Adjustable Workbenches
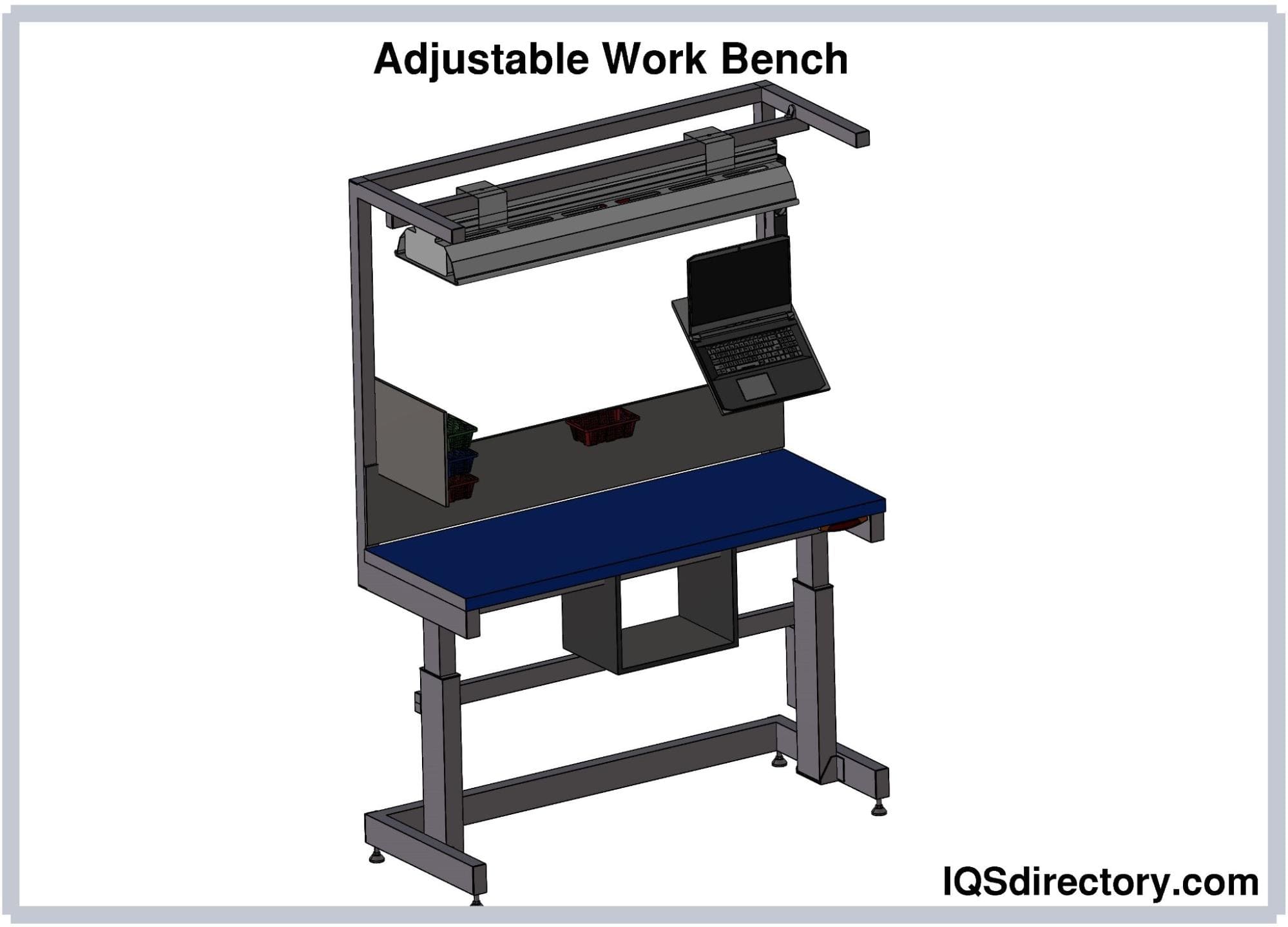
An adjustable work bench is a tool that allows the user to adjust and regulate the height of the work surface to a more ergonomic and comfortable position for the safe and effortless performance of work...
Please fill out the following form to submit a Request for Quote to any of the following companies listed on
This article will take an in-depth look at caster wheels.
The article will bring more detail on topics such as:
This chapter will discuss what caster wheels are, their manufacturing, and how they function.
A caster is a non-powered wheel that is designed to be fitted to the bottom of a bigger object and used to move it. Caster wheels are used in shopping carts, office chairs, medical beds, and material handling equipment.
Caster wheel variations vary greatly based on the application requirements and are widely employed in a wide range of applications. It is a wonderful mobility enabler, with properties such as strength, corrosion resistance, water resistance, and weather resistance. The applications of caster wheels necessitate precise sizing based on the terrain on which they will be used and the weight they are expected to carry. Heavy items need casters with thicker wheels, some larger objects might need multiple wheels to evenly distribute weight.
This section will discuss the manufacturing processes involved in making caster wheels.
The first plate to be cut is the top plate. This is the plate used to mount the caster underneath the object, for example the industrial cart. The process begins with a thick sheet of steel that is cut by a CNC (computer guided machine that combines oxygen and electricity to produce plasma). Plasma cutting is a type of thermal cutting that uses an ionized gas to cut the metal. This means that the process uses heat to melt the metal rather than mechanically cutting it. It's one of the most common methods for cutting thick metal plates, but it's also useful for sheet metal. This method is very accurate and fast when cutting steel sheets.
The next part to be cut is the fork. Forks are the arms that hold each side of the wheel axle. The forks are made out of steel coil, a more flexible and thinner type of steel. The steel coil is rolled out and fed into a punch press machine which breaks it with the yoke shaped dye. The broken yoke shaped pieces are placed onto a forming press. The press bends the piece into the required shape and it also makes a circular groove around the hole in the middle. The hole is filled with steel ball bearings that allow the yoke to swivel. A steel retainer is fitted to hold the ball bearings in place. The grooves of the steel cap are filled with ball bearings as well then they place it onto a punch press and position the yoke on top. The press joins the cap to the yoke’s retainer, sandwiching the ball bearings in between. After riveting the top plate to the yoke, put a steel seal over the retainer and lock it in place with a pneumatic press.
The next machining process on the production of caster wheels is the extrusion of the wheel material. To make the wheels, nylon inserts are required. The inserts are placed in an injection molding press, which melt neoprene rubber and injects it into the mold. Once it cools to a solid state, the machine ejects rubber edged wheels. The rubber edge absorbs shock, reduces noise, and prevents damage to the floor or surface.
For bigger sized wheels, a different molding press is used to suit the required size. The molding process to produce the wheel is the same. These larger molding press machines usually make one wheel at a time. After the wheel is ejected from the molding press it is placed on a cool down rack for 2 and a half hours. The wheel mold is made up of two parts, which form a sim once attached. The rubber sim is then grinded down until the surface is smooth.
A two part bearing is placed inside the wheel, and locked into position with a pneumatic press. A steel guide is then installed on either side of the wheel. The steel guides prevent anything from entering the wheel and inhibit its movement. The steel guides position the wheel between the yokes and insert the steel wheel axle. A bolt head secures one end and a nut is attached to the other end. Grease is injected to lubricate the ball bearings.
The wheel must undergo a series of quality control tests that count the number of revolutions a caster can withstand before it finally breaks.
The considerations when selecting caster wheels include:
Fixed casters may be sufficient if the equipment simply moves in a straight line, such as large equipment that is hauled out for cleaning and then returned to the same location. A swivel caster, on the other hand, may be a better alternative if there’s need for more maneuverability. Consider also whether there's need for swivel locks, if equipment is to be moved in a straight line. The ability to move something is why casters are put on it, but there's also need to know how much freedom there is in that movement.
While this may not appear to be a significant issue, it can limit which caster is chosen for the assignment. Many applications require a stem mounted caster, although this can limit the caster's weight capacity. Heavy-duty casters will use a plate mount to secure the caster and disperse the load over a greater mounting area. Knowing the mounting preference can help narrow down the options when selecting casters from a huge number.
What kind of machinery will the casters be mounted on? This may appear to be a simple question, but it is important. This question will help evaluate if there's a need for light-duty, medium-duty, or heavy-duty casters based on the overall weight that will be put on them. This question necessitates taking into account the environment in which the casters will be employed. Is noise reduction going to be a big deal?
Caster wheels differ ranging with applications that are from medical, industrial, furniture casters, etc.
Soft treaded caster wheels are ideal for offering a comfortable ride while also safeguarding delicate floor surfaces. They are chemical, oil, and acid resistant because they are composed of thermoplastic and mold-on rubber. While a soft tread allows wheels to roll over small debris and is usually quieter than other materials, it also makes it more difficult to roll and reduces the caster's overall load capacity. Thermoplastic rubber, rubber tread on iron core, and polyurethane tread on plastic core are all common soft tread caster wheels.
The soft tread wheels are typically applied in medical and pharmaceutical equipment. They are also applied in food service equipment, processing plants, and other light to medium loads.
Ferrous wheels provide the highest load capacity, impact resistance, temperature range, and rollability of any caster wheel available due to the solid structure it has. Ferrous wheels, as the name implies, are made of forged steel or cast iron, making it excellent for harsh situations such as warehouses and manufacturing factories where floor protection is not a priority.
The wheel is what distinguishes a caster, therefore selecting the appropriate wheel for the location and application is crucial. When selecting a wheel, there are numerous factors to consider, ranging from impact, chemical resistance to roll ability and capacity.
Soft tread wheels are more difficult to roll than polyurethane tread wheels, though they provide good floor protection. These wheels are made of solid urethane, chemically or mechanically bonded to plastic, or chemically bonded to cast iron or aluminum cores, and have a 3,000-pound capacity and strong impact resistance.
One downside of poly wheels is that if the wheel is overloaded or the tread sustains other damage that undermines its construction, the tread can separate from the core. However, solid urethane wheels are one approach to prevent these issues. The concern of tread separation and core corrosion is minimized because the entire wheel is made of molded urethane with no core.
Synthetic wheels with a harder tread have a lower rolling resistance and a higher impact strength and reliability. Solid elastomer, polypropylene or polyolefin, fiberglass reinforced polypropylene, phenolic, and solid nylon synthetic wheels all fall under this type of caster wheel. While most synthetic wheels are ideal for high-impact and harsh situations, they are louder than softer materials and are less forgiving when colliding with debris.
Phenolic wheels, which are made of phenolic resin and macerated canvas, are a frequent choice for push pull applications. Phenolic wheels are strong and resist grease and other chemicals, making mobility easier. Some synthetic tread materials cannot be used in wet areas, therefore knowing where the wheels will be used is critical when choosing a synthetic tread material.
Gray iron is used to make cast iron wheels. They're abrasion-resistant and start rolling with little effort. These wheels are extremely long-lasting, designed for high-capacity applications, and can tolerate tremendous heat. This type of caster wheel can operate on concrete and smooth steel surfaces. Some of the specs found on this caster wheel include hardness of 90-95A; Brinell 145. The wheel has bearings which include a roller, precision ball, and delrin. This type of caster wheel can operate in the following conditions: mild chemicals, oily and greasy areas, metal chips on the surface, high heat (+250°F), and extreme cold (+45°F).
To reduce guiding and rolling effort, the flanged wheel is designed to run on steel tracking. Rolling on tracks has the added benefit of lowering the toll of load capacities on floors, allowing for bigger capacity, simpler rolling, and floor protection. For great strength and long wear, the majority of these wheels are made of cast iron and steel.
These wheels have a hardness of 130 – 150 brinell. Bearing utilized on these wheels may include: a plain bore, straight roller, and precision tapered roller. Flanged caster wheels can operate within a temperature of 800°F given it has proper bearings and lubrication. This type of caster wheel can operate in the following conditions: mild chemicals, oily and greasy areas, and metal chips on the surface.
These wheels are utilized when the loads are too heavy for floor protecting wheels or where floor protection is not a concern. The solid wheels are unbreakable in normal use, can tolerate high temperatures, and absorb shock and impact without failure. Forged steel wheels outperform ductile steel wheels in terms of load capacity, impact strength, and rollability of all caster wheels.
Forged steel caster wheels can be operated on concrete and smooth steel surfaces. The hardness of forged steel (Drop forged) is Rockwell 80B. Bearings that can be utilized include plain, tapered, Teflon, and roller bearings. These caster wheels can operate under the same conditions which are mild chemicals, oily and greasy areas, and metal chips on the surface.
These wheels are composed of a nylon and glass combination and are engineered to withstand extreme temperatures. These wheels are tough, non-marking, resistant to hard impacts, long-lasting, and oil, grease, and cleaning agent resistant. Glass filled nylon caster wheels have a hardness of 65D. These caster wheels utilize either plain, roller, or spanner bearings.
Glass filled nylon wheels can also operate within the temperature range of up to 490°F continuous or 550°F intermittent. These caster wheels are also suitable to be operated on the following floor types: carpet, brick and concrete, linoleum, asphalt, terrazzo and wood, smooth steel, and tiled floors. These wheels can operate in an environment with the following conditions: water clogged, steamy, mild chemicals, oily & greasy, metal chips, high heat (+250° F), extreme cold (+45° F), and even with animal fats on the ground.
Molded in one piece, black or gray is the most common color. Hard rubber wheels have a larger load capacity than soft rubber wheels and will not flatten while sitting under loads, unlike soft rubber wheels. They have good rolling ability, are simple to start, and are long-lasting. Most chemicals, oils, grease, solvents, and cleaning agents are resistant to hard rubber wheels. These are not non-marking wheels. These rubber caster wheels have a hardness of 70-80 D.
Bearings that are utilized include plain, ball, and delrin bearings. Operating temperatures for these caster wheels are -40°F to 180°F intermittent. They can be utilized on the following floor types: carpet, brick and concrete, linoleum, asphalt, Terrazzo, wood, smooth steel, ribbed steel, and tiled floors. Hard rubber caster wheels can operate in the following conditions: water on the surface, steamy areas, mild chemicals, metal chips on the floor, and extreme cold such as +45°F. Hard rubber caster wheels bring about noise reduction and floor protection.
Rubber wheels with air inside that provide optimal floor protection and the capacity to roll over diverse obstacles. Pneumatic wheels provide cushioning and stress absorption, making it suitable for transporting sensitive loads over a range of floor surfaces. Pneumatic caster wheels are well suited for aerospace and other applications.
These wheels are a lightweight, cost-effective strong tread wheel that can endure harsh impacts. They protect the floor, are non-marking and non-conductive, and resist abrasion better than hard rubber wheels. These wheels are resistant to water, oils, grease, solvents, and many chemicals, making it ideal for application in bakeries, dairy, food processors, meat processing, laundries, supermarkets, warehouses, and manufacturing.
The extra thick, perfectly molded gray rubber tread is chemically bonded to an aluminum core for remarkable robustness and movement on these wheels. On rough surfaces, these wheels give a quiet, cushioned ride. These non-marking, non-conductive wheels provide exceptional floor protection.
Gray iron castings are used to make these wheels. The load is directed to each face of the inverted angle iron track by the 90° grooves drilled into the face of the wheels. V-Groove wheels can also be used to manage the flow of a load over vast distances in a variety of procedures. For big loads, these wheels are perfect. The "V" groove's design ensures optimal weight distribution per wheel.
For heavy-duty industrial casters with brakes, brakes are a popular alternative. Brakes allow users to stop and keep carts in place, which can be useful in some situations or boost safety by minimizing the risk of a runaway cart. There are numerous varieties of caster brakes available, each with its own set of characteristics. This article will go through a few of the most common heavy-duty caster brake designs.
A polyurethane cam is used in the polyurethane cam caster brakes. The cam is then utilized to lock the wheel in position by tightening a plate against the wheel's running surface. A number of mechanisms, including handles and levers sculpted directly into the cam, can be used to operate the cam. The cam brake is made of polyurethane and has an excellent holding force that may be modified based on how far the cam is turned into the wheel. Another advantage of this sort of brake is that the actuation method can be done with the feet, which eliminates operator strain from bending down to actuate with a hand. These brakes can be installed on a caster's leading or trailing edge.
Face contact brakes work by pushing a plate onto the wheel's running surface using a threaded rod. A handle is affixed to the threaded rod, which is tightened by hand. These brakes provide a strong holding force and are suitable for heavy-duty applications. These brakes can be installed on a caster's leading or trailing edge. The disadvantage of this form of brake is that it requires the operator to bend over and tighten or loosen the brake by hand, which puts more strain on the operator and takes longer than a foot actuated brake.
Side brakes work by pressing a washer into the wheel’s hub when a foot pedal on the side of the caster is pressed. Locking and unlocking these brakes is simple and can be done with the operator's foot. They also take up very little space because they are attached to the caster’s side and fit within the caster wheel's swivel radius. The disadvantage of these brakes is that they don't have a lot of holding power and so are better suited for light-duty situations. These are only a few of the most common brake designs for industrial casters with brakes. The caster application's operation and safety can be improved by selecting the right brake design.
This chapter will discuss the applications and benefits of caster wheels. It will also discuss the maintenance of caster wheels.
In the home, standard light duty casters are frequently used to move and support furniture and appliances. Shelving units, such as TV stands and desks, can be outfitted with decorative casters. Heavy-duty casters, on the other hand, are commonly seen in industrial plants, warehouses, and other huge objects that require mobility.
Heavy-duty caster wheels are used to move heavy work items, assemblies, and equipment in the aerospace and aircraft production process. Heavy-duty casters are an important component of aircraft engine stands because they allow the technician to easily move and lock the work stand. On aircraft tow bars, heavy-duty casters with high-speed bearings are also used.
Heavy-duty wheels can also be found on aviation hangar doors, which is a unique application. Although rigid heavy-duty casters for hangar doors are available, they must be able to handle the weight of the massive doors. The doors can be simply moved by one or two people or by an automatic switch, thanks to these casters. Heavy duty casters are also used on helicopter landing pads and dollies to manage a heavy helicopter after it has landed.
When landing dollies are equipped with heavy-duty wheels, the landing platform gains more stability and maneuverability. Heavy duty casters are frequently used to move loaded or unloaded containers. These casters are mounted directly to shipping containers using a unique corner fitting bracket.
Caster wheels are used in supermarkets to move the shopping carts carrying groceries. Hospitals aren't like assembly lines; they don't operate on the principle of "patients in, patients out." Patients' safety and comfort are prioritized at all times. The better they are treated while they're under the hospital’s care, the more likely they are to recover and thrive. This is why movement – and particularly smooth mobility – is so important.
Endless hours laying in a hospital bed while resting or waiting for a procedure to begin can be soul-destroying. Patients are frequently responsible for moving personal health monitors in order to get a change of environment. It's crucial that mobility isn't hampered, and smooth-rolling, dependable casters are essential for this. Patients must be wheeled from the beds to surgery, recovery, and then back to the beds throughout the hospital.
Shock absorption is excellent. Pneumatic wheels are appropriate for situations with uneven or rough terrain or where the cart contents must not be subjected to unexpected shock loads. These wheels are used for both on-and off-road applications. Because they can withstand the unevenness of off-road terrain, these wheels are ideal for applications that require both off-road and on-pavement operation.
Noise Attenuation: Reduces noise, which improves working conditions. Because of the soft rubber tread and stress absorption capacity of pneumatic tires, they are also quiet when in use. Loud noises that can harm hearing are reduced, and working conditions are improved. The flooring will not be harmed. The softer wheel protects floors from scratches and other damage as well.
Wheels and casters reduce physical strains and demands on employees when moving big loads because they promote motion.
Wheels and casters aid to speed the movement of component parts and inventory within a plant, making storage and manufacturing operations easier.
Casters are extremely simple to use since they are designed to provide optimum support with the least amount of resistance. On any supermarket or grocery store shopping cart, caster wheels can be seen in action. The wheels of the cart will normally turn with it, but the cart frame does not have to move. The supermarket's wheels produce the least amount of resistance against the floor, and the same is true of the industrial casters that make moving any big machine or equipment much easier.
Casters have the advantage of handling a lot of weight without breaking. Because the caster wheel revolves around an axle and a bearing race, it is subjected to far less direct pressure than a conventional wheel. Because the wheel moves instead of the chassis when it turns, the load bearing capability is far higher than a standard wheel.
Another advantage of caster wheels is that they come in a variety of shapes, sizes, and materials. Larger caster wheels will reduce the amount of effort necessary to move heavy objects and will be more durable while moving gear and equipment that weighs more than a person can move.
Before deciding if a pneumatic wheel is ideal for the application, there are a few things to consider, such as the amount of force required to begin it rolling. The initial push force is higher due to the bigger footprint and deflection of the air-filled tire. Because of the huge footprint, swiveling the wheels is more difficult, and the caster will generally require a longer swivel lead. It's important to keep an eye on the air pressure. Another disadvantage of pneumatic wheels is that they require more maintenance because air pressure must be monitored. Flats are common with these wheels since they are easily punctured. Filling the wheels with polyurethane foam is one approach to get around this. This wheel is classified as semi-pneumatic. They won't go flat because they don't need air, but they will lose some of the cushioning effects.
The maintenance of caster wheels involves considerations such as:
When it comes to ensuring that casters last as long as possible, lubrication is crucial. In most situations, this entails lubricating caster wheels and the fittings every six months or so. It's a good rule to follow, and it should be a regular occurrence when all of a company's casters and other components are inspected, oiled, and tested to guarantee they're in good working order.
However, it should be emphasized that the six-month duration is not universally recommended. Because of the nature of several varieties of casters, they're typically utilized in volatile situations where they become wet. Other casters work with materials that are highly caustic on a regular basis. Casters should be checked and greased on a much more regular basis in each of these situations. Casters should be greased at least once a month if they are exposed to moisture or corrosive compounds frequently.
The hardware fittings that keep the wheel from moving — or falling off completely — are just as crucial as the caster's lubrication. These vital pieces of equipment are prone to wear and tear, especially because they work against gravity on a daily basis in most locations. Every item with casters should be flipped on its side once a month. Then, business managers should start looking at the gear that connects the caster to the machine. That involves looking for nuts, bolts, screws, and other fasteners that maintain the wheel in place.
Anything that is crooked, worn, or out of place should be repaired or replaced as soon as possible. Minor flaws can steadily deteriorate a caster and necessitate its replacement in some cases, so it's critical that they're addressed sooner rather than later.
Lubrication and fastenings are necessary, but the caster wheel's integrity is also crucial. In most situations, casters are equipped with a little tread or rubber fitting that lets them turn more smoothly and quietly. The floor on which these treads are rolling may cause them to flatten or be somewhat damaged. Such flaws can cause unnecessary wear and tear on the caster wheel over time, as well as wreak havoc on the hardware and lubricant solutions applied earlier in the maintenance procedure.
Check the treads and construction of a caster wheel for deterioration on a regular basis. Replace a damaged wheel or tread if necessary before it becomes a larger problem requiring the replacement of the complete caster. Most business owners would benefit from a monthly inspection regimen when it comes to guaranteeing the caster's long-term integrity.
The easiest approach to keep casters in good repair and ensure that they last the entire rated life after purchase is to inspect them on a regular basis. They will survive for many years with proper lubrication, inspection, and maintenance, and will not require costly replacement and installation.
A caster is a non-powered wheel that is designed to be fitted to the bottom of a bigger object and used to move it. Caster wheels are attached on the base of device moving equipment and bring about mobility of those objects. They enable movement of heavy objects with less force being applied. Caster wheels require regular maintenance to live longer in operation.
An adjustable work bench is a tool that allows the user to adjust and regulate the height of the work surface to a more ergonomic and comfortable position for the safe and effortless performance of work...
A lab bench is a specially designed bench or table that is able to assist in the performance of laboratory experiments and tasks, including the handling of reagents and test samples. Part of the design process for...
A pallet rack is an upright structure made of steel framing with beams and connectors that are bolted, welded, or clipped together to form a shelving unit to store inventory and equipment. In warehousing, pallet racks are...
A polyurethane bushing is a friction reducing component that is placed between moving and stationary components as a replacement for lubricants. The use of polyurethane for the production of bushings is due to...
Polyurethane molding is the process of fabricating or manufacturing plastic parts by introducing a urethane polymer system into a tool or mold and allowing it to cure. Like any other type of plastic, the excellent processability...
Polyurethane rollers are cylindrical rollers covered by a layer of elastomer material called polyurethane. Depending on the application, the inner roller core is prone to scratches, dents, corrosion, and other types of damage...
A portable workbench is a flexible and mobile work surface that is designed to function in multiple environments for the purpose of preparing, constructing, or servicing a wide variety of industrial and commercial applications...
Storage rack, also known as racking, is a structure that stores items and materials and comprises at least two upright (vertical) frames, horizontal beams, and some sort of decking (bars, panels, meshes, or none)...
Urethane casting is the process of injecting polyurethane and additive resins into a soft mold usually made of silicone elastomer. The casting process is similar to injection molding; injection molding differs by using hard, metal molds...
Urethane wheels are wheels made of molded urethane, also known as polyurethane. Urethane is an elastomer that comprises urethane carbamate linkages and is a portmanteau phrase for elastic polymer...
Warehouse racking, also known as storage or pallet racking, is a material handling system suitable for mass storage of goods unitized on skids or pallets. It allows efficient utilization of space while providing easy access to stockpiled items for better inventory control...
A workbench is a sturdy flat, smooth, molded surface that comes in a variety of sizes designed for specific tasks. They can be very complex for engineering design work, complicated machining, and intricate precision tooling or be a highly finished wood table for woodworking, metal work, and project design...