Closed Cell Foam
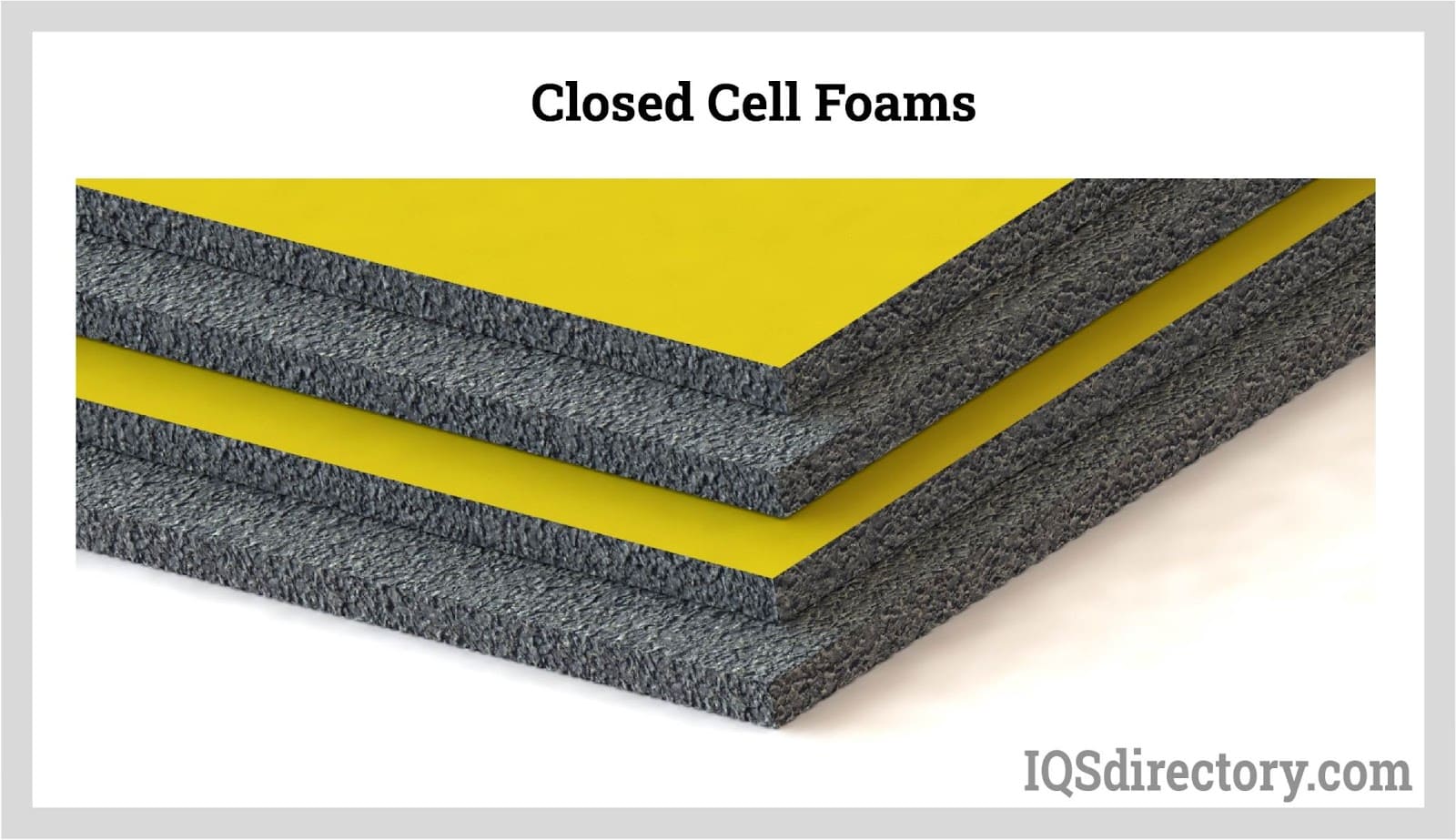
Closed cell foam is a type of foam where the “cells” are tightly pressed together and enclosed, contrasting with the open, traditional polyurethane foam variation or interconnected cells of the open cell...
Please fill out the following form to submit a Request for Quote to any of the following companies listed on
This article takes an in-depth look at polyethylene foams and their properties.
Read further and learn more about topics such as:
Polyethylene foam is a valuable closed-cell thermoplastic foam material. A closed-cell foam consists of tiny dense cells enclosed by its walls. The cells sit close to each other, but they are not interconnected. Hence, closed-cell foams like polyethylene foams are ideal for blocking the flow of liquids and gases. They are resistant to air, moisture, and chemical penetration. Their structure makes them stronger, denser, and more rigid than open-cell foams. Polyethylene foam remains a lightweight and flexible material despite its closed-cell structure.
Polyethylene foams are impact-resistant and highly resilient, critical for cushioning applications. Their low thermal conductivity makes them suitable insulating materials. They are soft, non-abrasive, and resistant to dusting, tearing, and degradation. They have high dimensional stability allowing them to withstand several fabrication processes. They also have antimicrobial properties that inhibit the growth of bacteria, molds, and other microorganisms. These properties make polyethylene foams fit for many personal and industrial uses. Special properties are imparted to polyethylene foams by blending chemical agents or additives followed by a series of treatments.
The types of polyethylene foams are the following:
In XLPE foams, the constituent molecules connect by molecular bonds, forming chained connections from straight carbon chains. The cross-linking of the molecules creates a strong and rigid structure. XLPE foams are more durable and resistant to chemical, gas, and moisture permeation. They have greater thermally and dimensionally stability, insulating properties, and shock and vibration resistance. However, the production of cross-linked structures removes the recyclability of polyethylene foam as a thermoplastic.
XLPE foams can be formulated to be fire-retardant, static-dissipative, or conductive.
Cross-linking may be carried out by either of the following methods:
XLPE foams are used when thicker sections of foam material are needed. Their applications include expansion joints, gaskets, padding material, insulating materials, orthopedic bracing, and protective packaging for sensitive medical devices. Due to their low water permeability and high buoyancy, they are suitable as a material for floating devices.
EPE foams are made by applying heat and pressure to the polyethylene resin, blowing agents, and additives inside an autoclave in order to form tiny beads. These beads are cooled and later used as feed material for injection molding. They are melted and poured into the mold cavities. EPE foams are characterized by their high strength-to-weight ratio and high thermal resistance. Unlike XLPE, EPE foams are recyclable.
Extruded polyethylene foams are foams having constant cross-sections that are produced by an extrusion process. They are manufactured by forcing the molten polyethylene resin and additives over the hole of the extruder die, making a long and continuous polyethylene foam. The continuous foam is then cooled and rolled into coils or cut into specific thicknesses or lengths.
Polyethylene foams can be manufactured based on the density requirements of a specific application. The varied foam densities of commercial polyethylene foams are brought by the foaming method utilized. For instance, LDPE plastics can be manufactured into low or high-density polyethylene foams.
Low-density polyethylene foams have more voids in their cellular structure; hence, their density is relatively lower. These foams are softer and have better thermal insulating materials than high-density foams. They are also valued for their buoyancy and water resistance. However, their thickness decreases due to prolonged exposure to compressive stress. Low-density polyethylene foams are commonly used as a packaging material.
High-density polyethylene foams have smaller and thicker cellular walls. They are characterized by their high compressive and tensile strength, fatigue resistance, and low thermal shrinkage. They are more preferred than low-density foams for heavy-duty applications. They are used as sport underlays and cushions for shoes and couches.
Below are the stages involved in a closed cell foaming process when observed at the molecular level:
The primary raw materials in the production of polyethylene foams are as follows:
It is the main component of polyethylene foams. Low-density and high-density polyethylene (LDPE and HDPE) resins are the most common types of polyethylene manufactured into foams. LDPE foams are lightweight, elastic, water-resistant, and low cost. On the other hand, HDPE foams are stronger and tougher than LDPE foams. In all methods of polyethylene foam production, the resins are melted and combined with agents and additives, which modify the original properties of polyethylene.
A blowing agent is primarily responsible for supplying the gas needed to grow fine cellular structures in the polyethylene matrix. Blowing agents are categorized into chemical and physical blowing agents:
Chemical blowing agents liberate the gas needed for the foaming process through thermal decomposition or a chemical reaction of a reactive blowing agent. The gas is unreactive with the polyethylene matrix. Reactive blowing agents may exhibit an endothermic or exothermic reaction and usually produce nitrogen or carbon dioxide gas.
Organic blowing agents are known to enhance the foaming process because they constantly produce dispersible gas. They also make uniformly-sized bubbles.
Some examples of chemical blowing agents are azodicarbonamide (exothermic), sodium bicarbonate (endothermic), zinc carbonate (endothermic), and acylhydrazide (thermal decomposition).
The common thermoplastic foaming techniques utilized in the production of polyethylene foams are the following:
Batch foaming is suitable for relatively low production orders. It is used for testing novel foam formulations which is challenging to support in continuous foaming machines. Batch foaming is normally carried out in an autoclave and series of thermal baths. Thus, they are less expensive and take less time to set up.
Batch foaming can be a pressure-induced or temperature-induced process:
In pressure-induced batch foaming, the molten polyethylene resin is saturated with the blowing agent in an autoclave operating at high pressure. Then, the gas-saturated polyethylene sample is depressurized to atmospheric pressure by opening the relief valve of the vessel. The sudden pressure drop induces cell nucleation and subsequent growth. The foam is then allowed to expand to a certain volume. Finally, the foam is allowed to cool by air or a solvent for cell stabilization.
In temperature-induced batch foaming, the gas dissolution stage is performed in a high-pressure autoclave (2-5 MPa) but at a lower temperature (10-250C). Then, the gas-saturated polyethylene sample is taken out of the autoclave chamber and immersed in hot oil, water, or glycerin bath (80-1500C) for a specific duration. Plunging the sample into a high-temperature fluid triggers cell nucleation and subsequent growth. The foam can then expand to a certain volume while in the hot fluid. Finally, the foam is quenched into cold water or a solvent bath for cell stabilization.
Foam extrusion is a continuous foaming process that produces foams with a constant cross-section such as sheets, rods, and tubes. In a foam extruder, the polyethylene pellets and additives are fed from the hopper into the barrel consisting of several heating zones. The blowing agent is introduced into the polyethylene melt at the hopper or at a specific point in the barrel. The polyethylene resin is melted inside the barrel. The extruder screw exerts high pressure to push the melt through the barrel and over the hole of the extruder die. As the melt leaves the hole of the extruder die, it experiences a sudden pressure drop which induces cell nucleation and growth. The screw speed, discharge rate, and extruder zone temperatures are set at optimal values. After cell growth, the foam is cooled, stabilized, and advances to downstream processes (e.g., cutting).
Foam extrusion is suitable for high production orders.
Foam extrusion can either be a physical or a chemical foaming process depending on the type of blowing agent utilized:
Foam injection molding is a large-scale batch-mode foaming process. Like foam extruders, a foam injection molding machine consists of a barrel with zone heaters, a reciprocating screw, and feeding mechanisms for the resin and the blowing agent. The blowing agent is introduced into the polyethylene melt either at the hopper (chemical blowing agents) or at a specific barrel point (physical blowing agents). The melt is pushed from the barrel with sufficient injection pressure and speed until it reaches the nozzle. The melt experiences a sudden pressure drop as it leaves the nozzle and fills the mold cavities. Thus, cell nucleation and growth are initiated. The foam expands to the shape of the mold cavities and dwells for a set duration. The mold halves are then opened, and the foam is taken out from the mold cavities. Finally, the excess materials (e.g., flashes) around the foam product are trimmed. This cycle is repeated to accommodate the production orders.
Foam injection molding can produce foams with complex shapes accurately. However, the tooling and the energy requirements can be expensive.
There are several machines available to produce polyethylene foam, and these machines are important to society as polyethylene foam is widely used for packaging, insulation, cushioning, and buoyancy applications due to its lightweight, insulating, and excellent shock-absorbing properties. Below, we discuss many notable brands of machines used for producing polyethylene foam in the United States and Canada:
Zotefoams offers AZOTE® Foam Extrusion Systems that are designed for producing polyethylene foam, featuring advanced extrusion technology, precise temperature control, and customizable foam formulations.
EPE Foam specializes in manufacturing machines for producing polyethylene foam, providing a range of models that offer high-speed production, reliable cutting systems, and the ability to produce various foam densities.
Polycraftpuf Machine Pvt. Ltd. offers polyethylene foam machines that enable efficient production, including foam extrusion, shaping, and cutting processes, with customizable foam thicknesses and densities.
MuCell Extrusion specializes in microcellular foam extrusion systems that can be used for various materials, including polyethylene foam, offering benefits such as weight reduction, improved mechanical properties, and enhanced surface finish.
Foam Supplies Inc. offers FSI Ecomate® Foam Systems designed for polyethylene foam production, providing precise control over foam density, customizable foam formulations, and environmentally friendly blowing agents, ensuring efficient and sustainable foam manufacturing processes.
The following are some of the products made from or uses polyethylene foams:
Polyethylene foam insulation is an effective temperature barrier valued for its high flexibility, durability, and resistance to corrosion, weathering, moisture, and rupture. These foams are typically laminated with aluminum foil to increase their heat reflectivity and durability. They can also help in vibration and sound-proofing. Due to their flexibility and low density, polyethylene foams can be easily installed in roofs, ceilings, walls, floors, and pipes. Installation is even made easier for insulation foams backed with adhesives. Polyethylene foam insulation with fire retardant properties is also available commercially.
Aside from homes and buildings, polyethylene foam insulation is also found in pipes, refrigerators, and cold boxes.
Anti-static polyethylene foams prevent the build-up of static electricity on electronic devices and protect them from electrostatic discharge. They provide cushioning and minimize the effects of shock and vibration during transportation and handling. They also protect the device from moisture, heat, and accidental spills. Hence, they are ideal for packaging electronic and semiconductor devices. Anti-static polyethylene foams are typically pink in color and available in sheet form.
Sheet polyethylene foam can serve as a carrier for the adhesive film in tapes. Polyethylene foam tapes are available in one-sided or double-sided types. One-sided foam tapes have an adhesive film covering one side of the polyethylene sheet. They are used in gaskets, cushioning, packaging, and insulation applications. On the other hand, double-sided foam tapes have an adhesive film covering both sides of the polyethylene sheet. They are used in mounting and bonding applications. Polyethylene foam tapes vary in thickness and softness. They are more durable than tapes consisting of plastic film and paper carriers. They are widely used in HVAC equipment, homes, and buildings.
Polyethylene foams are naturally combustible, like wood and paper. They are treated with synergistic antimony oxide-halogen or phosphorus-halogen systems to make them fire retardant. However, there are environmental and health concerns on the use of halogens in the anti-flaming methods of polyethylene foams. Halogens can generate large amounts of toxic fumes.
However, mold processing techniques and halogen-free additives are being developed to impart fire retardant properties to polyethylene foams. Magnesium hydroxide is being examined to see if it can be a viable substitute for halogen-containing fire retardant additives. Moreover, high-temperature melting, chemical cross-linking, and mold processing are optimized to develop a fire retardant, low-density polyethylene foam with ethylene-vinyl acetate.
Sheets of polyethylene foams and other materials can be laminated together to form thicker sections. Laminating can also help increase mechanical stability, cushioning, insulating properties, and durability of polyethylene foams.
Polyethylene foams can provide comfort and enhance ergonomics. They can be used as padding and cushioning for chairs, couches, beds, car seats, arm and headrests, and other furniture. However, open-cell foams are softer and more comfortable than polyethylene foams.
Polyethylene foams have high buoyancy (the tendency of an object to float) and low water permeability. Hence, they are ideal in flotation devices such as swimming noodles, life jackets, buoyancy aids, and lifeguard floats. They may also be found beneath the straps of backpacks.
Closed cell foam is a type of foam where the “cells” are tightly pressed together and enclosed, contrasting with the open, traditional polyurethane foam variation or interconnected cells of the open cell...
Polyurethane foam is a porous, cellular-structured, synthetic material made from the reaction of polyols and diisocyanates. Its structure is a composite of a solid phase and a gas phase. The solid phase is made from...
Die cutting is the mass fabrication of cut-out shapes by shearing a stock material such as paper and chipboard using tooling called a die. A die is a specialized tool used in manufacturing to cut or shape a material fitted into a press...
Kiss cutting is a method for cutting into a material where the upper layers are pierced, but the back layer is left intact. The term "kiss" refers to the way the blade touches the upper layers of the material and leaves a pattern or cut with a sufficient amount of force to leave an impression...
Plastic fabrication is the process of designing, manufacturing, and assembling a product made out of plastic material or composites that contain plastic. There are numerous plastic fabrication methods known today, considering the wide variety of products made out of plastic...