Chemical Milling
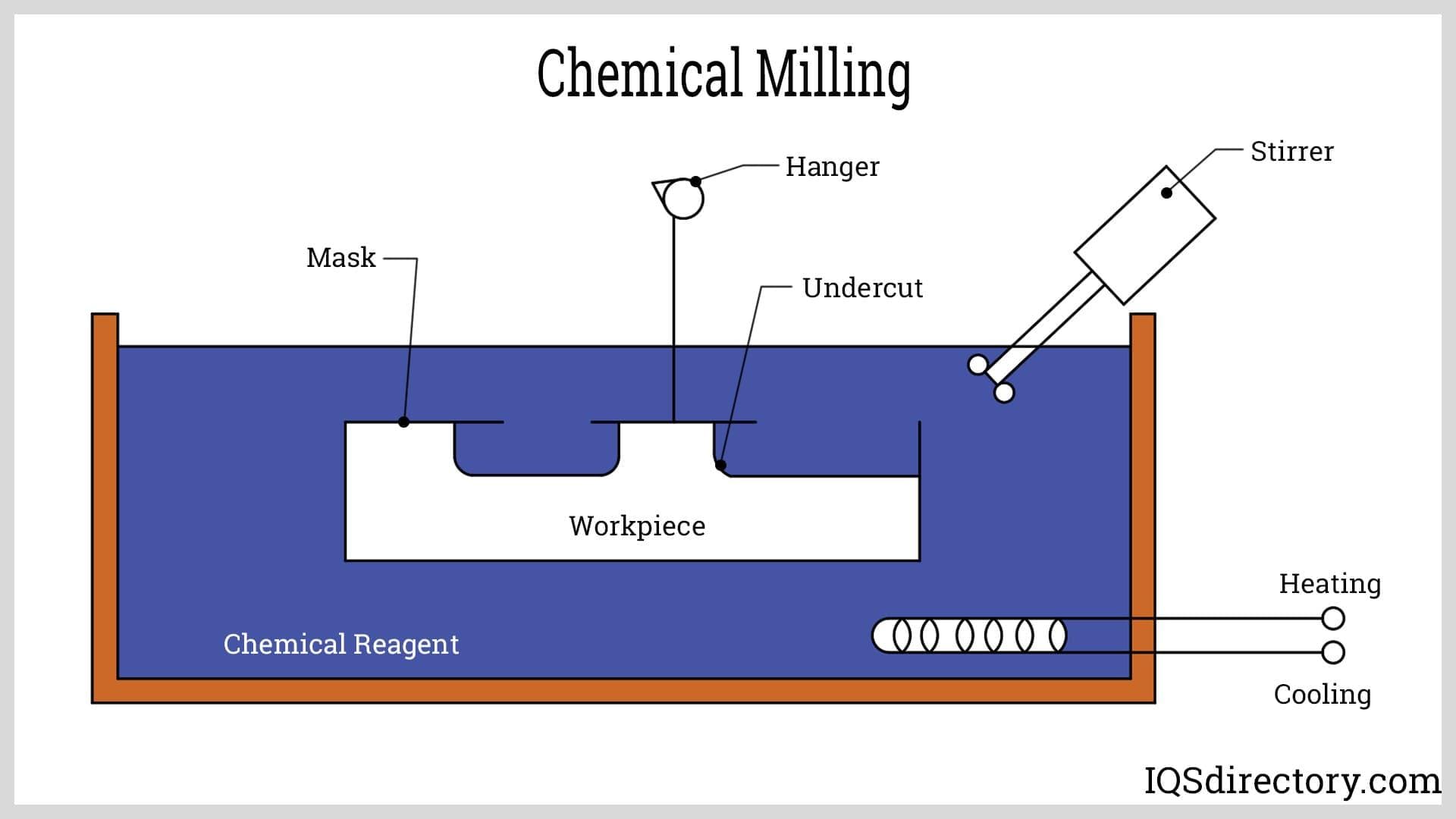
Chemical milling is a subtractive machining process that removes material from a workpiece to achieve a desired shape. Unlike aggressive milling methods that depend on sharp tools to produce a design, chemical...
Please fill out the following form to submit a Request for Quote to any of the following companies listed on
This article will take an in-depth look at acid etching.
The article will bring more detail on topics such as:
This chapter will discuss what acid etching is, its uses, components, and procedure.
Acid etching is a chemical process where a strong acid, known as an etchant, is applied to the surface of a piece of metal to remove a portion of the metal’s surface to create an image, design, or component.
Unlike other processes, acid etching does not change the properties of a metal. The grain structure and strength of a metal remain intact after the etching process. Acid etching can be used on every type of metal and is ideal for thin materials that could be damaged by other processes.
Acid etching is a sheet metalworking technology that utilizes acid etchants for the machining of complex, highly accurate precision metal components. Acid etching is used to reproduce works of art with high quality. Initially, the process of acid etching was used to get the work of an artist into the hands of as many people as possible.
In this process, the engraver takes a plate of copper or mild steel. The artist covers the entire surface of the plate with a waxy substance called ground that is resistant to the selected acids. Using a variety of tools, the engraver will then reproduce the original work of art by engraving the image into the waxy ground. The plate will be submerged in a bath containing the mordant. After a prescribed time, the plate is removed and rinsed off, and the ground is removed. This will leave an image that is an exact copy of the engraver’s work. This process is a very skilled one; it takes time and money to use this way of producing works of art.
Acid etching works equally well on materials such as stainless steel profiles, sheets and plates, and other metals like aluminum and brass. The surface of the stainless steel left behind is different in texture (matte) from the unetched stainless steel. This means that acid etching produces a non-slip grip on the stainless steel surface, making hand tools safer. Acid etching is also used to create patterns for decoration, contrasting surfaces, or text.
Various types of acids can be utilized in the etching of steel and stainless steel, including nitric acid, hydrochloric acid, or sulphuric acid. All of these acids require careful handling; they are capable of dissolving stainless steel as well as fingers.
Chemicals that form acid when mixed with water, like ferric (iron) chloride or copper sulfate, can also be utilized as etching chemicals. These chemical compounds work faster than acids. The rate at which the steel will be etched is generally determined by the acid’s strength. The stronger the acid, the faster the etching process.
Etching acids and chemical compounds can be obtained from online chemical supply stores.
The type of metal etched affects the acid etching process because some metals etch quicker than others. For example, steels and nickel take much more time to etch than softer metals like bronze, copper, and aluminum.
Any metal can be acid etched, with attractive metals being the most popular because of their properties and characteristics. Metals that are commonly used in acid etching are shown below:
Aluminum – this metal is strong, lightweight, and possesses an excellent weight ratio as well as corrosion resistance.
Bronze – this metal is ductile, harder than copper, stiff, and firm.
This chapter will discuss the different types of acid etching on different metals. It will also discuss examples of procedures taken in executing the different types of acid etching.
The following procedure was followed during the process of acid etching a steel folding knife.
The most important step in this whole process is preparation. If there is no proper preparation, the results will be poor and frustrating.
No acid must get on the scales, washers, or liners. Store all the little screws in a safe container or magnetic tray. If you don’t feel comfortable with taking the knife apart, then make sure that you mask off any part of the knife that you would not like to get the acid on.
This is done to provide a clean surface for the etch resist to adhere to. Avoid touching the blade with bare hands after finishing the cleaning process. The oil from your fingers will damage the etch.
Create a pattern on the steel with the etch resist. The basic idea is to create a barrier that prevents the acid from reaching the steel. This will leave a pattern after the removal of the etch resistance. Every part of the metal that is exposed will be darkened and marked by the acid. If caution is not taken, too much metal will be eaten away, ruining the knife.
Using a bright color nail polish helps by making it clear where the etch resistance has been applied. You can experiment with sharpie markers, nail polish, vinyl, electrical tape, stickers, and different stenciling materials. If you need to black out the whole blade, then use very little etch resist on only the pivot and lock face. If you need only a small logo, you must protect most parts of the blade with tape or even nail polish. If you are etching a folding knife, you will want to protect the detent, pivot, and lock face area in order to avoid messing with the tolerances of those areas. Similarly, if you are etching liners and scales, protect the ball detent and the same pivot area.
The first step before mixing the etch ratio is always to put on protective gloves. Then, mix the ferric chloride with distilled water in a 1:1 ratio; i.e., pour the same quantity of water and acid into the plastic container. There is no need to go full strength to obtain good results. As you are filling the container, leave some space to allow for the displacement of the blade.
The best practice is always adding acid to water to avoid dramatic chemical reactions or splashed acid. Using a container with a good lid is important, especially some sort of snap-on lid. A screw lid may work less effectively if the dried acid solution is caught in the threads, and a metal container will be ruined when the acid eats through the metal. A small amount of this acid mixture goes a long way toward etching, but it depends on the type of metal and how much material is being stripped away.
Before you start etching, always make sure you are in a ventilated area. The acid will cause a chemical reaction that will produce a vapor by-product. Safe locations for this procedure can be outdoors or under a vent or stove hood.
The two processes of acid etching are explained below:
Short dips together with quick rinses under the tap can give the best etching results because these short dips help to provide better control over the end result. Use a paper clip or dental floss to dip the knife into the acid, repeating this process until the desired results are obtained. The recommended timeline is 10-60 seconds in the bath, 10 seconds rinsing under the tap, 10 seconds in the air, and repeat. This process will also preserve any of the laser factory markings that are on the blade.
It is also recommended to move the blade around in the acid, which helps by ensuring a consistent etch with less pitting. Some sophisticated systems can agitate the acid with fish tank aerators.
Other processes use only one long bath in the acid as opposed to short dips. This eats away the metal and makes it difficult to see when the limit has been reached. The recommended length of these baths is 10 minutes.
Caution should also be taken with fingerprints; try not to touch the blade with your bare hands when rinsing it, as this may leave a fingerprint mark on the blade’s surface.
This works better when you want to put a small mark on the blade or when you are only marking one side of the steel. First, ensure that the blade is tapped off using electrical tape, nail polish or vinyl to protect the steel. You can make use of a cotton Q-tip for soaking up a bit of acid.
Next, apply the acid to the stenciled steel; you can use the same timeline as before or feel with the Q-tip for when the acid begins to bite the steel. The Q-tip must be rubbed around the stencil, working the acid into the steel. The tip of the Q-tip will turn black as the metal is removed.
Depending on your goals, some finishing options include:
After obtaining the desired results, acetone and cotton swabs are used for the removal of the etch resist, including any sharpie marker or nail polish applied to the blade, pivot and lock face areas. The knife can also be reassembled at this point.
If there is no need to keep the acid, it is recommended to take it to a hazardous waste disposal facility. To neutralize the acid, you can make use of baking soda. It is still recommended to take the acid to a hazardous waste disposal facility after the neutralization because the solution contains a concentration of metals that could prove harmful to the environment.
There are a few last things to keep in mind, which are:
The etching of aluminum with copper sulfate is a less toxic, safer, simpler and cheaper kind of electro-chemical metal etching. Aluminum etching is less toxic and is also a lot of fun to mess around with.
An example of step by step aluminum etching follows these steps:
After the salt and copper sulfate has dissolved and the solution has cooled down a bit, the solution is ready to etch. In large quantities, copper sulfate is toxic; therefore, you must protect your hands with gloves, wear a mask, and protect your eyes. If the solution has not cooled down, the etch is more aggressive and might even produce smoke during etching, so allow it to cool down before using it.
The proportions of the copper sulfate and salt can be adjusted to make a weaker or stronger solution. It is also possible to do the etching process without salt, but this will reduce the reactivity of the etchant. This solution can also be used in the etching process of zinc and steel, but not copper.
The etching process is fast. With the proportions mentioned in the recipe above, it takes about 4 minutes to etch a line, 10 additional seconds to obtain a light gray tone, and 4 minutes to get a deep black. However, unlike with copper and zinc etching, the lines are not that crisp. Additionally, since the time of the etching process is much shorter and the etch is more erratic, it is hard to play with different line thicknesses.
The mordant exhausts fast compared to other types of acids, though it is possible to recycle it. While in the mordant, it takes a very short time to cover the plate with copper sediments – regularly removing the sediment with a soft brush or feather helps the etching process. It is recommended to use fine grain salt and fine grain copper sulfate because they dissolve better, even though interesting textures in the aquatint can be obtained if coarse salt is used.
To etch lines, you can use charbonnel ultra flex. Always make sure that you draw your lines firmly, scratching the metal slightly. The lines are usually not as consistent as they are with copper and zinc.
Aluminum feels quite greasy compared to other metals due to its softness. This makes the ink stick and take a long time to clean, so around 10% of softener can be added to the ink to make it faster and easier to clean the plate. It also makes the aquatint texture finer and more even. A softener makes a big difference in the printing process and result.
Treating a ceramic bonding surface is required to assure a long-lasting bond between orthodontic brackets and composite material used for repair, ceramic materials, and tooth structures. These treatments can be grouped into three categories, according to the mechanism of action: chemical, mechanical, or chemical-mechanical surface treatments.
The surface conditioning method selected depends on the ceramic restoration’s chemical composition. Surface acid etching can be used to achieve mechanical alteration, while universal or ceramic primers undergo chemical treatment.
Ceramics with silicon dioxide are recommended to be treated with acid etching. These ceramics include conventional or glass-ceramics, such as leucite-reinforced, feldspar-based, zirconia-reinforced lithium silicate ceramics, lithium disilicate, and fluorapatite ceramics.
The acids that are utilized as ceramic etchants are acidulated phosphate fluoride (APF), hydrofluoric acid (HF), and ammonium hydrogen fluoride. The most frequently used acid is the hydrofluoric acid, which, when applied onto the ceramic surface, reacts with the silica matrix to release molecules of silicon tetrafluoride and water. The silicon tetrafluoride reacts with other hydrofluoric acid molecules, forming a complex, soluble ion called hexafluorosilicate.
Further on, the hydrogen ions react with the complex ion of hexafluorosilicate to form a fluorosilicic acid. It can be rinsed off by dissolving and removing the surface layer of the glassy matrix that contains silica, silicates and leucite crystals; then, the surfaces becomes porous with a pore size of 3 to 4 micrometers. The acidulated phosphate fluoride has a composition of 1.23% fluoride ions that originate from sodium fluoride and hydrofluoric acid, acidified with phosphoric acid of 0.1 M concentration.
The ammonium hydrogen difluoride, NH4HF2, creates silicon tetrafluoride and ammonium fluoride when it reacts with a silica matrix. This acid is suitable for use as a glass etchant or as an intermediate in the production process of hydrofluoric acid. Different products may be used for ceramic etching. It must be noted that, besides their efficiency, these products are not allowed in some countries due to their high toxicity.
An IPS ceramic etching gel, Ivoclar Vivadent, is an aqueous gel solution of 4% hydrofluoric acid. This is unlike VITA ceramics etch, which is an alcoholic solution with a composition of 5% hydrofluoric acid and 10 % sulphuric acid. Porcelain Etch Ultradent has a composition of 9% hydrofluoric acid gel, primarily due to its high viscosity. According to the manufacturer’s instructions, it may be utilized in intraoral repairs of fractured porcelain, in porcelain-fused-to-metal or all-ceramic restorations, or in the surface treatment of porcelain before placing orthodontic brackets.
Porcelain etchant, BISCO, can be supplied in two different concentrations, like 4% and 9.5% of hydrofluoric acid gel. Additionally, Mirage offers two different types of porcelain etchants: 9.6% gel of hydrofluoric acid and 4% gel of acidulated phosphate fluoride. APF-gel may be made use of intra-orally and for luting of orthodontic brackets to porcelain crowns.
The acid etching effect is dependent on the type of the acid and its concentration, the etching time, and the type of ceramic being treated. Hydrofluoric acid is the most effective acid; it increases the concentration and the time taken for etching, which increases the etching effect.
The type of ceramic being treated also determines the roughness of the surface and etching pattern; acids do not affect polycrystalline ceramics that consist of glassy matrices. In contrast, the matrix of silica and leucite crystals are dissolved selectively in glass-ceramics, creating a three-dimensional porous structure. The effect cleanses the bonded surface, removing unwanted oxides, debris, and grease. This reaction also increases the roughness, hence increasing the bonding area and wettability of the ceramic’s surface, and creates micro retention that can be infiltrated easily with uncured flowable composite cement, altogether increasing the resin significantly. The characteristics below further impact this effect.
Acid Type: The acid type determines the expressiveness of the surface micromorphology after acid etching. Hydrofluoric acid etching results in stronger ceramic roughness than other acids.
Acid Concentration: The effect of acid etching does not only depend on the acid type but also on the acid concentration. An increase in the concentration of hydrofluoric acid increases the microroughness of the ceramic surface. A uniform crystal structure is observed as a result of dissolving the glassy phase when the performance of the treatment is done by hydrofluoric acid with a higher concentration (52%). Whereas a structure that is amorphous and also expressing large porosity can be detected when etching is done with a lower concentration (20%), when there is more dissolved crystalline phase.
Etching Time: The time taken for hydrofluoric acid etching affects the expressiveness of micro-morphological changes and microroughness of the surface of the ceramic. If the etching time is extended, the depth of the pores is increased.
Photochemical etching can be used to achieve excellent accuracy. Minimum standard etching tolerances are plus or minus 10% of the thickness of the metal that is being etched, to a minimum of plus or minus 0.025 mm. Greater accuracy can be achieved with development.
There are many companies available in the United States and Canada that offer acid etching services; these companies are essential as they provide specialized expertise and equipment for precision etching on various materials. Their success is often attributed to positive traits, characteristics, and factors that set them apart from others in the market: We discuss many of these companies, and the traits that have led to their success, below.
Metal Etch Services is a reputable company specializing in acid etching services for metal components. Their success can be attributed to the following factors:
Expertise and Experience: Metal Etch Services has built a strong reputation based on their expertise in acid etching techniques and their years of experience in the industry.
Customization: They have offered customized acid etching solutions tailored to meet specific customer requirements.
Quality Control: Ensuring high-quality results and strict quality control processes contributed to their success and customer satisfaction.
Qualitetch Components is a prominent name in the Canadian acid etching market. Their success may be attributed to:
Diverse Capabilities: Qualitetch offered acid etching services for a wide range of materials and industries, making them a versatile solution provider.
Innovative Approaches: They utilized innovative techniques and technologies in their acid etching processes, leading to unique and high-quality results.
Customer Focus: Successful companies often prioritize customer satisfaction, and Qualitetch's commitment to meeting customer needs contributed to their prominence.
Newcut Inc. is known for providing precision acid etching services. Their success could be attributed to:
State-of-the-Art Equipment: Investing in advanced acid etching machinery allowed Newcut to handle complex projects with precision and efficiency.
High-Quality Standards: A focus on maintaining stringent quality standards earned them a strong reputation in the market.
Diverse Clientele: Serving a diverse clientele across different industries contributed to their success and stability.
Metal Etching Technology specializes in chemical etching and electrochemical etching. Their success could be due to factors such as:
Technological Advancements: Embracing the latest technologies and methods for acid etching set them apart from competitors.
Strong Partnerships: Collaborating with key industry players and forming strong partnerships expanded their reach and customer base.
Advanced Metal Etching is a prominent company offering acid etching services. Their success may be attributed to:
Customization and Prototyping: Offering rapid prototyping and customized solutions attracted clients seeking quick and tailored acid etching services.
Quality Assurance: A strong focus on quality assurance and precision contributed to their success in delivering high-quality products to customers.
Please note that the companies mentioned above are based on information available up until September 2021. Market dynamics and the leading companies in the acid etching industry may have changed since then. For the most current information, it is recommended you conduct up-to-date research to identify the top companies in the United States and Canada that specialize in acid etching.
Industrial acid etching is a process used to produce high-precision parts and components with complex and intricate details. It is a highly technical and sophisticated process that relies on the use of a computer aided design (CAD) rendering to establish the parameters for the production of a part.
Computer generated drawings and sketches are computer plotted and placed on photographic film, a process referred to as phototooling. The size of the part determines how many images will appear on the film, which ranges from just one to thousands. Areas on the film are black or clear, with either the black areas or clear areas being the images of the desired part.
It is during the initial phototooling process that customers have the opportunity to adjust and make changes to the CAD design. This aspect of the process makes it far less expensive than other metal-shaping methods.
During the design process, the type of metal necessary to produce the part is determined. In the manufacturing area, the selected metal is cut into sheets and thoroughly cleaned of contaminants to create a clean, even smooth surface for etching. The cleaning aspect of the process ensures that the applied resist will uniformly and evenly adhere to the metal sheet.
TAfter selection, the sheets of metal are coated with the photoresist, a polymer material that is sensitive to ultraviolet (UV) light and resistant to acids. The sheets of the phototool are placed on the top and bottom of the metal sheet and vacuum sealed to its surface.
The phototool, photoresist, and metal sheet are exposed to UV light to place the engineered image on the coated metal. Where the light shines through the clear areas of the phototool, the resist is exposed and becomes harder and more firm. In the areas where the resist is blocked from the UV light, the resist remains soft.
In the developing process, a solution washes away the unexposed coating, leaving the configuration, shape, and pattern of the part to be produced. The only material that is left is the portion that will be etched away during the etching process.
In the etching machine, where the etchant is applied, the uncoated areas of the metal sheet are etched away by the acid chemical solution that is sprayed onto both sides of the sheet. In the areas where the etchant comes in contact with the exposed metal, the metal is dissolved. The other portions of the metal sheet are protected by the coating or resist from the effects of the etchant.
When the metal sheet leaves the etching machine, it is necessary to remove the remaining resist. A specially blended resist solution removes the resist, which, in some cases, may be an alkaline mixture.
Once the resist is removed, the finished part is ready for delivery or further processing, which can include plating, forming, electropolishing, and machining. Each of the finishing processes is used to make the formed piece comply with the needs of the application.
This chapter will discuss the applications and benefits of acid etching.
Acid etching can be applied in the areas listed below:
Acid etch tooling is digital, meaning component designs can be quickly set up and optimized without financial penalty. There is no application of heat or mechanical force during etching, meaning the properties of materials are not altered and components are produced burr and stress-free. Nearly limitless part complexity is achievable, with an accuracy of plus or minus 0.025 mm.
Chemical etching is capable of simultaneously producing very accurate engraved features during the profiling of the material, like fluidic channels, part numbers, or logos. These features come without any additional cost.
Other benefits include:
Acid etching is the process of cutting a hard surface like metal by means of a specially formulated acid for the process of etching in order to allow for the creation of a design onto the metal. It is also known as chemical etching or photo etching. Acid etching can be applied on ceramic components as well as in dentistry. There are different types of acid etching techniques including total etching, selective etching, and self-etching. The effects of acid etching are affected by several parameters such as the acid type, the acid concentration, and the etching time. Therefore when performing acid etching, one must consider the type of acid going to be used, the concentration as well as the time it is going to take to finish the process of etching. It must be noted that even though the acid can also be neutralized with baking soda after etching, if there is no need to keep the acid, it is recommended to take it to a hazardous waste disposal
Chemical milling is a subtractive machining process that removes material from a workpiece to achieve a desired shape. Unlike aggressive milling methods that depend on sharp tools to produce a design, chemical...
Metal etching is a metal removal process that uses various methods to configure complex, intricate, and highly accurate components and shapes. Its flexibility allows for instantaneous changes during processing...
Photochemical etching, also known as photochemical machining or metal etching, is a non-traditional, subtractive machining process in which photographic and chemical techniques are used to shape the metal workpiece...
EMI shielding is a technique of creating a barrier that prevents leakage of strong electromagnetic fields that can interfere with sensitive devices and signals. They can be installed to isolate the electromagnetic field source or as an enclosure of the device that needs protection...
Laser cutting is a non-traditional machining method that uses an intensely focused, coherent stream of light called lasers to cut through the material. This is a type of subtractive machining process where the material is continuously removed during the cutting process...
Radiofrequency (RF) shielding is the practice of blocking radiofrequency electromagnetic signals that cause radio frequency interference (RFI). RFI can disrupt the electrical circuits of a device from working normally...
Water jet cutting is a manufacturing process that uses high pressure jets of water provided by pressurizing pumps that deliver a supersonic stream of water to cut and shape various types of materials. The water in water jet cutting is...