Mailing Tubes
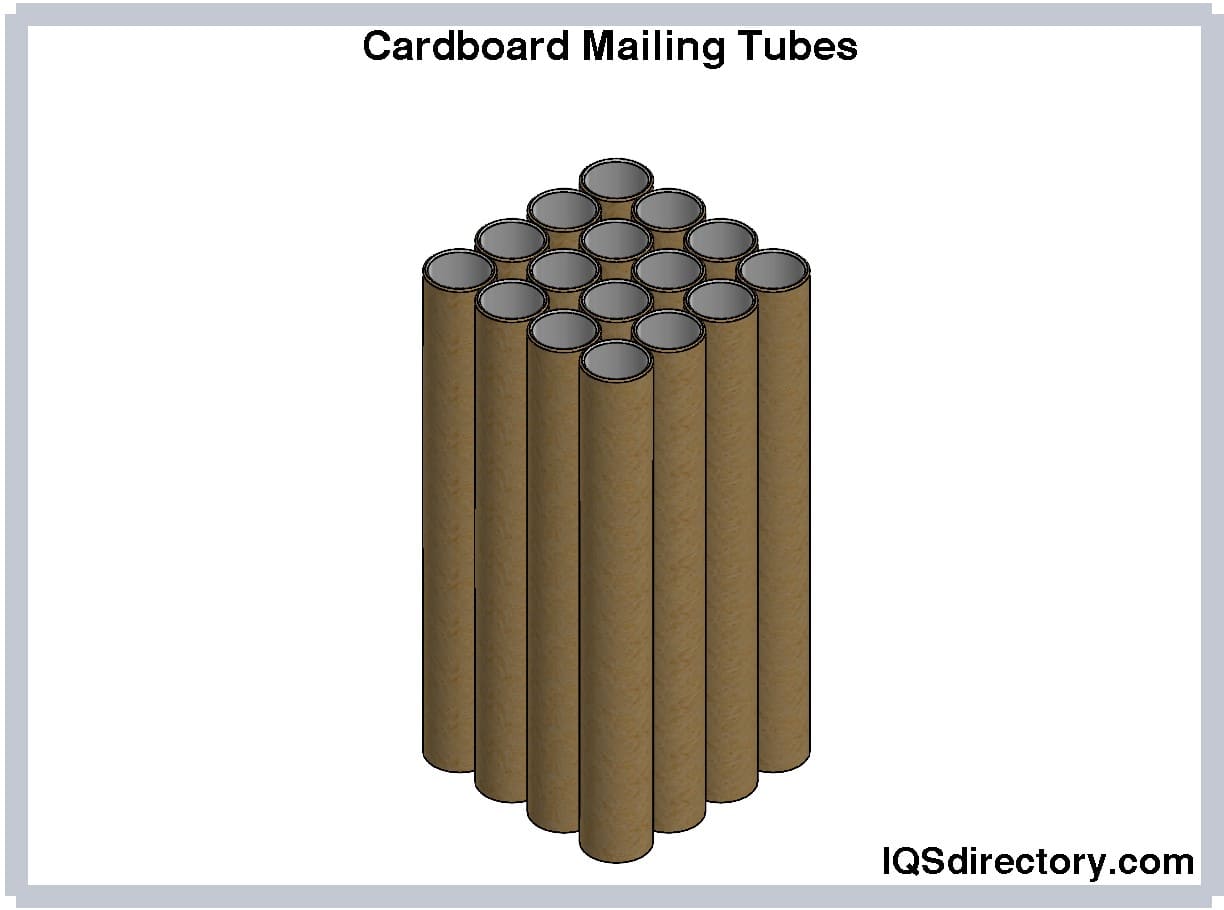
A mailing tube is a sturdy, solid, and durable cardboard container designed for shipping long slender devices and products or rolled up maps, banners, and posters. The indestructible exterior of mailing tubes...
Please fill out the following form to submit a Request for Quote to any of the following companies listed on
This article contains information regarding Sonotubes® and their use.
You will learn more about topics such as:
A Sonotube® is a cardboard concrete forming tube made of waxed paper or lamination that is wound into a tube into which concrete is poured to create supports, columns, and supports for posts. Sonotube® is a registered trademark owned by SPC RESOURCES, INC.They are made of fiber, plastic, and composite materials and are used for a variety of applications, from DIY projects to the construction of large buildings. According to the application, they vary in size from ones small enough to be purchased at the local hardware store to others several feet long with diameters measured in feet.
To create a column or support, Sonotubes® are positioned properly and securely. Concrete is poured into them and left to set. Once the concrete has cured and set, the tube is cut away, leaving a durable strong support or column.
The different sizes of Sonotubes® can fit any application, which one is chosen depends on the design of the structure, building codes, and the supporting soil. Sonotubes® can withstand water for 24 hours with custom designed ones capable of withstanding water for 72 hours.
To form columns and supports of the exact dimensions, concrete forms must have smooth flawless interiors and be able to withstand the pressure produced by poured concrete and maintain their shape. For a long time, creating supports required the construction of wood or steel molds that took time to assemble and disassemble. The time and effort involved in the process delayed and slowed construction, and columns produced from the process did not have a smooth and even surface.
The introduction of Sonotube® forms has removed the labor intensive time consuming methods for creating molds, forms, and castings for column making and radically simplified the process. Sonotubes® have made it possible to efficiently place columns and supports that have exceptionally smooth surfaces that are cost effective and structurally sound.
The strength of Sonotubes® is due to the tightly wound fibers that are adhesively bonded to produce a smooth and uniform surface. The process includes wrapping ribbons of heavy paper, cut into strips, around a mandrel, and sealed by a pressure roller.
The invention of Sonotubes® opened a whole new world to architects, contractors, and designers since they provided the flexibility and adaptability to easily place columns without the concerns of fitting a form or mold. Sonotubes® are a convenient alternative for forming columns that provide a faster, easier, and more efficient method.
The many sizes of Sonotubes® make it possible to adapt them to a wide range of applications. The most common is columns forming as supports for buildings, patios, cabanas, and other structures. Though Sonotubes® are made of paper tightly wound to form a sturdy cylindrical shape, they are sufficiently strong to hold several yards of concrete. This factor, added to their cost, makes them an ideal choice for the construction of structural supports.
The chart below provides a brief overview of the available dimensions of Sonotubes® with the cubic yards of concrete required for the various column heights.
Each manufacturer produces Sonotubes® of different sizes but offers custom designs to accommodate customer requirements.
Forms of Sonotubes® | |||||||
---|---|---|---|---|---|---|---|
Diameter in Inches | Column Height in Feet | ||||||
3 | 6 | 8 | 10 | 12 | 16 | 20 | |
6 | 0.02 | 0.04 | 0.06 | 0.07 | 0.09 | 0.12 | 0.15 |
8 | 0.04 | 0.08 | 0.1 | 0.13 | 0.16 | 0.21 | 0.26 |
10 | 0.06 | 0.12 | 0.16 | 0.2 | 0.24 | 0.32 | 0.4 |
12 | 0.09 | 0.18 | 0.23 | 0.29 | 0.35 | 0.47 | 0.58 |
14 | 0.12 | 0.24 | 0.32 | 0.4 | 0.48 | 0.63 | 0.79 |
16 | 0.16 | 0.31 | 0.41 | 0.52 | 0.62 | 0.83 | 1.03 |
18 | 0.2 | 0.39 | 0.52 | 0.65 | 0.79 | 1.05 | 1.31 |
20 | 0.24 | 0.49 | 0.65 | 0.81 | 0.97 | 1.29 | 1.62 |
22 | 0.28 | 0.59 | 0.78 | 0.98 | 1.17 | 1.57 | 1.96 |
24 | 0.35 | 0.7 | 0.93 | 1.16 | 1.4 | 1.86 | 2.33 |
26 | 0.41 | 0.82 | 1.09 | 1.37 | 1.64 | 2.19 | 2.73 |
28 | 0.48 | 0.95 | 1.27 | 1.58 | 1.9 | 2.53 | 3.17 |
30 | 0.55 | 1.09 | 1.45 | 1.82 | 2.18 | 2.91 | 3.64 |
32 | 0.62 | 1.24 | 1.66 | 2.07 | 2.48 | 3.31 | 4.14 |
34 | 0.7 | 1.4 | 1.87 | 2.34 | 2.8 | 3.74 | 4.67 |
36 | 0.79 | 1.57 | 2.09 | 2.62 | 3.14 | 4.19 | 5.24 |
40 | 0.97 | 1.94 | 2.59 | 3.23 | 3.88 | 5.17 | 6.46 |
42 | 1.07 | 2.14 | 2.85 | 3.56 | 4.28 | 5.7 | 7.13 |
All of the various types of Sonotubes® are designed for commercial construction use. The many different sizes provide capabilities that assist in increasing the efficiency of a construction project.
Finish free Sonotubes® are designed for applications that require smooth columns without spiral marks, seams, air bubbles, voids, or other types of imperfections. The interior coating of the tubing creates an exceptionally smooth finish. An added benefit of this type of Sonotube® is a strip cord that makes it easy to quickly remove the form. The limitation on finish free Sonotubes® is the diameter sizes, ranging from 12” up to 36” with cubic yards of cement varying from 0.349 cubic yards up to 3.142 cubic yards.
The manufacture of commercial Sonotubes® requires materials capable of withstanding the demands of commercial construction. The process begins with water resistant paper able to withstand rainfall up to 72 hours. They are made of material that is tear resistant with superior strength and capable of withstanding pressures up to 20 feet.
The superior strength commercial Sonotubes® is the result of a poly woven exterior shaped for the requirements of commercial grade applications. Commercial grade Sonotubes® are available in the complete array of diameter sizes from 6” up to 60” in lengths of 12 to 20 feet.
In mining, blasting Sonotube® tubes are placed in blast holes to maintain their integrity and keep them from collapsing. These highly durable and sturdy tubes are designed to last for days and are made of specialized paperboard to form a watertight seal that is exceptionally water resistant.
Blasting holes are drilled into the face of a rock and packed with explosives that are detonated. The purpose is to crack the rock to allow for further drilling. The holes have to retain their size in order to facilitate the drilling process.
DIY builders Sonotubes® have the same strength and endurance found in commercial Sonotubes® but come in smaller diameters. They are designed for building decks, placing fence and lamp posts, swing sets, and mailbox posts. DIY builders Sonotubes® are available in 6 inches up to 12 inches sizes and can be purchased at any hardware store. They are available in standard lengths up to four feet.
The manufacture of Sonotubes® is similar to the processes used to make tubing for other applications. The main difference between the methods is the strength, durability, and unique construction of Sonotubes®, which requires materials capable of withstanding the stresses produced by poured concrete.
A further difference in the manufacture of Sonotubes® is the size of the tools since Sonotubes® can have diameters of 60 inches, which requires the use of a larger mandrel for winding the strips of paper.
The first step in the process of making Sonotubes® is the trimming of cardboard sheets into ribbons. The sheets are fed from a large roll of cardboard material into a cutting machine that trims them to the appropriate width for being wound onto the mandrel. As the sheets are cut, the ribbons are wound onto a reel.
The ribbons that have been wound onto a heavy metal reel are taken to the winding machine. Several windings are lined up side by side to be wound onto the mandrel, a cylinder shaped whose outer diameter matches the inner diameter (ID) of the Sonotubes®. The winding of the ribbons is completed at less than 90o in a helical fashion such that the windings are not at a right angle to the mandrel. This enhances the strength of Sonotubes® and makes them stronger and durable.
During the winding process, multiple layers of cardboard ribbons are applied that determine the thickness of the Sonotube® and its outside diameter (OD). To meet the strength requirements, Sonotubes®are wound several times to meet the correct thickness and durability.
As the ribbons are wound around the mandrel, a heavy duty foam adhesive is applied such that the ribbons are sealed and secured tightly together to avoid air pockets, bubbles, or voids that would ruin the smoothness of the Sonotube® and damage its strength. The image below is a simplified example of how the adhesive is applied as the paper ribbons are wound.
Specially blended coatings and adhesives provide Sonotubes® with their water resistance, tear resistance, and exceptional strength. These factors are necessary to meet the pressure standards created by poured concrete.
An essential part of the manufacture of Sonotubes® is to ensure that the cardboard ribbons are securely attached. The adhesive applied to the ribbons as they are wound onto the mandrel affixes them such that they cannot shift or move during the winding process. A second measure of the process is a pressure roller that firmly presses the layers of ribbon. As with winding, the pressure roller guarantees that the final product will not have voids, air pockets, or bubbles. The pressure from the pressure roller flattens the ribbons and spreads the adhesive evenly.
Sonotubes® are a convenient and efficient method for forming parts of a construction project. Their firm and rugged material as well as their lightweight, make them easy to use and install. To properly place Sonotubes®, it is important to follow a set of carefully planned steps that ensure the successful completion of a project.
The preference for Sonotubes® is due to their exceptional strength in relation to the material from which they are manufactured. Additionally, in the traditional method for placing columns, a great deal of labor is required to build the structure into which the concrete is poured. This aspect of the process takes a great deal of time, planning, and effort. The time and equipment used to mold, shape, and fabricate them limits the number of columns that can be formed at one time.
Sonotubes® are disposable after one use and do not require exterior support to hold them in place. Several columns can be placed at one time, which dramatically cuts down on construction costs and time. The material from Sonotubes® is recyclable and made from biodegradable paper that can be used to form new Sonotubes®.
The use of Sonotubes® costs much less than purchasing manufactured concrete columns or other supportive structures. A company can purchase several Sonotubes® for far less than buying a set of prefabricated ones that would include the expense of delivery and storage.
Most Sonotubes® are partially buried in the ground and rest on a footing form that supports the column and prevents it from settling. Footings are essential when there is difficulty with the supporting soil. Since the concrete column will rest partially in the ground, it is important that the bottom or base of the hole be level. Water cannot be present in the hole since it will interfere with the placement of the Sonotube®.
The footing base can be round or square and made of plastic. To have the Sonotube® fit properly, the top of the footing should be cut to the diameter of the Sonotube®. This type of footing may not apply to the use of larger Sonotubes® where more substantial and solid footings are necessary. The footing should fit snugly around the Sonotube® such that the tube does not shift when filled with concrete.
It is essential that the Sonotube® be level when it is placed and should be checked to ensure that it is properly plumbed.
Footings can also be made of concrete and shaped inside the hole using wood forms and rebar. They can be premade and placed in the hole with rebar and have concrete poured into the form.
Prior to pouring in the concrete, the hold around the footing and base of the Sonotube® can be refilled with dirt being sure to not push the Sonotube® out of plumb. The compaction of soil around the tube will ensure its stability and make the concrete application easier and efficient.
Several types of concrete can be used with a Sonotube®. The type of concrete will vary according to your geographical location, the type of column you are making, and what the columns will be supporting. It is important to understand the difference between concrete and cement since cement is a concrete component.
Concrete was developed in the 1980s as a replacement for cement and was formed by adding various ingredients that reduced the water that remained after hydration. The mixture of concrete decreased the size of water filled pores, which improved the strength of the material.
Depending on the type and kind of structure being supported, it may be necessary to place rebar in the Sonotube® for increased stability. The rebar will enhance the strength of the concrete mixture and should be placed during the pouring process such that the concrete can hold it in place.
By volume, concrete is 60% to 75% sand, gravel, and rock with 15% to 20% cement and another 15% to 20% water. The water in the concrete reacts with the cement chemically to bind and harden the concrete into a single substantial solid form.
The curing time for the concrete is dependent on the composition of the concrete and the weather. For concrete to completely cure takes about a month but is ready for use far sooner. Curing normally follows this pattern:
These figures are approximations and may vary according to the conditions of the site and the environment. The essential part of a careful curing process is to improve the strength, durability, water resistance, and wear resistance of the concrete. The strength of concrete is dependent on the growth of crystals in the matrix of the concrete, which grow from the chemical reaction of the cement and water.
Sonotubes® are the most eco-friendly, economical, efficient, and effective solution for forming cylindrical column structures. They are an ideal method for forming underground footings as a way to reduce labor costs. The configuration of Sonotubes® makes it easy to cut and remove them without the need for extra machinery or equipment.
The rounded shape of Sonotubes® makes it easy to fit them into any structure. They do not have edges that can chip or crack and have smooth surfaces that will not interfere with the overall design of a structure.
Sonotube® forms are less expensive than metal or fiberglass ones, making it possible to purchase several Sonotubes® for the same cost as one fiberglass form. The multiple sizes make it possible to purchase every size necessary for a project at once.
The lightweight of Sonotubes® is one of their major benefits since it makes it possible to place them with little effort or labor costs. Transporting, maneuvering, placing, and storing of Sonotubes® is far less problematic. Once the tubes are used, the cardboard material can be repurposed, recycled, and reused.
A very obvious benefit of Sonotubes® is how easy they are to install since they do not require any form of construction or heavy equipment. They can be placed by hand, positioned with supports, and have concrete poured quickly and conveniently.
Sonotubes® are ideal for projects that have multiple columns. Instead of waiting for one column to set before moving on to the next, several columns can be placed at once, which drastically cuts into the time of a construction project. All of the columns can be poured at once.
A mailing tube is a sturdy, solid, and durable cardboard container designed for shipping long slender devices and products or rolled up maps, banners, and posters. The indestructible exterior of mailing tubes...
Paper tubes consist of paper or paperboard sheet layers wound together to form strong, hollow, and usually cylindrical shapes. The paper layers are laminated or bonded together using adhesives. The wall thickness of the tube can vary depending on the number of layers wrapped during manufacturing...
A poster tube is a cylindrical, triangular, or rectangular hollow prism that is commonly used to transport rollable, unframed art, important documents, or long and slender materials. They also carry objects like...
A shipping tube is a long container used for mailing long items that are rolled or folded to fit in the tube. They are constructed of various types of materials with Kraft paper being the most common and widely...
A tape and label core is a thick durable tube that forms the center of a label or tape roll with the same shape as that of a toilet paper or paper towel core but is sturdier and more resilient. Although the shape of tape and...
Pressure-sensitive adhesive tapes consist of a backing material film coated with an adhesive intended for relatively low-stress applications. Light pressure, usually done by the fingertips, is applied to initiate the binding. In the sticking process, the fluid properties...
A cardboard box is a shipping container made of thick heavy duty paper known as paperboard, which is more than 0.01 inch or 0.25 mm thick. The term cardboard is used as a generic descriptor for various types of solid firm papers used to produce boxes
Carpet tape is a double-sided tape designed for securing carpets or rugs to the floor. It's made of strong, durable, and adhesive material that can hold the carpet in place and prevent it from sliding or wrinkling. Carpet tape is used in
A corrugated box is a disposable container whose sides are made up of layers of material that include an inside layer, outer layer, and middle layer. The middle layer, between the outer and inner layers, is fluted, which are rigid wave shaped arches that provide cushioning...
One kind of pressure-sensitive self-adhesive tape is foam tape. It has one of several different backing materials and is made of foam. It may have adhesive on one or both sides. Foam tapes are, at their most basic level, tapes that are applied to uneven or
Masking tape is pressure sensitive, thin and very adhesive, easy to tear paper that is used in various tasks ranging from masking off areas that are not to be painted or as insulation for electric wires among other...
PTFE stands for polytetrafluoroethylene and is a synthetic fluoropolymer used widely in many industries and many other applications. PTFE is also commonly referred to as thread seal tape, teflon tape, and plumber‘s tape...