Epoxy Adhesives
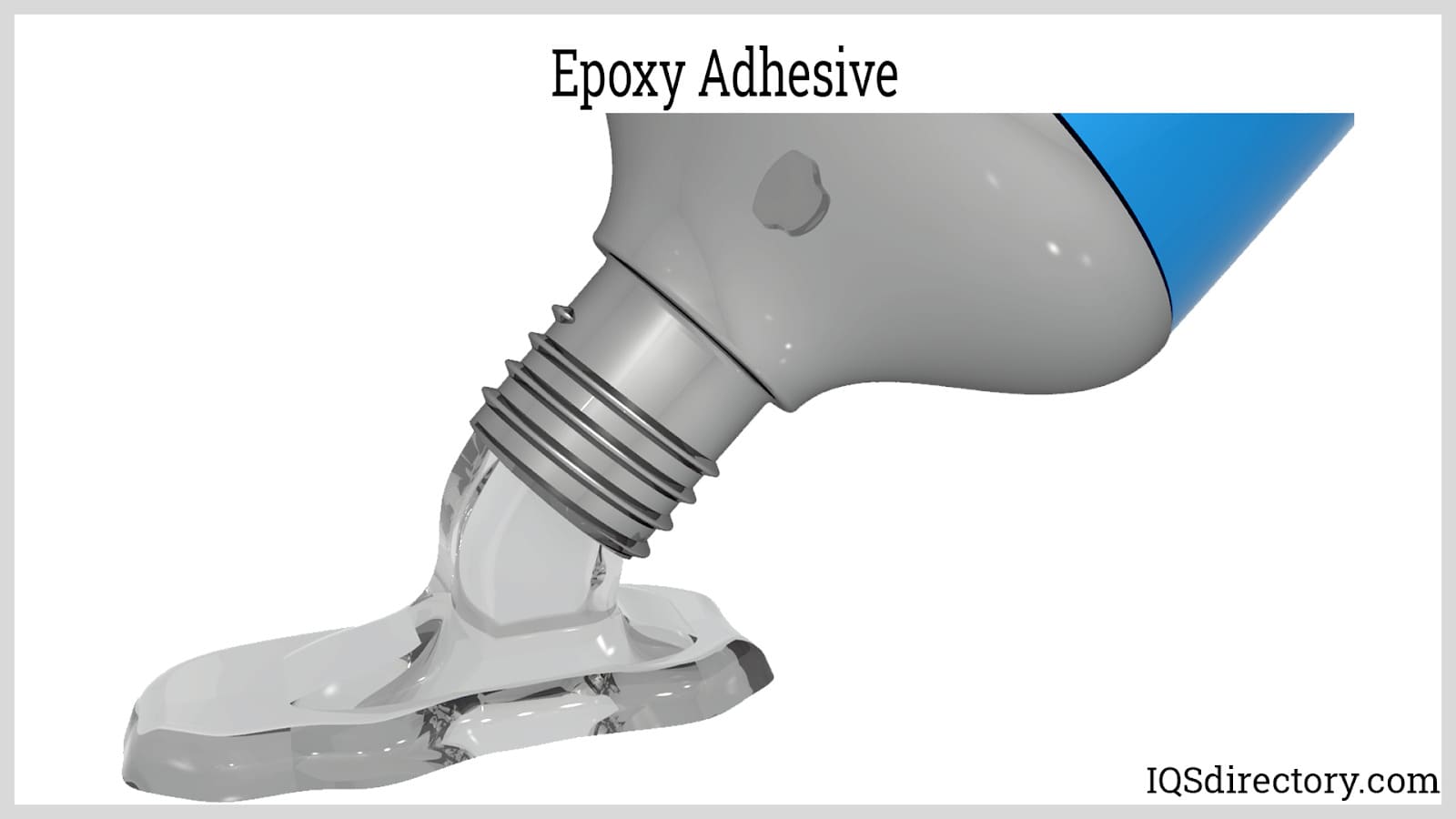
Epoxy: Epoxy glue is a thermosetting adhesive made up of a resin or epoxy polymer and a hardener that is used to adhere or join a range of surfaces together with a strong, permanent, and robust bond that can...
Please fill out the following form to submit a Request for Quote to any of the following companies listed on
This article takes an in depth look at Silicone Adhesives.
You will learn:
Silicone adhesive is a versatile water resistant polymer whose primary ingredient is silica, a common form of sand found in quartz. The term silicone refers to a group of polymers that have a siloxane bond with organic compounds. Their production begins with the isolation of silicon from silica, also known as silicon oxide.
The many positive properties of silicone adhesives has made them a popular choice for a wide range of applications. They are used as a non-toxic alternative to toxic adhesives. Inert and versatile, silicone adhesives are used in a wide array of industries as a safe method for securing and bonding surfaces.
Since silicone adhesives are biocompatible, they are commonly used in the medical field as a bandage adhesive that adheres easily to the skin and creates a tight seal to prevent infection but can be easily removed without leaving a residue. They are long lasting due to their excellent chemical stability and resistance to weathering and moisture. Regardless of the type of surface, whether it is metal or skin, silicone adhesives form a strong long lasting bond.
Silicone‘s special properties make it an exceptionally resilient adhesive. Its elasticity and other properties remain unchanged at any temperature. Silicone adhesives are used to bond metals due to their flexibility and temperature characteristics as well as their ability to bind unlike dissimilar substrates.
The principal ingredient in silicone adhesive is silica, which is a common mineral that is present in sand, soil, granite, and rocks. Silica is a natural compound that is found everywhere in nature and is one fourth of the earth‘s crust. It takes the form of emerald, quartz, clay, and glass.
Silica, known as silicon dioxide (SiO2), is a combination of silicon and oxygen. The three main forms of silica are quartz, tridymite, and cristobalite with celestite, keatite, and lechatelierite being fewer known forms. Silica is a widely used mineral that can be found in concrete and grinding abrasives.
The manufacture of silicone adhesives begins by isolating silica from silicon. Silica can be found in its pure form in some minerals. The most common places to find silica is in sand and quartz. The difficulty in extracting silicon from its natural form is due to its high melting temperature.
Quartz ore is composed of quartz and silica sand. To extract the silica, the quartz ore is crushed to 25mm and then ground. Once the material is ground to the right configuration, it is scrubbed, washed, and put through flotation. The resulting quartz sand is screened for impurities.
The final step in extracting the silicon is to heat the purified sand. Since silicon has a very high melting temperature, the sand has to be heated to 1800° C. The result of the heating process is pure isolated silicon, which needs to cool before further processing. Once the sand mixture is sufficiently cooled, it is ground into a powder.
To make silicone, the fine silicon powder is mixed with methyl chloride and heated. The heating process triggers a reaction between the compounds to form methyl chlorosilane, which contains dimethyldichlorosilane, the main component of silicone. The dimethyldichlorosilane is distilled by being heated at several different temperatures.
After distillation, water is added to dimethyldichlorosilane, which makes it separate into disilanol and hydrochloric acid. The disilanol is condensed by the hydrochloric acid to form polydimethylsiloxane, which contains the siloxane bond, the backbone of silicone. To create the right type of silicone, it is polymerized to make it a rubber based adhesive.
Silicone adhesives and sealants are made from polymerized silicone. When silicone is uncured, it is a highly adhesive gel or liquid. It is a chemically inert substance that is safe for use in a variety of applications and is non-toxic. The final result of the production of silicone adhesives is a flexible heat resistant glue that can be used for electronics, automotive manufacturing, and construction.
There are several types of silicone adhesives and sealants including silicone bond, high temperature, room temperature vulcanizing (RTV), and silicone rubber sealant. The tight flexible seal of silicone adhesives has made them a very popular solution for a widely diverse number of applications.
Regardless of the many varieties of silicone adhesives, there are two predominant types, which are two part and single part. The difference between the two forms is the location of the curing agent, which can determine the drying time of the adhesive.
High temperature silicone adhesive can withstand temperatures in excess of 600° F or 315° C and is resistant to aging, vibrations, and shock. It is a liquid adhesive that has the appearance of a gel. High temperature silicone is an RTV silicone that needs to cure for 24 to 48 hours depending on how thick the application is.
RTV silicone is a mild adhesive that creates a gasket like adhesive when gluing two surfaces and develops a cushiony texture. It is often used for electrical insulation due to its high resistance to weathering and chemicals. RTV silicone begins to cure as soon as it is exposed to the air, unlike other silicone adhesives that take over 24 hours. It is for this reason that it is stored in an airtight container.
Silicone rubber adhesive has all of the typical properties of silicone adhesive. It is often used for marine applications as a means for sealing and waterproofing boats due to its watertight properties. Silicone rubber adhesive does not crack or deteriorate over time.
One part systems do not require the mixing of the glue and the curing agent. They offer all of the benefits of silicone adhesives including the ability to maintain their elastic properties over a wide range of temperatures. One part systems are available in different hardness and viscosities with certain grades having optical transparency. Much like other forms of silicone adhesives, the curing rate is dependent on the thickness of the application.
Two part silicone adhesives have the glue and curing agent separate. They are mixed a short time before application in order to achieve the desired cure and physical properties of the silicone adhesive. The reaction between the curing agent and adhesive begins immediately when they are mixed. The curing process affects the viscosity of the adhesive, which increases until the adhesive is no longer useful.
Fluorosilicone adhesive contains trifluoropropyl, which increases its chemical resistance to solvents, fuels, oils, acids, and alkaline beyond silicone adhesives. It has excellent mechanical properties and bonds well with any type of substrate. It is available in one or two part versions. The curing of the two types of fluorosilicone is similar to the silicone adhesive types where one part cures when exposed to the air and two parts requires mixing.
Pressure sensitive silicone adhesives are made of synthetic elastomers that are resistant to high temperatures and adhere to low energy substrates. They are attached to some form of material such as plastic, cloth, paper, or metal that bonds to a surface when pressure is applied. PSAs are made of polymer chains with large molecules that are interlinked with repeating chains of smaller molecules.
The unique properties of PSAs makes it possible to design and formulate them to serve a variety of purposes including masking tape, film for screen liner protection, and easy to install electronic insulation. They come in a variety of packaging options and are resistant to exposure to extreme climate changes and environments. PSAs bond well with hard to wet surfaces and low energy substrates.
PSAs are long lasting but can be easily removed without leaving any residue. They have been adapted as a biocompatible, hypoallergenic, and non-invasive adhesive for bandages, dressings, and surgical tape. The main attraction of PSAs for medical use is their ability to prevent bacterial growth and keep out harmful substances during the healing process.
Although all PSAs function the same and have similar characteristics, their tackiness and adhesion can be adjusted for different viscosities and cured kinetics. Their properties can be further customized by changing the coating process and varying the substrates. In essence, PSAs can be formulated to specifically meet the needs and requirements of a wide variety of applications.
Silicone pressure adhesives have exceptional bonding strength and act as a flexible sealant with the characteristics of a gel. They have flexibility at lower temperatures and are resistant to UV rays and solvents.
Industrial uses of silicone adhesives have necessitated the development of methods that will cause the adhesive to rapidly cure. Silicone adhesives are widely used due to their excellent elastomeric properties, extended temperature range, resistance to the effects of fuels, and low shrinkage and shear stress. The fast curing of silicone is completed in a little over ten minutes.
Ultra-violet cured silicone adhesive has photoinitiators to activate the curing process. When the photoinitiator absorbs light at the proper wavelength and intensity, the polymerization reaction starts, and the silicone adhesive cures. The curing process takes a few seconds and is a solvent free curing system.
If the UV light is removed, the curing process stops, which makes it essential to continue the process until the adhesive is fully cured.
Fast cure silicone uses a two part platinum system and does not require air or moisture for the initiation of the process. The two parts have a vinyl functional silicone polymer with a platinum catalyst that includes a cross linker and inhibitor. The curing process begins with the addition of the cross linker to the vinyl polymer. It takes nearly 24 hours for the curing process to be completed.
Much like the ultra-violent process, LED curing involves the initiation of a photochemical reaction in the silicone that links the polymers. LED lights can be set to the precise wavelength that fits the needs of the silicone adhesive. They offer more uniform lighting throughout the process, are energy efficient, and environmentally friendly. LED lights are available with wavelengths in the UV range of 365 nm to 395 nm as well as the visible light range of 405 nm to 460 nm.
Aquarium silicone adhesive is an important and necessary part of aquarium maintenance. It is used to keep the tank from leaking and attaching rocks, plants, and decorations. Since it dries clear and is unnoticeable, it is the ideal adhesive for aquarium use. Silicone aquarium adhesive has the appearance of a gel and is exceptionally easy to apply. The curing of silicone aquarium adhesive takes about seven says but maintains its seal in its tacky state.
Silicone adhesives are a widely used adhesive due to their many positive properties, especially their ability to maintain a bond in a varied range of temperatures. They are able to relieve thermal stress between substrates with different coefficients of expansion and contraction.
A major benefit of silicone adhesives is how long they are able to sustain their bond regardless of the environment. This single feature makes them an ideal source for several applications including medical ones.
Ceramic material is a highly resilient, non-metallic, inorganic product that is wear resistant, corrosion resistant, has thermal stability, exceptional strength, and can serve as electrical insulation. There is a wide assortment of products that are available made from ceramics and is a material that engineers rely on. Silicone adhesives offer the ability to bond ceramic material with dissimilar substrates that have chemical compositions that are unsuitable for bonding with ceramics.
Glass is a unique and difficult substrate that is a challenge to bond. Most glass bonding does not involve load bearing seams but is more than likely designed for use in an array of environmental conditions that require an invisible bond. Adhesives for bonding glass have to be strong enough to create a watertight seal but flexible enough such that they do not snap under multi-directional pressure. It is for these reasons that silicone adhesive is the most widely used adhesive for bonding and sealing glass.
Though not as fragile as glass, bonding rubber is a time consuming process that requires significant surface preparation using expensive and hazardous materials. For the bond to hold tight and firm, the surface has to be primed and roughed before applying the adhesive. Elastomeric technology has made it possible to bond many types of rubber. Silicone adhesives are a major development in the ability to bond and seal rubber, expanding its usefulness and number of applications. One part or two part systems can be used with two part systems ideal for rubber since they cure in thick layers.
Silicone adhesives are used for bonding metals because they are able to bond dissimilar substrates. For other adhesives to be able to bond metals, they have to be specially blended and formulated. This is not the case with silicone adhesive. One or two part silicone adhesives are capable of joining any two different metals. Variations in the curing time depend on the amount of adhesive applied and the type of metal.
Silicone adhesive is an ideal product for joining wood and can be applied directly. Since silicone adhesive is very strong, it does not need to be broadly applied but can be placed in critical areas of the pieces to be joined. When working with small pieces, a very limited amount of adhesive is required.
Silicone adhesive is the strongest and most versatile of adhesives. It provides a firm grip, is flexible, and seals as it bonds. The fact that it is resistant to UV rays, temperature variations, and water makes it ideal for use with wood.
Silicone adhesive is a widely used bonding agent that has been popularized by its many positive properties. The raw material for the production of silicone is produced in high volume, which makes it easy to produce the adhesive. Silicone adhesive can be found in every industry from the production of aircraft to the installation of windows.
The base material for the production of silicone is silica, the fourth most abundant mineral on earth. Silica is found in a wide variety of mineral formations, which makes the synthesizing of silicone relatively easy.
A key necessity for adhesives is to have the ability to maintain their bond regardless of any variations in temperature. This particular property is one of the reasons that silicone adhesives are so widely used in industrial applications. The significance of this characteristic is reinforced by silicone adhesive‘s ability to bond to any type of material.
Though silicone adhesive forms a very secure and tight bond, it does not harden and become rigid. For many applications, flexibility in a bonding agent is a crucial necessity since most materials flex with environmental changes. Silicone adhesive is a clear gel during application and cures over time into a flexible adhesive.
Much like the other characteristics of silicone adhesive, its durability in stressful and demanding conditions has made it an ideal choice for aerospace applications and extreme weather. Unlike other adhesives, silicone can withstand many environments where other adhesives fail. Manufacturing and industrial operations require that adhesives be able to endure the production process as well as provide a lasting performance for products.
Though it takes several hours for silicone adhesive to cure, once it is cured and set, it is barely noticeable due to its transparency. This particular trait is the reason that it is used to bond windows and aquariums. Engineers rely on silicone adhesive to perform as a bonding agent but not destroy the aesthetic appearance of a design.
The water repelling capabilities of silicone adhesives can be seen in their wide use in marine applications. When silicone adhesive is applied, it reacts like a sealant and is uninfluenced by water or moisture. Again, this is the reason that is used in aerospace applications and transportation as well as a method for securing windows.
One of the concerns for the application of adhesives is the negative effectives of their fumes. In addition, many highly durable adhesives require significant preparation before being applied. This is not the case with silicone adhesives, which are very user friendly and capable of bonding any two materials regardless of the materials‘ composition.
Modern manufacturing and production have a growing concern for environmental impact and their environmental footprint. Sustainability has become a central concern during the development of new products as society has become intensely aware of the negative impact of various harmful substances.
Since the ingredients in silicone adhesives are taken from natural elements, it has very little impact on the environment. Silicone adhesives are resistant to most chemicals and are non-chemical reactive, a factor that emphasizes its environmental safety.
When engineers are designing and developing a project, every aspect of the project is planned down to the smallest detail, which includes the selection of an adhesive. Industrial applications require that materials be lasting and durable due to the rigorous and stressful conditions to which products may be exposed.
The strength and endurance of silicone adhesives as well as their non-chemical reaction have made them the first choice for many industries.
The harsh and unrelenting conditions of outer space place a great deal of strain and stress on the materials used to produce spacecraft. Pressure, atmospheres, and sealing requirements demand the most substantial of adhesive materials. Silicone adhesives have been found to be capable of meeting all of the requirements.
In the film industry, prosthetics are applied to the skin of actors to create various types of illusions. For many years, several forms of adhesives and bonding chemicals have been tried, with some very deleterious effects. Over the last few decades, silicone adhesives have been found to be the best method for securing and applying prosthetics. It is odorless and does not cause discomfort to the skin. Once the prosthetic has been placed, the curing process is activated by pressing on the prosthetic.
The elasticity of silicone adhesives makes them an ideal glue for use in dentistry. Since silicone adhesives are chemically inert, they are safe to use in placing prosthetic appliances in the mouth. In most cases, dentists apply appliances, glue it in place, and cure the adhesive with an ultraviolet light.
There is a wide array of materials used in the automotive industry, which includes plastics, aluminum, steel, stainless steel, and various fabrics. In many cases, unlike materials need to be tightly joined and have a secure bond. It is for these reasons that silicone adhesives are used. They offer excellent adhesion to a variety of substrates and are long lasting.
Some of the reasons that automobile producers prefer silicone adhesives include durability, weathering resistance, waterproof, impact resistant, does not crack or peel, and makes a flexible bond.
Medical products have several intricate parts that have to be permanently joined and tightly sealed. Silicone adhesives are used due to their ability to bond and adhere unlike surfaces. Medical products are made using polycarbonate due to how easily it can be shaped and molded. Also, polyamide, or nylon, is used for tubing and catheters as well as titanium, which is used for implants like pacemakers, cochlear implants, hydrocephalus shunts, and infusion pumps.
Each of the materials used to produce medical products are required to follow the strict guidelines of the American Medical Association (AMA) and the Food and Drug Administration (FDA). Silicone adhesives are inert and ideal for use in the manufacture of medical products. They provide a very tight seal and are long lasting, which is a necessity for medical devices.
Food grade silicone adhesive is non-toxic and does not contain chemical fillers. It is far safer than normal glues and adhesives and provides a superior bond. Food grade silicone adhesives are durable and resistant to temperature changes, moisture, ozone, vibrations, and weathering.
Epoxy: Epoxy glue is a thermosetting adhesive made up of a resin or epoxy polymer and a hardener that is used to adhere or join a range of surfaces together with a strong, permanent, and robust bond that can...
Hot melt adhesives are also known as glue adhesives. They are thermoplastic polymer adhesives that are solid at room temperature. Hot melt adhesives liquefy if heated to a temperature above their softening point...
Pressure-sensitive adhesive tapes consist of a backing material film coated with an adhesive intended for relatively low-stress applications. Light pressure, usually done by the fingertips, is applied to initiate the binding. In the sticking process, the fluid properties...
Carpet tape is a double-sided tape designed for securing carpets or rugs to the floor. It's made of strong, durable, and adhesive material that can hold the carpet in place and prevent it from sliding or wrinkling. Carpet tape is used in
One kind of pressure-sensitive self-adhesive tape is foam tape. It has one of several different backing materials and is made of foam. It may have adhesive on one or both sides. Foam tapes are, at their most basic level, tapes that are applied to uneven or
Industrial coatings are a type of substance that is spread over a surface of various derivatives like concrete or steel. They are engineered chemically to give protection over industrial products that include pipelines and...
Labels are an important aspect of product packaging, identification, presentation, and traceability. They are a way of communicating the manufacturer to the customers and the rest of the world. Labels promote the brand of the product and...
Masking tape is pressure sensitive, thin and very adhesive, easy to tear paper that is used in various tasks ranging from masking off areas that are not to be painted or as insulation for electric wires among other...
PTFE stands for polytetrafluoroethylene and is a synthetic fluoropolymer used widely in many industries and many other applications. PTFE is also commonly referred to as thread seal tape, teflon tape, and plumber‘s tape...