Gear Drive
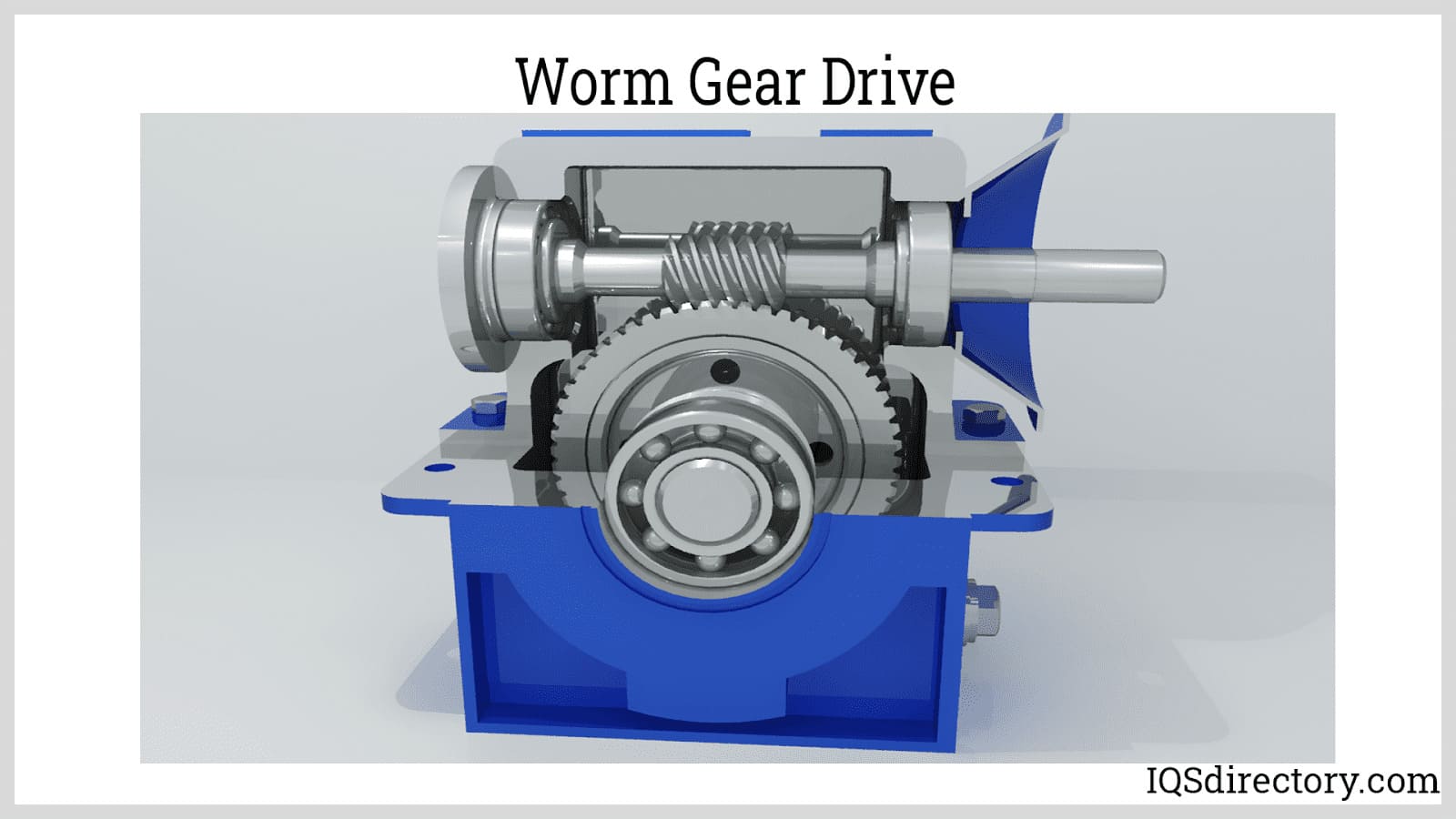
Gear drives, sometimes referred to as gear trains and gearboxes, are mechanisms consisting of an assembly of gears, shafts, and other machine elements for mounting the rotating parts...
Please fill out the following form to submit a Request for Quote to any of the following companies listed on
This article takes an in depth look at gear reducers and their use.
You will learn more about topics such as:
A gear reducer is a mechanical device designed to reduce the speed of an input rotation while increasing the torque output. It operates through a series of interlocking gears, where a high-speed input shaft drives a set of gears that adjust the speed and torque. The specific number of gears in a gear reducer setup varies based on the desired speed and torque characteristics for the particular application.
Gear reducers come into play when the driving gear has fewer teeth and a smaller size compared to the driven gear. This setup contrasts with an overdrive scenario, where the driving gear is larger and has more teeth relative to the driven gear.
Gear reducers are crucial in vehicles like cars and trucks, where they adjust the high-speed rotation of the engine to produce a lower-speed motion that allows the tires to harness and utilize the power effectively and safely.
Gear reducers, also known as reduction gears, are vital for machinery that operates at high speeds to ensure optimal efficiency. To make the machinery's high-speed output practical, it must be reduced to a slower speed to suit the requirements of the driven application. Typically, a gear reducer is constructed with a larger gear paired with a smaller gear, with both gears engaging and rotating together.
In a basic gear reducer setup, where a larger gear drives a smaller gear, the smaller gear completes two revolutions for each revolution of the larger gear. Although this setup increases speed, it results in a decrease in torque.
The gear reduction is achieved through specific ratios that align with the input and output gear characteristics. The gear reducer modifies the energy transfer by adjusting the ratio between the rotating gears.
The gear ratio quantifies how gears of different sizes interact to transfer motion and energy. This ratio is primarily determined by measuring the circumference of the gears. For instance, if a smaller gear completes two rotations to make a larger gear rotate once, the gear ratio is 2:1, indicating that the output speed is reduced by half.
This example illustrates a fundamental concept that can be extended to more complex gear systems, where multiple gear pairs are used to convert revolutions per minute (RPM) into torque. Consider a more intricate gear reducer with an additional idler gear placed between the smaller and larger gears.
When calculating the gear ratio, only the drive gear and the driven gear are considered; any intermediate gears do not affect the ratio. To find the gear ratio, count the number of teeth on the drive gear and the driven gear. For example, if the drive gear has 7 teeth and the driven gear has 30 teeth, the drive gear must rotate approximately 4.3 times to make the driven gear complete one rotation.
Torque refers to the rotational force that is input into a gear reducer and is then transformed into a different force and speed while maintaining the same power level. Gear reducers are designed to decrease the torque from a motor, which scales directly with the reduction in the number of rotations per minute (RPM). This is achieved through gear reducers mounted on either the base or the shaft.
Gears play a crucial role in adjusting torque, either amplifying or diminishing it, based on their size. The gear ratio, which is determined by the relative sizes of the gears, affects the amount of torque produced. This principle is fundamental to the operation of gearboxes.
Drive gears or gear drives are designed to change the speed, torque, or direction of a rotating shaft. In their simplest form they are a small gear that drives a larger gear connected to the output shaft. They are essential for providing variable output speed from a constant power source.
In the image below, the silver worm shaft paired with the worm gear serves as the drive gear in this two-gear reducer setup. The driven gear is represented by the brass-colored worm wheel within the worm gear assembly.
The driven gear is attached to the output shaft and conveys the reduced power to the application. It is typically the larger gear in the set, regardless of the number of gears in the series, and can come in various shapes. In the compound gear train example below, two driven gears are linked to different shafts, B and C. The gear ratio for the driven gear on shaft B is identical to that on shaft C.
A speed reducer, also known as a gear reducer, is a device that adjusts the rotational speed from a motor before it reaches the machinery. It consists of a gear train that reduces the high-speed rotation of the motor's shaft to a slower speed, thereby increasing the output torque. The gears in a speed reducer have more teeth compared to the input gear, allowing the output gear to turn more slowly while providing greater torque.
Positioned between a motor and machinery, a speed reducer moderates the motor's speed to ensure that the machinery can effectively utilize the motor’s power. It achieves this by employing a combination of large and small gears that work in tandem to decrease the input speed and boost the torque. This adjustment in speed enables finer control over processes, leading to improved performance and results.
Speed reducers take the same form as gear reducers and have four basic forms, which are worm, planetary, spur, and bevel with transmission single and multiple stages. Included in the types of speed reducers are the shapes of the gears that are cylindrical, bevel, and cone cylindrical.
A worm speed reducer utilizes a worm wheel to achieve reduction ratios ranging from 10:1 to 60:1. It features perpendicular input and output shafts and is designed to be irreversible, offering a high degree of system reliability and security.
Planetary speed reducers offer several benefits, including a compact design, low ground clearance, high efficiency, extended service life, and high output torque with a coaxial arrangement. Despite their compact size, planetary speed reducers provide excellent transmission efficiency, with losses of only 3% per stage, ensuring that a significant portion of the input energy is converted into torque.
However, the intricate design of planetary speed reducers necessitates specialized maintenance and regular attention to ensure optimal performance and longevity.
Spur speed reducers feature a straightforward design that delivers substantial torque. Their gears are aligned in a straight configuration, making them highly efficient and well-suited for high-speed applications. Among the various types of speed reducers, spur speed reducers are the most widely used and are favored across many industries for their reliability and effectiveness.
Bevel speed reducers are used for applications that require a right angle speed reducer with a low ratio. They have an angled bell crank, which allows users to change a machine’s rotation system from lateral to longitudinal. Bevel speed reducers are designed to handle high power and high torque. The gear meshing ratio can be increased on a bevel speed reducer by using helical gears.
A gear reducer is a device that adjusts rotational speed through the use of gears, shaft alignment, and gear configurations. It is commonly employed in reduction transmission systems where the drive motor is integrated with the gearbox or gear reducer.
Gear reducers can incorporate various types of gearboxes, including planetary, cylindrical, parallel shaft, worm, or screw types, each serving specific functions to meet application needs. Most gear reducers feature multiple gear series with varying gear ratios, which facilitate substantial gear reduction.
Bevel gear reducers feature an angled bell crank that enables the system's rotational direction to shift from transverse to longitudinal. They are designed to be compact yet capable of handling substantial power from three-phase asynchronous motors, synchronous motors, or asynchronous servo motors.
Similar to helical and hypoid gear reducers, bevel gear reducers operate with minimal noise while delivering high performance and exceptional energy efficiency.
In a cycloidal gear reducer, the input shaft drives a bearing assembly that moves a cycloidal disc, which in turn is connected to an output shaft. The cycloidal disc's teeth mesh with a cam follower equipped with pin or needle bearings. This mechanism allows the output shaft to rotate at a significantly lower speed and with higher torque compared to the input shaft.
The primary advantage of cycloidal gear reducers is their ability to eliminate backlash, providing the precision and accuracy required for robotic applications and machine tools. Moreover, their rolling contact design results in reduced wear and increased durability.
A gear train gear reducer consists of a sequence of gears that transmit power from an input shaft to an output shaft. These reducers are used in applications requiring substantial power and operate on parallel axes. The simplest configuration involves two gear trains: a drive gear and a driven gear. More complex versions include additional idler gears between the drive and driven gears to further refine the power transfer.
Helical gear reducers are compact and durable, designed to handle high overloads while saving space. They are ideal for applications requiring medium to high-speed operations. The helical gears feature slanted teeth, which enhance the meshing ratio, reduce noise, and increase strength. Their synchromesh design ensures continuous engagement and provides a larger contact area.
The angled teeth of helical gears allow for a longer tooth profile while maintaining the same number of teeth as a spur gear.
Hypoid gears are cone-shaped and used to transmit power between non-intersecting shafts. The offset between the smaller hypoid pinion and the larger hypoid gear allows them to mesh smoothly without interference. This design provides a large contact ratio, enabling the transmission of heavy loads with smooth operation and reduced noise, similar to helical gear reducers. Hypoid gear reducers are capable of achieving significant speed reductions.
Hypoid gears are commonly employed in applications where the shafts are at right angles and the distance between them is limited. They often serve as an intermediate solution between bevel and worm gears.
Magnetic gear reducers represent a distinctive type of gear reducer that operates using magnetic attraction rather than physical contact. Instead of gear teeth, they rely on opposing magnets that repel each other, allowing them to apply force at various angles without direct contact. This design eliminates wear and tear, as the gears do not physically touch each other.
Moreover, magnetic gears do not need lubrication or sealed barriers. They are typically constructed using permanent magnets or electromagnets, making them a low-maintenance and durable option.
A planetary gear reducer consists of a central sun gear, orbiting planet gears, and a large ring gear. The planet gears are supported by the output shaft, the inner ring gear, and the sun gear. Power is transmitted through the sun gear at the center, which drives the planetary gears to rotate around the inner ring gear. This rotation of the planet gears then drives the output shaft, which delivers the output power.
A planetary reducer offers a long service life, compact size, high load capacity, low noise, high output torque, and excellent efficiency. It features power splitting and multiple tooth meshing, making it a highly versatile reducer suitable for various applications.
Spur gear reducers feature straight teeth that are aligned parallel to the axis. They are the most common type of gear reducer and can incorporate multiple gears with varying gear ratios. Spur gear gearboxes are known for their high efficiency, minimal backlash, and robust stability.
A worm gear reducer features a worm pinion input and an output worm gear arranged at a right angle. It converts the motor's high speed into a lower speed output with increased torque. Worm gear reducers are especially suited for space-saving applications due to their compact design and the small diameter of the output gear, while still providing excellent speed reduction in a compact package.
A coaxial axis gear reducer employs planetary gears that revolve around a central sun gear. Both the input and output gears are arranged concentrically, enhancing torque and efficiency. Typically, three to five planetary gears mesh with the internal gear, distributing power across multiple branches. The design aims for an even distribution of power.
The fundamental mounting options for gear reducers are base mounting and shaft mounting.
Gear reducers with orthogonal axes, such as bevel gear reducers, feature input and output shafts that are perpendicular to each other. While they are less precise than parallel axis gear reducers due to less optimal tooth contact, they are commonly used for power transmission and branching applications.
Parallel axes gear reducers have the output and input shafts parallel. They have very high precision and transmission efficiency. Parallel axes gear reducers can use large sized standard spur gears or helical gears. They are used in machines with high rotations on the load side, such as cranes, elevators, and conveyors.
When the input and output axes of a gear reducer are offset but orthogonal, it is known as a skew axes gear reducer. This design features non-intersecting, non-parallel axes with an offset gear centerline, leading to greater tooth surface contact and a higher contact ratio. Consequently, this results in increased torque capacity and smoother power transmission.
Before purchasing a gear reducer, several factors need to be considered. The primary role of a gear reducer is to adjust the torque and speed characteristics between the input and output shafts of a system. Understanding the application’s torque and rotational speed is therefore crucial.
A gear reducer enhances the torque from a motor and provides a new torque value for the application. Manufacturers indicate both maximum and minimum torque values in newton meters (Nm) for their products, with varying torque densities across different gear reducers.
Another key function of a gear reducer is to lower the motor speed, which is expressed as a reduction ratio. The motor’s rotational speed is adjusted by this ratio to achieve the desired output speed, typically measured in revolutions per minute.
At this stage of selection, it is crucial to consult with an expert, engineer, or designer familiar with gear reducers due to the variety of types available, each suited to different functions and specifications. The initial criteria involve determining the configuration of the input and output shafts.
Choosing the right dimensions for a gear reducer involves selecting the appropriate shaft type, such as orthogonal, coaxial, or parallel. Each shaft type has a specific orientation relative to the gear reducer—perpendicular, aligned, or parallel.
For applications subject to shock or cyclic loads, it is important to consider these conditions when selecting a gear reducer. This ensures that the gear reducer can handle increased torque effectively.
It is important to choose a gear reducer that operates efficiently to manage long-term costs effectively. Selecting the right gear reducer can offer significant benefits in terms of cost-efficiency over time.
Planetary gear reducers are suited for applications requiring rapid acceleration, low speeds, and high torque. They are commonly used in machine centers, machine tools, and agricultural machinery.
Worm gear gear reducers are used in applications with a high transmission ratio. They are less costly than other gear reducers and operate very quietly. Worm gear gear reducers are used on conveyors, winches, and material handling due to their non-reversibility.
Gear train reducers are designed for high-power applications and offer cost savings on maintenance due to their exceptional performance and low reduction ratio.
Bevel gear reducers allow for changes in rotational direction. They are compact, robust, and capable of handling substantial force. However, they may have lower performance, higher costs, and require frequent maintenance. They are typically found in farm equipment and heavy-duty conveyors.
Gear reducers play a crucial role in various machines and are essential for smooth operation. Proper selection of a gear reducer ensures the efficiency and effectiveness of a system. A knowledgeable manufacturer can provide guidance on the optimal solution for any application.
After selecting the appropriate gear reducer, maintaining a regular maintenance schedule is crucial for its effective and efficient operation. Regular upkeep is essential to prevent failures, errors, and reduced performance. Routine inspections help minimize or avoid potential issues.
Gear reducer manufacturers provide or recommend specific lubrication materials for their products. The lubricant must have the correct properties to optimize performance. During the break-in period, it may be necessary to filter the lubricant to remove contaminants. Regular checks on the lubricant’s quality and level are also important.
Only the lubricant should be present in a gear reducer. Contaminants such as dust and water, which can enter through faulty seals, can cause significant damage to the gears.
Gear reducers should be stored in clean, dry, and climate-controlled environments with all covers, vents, and drains securely closed. Even when not in operation, the lubrication cycle must be maintained, and the reducer should be rotated periodically to ensure even lubricant distribution.
Noise is often an early sign of problems with a gear reducer. Running the reducer without a load can help assess the issue. Persistent noise and vibration may indicate the need for an overhaul or replacement.
Overheating usually signals inadequate lubrication. Regularly checking the gear reducer's surface temperature can prevent overheating, which is often caused by friction due to insufficient lubricant.
Proper maintenance ensures the gear reducer's reliable operation for many years.
Gear drives, sometimes referred to as gear trains and gearboxes, are mechanisms consisting of an assembly of gears, shafts, and other machine elements for mounting the rotating parts...
A speed reducer is a gear train between the motor and the machinery that is used to slow down the transmission of power. Speed reducers, also known as gear reducers, are mechanical devices that serve two roles...
Ball screws are mechanical linear actuators that consist of a screw shaft and a nut that contain a ball that rolls between their matching helical grooves. The primary function of ball screws is to convert rotational motion to linear motion. Ball nuts are used in...
A bevel gear is a toothed rotating machine element used to transfer mechanical energy or shaft power between shafts that are intersecting, either perpendicular or at an angle. This results in a change in the axis of rotation of the shaft power...
A gear is a particular kind of simple machine that controls the strength or direction of a force. A gear train is made up of multiple gears that are combined and connected by their teeth. These gear trains allow energy to move from...
A lead screw is a kind of mechanical linear actuator that converts rotational motion into linear motion. Its operation relies on the sliding of the screw shaft and the nut threads with no ball bearings between them. The screw shaft and the nut are directly moving against each other on...
A planetary gear is an epicyclic gear that consists of a central gear, referred to as the sun gear and serves as the input gear, which has three or more gears that rotate around it that are referred to as planets...
A plastic gear is a toothed wheel made up of engineering plastic materials that work with others to alter the relation between the speed of an engine and the speed of the driven parts. The engineering plastic materials used in manufacturing plastic gears can be...
Shaft couplings are devices that connect two shafts to transmit power from the driveshaft to the driven shaft while absorbing some degrees of misalignments and mounting errors between the two shafts...
A spur gear is a cylindrical toothed gear with teeth that are parallel to the shaft and is used to transfer mechanical motion and control speed, power, and torque between shafts. They are the most popular types of cylindrical gears and...
A worm gear is a staggered shaft gear that creates motion between shafts using threads that are cut into a cylindrical bar to provide speed reduction. The combination of a worm wheel and worm are the components of a worm gear...
A rotary circular machine with a tooth in its structure and is used to transfer torque and speed from one shaft to another is called a gear. Gears are also known as cogs and have cut teeth in the cogwheel or gear wheel...