Plastic Materials
The term "plastics" refers to a broad group of materials and products that are derived from the processing of polymer resins. These long chains of molecules consist of several smaller monomers held together by covalent bonds. This generic formula underlies a tremendous number of specific chemical formulations that create a diverse field of different plastics, including such things as acrylics and polystyrene products. Each type of plastic has unique properties, such as varying levels of tensile strength, wear resistance, dimensional stability, machinability, temperature resistance, chemical resistance, impact resistance, transparency, moisture absorption and electrical properties.
Quick links to Plastic Material Information
The History of Plastics
Early Use of Plastics
While many people tend to think of plastic as a relatively recent invention, it is actually neither recent nor an invention, per say. Rather, the use of natural plastic materials goes back thousands of years. Early plastics were bio-derived, organic polymers, such as egg and blood proteins. Also, around 1600 BC, native peoples living in the region between present-day central Mexico and northern Costa Rica were using natural rubber figurines, bands, and balls. By the Middle Ages, people were using cattle horns treated with material derived from casein (milk proteins), a component of early plastics.
Plastics in the 1800s
It was in the 1800s that chemical engineers began developing synthetic plastics as we know them today. One important mile marker in plastic’s history was Charles Goodyear’s discovery about vulcanization. He discovered that you can thermoset plastic materials derived from natural rubber, via vulcanization. Nitrocellulose, or Parkesine, is widely considered the first man-made plastic. It was made from cellulose treated with a chemical solvent of nitric acid, then dissolved in alcohol. When dissolved, it would harden into an elastic, transparent material that one could heat up and mold. It could also accept pigments. Patented in Birmingham, England by Alexander Parkes in 1856, he revealed his invention to the public in London at the 1862 Great International Exhibition. That same year, Parkesine won a bronze medal at London’s World’s Fair. In 1868, John Wesley Hyatt invented a synthetic plastic called celluloid, which was similarly derived from cellulose and alcoholized camphor. He invented this plastic in order to replace ivory billiard balls with something else. Next was the invention of casein plastics, which were milk proteins mixed with formaldehyde. This took place in 1897 in Germany. In 1899, Arthur Smith received a British patent for processing formaldehyde resin to make electrical insulation. His process was improved upon a bit later, in 1907, by a man named Leo Hendrik Baekeland. Using his own techniques, Baekeland invented the first commercially successful fully synthetic plastic resin, which he later named "Bakelite."
Plastics in the 1900s
In 1908, Swiss textile engineer Jacques E. Brandenberger invented a plastic product we still use today, cellophane. His goal was to invent a clear, flexible film to put on top of cloth and make it waterproof. While his invention did not end up being used for that purpose, it ended up being quite popular for others. For example, his first American customer was Whitman’s Candy Company, who used Cellophane to wrap their chocolates.
After World War I, thanks to advances in chemical technology, the world experienced a huge boom in plastic materials development. Then, around World War II, mass plastic materials and product production began. Some of the earliest mass-produced plastic polymers were polystyrene (PS), polyvinyl chloride (PVC), polyethylene and polyethylene terephthalate (PET). The 1950s saw great plastic development as well. For example, in 1954, Dow Chemical invented expanded polystyrene, which they used for cups, packaging, and building insulation. In 1957, mass production began on polypropylene, which had been discovered three years earlier by Giulio Natta.
Since the 50’s, scientists and chemical engineers have continued to diversify the polymers and plastics industry. They’ve also found ways to produce plastic products with more consistent and precise results. In the last 20 years or so, they have turned their eyes to sustainability of polymers and polymer production. Because plastic is so pervasive and rarely biodegradable, we now have great concerns over their potentially harmful impact on the environment. To that end, chemical researchers are now looking into bioplastics made from synthesizing polyethylene from ethanol obtained from sugarcane. There could soon be a present where all plastic products are biodegradable. However, until bioplastics are developed enough to be mainstream, it is the responsibility of each consumer to diligently recycle the thermoplastics used on a daily basis so they might be reused. You can find thermoplastics manufacturers working to develop these types of products on IQS Directory's company listings
The Benefits of Plastic
Though you must be diligent to recycle them, there are many benefits to plastics. First, they are incredibly versatile. They can take on virtually any shape, color, texture, and dimensions. Plus, they can be made to exhibit nearly any property under the sun. Next, they are lightweight, yet durable. In addition, they are easy to work and quite inexpensive. Finally, they are recyclable, a quality that is of the utmost importance.
Plastic Production Process
Raw Material Production
The processes required to form specific plastic materials vary significantly. Suspension, emulsion/dispersion, mechanical mixing, solution, and mass methods are commonly used to produce the resins, liquids, gels, and powders that manufacturers distribute. While this raw form is used for thermosetting plastics that undergo only one manufacturing process, most plastic suppliers provide thermoplastics in stock solid shapes that have undergone some initial processing. The shapes and performs provided are more easily handled that way, and in some instances, may be used as the final product.
Plastic manufacturers can combine the raw plastic materials with a number of additives such as heat stabilizers,lubricants, fillers and plasticizers for custom plastic fabrication. These can have a significant impact on the color, strength, density, working temperature range, structural integrity and corrosion and heat resistance of a polymer.
Thermoplastics vs. Thermosetting Plastics
Plastics made of synthetic, natural and organic monomers are divided into two categories: thermoplastics and thermosetting plastics. While the names are very similar, it is important to distinguish between the two when selecting the proper material for a given application. The former, thermoplastic, is more commonly used because it can be melted and remolded numerous times. The composition is formulated to become pliable when heated and rigid when cooled. The pitfall of thermoplastics is that they may become glass-like and fracture at extremely cold temperatures. Thermosetting plastics are more adept to cold applications but chemically deteriorate when subjected to high heat. While thermoplastics can be purchased as pellets or any number of stock shapes for secondary processing, thermosets are available only in two-part liquid resins or non-flowing mass premixed blends. Far more limited in their possibilities, thermosets cannot be remolded after curing and must, therefore, be supplied in raw form or finished products. Cure technology is as diverse as plastic itself and includes air setting, film drying, anaerobic, hot melt, cross-linking, room temperature curing, and vulcanizing. The cure technology and type of polymer used depends largely on the manufacturing processes and purpose of the complete product.
Manufacturing Processes
Plastic sheets, pipes, profiles, and rods, which are the most common stock shapes, are usually produced through manufacturing processes like plastic injection molding or plastic extrusion. Films are made using blown film extrusion, in which an extruded tube of plastic is inflated to stretch the material to the desired length and thickness. Some films are available as thin as .0004 inch.
Manufacturing processes plastic manufacturers use in addition to plastic injection molding and plastic extrusion include foam extrusion, rotational molding, precision plastic machining, vacuum forming, pressure forming, thermoforming, casting, pultrusion, welding, and grinding. Each method uses heat and pressure to combine the resins before cooling to create the final form.
Plastic Images, Diagrams and Visual Concepts
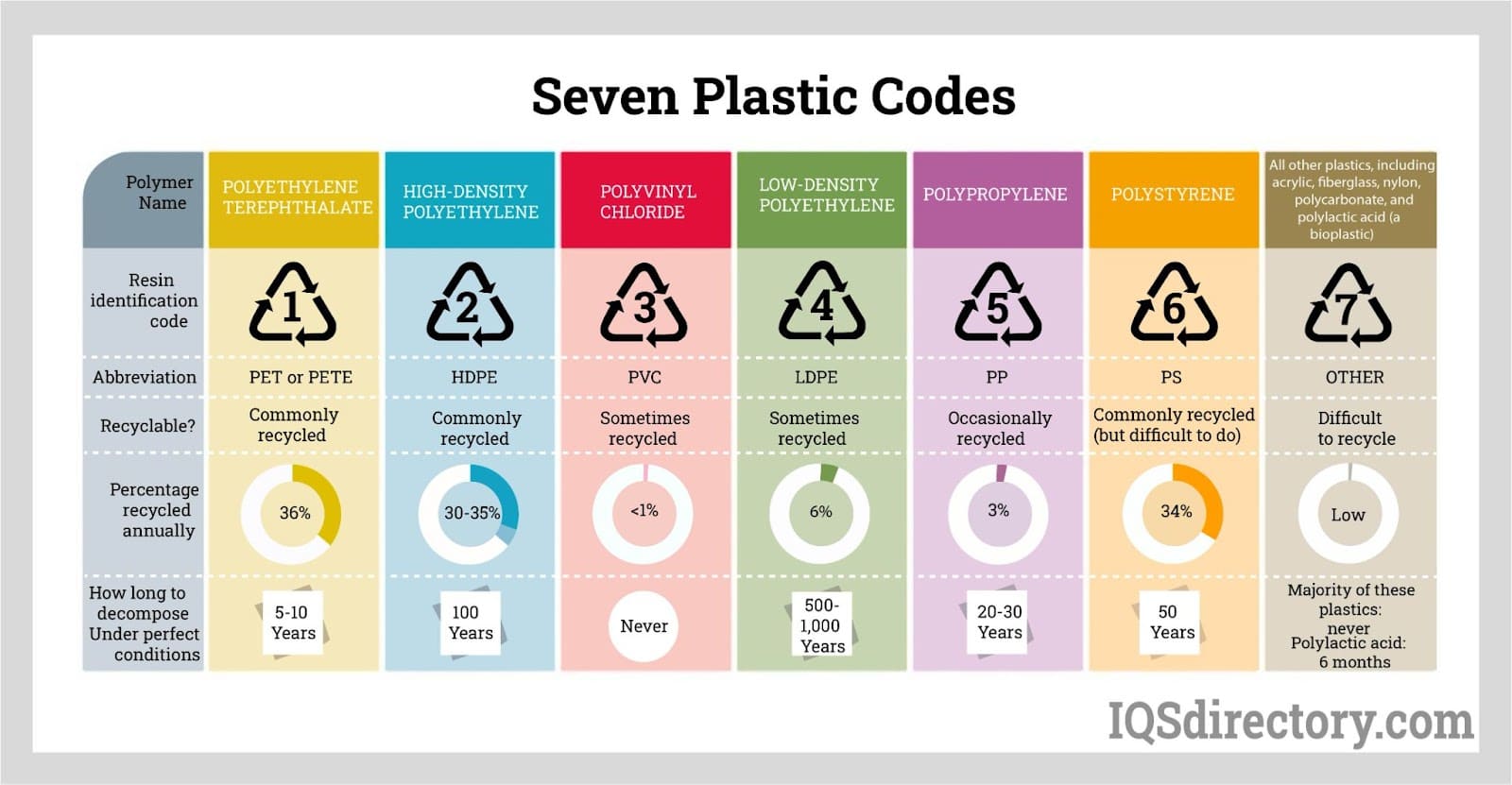
The seven types of plastics that are used the in production of plastic.
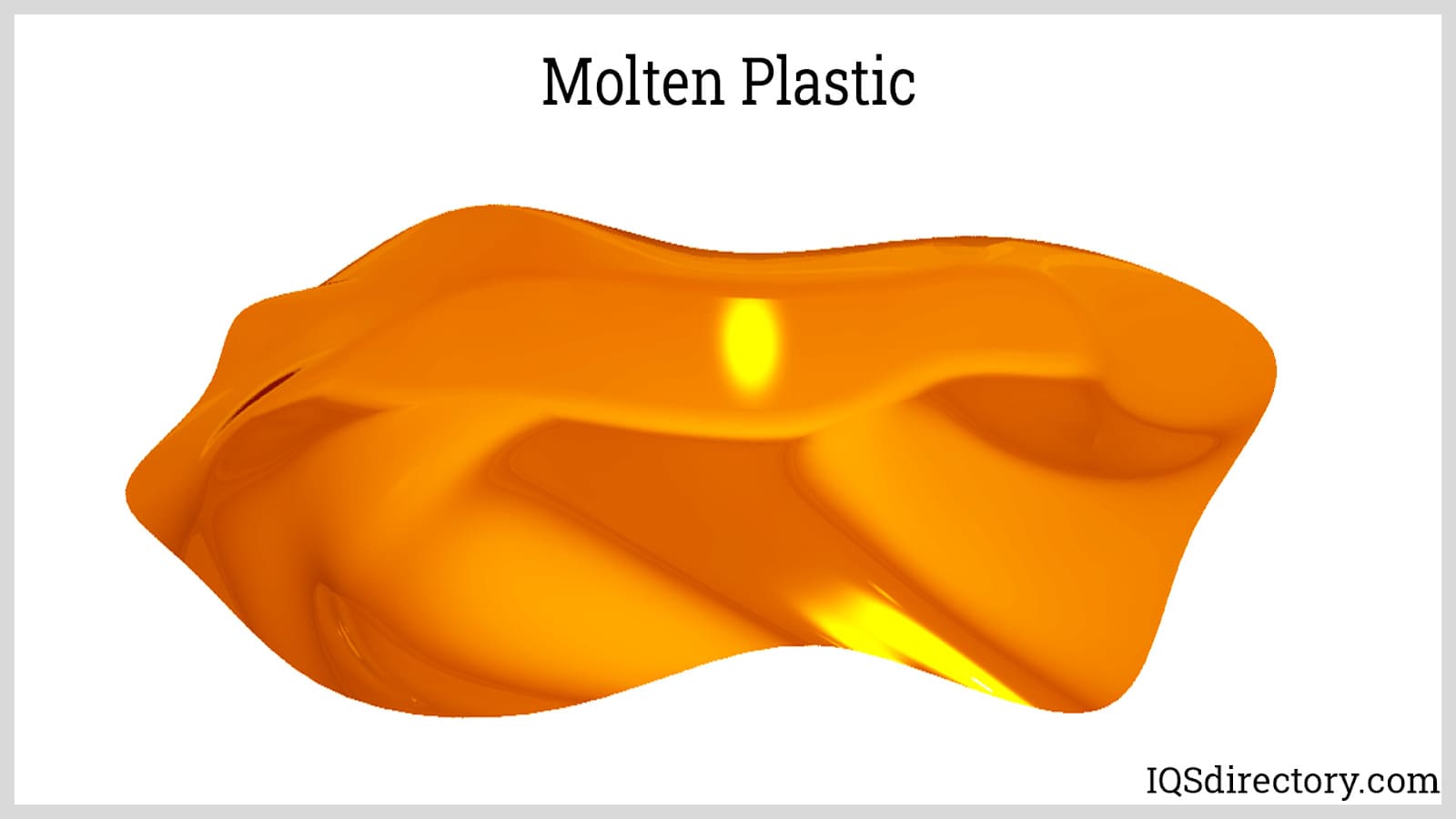
Plastic in it heated molten form.
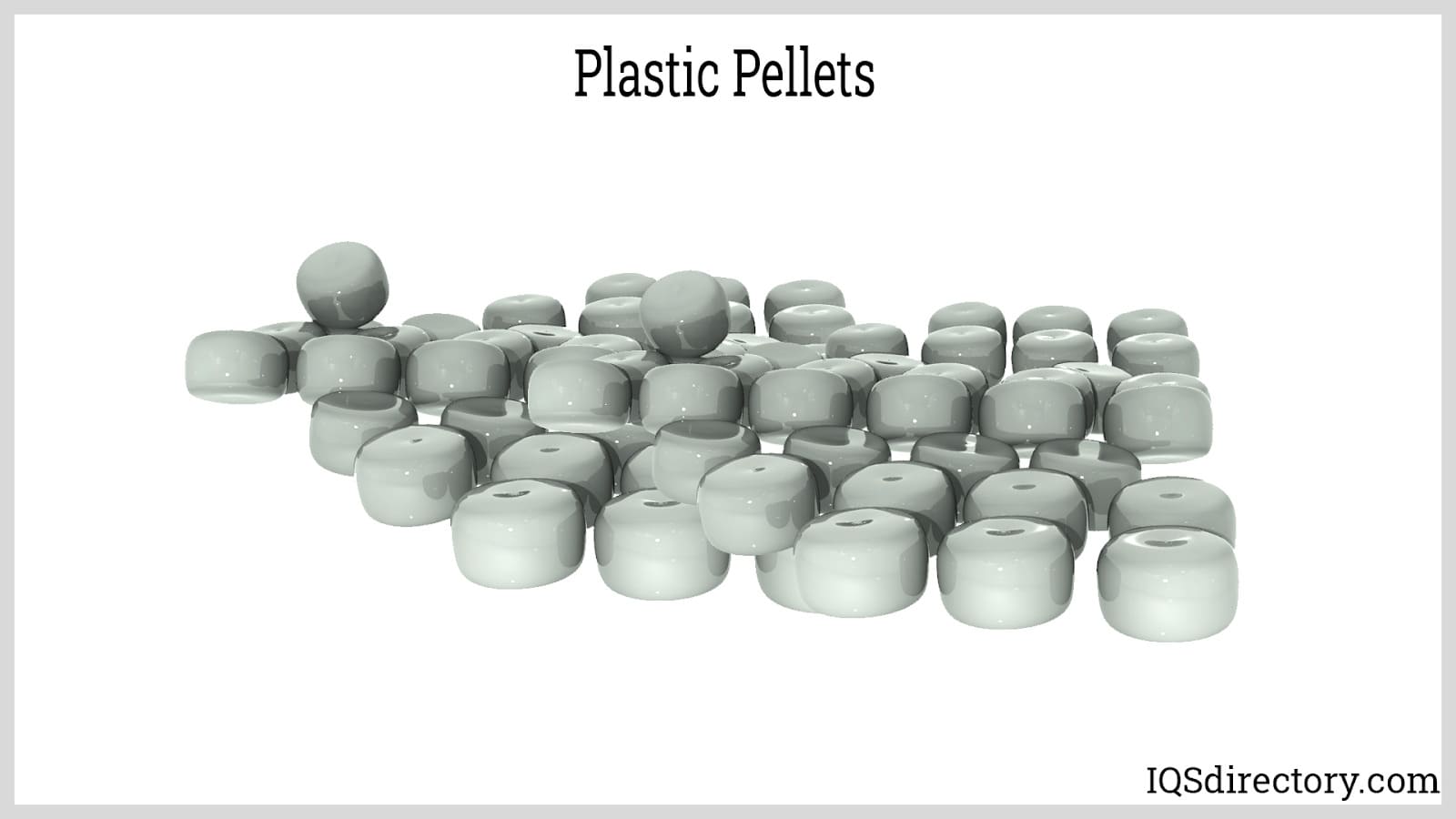
Raw plastics are supplied to pellet form for manufacturing where they are processed to create the final product.
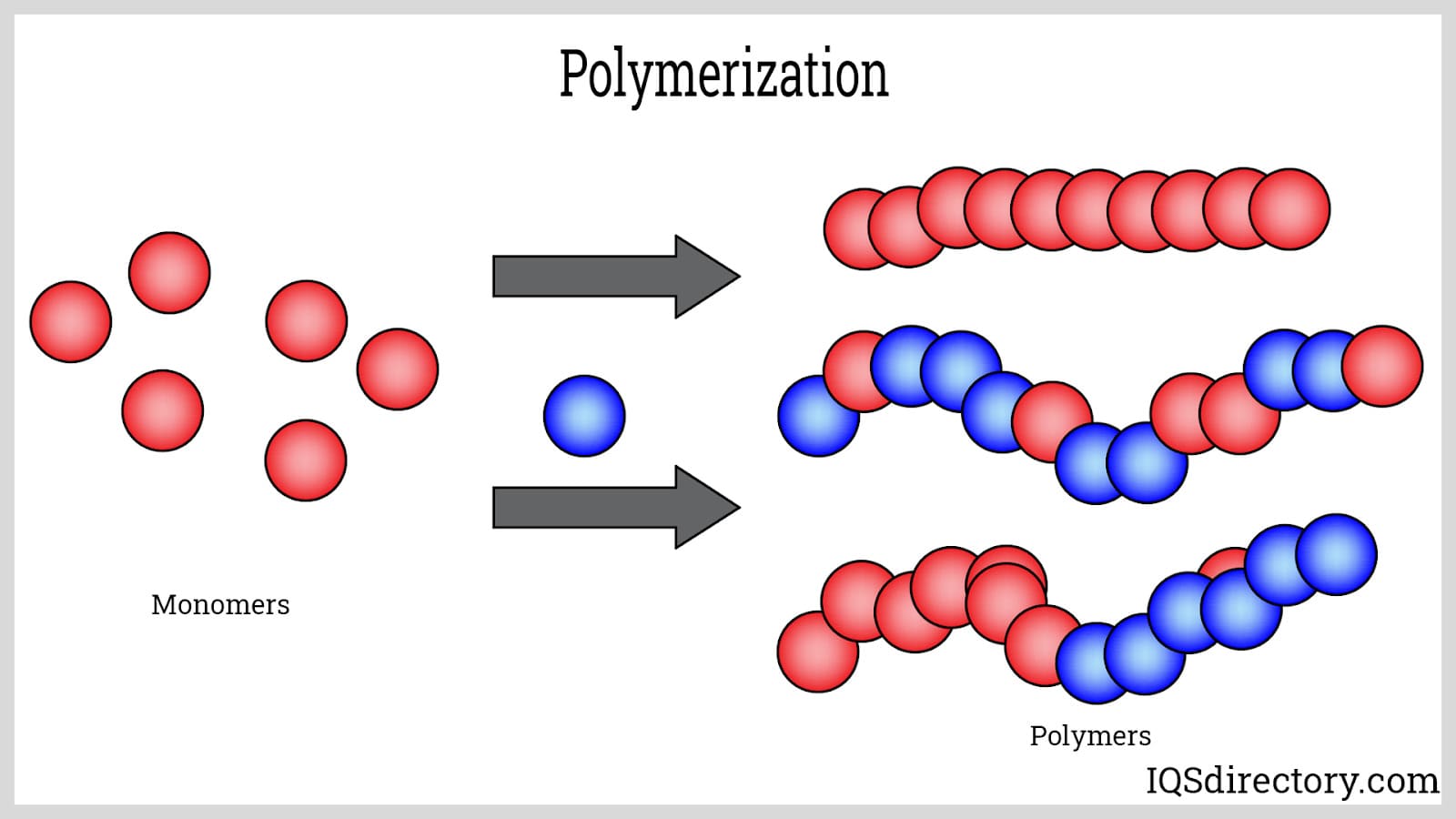
Polymerization is the process of forming macromolecules with monomers to create polymers.
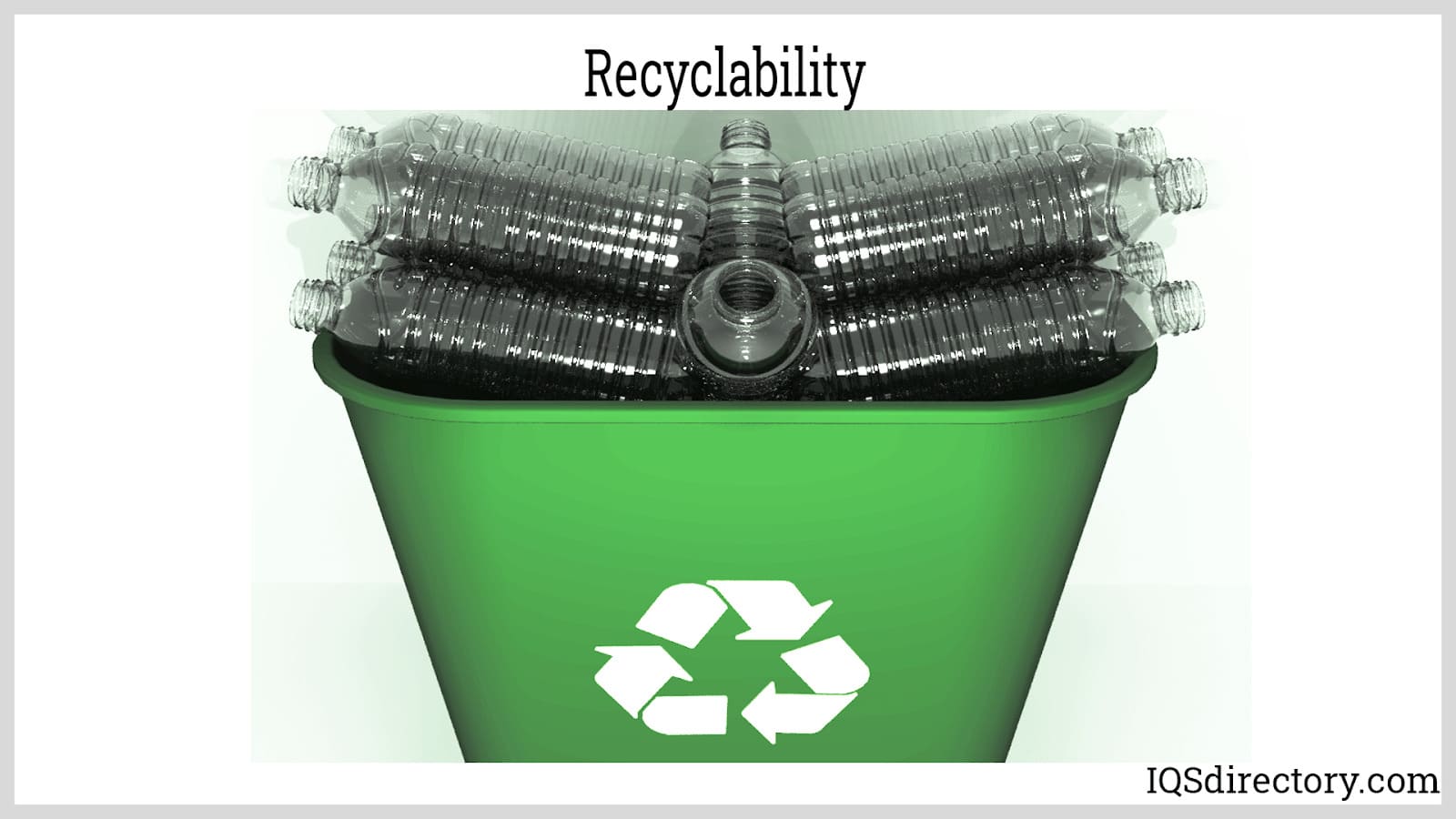
Varieties of plastics can be recycled, which in turn are melted and reformed into a new product.
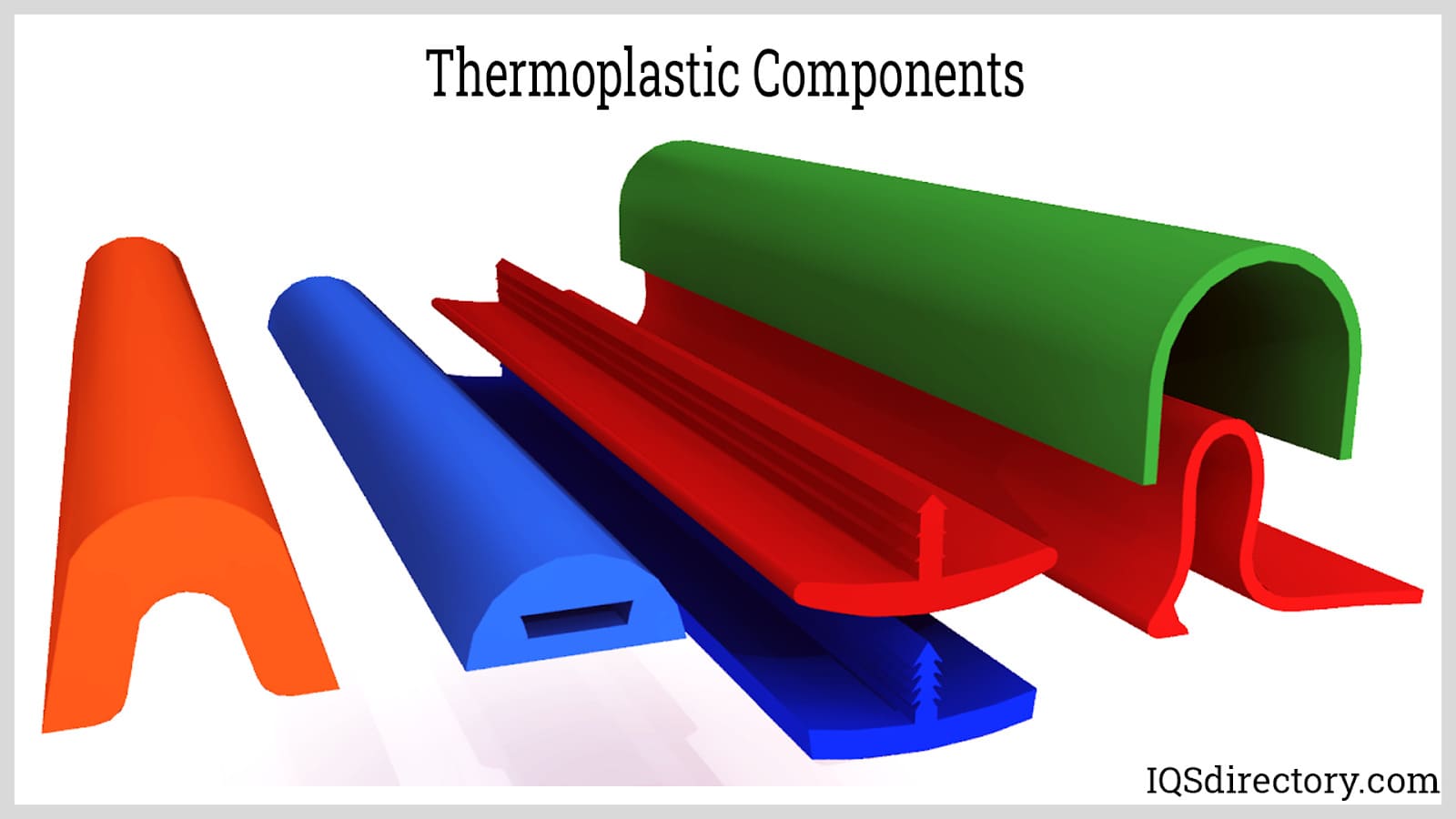
Thermoplastics are less prone to damage from chemical reactions.
Types of Plastic Produced
There is a wide variety of plastic materials on the market today. Some of these include polyethylene, polystyrene, high-density polyethylene, low-density polyethylene, polyoxymethylene, polyvinyl chloride and more.
Polyethylene
Polyethylene is the most commonly used member of the plastics family. It is being used to produce a plethora of products, from artificial knees to shampoo bottles and milk cartons.
Polystyrene
Polystyrene is also ever-present in modern life, though more frequently referred to as the trademarked extruded foam, StyroFoam™. Styrofoam is highly useful for insulation, but it is not recyclable.
High-Density Polyethylene HDPE
HDPE is a thermoplastic made from petroleum. It is known for its high strength-to-weight ratio and solvent resistance. It is often found used to make bottle caps, swimming pool components, vehicle fuel tanks, and food storage containers, among other things.
Low-Density Polyethylene LDPE
LDPE was the first grade of polyethylene ever mass produced. Though a wide range of other plastics have been invented since it was first sold on the mass market, it remains popular today. It is known for its chemical resistance, flexibility, and toughness. Most often, it is used to make all-purpose containers, soft parts like snap-on lids, plastic wrap, and packaging.
Polyoxymethylene
Polyoxymethylene, also known by names like acetal and Delrin, is another common plastic, often used as a metal substitute and therefore very popular in the automotive and construction industries. It has good tensile strength and excellent machinability.
Polyvinyl Chloride PVC
Polyvinyl chloride, known more commonly as PVC or vinyl, is a thermoplastic that comes in two basic forms: rigid and flexible. PVC is the third-most produced synthetic polymer in the world, and it is popular for use in construction, packaging, card fabrication (credit cards, debit cards, etc.), plumbing, electrical insulation, inflatables construction and more.
ABS (Acrylonitrile-Butadiene-Styrene)
ABS is a popular family of resins that is strong and resistant to most chemicals and stains. ABS is created by the polymerization of acrylonitrile and styrene (liquids) and butadiene (a gas).
Acrylic
Acrylic is made of clear, thermoplastic resins that are found in acrylic acid and natural sources like petroleum.
Fluoroplastic
Fluoroplastics, such as Teflon, are heat, moisture and wear resistant, and thus are used for many different valve, gasket and bearing applications. Fluoroplastics are flexible thermoplastics.
Phenolic Plastic
Phenolic plastic is in the categories of polyester and vinyl ester. It is composed of phenol and formaldehyde, has the same strength as iso-polyester and is the best material for fire safety.
Polycarbonate
Polycarbonate has good light transmission and stability and the highest rating of all transparent thermoplastics. Some applications for polycarbonate include electronic housings, machine guards and aircraft panels.
Polypropylene (PP)
Polypropylene is a kind of plastic that is very flexible at low temperatures and resistant to chemicals. PP is frequently used for banner materials.
Polyurethane
Polyurethane is used for bumpers, gears, gaskets and roll covers. Polyurethane is a tough and durable plastic that has good abrasion resistance and a high flex-life.
Applications of Plastics
There are limitless industrial, commercial and residential applications for plastic. Virtually every industry utilizes some form of it. Chemical and food processing, water treatment, gas and oil, medical, pharmaceutical, aerospace, automotive, building and construction industries are among those that utilize the common applications for plastic parts and products.
Plastic Products Produced
Highly diversified, plastic materials can be purchased in supply stock forms such as plastic rods, plastic sheets, and plastic films. While these items may be used as the finished product, they easily comply with secondary processing such as plastic fabrication and precision plastic machining, in order to make a myriad of other products. Some of the countless plastic products available to industrial, commercial, and retail markets include flexible tubing, packaging material, storage containers, dishes, mechanical gears, electronic insulators, insulin pens, inhalers, toys, some instruments, shieldings, plastic wraps, milk cartons, toothbrushes, aircraft panels, windows, bottles, and pipes.
Things to Consider When Purchasing Plastic
If you’re searching for a plastic or plastic product, it’s important to know that you must carefully consider the unique properties of each specific plastic available to you. You need to think about requirements such as heat resistance, pliability, biodegradability, wear resistance, sterility, corrosion resistance, etc. You also need to consider any quality/performance standards to which you are beholden.
Once you know the general type of plastic in which you are interested, or at least your specifications, you need to bring your project to a reliable plastic provider or plastic product manufacturer. To make your life easier, we’ve compiled a list of those plastics companies and fabricators in whom we have the most confidence. You will find it near the top of this page. Check out the company profiles we’ve provided or go straight to their individual websites to learn more about them. Choose from among them by first narrowing them down to your top choices, and then reaching out these top choices individually. Talk to them about your application specifications, your design requirements, your budget and timeline, and their delivery options. Make sure to note the tone of which they speak or write to you, as you want to find a manufacturer that is both technically capable and a good customer service provider. After speaking with each of them, compare and contrast your notes, and choose the best fit, and give them a call.
Global Plastics Market
The global plastics market is booming, and competition is great. It’s undeniable that looking to overseas plastic engineering options can offer significant savings. Many customers, for example, now turn to companies in China for their plastic goods. However, before you take your business out of the country, consider these points:
Plastic Sustainability
Because we’ve come to understand the detrimental effects of plastics on the environment, both in waste and energy consumption, researchers have spent a lot of time coming up with more sustainable ways to manufacture and consume plastics. If you seek a manufacturer overseas, you have to be extra careful to make sure that they are using the latest sustainable technologies.
Clarity of Costs
Submitting bids to companies overseas is not always easy, and the answers you get are not always clear. You have to ask extra questions about factors like: warehousing and warehousing security, fair currency exchange, customs, and freight carriers and restrictions.
Regulations and Tariffs
Another thing you have to think about is regulations and tariffs. Has the US recently enacted new regulations related to your material or product? If so, does the company with whom you want to work honor these regulations? Do they use certification programs that will be accepted in the US? Are there any large tariffs or import fees?
Possible Miscommunication
When you work with a company overseas, you will likely run into all sorts of communication challenges. These include different language skills, time zones, and cultures. Even when you believe you’re communicating clearly, you may not be in the eyes of your manufacturer, and vice versa. Miscommunication can lead to all sorts of headaches. Imagine if your manufacturer gets your order wrong. If you’re working with someone internationally, you cannot simply ship it back to them and get it exchanged. Instead, you’ll have to go through all the international trade paperwork, fees and long wait periods that you did before.
In the end, the hassles and pitfalls of doing business overseas often far outweigh the benefits. So much of the exchange between the client and the manufacturer comes down to trust, and trust is much harder to gain and maintain with all of the challenges of international business. That’s why we recommend working with one of those regional companies we’ve listed above.
Plastic Terms
Additive
A substance that is added to a resin to enrich particular characteristics.
Aging
The chemical and physical changes a material undergoes over time, due to environmental forces that will deteriorate or improve the material.
Alloys
Combinations of polymers or copolymers with other elastomers or polymers.
Binder
A resin or other substance that unites particles. Binders supply mechanical strength and guarantee solidification, consistent uniformity or adhesion to a surface coating.
Clarity
The lack of cloudiness in a plastic material.
Composite
A plastic structural substance that is comprised of a blending of materials.
Compressive Strength
The capacity of a plastic material to withstand crushing forces.
Copolymer
Different monomers that chemically react with one another, resulting in a compound.
Cure
The process of altering properties of polymers into a state of greater stability and usability. Curing is achieved through radiation, heat or reaction with chemical additives.
Cure Cycle
The period of time at set conditions in which a reacting thermosetting material is cured.
Discoloration
A change in the original color of a plastic material due to environmental conditions, such as light exposure and chemical attack.
Forming
The procedure in which an existing plastic shape is changed into another one.
Hygroscopic
The tendency of certain plastic materials to absorb water.
Masterbatch
A concentration of material in a base polymer, such as pigments, additives and fillers.
Opaque
Plastic materials that will not transmit light.
Plasticizer
A high-boil organic or liquid low-melt solid, the addition of which gives flexibility to hard plastics. Plasticizers differ in their solvating capabilities and softening actions, due to the reduction of intermolecular pressures in the polymer.
Plastisol
A blend of resins and plasticizers that can be transformed into continuous films through the application of heat.
Polymer
A synthetic or natural compound of high molecular weight, which is comprised of long chains of repeating units, each relatively light and simple, including polyethylene and elastomer.
Reinforced Plastics
Plastic materials with increased mechanical properties, resulting from the embedding of high strength fillers in the composition.
Resin
A solid or pseudosolid organic material that typically has a high molecular weight with a propensity to flow when stress is applied and generally has a melting or softening range.
Surfactants
Chemicals that permit the formation of a close mixture or emulsion of usually mismatched substances by the alteration of the surface characteristics and the manipulation of the flowing and wetting characteristics of liquids.
Thermosets
Plastic compounds or resins that in their last stage are insolvable and infusible. After curing is complete, thermosets cannot be softened through heat.
Virgin Material
Plastic material, such as granules, pellets, floc or liquid, that has not had any processing applied to it other than what is needed for initial manufacturing.