point of water to – 60o F and increases the operative temperature of the cooling system.
The lower temperatures achieved through the use of glycol allows a cooling system to remain cooled and chilled longer than is possible using water alone. The additional benefits of glycol have made it an essential part of modern cooling systems.
Glycol industrial chillers are closed looped systems where the coolant constantly circulates and does not come in contact with the environment. Since the system is closed, the glycol coolant remains clean, uncontaminated, and does not cause fouling or scaling, and water loss from evaporation is eliminated. A closed loop system is exceptionally efficient and long lasting.
Closed loop systems require less pumping power, which reduces the cost of installation. The glycol coolant is pumped through tubing connected to the input and output sections of the chiller.
The heat exchanger allows the transfer of heat between the glycol water coolant and the refrigerant gas. It uses the flowing glycol to collect heat from the refrigerant and move the heat away from the area being cooled. The heat exchanger and glycol pipes are small since glycol is capable of removing more heat.
The low viscosity of glycol is the main reason that high powered pumps are not necessary to operate a glycol chiller. Pumps for glycol systems are small but are an essential part of the system. They help to circulate the glycol and assist in maintaining a constant cool temperature. Depending on the design of the chiller unit and the type of application, the cooling system may require more than one pump.
The compressor takes low pressure and temperature refrigerant and compresses it into high pressure and temperature. There are several different types of compressors that a glycol industrial chiller can use with ones designed to fit the needs of the chiller and the applications for which it was developed. The different types of compressors include positive displacement, screw, diaphragm, screw, diaphragm, rotary, and centrifugal.
The condenser collects the unwanted heat from the chiller from the compressor that it has gotten from the evaporator. The heat is then transferred into water that circulates around the condenser. The heat is then released into the ambient air.
Water is an essential part of glycol systems since glycol has to be mixed with water for the system to work properly. Major factors in the overall process are the type and amount of water, which can vary. Though city water can be used in a glycol industrial chiller, it is not recommended.
Manufacturers recommend the use of distilled or reverse osmosis water to mix with glycol. Deionized water can initiate the chiller process but should be replaced since it can attack metals in the chiller and damage other components. Reverse osmosis or hyperfiltration removes contaminants through the use of pressure that forces water through a semipermeable membrane. The process can be seen below.
There are many factors to consider when determining the ratio of water to glycol. Primary of the considerations is the location of the chiller and the ambient temperature of the environment. Indoor use of chillers has little chance of freezing and requires less glycol.
When a system has a very low operating temperature, such as below 20°F, the mixture of glycol to water should approximate that of an outdoor chiller system, which is the saturated suction temperature in the evaporator or 10o F below the setpoint temperature of the chiller.
Calculating the ratio of water to glycol is dependent on the coldest temperature the glycol system will reach during operation. The proper ratio is very critical since adding too much glycol can lead to inefficiency while too little can cause the system to freeze up or burst pipes.
After the proper type of water is chosen and glycol, the chart below offers an approximate percentage of water to glycol for outdoor and indoor glycol chiller applications.
Glycol Chiller Applications | |||
---|---|---|---|
Applications | Percent of Water to Glycol | Freeze Protection | Burst Protection |
Indoor | 30% to 70% | 5°F or -15°C | -20°F / -29°C |
Outdoor | 50% to 50% | -35°F or -37°C | -60°F / -60°C |
Maintaining clean water and proper glycol content are critical factors in regard to the life of the cooling system as well as an important part of reducing downtime. To keep the water and glycol free of suspended solids, it is important to have a filtration system as part of the chiller.
Automatic self cleaning screen filters provide a barrier to suspended solids and require very little energy though they lead to a certain amount of coolant loss.
A common filtration method for glycol chillers is a side stream filter that removes a portion of the fluid flow and filters out solids and contaminants before returning the filtered fluids to the system. Side stream filtration helps control suspended solids and assists in maintaining the integrity of the glycol and water mixture.
Glycol industrial chillers have been widely accepted as one of the most efficient cooling systems due to the precision control they offer, and the low temperatures the systems can achieve. The most common use for glycol industrial chillers is in the production of beverages, where the cooling process has to be at a specific level to ensure the quality of the final product.
Keeping products at a consistently low temperature can be expensive and require regularly scheduled monitoring. The introduction of glycol systems in their varied sizes has made it easier and less expensive to produce high quality products without the need for continually checking the cooling process.
One of the common concerns to refrigeration systems is the fear of leaks that can raise temperatures and destroy crops. This particular factor is non-existent with glycol chillers since glycol has inhibitors that make a system resistant to corrosion, scales, and rust, which can cause leaks and damage pipes.
Propylene or ethylene act as anti-refrigerants that prevent freezing inside coils. The glycol and water combination helps protect the chiller from the build up of algae and bacteria.
Adding to the safety features of a glycol chiller is its low maintenance. Glycol chillers can store products and keep them cool for long hours without the need for any form of costly maintenance. The system can last for years without falling apart or requiring maintenance while providing exceptional performance.
Glycol industrial chiller pipes can run longer distances and provide service from a single cooler and pump package to several processing locations. They come in several varieties with PVC80 being very common. The key to glycol industrial chiller piping is their installation, which can be reverse return to balance the flow across the pieces of equipment. With reverse return, the cooling medium travels the same distance to and from the chiller. The size of piping depends on the flow required by equipment with pressure drop and velocity being factors to be considered.
The economizer feature on glycol industrial chillers is designed to take advantage of cold air. When the ambient temperature is correct for the chiller, a control switch turns off the compressor and uses the chilled environmental air for cooling purposes. The economizer feature blends enough of the ambient air to meet the thermostats setpoint. This is a money saving device built into glycol industrial chillers to increase their efficiency.
Glycol industrial chillers operate at temperatures far below the freezing point of water, which can be controlled by altering the glycol mixture percentages. A 10% ethylene glycol mixture will freeze at 26°F, while a 60% mixture has a freezing temperature of - 60° F. The antifreeze properties of glycol ensures that the coolant remains in a continuous fluid condition.
A glycol industrial chiller unit can cost less than half of the cost of a self contained refrigeration unit since it involves purchasing a single glycol chiller instead of several separate ones. The chiller compressor cools the glycol and water without the need for other components or mechanisms.
Over the years, cooling systems have significantly improved by eliminating outdated and harmful cooling methods. The chiller manufacturing industry has become more environmentally conscious and developed cooling solutions that are compliant with environmental agency requirements.
The vast improvements in cooling systems have increased their use by industry and provided cooling solutions for applications where such solutions were previously unavailable. Part of the advancements in cooling technology is due to the use of glycol as an additive to cooling systems.
With the growing restrictions regarding environmental safety, grocery stores require chilling units that comply with all of the eco-requirements but offer long lasting and durable solutions. Propylene glycol industrial chillers are food grade and ideal for frozen food chiller cases. They are technically engineered to remove heat but be strong enough to endure constant use.
Keeping fresh fruits and vegetables fresh is a critical aspect of the produce packing industry. Failures, downtimes, and maintenance delays can completely destroy a shipment of products. As with grocery stores, cooling units must meet the requirements of food grade stipulations but be strong enough to endure their constant use. The operation and engineering of propylene glycol industrial chillers is ideal to meet all the requirements of the produce shipping industry.
One of the areas where glycol industrial chillers are used the most is the brewing industry, which requires precisely controlled temperatures and conditions. The maintenance of temperature has to be consistent since any fluctuations can have extremely negative effects on the quality of the final product. It is for these reasons that propylene glycol industrial chillers help to precisely regulate and maintain container temperatures.
The engineering of an outdoor ice rink in a warm climate can be a challenge. Since glycol chillers can be chilled below the freezing water limit, it is possible to install an outdoor ice rink in a warm climate. Mats are placed below the surface of the ice rink and pumped full of glycol. Water is sprayed over the mats, which freezes when it makes contact with the mats.
As with breweries, the quality of dairy products relies a great deal on the proficiency of a cooling system since incompetent or inappropriate systems can lead to bacterial growth. The dairy manufacturing process has to have consistent temperature control throughout the process. Milk is pumped directly from cows into cooling units, which store the milk until it is further processed.
Every step of the process demands that the raw milk be kept at a consistent temperature to avoid spoilage and the growth of bacteria.
The few uses for glycol chillers described above are only a small sampling of their many uses. Any industry that has heat as a part of their process will depend on glycol chillers to remove and dissipate the heat.
There are certain actions and factors that need to be avoided to keep a glycol chiller performing at its highest capacity. Neglecting to follow certain protocols can lead to damage to the chiller or complete shutdown. Glycol chiller manufacturers, during installation, make clients aware of these factors such that the product offers optimum performance.
Automotive antifreeze has the same chemical content as glycol coolants for chillers but is formulated differently. The use of automobile antifreeze can reduce flow rates, pressure problems, and a significant reduction in heat transfer.
Inhibited glycol has ingredients that protect against corrosion, scale, and rust, which is not present in uninhibited glycol. Glycol must be used at 25% combinations or higher to have sufficient amounts of the inhibitors present in the mixture.
All manufacturers will tell you never to mix ethylene and propylene glycol or different brands of glycol. The incompatibility between the various formulas can lead to clogged filters, strainers, pumps, and problems with transfer properties.
States, counties, and cities have different regulations regarding the use of glycol and antifreeze to protect water tables, drainage, and disposal of fluids. Before installing a glycol chiller, it is important to contact local authorities to ensure compliance with municipal regulations.
The ratio of glycol to water has to be continually checked and tested to ensure that the percentages are being maintained and corrosion issues are not present.
Glycol chillers work best if distilled or reverse osmosis purified water is used since city water has contaminants that can inhibit combining glycol with the water. Other forms of pure water include demineralized water, which removes the unpredictability of city and municipal water.
Air cooled chillers are refrigeration systems that cool fluids and work in tandem with the air handler system of a facility. Air cooled chillers are types of chillers that rely on the use of fans to reject heat outside the...
A chiller is a cooling mechanism designed to produce fluids that can lower temperatures by removing heat from the fluid. The type and use of a chiller depends on the required temperature and kind of refrigerant, which can be a liquid or a gas...
Laser cooling is a multi-process that includes a number of techniques in which atomic and molecular samples are cooled down to a temperature near absolute zero. These techniques depend on...
A water chiller, or chilled water system, is a type of refrigeration system which uses water as a secondary refrigerant. They are used for larger, more complex, heating, ventilating, air conditioning, and refrigeration (HVACR) applications...
Cooling towers are specialized heat exchangers that remove heat from water mainly by means of latent heat loss from evaporation while coming into contact with an airstream. Aside from evaporative cooling, water is also cooled by sensible heat transfer due to the temperature difference between air and water...
Heat exchangers are pieces of equipment used to transfer heat between two or more fluids. This process usually involves abundant working or utility media such as water or air that rejects or absorbs heat from a more valuable fluid such as crude oil, petrochemical feedstocks, and fluidized products...
Open loop cooling tower makes use of direct contact with the air in order to cool down the water. It is essentially a heat exchanger. In these types of cooling towers, there is the partial heat transfer due to heat exchange between...
A plate heat exchanger (PHE) is a compact type of heat exchanger that utilizes a series of thin metal plates to transfer heat from one fluid to the other. These fluids are typically at different temperatures...
A shell and tube heat exchanger (STHE) is a type of heat exchanging device constructed using a large cylindrical enclosure, or shell, that has bundles of perfectly spaced tubing compacted in its interior. Heat exchanging is the transfer of heat from one substance or medium to a similar substance or medium...